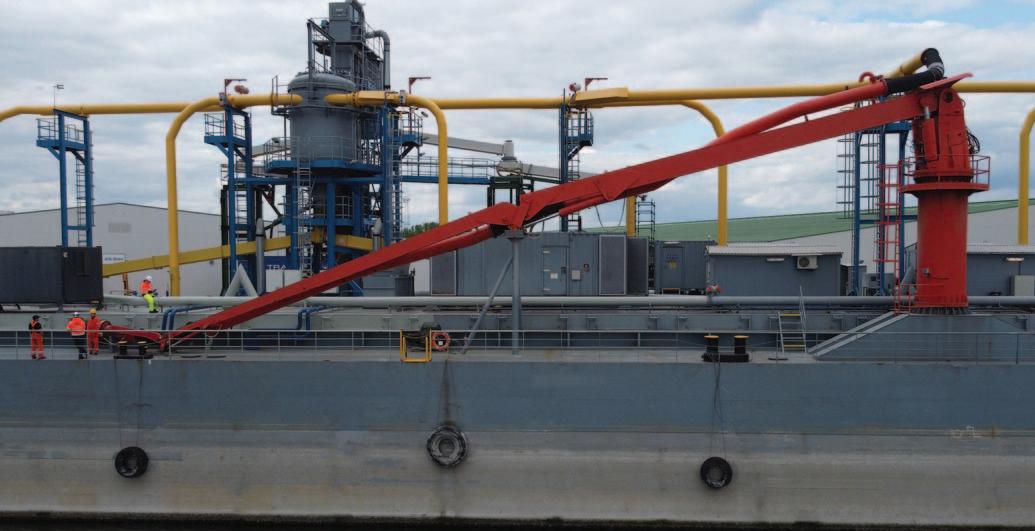
4 minute read
Floating terminals by Lion Bulk Handling
Mounted ship unloader floating terminal.
Lion Bulk Handling is an expert in maritime and portside material handling. The company designs and engineers its own key components, adding other proven technologies from leading manufacturers to form its completely integrated systems. The company has 50 years of design and engineering experience in equipping dry bulk ships, barges, supply vessels, harbour loading and unloading equipment, drilling rigs and floating terminals. For marine applications, Lion Bulk Handling has a range of floating terminal configurations.
Floating Terminals
A floating terminal can be used as a temporary facility for a large construction project or a permanent facility for terminals with insufficient space on land. One of the unique characteristics of a floating terminal is the capability to be stationed up to 200 metres offshore and pumping the cement or fly ash to shore via a floating pipeline. Therefore, the terminal does not need any dock. Another characteristic of a floating terminal is to act as extra storage for loading ships, bagging plants or even bulk trucks on the dock.
THE FOLLOWING CONFIGURATIONS ARE AVAILABLE FOR FLOATING TERMINALS:
AIRSLIDE LOADING SYSTEM
Airslide loading systems use a slope that harnesses gravity to convey fine powders. This is achieved by forcing air through a porous fabric for the required fluidization. The steel-structure boxed frames and housings, abrasion-resistant polyester fabric, and high-quality blowers combine to form rugged and versatile loaders to handle materials like cement, alumina, and hydrated lime, fly ash and plastic powders. Additionally, air-slide-based loaders are fully enclosed and self-cleaning and have no moving parts. This means they are quiet, dust-free and require almost no maintenance.
Material is loaded for transport pneumatically or mechanically. The central loading point with air slides, fitted with valves and drop-off pipes, distributes the dry material over the holds.
KEY BENEFITS gravity loading; v low energy consumption; v easy to operate; v central loading point; and v no weather delays v
TECHNICAL DETAILS max. vessel size: up to 40,000dwt; v maximum convey capacity: up to v 1,500tph; and project: new build or conversion. v
PIPELINE LOADING SYSTEM
The pneumatic loading principle is utilized when a ship is loaded through a pipeline system. In this case, the cement is transported via a pneumatic conveying system all the way to the ship through a pipeline. A flexible rubber hose connects the pipeline onshore with the ship’s onboard pipeline.
KEY BENEFITS
Loading by pressure through pipe and v hose connection
No on-board energy consumption v Easy to operate v No weather delays v
Adapted to shallow rivers and v estuaries
TECHNICAL DETAILS
Max. vessel size: Up to 10,000dwt v
Max. convey capacity: Up to 500tph v
Project: New build or conversion v
MOUNTED SHIP-UNLOADER
A floating terminal mounted ship-unloader is ideal for unloading open top ships or barges into the floating terminal. Large tidal differences do not influence the length of the suction arm, as the terminal and bulk carrier are both floating.
KEY BENEFITS operations possible with large tidal v differences; and unloading open top ships and barges v
TECHNICAL DETAILS max. vessel size: up to 15,000dwt; v max. convey capacity: up to 360tph; v and project: new build or conversion v
TERMINAL-TO -SILO CONVEYING
Terminal-to-silo conveying uses a completely closed bulk handling unloading system, like a double re-loader system.
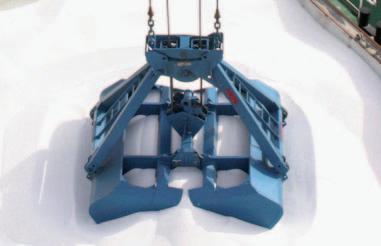
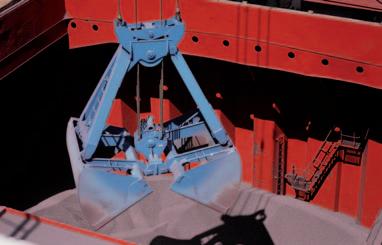
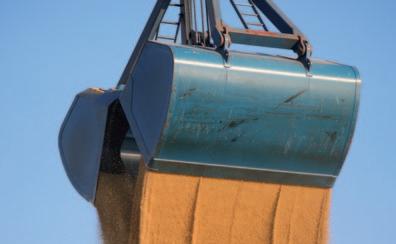
This unloading system is integrated into the floating terminals hull and uses a vacuum and pressure to convey the dry bulk material into the silo directly. Lion Bulk Handling’s floating terminal solutions are included with a fluidization floor for unloading the cargo from the holds in every weather condition.
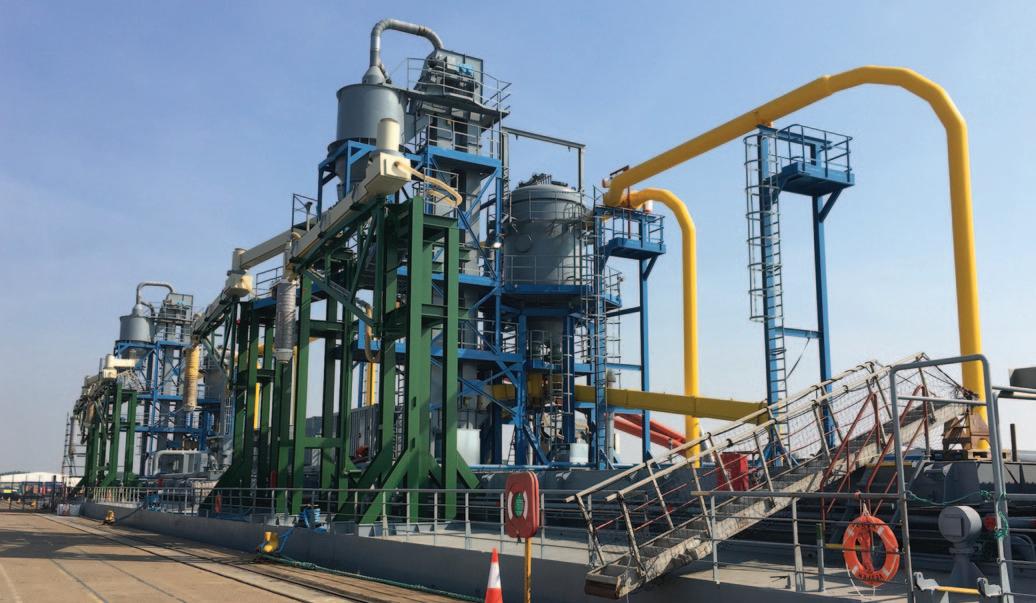
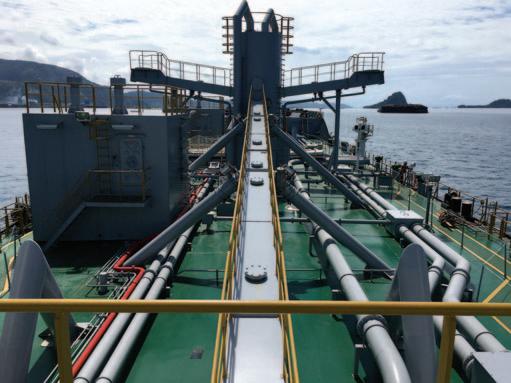
KEY BENEFITS operations possible with large tidal v differences; highly reliable pneumatic system; v fully automated; v no weather delays; v continuous material flow; and v flexible re-loader arrangement above v or below deck.

TECHNICAL DETAILS maximum vessel size: up to 40,000dwt; v maximum convey capacity: up to v 1,000tph; and project: new build or conversion. v
TERMINAL-TO -SHIP CONVEYING
A floating terminal can be used as a permanent dock storage facility for dry bulk materials when the shore does not have enough space or suitable storage facilities available. But a floating terminal can also be used as a loading station on the open sea for loading (smaller) ships for supplying inland storage locations. A specially designed shiploading bellows for gravity loading or pipeline loading system can be installed for loading ships from the floating terminal. Both solutions use a vacuum to retrieve the dry bulk material from the cargo holds.
KEY BENEFITS
TERMINAL-TO -TRUCK CONVEYING
When a floating terminal is used as a permanent dock storage facility for dry bulk materials and no storage facilities are not available, terminal-to-truck conveying is an excellent solution.
Terminal-to-truck solutions use the continuous suction pump solution, which uses only a vacuum and the CSP-pump to convey the dry bulk material from the floating terminal towards the bulk trucks on the dock site.
KEY BENEFITS operations possible with large tidal v differences; both open top or closed top ships or v barges possible; automated; and v continuous material flow. v
TECHNICAL DETAILS maximum vessel size: up to 10,000dwt; v maximum convey capacity: up to v 500tph; Project: New build or conversion. v direct truck loading; v operations possible with large tidal v differences; multiple terminals with unloading v operations; low energy consumption; v automated; and v continuous material flow. v
TECHNICAL DETAILS maximum vessel size: up to 20,000dwt; v maximum capacity: up to 200tph; and v project: new build or conversion. v
Louis Dreyfus Ports & Logistics (LDPL), is a company under Louis Dreyfus Transport and Logistics (LD T&L) and part of Louis Dreyfus Armateurs (LDA), a French familyowned company founded in 1851, writes
Arunabh Tripathi
LDA originally started as grain trader eventually entering into the shipping business by firstly chartering the ships and then later owning and operating them. As business grew over centuries, LDA ventured into various types of shipping and maritime solutions for a wide range of industries such as oil & gas, submarine cable, manufacturing, mining and utilities. This growth resulted in the creation of focused entities within LDA with specific objectives of identifying, developing, evaluating, realizing, designing, constructing, delivering and operating these maritime solutions for a wide range of customers. LDPL was hence formed and focused on providing customized ports and shipping solutions.
LDPL is pioneer in providing maritime solutions such as offshore transshipment, barging, freight forwarding, project cargo, port handling and ship management.
Dry bulk offshore transshipment is one of the native activities of LDPL commencing in the early 90s with the deployment of floating cranes in Indonesia for the transshipment of coal. It rapidly expanded its offshore business comprising floating cranes and barges worldwide from Asia to South America, working in Indonesia, India, United Arab Emirates,