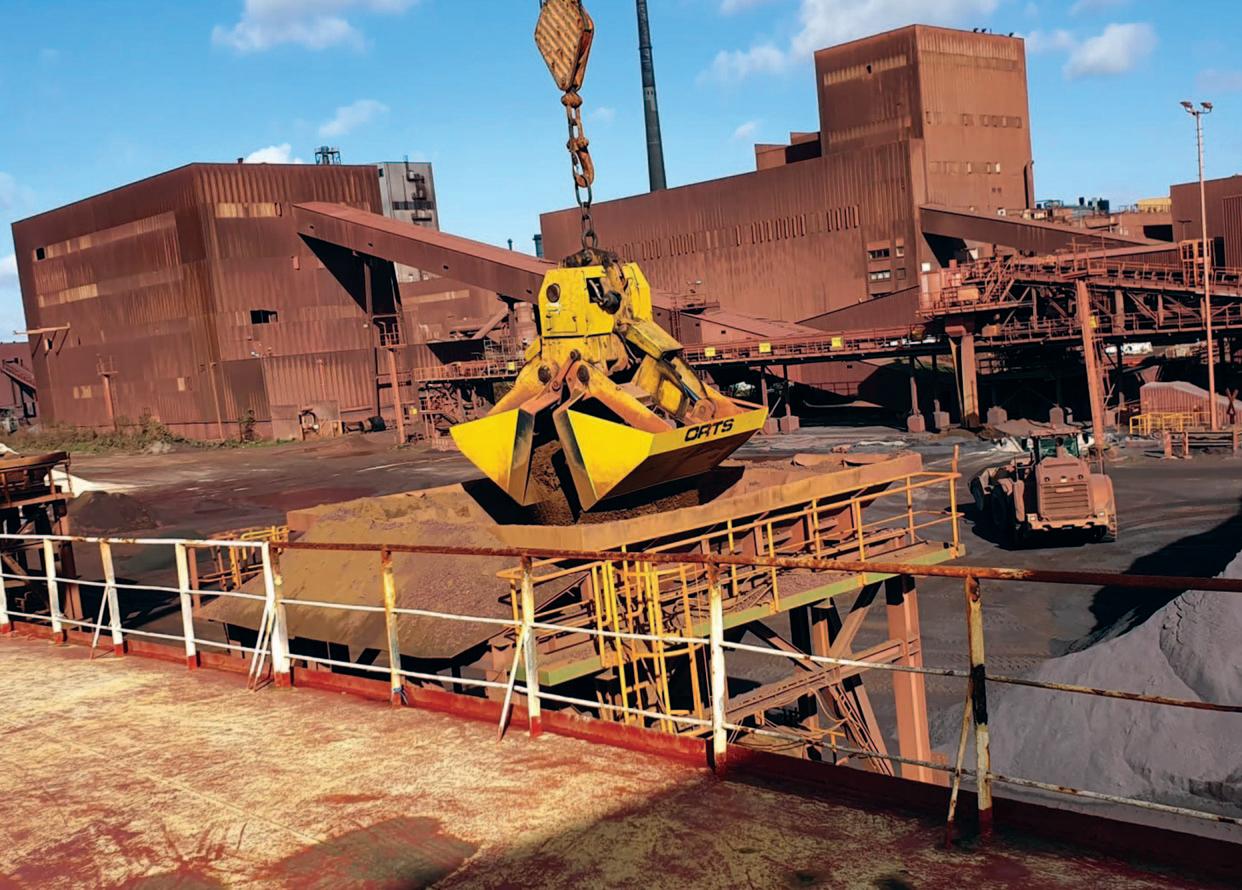
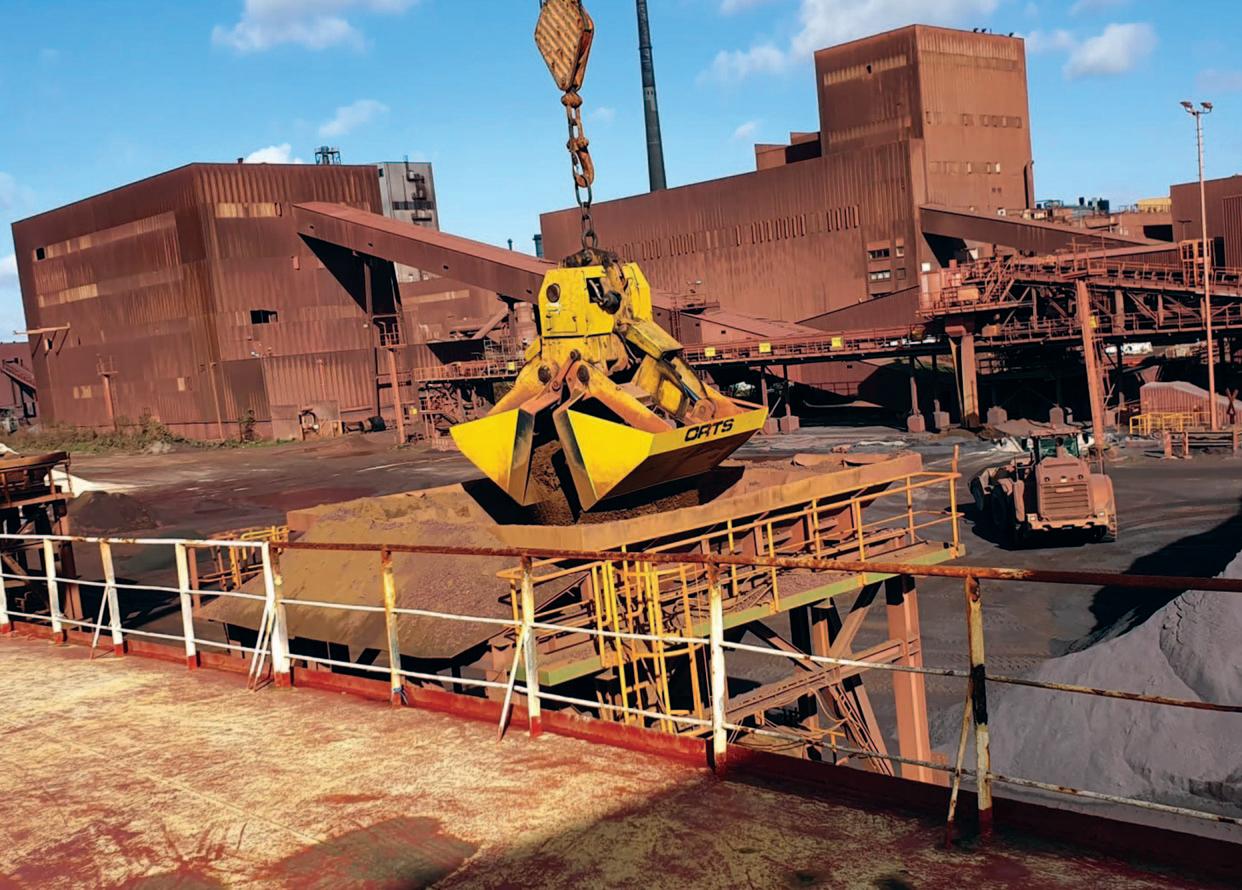
Rising star
The LH 110 M High Rise Port Litronic
With weight-optimised equipment and a preciselyengineered modular structure, each LH 110 M High Rise is individually tailored to satisfy the requirements of port customers around the world. The latest operator-friendly technology results in easier and faster handling.
www.liebherr.com
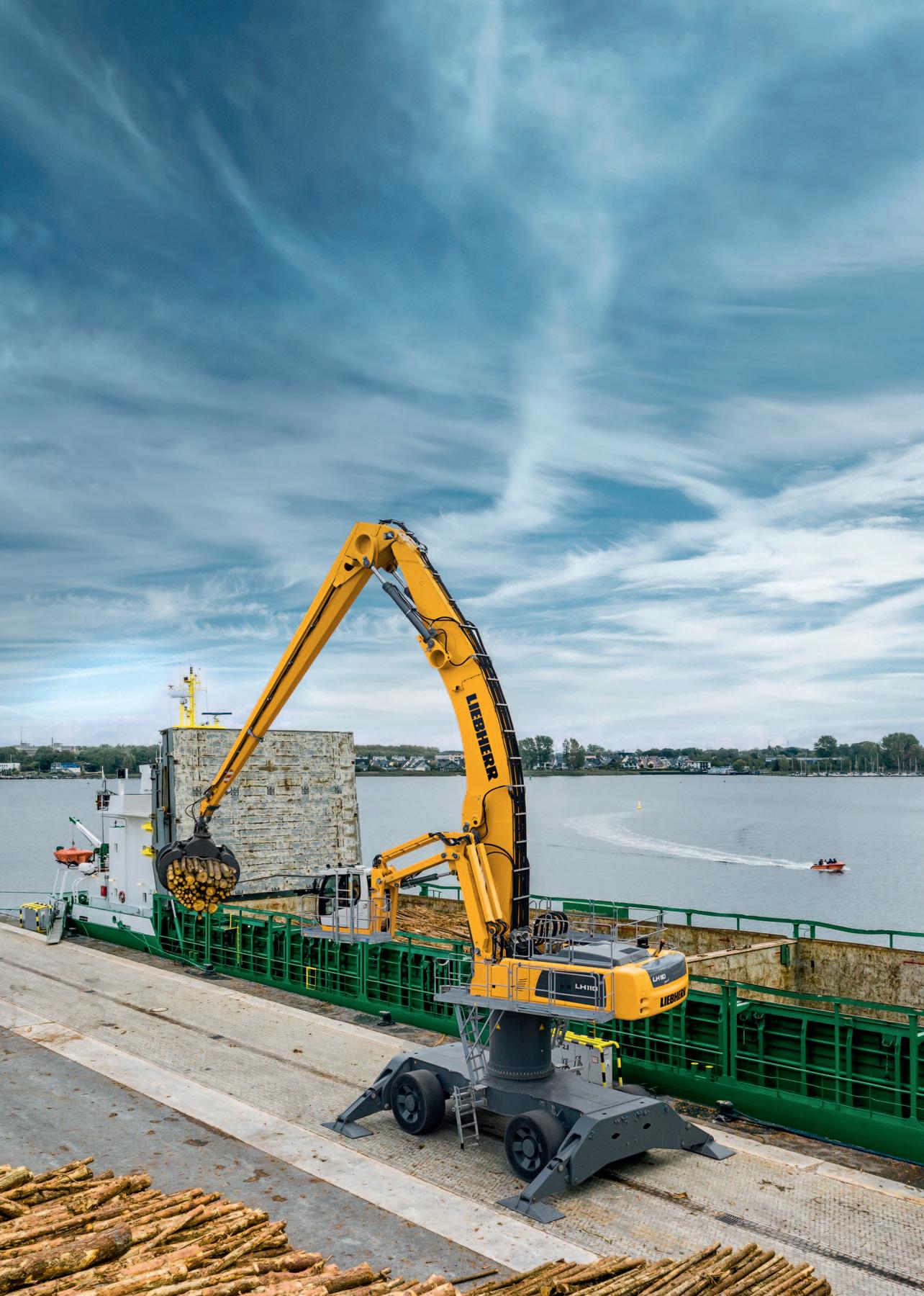
Material handling machine
DCi
ORTS fully radio controlled diesel hydraulic grab DHS-B unloads iron ore at Bremen port. Ship grabs were out of order, so ORTS rented grabs to the shipowner. With ORTS fully radio controlled diesel hydraulic motor grabs, only a hook is necessary.
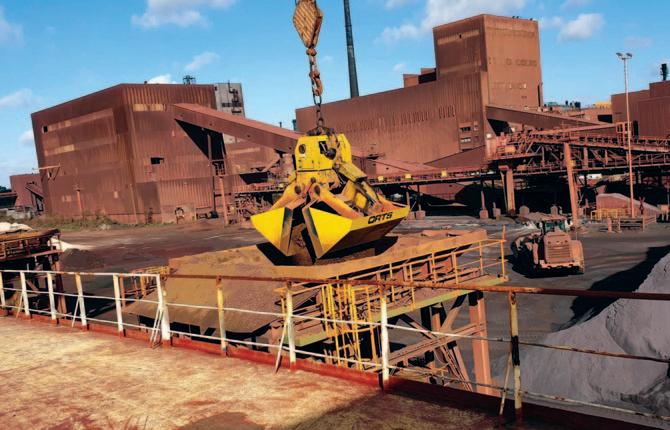
Orts GmbH Maschinenfabrik
E: sigvard.orts-jun@orts-gmbh.de
W: www.orts-grabs.de
T: (+49 451) - 39885 - 15
PUBLISHERS
Jason Chinnock jason@dc-int.com
Andrew Hucker-Brown andrew@dc-int.com
EDITORIAL
Louise Dodds-Ely Editor louise@dc-int.com
Jay Venter Deputy Editor editorial@dc-int.com
Samantha Smith Directories directories@dc-int.com
Bernice van Wyk Office Manager accounts@dc-int.com
SALES
Matthew Currin Senior Sales sales2@dc-int.com Executive
Zack Venter Advertisement Sales sales@dc-int.com Executive
CORRESPONDENTS
Brazil Patrick Knight
India Kunal Bose
Europe Barry Cross
UK Maria Cappuccio
UK Michael King
UK Richard Scott
ADMINISTRATIVE OFFICE
Business Publishing International Corporate Park, 11 Sinembe Crescent La Lucia Ridge, South Africa, 4051
Tel: +27 31 583 4360
Fax: +27 31 566 4502
Email: info@dc-int.com
Twitter: twitter.com/drycargomag
HEAD OFFICE
Trade Publishing International Limited
Clover House, 24 Drury Road, Colchester, Essex CO2 7UX, UK
Tel: +44 (0)1206 562552
Email: info@dc-int.com

Website: www.drycargomag.com
Twitter: twitter.com/drycargomag
ISSN 1466-3643
Insta: www.instagram.com/drycargointernational
Trade Publishing International Ltd does not guarantee the information contained in Dry Cargo International, nor does it accept responsibility for errors or omissions or their consequences. Opinions expressed herein are not necessarily those of Trade Publishing International Ltd
© Trade Publishing Int’l Ltd 2023
REGIONAL REPORT
More optimism about coal trade growth
Additional evidence emerging in recent weeks points towards strengthening commodity import demand in a number of countries. Consequently prospects for world seaborne dry bulk trade this year and into 2024 have become brighter.
Despite ongoing restraints, an International Monetary Fund appraisal of the world economy published at the end of July was slightly more positive. Forecast global growth in gross domestic product is now “modestly higher” than predicted a couple of months ago. But growth in 2023 is still expected to be 0.5 percentage points lower than seen last year, at 3.0%, and support is likely to be derived mainly from the envisaged acceleration in China to 5.2%, following a low 3.0% last year.
COAL
The outlook for world coal trade this year has improved recently. Several forecasts suggest that an increase of 3–5% or more now looks achievable, after a flat outcome in the previous twelve months. Both steam (or thermal) coal and coking coal segments are likely to see growth.
In an end-July update of trends in the global coal market, the International Energy Agency highlighted “elevated global demand for thermal coal imports” comprising the largest part, about fourfifths of the total. IEA analysts envisage that world seaborne coal trade as a whole in 2023 could exceed the peak
1,331mt (million tonnes) recorded four years ago, reaching 1,335mt. The total is equivalent to about a 6% rise from last year’s volume. Higher imports into China are a feature of the upturn unfolding.
IRON ORE
Resumed growth in iron ore trade is also evolving. This view is heavily dependent on assumptions about China’s imports, comprising three-quarters of the world volume. In the first half of 2023 imports into China increased vigorously by 40mt or 8%, to reach 576mt. However, signs suggest that the annual growth rate will not be so high.
An estimate published last month by the Australian Government Department of Industry, Science and Resources, suggested that global iron ore trade could increase by 2.2% in 2023 to 1,608mt (including land movements). Changes in some individual import demand elements may differ from those envisaged, including a flat imports volume in China, but the overall world growth predicted seems realistic. A further rise is foreseen next year.
GRAIN & SOYA
Prospects for world grain and soya trade in the period ahead are still looking positive. Estimates for trade in both wheat plus corn and other coarse grains, and soyabeans plus meal, indicate 2–3% growth could be seen in the new 2023/24 trade year starting October
2023 (beginning July for wheat). That outcome represents an improvement compared with the preceding twelve months when grain trade weakened.
According to a Bulk Shipping Analysis compilation of separate US Department of Agriculture calculations, global grain and soya trade is likely to be marginally (by1%) lower during the 2022/23 trade year ending next month. A 6mt decrease to 660mt is estimated. Forecasts published in mid-July indicate that a 24mt increase to 683mt could follow in 2023/24. Higher imports into Asian countries are expected to be a prominent feature.
MINOR BULKS
Global seaborne trade in aluminium raw materials — bauxite, and the processed alumina — apparently increased by about 8% in 2022, to around 190mt. Supported by further expansion of China’s imports, comprising two-thirds of the total volume, another similar rise is foreseeable this year.
BULK CARRIER FLEET
The world fleet of bulk carriers is expected to be augmented during 2023 by higher newbuilding deliveries than seen last year, as shown in table 2. The additional capacity is likely to be spread over several size categories. But fleet growth may remain below 3% because scrapping is also expected to increase, while remaining at a relatively low level.
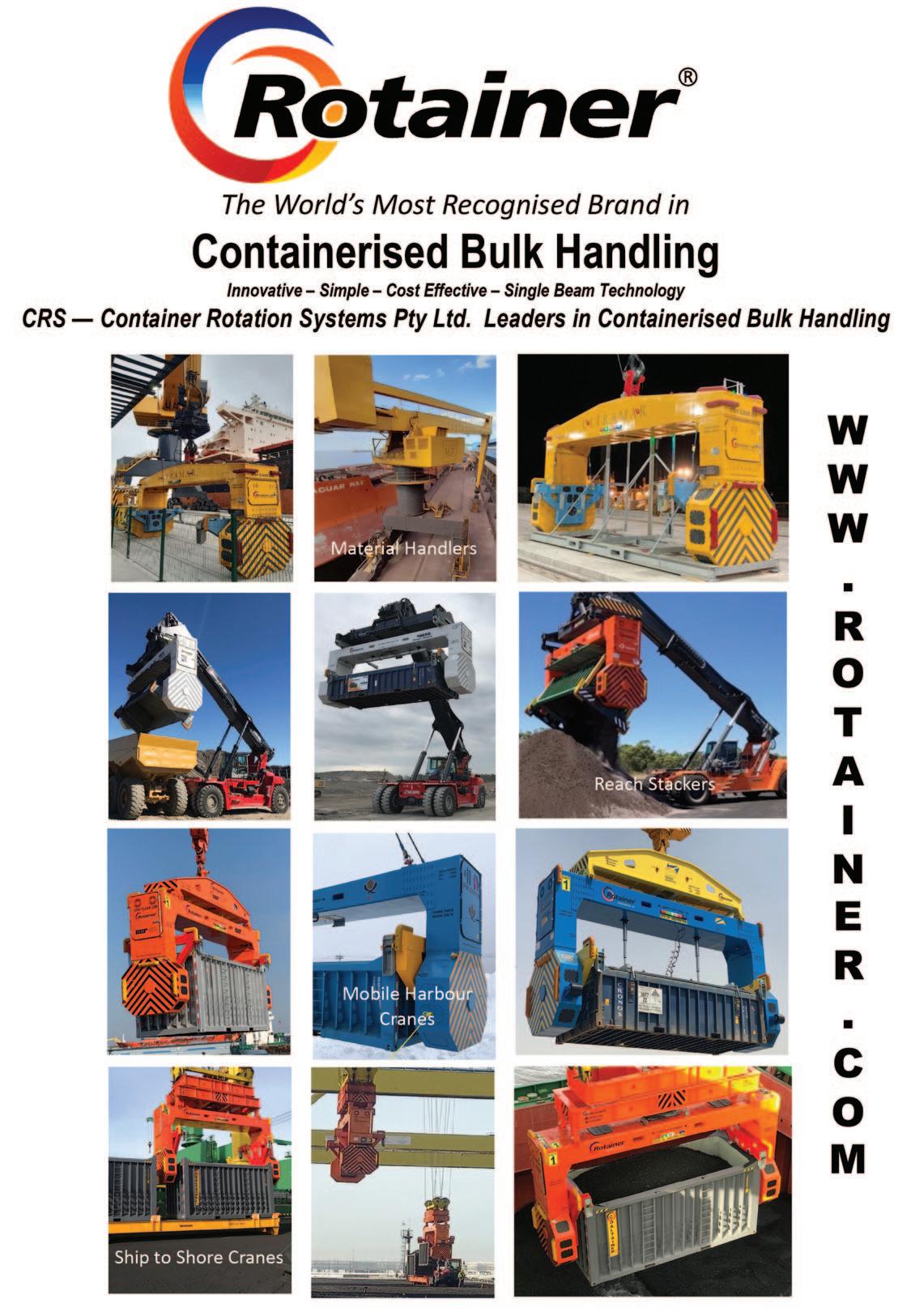
What moves China to centralize iron ore purchases?
To make a tonne of crude steel, around 1.6 tonnes of iron ore is needed. But that’s average. At the same time, the quantity of ore required to get a unit of steel will depend on the specific production process and iron (Fe) content in ore, says the World Steel Association.
Among the world’s most traded commodities, export trade of iron ore in 2021 generated revenues of $222bn in which China alone had a share of $146bn followed by Japan at $15.1bn, South Korea at $10.6bn, Chinese Taipei at $4.07bn and the Netherlands at $3.91bn. Mainland
China’s National Bureau of Statistics (NBS) says the country’s crude steel production fell by 2.1% to 1.013bn tonnes in 2022. This marked a second successive annual decline for the world’s largest steel producer. As a
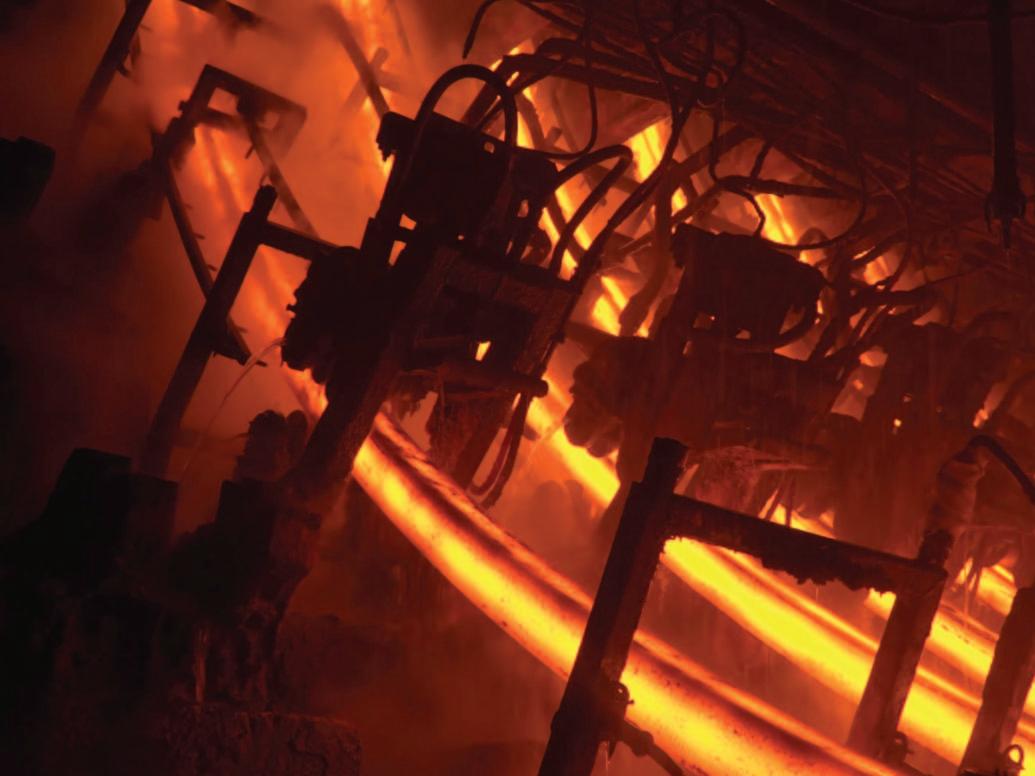
consequence of stepped up Beijing efforts to contain carbon emission by the ferrous sector, China’s steel output retreated for the first time in six years in 2021 by 3% to 1.03bn tonnes from the previous year’s record of 1.065bn tonnes.
As general economic activity moved to slow gear, particularly in sectors such as infrastructure, construction and house building (all major areas of steel application) along with Covid-related movement restrictions, China’s steel use in 2022 slipped by 3.3% or by 31mt (million tonnes) to 914mt. Even after all the corrections in Chinese steel production and consumption resulting from the country’s economic woes and commitment to make the steel industry carbon neutral by 2030, iron ore traders will always be
looking for cue in the working of the world’s largest steelmaker.
Nothing good is happening to the Chinese economy and therefore, to the steel industry and iron ore prices, except for occasional spurts, mainly on reports of restocking by steel mills. NBS says in a report to iron ore trade concern that factory gate prices fell further in June. This has fuelled concern about deflation risks at the same time adding to speculation about another round of potential economic stimulus. Bloomberg quotes a spokesperson for Societe Generale SA saying: “Today’s data certainly argues for more policy easing, which policymakers are already doing, but only in a measured manner.”
Concern is growing in China if
businesses, institutions, including banks and consumers in general postpone spending in the hope of prices further moving lower then that could be the reason for price dropping spiral. Not only this, steelmakers and iron ore producers are finding it to their concern that China’s passenger vehicle sales in June experienced a year-onyear contraction of 2.9% to 1.91m units in June. Is this not an indication of the growing ranks of consumers holding back on big-ticket spending because of stumbling economic recovery? According to China Association of Automobile Manufacturers, the country’s total vehicle production last year was 27.021m units, despite chip supply shortages. The automobile industry is a significant consumer of steel after construction and machinery building in China and any setback in vehicle sales has disturbing forebodings for steelmakers and in turn iron ore producers.
A Singapore based ore merchant has expressed concern about the “12.4% setback in June Chinese exports coming on the back of 7.5% reverse in May. Apart from a brief rebound in March and April, export shipments have suffered reverses since October because of weak demand in key markets. Over the past few decades China has built enormously large capacity in many sectors from engineering products to consumer goods to electronics for exports.
The World Bank tells us exports of goods and services constitute 20.68% of Chinese GDP. Since exports, a key pillar of growth of the Chinese economy continues to fare badly, Beijing is coming under increasing pressure to unveil a new set of
second largest economy. The occasional upward moves in iron ore prices on a low base at Dalian and Singapore exchanges are attributable to stimulus bets and active restocking by Chinese steel mills.”
RK Sharma, director general of Federation of Indian Mineral Industries says: “A country (read China) accounting for 57% of global iron ore demand and over 70% of seaborne trade in the mineral will all the time be necessarily counted as a big influencer of prices of iron ore and steel. Even while China owns the world’s fourth largest reserves of iron ore, domestic production size and also local ore quality requires of it to depend heavily on imports from Australia (BHP, Fortescue and AngloAustralian Rio Tinto) and Brazil (Vale).
In the meantime, iron ore producers all over the world are staying watchful as to how the newly constituted state owned mineral resources giant China Mineral Resources Group (CMRG) will consolidate the country’s mining investments and centralize purchase of iron ore.”
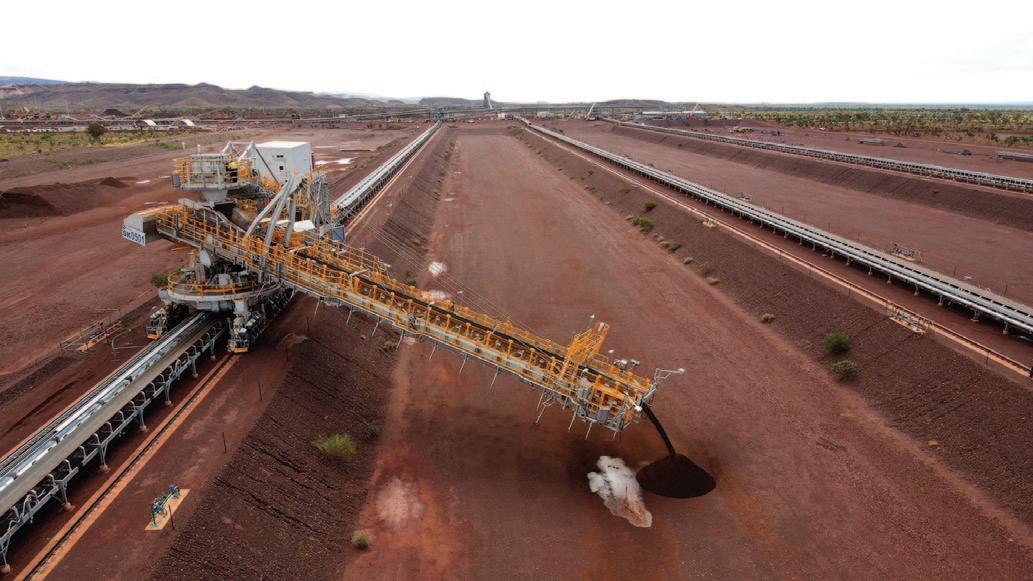
CENTRALIZATION OF CHINA ORE IMPORTS
The mandate of CMRG, which was registered in July last, includes housing of Chinese overseas mining assets assuming bigger and bigger dimensions all the time, particularly in Africa. Part of the country’s iron ore ‘foundation plan’, developed with inputs from the industry body China Iron and Steel Association (CISA) and supported by apex state planner National Development and Reforms Commission (NDRC) and governments of steelmaking regions, CMRG will attempt to consolidate all iron ore purchases by steel mills and the
China has been for long smarting under the discomfort that though it is importing over 1bn tonnes of ore, it has little say or influence on price movements in the commodity. Such is the volatility in the iron ore market — the price for benchmark 62% Fe, CFR China (TSI) SWA is now trading around $110 a tonne against the record high of close to $220 a tonne in July 2021 — steelmakers often are at the receiving end. Major ore producers in Australia and Brazil are extracting the mineral with such efficiency that their production cost is less than $30 a tonne. So in all situations through up and down cycles the ore majors remain in profits, the extent of profitability may vary depending on sale prices.
Nikkei Asia says in a report: “In 2021, China spent about $180 billion on iron ore imports. Its purchasing power is hobbled by the fact its steel industry is scattered among some 500 mills. Its sources are also concentrated, with Australia accounting for around three-fifths and Brazil about onefifth. Years of effort investing in mining abroad had only yielded equity of about 8% in overseas iron-ore mines as of 2020. The foundation plan aims to change the calculus in two ways: by changing the structure of China's iron and steel industry, and by changing its sources of iron ore.”
China wants the “unfair” situation to change which will allow its mammoth steel industry to exercise power in line with its very big purchase volume. CMRG that is mandated to handle purchases of ore of all constituents will be expected to bring down the cost of procurement of iron ore. Besides the programme to drive bargain for iron ore commensurate with the volume of
procurement, China would like to raise domestic ore production, albeit with care and get more and more steel by way of scrap recycling.
The challenge is Chinese ore is mostly of low grades of magnetite whose elaborate refining makes the cost more than double that of hematite variety found in abundance in Australia, Brazil and India. A factor that will have a bearing on iron ore prices in the medium and long term is Beijing’s focus to make growing volumes of steel through scrap recycling in electric arc furnaces. Steel derived from scrap recycling will use 75% less energy than when iron ore is processed through BF-BOF route. Recycling, therefore, emits much less carbon than is the case with making virgin steel from ore through a highly elaborate process.
However, at the same time, recycling puts a cap on iron ore demand. A CISA spokesperson said: “In 2030 and 2035, China’s scrap steel targets will increase to 350mt and then to 400mt.” This should be seen in the context of the country setting a peak steel production target of 1.065bn tonnes in 2025. Whatever official proclamations, China ore production does not show signs of any significant rise in near future. For, in a number of years in the past, hardly any China iron ore mines have received fresh investments in exploration and development. On the contrary, regular falls in investment for iron ore mine
development over the years has got everything to do with the nature of deposits, low Fe content in ore and challenges in getting a fair return. No wonder, Beijing saw it early that for the health of its giant steel industry it is desirable to buy large quantities of foreign origin ore and at the same time acquire iron ore assets abroad braving all political and economic challenges.
In a report last year, analysts at J.P. Morgan made the interesting remark: “As majors (foreign) grow volumes, Chinese domestic supply (of iron ore) will need to be curtailed to make room.” Their estimate is 2023 will see an additional 50mt of supply from global majors, including from Brazilian Vale, which has been able to ramp up production sufficiently after a tailings dam collapse at its iron ore mine in Brumadinho on 25 January 2019 killed nearly 300 people. The issue then for discussion at NDRC and CISA is how any new major investment in local mines development is justified when the world will continue to remain awash with the ferrous mineral. Instead should not CMRG move fast to have a major say in iron ore trading, particularly pricing favouring buyers as much as producers?
For major mining groups from BHP Billiton to Vale to leading steelmakers in China and elsewhere, ESG (environmental, social and governance) has a significant bearing on their policies. ESG standards
cannot but become more and more demanding in the face of governments from least developed to developed countries setting stringent conditions for grant of iron ore mining licences and implementation of mining projects post grant of licences. As lower emission steelmaking is becoming the order of the day, miners with access to high Fe content deposits will reap benefits of premiums over standard varieties. Vale has illustrated the point in a way that will encourage other miners to focus on making high grade agglomerates (HGA) for earnings improvement.
VALE EXPANSION PROGRAMME
Taking 2022 as the base year, Vale says of the total iron ore production of 308mt, the share of HGA was 32mt of 62.2% Fe. The 2030 ore output target for the company is 360mt in which HGA but with much higher Fe of 64% will be an estimated 100mt. During this period, the premium to be secured by HGA is to rise from $7 a tonne to $18–25 a tonne. The potential contribution to EBITDA (earnings before interest, tax, depreciation and amortization) through value addition to ore versus 2022 will be up to $10bn by 2026 and up to $50bn by 2030. But why should better quality ore fetch these high premiums to bolster EBITDA? Vale’s answer is: “High demand and challenged supply will support the premiums. The company is pursuing
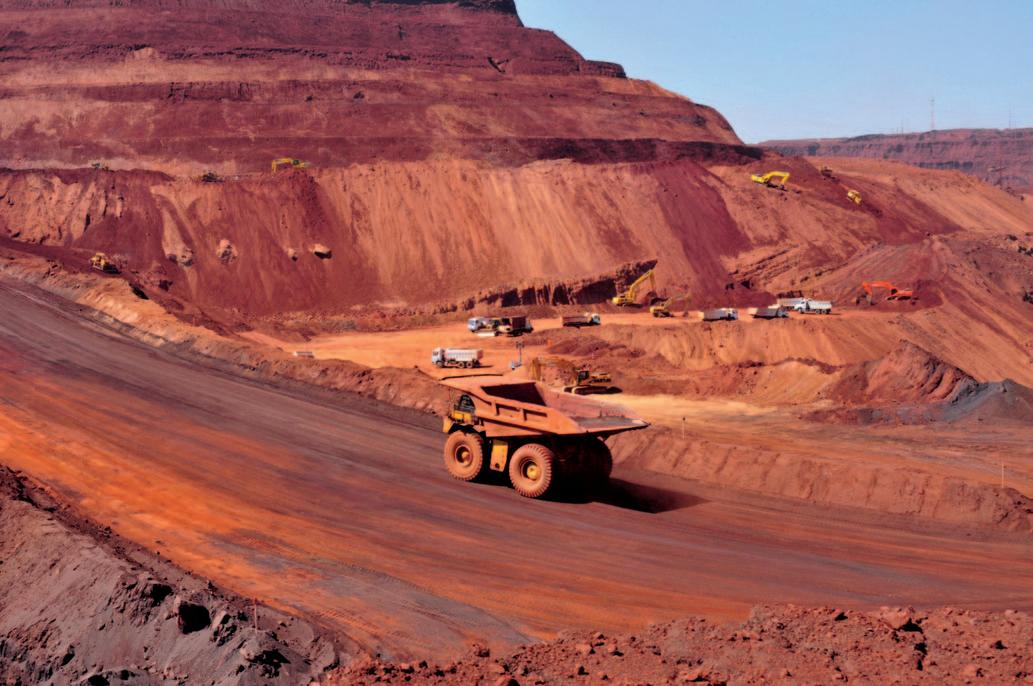
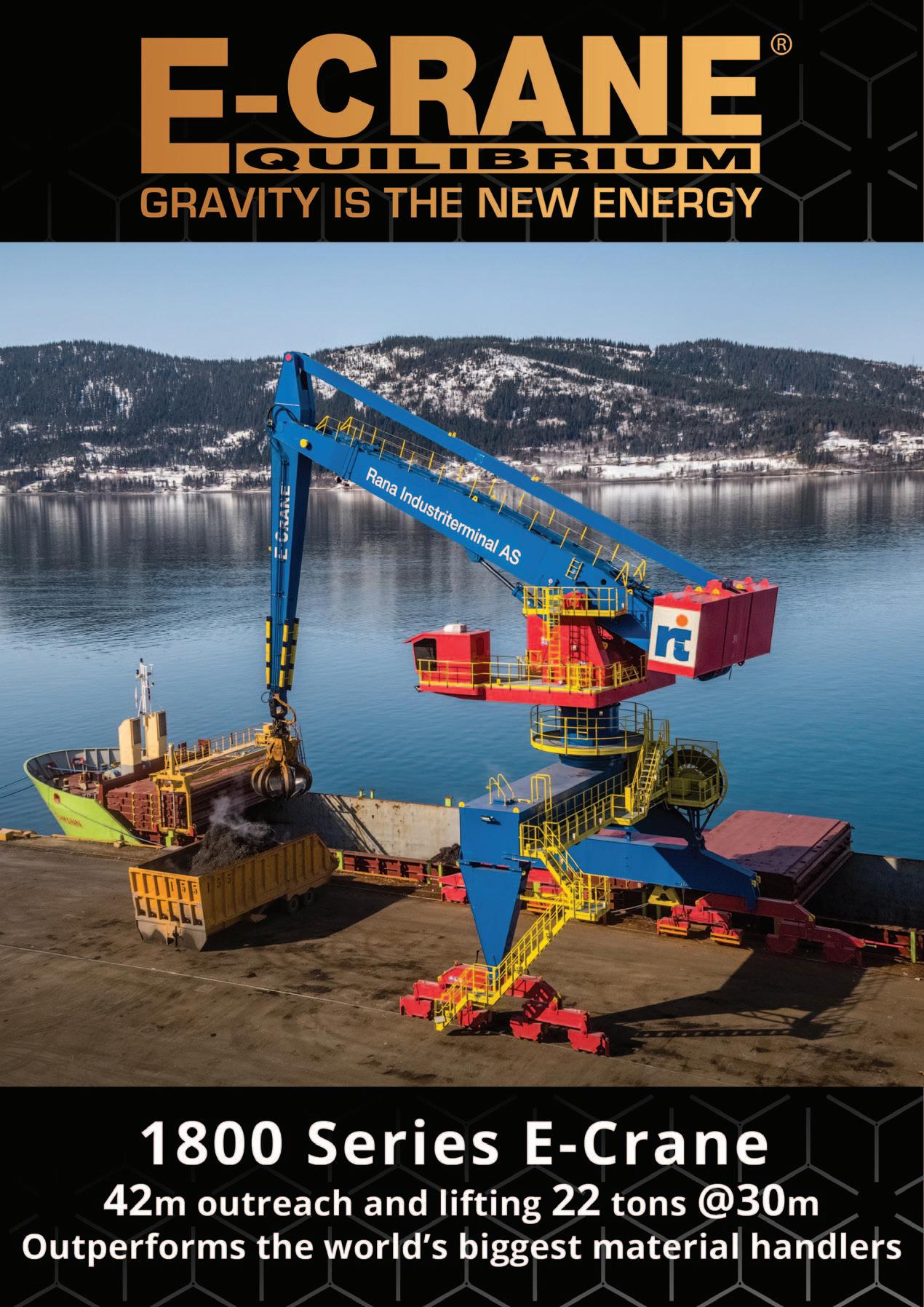
low-carbon solutions supply.” Vale is anticipating world steel production to rise to 2,090mt by 2030 and then to 2,300mt in 2040 from 1,887mt in 2022.
Vale’s mining strategy takes into account growing ESG pressure for lower-emission steelmaking requiring enhanced supply of quality ore and also for energy generation from renewable sources of a sufficiently large quantity. In fact, the Brazilian miner is investing $590m in Sol do Cerrado solar project that will generate renewable energy equalling 16% of Vale’s energy use by 2025. Any mine will suffer depletion over the years in the process of extraction.
A challenge for Vale will be to replace 400mt of depletion by 2030 and at the same time expand capacity. In the pursuit of that goal, Vale is keeping in view of the softening of futures in iron ore on demand easing in China. But at the same time richer grades of ore will command a premium with environment conscious steelmakers feeding BFs with high quality ore. No wonder then seeing the evolving demand trend, Vale has adopted a value over volume approach leading it to turn focus on stepping up output in the country’s north where it has ownership of high Fe content large deposits.
In comparison, it has lower grade mines in the south. Recently, Vale took a Press team to the world’s forested mountains of Carajas in Amazon where the world’s largest and richest open pit iron ore mine has been carved out to announce that it is on track to commission 30mt capacity. The overall plan is to have 260mt of quality ore market ready from Vale’s fast expanding operations in the north.
The S11D mine at Carajas is an important part of Vale’s development plans for the north. The government and the civic
society will closely monitor if iron ore mining in the sensitive Amazon where indigenous communities live is doing any damage to the environment. On behalf of Vale, it is claimed that several steps such as “use of conveyor belts (a substitute for fossil fuel driven trucks), mobile crushers reducing diesel use by 60% and electric excavators” have been introduced at the S11D mine to significantly cut mining impact.
Vale apart, the rest of Brazilian iron ore industry is giving top priority to safety and sustainable mining after the shocking Brumadinho disaster. In their existing operations and also while expanding capacity, this is much in evidence. The country’s Gerdau SA is both a producer of steel and iron ore. As it invests $667m in brownfield expansion of Miguel Burnier mine in Minas Gerais state to raise capacity to 5.5mt through the new platform, it is incorporating dry stacking to dispose of mining tailings constituting waste after ore extraction. The process will dispense with almost totally the use of water and therefore, a dam. At Vale’s S11D mine, dry processing system using natural humidity is saving water consumption by 93% compared to a conventional iron ore project. Over 70% of Vale ore production is dry. Dry stacking is fast becoming a common global practice. In the meantime, Miguel Burnier brownfield expansion will start yielding ore by 2025 end. The company has said production from the new platform will be routed to four steel production units also located in Minas Gerais.
AUSTRALIA SCENE
New capacity development both by way of compensating depleted ore in long operating mines and opening of new
deposits is also happening in Australia in a big way. That country of continental size has the world’s largest iron ore reserves and most of that of high quality. Last year Australia produced 880mt of ore and the world’s second largest producer Brazil made 410mt. All this apart, Australia has consistently remained by far the world’s leading exporter of ore with shipments in 2022 amounting to 896.7mt (1.5% year on year rise), making the mineral the biggest foreign exchange earner for the country at $118bn.
Australia’s Office of the Chief Economist (OCE) expects iron ore exports from Australia and Brazil to collectively grow by around 38mt or 3.1% in 2023. Research agencies say that iron ore exports will only rise slowly from there because of China restraining steel production and scrap recycling gaining traction. Ore prices will, therefore, remain under pressure. Even then Australian iron ore majors have big expansion programmes.
Take BHP Billiton. The company CEO Mike Henry said recently BHP’s Western Australian annual production capacity was initially set at 240mt, while the current actual production is in the range of 280–290mt. Production there is now sought to be raised to 300mt. Furthermore, attempts are made through a low capital-intensive growth method to further debottleneck the port and rail system, while launching autonomous delivery trucks to continue to improve productivity. In the meantime, BHP has begun to work to increase annual ore output to 330mt.
Rio Tinto, which last year raised production by just 1% to 321.6mt hopes iron ore shipments in 2023 will be in the range of 320 to 325mt with the mid-point
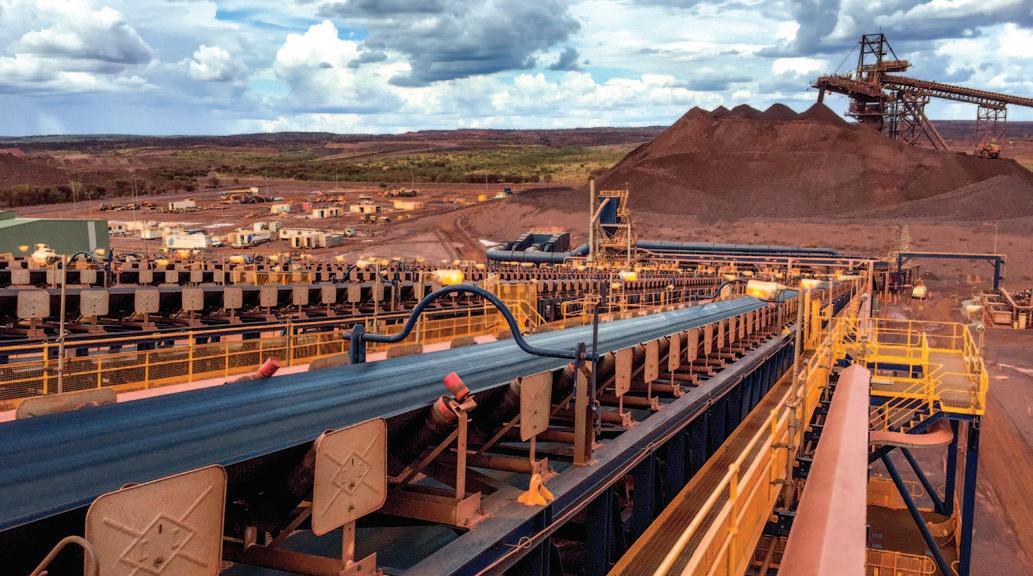
of the range indicating a year-over-year rise of 2%. Incidentally, guidance for 2023 says Pilbara iron ore unit cash cost will remain unchanged in the range of $21 to $22.5 per tonne.
In the middle of 2022, Rio Tinto started delivering ore from Gudai-Darri mine, which was brought online in the Pilbara region of Western Australia in over a decade. Built at a cost of $3.1bn or Australian $4.3bn, the mine with an annual capacity of 43mt has an expected life of over 40 years. Rio Tinto iron ore chief executive Simon Trot said the mine production would support “increased output of our flagship Pilbara Blend. It sets a new standard for Rio Tinto mine development through its deployment of technology and innovation for productivity enhancement and safety improvement.” A feasibility study to support an expansion of this new hub is in progress. The new mine is a testimony to the support of the “traditional owners, Banjima people, on whose land Gudai-Darri is situated... The company looks forward to continuing to actively partner with them in the future.”
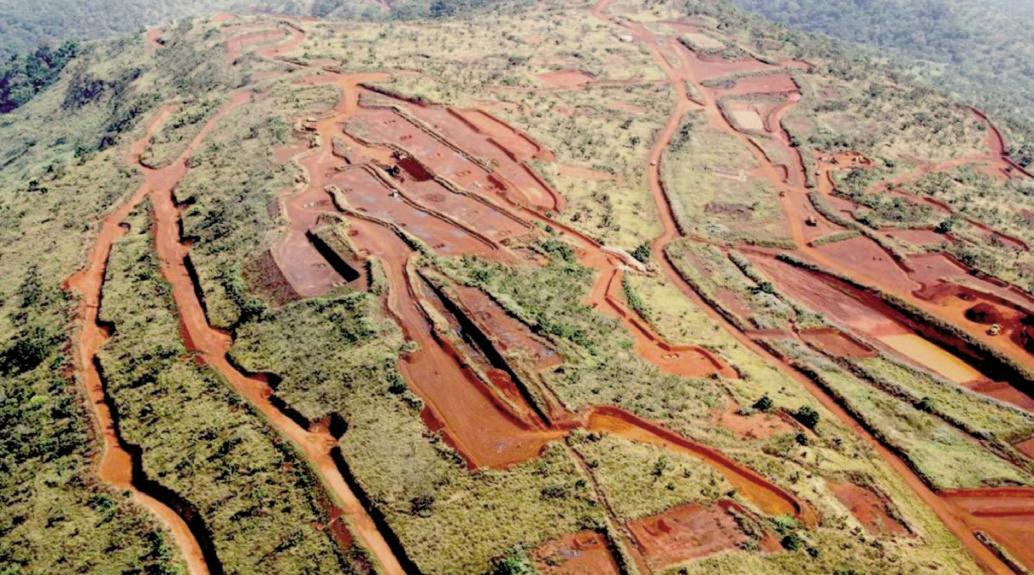
In fact, the Australian official requirement of promoters of mines first seeking the nod of locals, indigenous communities or otherwise and compensating them fairly before going ahead with mines development should become the global norm.
Many NGOs in India, where more often than not mining companies are in conflict with the locals, recommend the Australian model for the country. In September last, the world’s largest ore producer Rio made a deal with Baowu Steel of China, which is its biggest customer, to develop an iron ore mine in Western Australia that is to cost $2bn. Rio says it will invest $1.3bn to
develop the mine giving it a holding of 54%. The remaining stake will be Baowu’s pegging the investment at $700m. Rio says: “The Western Range’s annual production capacity of 25mt will help sustain production of the Pilbara Blend from its existing Paraburdoo mining hub.” Safe and environmental friendly mining are given priority in Australian industry. Moreover, miners are sensitized not to offend indigenous peoples by endangering sacred sites and many thousand year old rock shelters. Besides Australia and Brazil, capacity expansion is happening in a number of iron ore producing countries, including India where steel capacity is growing, South Africa, Canada and the US.
WORLD EYE ON GUINEA
But the country inviting most attention is West African coastal country Guinea, which has been the target for China to secure large quantities of ore in its pursuit of diversification of supply sources. This will explain why China has stuck to developing Simandou mine even though the project ran into a few controversies and operational snags over the last nine years. Simandou has the world’s single largest deposit at 4bn tonnes of high quality iron ore. The deposit is split into two projects. The north made of block 1 and 2 is owned by SMB-Winning Consortium of China Hongqiao, Winning International of Singapore, Yantai Port of China, Guinean logistics company UMS and Guinean government (10% holding). The south having blocks 3 and 4 is owned by Simfer, a joint venture between Rio Tinto (45.05%), Aluminium Corporation of China (39.95%) and Guinean government (15%). Incredibly big, the annual production capacity at Simandou is estimated at 200mt. Fitch
Solutions says in a report: “Our forecasts are currently expecting the start of mining operations at Nimba iron ore project in 2025 and at both Simandou projects in 2026, with the three projects ramping up in subsequent years. As such, we forecast Guinea’s iron ore production to boom starting 2025, with production reaching 210mt by 2030, or almost 6% of global iron ore production (compared with 0.1% currently.)”
In the meantime, the Australian government’s Office of the Chief Economist (OCE) says in a report that iron ore prices that are to average around $100 a tonne in 2023 will ease to $63 a tonne by 2028, principally because “structural changes in China” will rein in steel demand. The reasons cited by OCE are the following: (1) China has announced that its steel output will reach the peak by 2030, though this is likely to be achieved by 2028. (2) Steel demand has a correlation with population size, specially the working age population. For the first time in six decades, China had experienced a fall in population in 2022. (3) All this will likely see Chinese ore demand to contract by around 1% a year over the outlook period to 2028. During this time mines in Australia and Brazil are forecast to lift production by 3.2%. But what will happen to swing producers if ore prices dip to the level of $63 a tonne at some stage on supply chasing demand? It was seen in Australia that some now on now off most marginal miners that started production taking advantage of record pricing in the first half of 2021 to shut operation in SeptemberOctober on price falls will down shutters. Ore at $63 a tonne will make operation of even less marginal miners unviable forcing them out of business.
Cleveland Cascades to supply a vehicle loading system and two rail loading systems to Tula, Mexico
Cleveland Cascades has entered the assembly phase for the production of three Free Fall Cone systems to load petcoke which are destined for Tula, Mexico.
These consist of a FFC1000 sized system and two larger FFC2000 systems capable of handling contracted rates of 300tph (tonnes per hour) and 600tph respectively as per the clients requirements. The estimated annual material throughput is 1.6 million metric tonnes meaning the design of the systems must be robust in order to withstand the vast quantities of material delivered through them.
The extended length of the FFC1000 system which is to be utilized for open lorry loading is measured at 5.6m from the interface point to the base of the skirted outlet. This allows the skirt to form a seal with the material as it is delivered into the lorry and prevents any dust evacuation to
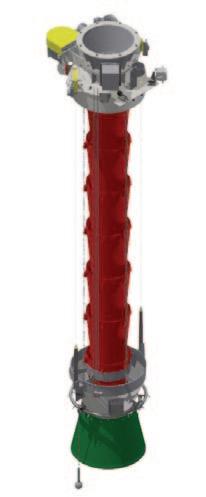
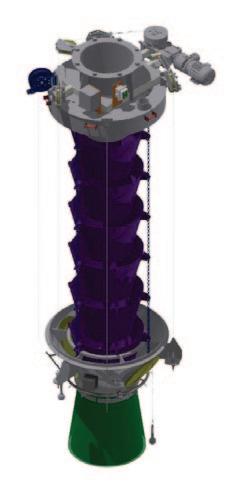
the surrounding environment. A fully retracted height of 2.5m is achievable providing enough clearance for the lorry to leave the area post loading.
The larger FFC2000 systems to be utilised for loading rail wagons have an extended length of 6.05m, again measured from the interface point to the base of the skirted outlet. Due to being physically larger, the achievable retracted height of these systems stands at 3.0m long but still provides clearance for the wagon to exit with no interference.
In order to combat the abrasive properties of the petcoke material which is stated to have particle sizing up to 100mm, each system employs the use of fabricated hardox cones which are finished with a red oxide spray. The hard wearing hardox material will ensure that these critical components of the system have a long service life before requiring replacement.
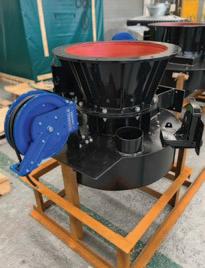
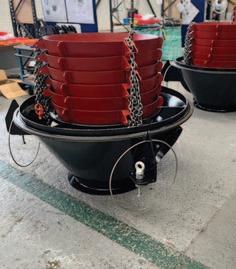
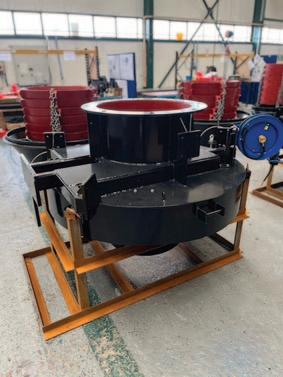
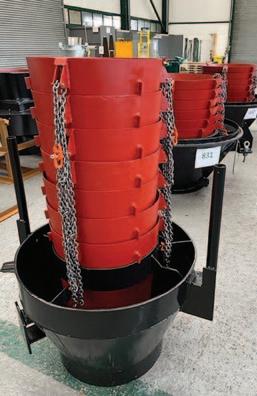
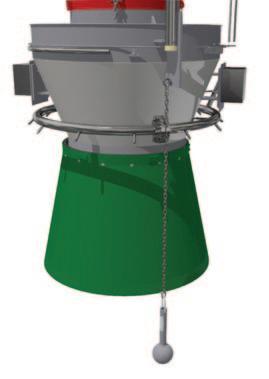
With the material to be loaded being
petcoke, a complex wiring and electrical specification had to be adhered to. The hazardous area classification for the chutes was specified as NEC Class II Div 1, Group F. With this in mind, all electrical components had to be sourced such that they are suitable for operation within the potentially explosive environment.
ABOUT CLEVELAND CASCADES
The company’s site in the North East of England covers area of 4,700m2 (50,000ft2) and includes manufacturing & assembly workshops, secure outside storage space, offices for engineering and support functions as well on site parking. The Cascade controlled flow technology system has undergone constant improvement and upgrading to maintain its position at the forefront of the loading chute industry. At the same time the product range has been widened to include Free Fall chutes, tanker loaders and vehicle loading chutes.
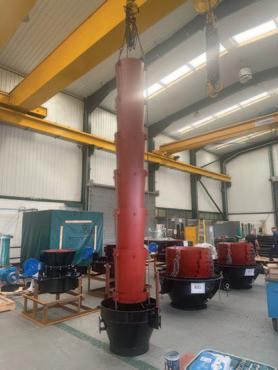
The petroleum coke (petcoke) market has been roiled by remarkable change over the last four years. The most obvious indication of this rapidly changing market has been historically high pricing volatility (see Figure 1 — US Fuel-Grade Petroleum Coke Prices). We focus on United States fuel-grade petroleum coke export prices because US fuel-grade petcoke provides approximately 75% of seaborne petcoke trade. Fuel-grade petroleum coke has lower pricing and is generally lower quality than petcoke used for carbon applications (see Coking Background for more information). Figure 1 illustrates that US West Coast (USWC) petroleum coke prices (unless specified otherwise, all references to petroleum coke prices refer to fuel-grade petcoke prices) are higher, sometime substantially higher, than US Gulf Coast (USGC) petcoke prices. USWC petroleum coke prices are higher because USWC petcoke typically has much lower sulphur content than USGC petcoke (there are exceptions) which allows it to go into higher value markets like the steel and glass industries, and export volumes are much lower (<6 vs. 24+ million tonnes),
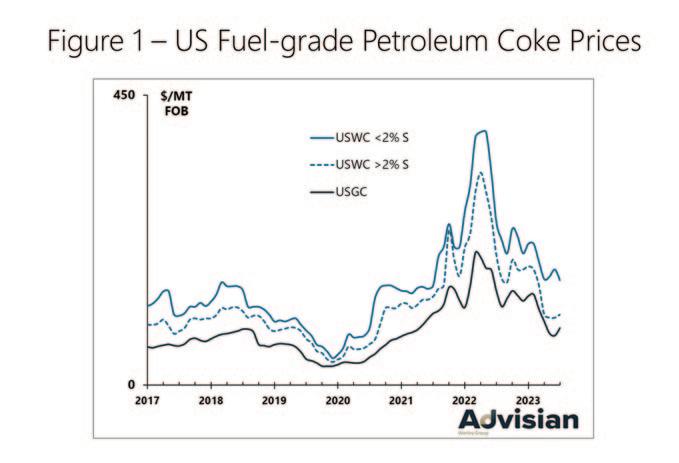
Petcoke market
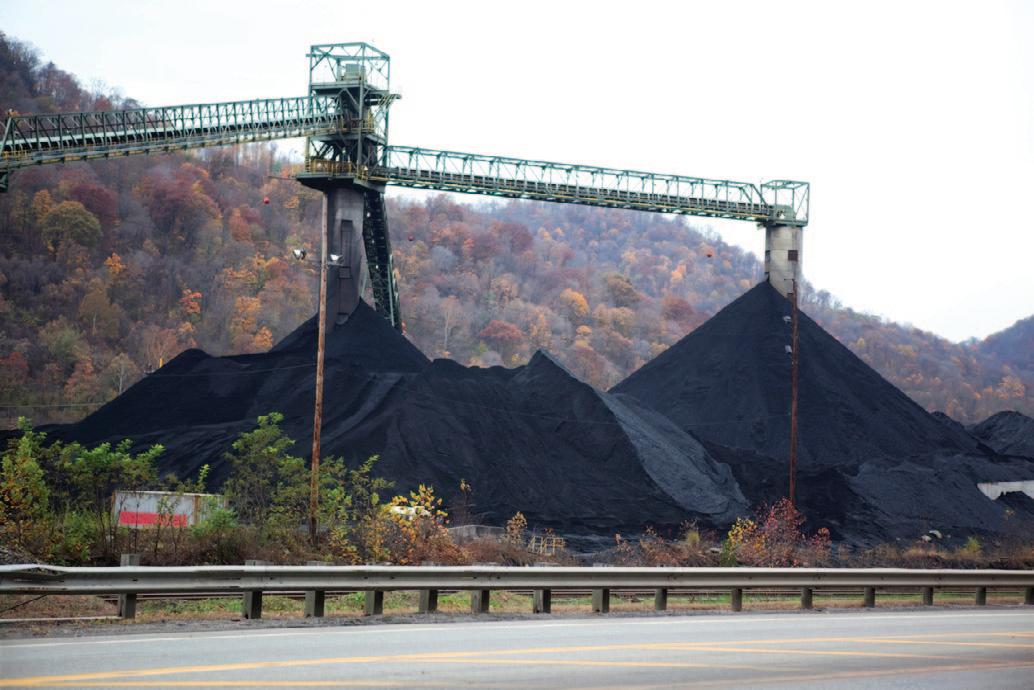
which makes it easier to limit sales to higher value markets. USWC exports are dominated by China and Japan which typically each receive about 40% of USWC exports. USGC export destinations are varied with shipments typically going to 40+ different countries in a year.
The historically high price volatility was
driven by a multitude of factors including volatile coal prices, trade policies, and major geopolitical events — the Covid-19 pandemic followed by Russia’s invasion of Ukraine. Almost simultaneously, with the implementation of Covid-19 lockdowns, there was a historic crash of oil prices in March 2020 followed by unprecedented oil
after a wild ride, heading to the new normalBen Ziesmer, Pedro Mackay & Rituraj Jha, Advisian
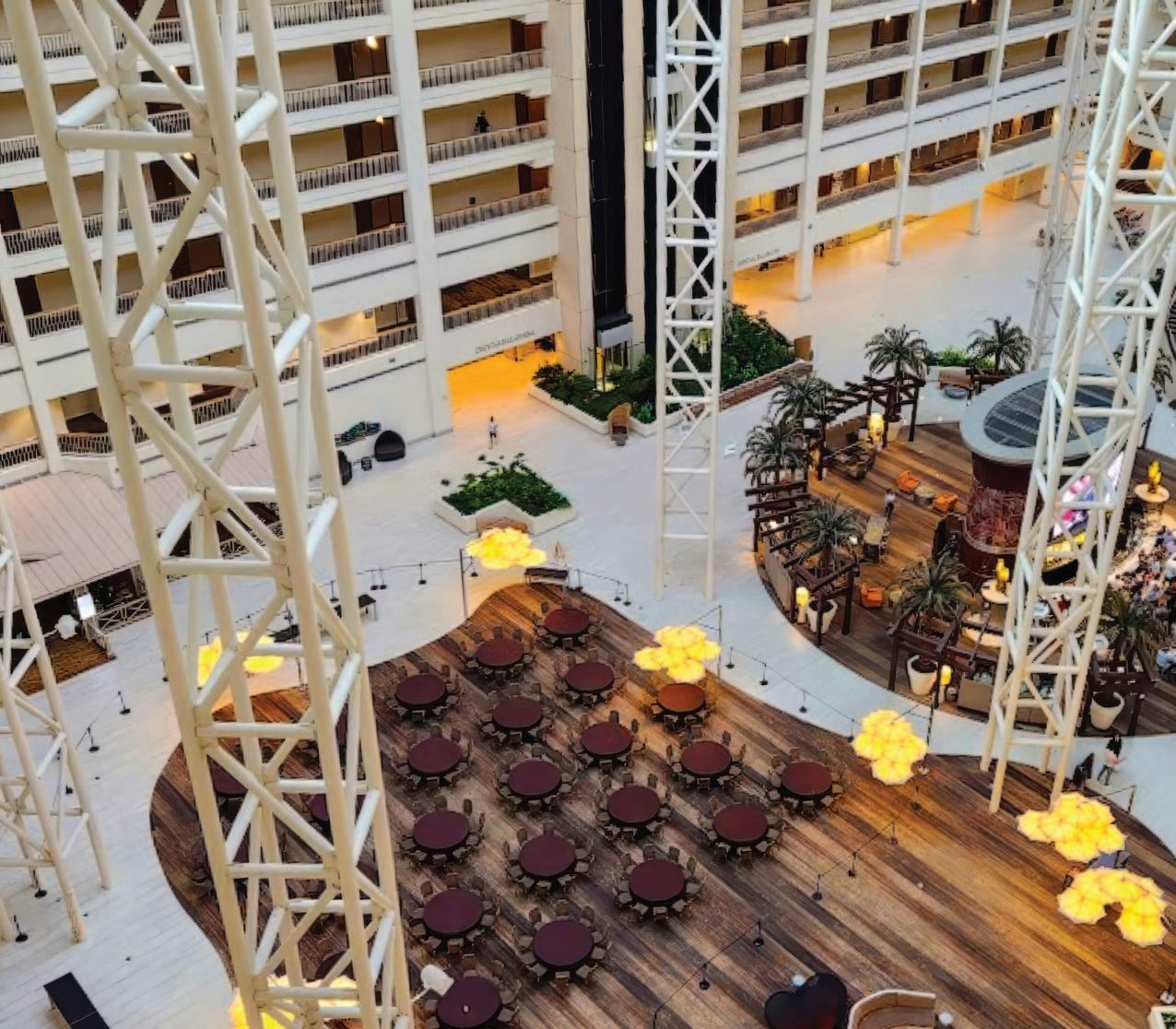
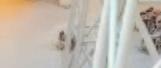
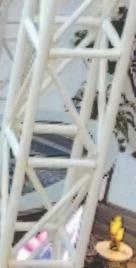
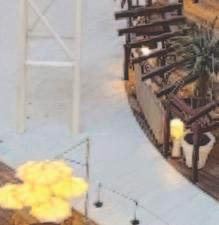
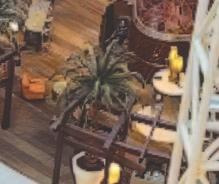
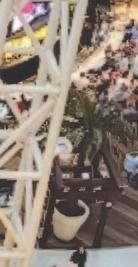



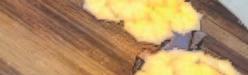
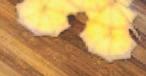

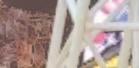
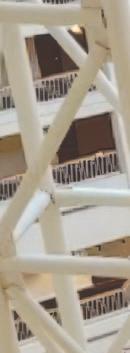


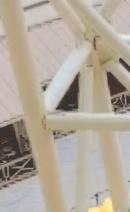
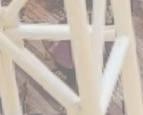
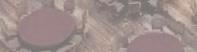
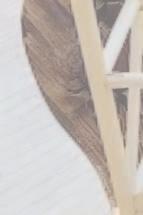



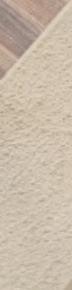
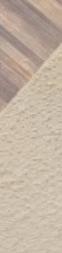

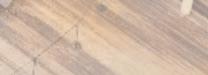
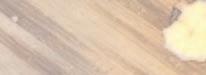
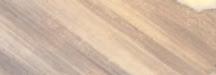

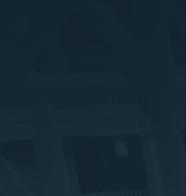
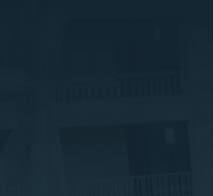
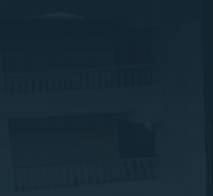
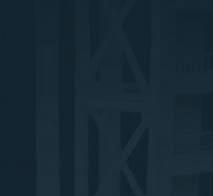
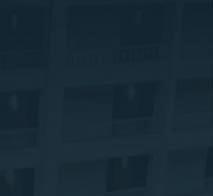
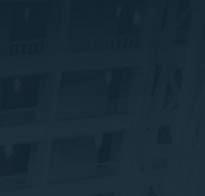
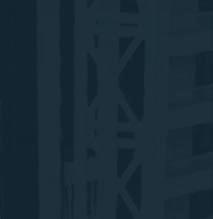
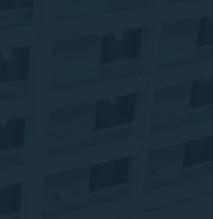


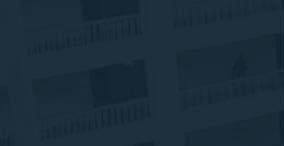

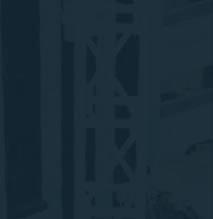
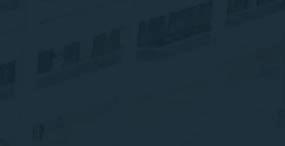

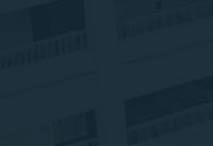
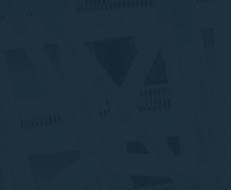
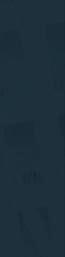
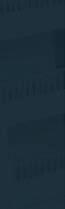
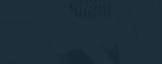

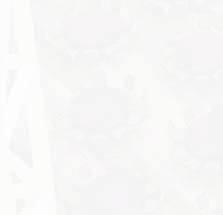
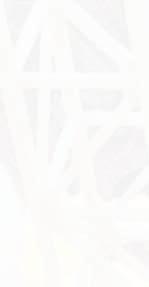




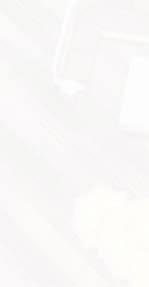
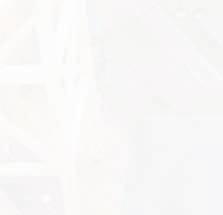
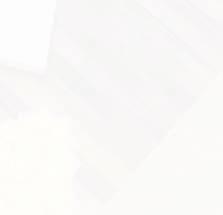

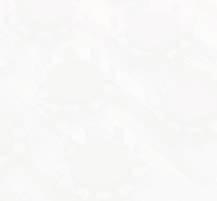


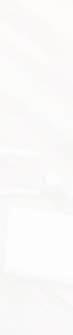
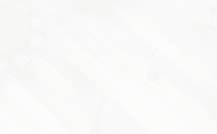
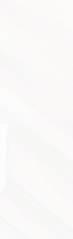
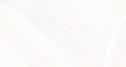

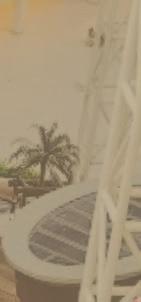

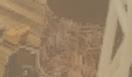


production cuts by OPEC+1. Prices have been generally declining since May 2022 and have recently decreased close to longer-term historical levels, indicating that the petroleum coke market is moving beyond the disruptions of the past and heading into a ‘new normal’. Before delving into the ‘new normal’, let us review a brief background on petroleum coke.
COKING BACKGROUND
Petroleum coke is produced as a byproduct in many oil refineries. Crude oil is first processed in an atmospheric distillation unit, followed by a vacuum distillation unit. The heavy residuum exiting the bottom of the vacuum tower (i.e., vacuum tower bottoms, or VTB) can be used to make asphalt, residual fuel oil (RFO)2, or used as feedstock for a coker (see Figure 2 — Simplified Coking Refinery Flow Diagram) or other bottoms upgrading technology.
For decades, the refining industry has faced the problem that demand growth for transportation fuels (i.e., gasoline, diesel, jet fuel) has been, and continues to be, much greater than for RFO. To put it another way, people are buying cars and trucks and flying in airplanes, but no one is building RFO fuelled power plants or industrial facilities. In response to this problem, the refining industry developed various technologies to upgrade VTBs to produce more valuable light products and eliminate the need to produce RFO.
Cokers have been and continue to be the dominant bottoms upgrading technology. They allow refiners to reduce production of RFO per barrel of crude oil processed and bridge the gap between growth in demand for light products and RFO demand growth. To summarize, the primary purpose of a coker is to reduce the production of residual fuel oil by converting heavy VTBs into high value transportation fuels (gasoline, diesel, jet fuel, etc.) with petroleum coke produced as a by-product of the coking process.
It is also important to recognize that the percentage of VTBs produced as a result of refining crude oil increases dramatically as the crude oil processed in the refinery gets heavier (i.e., lower specific gravity). For example, about 10% (by weight) of light Arabian crude oil becomes vacuum tower bottoms, whereas almost 40% of very heavy Mexican Maya or Alberta crude oils become vacuum tower bottoms. Consequently, the percentage of crude oil that converts into petroleum coke increases dramatically, and refineries that are designed to process heavy crude oils
are much more likely to have coking capacity (or other VTB upgrading technology) than refineries designed to refine lighter crude oil.
Traditionally, cokers are installed in oil refineries to convert VTB and other heavy residual oils into higher-value light transportation products (e.g., gasoline, jet fuel, diesel fuel). Until recently, a coker almost invariably increased refinery profitability because the yield of high-value transportation fuels is maximized and the production of low-value RFO is minimized3 While the coking process has been in use since the 1930s, petroleum coke production has seen its largest growth between 1995 and 2018 (production: 1995= ~30 million tonnes, 2018 =~140 million tonnes) principally because light transportation petroleum product demand grew faster than RFO demand worldwide, and the overall global crude slate got heavier. Consequently, petroleum coke production grew much faster than crude oil demand (1995–2018 CAGR = 6.6% for petcoke vs. 1.6% for crude oil).
Refineries run a blend of different crude oils (known as the crude slate), and choices of crude oils which are in the crude slate significantly impacts the quantity and quality of petroleum coke that is produced. The selection of crude slate is driven by a complex series of factors including the capacities and capabilities of the various processing units within the refinery, the expected operating state of various processing units, crude oil pricing and availability of different qualities of crude oil, and demand for various refined products.
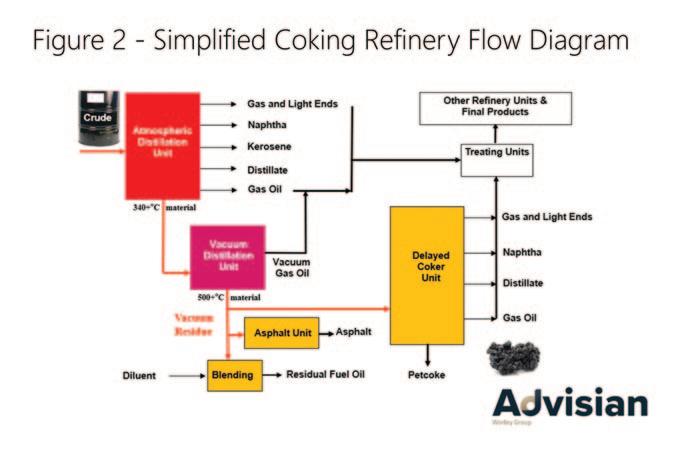
PETROLEUM COKE MARKETS
Petroleum coke is unusual because it is used not only as a heat source (i.e., fuel) but also as a carbon source in metal
production and chemical processes. Petroleum coke that is used as a carbon source requires better quality (e.g., low sulphur and metals content) and commands a higher value, driven by different factors than fuel-grade petcoke prices.
Green4 petcoke is usually upgraded by calcination when it is used as a carbon source. Calcination is a process that uses heat to remove moisture and volatile matter from petcoke, improves critical physical properties, and converts green petcoke into an electrically conductive form of carbon. Green petcoke that has been calcined is referred to as calcined petroleum coke (CPC). The largest market for CPC is in the production of carbon anodes for aluminium smelting. Other uses for CPC are in the production of carbon electrodes for electric arc furnaces, titanium dioxide (TiO2) production, as a recarburizer (i.e., carbon raiser) in the iron
1. OPEC+ is a combination of the 13 members of OPEC (Organization of Petroleum Exporting Countries) and a Russian led coalition of 9 additional petroleum exporting countries.
2. Typically, about 30% high value diluent such as light cycle oil needs to be added to meet RFO viscosity and density specifications.
3.Since the early 1990s, cokers have also been used in upgraders that produce various grades of synthetic crude oil (SCO) from bitumen or ultraheavy crude oils. This type of upgrader exists in Venezuela where ultra-heavy Orinoco Belt crude oil is upgraded and is exported as lighter crude oils, and in Canada where upgraders are used to produce SCO from the bitumen derived from Alberta oil sands. Upgrading economics are driven by crude oil economics, not refining and coking economics.
4. Technically, all petcoke that has not been calcined is green petcoke (GPC). However, within the petcoke industry, the term GPC is usually only used for petcoke that is used as calciner feedstock. Unless otherwise noted, discussion of petcoke or petroleum coke will be referring to green (i.e. not calcined) petroleum coke.
and steel industry, and, very recently, as a source of synthetic graphite in lithium-ion (Li-ion) battery production. A little over 30% of petroleum coke that is produced is sold into these higher value-added markets for higher quality petcoke; the remaining production is used as a fuel source. The carbon source market share has been growing recently as demand in these markets has been growing faster than overall petroleum coke production.
Fuel-grade petroleum coke is used in a variety of industries — primarily as a substitute for coal, but sometimes for fuel oil. Petroleum coke has higher calorific value (i.e., kcal/kg) and much lower ash content than coal. However, it is more difficult to burn, has higher sulphur content, and is more difficult to pulverize5 than coal because most fuel-grade petcokes are harder than coal, so it typically sells at a discount to coal. The cement industry is the largest consumer of fuel-grade petroleum coke because cement kilns are particularly well suited to burn petcoke, and cement kilns inherently capture approximately 90% of the sulphur oxides (SOX) emissions resulting from burning petcoke. The next largest demand segment for fuel-grade petroleum coke is the ‘other industry’ category, which includes lime6, brick, calcium carbide, and glass production, plus gasification of petcoke to produce chemicals (e.g., ammonia, urea ammonium nitrate, etc.). The remaining categories in declining market size are power generation, long-term storage, and iron & steel
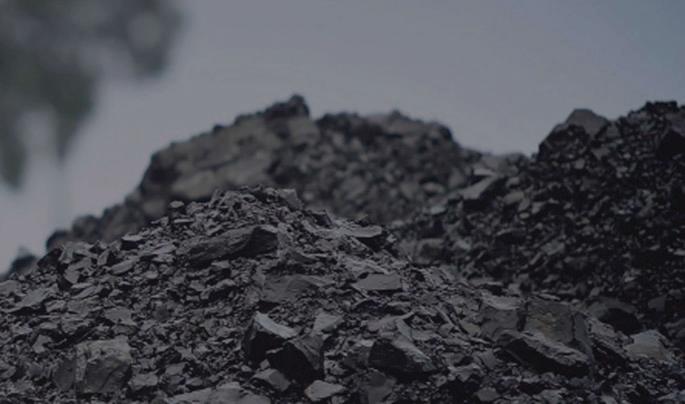
production. The ‘long-term storage’ category refers to petroleum coke produced as a by-product of upgrading bitumen (primarily Western Canadian oil sands) where petcoke is placed underground as part of the reclamation process associated with open cast (open pit) mining of bitumen.
PETROLEUM COKE PRODUCTION
Global petroleum coke production dropped by almost 10% in 2020 due to governments’ policies implemented in response to the Covid-19 pandemic and the indirect impact of sharp OPEC+ production cuts. Production partially rebounded in 2021. Production growth accelerated in 2022, and production slightly exceeded pre-pandemic levels (see Figure 3 – Petroleum Coke Production). Production growth is expected to slow in 2023, with OPEC+ production cuts being a key factor.
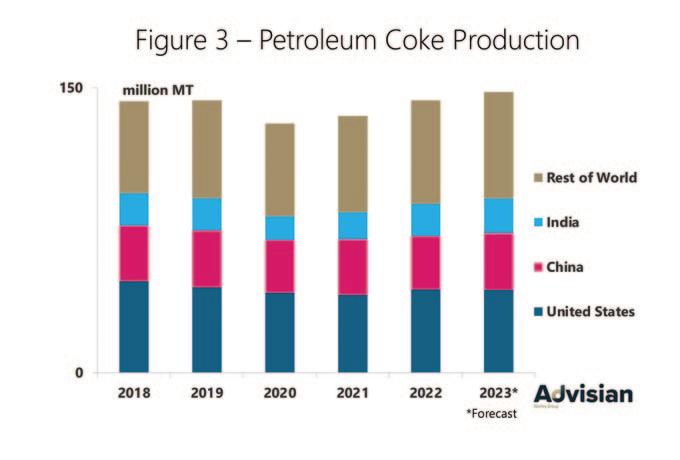
OPEC+ accounts for over 40% of the global crude oil production. After the price war between Saudi Arabia and Russia, which led to the oil price crash in March
2020, OPEC+ members decided to impose a historic production cut, equivalent to 10% of global oil demand, which, after succeeding extensions, came to end in August 2022. However, in April 2023
OPEC+ members decided to implement new cuts amounting to 3.66 million bbl/day and in June, Saudi Arabia announced an extra voluntary cut of one million bbl/day for July. Most recently, Saudi Arabia decided to extend its voluntary cut of one million bbl/day for the third consecutive month (i.e., through September 2023) and, in parallel, Russia announced it will be reducing 0.5 million bbl/day of its oil exports in August and by 0.3 million bbl/day in September. These extra cuts are over and above the original OPEC+ cuts decided in April. These production cuts are equivalent to ~6% of the global oil demand.
As we mentioned previously, OPEC producers tend to preferentially cut heavy oil production when they make production cuts in order to maximize revenue as heavy crude oil sells at discounts to light crude oil. This preferential cutting of heavy crude oil causes a relative shortage of heavy crude oil, and the discount for heavy crude oil tends to shrink. The shrinking discount for heavy crude oil hurts the profitability of coking and tends to induce coking refineries to migrate to lighter crude slates. Petroleum coke production reduces with lighter crude slates. Generally, but not always, lighter crude oils have lower sulphur content, which reduces petroleum coke sulphur content. We have begun to see the impact of the OPEC+ production cuts as some coking refineries are producing somewhat smaller volumes of petroleum coke with lower sulphur content. However, petroleum coke production at other refineries has not
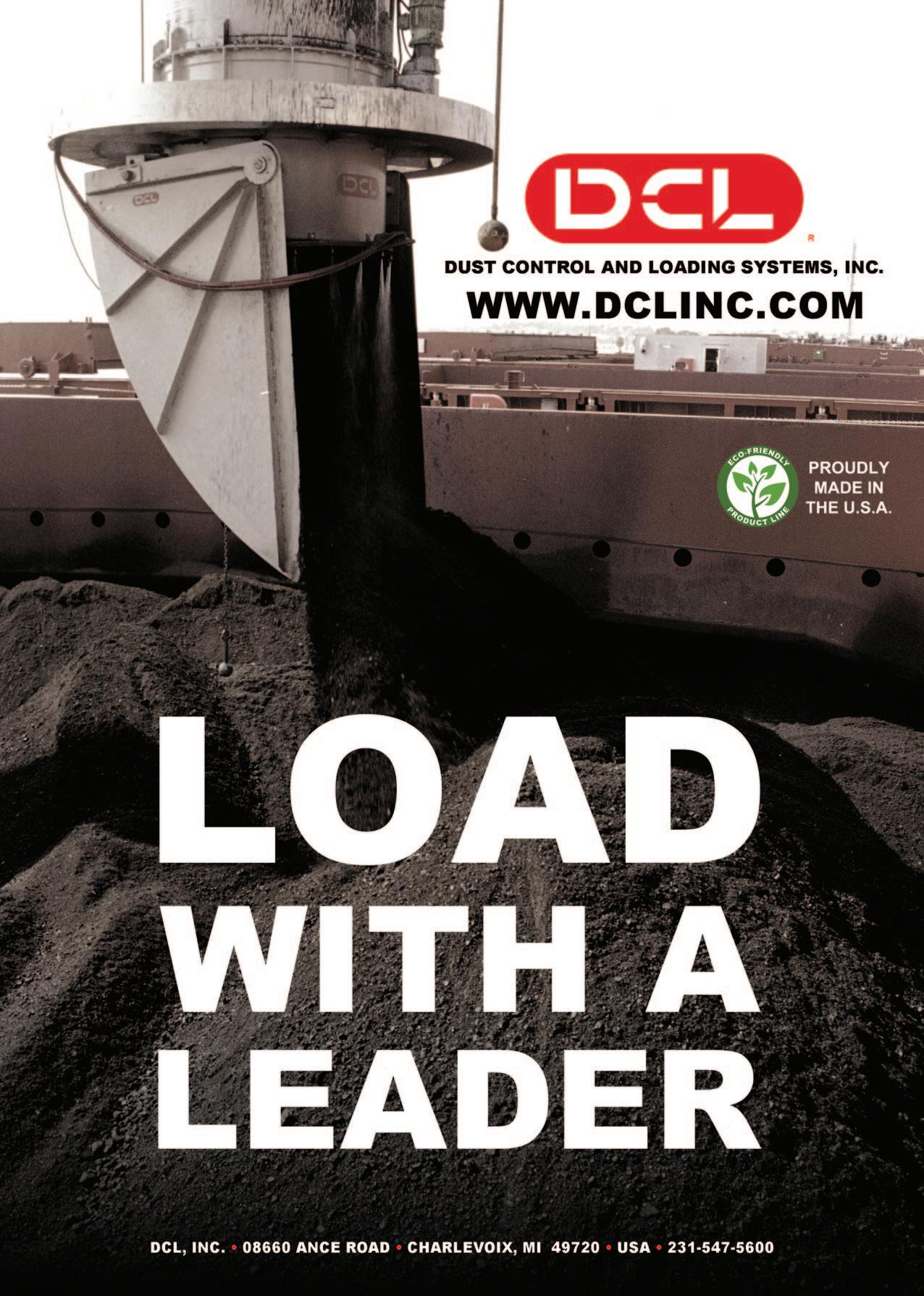
materially changed.
COAL MARKET PRICE RATIONALIZATION
The coal market is important to the petroleum coke market because fuel-grade petcoke typically is a substitute for thermal (steam) coal. The seaborne thermal coal market is approximately 25 times larger than the seaborne fuel-grade petroleum coke market, so the petcoke market cannot meaningfully impact seaborne thermal coal prices. On the other hand, thermal coal prices act as cap on petroleum coke prices as buyers will switch from petcoke to coal if petcoke is not economically attractive vis-à-vis coal ($/MMBtu delivered basis).
Prices for traditional ‘marker’ thermal coal prices (e.g., Northwest API2, South African RB1/AP14, Australian Newcastle) soared to historical highs after the Ukraine war began. The primary driver appears to have been the anticipation of a supply shortage due to sanctions on Russian coal imports into the EU because Russia accounted for 43% of EU coal imports in 2021.
Like the ban on importing Russian oil, the ban on importing Russian coal has had more impact on where Russian coal is exported than on the volume of Russian coal being exported. Russian coal was exported at heavily discounted prices to many countries including China, India, and Turkey. However, as time proceeded, the coal market recognized its fears were exaggerated, and coal prices, especially for ‘marker’ coals, decreased sharply while Russian coal prices were stable, causing the discounts for Russian coal to shrink (see Figure 3– Thermal Coal & Petcoke Prices).
IMPACT ON PETCOKE MARKET
USGC petroleum coke appeared to be very attractive compared to traditional ‘marker’ thermal (steam) coal prices for much of 2022 and into 2023. However, in key markets such as Turkey and India, USGC petroleum coke also had to compete against heavily discounted Russian coal (see Figure 3 — Thermal Coal & Petcoke Prices). It is this competition that constrained upward movement of USGC petroleum coke. As ‘marker’ and other coal prices have decreased to close to historical levels, the discounts for Russian coal have shrunk, and petroleum coke is now competing against a variety of coals.

SHIFTING PETROLEUM COKE TRADE FLOWS
Venezuela re-emerged in 2021 as an exporter of petroleum coke as petcoke from the huge (estimated at 18+ million
tonnes) inventory located near the Port of Jose began to be loaded onto vessels. Less than 0.3 million tonnes were exported in 2021, but export volume shot up to almost 3.2 million tonnes in 2022. Exports during the first four months of 2023 were running at the equivalent annual rate of about six million tonnes/year. Then contract disputes between Maroil, the primary exporter, and Petróleos de Venezuela, SA (PdVSA) caused export volumes to be sharply lower during May and June. Since Venezuela resumed petroleum coke exports, China has been the primary destination (70%) followed by India (15%) and Turkey (11%).
Historically, three key export markets for US petroleum coke have been China, India, and Turkey. Over the last three years these trade flows have shifted.
China is on track to import record petroleum coke volumes this year, continuing the trend as petcoke imports increased from 12.5 million tonnes in 2021 to 14.8 million tonnes in 2022. China’s petroleum coke imports surged during the first four months of 2023, far above volumes seen in either 2021 or 2022 (see Figure 4 — China Green Petroleum Coke Imports). During this same period, China’s domestic petroleum coke production was also up (+10%) versus 2022.
The combination of surging import volumes, increased domestic production, and somewhat lackluster demand caused petroleum coke inventories to surge to 6.5+ million tonnes. Import volumes reduced to more typical levels in May and June. Nonetheless, China’s petroleum coke imports for the first half of 2023 (1H23) were 40% higher than 1H22. Inventory levels have decreased, reaching a little over five million tonnes in July but are still high by historical standards.
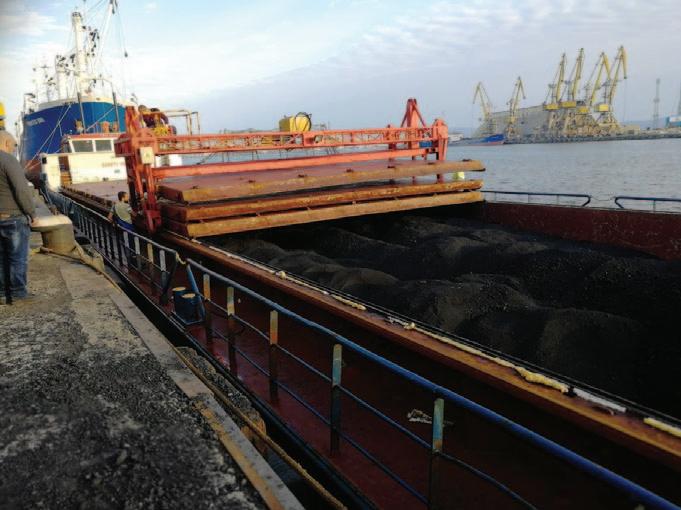
So far in 2023 (1H23), the top three petroleum coke suppliers to China are the US, Venezuela, and Russia, having a market share of 36%, 20%, and 11%, respectively. These three countries have provided ~70% of China’s petroleum coke imports this year. In 2022 Venezuela emerged as the second largest petroleum coke exporter to China, replacing Saudi Arabia. In 2021, Saudi Arabia exported around two million tonnes of petroleum coke to China, which was ~16% of China’s total petcoke imports. In 2022, Saudi Arabian petroleum coke volumes to China dropped to ~0.9 million tonnes, and so far, this year (1H23), they have exported a little over 0.5 million tonnes of petcoke to China. Conversely, Venezuela’s petroleum coke exports to China were negligible through 2021, then came up to ~2 million tonnes in 2022, and so far in 2023 (1H23), they have exported almost two million tonnes of petcoke to China. This year, import volumes from
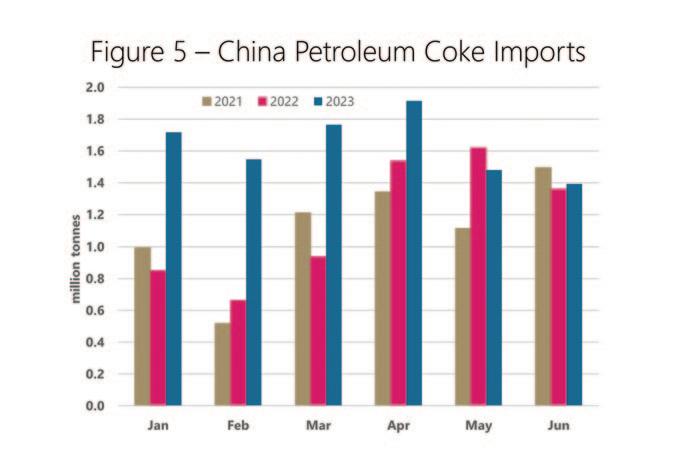
Russia are up a stunning 75% compared to the same period in 2022 as sanctions on Russia have pushed petcoke it formerly exported to Europe to different markets.
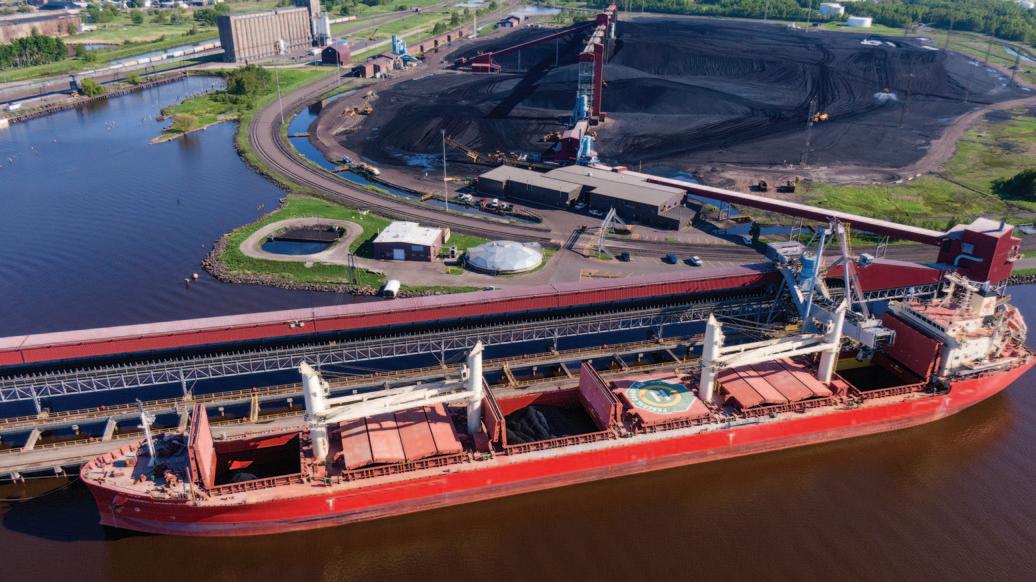
India’s petroleum coke imports through May 2023 are up 38% versus 2022. Petroleum coke imports during the first quarter of 2023 (1Q23) are the highest since 2016, when India’s petcoke imports reached an all-time high of 13.7 million tonnes. Petroleum coke imports in 2022 more than doubled to ~9.0 million tonnes, from ~4.3 million tonnes in 2021, which was significantly down due to pandemicrelated slowdowns.
Petroleum coke imports into India are regulated and changes in regulations have occurred recently. On June 2, 2023 the Indian Government approved the importation of needle petroleum coke to be used as feedstock in the production of synthetic graphite for Li-ion battery anodes and not for any other purposes, (e.g., for
fuel or for trade). Per the document, the sulphur content in the petroleum needle coke should be less than 0.8% and shall be monitored by the State Pollution Control Boards (SPCBs). Earlier, India’s Directorate General of Foreign Trade (DGFT) allowed integrated steel plants to import low sulphur petroleum coke only for blending with coking coal in recovery type coke ovens equipped with a desulphurization unit but not for any other purpose including as a fuel or for trade. So now, imports of petroleum coke into India are unlimited (i.e., having no quotas) for cement, lime kilns, calcium carbide, gasification, graphite electrode, and Li-ion battery industries. For integrated steel plants, there is no such quota, but petroleum coke usage is limited to 10% of the feedstock to coke ovens and to petcoke with sulphur content not exceeding 3%. The aluminum industry as a whole, is allowed to import a maximum 0.5 million tonnes of calcined petroleum coke (CPC) in one financial year and calciners a maximum of 1.4 million tonnes of GPC.
Turkey’s petroleum coke imports during 1H23 were down 48% Y/Y, to less than one million tonnes. After the earthquake that hit southern and central Turkey in early February 2023, the market was expecting a higher flow of petroleum coke imports by the Turkish cement industry, but so far, that has not materialized. However, there is another angle to this story. Turkey’s thermal coal imports during 1H23 are 18% higher Y/Y, reaching 14.8 million tonnes, and over 80% (~12.2 million tonnes) of which came from Russia. Russian thermal coal imports into Turkey gained astronomically by 140% Y/Y during 1H23 and were 6% higher vs. the same timeframe in 2019 (i.e., pre-pandemic levels). Historically, Russian
thermal coal share in Turkey’s total thermal coal imports were around 40–45%, but since the European Union’s (EU) ban on Russian solid fuels came into effect, it jumped significantly.
SUMMARY
The petroleum coke market is returning close to historical pricing levels, which is a strong indication that the petcoke market is moving beyond the disruptions of the last several years. Production will grow in 2023 but at a slower rate than in 2021 and 2022 when production was recovering from sharply reduced levels in 2020 as a consequence of government lockdowns and other policies implemented in response to the Covid-19 pandemic. In the first half of 2023, petroleum coke imports into China have been exceptionally high and petcoke imports into Turkey have been low. It remains to be seen if trade patterns return closer to historical norms as 2023 proceeds.
LONGER TERM OUTLOOK – PETROLEUM COKE MEGATRENDS
Developments in specific industries as well as the evolution of the energy transition are expected to significantly shape the petroleum coke industry going forward. We refer to these developments as petcoke megatrends and are summarized as follows:
Pace of the energy transition from oil- v based transportation fuels to renewable fuels and electric vehicles. Repurposing of petroleum refining v assets to renewable fuel.
Permanent shut down of marginal v refineries.
Increased demand for synthetic v graphite produced from petroleum coke for battery production to support increased use of electric vehicles and renewable power generation.
Growth in aluminium production v (primary and recycled).
Inert anode (also known as ‘carbon v free’) aluminium smelting technology (eliminates current need for calcined petroleum coke in consumable anodes)
Each of these trends will have a different impact on petcoke production or consumption and the net effect will determine the future course of petroleum coke. These megatrends will be discussed in more detail at our upcoming 22nd Annual Petcoke Conference.
About the authors
Ben Ziesmer (Senior Adviser)
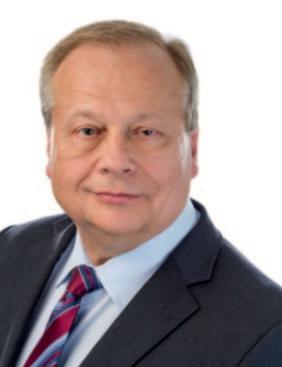
Ben is a widely recognized authority in global petroleum coke consulting. He successfully led Advisian’s Fuel Grade Petcoke practice for many years and now acts as a senior advisor to the team. Ben continues to be a key contributor to Advisian's Pace Petroleum Coke Quarterly, as well as providing support to single client consulting projects, the annual Advisian Petcoke Conference and other Advisian petcoke-related publications.
Pedro Mackay (Principal Consultant)
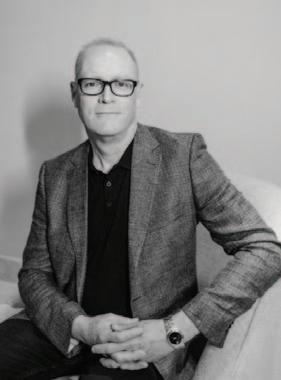
Pedro has over 25 years of experience working in various energy-related fields such as oil exploration, solid fuel purchasing and trading including petroleum coke and coal, ocean freight chartering, consulting in the petroleum coke industry, and raw materials purchasing in the coke calcining industry. Through his career, Pedro has held responsibilities focused on purchasing and supply chain aspects related to solid fuels for cement plants and raw materials for calciners, solid fuel trading, ocean shipping, and consulting. He holds a bachelor’s degree in Mechanical Engineering from the University of Texas at Austin and a Master’s in International Management from Thunderbird.
Rituraj Jha (Senior Consultant)
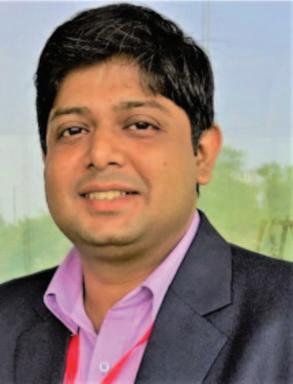
Rituraj is Mumbai-based senior consultant for Houston Market Services team (Advisian) and is a contributing author for Advisian’s Pace Petroleum Coke Quarterly© (PCQ) and Calcined Petroleum Coke Report© (CPC). He is also involved in numerous petroleum coke market studies and is team’s regional expert on Indian petroleum coke market and refining segment. Background-wise, Rituraj is a chemical engineer from one of India’s top engineering colleges, with a specialization in petroleum refining.
Advisian (formerly Jacobs Consultancy, Inc. and previously The Pace Consultants, Inc) has published the Pace Petroleum Coke Quarterly© since 1983. The report has been published monthly since January 1985 and is considered the global authoritative source of petcoke market information.
Voyager portal founders urge shipowners to take proactive stance to cut demurrage costs and risks
Voyager, the operations and demurrage management platform for bulk commodity shipping, is urging shipping companies to take a proactive stance and adopt a number of Best Practices in order to reduce the costs and risks of demurrage.
A dramatic surge in port congestion and associated supply chain disruptions have led to longer waiting times and higher demurrage costs, said Voyager co-founder and CEO Matthew Costello. “This issue is particularly severe in the bulk shipping sector, where demurrage costs can exceed 20% of the total freight cost for a voyage,” he said.
“However, demurrage doesn’t have to be a substantial burden on a company’s resources. By implementing three key Best Practices, companies can significantly reduce the cost of demurrage and streamline their operations.”
Voyager says companies should estimate and analyse demurrage in real-time, automate their Statement of Fact (SoF) data processing and logically analyse their charter parties.
“These changes will give your company the necessary tools to stay ahead, making informed, data-driven decisions that result in savings and greater efficiency,” said Costello.
According to Voyager, many businesses make the mistake of calculating laytime and estimating demurrage claims only after they receive a claim from the shipowner — leaving no room for adjustment. Instead, companies should take a proactive stance; by estimating and analysing demurrage immediately after the first load port, they can gain a real-time assessment of their demurrage risk at every stage.
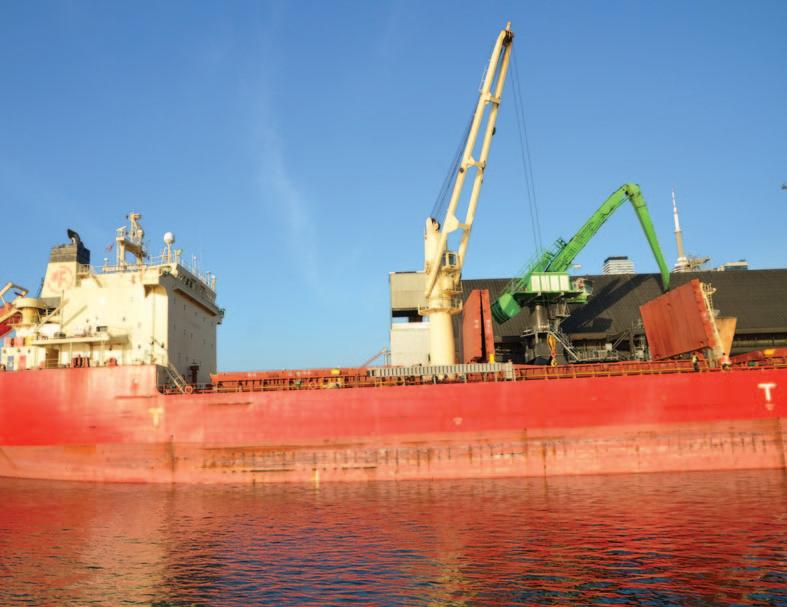
By taking into account historical factors such as waiting times, congestion and lineups, operators can gain a realistic estimate of the demurrage risk for the entire voyage; these costs can be allocated to profit-and loss-statements accurately and any claim can be anticipated in advance. This also offers dynamic opportunities for risk mitigation by co-ordinating with terminals and other vessels to expedite
discharge and avoid unnecessary delays.
Secondly, Voyager recommends that companies digitize all their SoF events data, to provide granular insight throughout the loading and discharging process — invaluable in assessing the efficiency of the terminal, the berth and the discharge itself. By automating the processing of this data, companies can streamline their demurrage calculations and gain real-time insights, informing decisions related to seasonality, congestion and efficiency.
Finally, Voyage urges companies to connect charter party agreements to demurrage logic. This involves more than just transferring data fields into a database — logic should be assigned contracts and fields, so that it can be understood how specific clauses in a contract are impacting demurrage claims. For example, there may be particular clauses that incur more cost at a certain berth or port. Analysis of the charter party enables dynamic optimization of contracts across the company, which can highlight areas of potential savings based on data-driven decisions.
Voyager Portal views demurrage as an opportunity for businesses to alleviate the impact of port congestion, improve tighten up contract weaknesses and drive overall business improvement, said Voyager cofounder and COO Bret Smart. “Demurrage costs due to inefficiencies
eventually get passed on to the customers, creating a situation where no one wins. Proactive management and intelligent data utilization are the keys to unlocking significant business improvement,” he said.
“Ultimately, automating document processing and laytime calculations can free up valuable time for demurrage teams, with up to 50% of time savings. The time freed up can be used by analysts to go back to contracts and review clauses to identify other savings opportunities.”
Voyager’s calculator automatically recognizes various events in both digital and handwritten SoFs, using contract clauses to apply deductions whenever it needs to. This unlocks both time and potential for demurrage managers and analysts, ensuring they aren’t missing critical, cash-saving deductions.
ABOUT VOYAGER
Voyager Portal is a demurrage & operations platform that helps bulk charterers improve efficiency while reducing cost, risk, and complexity. With Voyager, maritime leaders and operators can collaboratively manage their shipping process in a unified environment, automating manual tasks while leveraging real-time insights. Voyager is backed by leading venture capital funds and counts several Fortune 50 companies as customers.
NYK Bulkship (Atlantic) N.V. (Head Office: Antwerp, Belgium; NBAtlantic), an NYK Group company, will introduce a windassisted ship-propulsion unit on a bulk carrier engaged in a longterm charter contract with Cargill International S.A. (Switzerland), a subsidiary of Cargill, Incorporated (USA). This will be the first time for a unit of this type to be installed on an NYK Group vessel.
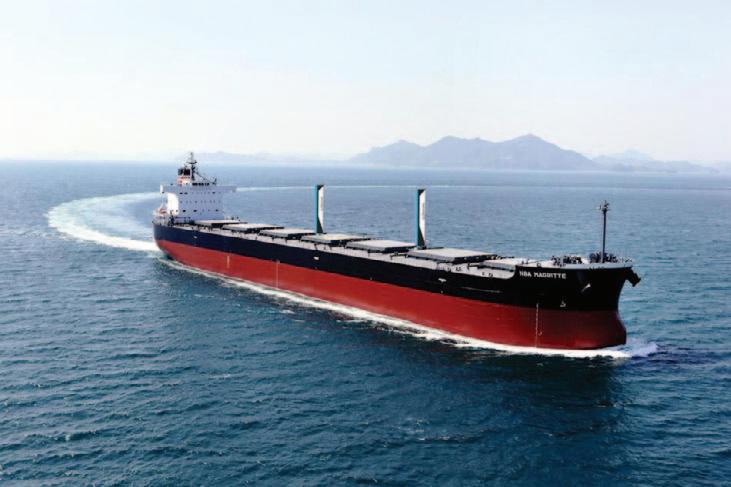
NBAtlantic will equip the bulk carrier with the VentoFoil windassisted propulsion unit from Econowind B.V., wingsail producer based in the Netherlands. This unit is expected to help reduce greenhouse gas (GHG) emissions during vessel navigation. NBAtlantic will collect data on the propulsion generated by this equipment, in addition to meteorological and ocean conditions during navigation, and measure the unit’s effectiveness in collaboration with Cargill International S.A.
Sitting on a 20ft-long (approximately 6m) flat rack container with no walls, VentoFoil has a 16m vertical wing that plays the role of a sail. Like an airplane wing, VentoFoil creates propulsion with the pressure difference on both sides of the wing. The unit takes in wind through its suction port and obtains greater propulsion by amplifying the pressure difference.
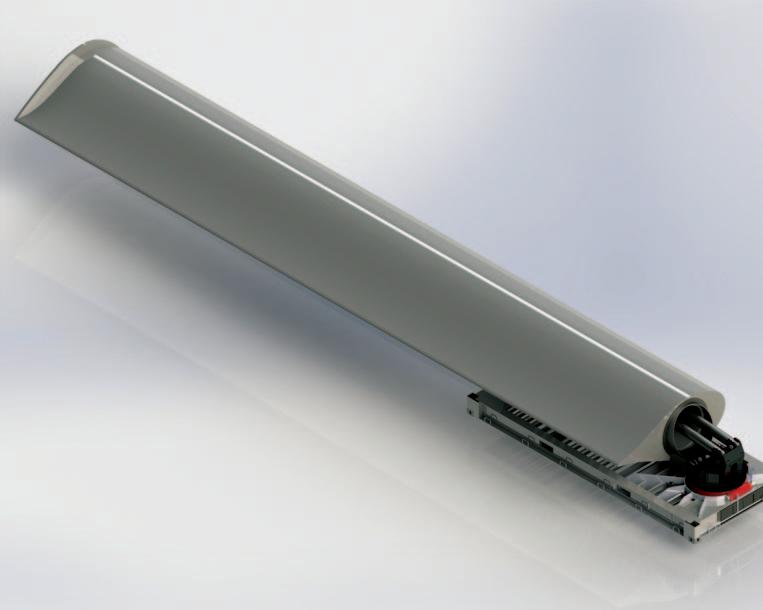
VentoFoil is smaller than similar equipment, keeping it more out of the way of cargo handling. It is also easy to install and relocate.
This initiative is part of NYK’s long-term target of net-zero emissions of greenhouse gas (GHG) by 2050 for the NYK Group’s oceangoing businesses. The NYK Group will utilize the knowledge gained in this research and development to promote initiatives related to various energy-saving technologies, including the
use of wind power.
On March 10, 2023, the NYK Group released its medium-term management plan “Sail Green, Drive Transformations 2026 — A Passion for Planetary Wellbeing.” The NYK Group is promoting growth strategies with ESG at the core, based on the Group’s basic philosophy of “Bringing value to life” and a new corporate vision for 2030, which reads, “we go beyond the scope of a comprehensive global logistics enterprise to co-create value required for the future by advancing our core business and growing new ones.”
This initiative is part of the ‘Sail GREEN’ brand, which emphasizes NYK’s efforts to reduce GHG emissions through the transport of goods and contribute to the eco-friendly supply chains of customers, regardless of the mode of transport (e.g., by sea or land, through terminals, etc.).
ELATED SUSTAINABLE DEVELOPMENT OALS (SDGS)
Econowind’s groundbreaking innovation, the VentoFoil®, is decarbonizing the maritime industry with its ability to achieve higher sailing speeds and significantly improve the Energy Efficiency Existing Ship Index (EEXI) and Carbon Intensity Indicator (CII). NYK will sail into the future of sustainable shipping with Econowind’s VentoFoil.
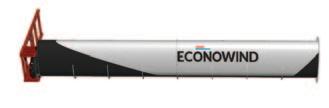
Norvic Shipping adds eco-friendly Ultramax to expanding fleet
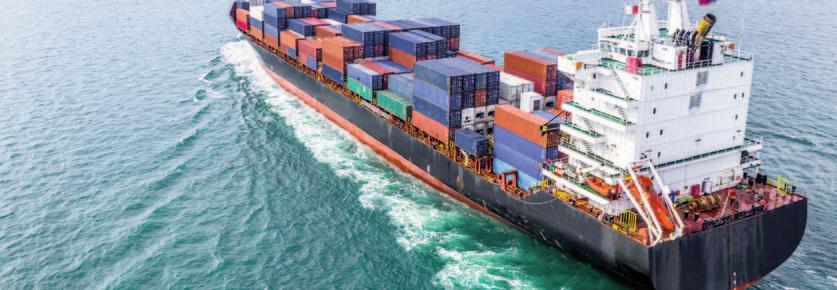
DRY BULK OWNER AND OPERATOR ADDRESSING MARKET DEMAND FOR GREENER SHIPS
Norvic Shipping, the global dry bulk owner and operator, has taken delivery of an energy efficient Ultramax vessel on a long-term charter as the organization continues to expand its fleet to meet increased demand from clients for greener ships.
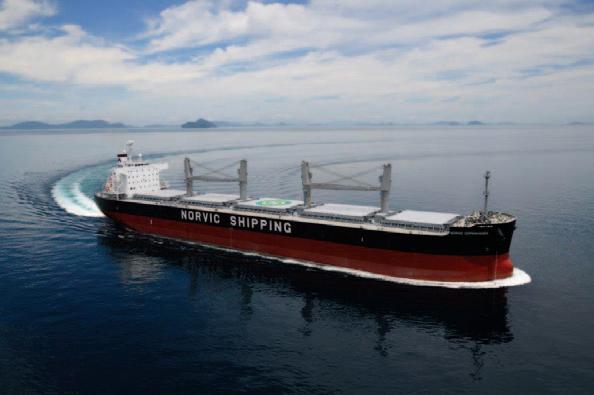
The 64,000dwt fuelefficient vessel, named Norvic Copenhagen, will be deployed worldwide after being delivered by Imabari Shipyard during a recent handover ceremony in Japan.
Commenting on the acquisition, AJ Rahman, Group Chairman and CEO of Norvic Shipping, said: “Acquiring dry-bulk vessels on lengthy charters is part of Norvic’s strategy to expand our long-term fleet, ensuring we meet increased demand from our customers for efficient ships.”
Rahman added: “Norvic employs an
active management approach to fleet trading, keeping in mind vessel utilization and performance. We put great focus on fuel and voyage efficiency and have an accomplished and qualified team of operators who proactively work towards reducing our impact on the environment.
“Alongside building our own modern fleet, we work with our network of vessel owners to provide customers with choices around how they can meet their ambitions,
including access to ships with a higher CII/EEXI rating, or, over time, those that can use alternative fuels.”
The arrival of Norvic Copenhagen is the first of three energy efficient vessels that the organization will add to its fleet this year. In the coming months, the company will also take delivery of two 40,000dwt Handysize vessels – to be named Norvic Houston and Norvic Singapore respectively —from Onomichi Shipyard in Japan.
The handover ceremony of Norvic Copenhagen was attended by AJ Rahman; Niels Kay Kjaer-Petersen, Commercial Director and Co-head of Atlantic Business Unit; Michael Fenger, COO and Head of Global Chartering; Abhijit Palande, Commercial Director of the Pacific Business Unit; and Tareef Rahman, Director, Strategy and Business Development.
The best choice for versatility
Cygnus 4+ General Purpose is a light, tough multi-mode ultrasonic thickness gauge. It is our top affordable all-rounder, ideal for the diversity of ship surveys.
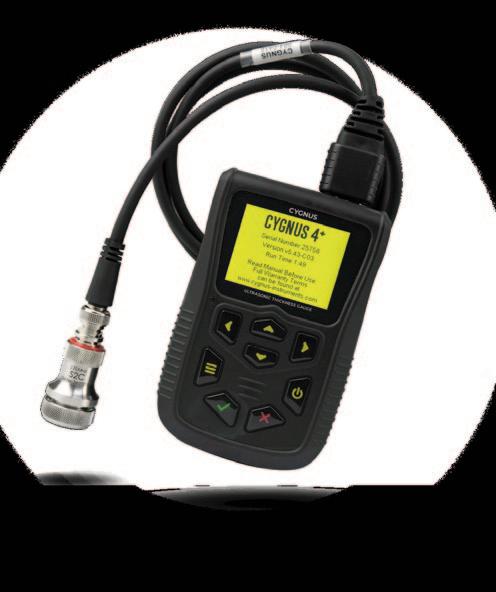
Extremely robust and simple to use 3 measuring modes for quick, reliable measurements - even for heavily corroded metals
Accurate through-coat measurement by multiple Echo mode as specified by Class societies
• Sunlight readable display with Live A-Scan for visual verification
• Sequential data logging for easy reporting and analysis
Port of Newport is Welsh and UK number one steel port for seventh successive year
Associated British Ports (ABP) has announced that the Port of Newport has maintained its position as the leading steel port in both Wales and the UK for the seventh consecutive year. This achievement further solidifies Newport’s pivotal role in supporting the UK’s steel industry and its contribution to the nation’s economy.
The UK Department for Transport’s recently published UK Port Freight Annual Statistics for 2022 reveal that the Port of Newport is the largest UK steel port by a significant margin, having exported nearly 600,000 tonnes more steel than all other 14 major steel-handling UK ports combined. Last year, Newport’s steel exports reached an impressive 955,000 tonnes, which represents 72% of the total UK exported iron and steel products from UK major ports.
Further, Newport isn’t only the UK’s number one steel port for exports, but it also stands as the leader in terms of total UK steel tonnage, handling a total of 1.4mt (million tonnes) of iron and steel products in 2022, 24% of the UK’s total iron and steel products.
The port’s exceptional performance is underlined by its continued partnership with Tata Steel, serving as the primary UK port for finished products exported from Tata Steel’s facilities in South Wales. The steel, manufactured at ABP’s port at Port Talbot, and finished at Llanwern near
Newport Docks, finds its route to international markets through ABP’s Port of Newport.
In Wales, Newport has retained its position as the fourth busiest port by tonnage. It serves as Wales’s largest general cargo port, supporting an array of industries spanning not just steel, but also mineral processing, agriculture, construction, recycled metals and forest products, and handling approximately £1 billion worth of trade each year.
ABP Newport’s crucial role is further emphasized by its contribution to the local and national economy. Supporting 4,100 jobs nationally, the port contributes £275 million to the economy annually.
Paul Ager, Divisional Port Manager for ABP, said: “Newport’s history in steel dates back to the late 19th century, and ABP is proud to continue to support the port’s historic legacy and play an integral role in the success of the UK’s steel industry.
“Newport’s steel expertise now extends to specialist steel products handler W.E. Dowds, which ABP acquired in 2018, and is helping to support the ongoing growth of the port.
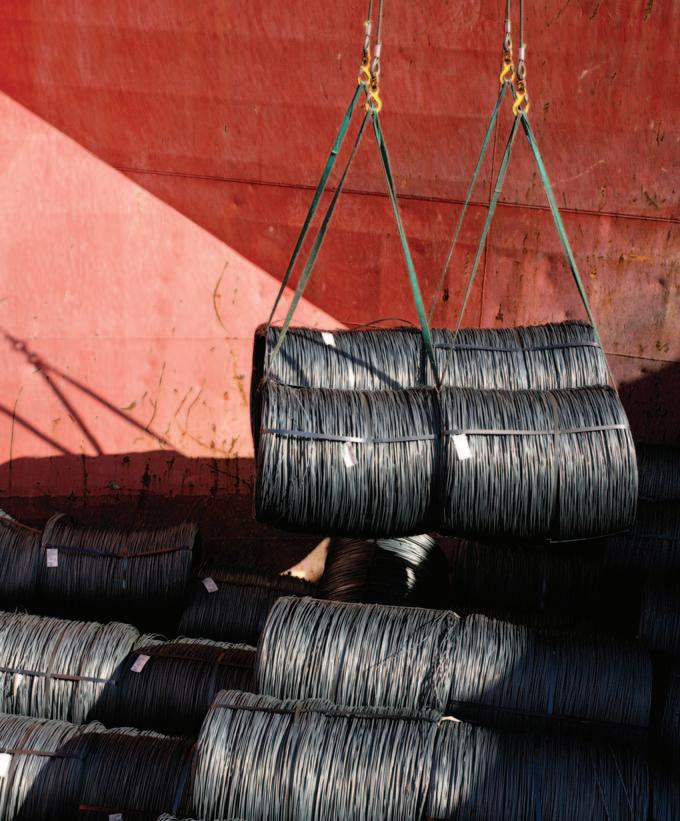
“As the most easterly of ABP’s South Wales ports, and with excellent links to the nearby M4 and direct rail connections, the port occupies a prime location to service the UK’s main industrial and commercial regions.”
ABOUT ABP WALES
ABP’s five Ports in South Wales, Barry, Cardiff, Port Talbot, Newport and Swansea contribute £1.5 billion to the UK economy every year, supporting 21,800 jobs across the UK.
ABP’s Port of Cardiff handles around v 1.8mt of cargo each year.
The Port of Newport’s steel terminal v provides over 30,000m2 of modern, covered storage dedicated to steel import and export operations.
Port Talbot supports steel production v in South Wales and handles project and heavy lift cargoes, steels and other metals, building aggregates and cargoes to support the offshore energy sector. Swansea is the most westerly of ABP’s v South Wales ports, with the capacity to handle vessels of up to 30,000dwt and offers berths and facilities for most types of cargo.
More than 14,000m2 of warehousing v and extensive open storage facilities are available at the Port of Barry.
ABOUT ABP
ABP, the UK’s leading ports group is Keeping Britain Trading with 21 ports and other transport-related businesses, creating a unique national network capable of handling a vast array of cargo.
It drives growth, contributing £7.5 billion to the UK economy every year and supporting over 119,000 jobs. Its current investment programme promises to further increase ABP’s contribution to regional economies around the UK.
ABP is also an essential partner for the Offshore Wind industry, providing Operations and Maintenance (O&M) for ever 50% of the sector’s activity, as well as investing in infrastructure to release future renewable energy generation.
ABP in numbers: handles around 90mt of cargo each v year; owns 5,000 hectares of port estate v with 1,000 hectares of open storage and 1.4 million square metres of covered storage; has 87km of quay; v handles over 1.5 million vehicles every v year; generates around 1/4 of the UK’s rail v freight; and has invested over £55 million in low v emission and renewable energy generation technologies.
We appreciate the opportunity to work with you.
Our strengths are our people and our innovative technologies, allowing us to move cargos safer and more efficiently than ever before. Our team strives every day to meet our customers’ waterborne transportation needs while also being leaders in sa fety and environmental stewardship. Waterborne commerce never stops, and neither do we.
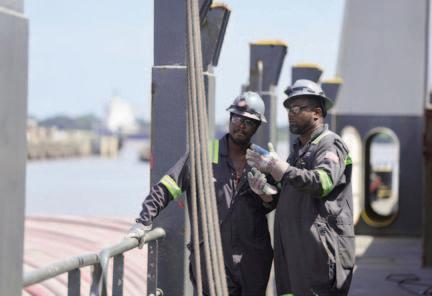
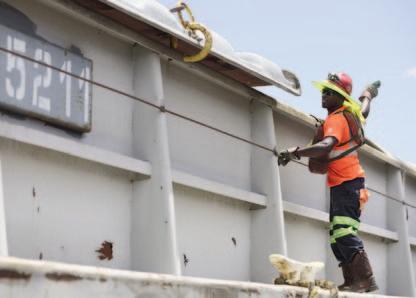
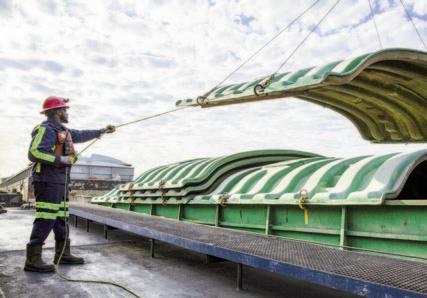
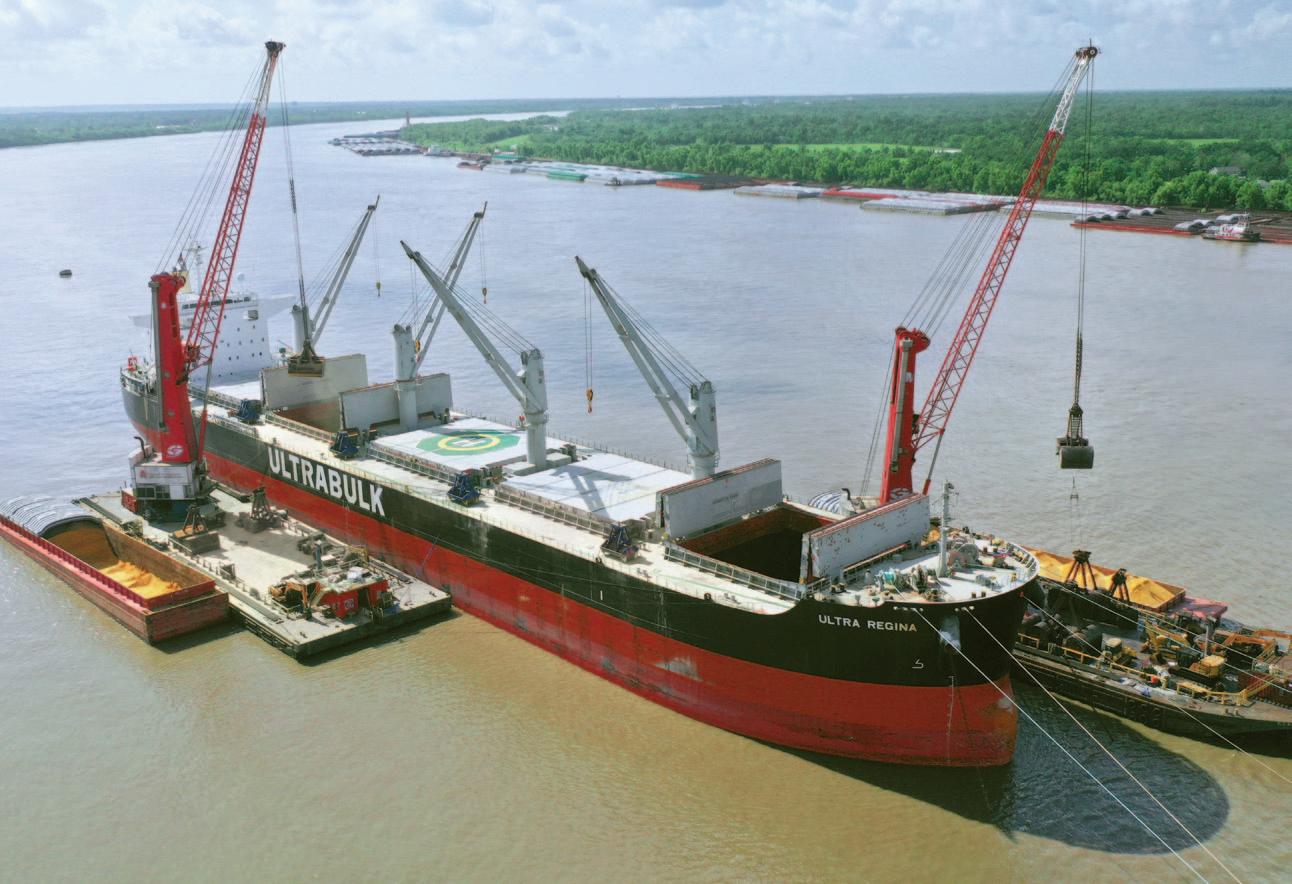
Grain export bonanza at Paranaguá
Operators of the Eastern Export Corridor at the Port of Paranaguá (Corex) handled almost 12.97mt (million tonnes) of agribulk in the first seven months of this year. This is the most ever recorded by the complex. The previous best was in 2020, when 12.92mt were shipped.
In terms of products, Corex transported 7.68mt of soybeans, 2.99mt of soy bran, 2.26mt of corn and 30,640 tonnes of wheat. In comparison, in the corresponding 2022 period, shipments amounted to 6.57mt of soybeans, 2.90mt of bran, 1.85mt of corn and 32,895 tonnes of wheat.
According to Gabriel Vieira, the director of operations at Portos do Paraná, “The intense movement of grain this year resulted in the Paranaguá Export Corridor recording the highest accumulated volume in seven months of its history.”
Just in the month of July, Corex reported traffic of 1,875,128 tonnes, of which corn accounted for 352,297 tonnes. This commodity had resumed shipment after a three-month break and the tonnage in July was up 42.7% compared to the 246,747 tonnes handled in July 2022. Also in that month, 1,522,831 tonnes of
soybeans and bran were moved.
Significantly, the daily average for grain shipments in July reached 62,504 tonnes, up from the 59,058 tonnes per day reported in July 2022. However, this year, despite handling operations being suspended for 8.4 days compared to 4.3 days because of rain, net berth productivity was higher.
Shipments generated by the Eastern Export Corridor are undertaken at three berths at the Port of Paranaguá: 212, 213 and 214. There handled 30 ships loaded in July compared to the 33 that used the facilities in July last year. Barry Cross
Dutch Seaports win International Award for Sustainability
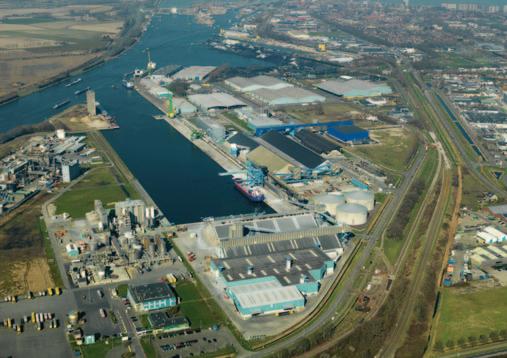
The Dutch seaports of Rotterdam, Amsterdam, Terneuzen/Vlissingen, Moerdijk, and Groningen have jointly won the ‘World Ports Sustainability Award’.
They received the award for a joint project aimed at the application of OECD guidelines for seaports. These government guidelines concern corporate social responsibility in international business. The seaports examined how they could contribute to making occasionally risky cargo flows more sustainable.
The Seaports Trade Organisation (Brancheorganisatie Zeehavens, BOZ) has examined how seaports can influence — from their position in the supply chain — the process of making cargo flows sustainable. These cargo flows sometimes involve risks such as environmental damage, human rights violations or exploitation. Such risks are also referred to as International CSR risks: International Corporate Social Responsibility.
On the basis of the OECD Guidelines for Multinational Enterprises, the BOZ has examined the role and responsibility of seaports as one of the many links in the supply chain. It has also examined how seaports can contribute to reducing the international CSR risks for cargo flows processed in or transiting through the ports. The seaports have used the results of this study to identify the international CSR risks and to list the arsenal of measures available to seaports.
The project exemplifies how the port community can make a positive contribution to making cargo flows more sustainable.
The study was part of the Work Programme Seaports in which the BOZ, consisting of Port of Rotterdam, Port of Amsterdam, North Sea Port, Port of Moerdijk, and Groningen Seaports, worked together with the Dutch Ministry of Economic Affairs and Climate Policy and the Dutch Ministry of Infrastructure and Water Management.
DUTCH SEAPORTS HONOURED BY AWARD
Koen Overtoom, CEO of Port of Amsterdam, responded with great pleasure on behalf of the Dutch seaports: “The Sustainability Award represents an important recognition of the efforts of the Dutch seaports by the International Association of Ports and Harbours (IAPH). This award therefore constitutes a significant honour for us. The project has strengthened the
co-operation between the seaports in the area of sustainability. This co-operation will strengthen us permanently in our shared ambitions to achieve progress in making a number of international supply chains more sustainable. We will also continue talks with the Dutch Ministry of Foreign Affairs and the Dutch Social and Economic Council on the topic of International CSR and the further elaboration of this theme.”
PROGRAMME BACKGROUND
The International Association for Ports and Harbours (IAPH), the alliance for the global port community, launched the World Ports Sustainability Program in 2018. The ports collaborate internationally within the IAPH by exchanging knowledge and experience concerning sustainable development in the international port community. Since 2018, the World Ports Sustainability Awards have been awarded annually for best practices. The Dutch seaports received the Award in the category of Governance and Ethics. The Awards are presented annually during the annual IAPH World Ports Conference. This conference was slated to take place in Antwerp, Belgium, in 2020, but has been cancelled due to the coronavirus disease (Covid-19) pandemic. The awards are now presented digitally to the winners, including the Dutch seaports.
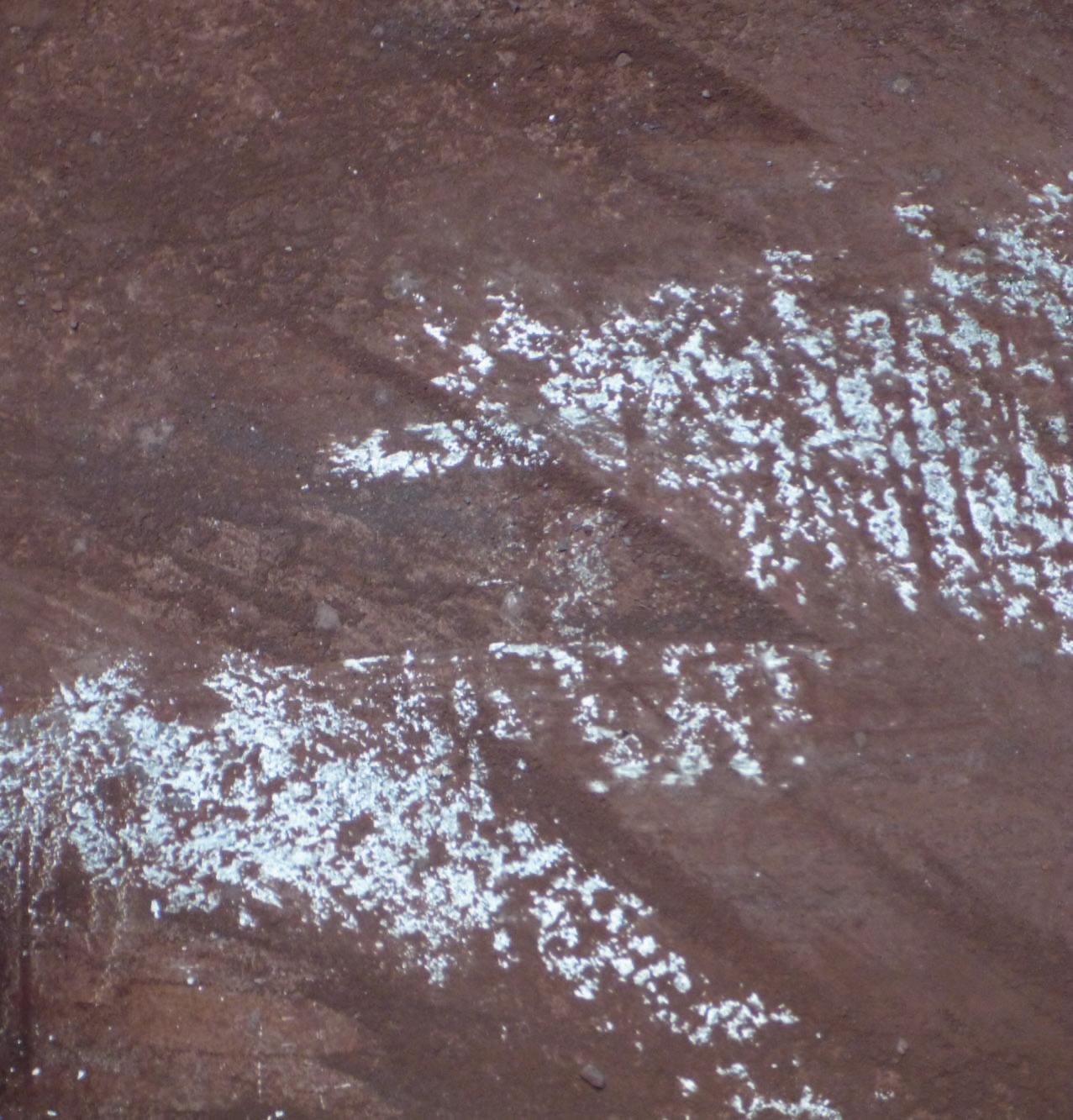
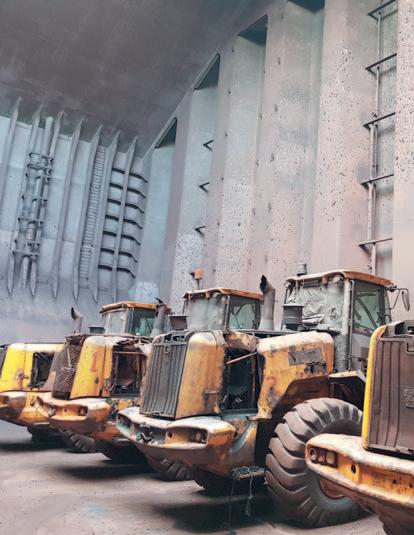
Minister unveils clean energy partnerships to drive Port of Newcastle into the future
On 12 July, Port of Newcastle in Australia unveiled, during a visit by Minister for Climate Change and Energy, Chris Bowen, that 30 supporting partnerships will underpin its advancement towards the enablement of a world-class clean energy economy in the Hunter Region.
The partnerships, which include domestic and multi-national organizations, complement the backing of the Commonwealth Government, with the Port securing a $100-million funding grant in the 2022 Federal Budget for the Clean Energy Precinct.
Port of Newcastle CEO Craig Carmody said the once-in-a-generation project is one of two key developments in the port’s 2030 diversification strategy.
“Our dedicated 220-hectare Clean Energy Precinct offers the perfect platform for large scale clean energy production. It will be supported by common user, open access, shared infrastructure across clean energy storage, transport and export facilities servicing production from the Precinct itself and from right across the Hunter Region,” Carmody said.
“We are standing at the forefront of the development of a new industry. Partnerships, both local and international, which bring together infrastructure, investment, knowledge, skills and resources, will be critical in the establishment and scale-up of a domestic clean energy economy and export trade pathway at Port of Newcastle.
“Creating a place for local, Australian and international commercial expertise and research knowledge to work collaboratively, ensures Newcastle and the Hunter remains Australia’s energy powerhouse,” he said.
Port of Newcastle’s Board Chair, Prof Roy Green, said the Port was advancing the Hunter region, the state and Australia’s global ambitions to be a leader in clean energy.
“For several years, Port of Newcastle has pursued a strategic direction outlined in our diversification strategy to deliver a clean energy industry. With today’s announcement, providing a clear path forward as to how these plans become a reality through the strength of our domestic and international partnerships,” Prof Green said.
“The Clean Energy Precinct not only
supports Commonwealth and state governments clean energy targets, it forms part of a domestic and global collective, all pursuing a common goal of producing and transporting sustainable energy,” he said.
As the Commonwealth Government priority hydrogen hub in NSW, to date, Port of Newcastle has signed 15 Memoranda of Understanding (MOU) agreements to support the development, storage and export pathway enablement of a clean energy economy at Port of Newcastle.
“These formal MOU agreements are also strengthened by the backing of 15 other critical organizations for the Clean Energy Precinct project via Letter of Support or a Letter of Intent for future collaboration,” Port CEO Craig Carmody said.
“Collectively, these relationships represent key industry support across clean energy production, mobility, export and bunkering, energy generation, transport, infrastructure, offtake, agriculture, education, innovation, research and development.
“This kind of collaboration allows for connections to be forged from the outset between the State’s renewable energy projects, clean energy production projects and the Port’s biggest assets, its deepwater channel and existing global partnerships,” he said.
Memoranda of Understanding agreements have been formalized with: coNEXA, EnergyCo, Energy Estate, Eurus Energy, Fortescue Future Industries, Hunter Hydrogen Network, KEPCO (Korea), Lake Macquarie City Council, Lumea (Transgrid), Mitsubishi Heavy Industries (Japan), MOL Group (Japan), Orica, Origin, Platform Zero (Rotterdam) and University of Newcastle.
Among those to also pledge their support formally for the Port’s Clean Energy Precinct plans are: AGL, Ampcontrol, Aurizon, bp Australia, Business Hunter, Hunter iF, Hyundai Australia, Infrabuild , Jemena, Keolis Downer, Linde Engineering, NewH2, Newcastle City Council, Snowy Hydro and Westrac.
Project Lead and the Port’s Chief Commercial Officer, Simon Byrnes, said the Clean Energy Precinct MOUs spanned collaboration on the development of inland and offshore wind projects, electricity transmission and water supply, clean energy
production, clean energy storage, distribution and export facilities, export and bunkering, skills and training pathways, advanced manufacturing and innovation hubs.
“By collaborating with all levels of government, with industry partners and education providers, we are working to deliver a shared ambition to accelerate innovation, foster technological advancement, generating jobs and educational pathways for this new industry at scale,” Byrnes said.
“Our vision is a thriving Hunter community which is viewed as the best place to work in the clean energy industry, both in Australia and across the world.
“Port of Newcastle is working to create connections between infrastructure, markets and people. The port has secured letters of intent from each of the entities that have the potential to be significant clean energy offtakers in the Hunter Region, and we are also working with existing export customers in key markets across Asia, such as Japan and Korea, to understand their needs and potential opportunities.
“Our existing supply chain is one of the most efficient in the world and we are seeking to leverage that expertise to generate economies of scale and scope,” he said.
The port released Stage 1 renders of its Clean Energy Precinct vision in May.
“Port of Newcastle has a long history in energy export and is diversifying further to drive the clean energy trade flows of the future. We are harnessing the Hunter region’s capability and critical energy assets to deliver Australia’s decarbonization objectives whilst creating new, and additional trade opportunities, jobs and economic growth for clean energy export at scale in Australia and locally,” Port CEO Craig Carmody said.
“There is a long way to go to make this project a reality, but we are committed to diversifying to support jobs growth and economic security for generations of locals and port workers to come. We look forward to working closely with industry and the community to bring a clean energy economy to life in sustainable and safe way that secures the prosperity of Newcastle and the Region for decades to come,” he said.
Port of Barranquilla handles bulk carriers with under 10m of available draught
In a report released by Asoportuaria, it was noted that the Colombian Port of Barranquilla was recently able to accommodate two bulk carriers when the maximum available draught was no more than ten metres.
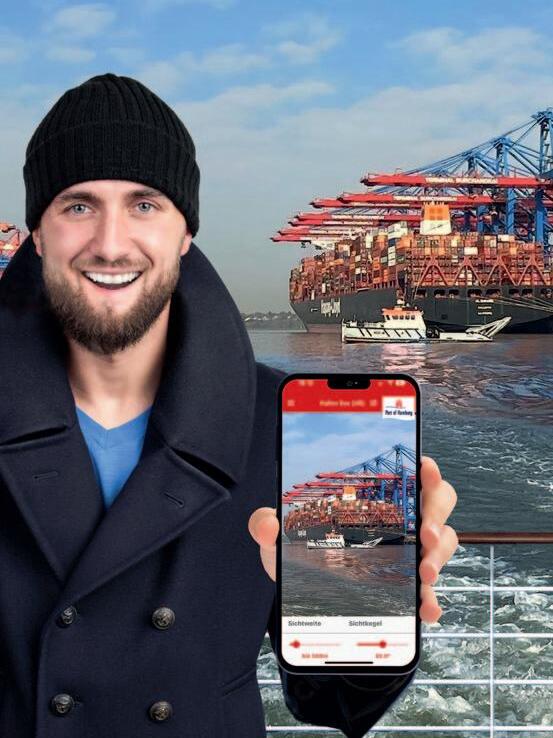
The Liberian-registered geared vessel Harvester docked at a berth of Sociedad Portuaria Riverport. There, it was loaded with grain using a tug conveying barges, from which grain could be extracted using the Harvester’s own cranes. The 2017-built vessel can carry up to 37,600dwt It requires no more than 7.7 metres of water, being 181 metres long and 30 metres wide.
Meanwhile, the Santa Maria called at Palermo Sociedad Portuaria. Built in 2015, this vessel can accommodate up to 61,323 deadweight tonnes. It draws a maximum 9.9 metres of water, being 199 metres long and 32 metres wide.
Barranquilla recently also reported another first, when the bulk carrier Josco Guangzhou delivered 39,750 tonnes of yellow corn to the Riverport terminal. Barry Cross
Galigrain expands presence at La Coruña
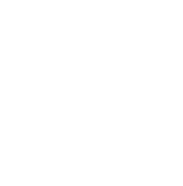
At the north-western Spanish Port of La Coruña, bulk handler Galigrain has applied to build a new 17,411m² storage warehouse, on what would be a total operating area of 21,049m² in the outer harbour. With the expected concomitant extension of its concession, that would mean the company would have a total of four large warehouses on the Punta Langosteira quay. In total, Galigrain would have more than 90,000m² of operating concession within the port, with its investment in these areas reaching €41 million. The company is currently the main agri-food bulk operator in the port of La Coruña. Although based in Galicia, the company, which forms part of the Nogar group, has port terminals throughout Spain, Portugal and Latin America.
The planned new warehouse will mainly handle agribulk foodstuffs for use by livestock in the surrounding Galician region, northern Portugal, and nearby areas of Spain, although the facility would also be able to potentially handle other commodities too, above all dry bulk.
Alongside the new warehouse, Galigrain is also introducing mechanized systems for the unloading and transporting of grain from docked vessels to its warehouses. This involves the introduction of a closed circuit of conveyor belts, hoppers and transfer towers. Automation, stresses the company, will improve both overall productivity and efficiency as well as environmental conditions involved in the handling process.
Barry Cross – Henry FordMajor infrastructure and equipment investments
Port Saint John is a part of the critical transportation infrastructure of Canada and a cornerstone of the New Brunswick economy. Its mission is to proactively manage, in a sustainable manner, the provision of infrastructure and service for present and future users of Port Saint John to the economic and social benefit of the surrounding region.
The port handles bulk, breakbulk, project cargo and containers, as well as cruise vessels. It is heavy lift and project cargo experienced — fully serviced and fully capable, providing unique and comprehensive breakbulk handling solutions. In terms of bulk, Port Saint John has four existing bulk operations; PotashCorp, American Iron and Metal, Crosby’s
Molasses and NB Power, with opportunities for additional bulk handling at its Lower Cove terminal.
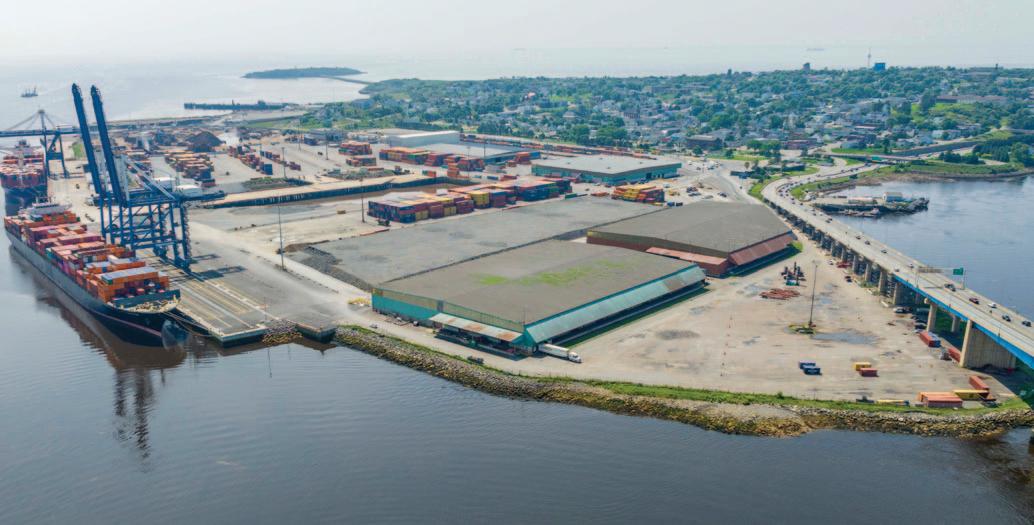
For handling cargo, Port Saint John offers three different stevedores to work with: DP World, LOGISTEC, and QSL. Each has a local presence in the market, but also are well known internationally. This enables these companies to be active globally in the project cargo space throughout the year. A well-trained labour force supports them: the International Longshoreman Association (ILA). The ILA has handled various project cargoes in the past few years, including, but not limited to: cable reels, monopiles, nacelles, blades, and towers. Recognizing the growth at the port, and planning for the future, the ILA
has been proactive in growing its workforce, and is expanding its numbers in the coming years. This bodes well for wind projects in the short, medium, and long term.
RECENT DEVELOPMENTS AT PORT SAINT JOHN
Five-year averages show that potash volumes at Port Saint John are continuing to increase. This is due to growing demand globally, but in particular in South America and Europe. Current annual volumes are anticipated to exceed one million tonnes again this year.
Stevedore DP World continues to increase the amount of shoreside equipment available at its site. Recent
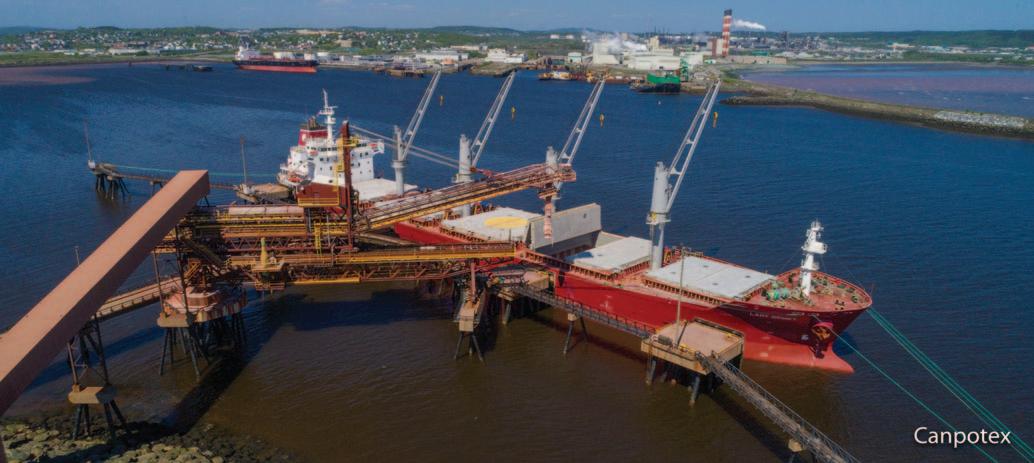
significantly enhance Port Saint John
investments in Saint John equipment exceed C$45 million. This includes new cranes and shoreside handling equipment.
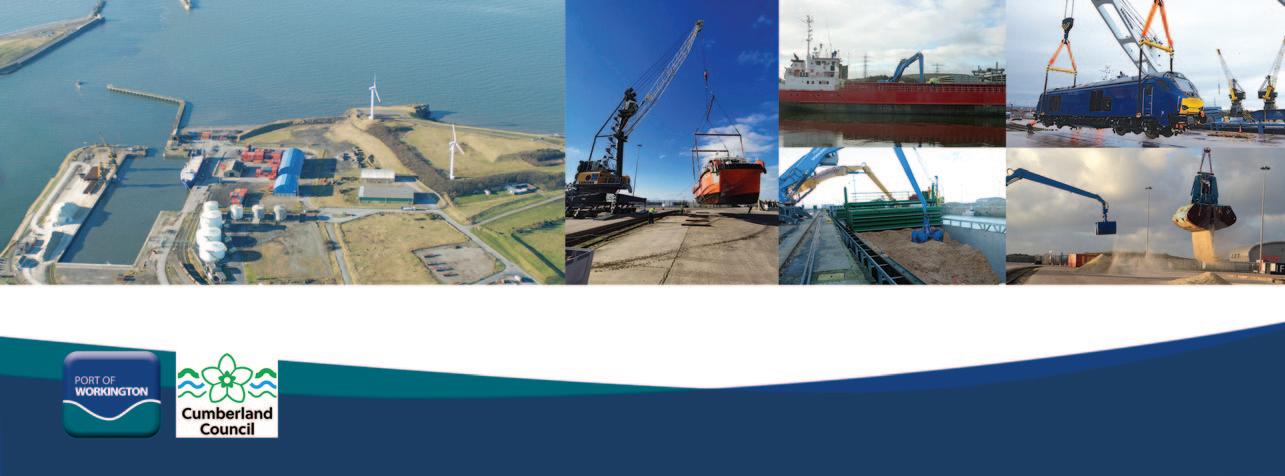
Recently Port Saint John and DP World reactivated two pier-side warehouses. In total this brings the available warehouse space at DP World’s terminal to more than 500,000ft2. The facilities are well suited to handle pulp, paper, and steel commodities.
Another major stevedore at the port, QSL, remains interested in offshore wind opportunities in Saint John. It has invested over C$4 million into new portable equipment to service the industry.

The newly completed 345m-long 17.1m-deep berth recently welcomed the first ship alongside. This berth is built to handle container, breakbulk, and bulk vessels to ensure Port Saint John remains well positioned to handle all cargoes.
Slip infill continues behind the new pier — once complete an additional 16 acres of
land will become available for various types of cargo. In total between the new pier, slip infill and the deepening and widening of the main channel over a quarter billion dollars has been invested by the federal, provincial and port authority.
This investment has been matched nearly dollar for dollar by the private sector in the region, bringing the total investment into Port Saint John and its immediate hinterland to a half a billion dollars.
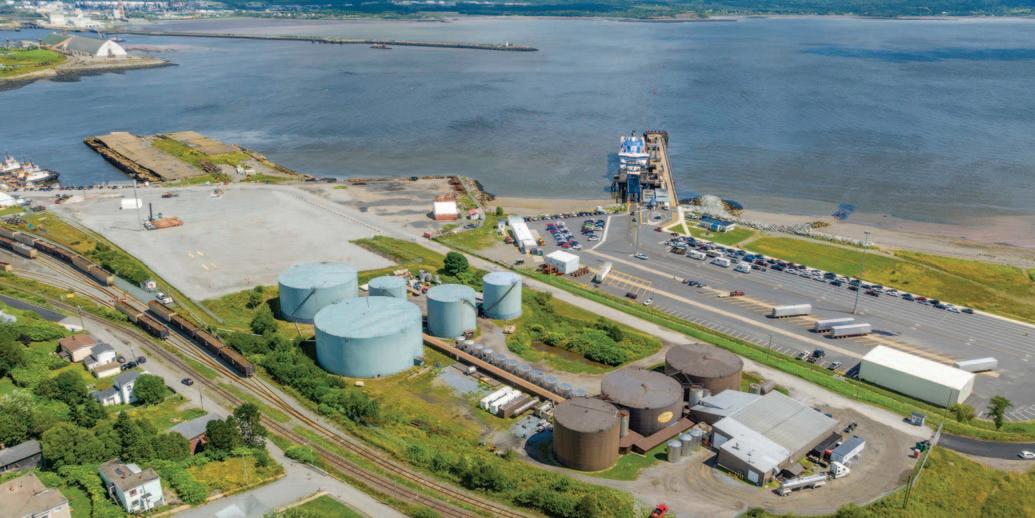
With the recent acquisition of Pan-Am Rail by CSX, Port Saint John now connects into three Class One Railway providers (CN, CPKC, CSX). CPKC recently strengthened its optionality in Saint John, with the acquisition of Kansas City Southern. Overall these three class ones enable Port Saint John to be well positioned to service: Canada, the United States, and Mexico well from an Atlantic
Gateway. This Gateway is, by nautical mileage, closer to Brazil than some US East Coast Ports and serves as a key location to move cargo from Europe and Asia (via the Suez) into an ice-free, deep water port.
On the liquid bulk side, Port Saint John boasts one of the only fully food grade facilities on the East Coast of North America in Crosby Molasses. The facility continues to import various liquid bulk commodities but is looking for opportunities to expand its food grade portfolio (for both imports and exports), and overall volumes that move through the facility in the coming years. With the proximity to the DP World Container terminal the Crosby facility has the ability to transload food-grade material to and from containers within minimal shunt time between facilities. This saves shippers time and money on their overall supply chain needs.
Sampling, Inspection & Analysis
HAVER & BOECKER Institutes: advising on all questions concerning packaging material, filling technology and processing technology
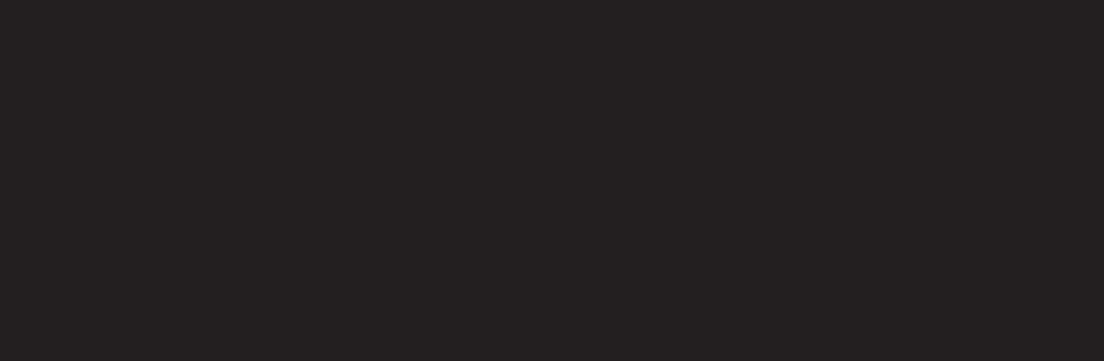
Product, packaging material and filling technology form a fixed but multivariable unit. If only one element is changed, then it always requires changes to the other components and variables. This packaging triangle is the foundation of efficient product filling, and is thus the basis of all activities at the HAVER & BOECKER Institute in Oelde, Germany. For mineral processing technology, HAVER & BOECKER founded HAVER ENGINEERING GmbH which was named an associated institute of the Technical University Bergakademie Freiberg in 2009.
70 YEARS OF EXPERIENCE
Seventy years ago HAVER & BOECKER opened its first test room that focused on packaging and processing technology. It grew steadily and became what today is known as the HAVER & BOECKER Institute at the headquarters of the global company in Oelde, Germany. Every year

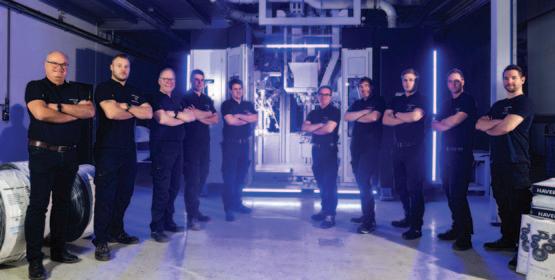
the HAVER experts carry out more than 1,000 product analyses, guide approximately 3,500 visitors through its laboratories and provide important specialist knowledge about HAVER & BOECKER machine technology and the packaging triangle in around 50 training courses. Since the pandemic the company has also become pretty well equipped with video and streaming technology to run any kind of test online.
In a close exchange with customers, it became clear that with the growing variety of fillable products and the associated everhigher market demands, the requirements on packaging materials in combination with the right choice of machine technology are also on the rise.
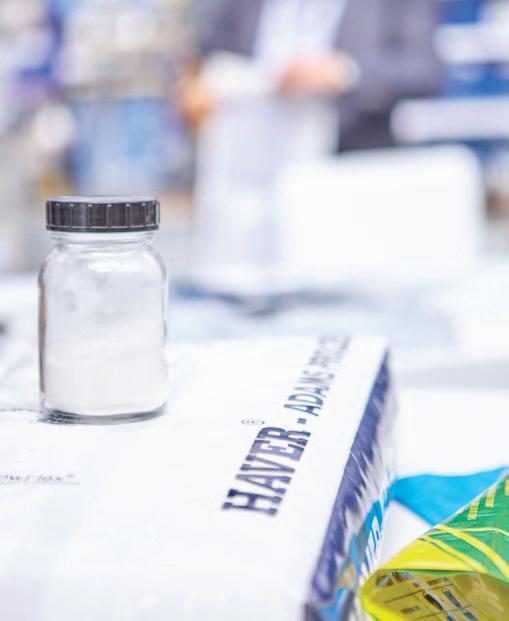
The very same trends apply to the requirements in mineral processing, which the company is researching at HAVER Engineering in Freiberg. As a competent partner, the company develops and
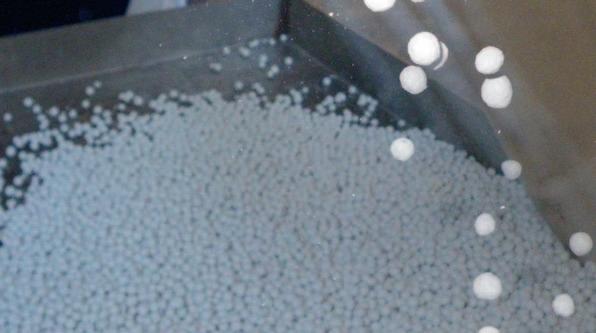
implements innovative and sustainable process engineering solutions in co-operation with its customers. HEM conducts research and development services in the fields of agglomeration/ pelletizing, screening and washing technology for ores, minerals, fertilizer and recycling materials.
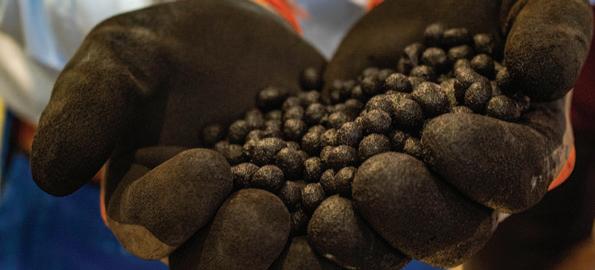
INSTITUTE AS A CENTER FOR RESEARCH AND DEVELOPMENT AND EDUCATION
“R&D and education are carried out in one institute, we can say. This is how we want to go about it,” says Thomas Hilling, General Manager of the HAVER & BOECKER Institute in Oelde. “We supply analysis data and test the product in our laboratory with respect to its physically relevant properties with the aim of determining the best filling technology. In this way the customer knows that the system really suits him,” says Hilling. For the customer, the HAVER & BOECKER
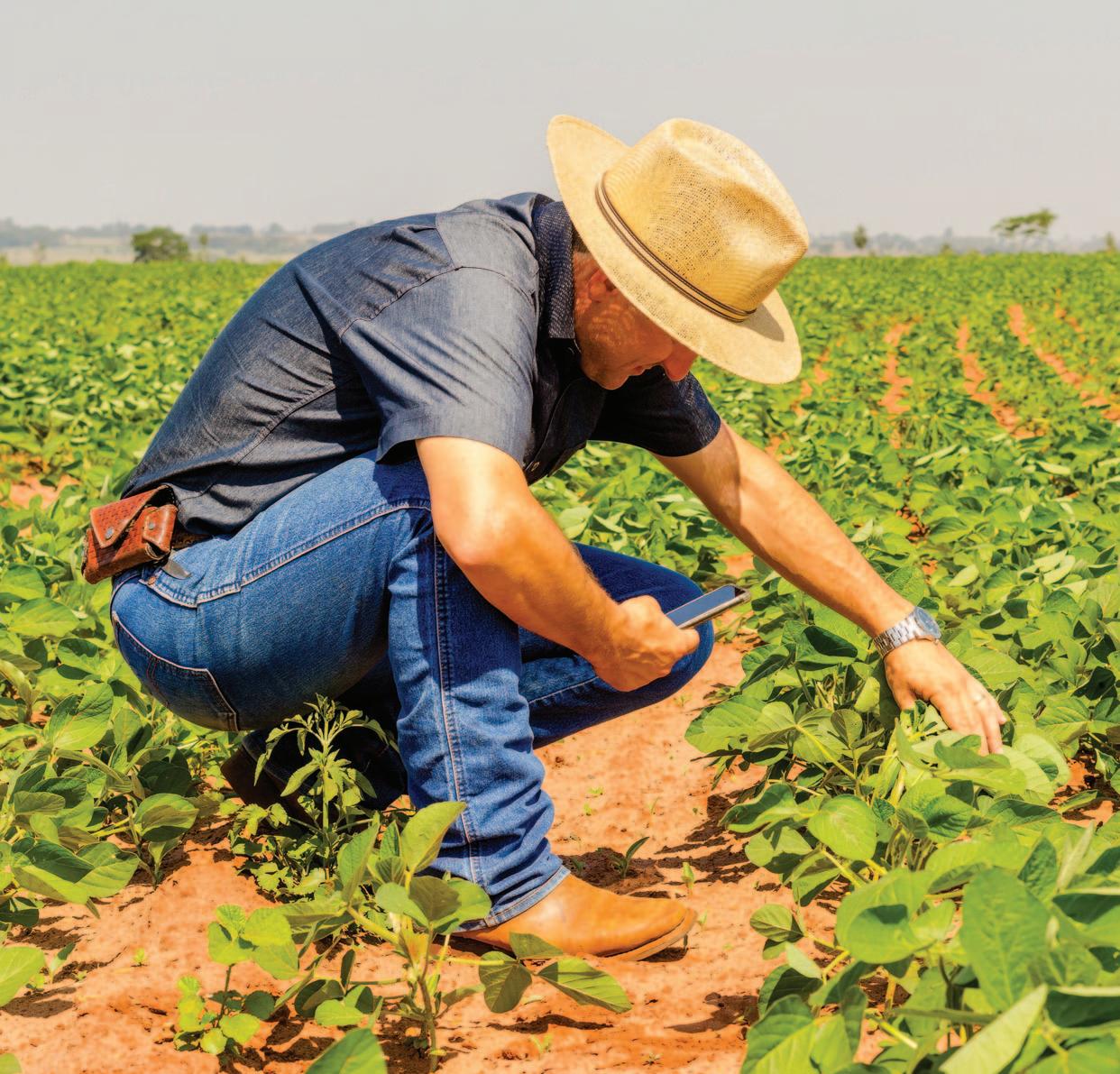
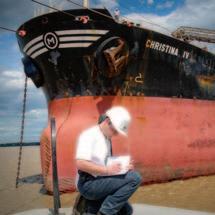
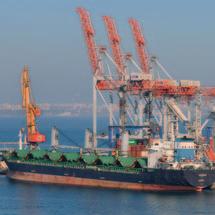

Institute offers training on planned machines or trains interested parties on various packaging materials. Finally, the experts in Oelde carry out and accompany commissioning, tests and inspections at the customer’s site.
For decades HAVER & BOECKER has been known for its screening, washing and pelletizing solutions in the field of processing technology, both dry and wet. As a global supplier, the company takes on the constant challenges of effectively processing of raw and recycling materials. New process engineering solutions often have to be developed. In doing so, they particularly focus on: conservation of resources;
v energy efficiency;
v higher productivity; and
v sustainability. v
“In Freiberg we carry out investigations on processing technologies. With initial laboratory-scale trials, we determine the feasibility of processes. Together with our customer, we evaluate the trial results and define the preferred concept for further pilot-scale investigations. Based on these results, we design the specific machine and process. Our location in Freiberg also allows for further studies of subsequent processes, for example processes in the fields of metallurgy or building materials technology. We are not only an engineering company, but also an associated institute of the Technical University Bergakademie Freiberg. In this way, we support the professional education of young engineers and are in close contact with the scientists,” says Sandra Weyrauch, who has been responsible for R&D since the founding of the associated institute. “The proximity to the university alone allows us to gain deeper insights into research. We are already working on concepts that we know will only be feasible in 10–15 years, and it is a pleasure to be involved in the development of future trends.”
In Freiberg the HAVER & BOECKER Institute employs six engineers and the technical centre is located directly at the Institute for Mineral Processing Machines and Recycling Systems Technology. Here customers can have their products intensively tested for screening, washing and pelletizing capabilities.
CLOSE CO - OPERATION WITH CUSTOMERS AND SUBSIDIARIES
“Not all conditions of the filling location can be simulated here in Oelde. For example these include special climatic
conditions, or the sequence of a complete production line. We test the individual systems at the customer’s site and assist in adapting them to the ambient situation,” Hilling adds.
“In Freiberg we have a special interest in the requirements that are placed on us with the focus on turning our customers’ raw or recycling materials into valuable and saleable products. Especially the development of individual solutions and the cooperation with the university inspire our customers,” Weyrauch proudly says.
CUSTOMER REQUIREMENTS IN THE FOCUS OF CONSULTATIONS
With the HAVER & BOECKER Institute, the machine manufacturer is clearly positioned as a consultant for all questions concerning packaging, filling technology and processing technology. The focus is clearly on specific customer needs. The company can draw on decades of practical experience and a wealth of knowledge from laboratory and field tests. With the Institute, HAVER & BOECKER offers its customers the opportunity to develop processes, comprehensively test and improve products that are to be processed and filled, or to test newly developed packaging materials prior to market launch. Especially the sustainability discussions around the right packaging material becomes more and more in focus. A sustainable and economical overall process for processing of different kind of materials requires individual solutions.
BESPOKE. EVERY BAG IS UNIQUE . THE SERVICE CONCEPT FOR CUSTOMIZED BAGS
At Interpack, the HAVER & BOECKER Machinery Division presented the new Bespoke concept for the first time, thus bringing services related to customized bags together. From customer-specific bag consulting to the development of a bag

design that matches the customer’s brand message and to the sale of the bags — the aim is always to design the packaging that ideally meets the respective customer requirements. The decisive factors are the product to be filled and the optimum filling technology because product, packaging, and machine technology form a multivariable unit known as the packing triangle.
The bespoke tailoring of a suit was used as an analogy during the presentation at the trade fair. “With bespoke suits, you can get your concepts fully transformed into reality,” explains Marta Bortolotti, PROcheck Segment Manager Consumables. “Bespoke clothing requires a great deal of accuracy and precision when it comes to design and size. In fact, bespoke suits are tailored to your body and individually customized in accordance with your ideas and concepts.” Just as a tailor sizes up a suit, HAVER & BOECKER guides its customers through the process in order to get exactly the packaging that best suits them and therefore their end-customers.
BENEFITS OF A BESPOKE BAG
As a bespoke tailor recognizes the importance of stitching and assembling the parts of the model, the experts of both companies know the value of proper gluepositioning and folding in a consistent paper bag. Bespoke bags from HAVER & BOECKER reduce costs from poor bag performance and equipment shutdown, thus leading to greater productivity and fewer complaints from end customers.
STEP-BY-STEP: PROCESS IN DEVELOPING A BESPOKE BAG:
1) Consultation
2) Testing
3) Customized Bag Report
4) FAT Bags
5) Starting up, supply and service:
PSB Inspection: decades of inspection and analysis experience


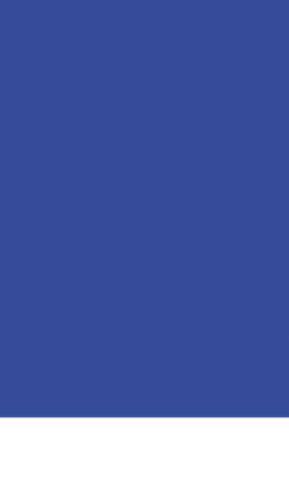
Founded in 2017 by CEO and owner Peter Bagchus, PSB Inspection is a prominent player in the field of inspection and analysis. Stationed in Vlaardingen within the Rotterdam port area, including its own laboratory, the company boasts a dedicated team of seasoned senior surveyors and skilled sampling preparation experts. Complementing these talents is an adept assembly of laboratory technicians operating within the company’s in-house laboratory. The operational and management teams, laden with decades of industry experience, collaboratively oversee these endeavours.

At the forefront of PSB Inspection’s activities lies a focus on coal and its derivatives. However, the company remains acutely aware of the swiftly evolving global energy landscape. This awareness propels its efforts to diversify into burgeoning markets, encompassing biomass, alternative fuels, minerals, metals, slag, fly ash, and fertilizers, each undergoing distinct developmental phases.
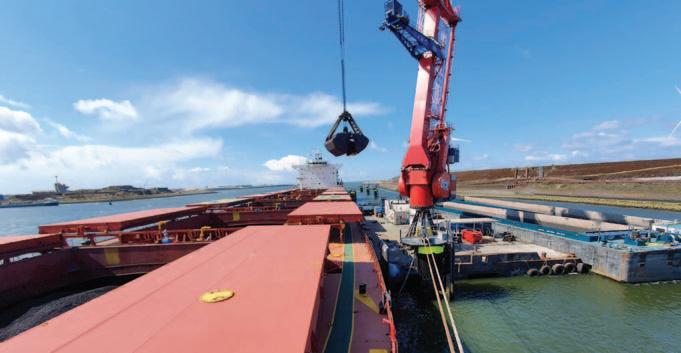
Throughout these pursuits, PSB Inspection staunchly upholds its
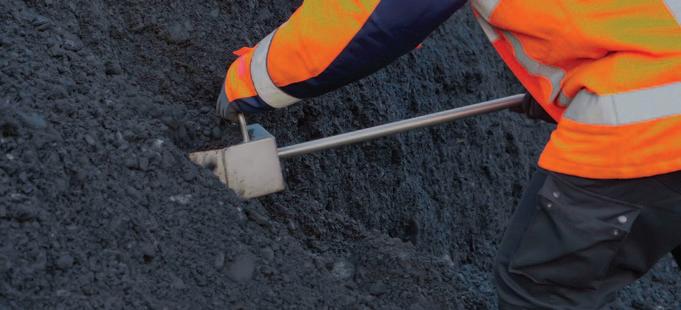
commitment to providing superior quality services in inspection, sampling, sample preparation, analytical analyses, and weight determination — a commitment that is deeply entrenched in the demands of its customer base.
PSB Inspection is regularly designated as an Umpire Lab, where they receive samples from loading and unloading ports. The judgments and results evaluated by PSB Inspection carry binding authority. The laboratory comprises two distinct preparation areas: one for solid fuels and another for clean fuels. These preparation spaces are meticulously designed to prevent any cross contamination. All operations strictly adhere to the latest International Standards ISO and/or ASTM standards. Additionally, their proprietary internal quality protocols are employed.
Consequently, PSB Inspection ensures unwavering quality and certainty for all stakeholders, including suppliers and recipients.
The analyses conducted by PSB Inspection ascertain the chemical composition, commercial grade, and adherence to regulatory standards for gas/toxin measurements, solid fuels, coal, coal-related products, biomass, alternative fuels, agricultural products, metal, and
mineral products.
Operations align with the most current International Standards ISO and/or ASTM guidelines, supplemented by their internal quality procedures. Leveraging cuttingedge technology and an in-house laboratory, they conduct analyses swiftly and with remarkable precision.
Upon a short turnaround period, clients receive a comprehensive report containing exhaustive findings, a strong commercial tool for the clients. This report comprehensively documents all data and calculations employed. The determinations and outcomes as evaluated by PSB Inspection bear the weight of binding authority.
With an international outlook, PSB Inspection extends its offerings to global traders, producers and power utilities/end users beyond Europe to countries such as South Africa, North Africa (including own laboratory), USA, Turkey, the UK, and LATAM. The orchestrations of the multifaceted activities are orchestrated from the company’s headquarters, a hub of activity governed by the rigorous ISO standards 9001 and 17025, including all the relevant DCC certificates (Round Robin) Certification processes for 17020 and GAFTA are also underway, complemented by PSB Inspection’s proprietary internal quality protocols.
Quality analysis and sampling processes in inspection, analysis & sampling of dry bulk commodities in Australian terminals
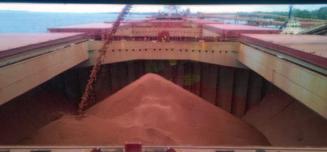

The quality analysis and sampling processes in the Australian dry bulk terminals are robust and adhere to international standards. They incorporate both manual and mechanical methodologies to ensure precision and accuracy. Regular bias testing, sophisticated laboratory analysis, and detailed draught surveys complement these processes to ensure the fair and transparent valuation of commodities cargoes.

The quality analysis and sampling of dry bulk commodities like coal are vital for both the supplier and buyer in terms of ensuring the stated quality, content, and value of the products. Ensuring the correct procedures and methodologies are used during these processes is crucial. This analysis includes the methods of manual sampling, mechanical sampling, bias testing, laboratory analysis, and draught surveys.

Manual sampling involves collecting samples — by hand- before, during and after loading operations, following specified procedures to ensure representativeness. The manual process can be subject to human error and bias. Proper training is
required.
Mechanical sampling utilizes automated systems to collect samples. This method enhances precision and reduces human error and increases accuracy, efficiency, and
compliance with international ISO standards.
Bias testing ensures that the sampling systems are free from systematic error that can influence the accuracy of the results.
Tests include comparing manual and mechanical methods and utilizing statistical analysis.
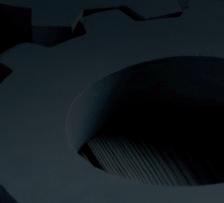
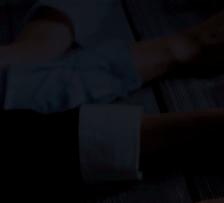
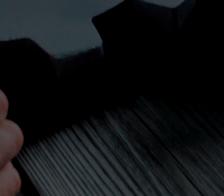
Laboratory analysis includes physical and chemical testing to verify the quality and content of the commodity.
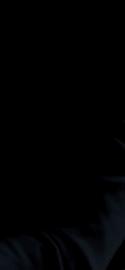
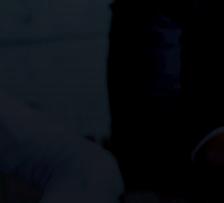
ALS Global, SGS and Bureau Veritas provide 80% of comprehensive laboratory testing and advisory services across Australian Terminals and Ports. In terms of bulk commodities such as coal, ALS provides a wide range of services such as coal quality assessments, coal petrography, auditing, and analytical services. These are achieved using advanced technological processes and instrumentation to assure precision and accuracy in the laboratory analysis. SGS offers a comprehensive suite of services for solid fuels, including coal testing and cargo inspection. SGS’s network of laboratories is equipped with the latest in testing technology and staffed with highly trained and experienced personnel.
Bureau Veritas is a global leader in testing, inspection, and certification (TIC) services. The company provides services in various sectors, including agriculture and food, where its analyses dry bulk commodities. It offers a wide range of services, including physical testing, chemical testing, and inspection services to ensure
the quality and quantity of the commodities. Its labs are equipped with state-of-the-art instrumentation and follow international standards to provide accurate and reliable results.
Draught survey is used by coal exporters to determine final cargo weight in total and is widely used across Australian dry bulk terminals.
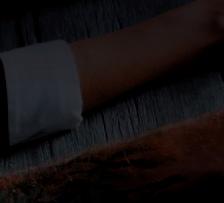
The Master of the Vessel, the Vessel Agent or the Vessel Owner must, at their cost, engage a Marine Surveyor to attend the loading of each vessel through the completion of the loading of the vessel.
The Marine Surveyor: carries out inspection to ensure the v holds are clean, dry, and free from any contaminants or residues that could compromise the quality of the incoming cargo; provides an official certification v attesting to the condition and readiness of the cargo holds for loading.; and ensures all operations and activities v align with the standards and best practices laid out in the pertinent maritime and cargo handling codes and strict adherence to the Australian Maritime Safety Authority (AMSA) Marine Orders, which provide detailed regulations for maritime
operations within Australian waters.
The Marine Surveyor’s role is pivotal in ensuring that maritime operations related to the vessel and its cargo are carried out efficiently, safely, and in strict adherence to regulatory standards. Their expertise provides an added layer of oversight and assurance to all stakeholders involved in the vessel’s operations, from the ship’s crew to the cargo’s recipients.
ABOUT S&WMARINE
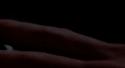
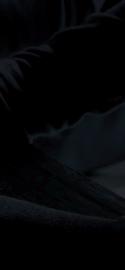
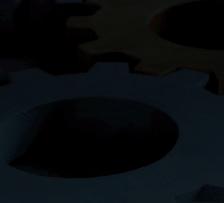
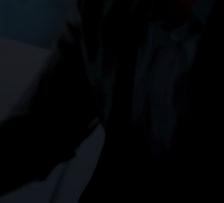
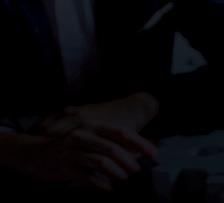

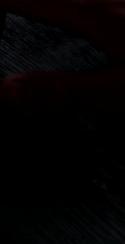
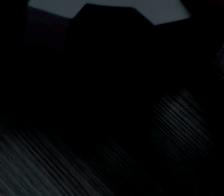
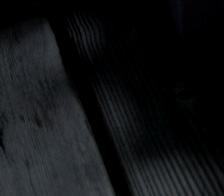
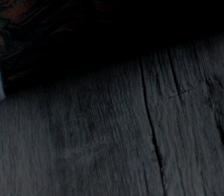
S&WMARINE’s team brings 50 years of combined experience in the maritime surveying scene after a long career as active mariners in senior seagoing positions.
Its generic strategy is how it wants to do things differently, assembling resources and smarter ways of thinking to deliver a unique mix of values and results and a strong culture around ethical drive, safety, and dependability.

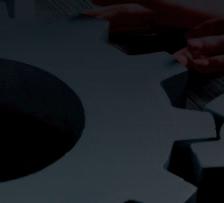
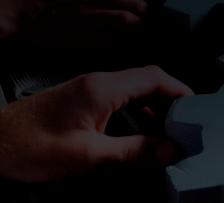
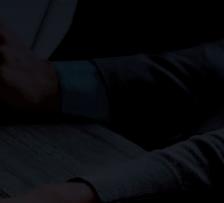
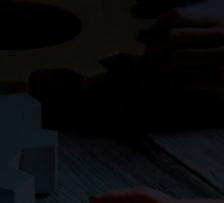
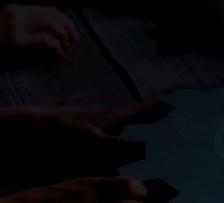
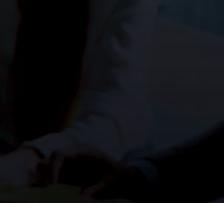

The engagement of the Marine Surveyor is of paramount importance to the maritime industry, guaranteeing that vessels and their cargoes remain safe, efficiently managed, and in compliance with relevant maritime regulations. Its specialized expertise ensures that risks are minimized and that operations remain in line with established standards.
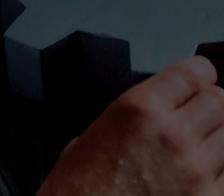
OUR ABC-CONCEPT
As Hudig & Veder Group, we are keen on creating an ultimate logistical plan for our customers by combining different departments and disciplines within our ABC-concept.
Our ABC-concept can therefore be best described as an existing supply chain under control of Hudig & Veder. Agencies, Chartering, Forwarding, Bulk & Projects, we offer the optimal collaboration between our business departments.
IMGS Revolutionary Silo Bagging quadruples bagging throughput at East African terminal
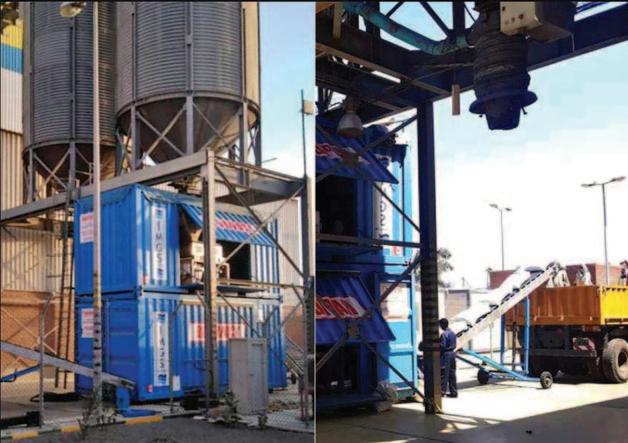
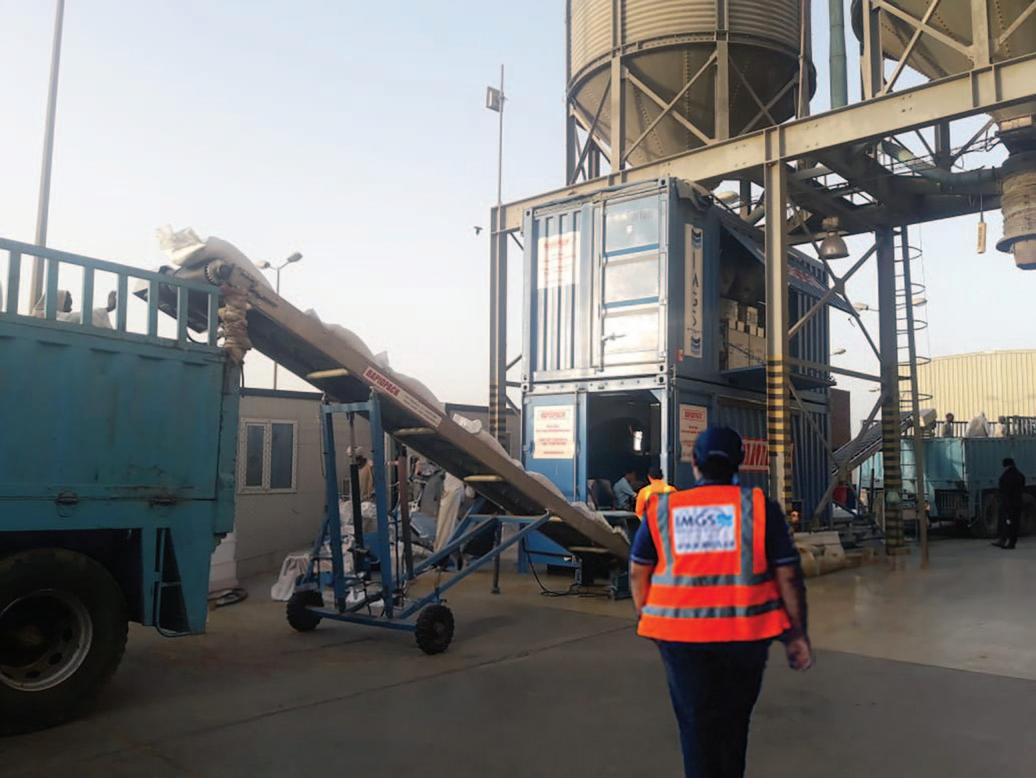
MAXIMIZE THE OUTPUT OF SILOS, MILLS AND GRAIN BINS
In East Africa, a bustling terminal faced a bagging dilemma. Its demand was soaring, but the facility couldn't keep up. And installing new bagging lines would be both time-consuming and costly.

Enter IMGS with its innovative solution — the Mobile Bagging Machine. Strategically positioned directly under the grain bins, each machine can bag 150 metric tonnes of cargo per hour. Equipped with two bagging lines, that’s a whopping 2,000 bags per hour. Constructed with high-grade steel and marine-grade materials, these Mobile Bagging Machines are engineered to withstand any conditions and round-the-clock (24hr) operations.
With the deployment of IMGS Mobile Bagging Machines, the terminal and silo facility didn’t merely double their bagging throughput — they quadrupled it.
Transporting, handling and storing rubber conveyor belts CONVEYING ADVICE
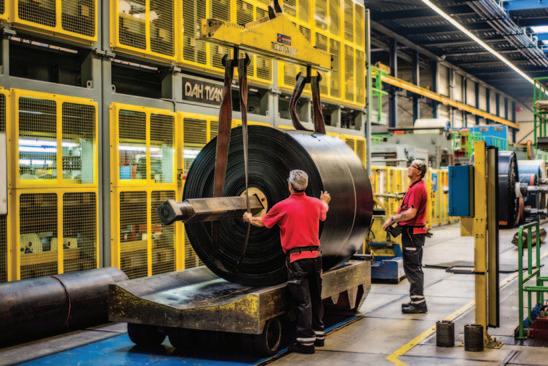
Safety: conveyor belts are packaged in rolls that can be of a considerable size and weight. It is therefore essential to maintain the highest safety standards and vigilance to avoid danger to human life and destruction of goods during their loading, transportation, unloading and storage. Before loading and unloading, always check that the protective packaging and handling elements integrated into the roll are not damaged and make sure that proper and adequate equipment is used throughout the process. For stability purposes, the height of a belt roll should not be higher than three times the width of the belt.
Transportation: despite their strong construction and durability, rubber conveyor belts can still be damaged during transit due to incorrect handling. At Dunlop, we help minimize the risk by providing one or more of four different kinds of hi-grade protective packaging for multi-ply belts — edge protection, plastic foil, wooden drums and steel reels. Very strong strapping is also used to prevent the belt from unrolling.
The belts are rolled using cores made of wood, steel or plastic with a square hole in the centre for mounting. The diameter of the reel and the hole for the core depends on the weight, width and physical properties of the rolled-up belt. The standard core sizes for both wood and plastic cores are 250mm with a shaft hole square of 110mm and 400mm with a draft hole square of 190mm. Before transportation the belt reel should be properly secured to avoid excessive movement caused by motion that could damage the vehicle, the belt or pose a health & safety risk.
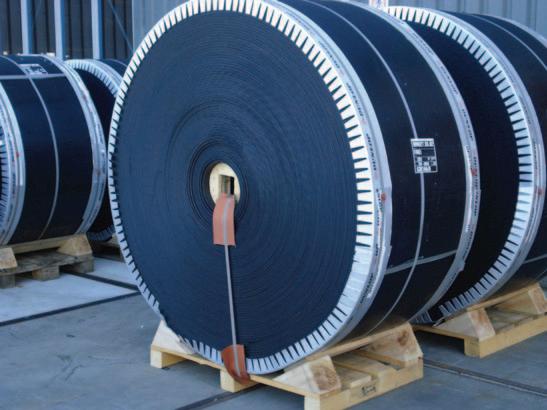
Lifting: the recommended method for lifting rolls is to insert a steel core of suitable size with a square cross-section through the reel centre hole. Slings, steel cables or chains suspended from a crane/hoist with beam should be used for fastening. The distance between the fastening points of the steel core sling should be longer than the width of the belt in order to avoid damage to the belt edges.
The manufacturer/supplier should always provide the dimensions and gross weight of each roll or drum and these should always be within the capacity of the equipment to be used to off-load and move the belt on site. When off-loading, always use skids, forklift truck or crane. Never drop the roll or roll it off the transporter.
Storage: there are a several factors that can have a detrimental effect on belting when stored. It is preferable that belts are stored in the manufacturer’s packing and in an upright position until required for use. Whether stored indoors or outdoors, the ideal storage temperature should be within the range of 10–20°C. Prolonged exposure to temperatures below 4°C or in excess of 30°C should be avoided. Although all Dunlop belts are fully resistant to the damaging effects of ground-level ozone and ultraviolet light, a great many belts on the market, especially those imported from Asia, have no resistance at all. Although packaging materials such as wooden drums, foil and cardboard do provide some protection, exposure to ozone, sunlight and/or fluorescent light is best avoided because it can begin to degrade rubber within a very short space of time.
Contact with all types of liquids, especially oils, solvents and corrosive liquids should also be avoided. It is recommended that belts stored outdoors be placed be on pallets and positioned on a solid, even surface so that they are not in contact with the ground in order to protect them against damage caused by water, mud, gravel, etc. Additionally, rolls should not stand on edge or lean against a wall.
Finally, it is advisable to rotate the belt 90° every 6 months to avoid a constant flex or bend at a single point. There is no need to do this with steelcord belts that are packed using steel reels which effectively suspend the belt in midair.
Les WilliamsChallenge your material limits
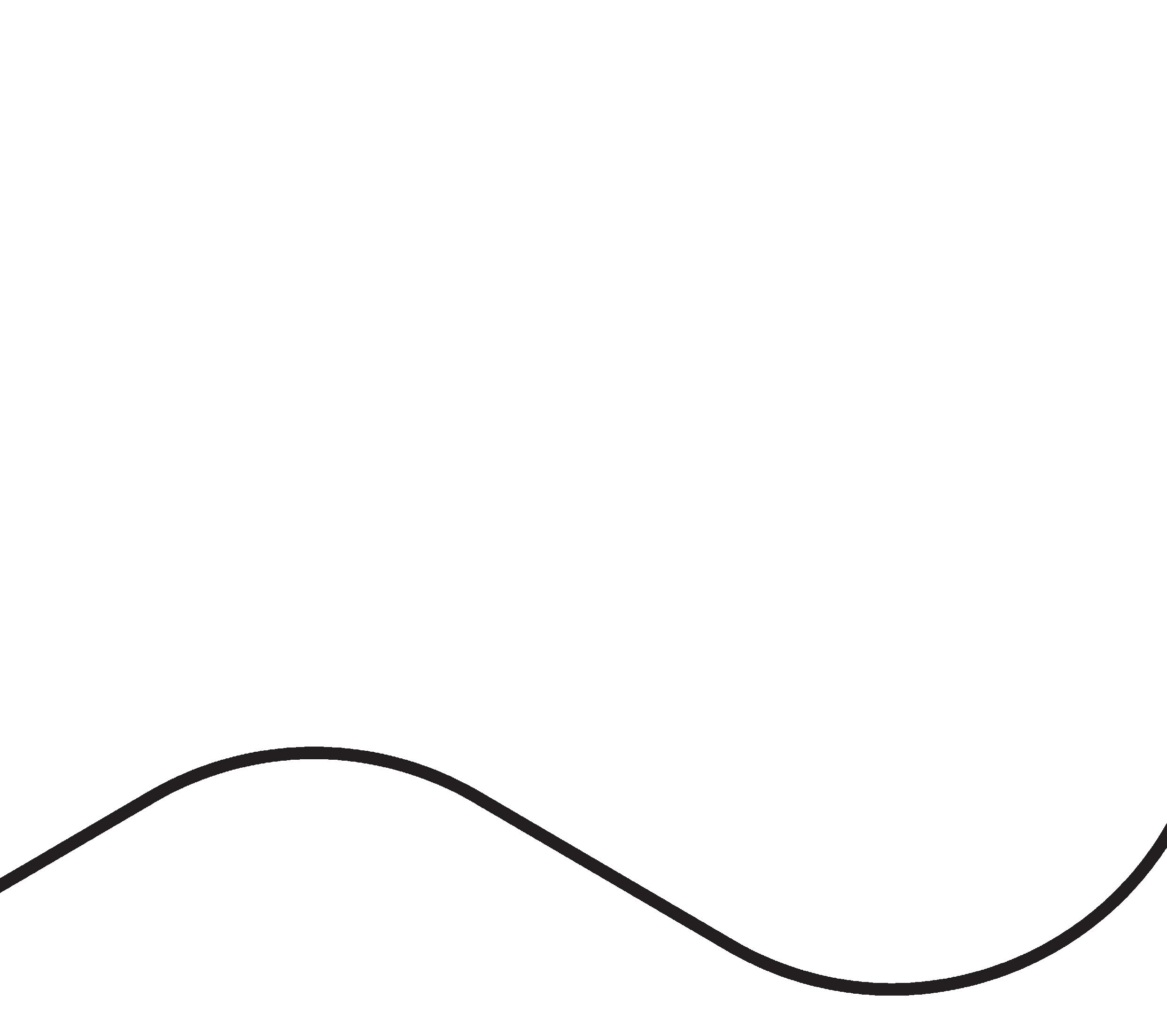
Nothing should stand in the way of your productivity – least of all the materials you move. With our compact Hägglunds direct drive systems, you can adapt easily to the job at hand, taking advantage of full torque at an infinite range of speeds. And should an overload try to stop you, the drives’ low moment of inertia and quick response will keep your machines protected. We’ll support you too, with an agile global network and smart connectivity to bring you peace of mind. Driven to the core.
Hägglunds is a brand of Rexroth. www.hagglunds.com
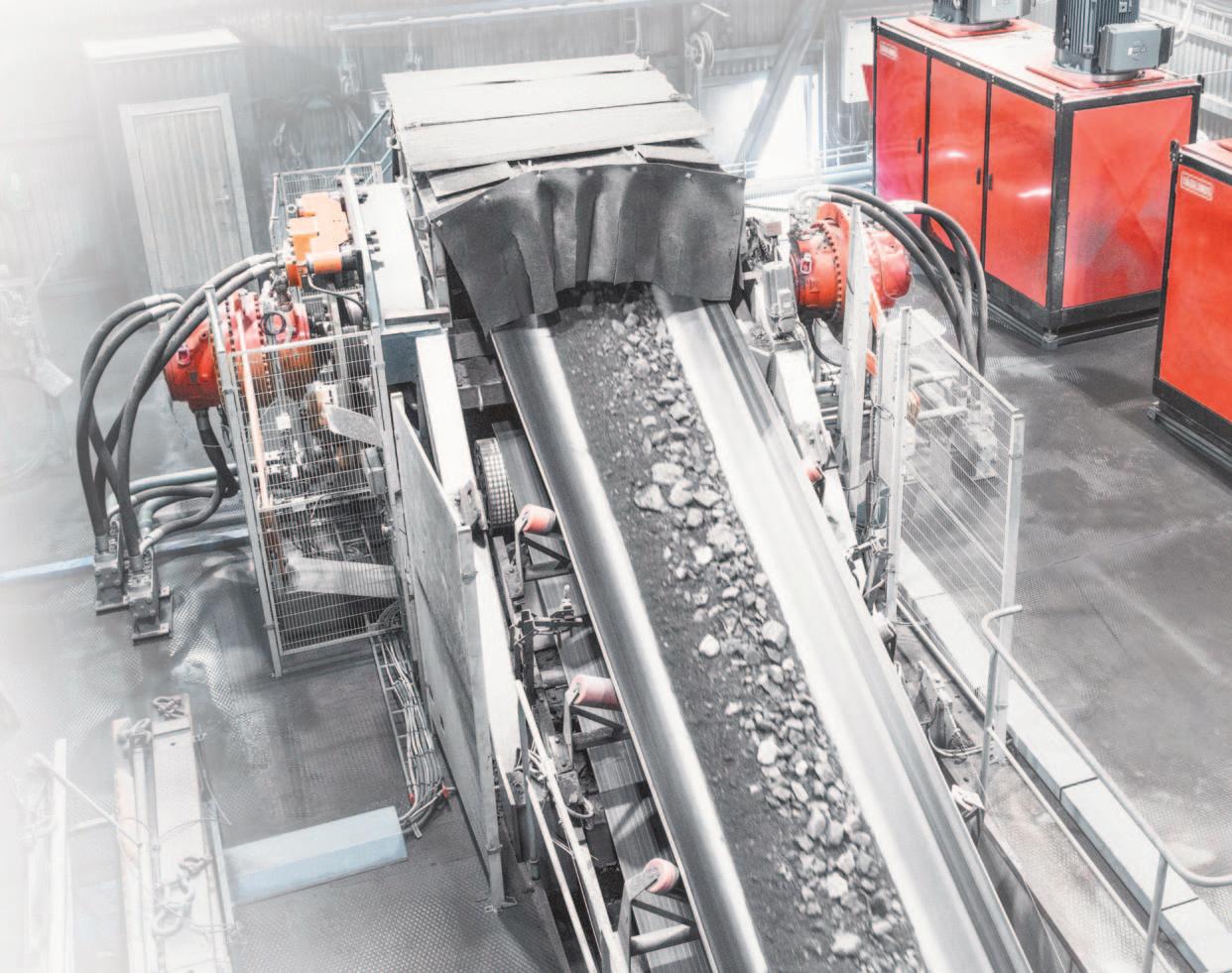
Elegant unloading with
VIGAN specializes in pneumatic ship-unloaders for gentle handling
VIGAN Engineering S.A., a global expert in bulk handling solutions, has been at the forefront of the industry for over 55 years. With its headquarters in Nivelles, Belgium, the company has established itself as a trusted provider of handling equipment for dry bulk products, primarily focusing on agricultural commodities such as cereals.
VIGAN’s extensive product portfolio includes pneumatic ship-unloaders, grain pumps, and turnkey solutions for complete port terminals. With an impressive 99% of its business exported, VIGAN has a strong global presence, with its equipment installed in ports around the world.
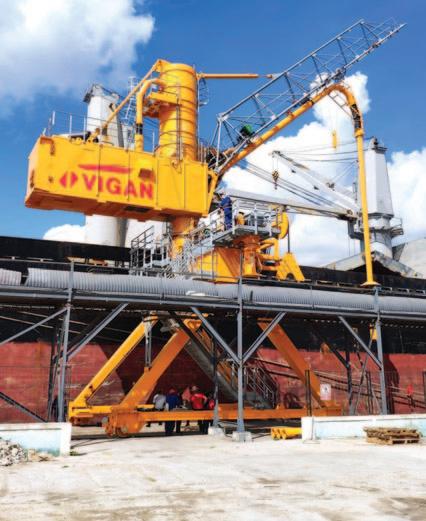
VIGAN’s commitment to innovation and customer satisfaction sets it apart in the industry. The company offers a range of equipment tailored to specific port requirements. Grain pumps, compact and mobile machines, offer exceptional efficiency with peak outputs of up to 250tph (tonnes per hour). These pumps
high-tech ship-unloaders
provide rapid implementation without the need for heavy mechanical handling investments. Additionally, VIGAN’s gantries, available in pneumatic and mechanical variants, cater to different capacity needs, with pneumatic gantries capable of reaching 800tph and mechanical gantries achieving throughputs of up to 1,500tph.
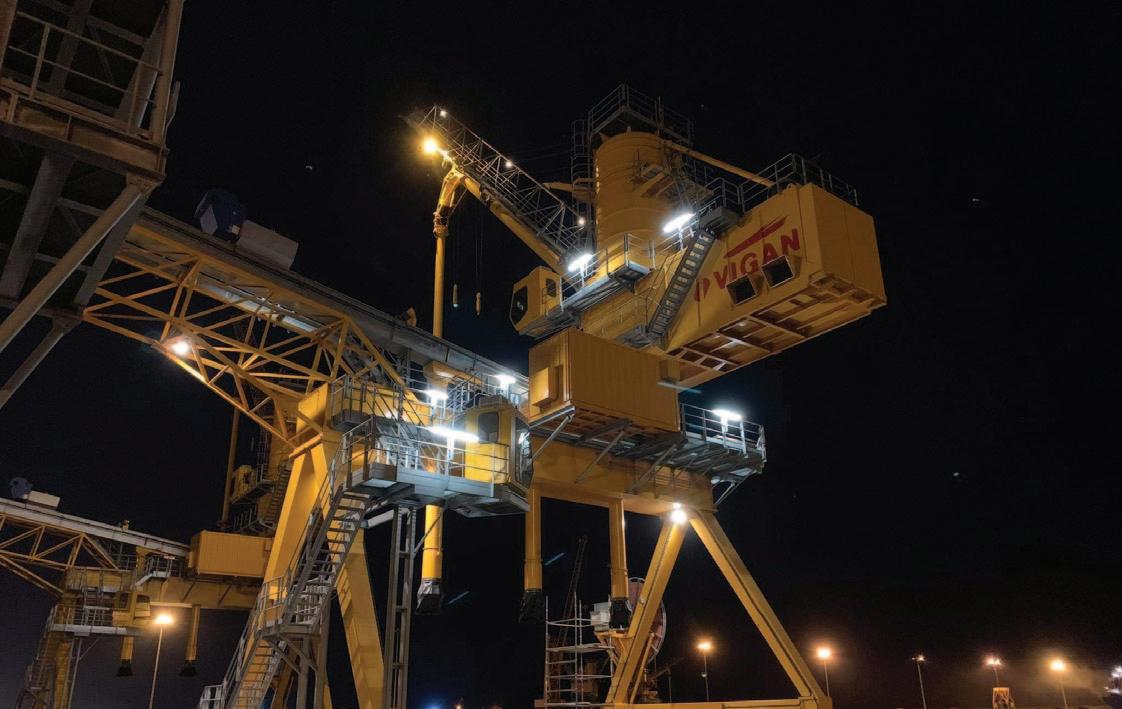
When it comes to customer priorities, VIGAN understands the significance of performance, energy efficiency, low noise levels, and ease of maintenance. The company consistently develops new technical solutions to meet these requirements while adapting to evolving industry demands. Notably,VIGAN has witnessed an increased emphasis on reducing dust emissions in recent years. With residential areas often encroaching industrial estates, VIGAN addresses this
concern with its pneumatic suction technology. Their systems, featuring hermetically sealed components and overpressure filters, keep dust emissions to a minimum, achieving or even surpassing emission levels of approximately 3mg/m3
Moreover, VIGAN recognizes the importance of noise reduction, particularly for port sites located in urban areas. By
employing meticulous acoustic calculations and targeting noise sources, the company ensures that its equipment operates within acceptable noise limits. Through insulation measures, including acoustic panels, soundoptimized exhaust systems, and concrete matrices for noise reduction, VIGAN achieves noise level reductions of up to 15 decibels, proving their commitment to acoustic excellence.
VIGAN’s key strengths lie in its vertical integration, robust technology, engineering and development capabilities, and customer-centric services. Unlike many competitors relying on subcontractors, VIGAN maintains complete control over quality and planning by designing, manufacturing, and assembling all aspects of its machines in-house. This approach ensures high-quality standards and timely deliveries. The company’s commitment to robust and proven technology guarantees reliable operation, even in challenging conditions. With ongoing engineering and development efforts, VIGAN continues to introduce new technical solutions that outperform the competition.
Customer satisfaction is paramount to VIGAN, and their comprehensive aftersales service, integrated with spare parts
sales, reflects this commitment. By offering flexible solutions, long-lasting components, and preventive maintenance programmes, VIGAN ensures that its machines operate at peak performance while minimizing the need for extensive technical expertise. The company maintains a strategic stock of spare parts to provide rapid assistance worldwide, even for machines from other brands.
In terms of recent innovations, VIGAN has focused on addressing noise-related challenges faced by port equipment operating in urban or environmentally sensitive areas. Through extensive research, calculations, and on-site

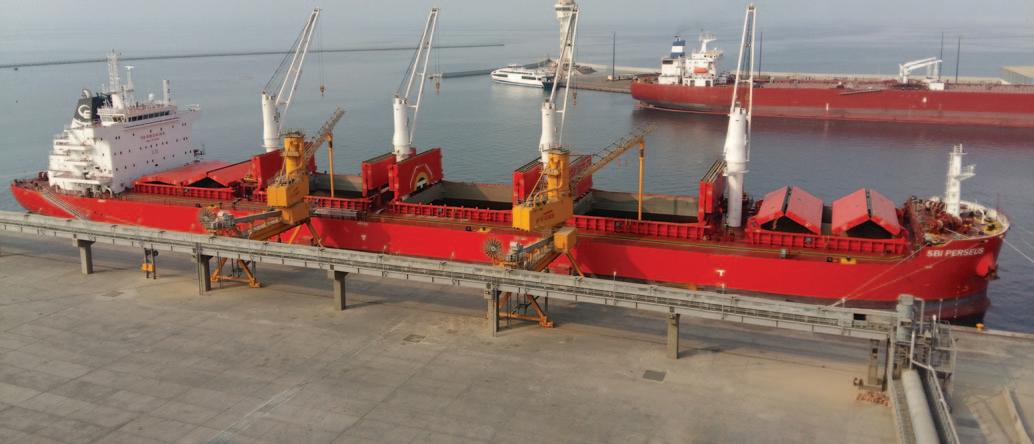
measurements, VIGAN has developed expertise in designing noise protection systems for turbo sets, machine rooms, suction pipes, and other components, enabling them to provide efficient and compliant solutions for their customers.
With a strong track record of delivering reliable, high-performance bulk handling equipment, VIGAN Engineering S.A. continues to drive innovation and set new industry standards. Their unwavering commitment to customer satisfaction, combined with their technological prowess and extensive experience, positions them as a leading force in the global bulk handling industry.
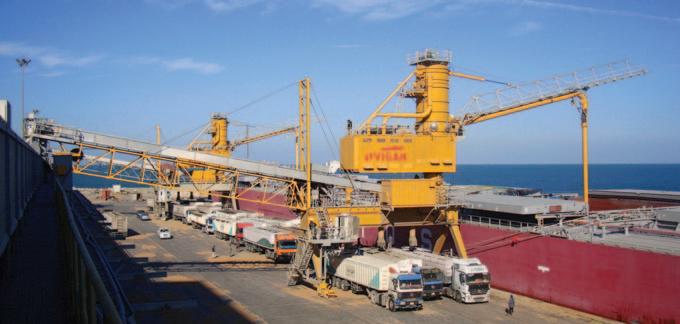
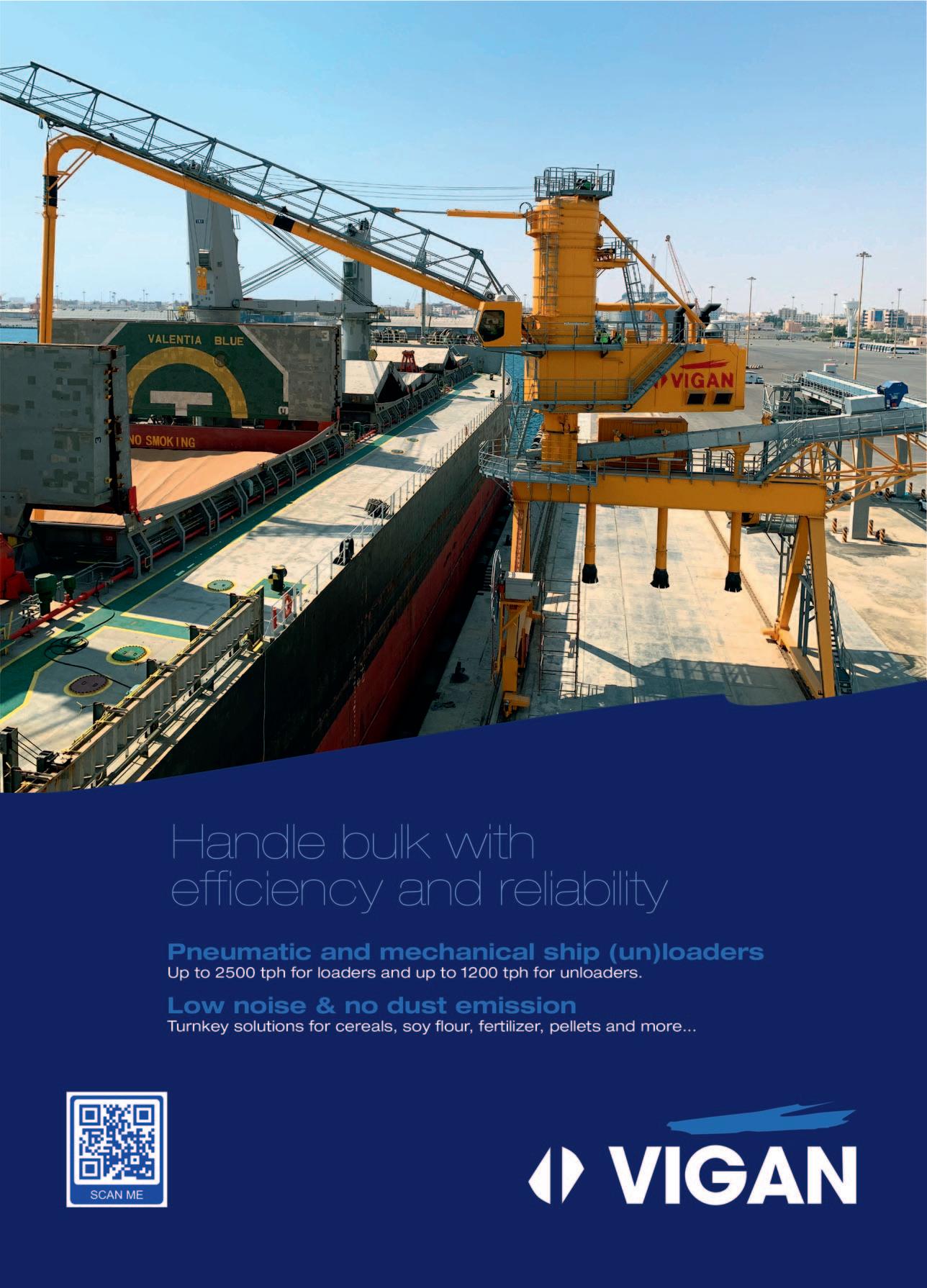
The yellow port workers: reliability when it counts
STAYING COOL IN THE IMPORTANT SITUATIONS
Stormy weather, a wet environment and the screaming of seagulls in the background form the backdrop for inconspicuous but extremely important equipment at a shipunloading site: the belt misalignment switches. Golden yellow, but usually dusty and unimpressive, always positioned in pairs to the right and left of the conveyor edge and rarely in action, they can be spotted on most conveyor belts, not only those of ship-unloaders.
WHAT DO THESE YELLOW SWITCHES DO ON THE CONVEYOR?
Ship-unloaders are always in use in ports to supply us all with goods from all over the world. Behind each ship-unloader is a smart transport logistics system which works to minimize the ships’ lay times as much as possible. Loading and unloading must be fast and trouble-free, because time is money. Large volumes of bulk cargo, such as coal, ores, gravel, grain, fertilizers or other bulk cargoes are transported by the unloader on conveyor belts to other transshipment points or storage locations at the port facility, where they can be transferred to rail or truck.
During loading or unloading, unevenly distributed material on the conveyor belt can cause the conveyor belt to leave its
intended path and drift outward during operation. A belt misalignment occurs. Undetected belt misalignment almost always leads to major consequential damage to the system, which is associated with high repair and logistical follow-up costs, up to and including total system failure. This is because the belts, which move at the speed of the conveyor belt, are reinforced by fabric or steel mesh like a car tyre in order to transport volumes of great weight. Their edges then act like the cutting blade of a band saw, making their way through the conveyor belt system or becoming damaged and requiring replacement.
Anyone who has ever had to buy a set of car tyres will understand that a few hundred dollars is not going to get you by on such conveyor belt repairs.
Economically minded operators, therefore, place special emphasis on good belt monitoring and purchase their equipment from conveying system manufacturers who provide design safeguards against misalignment. This is because cheap purchases can have drastic economic consequences in later operation.
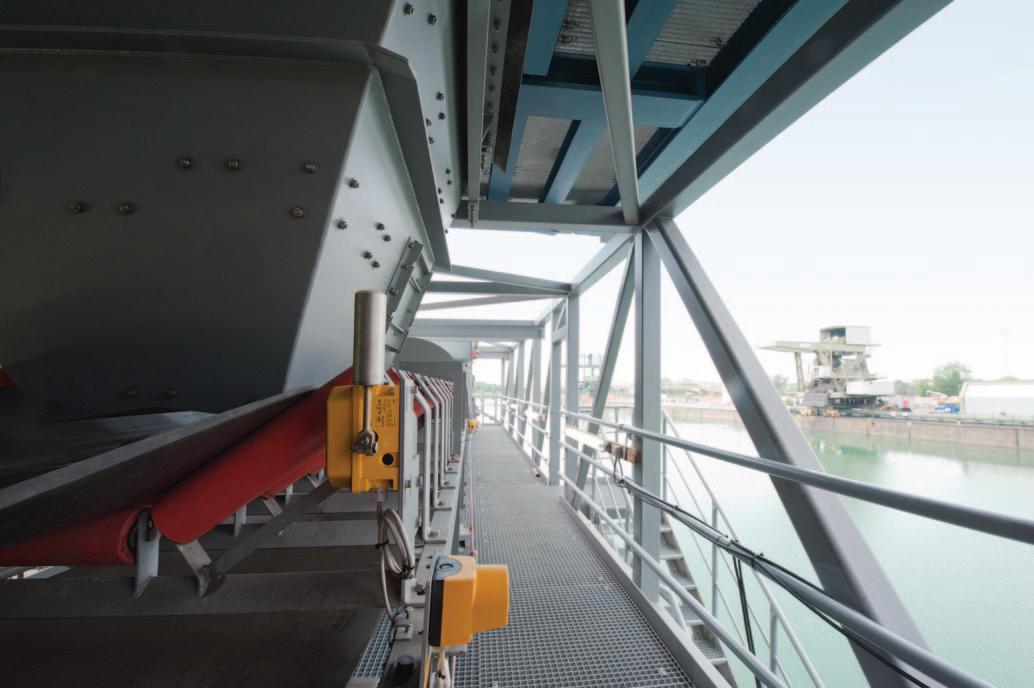
MURPHY’S LAW?!
Murphy’s law: ‘Anything that can go wrong will go wrong’. Even the best design protection measures cannot cover all safety
Kiepe misalignment switches
Kiepe Electric has its headquarters in Düsseldorf. There, these misalignment switches have been developed, manufactured and sold worldwide for more than 60 years. These robust devices have a proven track record of providing service for many decades. Their reliability is established by highquality materials, the construction as well as highly-trained personnel and 100% testing before leaving the production plant in Düsseldorf. A worldwide sales network additionally supports Kiepe customers locally in their tasks to find the right components for their application purposes.
risks that lead to misalignment over the entire service life of a conveyor system. In that case, it is a good idea to use a belt misalignment switch as a supplementary protective measure that watches over the conveyor belt. Here, the small, yellow port worker — the belt misalignment switch — must work reliably.
To guarantee reliability, the belt

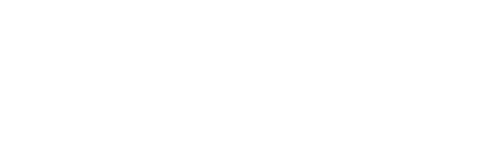

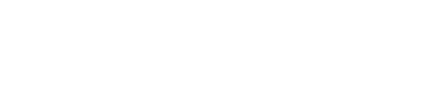
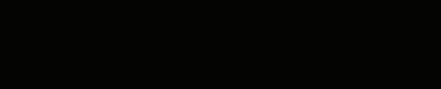
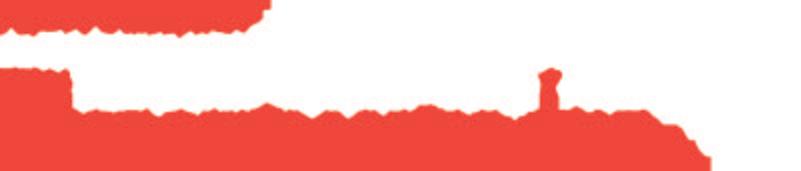

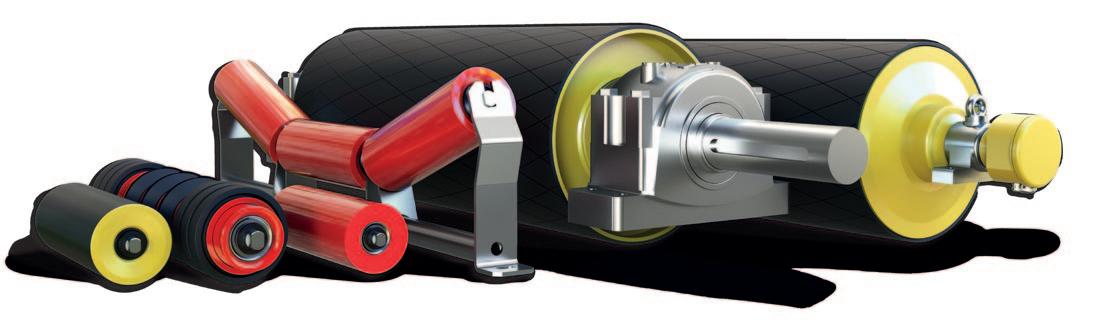
misalignment switches are positioned in pairs at the critical points where misalignment is potentially likely, e.g. at the loading and unloading points, or in curved positions of the conveyor belt. These helpers thus significantly reduce the risk of consequential damage due to belt misalignment.

HOW DOES A BELT MISALIGNMENT SWITCH WORK?




The belt misalignment switch shown in the photo on p42 (Figure 1), made by Kiepe Electric GmbH, is a robust, electromechanical position switch. It is equipped with switching contacts that can be used to signal a control system or contactor.
The roller lever of the belt misalignment switch does not touch the belt edge during normal operation of the conveyor belt. The roller lever of the belt misalignment switch does not touch the belt edge during normal operation (Figure 2, above) of the conveyor belt. Only in the event of belt misalignment is the roller lever contacted by the belt edge and deflected (Figure 2, below). After the belt misalignment, the roller lever of the switch automatically returns to its initial position.
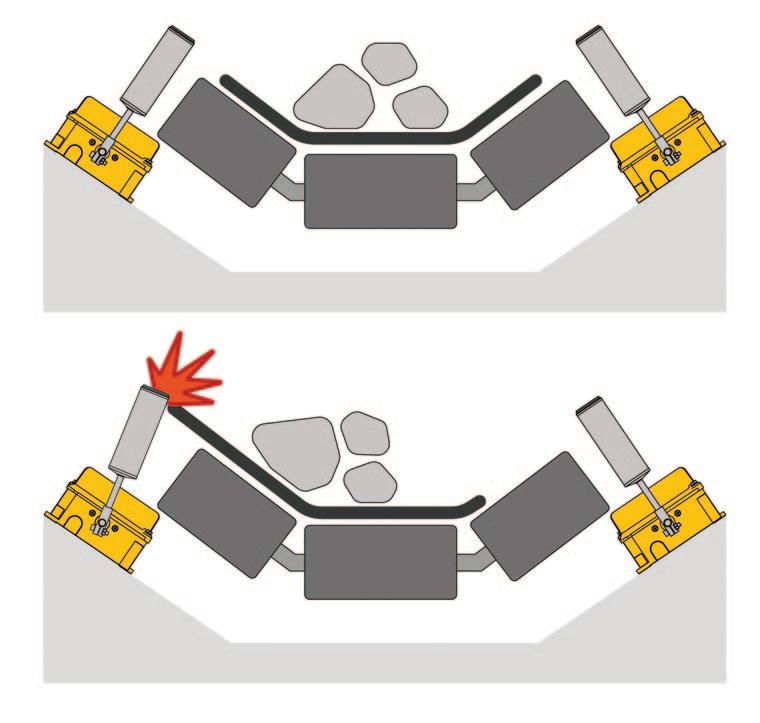
The switching points of the switch depend on which angles are predetermined by the switch design or can be adjusted. The switching points of the shown misalignment switch can be individually adjusted by means of adjustable cam rollers. Thus, a signal for pre-warning and a signal for switch-off can be sent. The special function of the adjustable angle helps to compensate for tolerances during commissioning, maintenance and servicing of the systems and to better adapt the switching points to the ambient conditions without having to set up complex adapter plates for the belt misalignment switches. Nevertheless, there are also less expensive variants where the switching angles are predefined.
WHAT IS THE SIGNIFICANCE OF THE ROLLER LEVER?

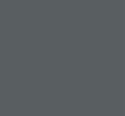



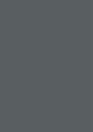
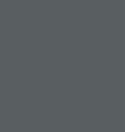


The roller lever is touched by the edge of the conveyor belt at full belt speed in the event of misalignment and is deflected slowly at a 90° angle. High-quality rollers of roller levers as shown are therefore protected by design measures against wear, friction and corrosion.







The roller circumference determines which edge defect can be tolerated or compensated for by the misalignment switch. If the diameter of the roller were to fit completely into an edge defect, the roller lever would immediately be carried away during operation and possibly also cause damage to the switch. This, in turn, generates maintenance costs, which must be avoided.
THE BOTTOM LINE



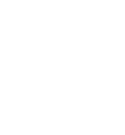









Belt misalignment switches are suitable for many different conveyor belts, not only for ship unloaders. As a supplementary protective measure, they are indispensable ‘port workers’ to safeguard against machine damage. High-quality processed belt misalignment switches are investments in a long service life, reliability and remain cool even if something goes wrong. Only when something goes wrong do you recognize their true value.

indurad technology makes shipunloading safer and more efficient
INDURAD REMAINS A KEY PLAYER IN COLLISION AVOIDANCE , OPERATOR ASSISTANCE AND AUTOMATION OF CONTINUOUS SHIP-UNLOADERS
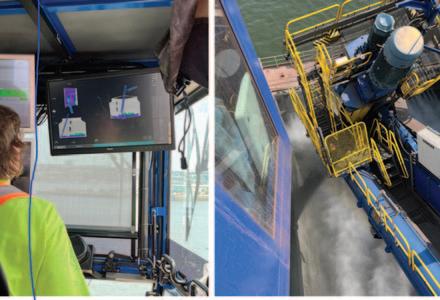
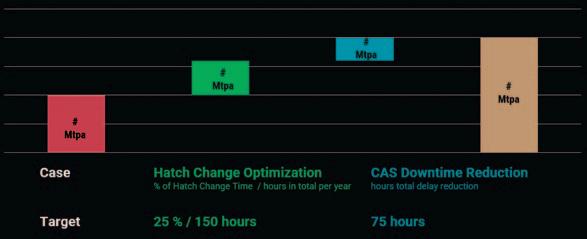
indurad develops and manufactures 1D, 2D and 3D radar sensors in Germany and provides full solutions for collision avoidance, operator assistance and automation for continuous shipunloaders. Through its local sales and service hubs in Australia, South Africa, Kazakhstan, Brazil, Chile and Canada. it addresses medium- and large-size (loading) and unloading operations for various commodities. In the last six months, projects in alumina and nickel bulk unloading have been completed in North America. The projects consist of several layers, with the collision avoidance being the base layer. indurad provides contactless anti-collision systems for all parts of the ship-unloader, including the vertical boom and the unloading instrument.
The second layer is typically a system that utilizes 3D radars to detect the hatch and the cargo inside the hold. This allows for easier manual operation as the radar penetrates dust and operates in harsh conditions, even when optical systems such as laser and lidar cannot provide meaningful data. It also allows remote control of machine during the entire unloading process.
As the system detects the hatches and the material, automation processes can be implemented relatively easily. Whether automated or remotely controlled, the indurad system ensures an efficient and homogeneous unloading process.
An indurad customer, who implemented an indurad system for collision avoidance and operator assistance in March this year, writes: “The collision avoidance system has been in operation for eight months. It has proven effective in reducing collisions between our unloader and the ship’s hatch covers and cranes.
We have found that the indurad 3D vision technology: Identifies the hatch opening and tracks it while the ship moves on its lines and with the tide: it provides an accurate image
v of the cargo in the hold;
generates an accurate image of the unloading equipment as it moves in the hold: we utilize computer-generated image videos v as a training tool to educate operators on effective unloading techniques and improving efficiency; by leveraging the 3D images from the indurad system, we expect our operators to optimize the unloading equipment’s v capacity and significantly reduce unloading times.”
“indurad is elevating unloading operations into the 21st century by adding radar-based perception systems to existing operations as well as new unloaders,” states Christian Augustin, Managing Director of indurad “which ultimately reduces the time it takes to unload a ship.” One customer could reduce 225 hours of unproductive time during unloading operation in the first year. A North American customer handling large amounts of nickel could unlock the following advantages: better utilization of the capacity of the equipment (being able to see where the cargo is); v improvement in cargo unloading in a manner (keeping the top of the cargo level) that further minimizes potential dust v emissions, complementing the multiple dust mitigation systems currently in use; and the minimization of the chance of the unloader colliding with the ship (providing information to interlock machine v movement).
indurad just started to roll out the solutions to other customers, both in loading and unloading and is looking forward to a great future: “indurad's USP is certainly the 2D and 3D radar technology, which is perfect for harsh environments — making it the technology of choice for bulk loading and unloading operations. It is no surprise that the marine industry uses radar technology for navigation — and so do we. It took us a couple of years to develop this technology and the necessary software packages, but the last year with several installations has proven the market acceptance and high value for our customers to achieve their individual goals — may it be to reduce berthing time, reduce emissions or to take the operator out of hazardous environments. The indurad team is very proud of what we have archived so far,” concludes Augustin.
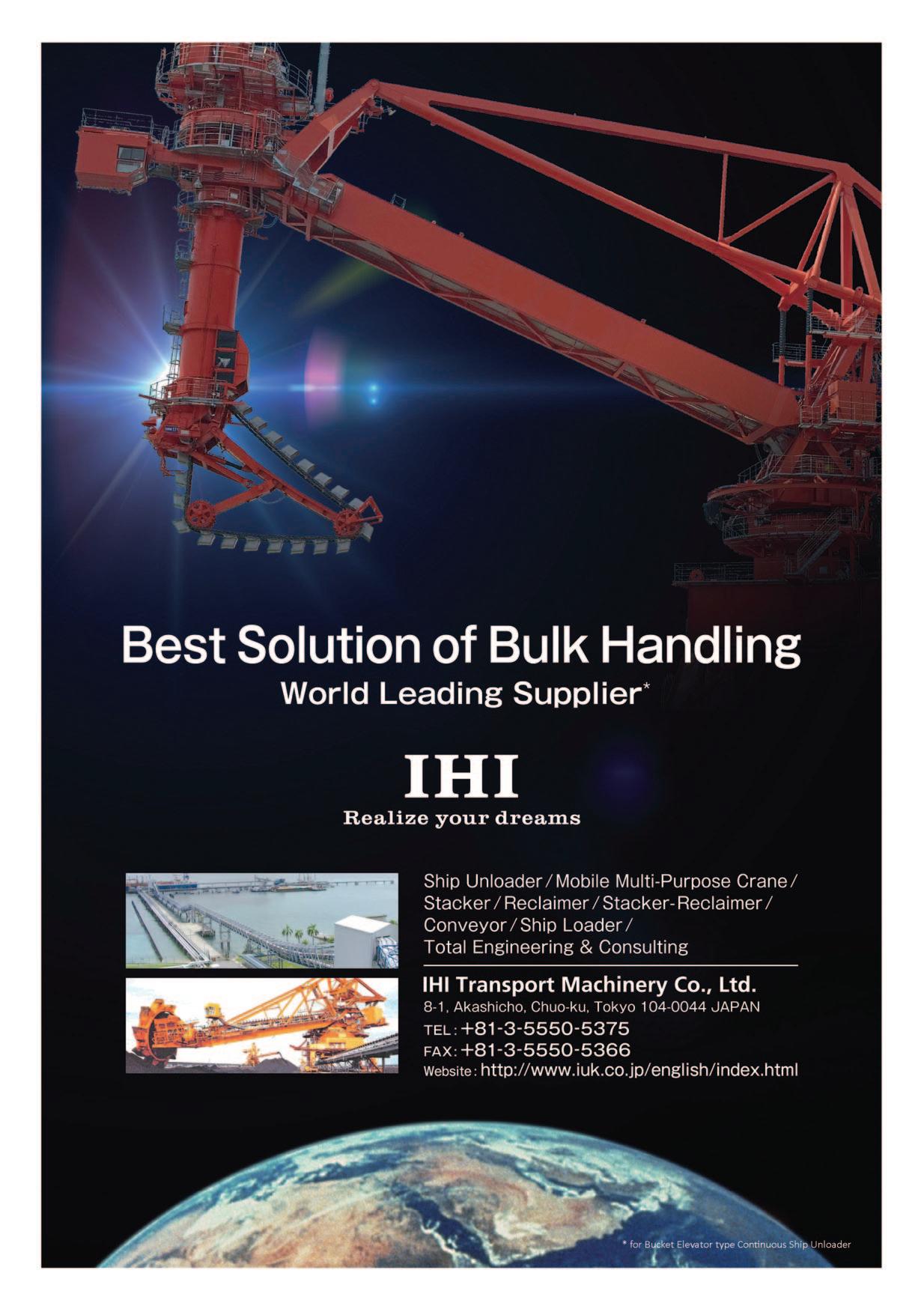
Bruks Siwertell adopts augmented reality in advanced service provision
Bruks Siwertell has introduced the use of augmented reality (AR) into its planned service agreements for Siwertell roadmobile ship-unloaders. The AR glasses allow operators to remotely connect with expert service support, enabling surveyors to have a direct visual link to equipment. This ensures that technical issues can be addressed even more quickly, along with streamlining communications.
“This latest advance is part of Bruks Siwertell’s ongoing commitment to improving customer service, and minimizing environmental impact through the use of digital technology,” says Jörgen Ojeda, Sales Director Mobile Unloaders, Bruks Siwertell.
“Planned service is always better than reactive,” continues Ojeda. “Siwertell Care agreements (STC) offer significant customer benefits, including maintaining peak operational performance, substantial cost savings and budgeting advantages. The
addition of AR only adds to these advantages.
“If both parties can see exactly the same in real-time, issues can be resolved much faster and equipment downtime minimized. The number and cost of engineer call-outs can also be reduced,” adds Ojeda. “This delivers an additional environmental benefit from minimizing travel and ensures that parts are not replaced unnecessarily.”
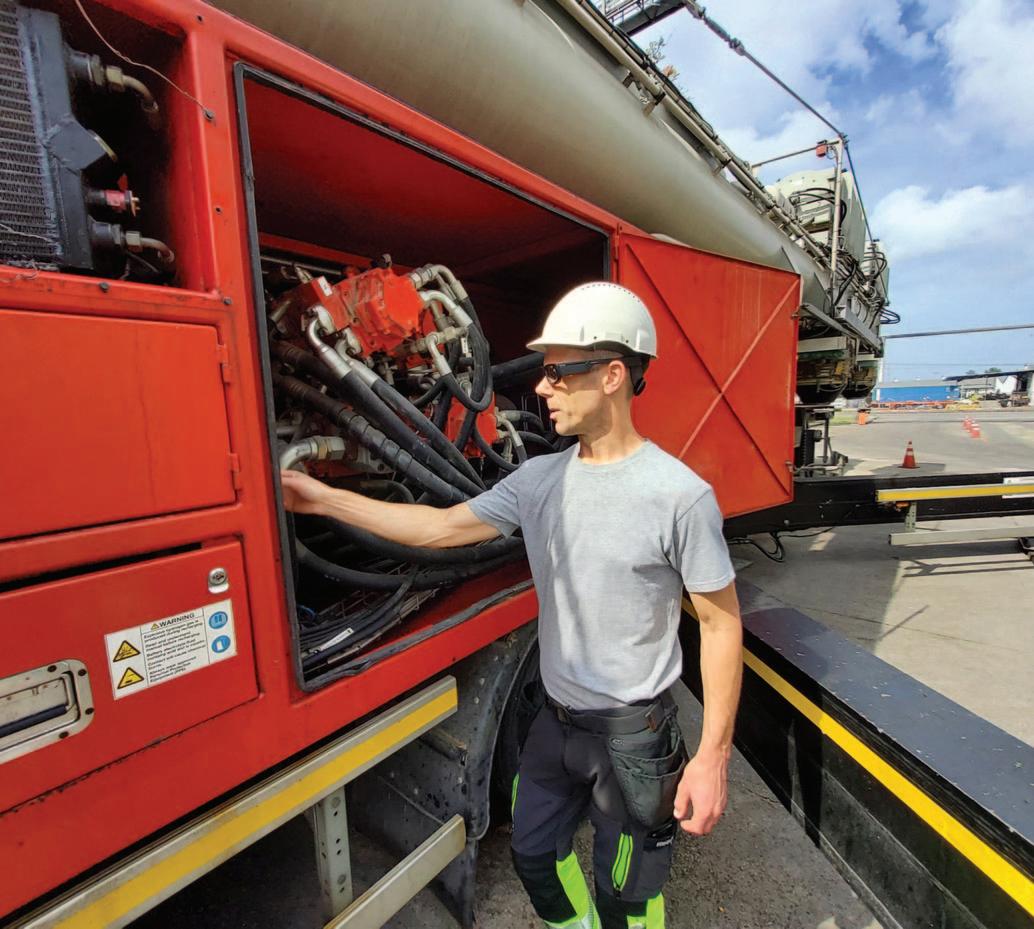
Specialist service agreements provide regular mechanical, hydraulic and electrical inspections; ongoing operator and maintenance training, based on in-house, expert knowledge; fixed-cost agreement for the required number of planned visits; and a spare parts discount.
In addition to these benefits, when customers opt for an STC-AR agreement, AR glasses can be used to remotely supervise any work being carried out, which can speed up tasks and ensure that they are correctly performed. The use of
AR glasses can also mean that more complex maintenance tasks can be undertaken in-house and the operational performance of equipment can be evaluated and discussed in real-time.
STC-AR agreements are currently available for Siwertell road-mobile ship unloaders.
ABOUT BRUKS SIWERTELL
Bruks Siwertell is a market-leading supplier of dry bulk handling and wood processing systems. The company designs, produces and delivers systems for loading, unloading, conveying, storing, and stacking and reclaiming dry bulk materials, alongside equipment for chipping, screening, milling and processing wood for the biofuel, board, saw mill, pulp and paper industries. All equipment is designed to ensure environmentally-friendly and efficient operations.
SAMSON Material Handling’s Eco-Hopper offers a major advantage in safe ship-unloading operations
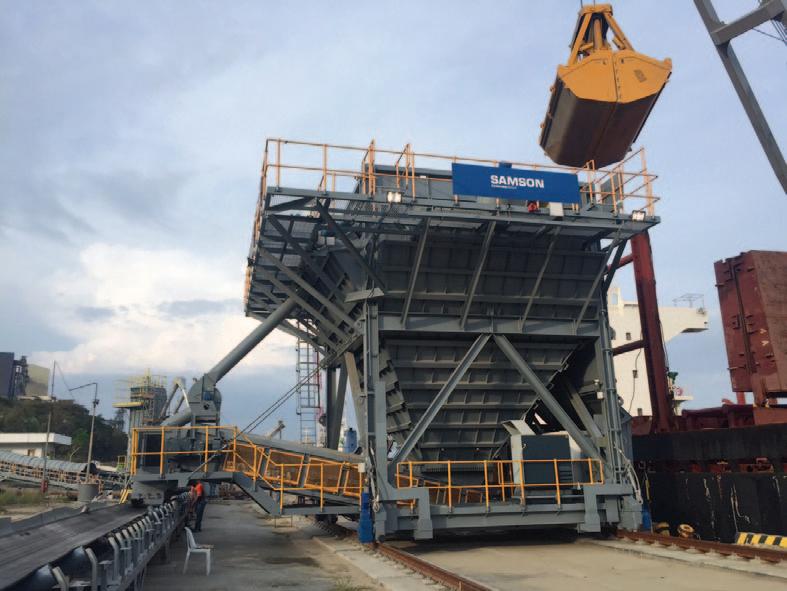
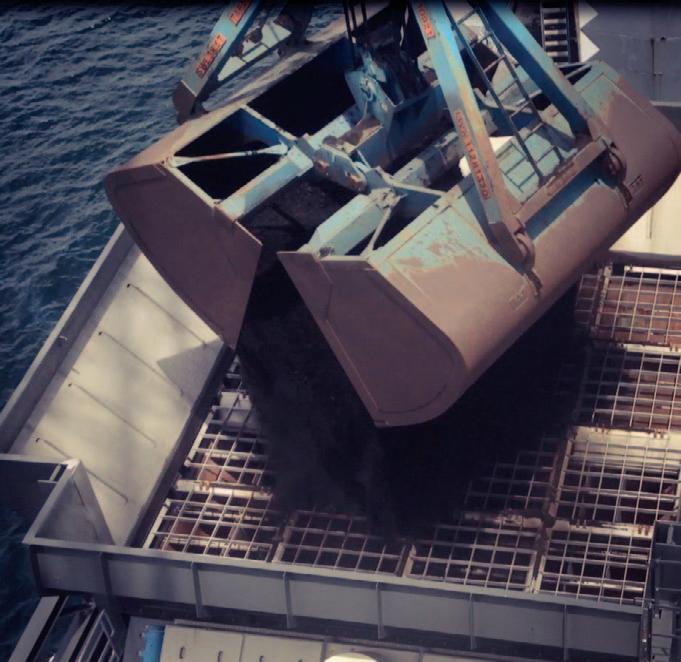
INTRODUCTION
In the age of automation and decarbonization via strict environmental policy shifts, solutions and investments turn a wide opened eye towards long-term sustainable equipment, writes Petar Karaivanov, SAMSON Materials Handling. Whether that is on a currently developing quay or a system that has been operational for some time, port operators and end users are exploring new and innovative ways to tackle the challenge of ship-unloading and the currently available systems.
The principle and purpose of these ship-unloading systems have been the same of over a century — to unload or import bulk materials from a vessel to shore as fast and as efficiently as possible. But how the game has changed over the past 100 years is a remarkable feat of engineering, creative thinking and challengers of the game. The speed and capacity of modern grab cranes for example has increased many times from their original design and, in order to keep
pace with that, so has the capacity of the unloading systems.
UNLOADING SYSTEMS IN AN EVER- CHANGING WORLD
While there are many ship-unloading systems for efficient unloading of bulk
materials and every system is based on innovative and powerful technology, the market demand has reached a peak era of different requirements. SAMSON Materials
Handling, part of AUMUND Group, offers a particular system that has stood the test of time — the mobile Eco-Hopper. This is a cost-effective and environmentally friendly solution for efficient intake of dry bulk materials via the ship-unloading process. This is a solution that fulfils all needs for the efficient import of dry bulk cargoes. The hoppers are designed to suit the characteristics and flow properties of virtually any bulk material. Rates of 5,000 tonnes per hour may be achieved, subject to grab crane performance. The throughput of the terminal can be increased by adding one or more hoppers, and ensuring that onward handling systems can accommodate the increased capacity.
The more fundamental functions and characteristics include:
some of the most intricate and state- v of-the-art dust control features (flex flaps, dust seals, dust control filters, air compressor);
multiple discharge options: to v conveyor, to truck, via telescopic chute, through ancillary material feeder;
multiple travel options: rail, static or v pneumatic tyre mounted, or powered and towable travel;
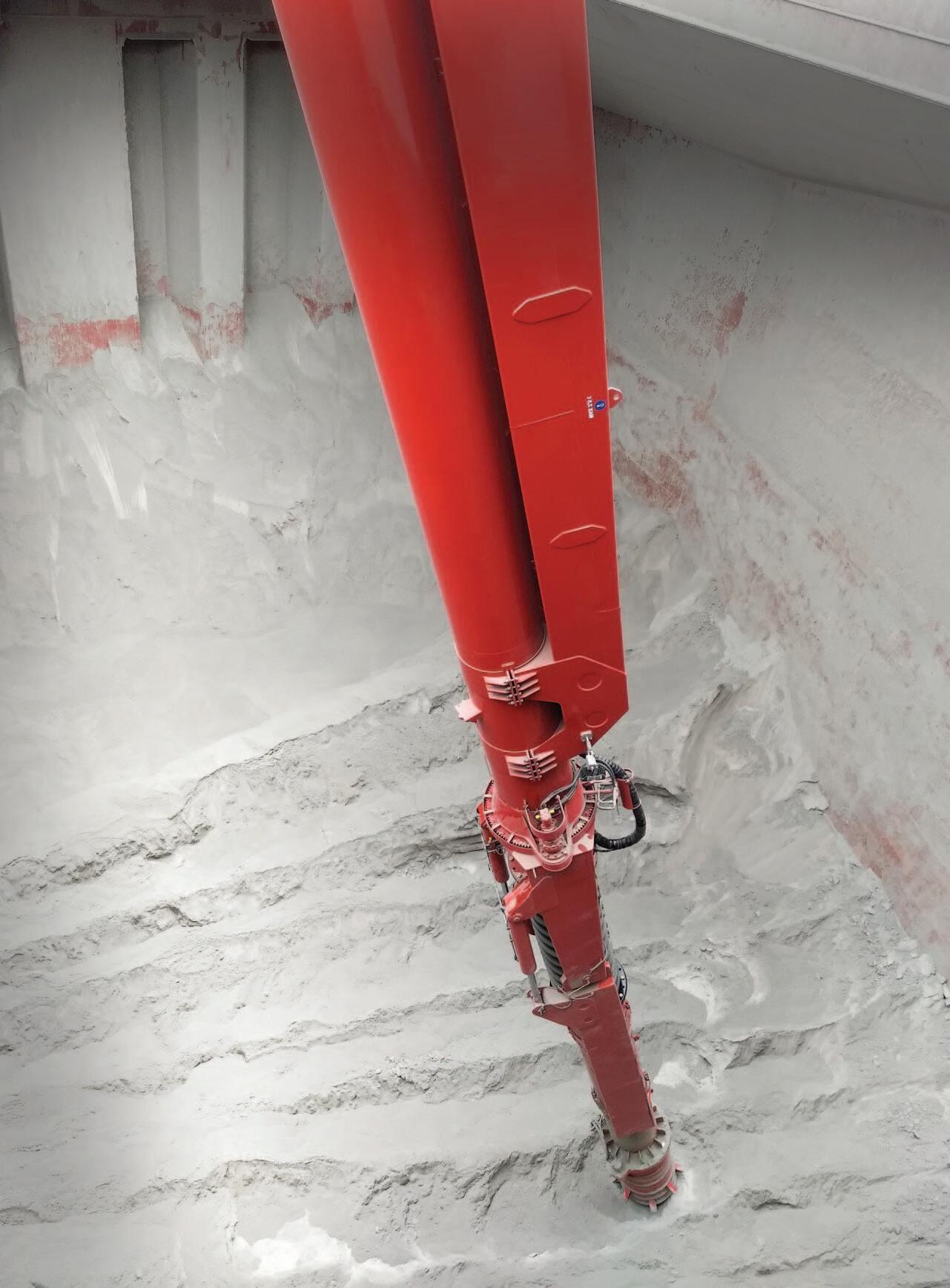
increased safety features (level v detectors, strain gauges, structural design to withstand overload to top of skirt); and a robust design (top shroud, grab v impact grill).
Some of the most notable benefits included in such a system include: minimizing fugitive dust; v being adaptable to a range of onwards v processing or logistics requirements; the ability to be used on non- v dedicated quays and moved off the
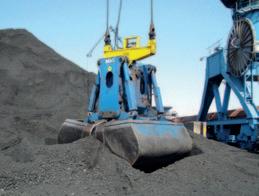
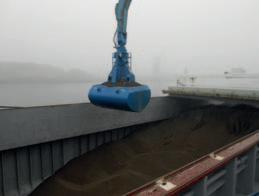
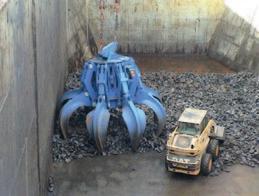
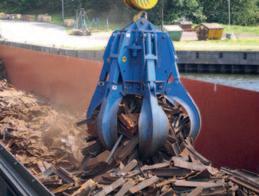

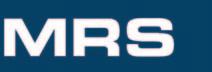


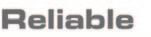


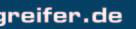
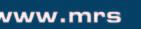


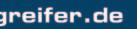

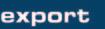
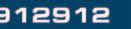






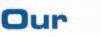





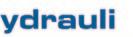








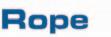
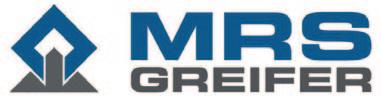
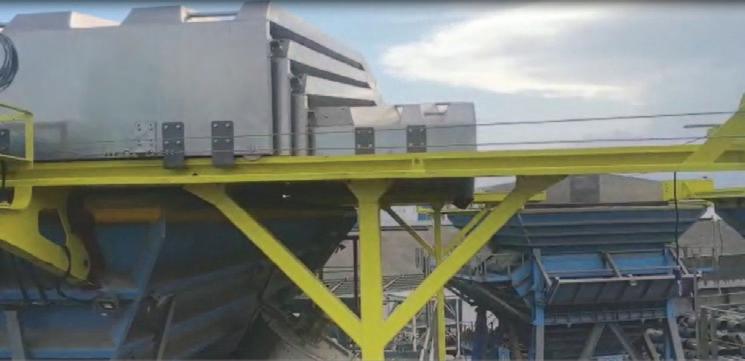
area when not in use; flexible positioning to suit unloading v vessel; and the ability to work with a wide variety v of materials with differing characteristics.
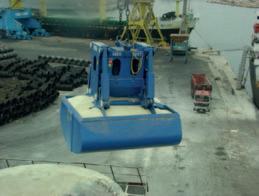



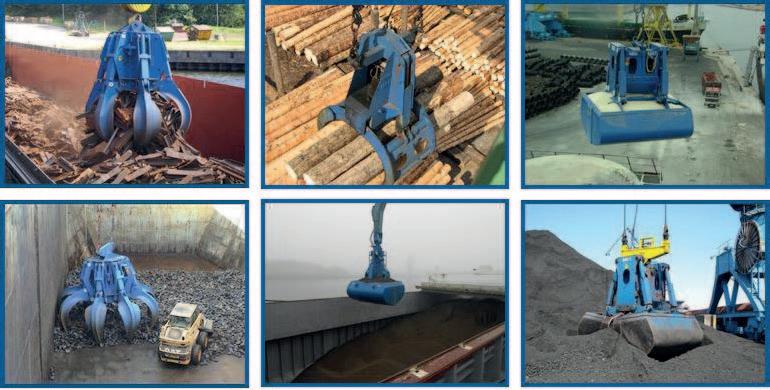
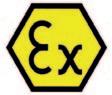
Furthermore, this type of equipment incorporates a low ground pressure design, ground level maintenance, enhanced mobility and controls and remote access for harvesting performance update information. The remote access for harvesting
information software is a particularly notable benefit for maintenance managers and bulk terminal operators. It allows for continuous automated feed of information about the overall state of the machine and in this way reduces the downtime needed when performing maintenance. It is a feature that has captured the attention of many industries worldwide and ports and terminals being one of the largest industries has rightly adapted to this new feature.
CONCLUSION


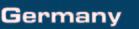

The implications and categories of these systems depend largely on the operations they will be channelled to support. For example, reduced total cost of ownership and lowest operating costs, ecological sensitivity to dust and noise, weights and dimensions, operating on a non-dedicated quay and easily transported out of the way when not in use (only for non-dedicated small multipurpose quays), flexibility in the unloading of different types of materials, and a more recent trend that has emerged is the possibility of carrying out unloading operations in adverse weather.

High performance winches and slewing gears from Zollern
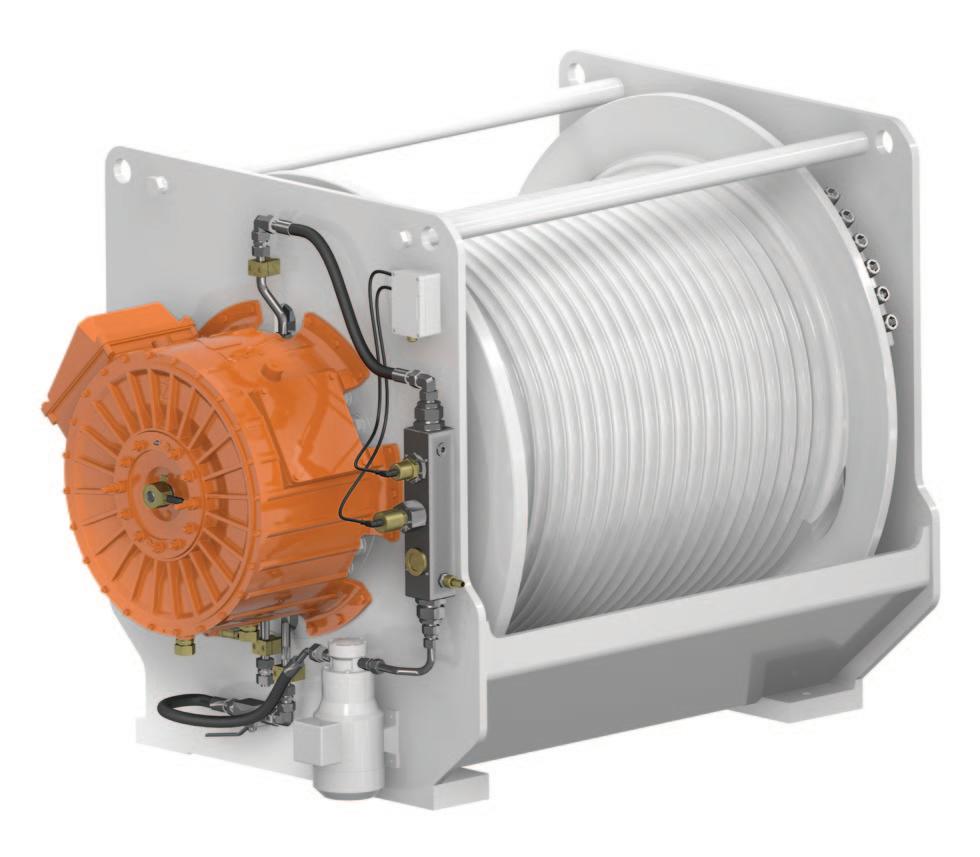
For shiploading and unloading the gearboxes and winches from drive technology specialist Zollern are used in applications such as mobile harbour cranes, straddle carriers and handling cranes for container in harbours and on ships.
They also work reliably and efficiently in heavy lift cranes, bulk material handling cranes and in handling technology for raw materials for shiploaders. Further maritime-related applications are dredging vessels, knuckle boom cranes, podded drives and jack-up systems.
By now, around 70% of these applications are hydraulically driven, and 30% are electrically driven. However, following the trend of electrification, the share with electrical input drive is on the rise. For high-end gearboxes, permanent magnetic motors become increasingly relevant, especially when limited space, energy efficiency or green energy ask for compact, emission-free drive solutions.
Zollern is a pioneer in integrated electrical drive systems. In addition to the trusted and proven planetary gearboxes, the newest technology permanent magnetic motors are manufactured and supplied by the international company. Premium customtailored drive systems with a minimum of interfaces, highest efficiency and reliability are tangible benefits for the customers. With the condition monitoring system Zollern Drive Guard, the drive system can be monitored from any location around the world at any time.
Zollern has been producing planetary gears for more than 50 years. Starting with planetary gearbox production in 1972, the drive portfolio based on planetary gear-boxes comprises a whole range of slewing gears and winches for various applications, markets and customers. The drive technology division of the company also offers electric motors, hydrostatic bearing systems and handling systems.
Compact dimensions, high performance and functional design characterizes the gearboxes and winches.
SHIPUNLOADING & WAREHOUSE STACKING SOLUTIONS
Customised two-part ship unloading intake and stacking system for cement clinker application.
•Eliminate double handling of material with no trucks/wheel loaders.
•Increased unloading rates with reduced operational costs.
•Utilise full potential of warehouse storage areas.
•Reduce dust emissions with comprehensive range of dust management options.
•Multi-functionality of equipment opens up other markets for client’s jetty.
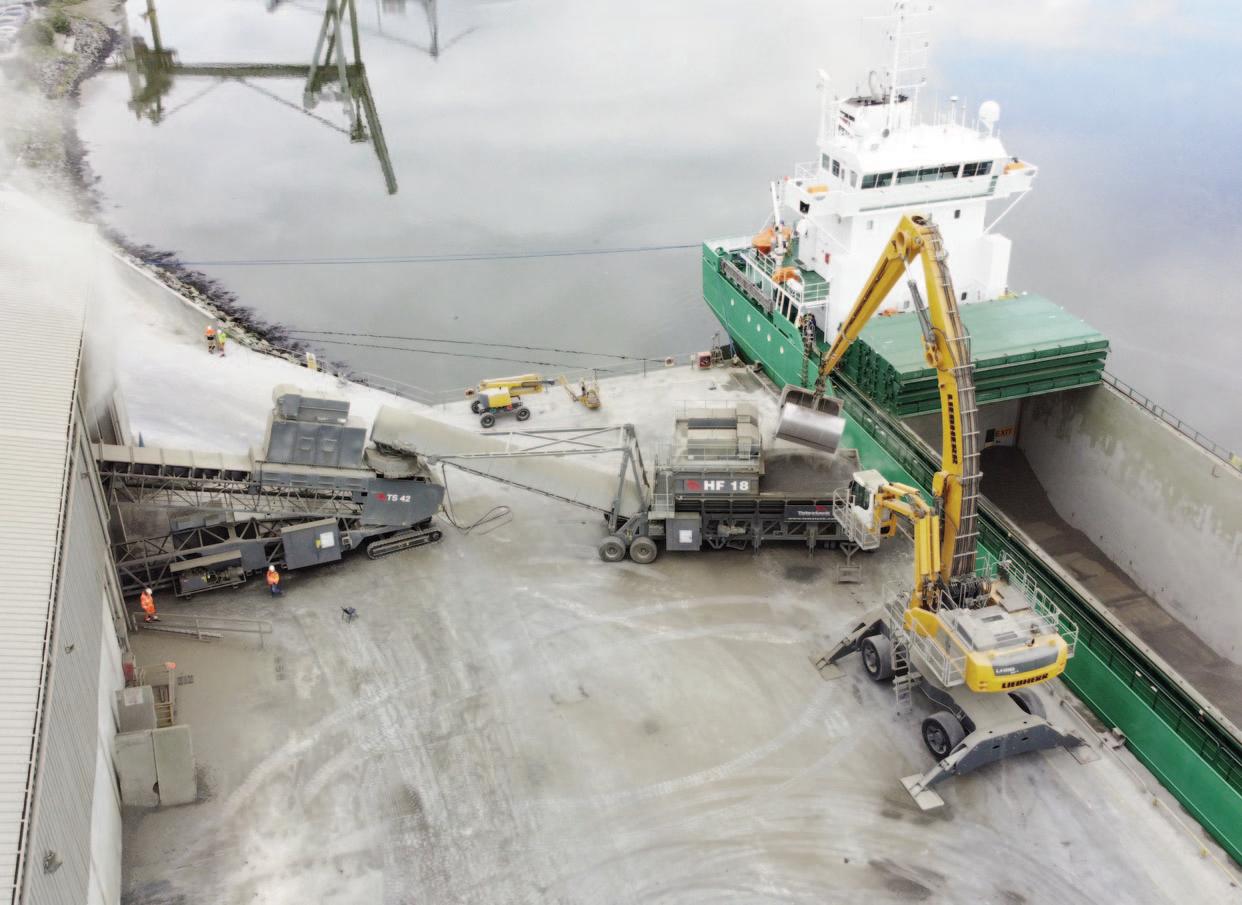
•Full range of shiploading, ship unloading and warehouse solutions custom-designed for the cement industry.
www.telestack.com
sales@telestack.com
New double-sided quay at Ukraine terminal relies heavily on NEUERO
shiploading and unloading systems
Equipment from shiploading and unloading expert NEUERO Industrietechnik is at the heart of the new two-sided quay built at Ukraine’s Risoil Terminal.
NEUERO’S TOWER SHIPLOADING SYSTEM : A KEY COMPONENT OF RISOIL’S INNOVATIVE DOUBLE-SIDED QUAY
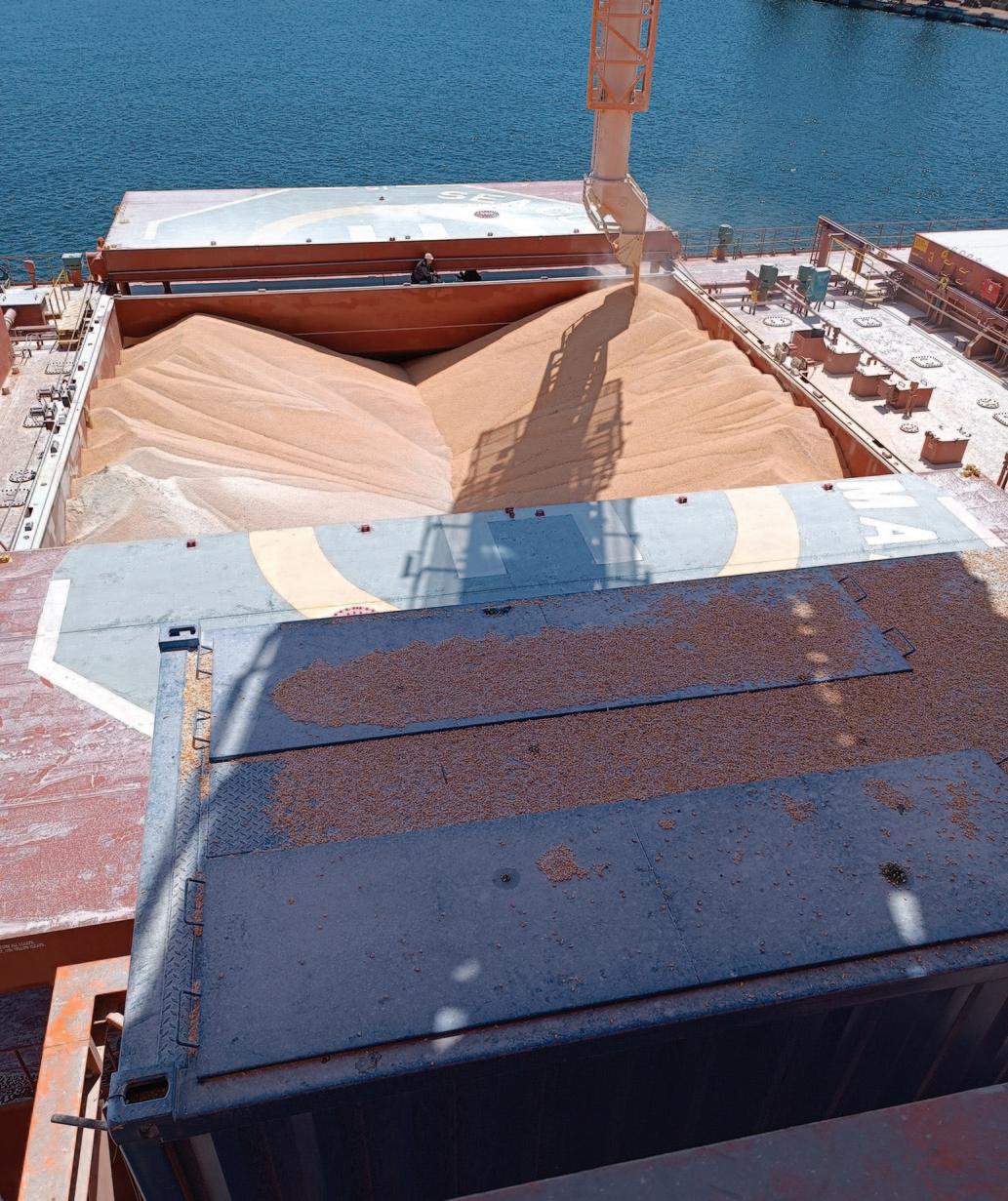
The future of port infrastructure in
Ukraine has taken a significant leap forward with Risoil’s introduction of the doublesided quay. One of the quay’s distinguishing features is its cutting-edge shiploading and unloading system, supplied by the reputable firm, NEUERO. This article delves into the specifics of NEUERO’s new tower ship loading system and how it enhances the operations at Risoil’s terminal.
NEUERO: A NAME SYNONYMOUS WITH INNOVATION
NEUERO, renowned for its shiploading and unloading solutions, has been at the forefront of providing environmentally friendly and efficient equipment for ports globally. Its latest offering, the tower shiploading system for Risoil’s double-sided quay, further solidifies its position in the industry.

KEY FEATURES OF THE TOWER SHIPLOADING SYSTEM
NEUERO’s system boasts several impressive features:
high capacity loading booms: v equipped with boom conveyors, KIKO (kick-in/kick-out) pendular movement, and DLH dustless loading heads, each boom has the potential to efficiently load cargo at up to 1,500tph (tonnes per hour);
pneumatic ship unloader: the system v also includes a pneumatic unloader, which can handle cargo at 600tph, ensuring versatile unloading operations when required environmental efficiency: the booms v come with state-of-the-art dust suppression heads, ensuring minimal dust emissions during loading and unloading. This not only contributes to a cleaner environment but also ensures compliance with global environmental standards.
IMPACT ON RISOIL’S OPERATIONS
With NEUERO’s system in place, Risoil enjoys several benefits: increased efficiency: with the v capability of handling cargo at up to 1,500tph through its loading booms and 600tph through its pneumatic
unloader, the system significantly optimizes the loading and unloading process; operational versatility: the design v allows Risoil the flexibility to either load two ships simultaneously or get the second ship ready while the first one is being loaded; and environmental compliance: the v dustless heads play a crucial role in keeping the operations environmentally friendly, ensuring Risoil’s operations meet stringent environmental norms.
THE CLIENT’S PERSPECTIVE
Risoil, being a visionary in the industry, recognized the potential of integrating NEUERO’s system into its double-sided quay. The decision has proven to be fruitful, as stated by Risoil’s representatives. The system has not only enhanced the terminal’s operational efficiency but has also aligned with Risoil’s commitment to environmental sustainability.
The project of a two-way quay was conceived by the shareholders of Risoil more than ten years ago. “The idea was to ensure the loading of ships with a larger draught. Risoil saw the possibility of building its own hydraulic structure to

ensure the draught of ships up to 15 meters,” says Yevhen Sadovoy, General Director of Risoil Group Terminals.
Before construction was completed, Sadovoy said, “We will carry out simultaneous loading of up to 3,000 tonnes of grain per hour on either side of the pier, or load two ships on both sides of the pier with a capacity of 1,500tph. Moreover, loading can be carried out in any combination, adjusting the types of cargo and the proportions of cargo flows on both sides of the pier. To date, there is no twoway quay in the ports of Ukraine, which would provide the ability to simultaneously handle two ships with two different cargoes.”
Another ‘feature’ of the facility is the ability to process not only export, but also import traffic. “The possibility of exportimport operations is a key feature of the pier. We can confidently say that by implementing this project, Risoil is taking a step into the future. That’s why it’s cool," emphasizes the top manager.
Sadovoy explains another interesting feature: the ability to handle grain from barges and ships of the ‘river-sea’ type. “We see the prospects for transportation by small-tonnage vessels — the reception of a small-tonnage fleet for the efficient
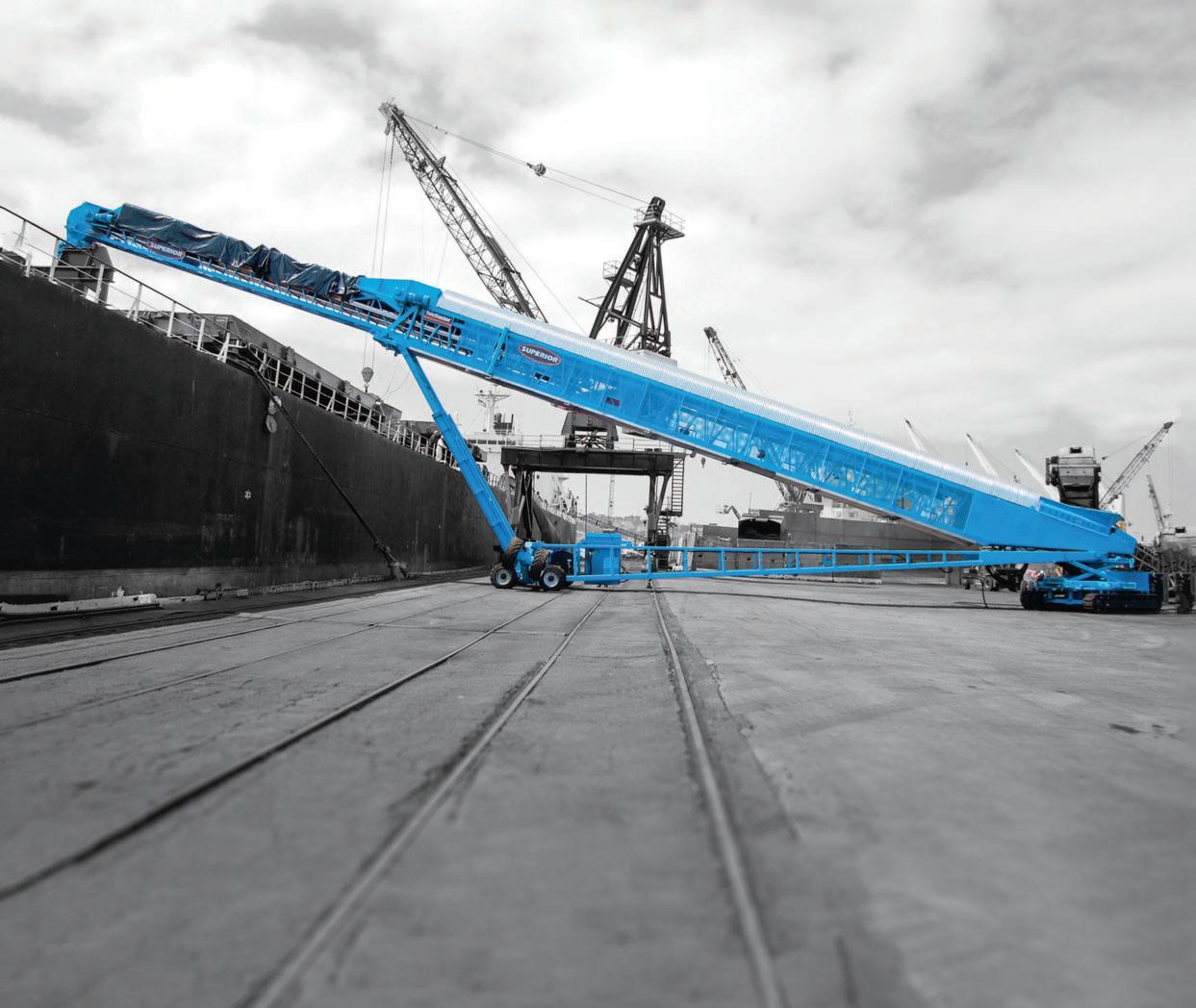
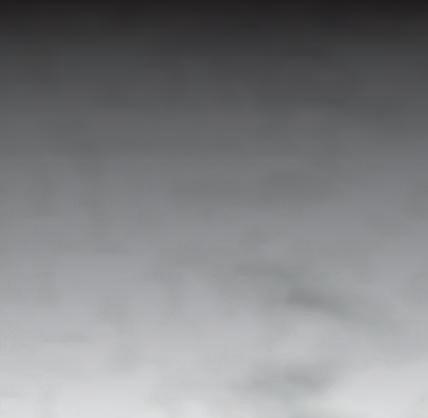
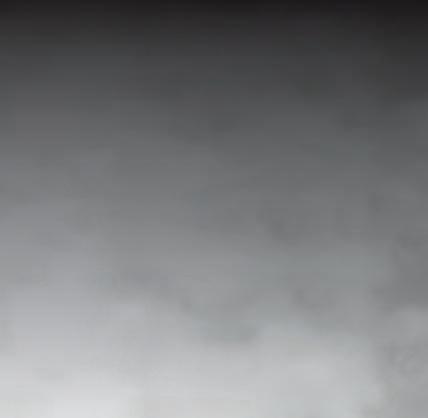

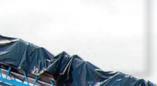

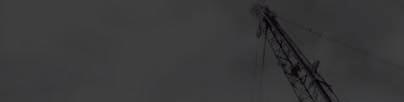
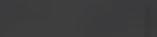

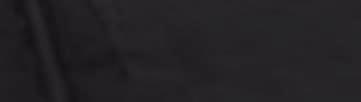


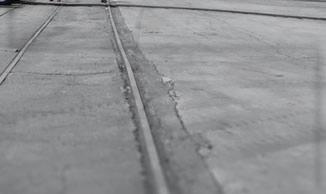
organization of export-import operations. This is another factor why this is the project of tomorrow,” he says. The ability to handle small-tonnage vessels also reduces the load on the port’s railway infrastructure and expands the logistics capabilities of customers.
The impressive operational potential of the pier was the result of the company’s cooperation with partners — the designer and equipment supplier. The project was developed by the State Design Institute ‘ChernomorNIIproekt’ in active co-operation with the engineering service of Risoil.
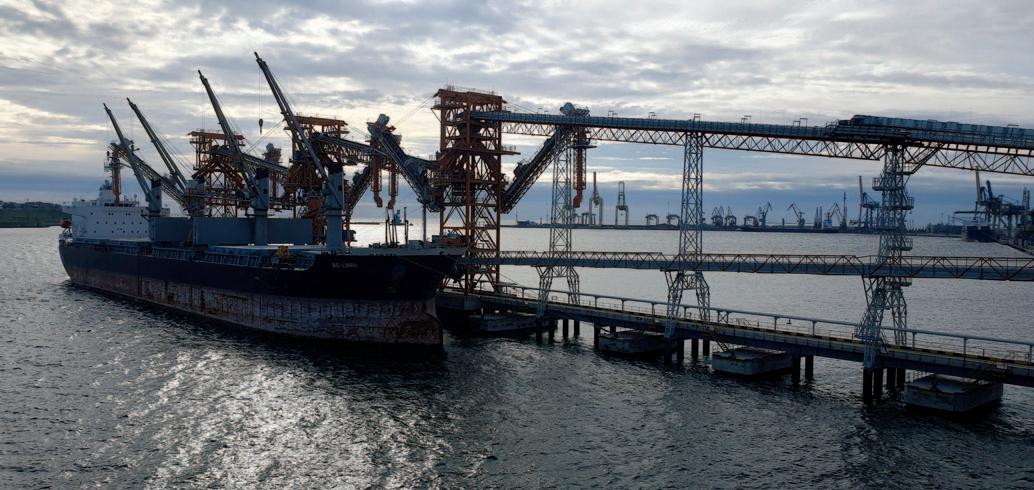
CONCLUSION
The collaboration between Risoil and NEUERO in the construction of the double-sided quay marks a significant advancement in Ukraine’s port infrastructure. NEUERO’s tower shiploading system stands as a testament to how innovative technology can transform traditional port operations, ensuring efficiency, versatility, and environmental compliance. As ports around the world look for ways to optimize their operations, the success story of Risoil’s terminal serves as a benchmark for the future.
ABOUT NEUERO
NEUERO has been a major manufacturer of mechanical and plant engineering since 1914. It stands for mechanical engineering, innovation and maximum customer benefit.
The company’s aim is to offer the best shiploading and unloading in the world to make it easier for its customers to work at ports and to ensure the supply of goods worldwide. With over 5,000 built references in over 140 countries, NEUERO is a respected manufacturer of shiploading
and unloading equipment. Several thousand tonnes of grain are handled every hour worldwide using NEUERO machines.
NEUERO’s machines are characterized by advanced, efficient, reliable and userfriendly design. The systems have the lowest maintenance and operating costs and thus ensure a fast return on investment.
All NEUERO equipment follows the best engineering practices, with quality German manufacturing and on-time deliveries. This high-quality, customized equipment places NEUERO among the most popular global suppliers for the grain and grain by-product market. The company is also seeing great success in its unloaders that are used to handle alumina and petcoke. NEUERO is now also making unloading equipment tailored for wood pellets, PKS (palm kernel shells), as well as other biomass products that are becoming ever more popular to fuel electric power plants that are moving away from coal as a fuel source.
NEUERO’s aim is to supply every client with the most reliable, efficient, environmental friendly, and user friendly ship-unloaders and shiploaders possible. Special attention is paid to using the most advanced and best designed components to make all equipment. The result provides a equipment solution that gives clients the lowest operating and maintenance costs while at the same time giving them the highest operating efficiency.
NEUERO also focuses specifically on environmental issues, and it strives to deliver equipment that offers the lowest possible pollution to the environment. This also makes the work area safer for clients’ employees, as well as giving a clean work area for the neighbours of all clients.
NEUERO’s shiploaders and unloaders set standards worldwide.
NEUERO is ISO certified and has guidelines on work safety, health and the environment. More than 300 customers already rely on NEUERO’s expertise. Continuous unloading performance is guaranteed, even during residual cleaning. Less dust is emitted during loading with NEUERO’s special engineered loading head and noise reduction through its insulated machine houses. NEUERO’s lightweight designs make its machines very safe and environmentally friendly for handling.
TECHNOLOGICAL DEVELOPMENTS
NEUERO works constantly on ways to improve operating efficiency in both capacity increases, and power consumption reductions. Just as important, the company is always making changes to make the equipment last longer, and lower maintenance costs. NEUERO studies the flow of material in the conveying line to learn ways to improve the flow which reduces wear on parts, and improves the operating efficiency. Constantly monitoring of temperature and vibration of key bearings helps NEUERO fine-tune its designs, and this information is provided on the clients’ PLC so they can monitor these items and make any necessary repairs when the equipment is not in operation. NEUERO also offers its clients a telediagnostic service so that it can more efficiently assist them with any questions or concerns they have with their equipment.
COMBINED SHIP LOADER AND UNLOADER
These can be used to unload and load many types of bulk goods, particularly from the food sector as well as products from the power plant and aluminum industry.
These systems are tailor made for the customer and adapted to local conditions. All types of inland or oceangoing vessels can be unloaded, and the bulk material can be delivered directly to conveyor systems, trucks or wagons. Reloading is often loaded with smaller power to smaller vessels. This is done virtually dust-free through the use of closed conveyor systems and dust control systems.
They:
offer unloading capacity up to 800tph
v handling wheat at 0.75t/m3; are available stationary, mobile on v rubber wheels or from rails; have a power supply that is via v external feed-in or from diesel generators; have pneumatic support with v conveyor facilities for the loading of band-facing belt systems, trucks or railway carriages; have an auxiliary winch on the boom, v so a small front loader (e.g. bobcat) or larger chain excavators, weighing up to 15.0 tonnes, can be lifted into the ship’s hatch for residual cleaning
Advantages include: low energy consumption;
v easy operation by extensive automatic v operation; low dust and noise emissions; v taking into account ATEX guidelines; v good accessibility with low v maintenance; and large cover inside the ship hatch with v the use of horizontal and vertical telescopic tubes.
CONTINUOUS SHIP-UNLOADERS
Continuous ship-unloaders offered by NEUERO include:
Multiport unloading capacity up to 800tph, based v on wheat; supply via the low or medium voltage; v use of diesel generators possible; v stationary, rail or rubber-tyred v steerable wheels; broad coverage of the ship’s hold by v horizontal and vertical telescopic tube; auxiliary winch for residual cleaning on v the boom for an excavator or front loader; and if necessary, with explosion protection v concept following ATEX guidelines.
Flexiport
v pneumatic ship-unloading for non-freeflowing materials;
v the vertical tube can be equipped with a rotating feeder to loosen up the
product; and
v full coverage of the ship’s hold due to additional extending and kick-in-kickout movement of the vertical boom.
NEUERO developed the Flexiport many years ago, to achieve higher efficiency for non-free flowing materials. The Flexiport unloader combines both a mechanical feeder and pneumatic conveying. The advantage of pneumatic is the ability to unload to the ship hold’s bottom, vacuuming the material and avoiding the need for extra hoppers to lift the material during clean up as required by a mechanical unloader.
The unloading process is different from regular free-flowing materials, because it is carried out with layers instead of positioning in one point and going down (inverted cone).
Nowadays, NEUERO incorporates many features like blower redundancy for high capacity and measurement sensors for vibration and temperature for the bearings. This is also available in the company’s Multiport pneumatic equipment. It is interesting that it is required in all bucket elevators but not in the main drive of a ship unloader. Efficiency for small ships: for example, when unloading wood pellets from 2,000dwt vessels, an average of 70% was promised and delivered — including clean-up operation. This has already been proven in 2002 at the Essent plant in the Netherlands.
Tower
v unloading capacity of up to 1,600tph, based on wheat;
v movable on rails;
v optional with a loading boom;
v integrated auxiliary winch per boom;
v two separate suction lines (50% each); and
v integration of various conveyor elements, such as container scales, magnetic separators, etc.
MECHANICAL SHIPLOADER FOR BULK CARGOES
NEUERO designs shiploaders for bulk goods. Its tailor-made mechanical shiploaders match the local conditions and transport bulk material as gently as possible to avoid breakage and abrasion. The aim is to achieve the best environmental conditions with maximum performance.
NEUERO shiploaders are for dry bulk goods, particularly from the food sector, fertilizer industry and the power plant industry.
NEUERO shiploaders load all types of inland or deep-sea vessels. The NEUERO DLH (dustless loading head) ensures that the loading process is nearly dust-free.
Shiploaders on rails
loading capacity of up to 3,000tph; v supply via low or medium voltage v lines; large coverage within the ship’s hold v through telescopic loading tubes, swivelling boom, KIKO system and traceability of the relay; and low dust and noise emissions. v

Stationary shiploaders
loading capacity of up to 3,000tph; v power supply via cable drum; and v low dust and noise emissions. v
BUTTIMER CASE STUDY: Belfast port ship-unloading and grain storage facilities upgrade
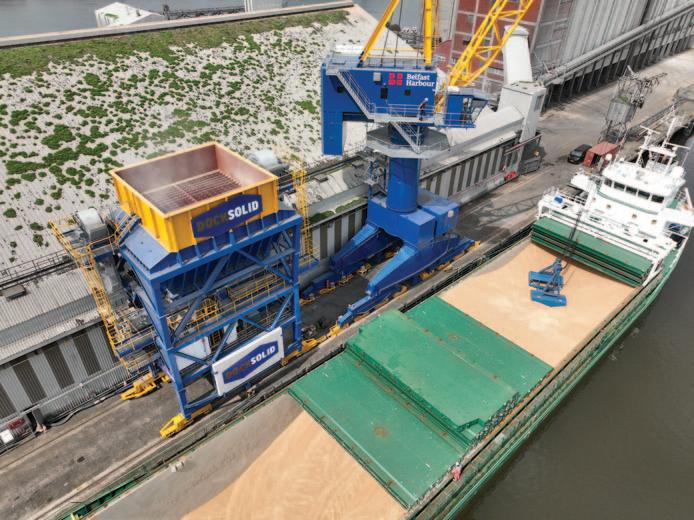
Delivery and assembly of the Buttimer Engineering designed and manufactured Docksolid® New Ship-Unloading Hopper and Conveyor System is now complete and operational with the final commissioning works well under way at Belfast port.
Completed in August 2023, the Docksolid® system provides fully automated crane and hopper operation, with real-time integrated control, reducing cycle time, eliminating cargo spillages, and increasing overall efficiency.
The system provides 1,000tph (tonnes per hour) capacity and facilitates offloading via four different routes and capacity modes.
ABOUT THE CUSTOMER
The customer is part of a diversified group of international commodity trading, storage, agribusiness, and industrial companies. The site is one of the largest grain storage facilities in Europe, discharging commodities directly from ships to storage. The site operation involves unloading bulk cargo ships, using a crane and ‘grab’ discharging to hoppers, that deploy cargo to a network of conveyors transporting the cargo to storage. The 24/7 ship-unloading, and storage operations handles ships from the UK, Europe, the Americas, and Southeast Asia. Further conveyors unload the product from storage, into road wagons for distribution to the market. Much of the existing equipment and infrastructure on site was 1960s technology, with filling and cargo route management being manually controlled in the storage building.
SUMMARY OF PROJECT REQUIREMENTS
Docksolid® loaders are bespoke designed for each client and each application — ensuring they are made to meet the specific environmental requirements, and flow characteristics of the product being handled.
FOR THIS PROJECT THE CUSTOMERS’ REQUIREMENTS
WERE AS FOLLOWS:
Due to the replacement of two existing cranes and their associated smaller hoppers with a single new higher capacity grab crane the customer required a single bespoke design high-capacity rail mounted quayside hopper and integrated cargo handling system. The system required fully automated crane and hopper operation,
with real-time integrated control, reduced cycle time, eliminating cargo spillages, dust suppression, and increasing overall efficiency, by doubling capacity from 500 to 1,000tph, plus facilitating offloading in four different route and volume capacity modes.
THE BUTTIMER ENGINEERING-DEVISED SOLUTION INCLUDED :
Automation of cargo routing from v hopper to storage locations, plus connecting new hopper into both gantry conveyor routes on the berth side of the store.
Creation of a parallel feed system to v both gantry conveyor routes; this parallel feeding requires bespoke hopper geometry with a double conveyor discharge arrangement which is connected to two diverter inlet points at one time. Upgrading of all conveyors within the v store, to ensure increased throughput, replacing the existing open belt conveyors with enclosed chain and flight conveyors with slides and diverters to the silo bins. All new equipment to use innovative control technologies, digital integrated RADAR probes, and level sensors. Provision of mechanical spot filters on the new conveyors to reduce dust emissions.
The hopper-control systems were v integrated with the overall facility automation system, and equipped with interlocks to ensure the hopper’s
handling equipment does not operate until downstream equipment is confirmed to be running. Pneumatic hopper slides for filling vehicles were controlled remotely by the control system combined with CCTV monitoring, with option for hopper movements to be controlled by site personnel, independent of the control system.
There was a strict requirement that v ongoing site operations are not impacted, and that intake, storage and product discharge operations are fully maintained during the re-fit project. Working space alongside the deepwater berth and within the storage facility was very limited, given the scale of upgrade required.
Extensive discussions with the v customer’s dedicated and experienced project management team throughout the design phase ensured we fully understood their business requirements and that the final solution included the highest EHS and ESG standards expected.
KEY ASPECTS OF BUTTIMER ENGINEERING’S SOLUTION:
The solution offered to the customer by Buttimer Engineering’s team called on the company’s extensive knowledge and four decades experience of design and manufacture of bulk materials handling solutions. There was intensive competition from other bulk handling specialists bidding the project, with Buttimer Engineering’s
innovative use of digital technologies being a key differentiator from the competition, enabling the project to be secured and a unique cutting-edge Buttimer solution be provided.
As some of the existing equipment and entire site infrastructure was based on 1960s technology, the level of detail of building and equipment dimensions required for a project of this scale was limited. This can preclude use of modern design technologies from being used, however Buttimer overcame this challenge by carrying out full 3D scanning of the existing facility to enable the project to benefit from its BIM technology.
Once processed and refined the 3D scan provided a digital baseline to enable Buttimer’s engineers to create a 3D Model using its Solidworks software system. This enabled real-time online input from the customer on finer details and functionality of the hopper machine and grain store upgrade solution.
The combination of the scale of the Hopper Machine required (approximately 180 tonne weight) coupled with the automation and complex operational features required by the customer, did provide many design challenges to be overcome. The confined site location of the machine’s final destination adjacent to the deep-water berth at the port meant that the machine had to be designed narrower than typically used. An innovative structural design using a 12.5t pre-cast concrete counterbalance was required to enable the automated hopper to operate in the confined site and provide the high performance and versatility required.
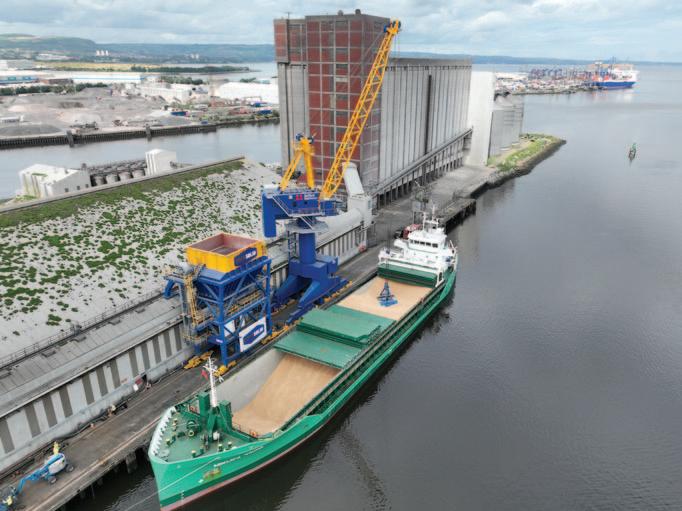

Buttimer Engineering’s energy efficient design utilized low power consumption
drives and motors, it enabled faster cycle times, and hence reduced ship unloading time, providing long-term cost and sustainability advantages to our customer.
During Buttimer Engineering’s early concept and design development evaluation, the tight programme time and requirement not to impede ongoing site operations became a key consideration.
The original grain store used open belt conveyors for the cargo transfer; while being equipped with dust handling cyclone systems, these belts created dust emissions in the upper levels of the store. Buttimer Engineering’s innovative design evaluation resulted in utilization of higher specification, and higher cost, enclosed chain and flight conveyor systems. This was in keeping with the customer’s EHS focus and ensured Buttimer Engineering presented a high quality, energy efficient,
environmentally friendly, and sustainable working environment into the future.
Buttimer Engineering’s BIM design evaluation also resulted in the decision to increase the utilization of its OSM facility (off-site manufacturing), and pre-assembly off-site. Rather than deliver standard-size manufactured components to site for assembly, use of its OSM facility enabled large components of the 180-tonne weight steel hopper machine to be pre-assembled and delivered to Belfast by the company’s heavy lift specialist transport partners.
Pre-assembly provided programming and scheduling advantages, which lead to cost efficiencies and sustainability benefits. Buttimer Engineering’s location adjacent to the motorway network proved to be advantageous for the OSM approach, however the BIM modelling system was the true enabler of this innovation. The 3D modelling and detail design created in Solidworks was used to ensure that each component manufactured off-site would fit into the site, accurately join to adjacent new components, and provide the overall solution required by Buttimer’s customer.
GLOBAL SOLUTIONS
For wider international markets, Buttimer Engineering operates with its global partner Terex Prostack, who are the bulk materials division of Terex Corporation, a leading global provider of materials handling and processing equipment. The Buttimer Engineering/Terex Prostack offering provides a wider product portfolio of custom-made bulk materials handling and conveying port equipment and the partnership can provide significant advantages to port operators throughout the world.
Siwertell ship-unloading technology ordered for enclosed, efficient multi-material handling in Africa
Bruks Siwertell has secured an order from Senegal Minergy Port SA (SMP) for a highcapacity Siwertell ship-unloader for the new port of Bargny-Sendou, which is under construction near Dakar, Senegal, west Africa. Established to undertake the development of this new liquid and dry bulk facility, SMP needed a ship-unloading solution that was able to efficiently and safely switch between multiple dry bulk cargoes.
“SMP spoke with many industry professionals regarding our technology and reputation before approaching us,” says Bertil Andersson, Sales Manager, Bruks Siwertell. “All spoke extremely highly of Bruks Siwertell and did not hesitate to give their recommendations.”
Around 90% of Senegal’s trade comes through its current Atlantic Ocean port, the Autonomous Port of Dakar. However, growing import and export demands has outstripped its capacity and Senegal urgently needs to address this, hence the construction of the new port in BargnySendou, which upon opening, will take over all of the bulk commodity flows from the Autonomous Port of Dakar.
“Bargny-Sendou Port will be the largest
and most sophisticated of its kind in west Africa,” says Alexander Zalocosta, CFO Senegal Minergy Port SA. “Having an initial dry bulk capacity of 20mt [million metric tonnes], it is predicted to handle 15mt of commodities in its first year of operations.
“In addition to catalyzing both regional and national growth, Bargny-Sendou Port will deliver significant environmental benefits,” continues Zalocosta. “Its new location will mean a substantial reduction in traffic and air pollution in downtown Dakar, where the current port is located. All Senegalese residents will benefit from the port’s modernized infrastructure not only environmentally, but also because transportation and freight costs will be reduced, and there will be fewer import and export delays. The port will also create a significant amount of jobs for the local population.”
The Siwertell 640 M-type ship-unloader will deliver market-leading dry bulk handling capabilities, realizing SMP’s ambitions for the new port to act as a major hub for global trade. It will handle dry bulk material imports of sulphur, coal, urea, and fertilizer, at a rated capacity up to 1,500tph (tonnes per hour).
“These are very abrasive and volatile dry bulks, but our technology enables them to be handled safely, in totally enclosed conveying lines, protecting the environment from dust emissions and ensuring no material waste through spillage,” explains Andersson. “SMP has ordered this unloader because it is aware of our ability to deliver this type of world-class dry bulk material handling asset.”
All Siwertell ship-unloaders that handle sulphur, are fitted with the Siwertell Sulfur Safety System (4S), which was first developed over 30 years ago to minimize the risk of explosions when handling this extremely volatile and corrosive dry bulk material.
“Siwertell technology is the only ship unloading system able to offer safe, totally enclosed sulphur handling, protecting the environment, personnel and the port,” he adds.
The Siwertell ship-unloader will be installed on a jetty 1,500m from the shore, and also ensures the advantage of being low in weight, which minimizes jetty loads. It will be assembled on site under Bruks Siwertell supervision and is planned to commence operations in mid-2024.
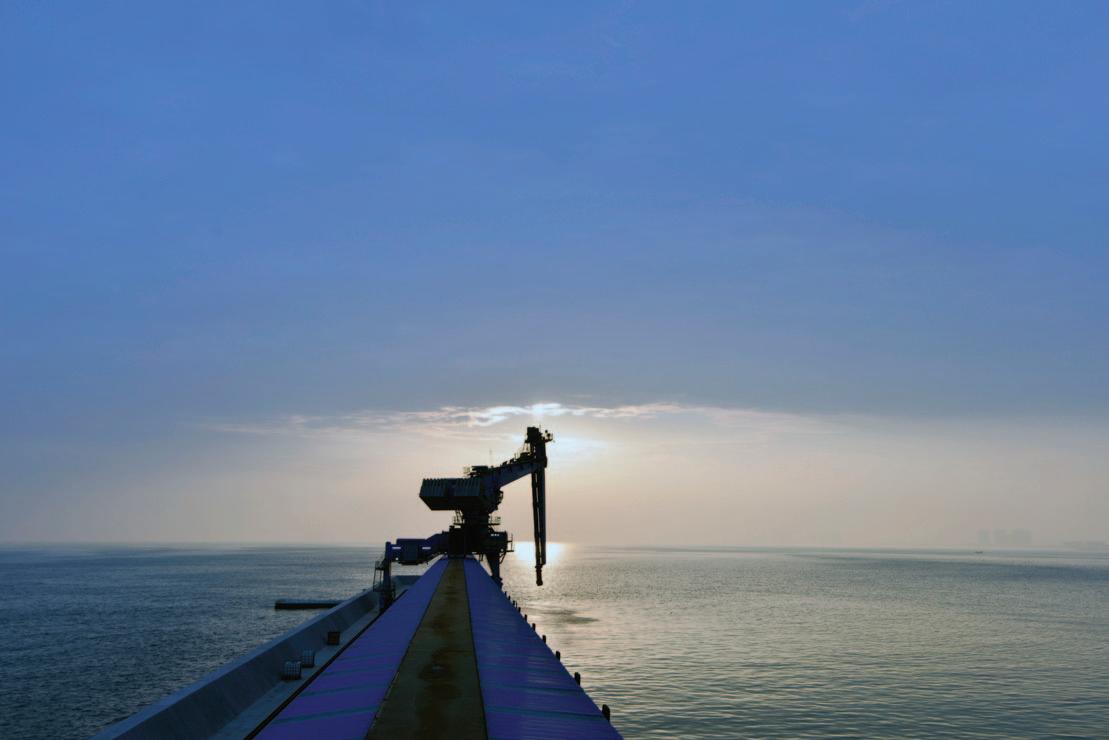
INNOVATIVE DESIGNS THAT ADAPT TO CHANGING DEMANDS
Your challenge might be finding a dry bulk handling solution that ensures the profitable, sustainable growth of your business.

Our expertise can provide just that. A totally enclosed Bruks Siwertell solution that ensures operations are efficient, reliable, and free from dust and spillage.
bruks-siwertell.com
Seize the day...
...and the cargo, with onboard and onshore bulk handling grabs
ORTS Maschinenfabrik grabs strengthen the bulk industry
German company, ORTS GmbH Maschinenfabrik, is renowned for the manufacture of high quality grabs, which are in use both onshore and on geared bulk vessels. Its product portfolio includes:
v electro-hydraulic grabs;
v the equipment necessary to operate electro-hydraulic grabs;
v independently operating dieselhydraulic grabs;
v mechanical rope grabs; and
v heavy lift beams.
The company started operations in 1972, as ‘S.F. Orts Engineering’, as an engineering and consulting office, specializing in the construction of grabs and other maritime transport equipment.
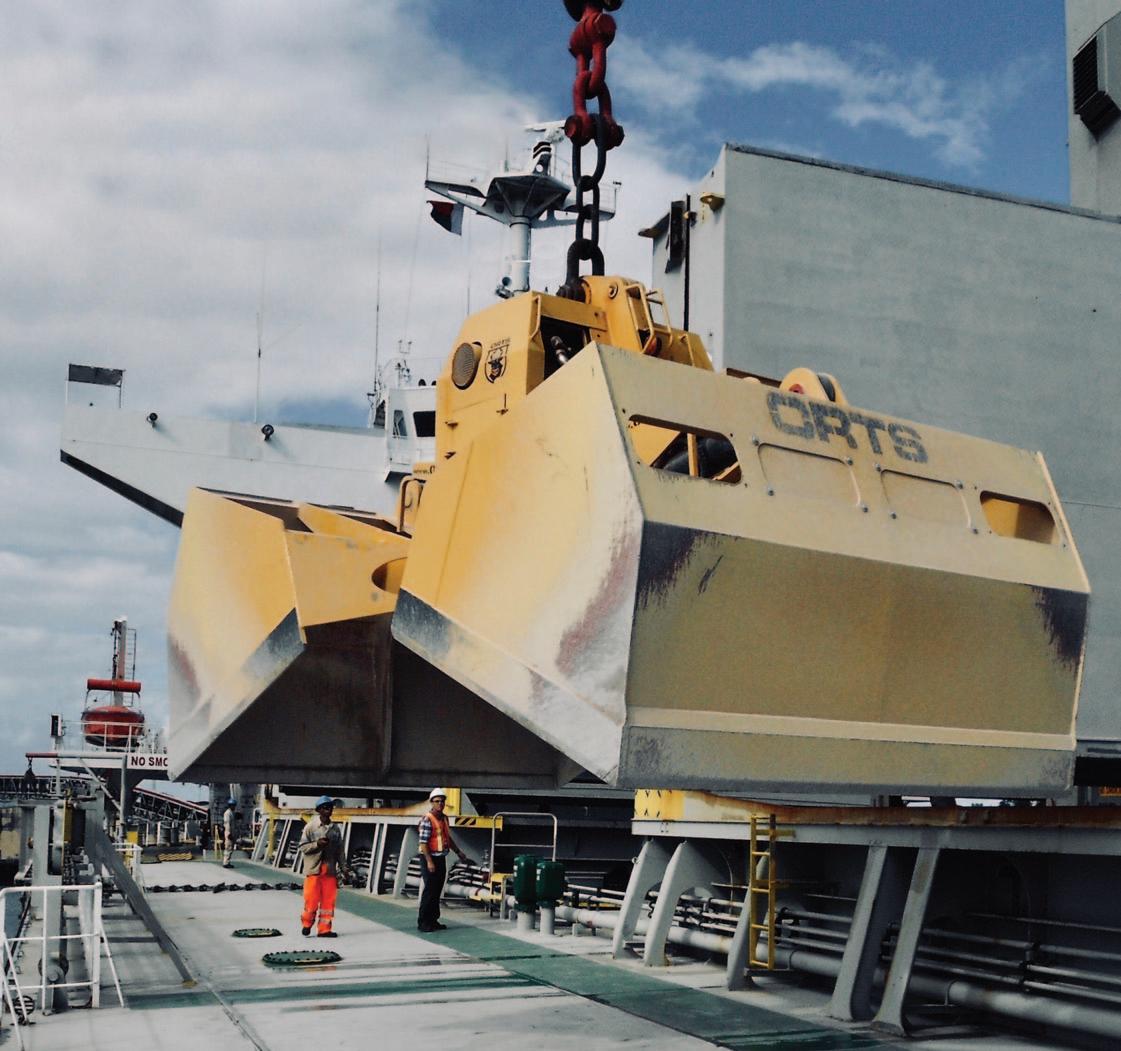
In 1985, the production workshop was founded and the name changed to ORTS
GmbH Maschinenfabrik. The company is still family owned today and the production facilities are located in Germany.
In 1995, the radio-controlled diesel hydraulic clamshell grab was constructed. Over the years it became a reliable and fast bucket, working with every kind of crane and offers great flexibility to the owner. Some customers refer to the Orts diesel hydraulic grabs as their ‘workhorses’.

Grabs from Orts are highly valued by customers, and spare parts for 30 year old grabs are still delivered to customers. The high quality of each grab means that they offer a long lifetime, and a reliable, highly efficient, powerful, can handle a large payload, and have low spare part consumption.
ORTS GRABS
Orts grabs are suitable for all types of dry bulk cargo. Of course, each type of material has its own physical characteristics, which could mean having to design a grab for specific products.
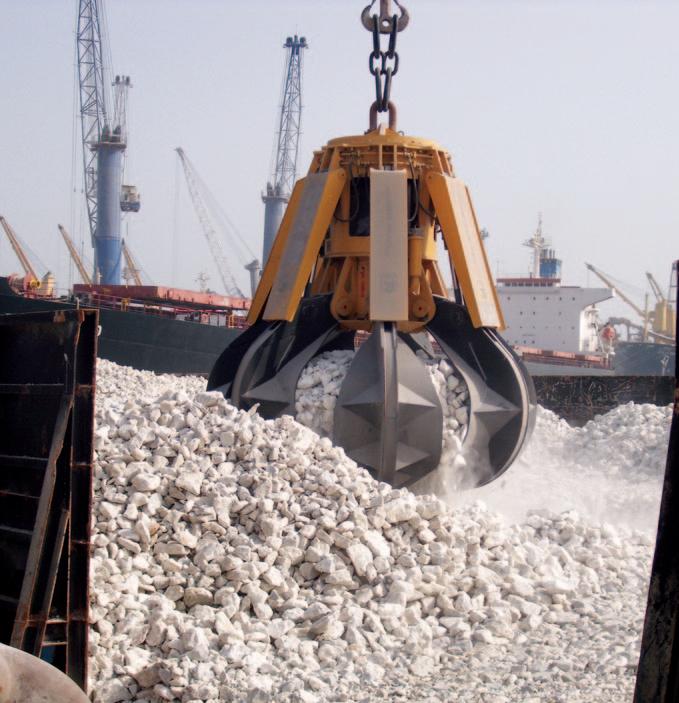
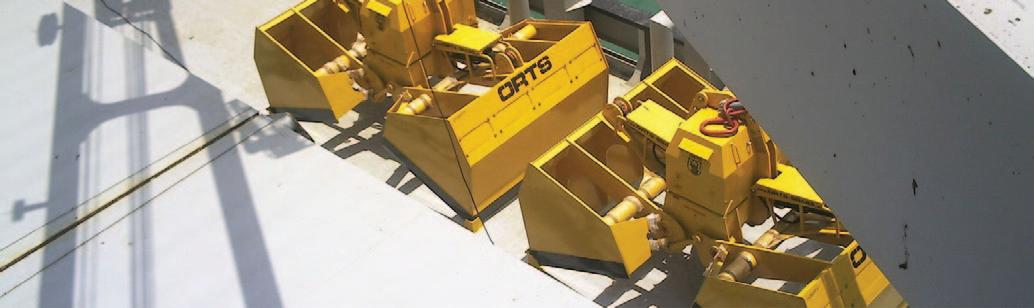
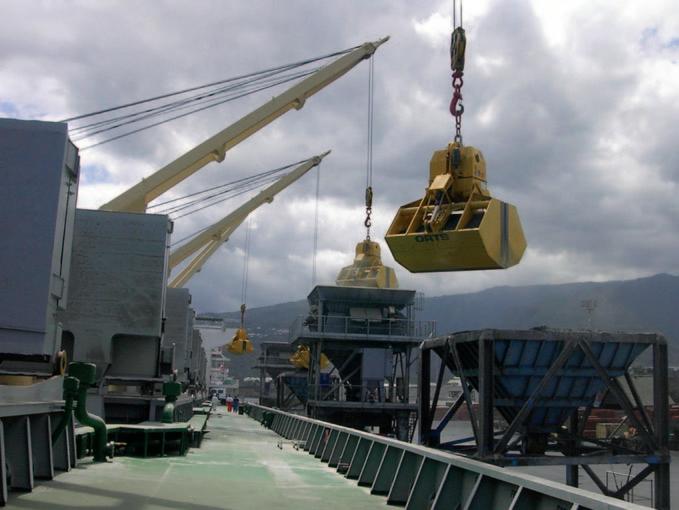
“However, in most cases, shipping and stevedoring companies need an ‘all-round’ grab, which they can use to handle different types of cargo efficiently,” explains CEO Sigvard Orts, adding that scrap metal, pig iron, HBI and large stones also fall within the range of such equipment too.
For this kind of bulk cargo the independent diesel-hydraulic grabs are available as orange-peel grabs with the ability to handle bulk cargo with high density. The biggest diesel-hydraulic orange-peel grab from Orts has a 12m³ capacity. This DHM 12m³ is in use to discharge HBI.
In terms of productivity, Orts emphasizes that this is dependent on three key factors: low dead weight, kinematics and the closing force of the knives. In fact, a 12m³ Orts independent diesel-hydraulic
grab could in theory achieve average loading rates of around 350–450 tonnes per hour (this depends on the density of the bulk cargo).
“The reliability of the grab is also
extremely important when discussing productivity. It is pointless to buy a cheap grab, if it then breaks down during vessel handling, effectively prolonging the length of the port call. The grade of filling is also crucial; the better the grade of filling of the grab, the shorter the loading/discharge time,” stresses Orts.
ELECTRO HYDRAULIC GRABS
Electro-hydraulic grabs are designed and produced by ORTS GmbH. The electrohydraulic grab is equipped with an electric motor to power the hydraulic pump. The hydraulic pump brings the hydraulic cylinder into action, forcing grab buckets to open and close. Power is supplied to the electro-hydraulic grab via a power-cable that is situated at the crane jib with some additional equipment, e.g. cable drum, rope drum, guide rollers.
INDEPENDENT DIESEL-HYDRAULIC GRABS (SINCE 1995)
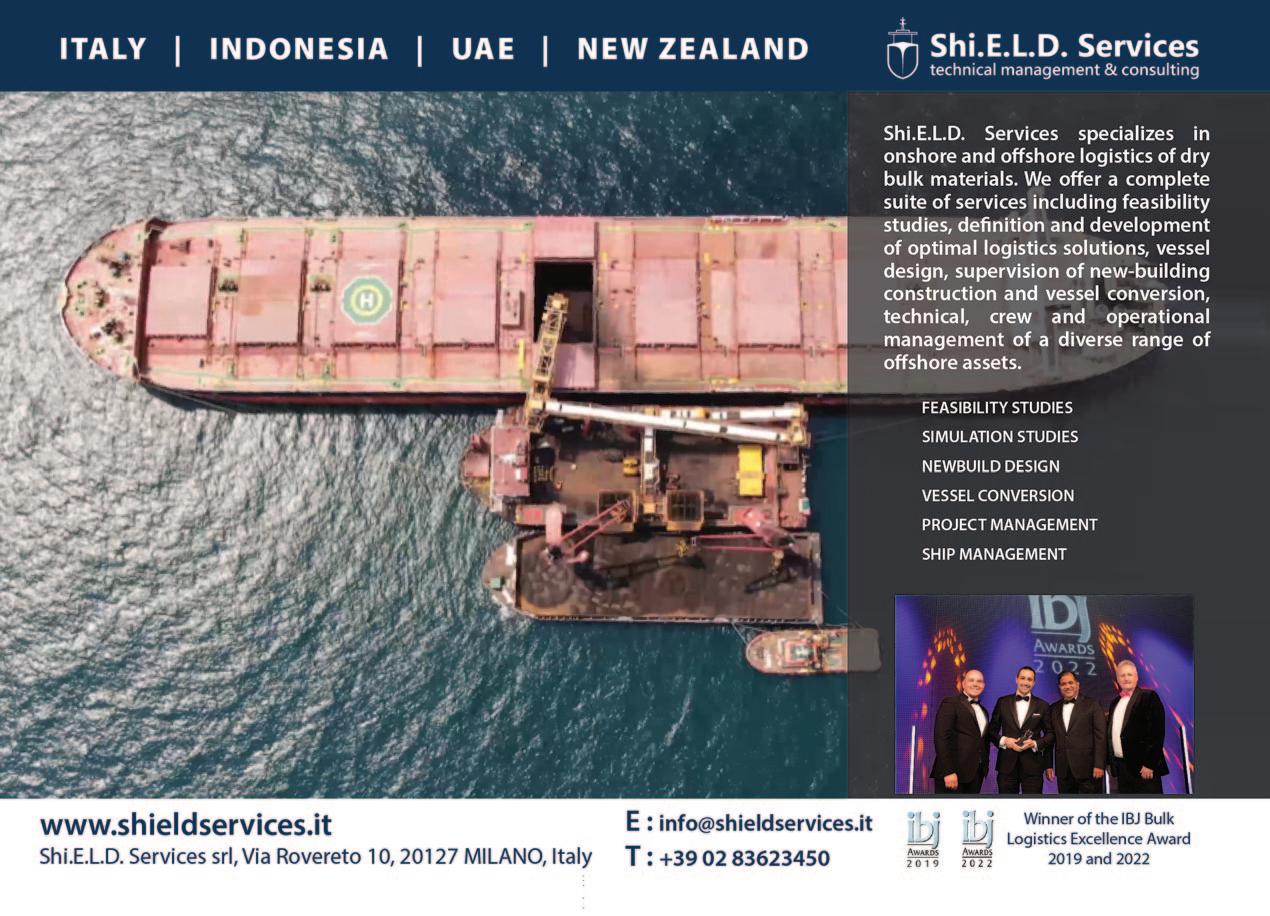
Fully radio-controlled diesel-hydraulic grabs have been constructed and produced by ORTS GmbH for more than 25 years. A radio-controlled diesel hydraulic grab is a crane attachment that is operated independently of power cables or hydraulic lines; it is completely selfsufficient and is operated via a radio control device by the crane driver or another person at the loading room.
Thus, a radio-controlled grab can be used on any crane, since an external power supply is not necessary. A diesel engine inside the grab provides the power to drive the hydraulic pump. The crane operator has to send commands to move the buckets via a radio control. The way of controlling the movements of the buckets/clamshells is identical to that on an electro-hydraulic grab. They are fast, reliable and a better alternative solution compared to mechanical single rope grabs.
Another advantage to mechanical singlerope grabs is the lower dead weight and that there is no working/operational height
requirement.
A few years ago ORTS also developed smaller diesel-hydraulic grabs for construction places, biogas-plants and truck cranes.
MECHANICAL ROPE GRAB
Mechanical rope grabs can have one rope, two ropes or four ropes. Some rare special cranes need three-rope grabs. As the name suggests, a mechanical grab is operated by
means of cable/rope systems only (‘pulley block/lifting block) and requires no power supply or hydraulic lines. A mechanical grab is used for loading and unloading of bulk materials in ports, at industrial plants, as well as in operations at ore smelting and blast furnaces. It is also used in port facilities. Here a purely mechanical grab is a great advantage, as they are mechanical and robust. No electronics, no hydraulic parts. ‘Pimped’ mechanical grabs with e.g. radio control and hydraulic system lose this advantage. Mechanical singlerope grabs are the oldest grab system. They are slower, and handle fewer tonners per hour, and have a higher dead weight compared with motor grabs (diesel hydraulic or electrohydraulic).
LIFTING BEAMS
Beside the motor-grabs (electro-hydraulic and radio controlled diesel-hydraulic) and the mechanical rope grabs, ORTS GmbH also provides the construction and production of lifting beams, traverses and lifting frames.
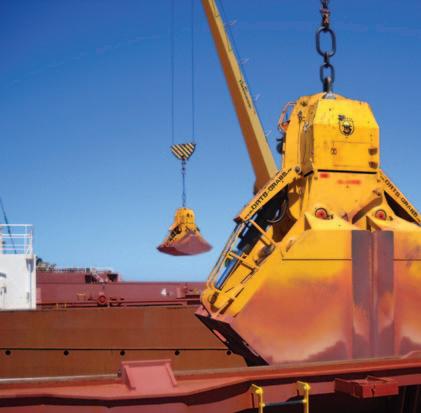
J&B Grabs offers a wide range of attachments to the bulk market
J&B Grijpers B.V. (J&B Grabs) is a holding company engaged primarily in the developing, manufacturing and reconditioning of hydraulic and wire rope grabs. The company started in 1945 in the manufacture and overhauling of re-handling grabs. The company’s nearly 80 years of expertise means that it is able to supply a perfectly balanced product for its customers’ bulk handling operations.
J&B Grabs use 3-D solid modelling and FEA analysis is the design of its grabs. This means that customer-specific requirements can be implemented in the design and production process.
The company has a wide range of standard type grabs, which are readily available.
J&B Grabs are used by many brands and types of available cranes, including: E-Crane, Sennebogen, Caterpillar, Hitachi, Liebherr, Volvo, Fuchs and more.
Due to the many brands and types of cranes using different connecting systems, J&B Grabs has developed a number of quick-change connectors.
Mechanical and hydraulic systems make it possible to swap between grabs in just ten minutes.
J&B Grabs deliver parts and grabs internationally. The company is located in Utrecht in the Netherlands.
HYDRAULIC GRABS FROM J&B
J&B’s hydraulic grab is available as:
v rehandling grab (clamshell);
v closed rehandling grab;
v dredging grab;
v horizontal profiling clamshell;
v log grapple;
v woodchips; and
v bale grab.
HYDRAULIC CLAMSHELL
The Type LH for sand and gravel is available in five body sizes, with buckets from 1,000 litres and up. It is suitable for sand, gravel, coal etc. The grab’s capacity is decided according to the crane size and material to be handled.
The Type LHS, for sand and gravel (low built), is fitted with cylinders mounted on the edge of the buckets. It is ideal for higher closing forces and is low built. It is available up to 7m³ for sand.
The Type LHS-4 is available up to 30m³ for coal. It is suitable for cranes with lifting capacities of over 15 tonnes and up to a massive 45 tonnes. It is used to handle materials including cereals, coal, limestone, sand, bauxite etc.
CLOSED REHANDLING GRAB
The Type LHG rehandling grab is ideal for dusty materials such as cereals, fertilizers, phosphates and biomass. It is available in sizes ranging from 1,500 litres up to 15m³. The grab’s capacity is decided according to the crane size and material to be handled.
The Type LHGS-4, for larger sizes, is a closed rehandling clamshell. It has four cylinders and is used with the larger cranes with a lifting capacity of up to 45 tonnes in grab operation. It is available in sizes ranging from 12m3 to 45m3
DREDGING AND DIGGING CLAMSHELL
The Type LHSz180-4 dredging and digging clamshell:
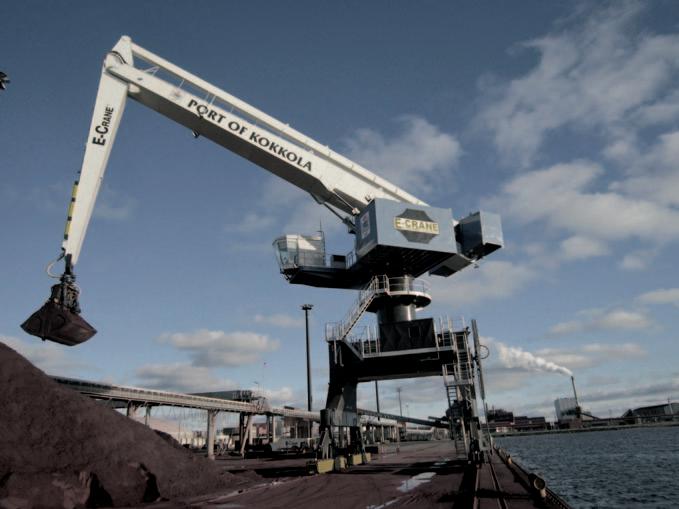
v has large closing forces;
v is fitted with floating pins for the best sealing;
v has an option for dismountable teeth;
v offers high penetration force; and
v has a large volume.
HORIZONTAL PROFILING GRAB
The Type LHM for environmental works hydraulic profiling grab is designed to remove polluted soil from the river bed. The grab will dig the first piece of the curve and will then close horizontally.
LOG GRAPPLE
The Type PLH125 short log grapple is for short logs, and is fitted with a chain.
HYDRAULIC CLAMSHELL FOR WOODCHIPS
The Type LHL clamshell for rehandling of wood-fibred woodchips is fitted with special teeth for good penetration, without damaging the ship. Because of its large spread, the grab has a good filling rate.
HYDRAULIC BALE GRAB
The hydraulic bale grab/clamp is used to handle material packed in bales such as garbage.
HYDRAULIC CACTUS GRAB/ORANGE PEEL GRAB
J&B’s hydraulic cactus grab is suitable for various applications:
v scrap handling;
v garbage/refuse;
v rock; and
v woodchips.
The capacity of the grab is determined by the material density and condition and the capacity of the material handler/ excavator.
HYDRAULIC CACTUS GRAB FOR SCRAP
The Type JHT hydraulic cactus (orange peel) grab for scrap has five tines, and is available from capacities starting at 600 litres.
The JHT-4 model has four tines for scrap handling, and is also available from a 600-litre capacity. It is extremely suitable for long pieces.
HYDRAULIC CACTUS GRAB FOR ROCK
The Type JHS five-tine cactus grab for rock is available for capacities starting at 600 litres. The shape of the tine depends on the rock size.
The Type TH four-tine rock grapple starts at a one-tonne capacity, and is ideal for large rocks.
The Hand special grab for rock placement is used for fast and accurate rock/armour placement. It is available up to capacities of eight tonnes.
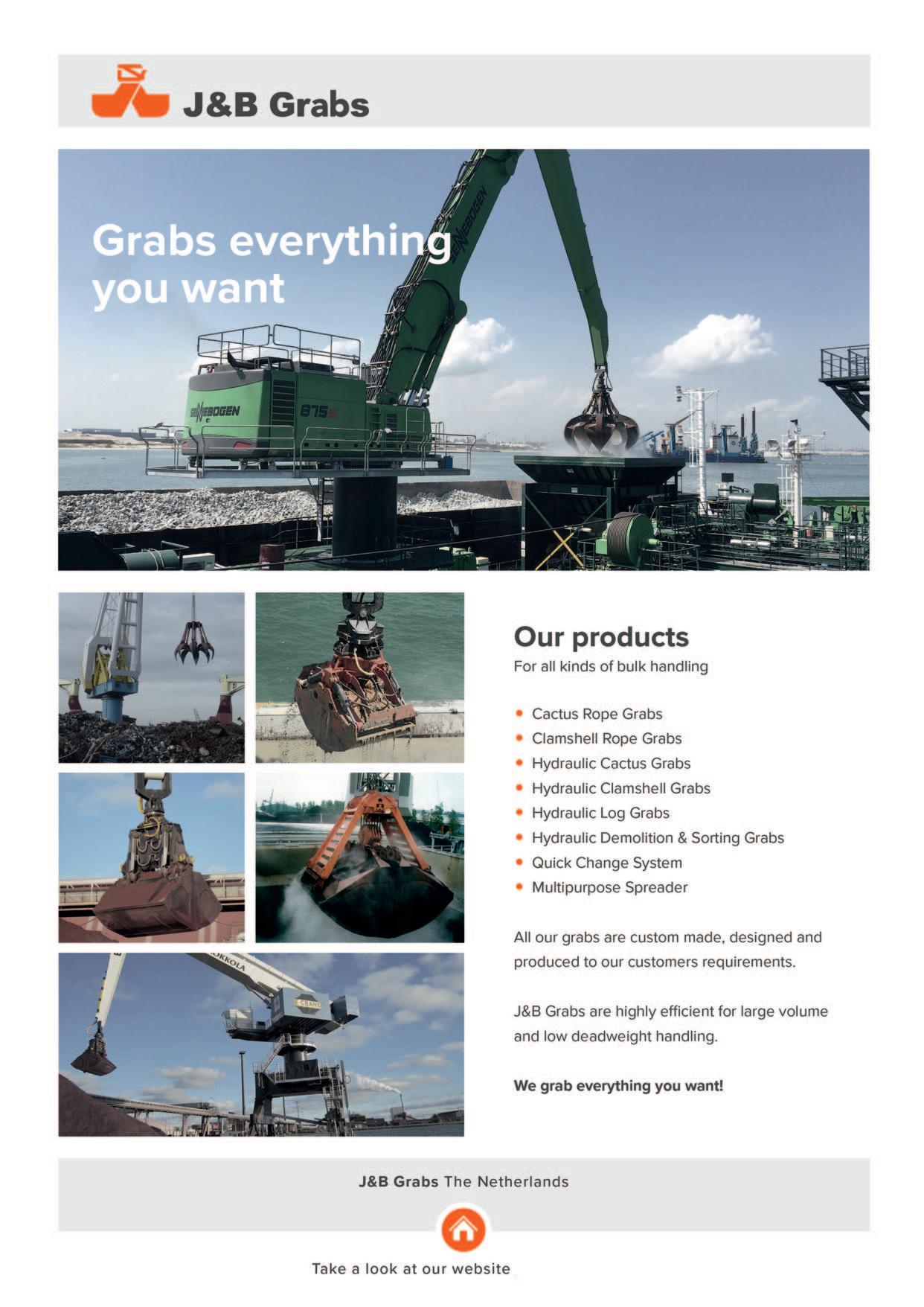

KINSHOFER attachments — on and off-shore
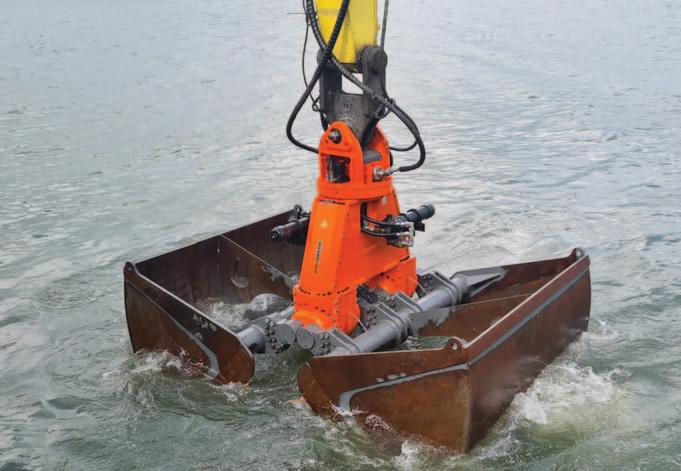
Since 1971, Kinshofer GmbH has been a major manufacturer of high-quality attachments for truck-mounted cranes and it is now on the way to becoming one of the leading excavator attachment producers worldwide, too. In the last two decades, KINSHOFER has become more and more popular for the re-handling business, producing large orange peel grabs (P-Series) for excavators with an operating weight of up to 120 tonnes and re-handling clamshell buckets (C-Series) for excavators and carriers with an operating weight from 18 tonnes of up to 100 tonnes.
The durable KINSHOFER re-handling clamshell buckets of the C-Series have been developed especially for the loading and unloading of bulk materials in large amounts. The widely spaced pivots and the flat closing curve provide maximum volume and the ground surface is protected when discharging from e. g. boat or train carriages. The two shells are driven by sturdy hydraulic cylinders.
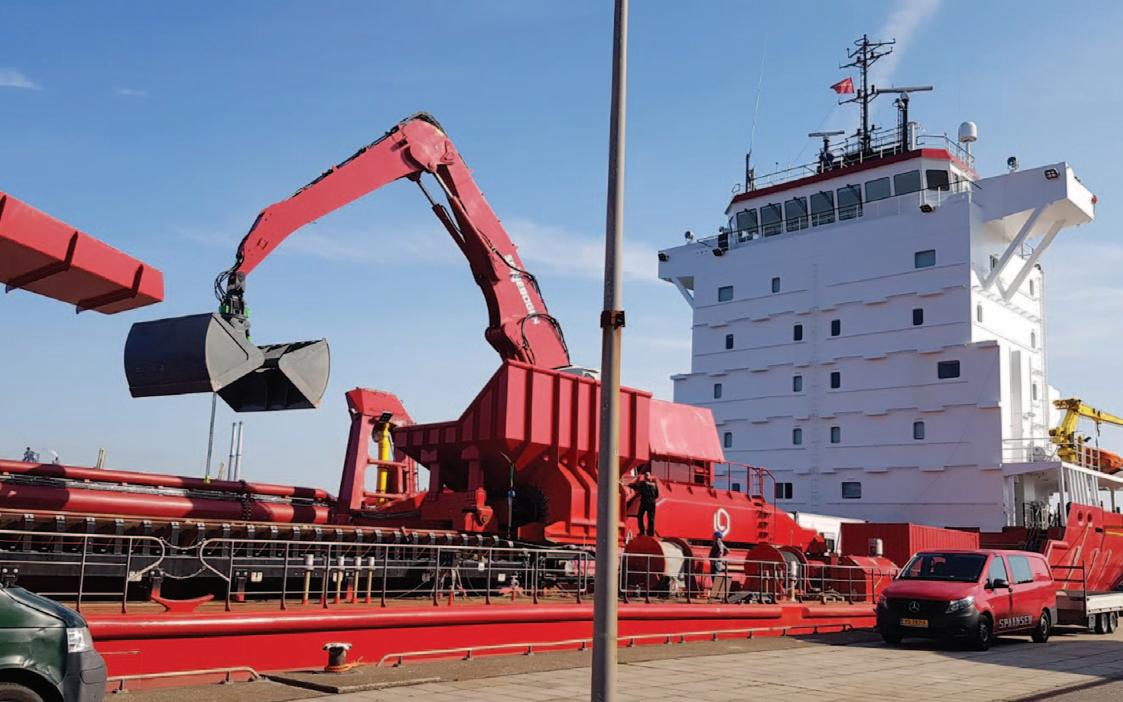
The C-series grabs are available for excavators with 18t up to 100t operating weight. The smaller versions up to 65t are equipped with two vertical cylinders, the C100VHD up to 100t with four cylinders. The shells are very robust to withstand highly abrasive materials and the integrated
endless rotation guarantees the precise positioning of the grab.
An alternative to the clamshell buckets is the KINSHOFER orange peel grab P-series. Sizes range from the smallest P22V for excavators from 16 tonnes operating weight up to the huge P120VHD with a staggering volume of 3,500 litres in the largest variant. Different shell designs — narrow or wide, half or fully closing tines — allow to match the grab to the task.
These heavy duty, sturdy grabs are often used to handle scrap, waste or rocks. As the C-series, the orange peel grabs are
equipped with a robust 360° rotation. Accurate fittings eliminate tine distortion, the end stops for closing and opening are especially solid. Bolts are reinforced and have a large bearing surface. The hydraulic cylinders that operate the arms are protected by replaceable piston rod protections.
All KINSHOFER’s grabs can be used on- and off-shore — in the end it does not really matter where the carrier machine is located and what size it is. As KINSHOFER also has a department for special constructions, every attachment can be adjusted or designed from scratch.
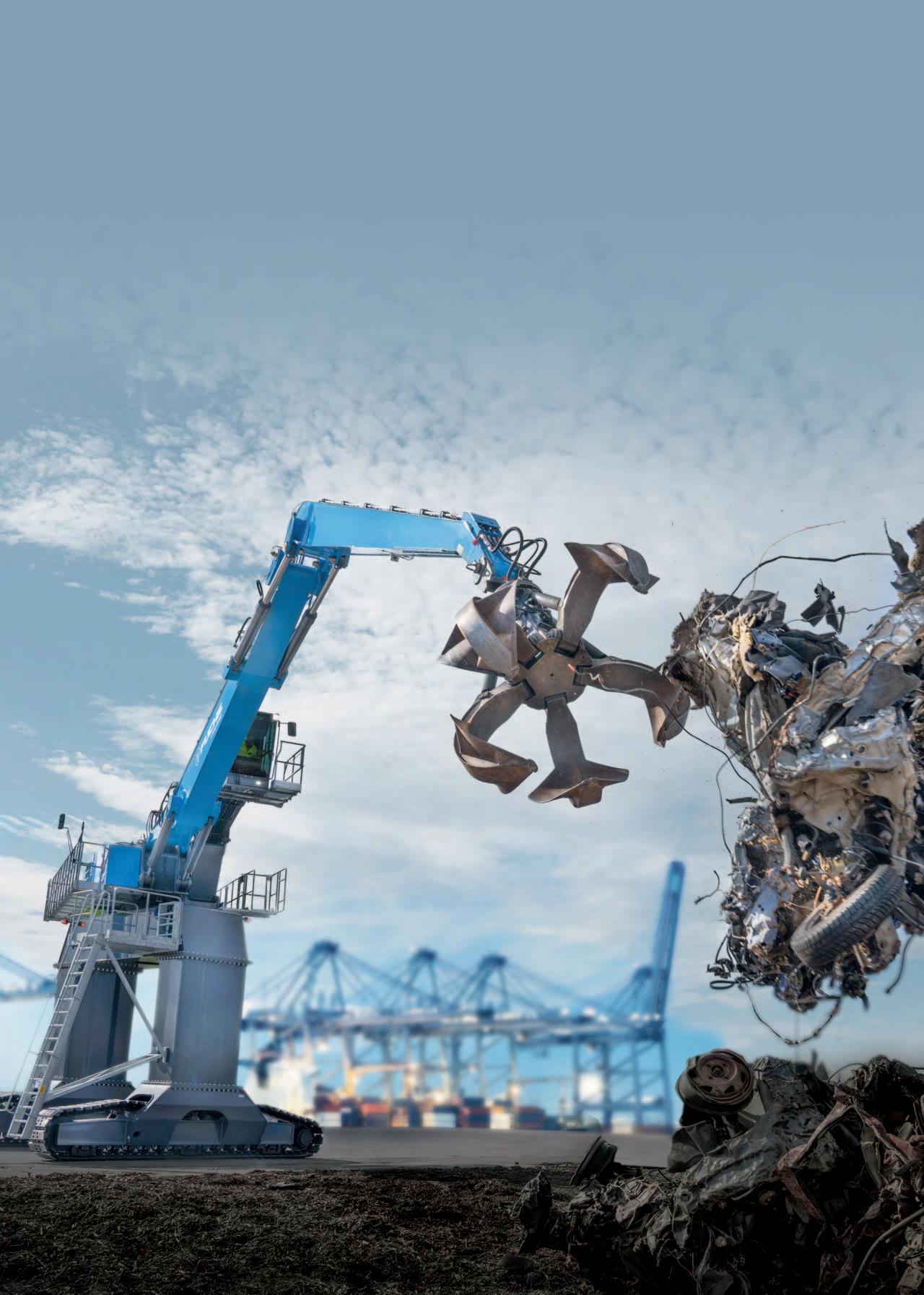
Blug grabs for onboard & shore-based cranes for smooth bulk operations
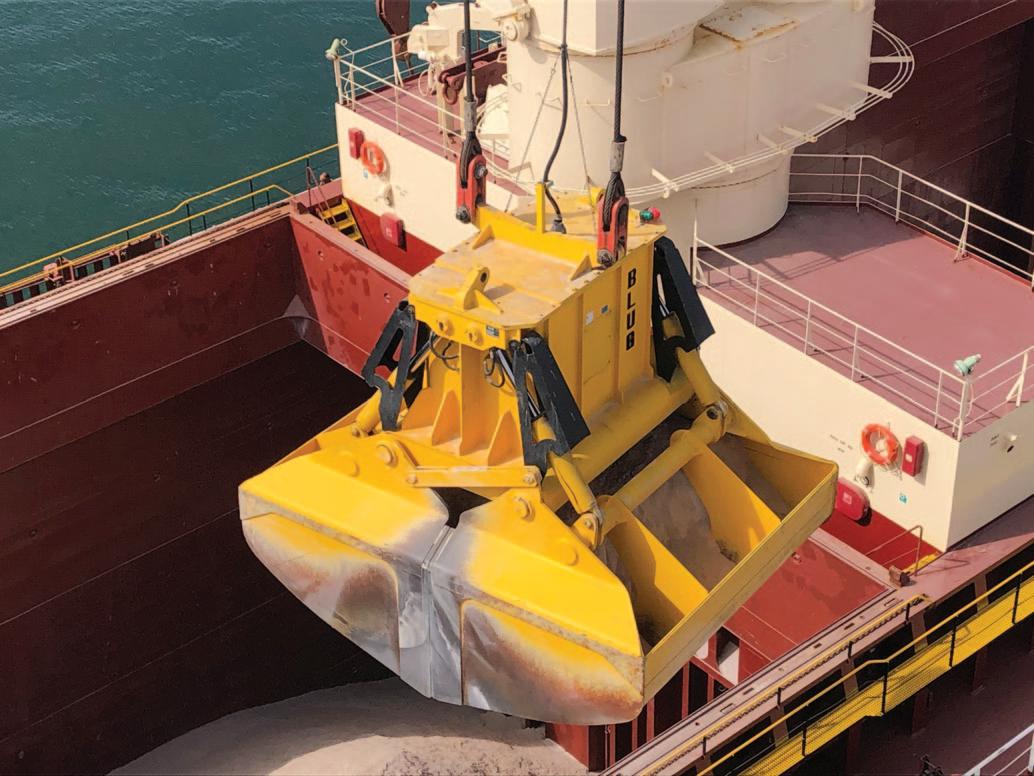
In 1965, Spanish grab specialist Blug Ibérica S.A. was founded by Jesus Letona with the clear idea of giving adapted solutions to any handling or production need, principally in the metallurgical sector. For many years the company has successfully designed different types of rolling mills, cutters, presses, roller tracks and many other machines of great technical complexity, always maintaining the company’s brand guarantee of quality.
At the same time, Blug also gained significant experience in grabs — from orange peel grabs, clamshell grabs and tongs, designed and manufactured to handle a wide variety of materials. The company’s grabs have found application all across the bulk industry, for ship- and shore-based cranes. The market was very positive about Blug’s grabs, allowing the company to specialize in these types of products.
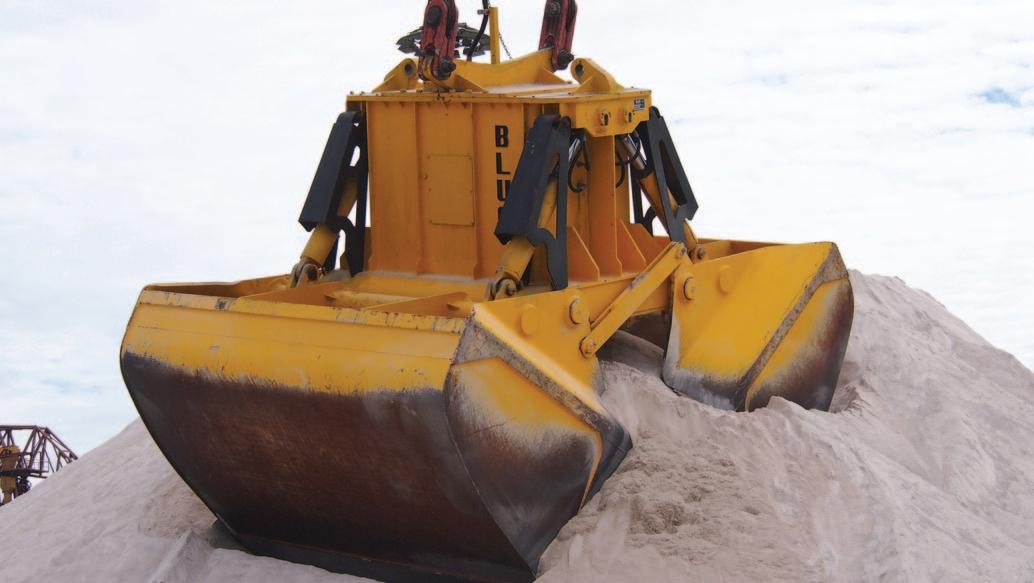
In 1993, Blug Ibérica became Credeblug
S.L., heralding a new stage in the company’s history in which Blug products have become a reference worldwide. With more than 5,000 machines manufactured, Credeblug offers an extensive handling solutions’ catalogue and is technically and structurally ready to face new challenges as well as continuously evolve its products and systems.
Since its inception, Blug’s grabs, tongs and grapples have been exported to over
Grab stronger performance
konecranes.com/generation6
mhc-product-advisor.konecranes.com
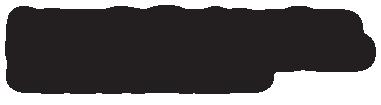
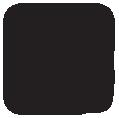
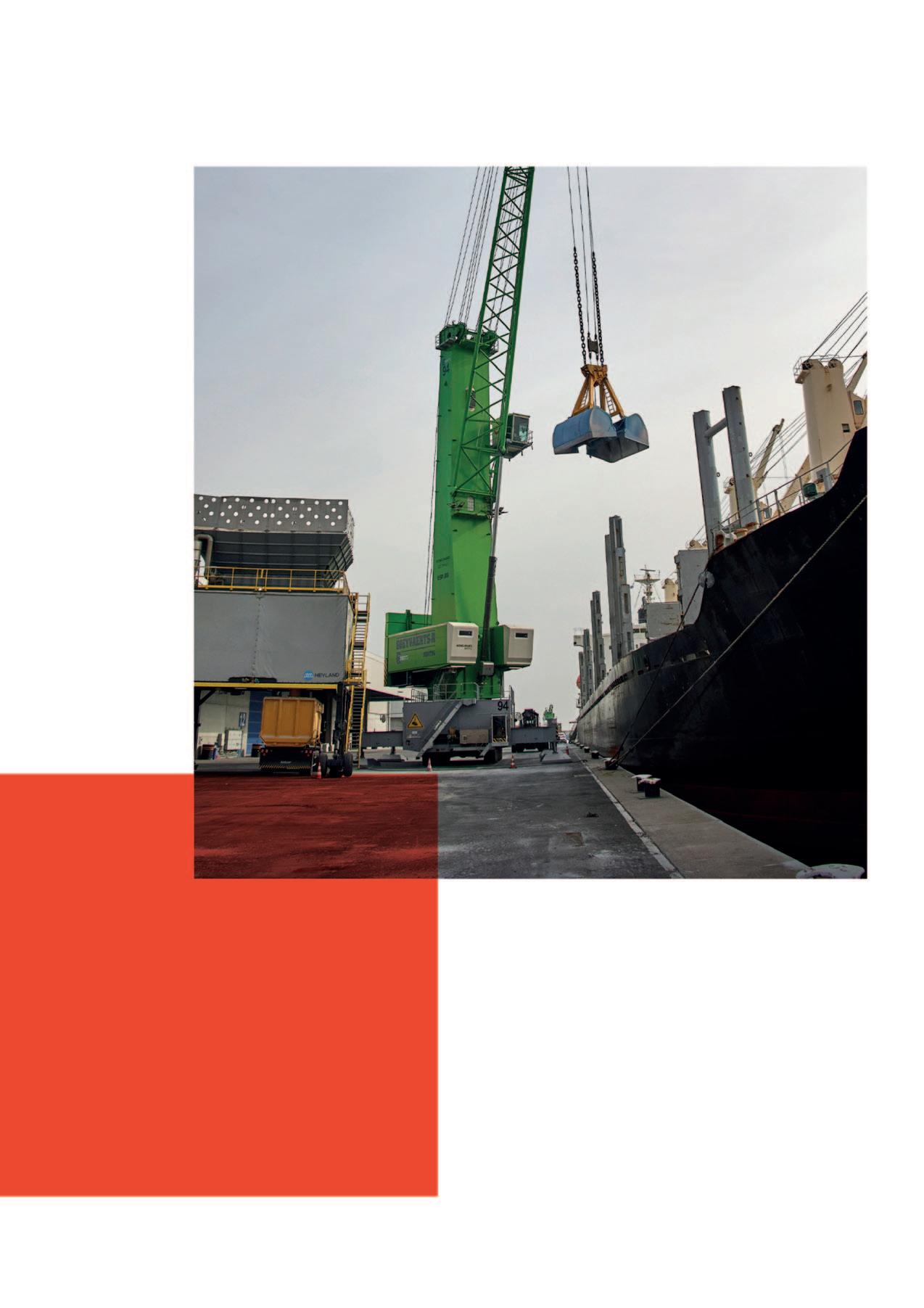
Konecranes Gottwald Mobile Harbor Cranes ensure highly efficient handling of bulk materials of all kinds. Our Generation 6 four-rope grab cranes will impress you with their robustness. With their 74 t grab curves and high classifications for a long service life, they handle up to 2,200 tph. The result: strong performance over the long term – even in continuous operation.
Strengthen the efficiency of your bulk handling with our new Generation 6!
Just scan this QR code to configure the right crane model for your needs56 countries. During that time, they have become renowned worldwide in the material handling market. The company’s international ambitions, and geographical expansion, have led it to export more than 70% of its turnover.
Credeblug is at the forefront of the design and manufacture of equipment for the domestic market and has one of the most extensive catalogues of handling solutions on the market. The Credeblug range responds to new customer
requirements through specific solutions for each application, with excellent product recognition.
Solutions that Credeblug offers include:
v orange peel grabs for MSW (municipal solid waste), biomass, scrap, industrial waste, shredded chips, rocks, etc.;
v clamshell grabs for biomass, coal, clinker, minerals, sludge, cereals, sand, fertilizers and all types of bulk materials; and
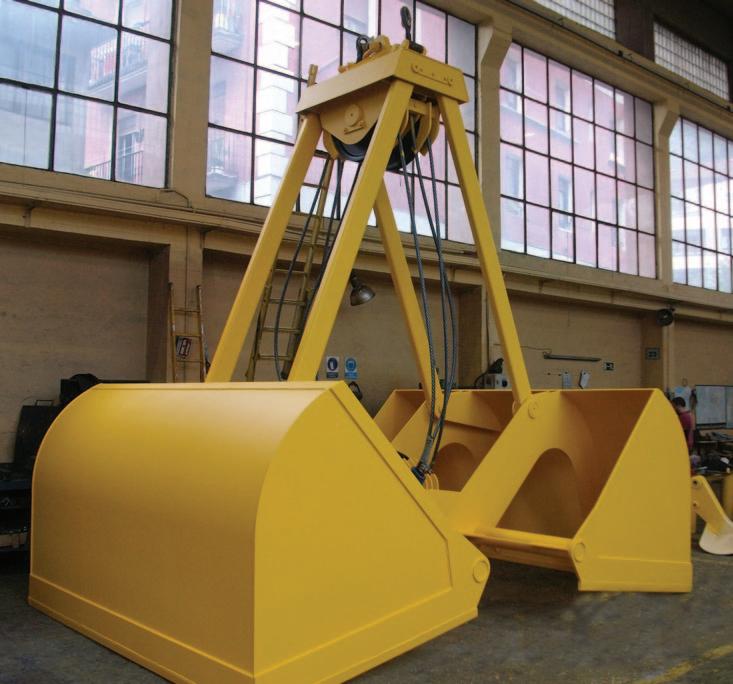
v tongs and grapples for coils, slabs, ingots, paper coils, pipes, logs, dowels, etc.
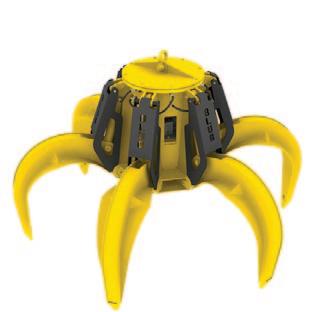
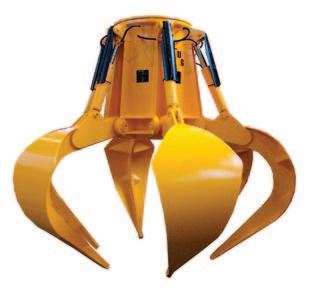
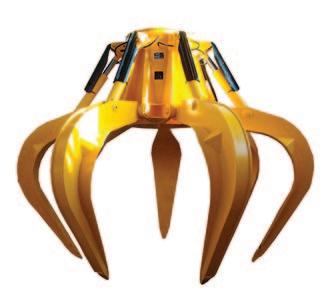
Credeblug is also fully market oriented and continues to evolve and consolidate its position as a global service provider. It has a global network of services distributed both internationally and in Spain to offer more robust and efficient machines.
Credeblug’s continuous innovation has been especially valued, and has been recognized by the IBJ 2010 & IBJ 2017 award as the world’s best handling machinery manufacturer — Best Grab.
ARIABLE FLOW HYDRAULIC POWER PACK
The hydraulic circuit of Blug’s grabs are equipped with top brand elements (Parker, Rexroth and Vickers) which are necessary to control and prolong the life of the machine and its components. The variable flow hydraulic system optimizes the power developed during the opening/closing of the machine at each movement. It also reduces oil heating by more than 40% compared with fixed flow circuits. The hydraulic systems in Blug’s equipment minimize the CO2 emissions associated with electrical consumption, offering excellent energy consumption.
EPAIRS, MAINTENANCE AND OVERHAULS
BLUG attaches great importance to the reconditioning of its machines in order to extend their useful life, and is able to carry out repair and maintenance service for its customers.
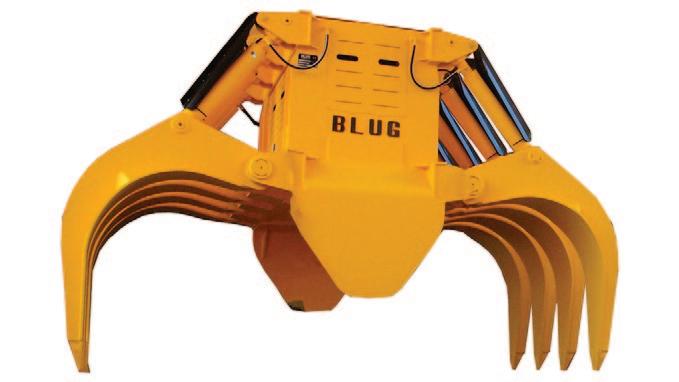
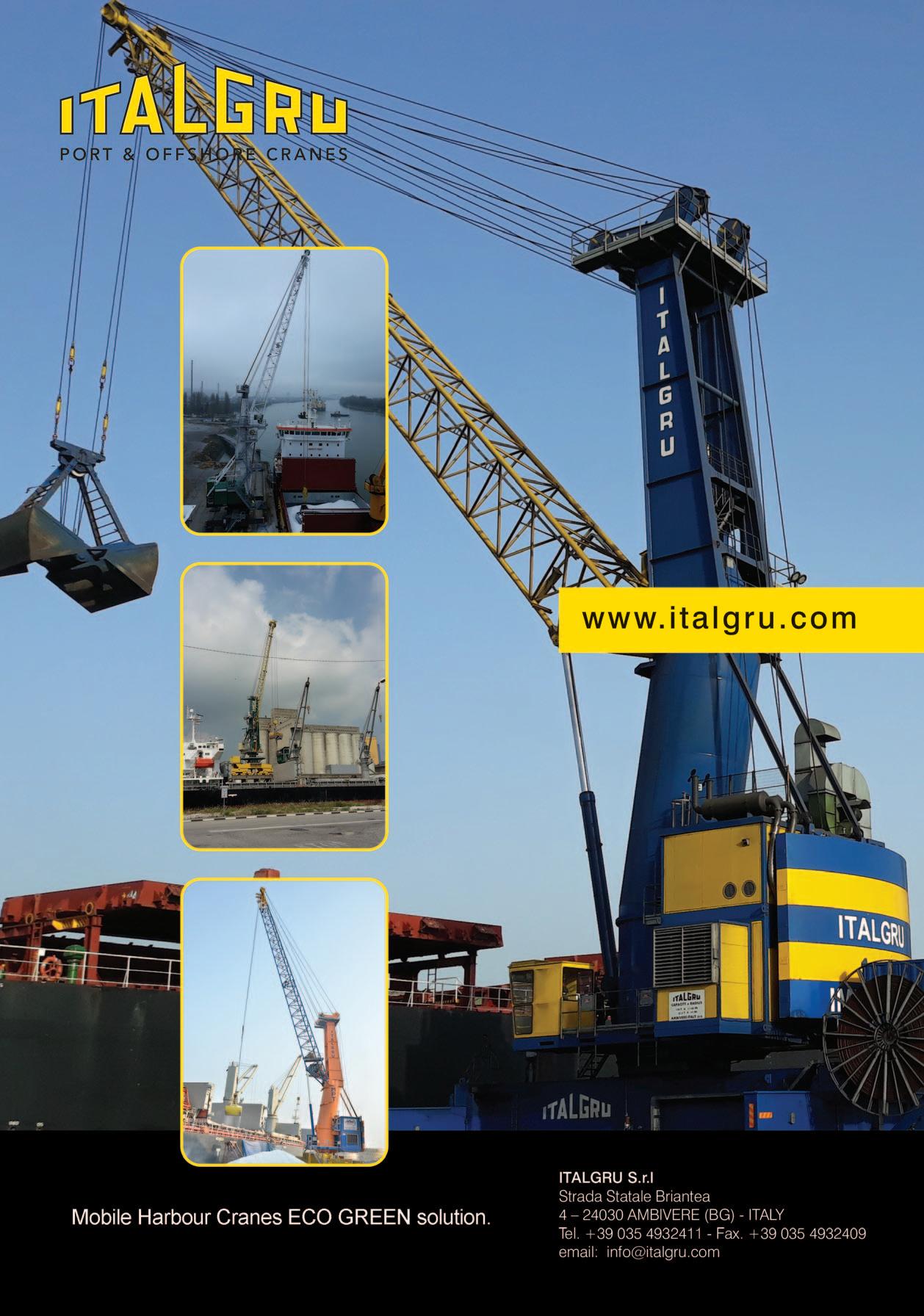
Negrini’s adaptive grab works with Industry 4.0 for optimized performance
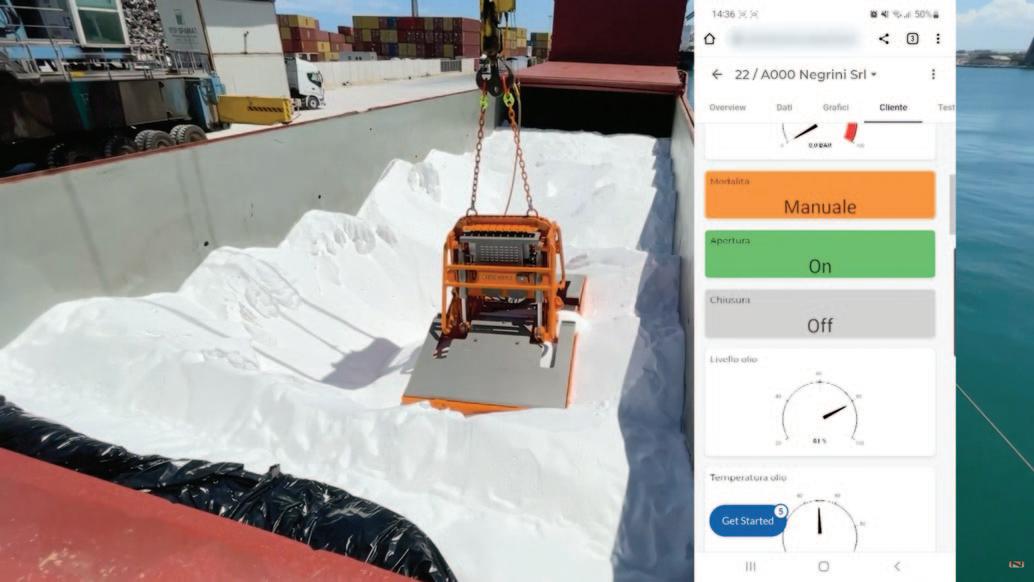
The business philosophy of Italian grab manufacturer, Negrini srl, is centred on a professional and a versatile approach to the different requirements of its customers.
Ongoing research into improving quality, showcased in the entire range of products offered by Negrini has led to dynamic, innovative and cutting-edge developments in engineering.
One of the company’s significant recent developments is its application of an Industry 4.0 solution to its grabs, which has allowed it to develop a unique product on the market: an adaptive grab that optimizes its operation in real-time, based on the operations carried out and the materials handled. Negrini Srl’s Industry 4.0 equipment offers remote access, data logging and alarm management.
The new development is the starting point for what has become a new phase of industrial design and business planning implemented by owner Massimo Negrini: “The desire was not to limit ourselves to tax benefits, but to develop a useful and functional device. This is how we achieved a unique solution in the market.”
In the construction of material handling equipment, the manufacturer is confronted with design, economic and service constraints. The grabs of Negrini Srl — orange peel grabs, clamshell grabs, diaphragm wall grabs and draglines — are built according to specific criteria determined by the material that the customer has to handle. The heart of the grab is the hydraulic power unit, which
drives the pistons that open and close the device for the number of cycles required for loading and unloading.
Without information from the operation of the equipment, the manufacturer doesn’t have accurate information about the actual critical operating thresholds. He has to provide high safety margins for the components, the energy supply and the operating pressure of the hydraulic power unit, to ensure maximum performance throughout the duration of operations, without interruption. Downtime is expensive: in the harbour sector, penalties can be as high as $25,000 per day per ship for the manufacturer responsible for the downtime.
Negrini Srl has included the IXON Cloud solution to make its equipment more efficient, offer better services to its customers and stand out from its competitors. The IXrouter installed on the grab collects real-time data from the Siemens PLC and transmits it to IXON’s IIoT platform.
The IXON solution is an integral part of the equipment, interacting with the grab in both readings and settings: based on predefined intervals, the grab is reprogrammed as forces and speeds change, depending on the operations it’s performing. This is a particular application of machine learning that allows Negrini Srl to supply the only adaptive grab on the market and to be a partner of the major players in the harbour, steel and
construction sectors on the Italian and European markets: Arvedi, Acciaierie d’Italia, Italgru, Gottwald (Konecranes group), Liebherr and I.P.M. from Pasquale Divella.
REMOTE TROUBLESHOOTING AND COLLABORATION WITH CUSTOMERS
Massimo Negrini emphasizes the simplicity and reliability of the IXON Cloud solution for remote assistance activities. In a particular emergency situation, Negrini received an alarm from its customer Arvedi, the largest player in the steel industry in Italy. Negrini was able to remotely access the machine via the IXON app to intervene from his smartphone. He corrected the value of the hydraulic pressure of a grab in operation and solved the problem. The data logging feature allows the company to record and store process data for up to seven years, far exceeding the data retention requirement outlined in the Industry 4.0 Italian regulation, which is currently three years.
Together with alarms and notifications, the company can support the customer with just-in-time scheduled maintenance activities, and notify them when attention thresholds (low oil) or critical thresholds (boiling oil) are reached, before critical grab components are irreparably damaged.
Monitoring data on the functioning of the equipment has allowed Negrini Srl to develop excellent collaborations with its customers. They appreciate the assistance and maintenance services offered by the
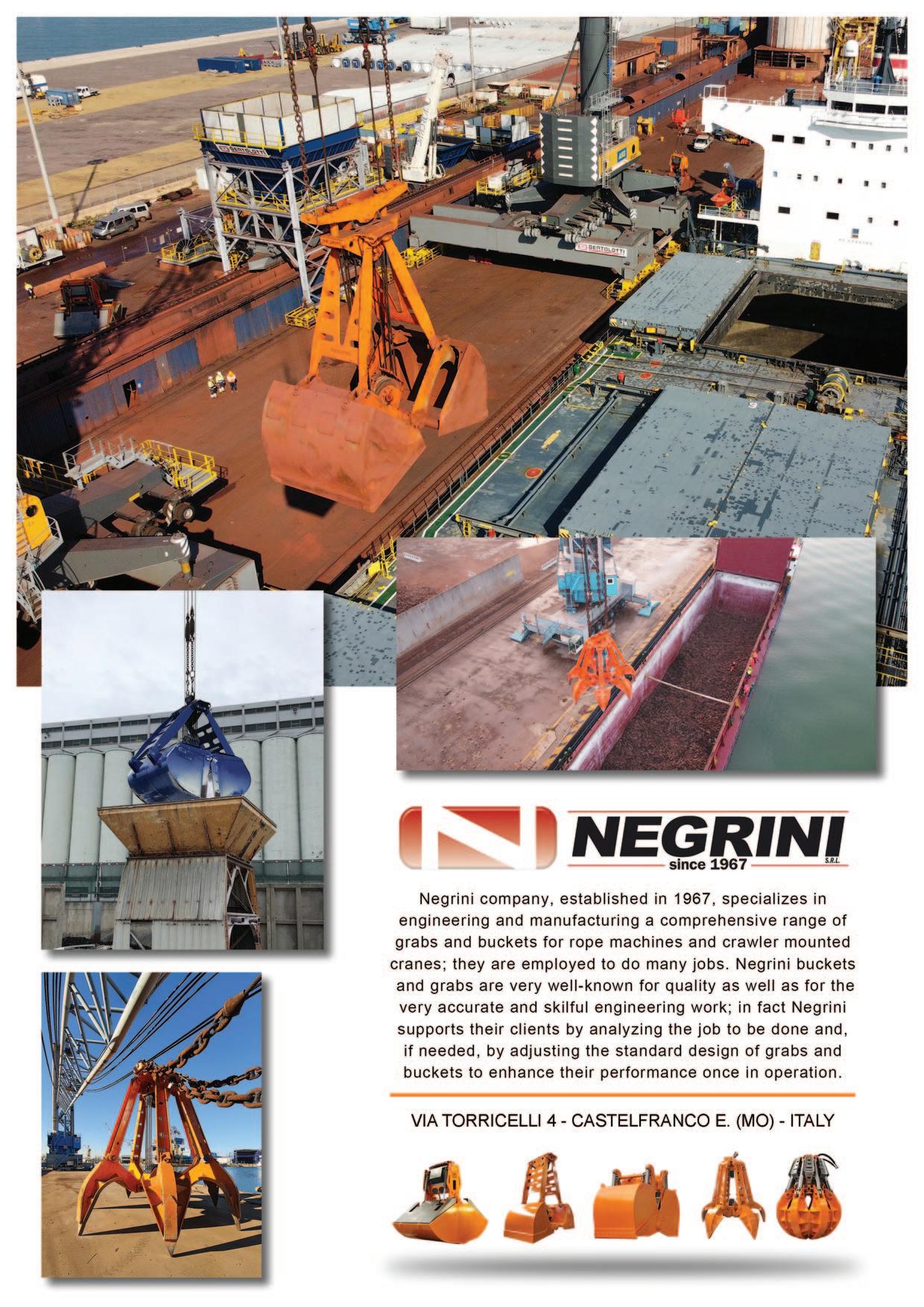
manufacturer, to the advantage of a generalized efficiency
NEXT CHALLENGE : FURTHER REDUCE ENERGY CONSUMPTION
One of the main challenges manufacturers are facing is the cost of energy. For years, Negrini’s plant has been equipped with photovoltaic panels that cover most of the energy needs of production activities. But the need to reduce the energy impact goes far beyond this and affects the entire supply chain. The possibility of collecting and analysing large quantities of data provides valuable information for the design of increasingly high-performance products and services, with a significant reduction in costs and waste.
Thanks to the possibility of monitoring and optimizing the operation of the grab in real time, energy consumption is only as high as necessary. In concrete terms, this means a reduction (from 30% to 70%) in energy absorption and costs and stress on the components and the hydraulic power unit of the grab, as well as a significant improvement in the customer’s equipment (OEE — Overall Equipment Effectiveness), starting with the electrical equipment.
The result: equipment that works harder, works longer, costs the manufacturer less and provides better service to customers. Massimo Negrini has no doubts: continuous innovation is his goal and IIoT is a key element in achieving it.
DRY BULK HANDLING GRABS PRODUCED BY NEGRINI
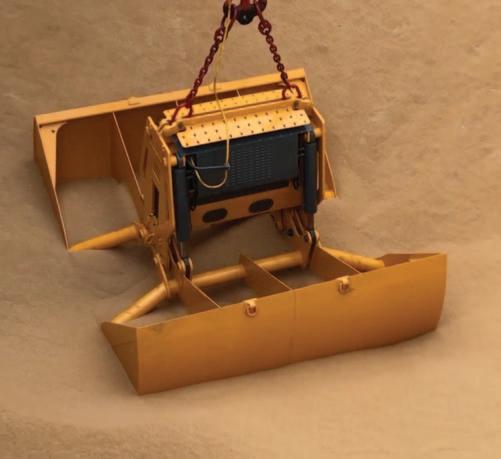
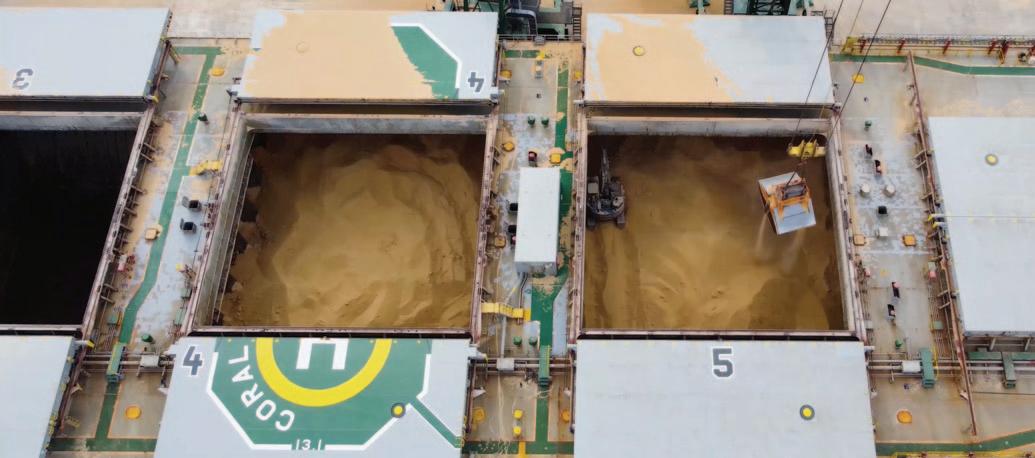
FOR THE MARITIME INDUSTRY
v environmental hydraulic clamshell;
v hydraulic clamshell grab;
v clamshell grab for hydraulic excavator; and
v hydraulic orange-peel grab.
FOR PORTS
v two- or four-dual-scoop grab;
v radio-controlled single-rope grab; and
v two- or four-rope orange-peel grab.
ACTIVITY
The reliability of Negrini srl lies in its professional expertise and experience acquired by the entire, highly specialized workforce. Negrini’s technical department is always on hand to tackle and solve any technical problem, explaining and motivating the solutions adopted. When necessary, Negrini srl calls upon partners to find solutions to the most complex design issues.
PRODUCTION SYSTEM
Every customer request is carefully assessed for feasibility from both a
technical and capacity point of view.
The requested elements, including the drawings, are examined and planned in collaboration with the head of department to guarantee delivery times, reliability and the best use of resources.
The technical data, including the drawings, are entered into a Cad-Cam electronic processing and 3D CAD solid modelling system for a more efficient management of the product and rational organization of the machinery.
Before shipping occurs, a final test is carried out by the head of production, overseen by the company owner.
The company’s policy is to supply products to firms operating in the excavation and handling industry, developing customized projects.
All products adhere strictly to the technical specifications and drawings and are sourced from reliable and well-established suppliers.
On specific request, Negrini can provide individual certificates and reports.
WELDING PROCEDURES
Negrini works with qualified welders according to UNI EN ISO 9606-1:2013, to cover the welding procedures required.
The welders are regularly tested and work in their area of expertise.
NON DESTRUCTIVE TESTING
On request, these tests are carried out by external qualified personnel. The testing procedures comply with current European standards. DCi
Professional companies in more than 110 countries worldwide work with Verstegen grabs, because our grabs offer them the highest reliability and best productivity. Combining our extensive knowledge and experience with the feedback from our loyal customers results in optimized grabs for all bulk materials and unloading situations. We call this ‘Grab Intelligence’.


Looking for increased reliability and productivity, lower maintenance costs and an extended lifespan? Let us know, because together we can move mountains.
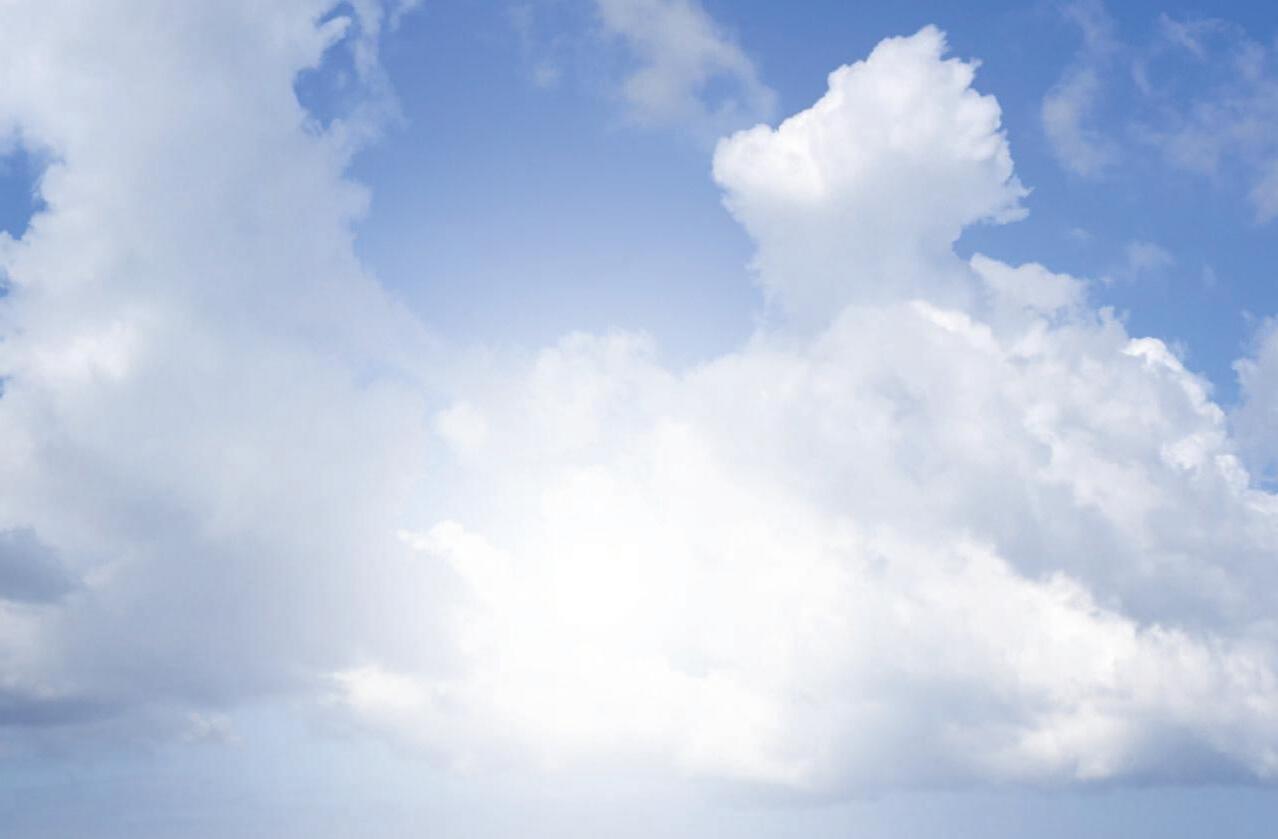
LET’S MOVE MOUNTAINS
Taking the high road
with Hwy H2O: focusing on the Great Lakes & St. Lawrence Seaway System
The Great Lakes–St. Lawrence
System is a
waterway extending 3,700km (2,340 miles) from the Atlantic Ocean to the head of the Great Lakes, in the heart of North America. The St. Lawrence Seaway portion of the System extends from Montreal to mid-Lake Erie. Ranked as one of the outstanding engineering feats of the twentieth century, the St. Lawrence Seaway includes 13 Canadian and two US locks.
The Great Lakes and St. Lawrence River have been major North American trade arteries since long before the US or Canada achieved nationhood. Today, this integrated navigation system serves miners, farmers, factory workers and commercial interests from the western prairies to the eastern seaboard.
With economic output estimated at $6 trillion, the provinces and states bordering the Great Lakes–St. Lawrence Seaway System account for 30% of combined Canadian and US economic activity and employment.
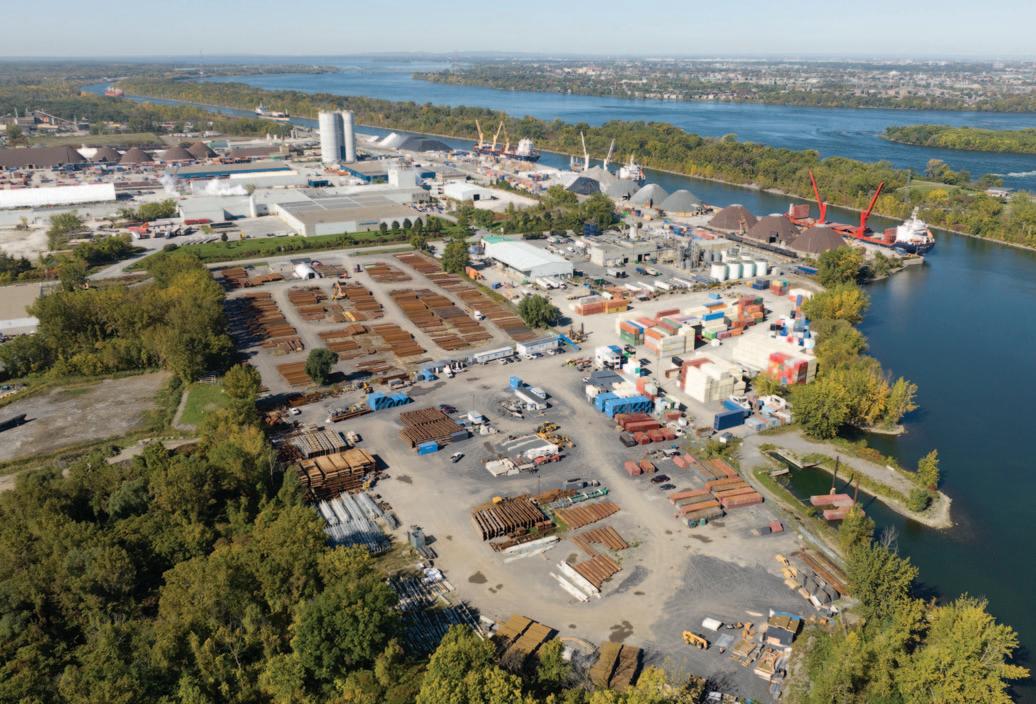
The region would rank as the third largest economy in the world if it were a country. Positioned at the core of this economic powerhouse, the Great Lakes–St. Lawrence Seaway System serves as a vital supply chain.
The Great Lakes/St. Lawrence Seaway was built as a binational partnership between the US and Canada, and continues to operate as such. Administration of the system is shared by two entities, the Great Lakes St. Lawrence Seaway Development Corporation (GLS)
QUICK FACTS
v Cargo shipments on the Great Lakes-Seaway system generate $45 billion of economic activity and 238,000 jobs in Canada and the US.
v The binational St. Lawrence Seaway serves as the linchpin within the broader waterway, connecting the lower St. Lawrence River to the Great Lakes. Beginning in Montreal and extending to points west, the Seaway’s 15 locks (13 Canadian and 2 U.S.) enable ships to climb a total of 168 metres from sea level up to Lake Erie.


in the US, a federal agency within the US Department of Transportation, and The St. Lawrence Seaway Management Corporation in Canada.
The Great Lakes St. Lawrence Seaway Development Corporation (GLS) is a wholly owned government corporation created by statute on 13 May 1954, to construct, operate, and maintain that part of the St. Lawrence Seaway between the Port of Montreal and Lake Erie, within the territorial limits of the United States. Trade development functions aim to enhance Great Lakes/St. Lawrence Seaway System utilization without respect to territorial or geographic limits. The mission of the Corporation is to serve the US intermodal and international transportation system by improving the operation and maintenance of a safe, reliable, efficient, and environmentally responsible deep-draught
waterway, in co-operation with its Canadian counterpart. The GLS also encourages the development of trade through the Great Lakes Seaway System, which contributes to the comprehensive economic and environmental development of the entire Great Lakes region.
The St. Lawrence Seaway Management Corporation is a not-for-profit corporation responsible for the safe and efficient movement of marine traffic through the Canadian Seaway facilities, which consists of 13 of the 15 locks between Montreal and Lake Erie. The Corporation plays a pivotal role in ensuring that the waterway remains a safe and wellmanaged system, which it shares with its American counterpart, the Great Lakes St. Lawrence Seaway Development Corporation.
BI-NATIONAL MARKETING INITIATIVES
HWY H2O provides direct access to North America’s commercial, industrial, and agricultural heartland, driving sustainable infrastructure advancement while connecting stakeholders to their market. The SLSMC and the GLS collaborate on joint strategic initiatives.
Participation in conferences like Breakbulk Americas, Breakbulk Europe, and other cargo-focused events expands the System’s advantages. Interactions among carriers, shippers, freight forwarders, ports, and terminal operators foster new opportunities.
The annual HWY H2O Conference attracted attendees from various commodity sectors and industry interests, discussing emerging trends, new technology, and partner synergies.
SLSMC enjoys a year of remarkable growth and resilience
In his annual message, Terence F. Bowles, President and CEO, The St. Lawrence Seaway Management Corporation (SLSMC) looked back at 2022, describing it as “a year of remarkable growth, resilience, and, most importantly, a renewed commitment to sustainability.” He noted the importance of ESG (environmental, social, and governance) initiatives, a prime example of which is the SLSMC’s long track record in generating clean hydro-electric power.
Traffic results — 2022 Navigation Season (million tonnes)
Notably, the Welland Canal operates on self-sufficient energy, resulting in a substantial reduction in carbon footprint. Says Bowles, “Our decarbonization efforts include the gradual replacement of gasoline and diesel-powered equipment with electric alternatives, enabling the SLSMC to surpass the greenhouse gas emission reduction targets set by the Federal Government for 2030.
Bowles expressed pride in the SLSMC’s resilience in the face of economic uncertainty and global conflict, when it “continued, without pause, to support shippers and carriers supplying the essential needs of society, including grain, salt, steel, aluminum, cement and potassium.”
Bowles knows that reliability is key to the SLSMC’s success. Its consistently high reliability rate of over 99% makes it a trusted partner for industries and communities, and also helps reduce fuel consumption and emissions.
TRAFFIC RESULTS
Despite the many headwinds faced in 2022, such as global supply chain issues, droughtreduced crops, geopolitical tensions, and market uncertainties, the Seaway continued to deliver.
Canadian grain movements decreased v by 7.5% or 0.70 mt, with droughtreduced Prairie crop impacting exports in the first half of the season. US grain exports started strong and v finished the navigation season 5.9% or 0.08mt above 2021 exports.
Iron ore traffic finished off the year v below 2021’s record results by 9.8% (0.67mt [million tonnes]).
Coal movements trailed 2021 results v by 16.3% (0.35mt).
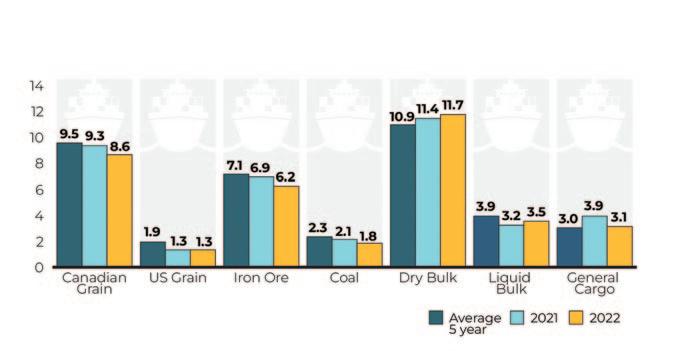
Dry bulk cargo movements ended the v season ahead of 2021 by 2.7% (0.31mt), led by potash exports and salt replenishing, up 112.8% (0.58mt) and 15.8% (0.44mt), respectively.
Liquid bulk traffic increased by 8.8% or
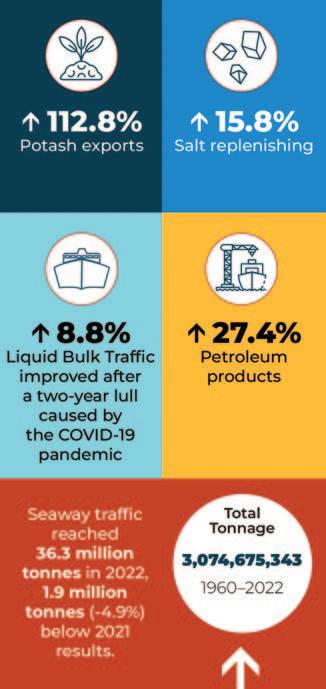
0.28mt compared to 2021, driven primarily by a 27.4% (0.53mt) uptick in petroleum products.
General cargo posted a 21.8% or v 0.85mt decline, led by a drop of close to 0.50mt in both steel and slab imports.
OPERATIONAL EXCELLENCE AND SAFETY

The SLSMC believes in a ‘Zero Harm’ safety culture. It aims to deliver secure, consistent and predictable service to Seaway customers, and to continue to enhance the organization’s culture of continuous improvement and leverage technology.
Safety is a core value of the Corporation, with the utmost priority placed on the well-being of employees, ensuring their safe return after each shift. The SLSMC takes great pride in its commitment to safety, which is further highlighted by these excellent results.
In January 2023, the Montreal/Lake Ontario region celebrated a remarkable achievement: 1,000 consecutive days without a lost-time incident. Adding to this exceptional record, the Iroquois employees, in the Montreal/Lake Ontario
section, reached an astounding 30 years without a lost-time incident in March of 2023. These milestones are a testament to the SLSMC employees’ unwavering commitment to cultivating a safe and secure workplace.
MARINE SAFETY AND MARINE SECURITY

The marine mode of transportation remains the safest and most reliable means of moving cargo. During the 2022 season, there were ten commercial vessel incidents in which damage occurred to vessels or Seaway structures, resulting in a vessel incident rate of 2.2 per 1,000 transits. This result demonstrates that marine transportation is a safe mode of transportation. Following the renewal of a Transport Canada Marine Facility Security Certificate in 2022, the SLSMC enhanced security measures to protect critical infrastructure, such as improved intrusion detection.
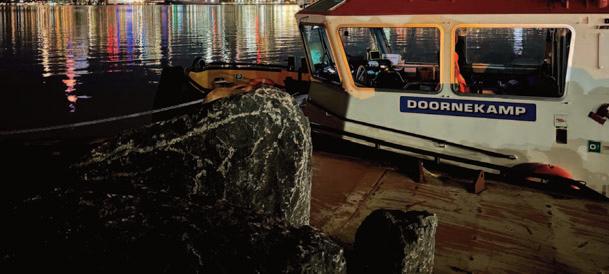
NAVIGATION SEASON
The St. Lawrence Seaway’s 64th navigation season opened on 22 March 2022 for the Montreal/Lake Ontario (MLO) Section and on 24 March 2022 for the Welland Canal

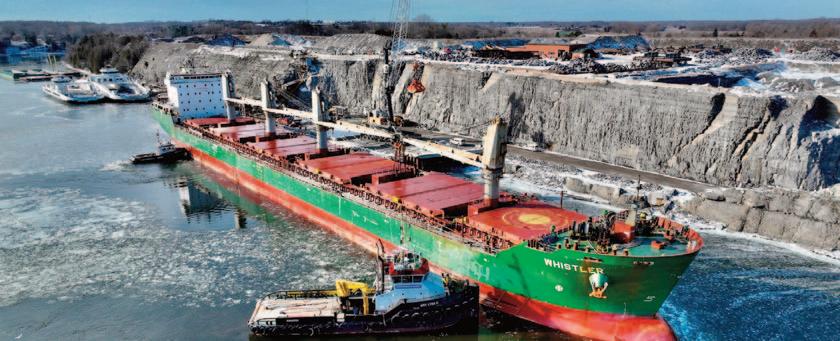
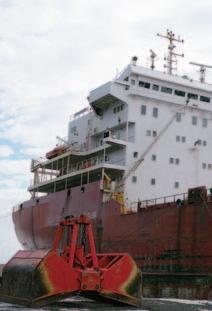
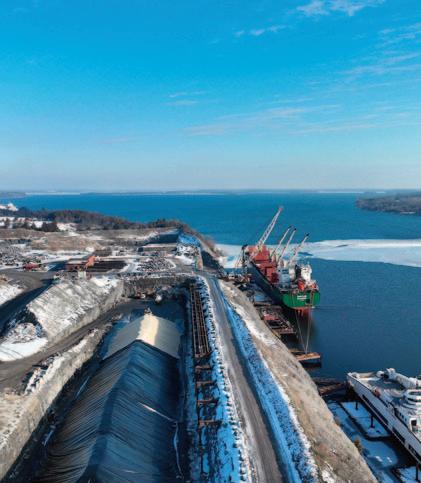

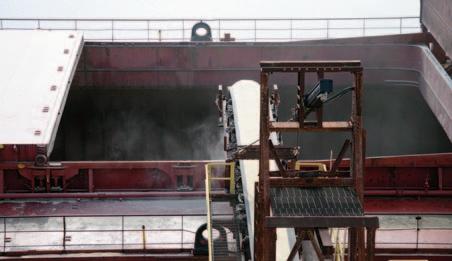
(Niagara Section). The last commercial transit through the system occurred on 1 January 2023, providing a total of 286 days of navigation.
INFRASTRUCTURE MANAGEMENT AND ASSET RENEWAL
The Seaway’s competitive standing as a critical link in the supply chain relies on a secure, reliable, and economically efficient transportation infrastructure. To achieve this, the Corporation implements a robust Asset Management System, ensuring consistently high system availability.

In 2022, the SLSMC invested $73.7 million in infrastructure renewal and maintenance, bolstering the strength of the supply chain and promoting the long-term safety and economic growth of communities.
Examples of major projects executed over the course of the 2022/2023 Fiscal year include:
Niagara Section (Welland Canal): v Welland Lock 8, complete removal of gates in anticipation of replacement; and replacement of the steel deck at the Queenston St. Bascule bridge (Homer Bridge).
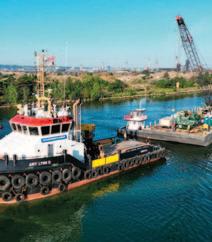
SERVICES
n Material/Product conveyor loading 1,000 tonnes/hr
n Covered/dry stockpile, numerous volume options
n Gearless vessel discharging via Port crane 300 MT/hr
n Crushing/processing of aggregate materials on site
n Custom packaged options available
n Truck hauling of all materials
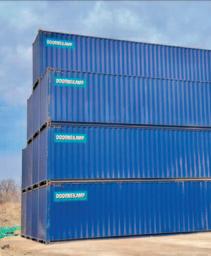
n Crane loading and unloading
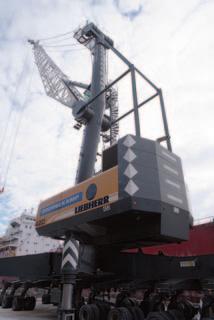
Fastest route to the Heartland of North America
The Great Lakes St. Lawrence Seaway System

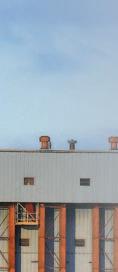
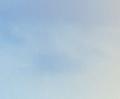
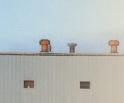
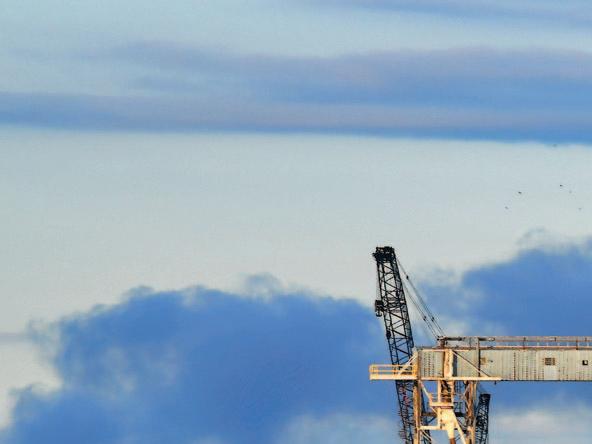
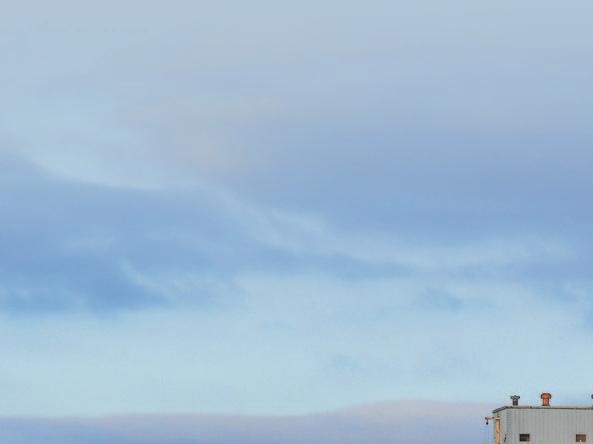
Sailing from Europe, Africa or South America, the Great Lakes St. Lawrence Seaway System enables carriers to bring cargo deep into the Heartland of North America. The 3,700 kilometer waterway consists of the St. Lawrence River, St. Lawrence Seaway, five Great Lakes and connecting deep-draft channels. Ports as far inland as Chicago, Illinois and Duluth, Minnesota are easily accessible.
Why stop at the East Coast when you can sail this close to your last mile?


The binational System consists of 110 ports in the United States and Canada. Skilled stevedores, freight forwarders, dock and crane workers, vessel agents and more are on hand to unload and load dry bulk cargo and swiftly connect ships with trains and trucks for last mile delivery.
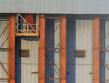

With a consistent reliability rate exceeding 99%, the Great Lakes St. Lawrence Seaway System provides global shippers with a simple, direct route to your destination.


Dry Bulk Cargo our specialty
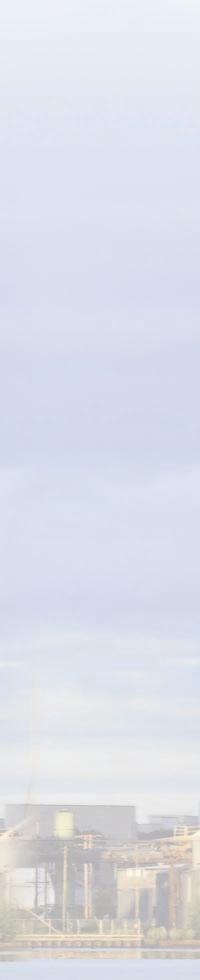
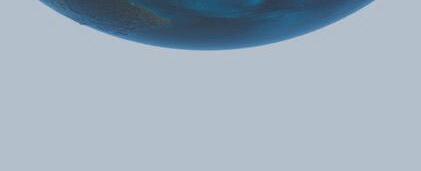

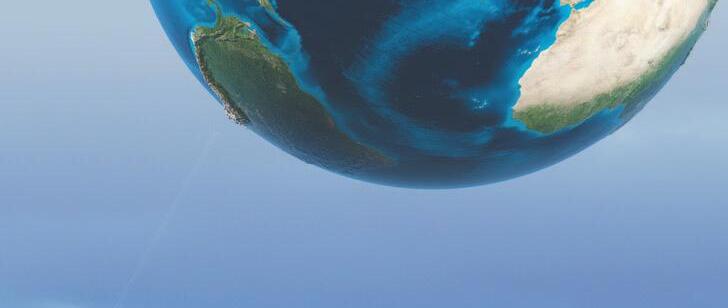

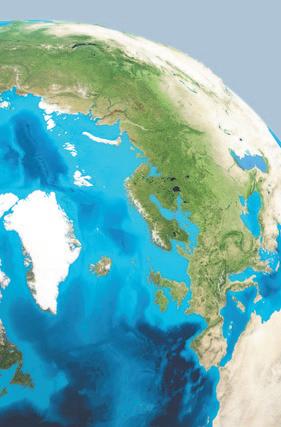
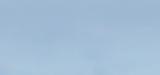
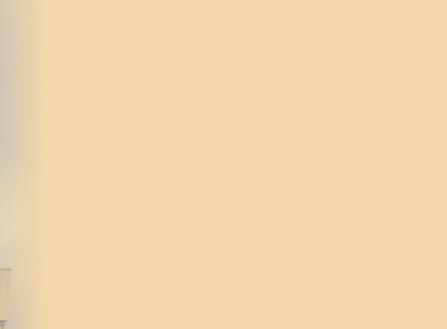
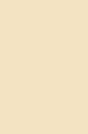
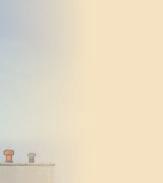

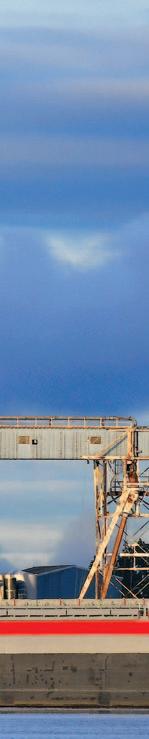

The ports and cargohandlers throughout the Seaway System specialize in moving dry bulk cargoes. Moving with efficiency and reliability, bulk cargo is a mainstay of the System.
New terminals with advanced and enclosed conveyor systems serve as key connectors to the last mile destination.
Bulk cargo handled in the Seaway System includes products that are loose and unpackaged, such as grain, sand and coal, which are typically loaded and unloaded via conveyor systems, as well as break bulk cargoes in bags, drums or bales. $6 trillion
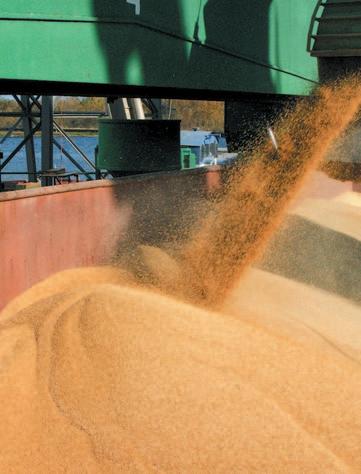

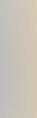
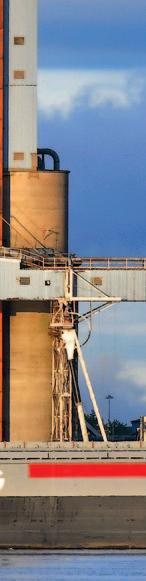
Great Lakes region Economic Impact
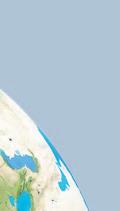
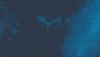

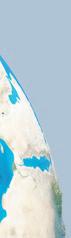
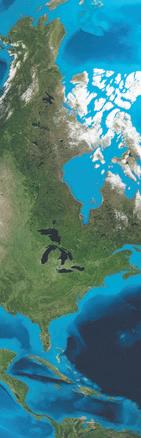

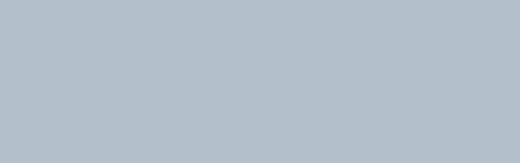
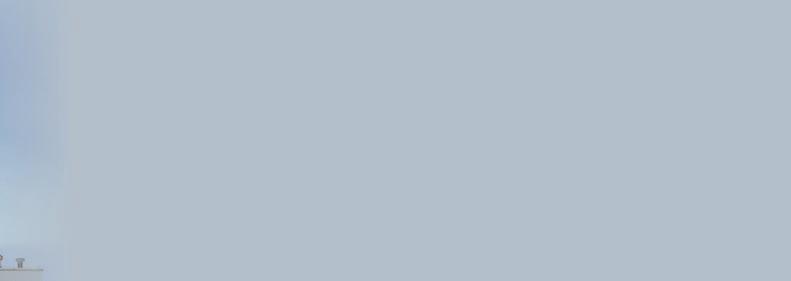
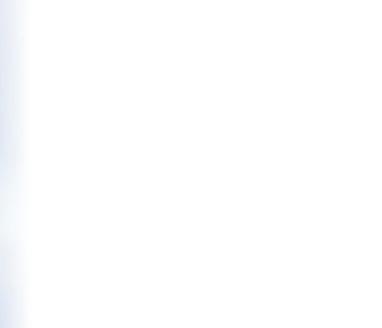
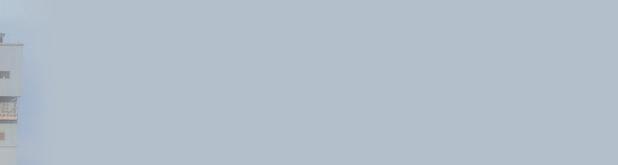
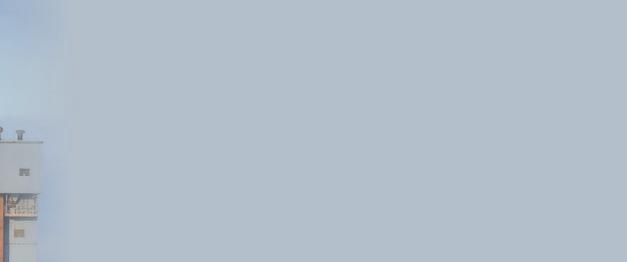
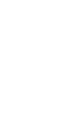

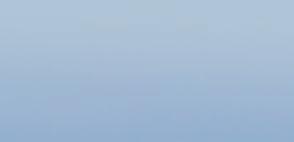
MLO
Section (Montreal/Lake v
Ontario): replacement of counterweight cables on the St-Louis de Gonzague vertical lift bridge (near Salaberry-de-Valleyfield, Quebec); and installation of new and improved air bubblers and air curtains at the St-Lambert lock, aimed to enhance the management of ice during winter operating conditions (on top, challenge of ice on wall, on bottom, installation of air bubblers).
TECHNOLOGY AND DEVELOPMENTS CYBERSECURITY
The SLSMC maintains a robust network infrastructure with high capacity, encryption, diversity, and resilience for smooth information transmission in automated systems. Multiple cybersecurity protocols prevent unauthorized access, monitor IT asset performance, and counter potential threats. IT specialists follow a comprehensive security framework, and employees receive training to detect and report social engineering tactics.
“Securing our critical infrastructure and data is paramount. While our dedicated IT team works hard to maintain robust cybersecurity protections, the collective vigilance of every employee remains vital in safeguarding against evolving threats.”
VOYAGE INFORMATION SYSTEM (VIS)
VIS, a collaborative data sharing environment, connects maritime stakeholders, strengthening the supply chain through informed mutual decision-making. This technology will: Create a virtual network for v stakeholders to exchange vital vessel voyage and transit information. Be an extension of the powerful v Seaway Traffic Management System (TMS) engine, supporting the decision-making processes. Improve scheduling and coordination v of resources for optimized vessel transit through the system. Improved planning can lead to GHG emission reductions
Together, VIS partners can: Address pain points and inefficiencies v in data exchange. Improve planning and execution of v vessel transits. Enhance scheduling of key resources. v
To ensure the system aligns with the marine industry’s reality, valuable insights and information needs were gathered from various industry stakeholders through consultations. Ongoing work continues on this collaborative initiative.
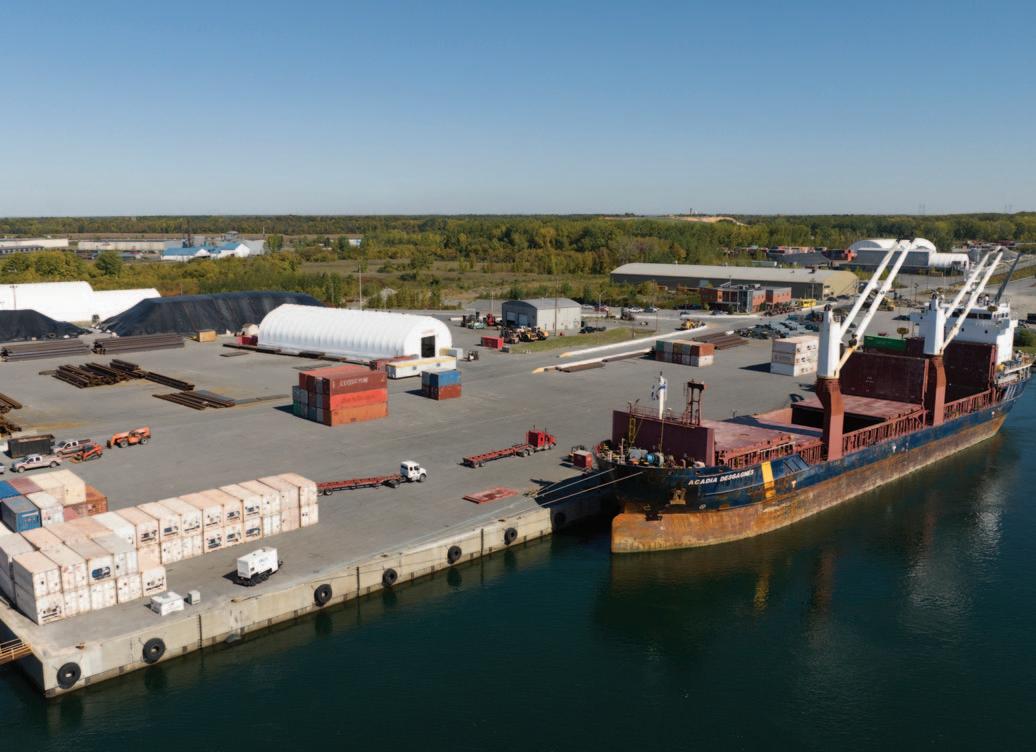
PATH TO NET ZERO
In support of the SLSMC’s commitment to reduce greenhouse gas (GHG) emissions and protect the environment, various initiatives and achievements were celebrated across the Corporation.
GHG EMISSION REDUCTION
Achievements: The federal government released the ‘Canadian Net-Zero Emissions Accountability Act’ in 2021, through which GHG reduction goals of 40–45% below 2005 must be reached by the year 2030. The SLSMC has already surpassed the Federal Government’s 2030 GHG reduction targets.
The reductions are due to activities, including: increased energy efficiency for SLSMC v buildings; replacement of fuel-powered v equipment with electrical equipment; increased fuel efficiency of corporate v vehicles.
GREEN MARINE PROGRAM
Achievements: the Corporation is an active and founding member of the Green Marine voluntary environmental programme, a world-leading environmental performance measurement programme for the marine industry.
Port of Belledune strengthens Canada’s supply chain with $25m conveyor loop investment
Belledune Port Authority is doubling its bulk cargo handling capacity with a new, $25m conveyor loop system, enabling more goods to be moved more quickly between vessels and to other modes of transport.
The northern New Brunswick port specializes in forest products, minerals, and energy. This expansion is part of a longterm plan to expand and diversify the port’s core business, with a renewed focus on renewable energy and green manufacturing.
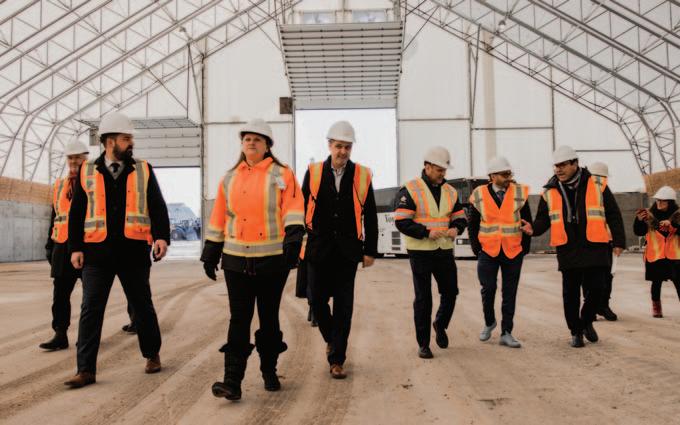
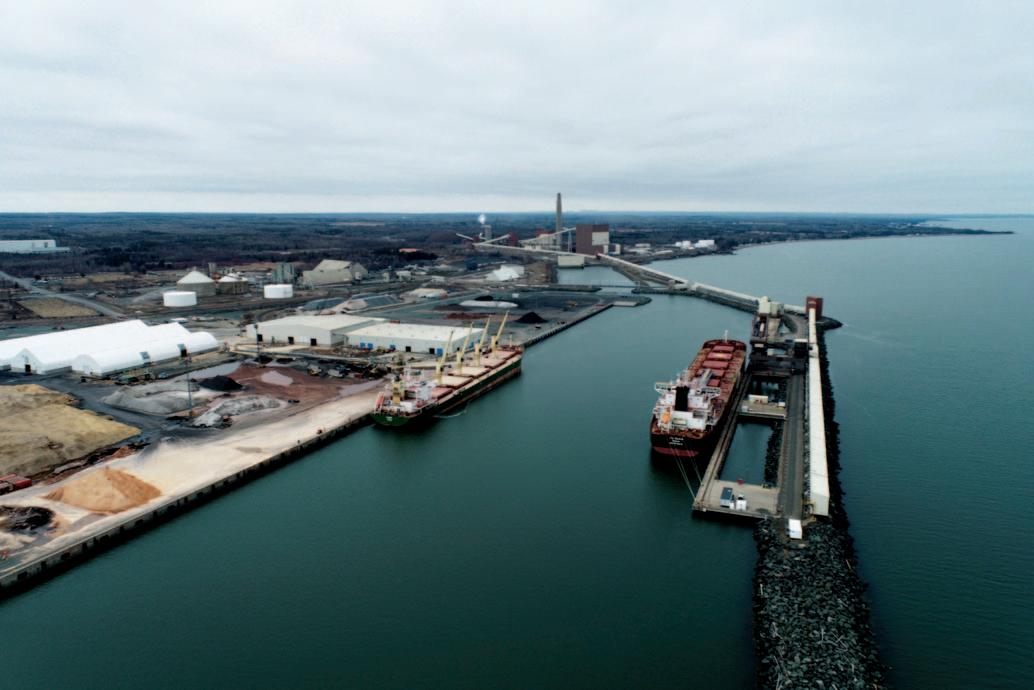
The investment is supported by the Government of Canada, the Province of New Brunswick, QSL, and BPA.
Canada’s then-Minister of Transport, the Honourable Omar Alghabra announced the federal government’s share of the investment, up to $12.5m from the National Trade Corridors Fund, during a visit to the port in early 2023.
The New Brunswick government contributed $4m from its Regional Development Corporation.
“We are partnering in the long-term development of the port which will create new opportunities for economic growth in the north,” said Réjean Savoie, minister responsible for the Regional Development Corporation. “This investment will
increase capacity and efficiency, making the Belledune Port Authority more competitive and prepared for new business.”
The funding will support the construction of a conveyor system that will alleviate congestion issues at Terminal 3 by using Terminal 2 to unload material in new laydown areas. This will increase the port’s capacity and efficiency and allow larger vessels to dock at Terminal 2, reducing the cost of shipping for the port’s clients. The new fixed conveyors will link the deep
water terminal to the staging area. Other works will include the renovation of existing storage, and the construction of a new warehouse and transfer tower.
“In addition to greatly enhancing the performance of our operations, the new conveyor system will electrify the movement of cargo and make an important contribution to reduce our operations’ greenhouse gas emissions,” said Denis Caron, president and CEO of the Belledune Port Authority. “This project is a game changer for our efficiency
improvements and allows our partner, QSL, a competitive advantage for cargo handling ... We are excited to work with public and private partners to invest in modern infrastructure that enables us to double our cargo capacity while reducing our carbon footprint and greening our operations. This new conveyor system is a game-changer for port operations, allowing us to move cargo more quickly and efficiently. With this project and others, we
are anticipating the needs brought on by climate change while transitioning to sustainable solutions for our business and operations.”
“At QSL sustainable development is a key to our business model,” said Robert Bellisle, president and CEO of QSL, the port’s stevedoring and logistics services company. “The Port of Belledune’s vision of a Green Energy Hub and its work with all stakeholders including First Nations is
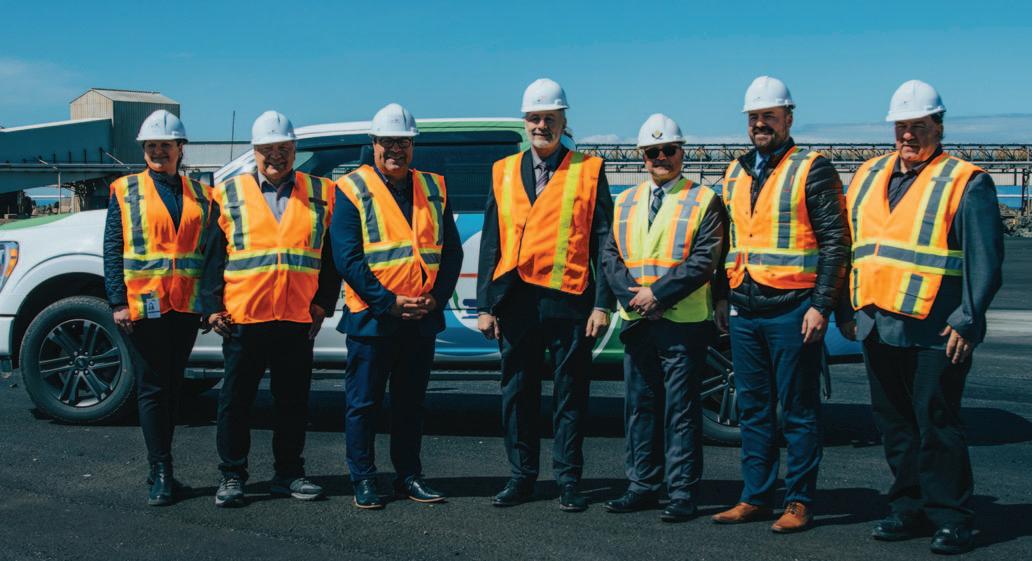
perfectly aligned with the reasons that propelled QSL to sign the United Nations Global Compact and why we are so proud to operate in Belledune.”
The port’s long-term development plan incorporates strategic initiatives to accomplish significant business growth over the next several years including the creation of a Green Energy Hub, which is intended to work as a catalyst for regional economic development.
Iron ore leading tonnage upturn in Duluth-Superior
Driven primarily by a very strong first half for iron ore shipping, total tonnage through the Port of DuluthSuperior tracked 11% ahead of last year’s pace through July 2023, topping 14mt (million short tons). Iron ore comprised more than 9.6mt of that total. A banner June float—nearly 2.6mt of iron ore — provided the biggest boost. It was the most in a single month since May 1993.
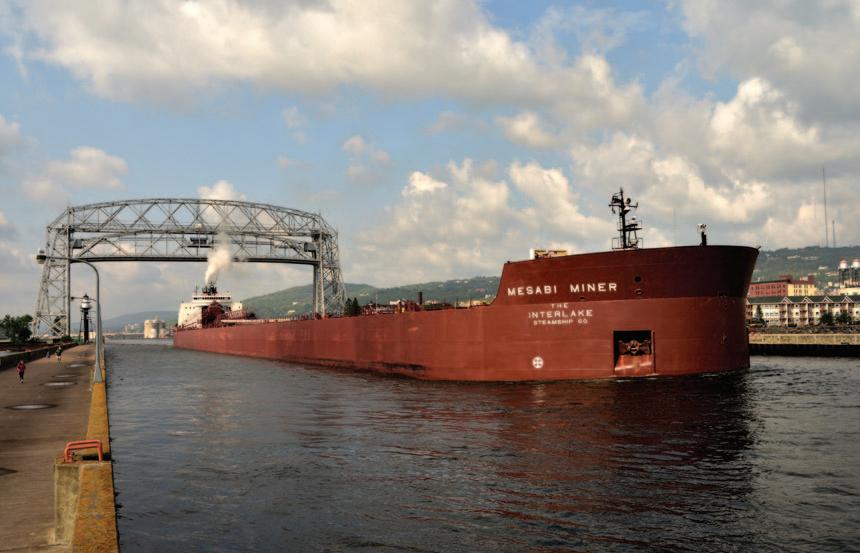
Several other bulk cargoes also posted summer gains through North America’s furthest-inland seaport, including salt (up 13.2% YOY), limestone (up 5.9% YOY) and cement (more than double the 2022 pace).
“It’s definitely been a good first half for many of the bulk cargoes that move through our port, led of course by our king cargo, iron ore,” said Deb DeLuca, executive director of the Duluth Seaway Port Authority. “We’re seeing the effects of steady manufacturing and construction activity throughout the Great Lakes region, which helps drives demand, and also an increase in exported iron ore, which was up more than 26% over last year’s pace through July.”
Mark W. Barker, the first new US-flagged Great Lakes bulker in almost 40 years, successfully completed sea trials and is now trading throughout the freshwater lakes and river networks with oil-free propeller shaft bearings from Thordon Bearings.
Built in Sturgeon Bay, Wisconsin, by Fincantieri Bay Shipbuilding for The Interlake Steamship Company, Thordon’s scope of supply includes a water-lubricated RiverTough bearing, Nickel-Chromium-Boron (NCB) alloy liner for a propeller shaft diameter of 445mm (17.5in), and two Thordon Water Quality Packages. Thordon’s authorized distributor in Ohio, Advanced Sealing Technology, worked with the shipowner to get the RiverTough package specified.
Designed to transport salt, iron ore, stone, and other bulk cargoes throughout some of the narrowest rivers in North America’s Great Lakes region, including the tight bends of the Cuyahoga River, the single screw Mark W. Barker is the sixth Interlake Steamship vessel that Thordon’s proprietary polymer bearings have been installed.
“Interlake has had a lot of success with our propeller shaft bearings,” said Jason Perry, Thordon’s Regional Manager, North America. “Their vessels operate in some of the region’s narrowest, shallowest waterways which means vessels are unable to turn and instead must reverse using bow and tunnel thrusters. When operating at lower shaft speeds, the RiverTough polymer formulation reduces friction and bearing wear. The material can also withstand operations in highly abrasive, very sandy environments.”
Wear rates for RiverTough are typically less than half that of rubber bearings based on ship owner feedback. Offering increased resilience, easier shaft alignment and less edge loading, lubricants in the polymer material reduce friction levels during nearly-dry starts, significantly eliminating stickslip and vibration at low shaft speeds. Results from shipowners have shown wear rates of 0.075mm to 0.100mm (0.003in to 0.004in) in 6,000 to 7,000 hours of annual use.
Commenting on Interlake’s long-term relationship with Thordon, Ian Sharp, Interlake’s Director of Fleet Projects, said: “From the outset, Thordon always responds quickly to our requirements with its bearing expertise, technical know-how and customer service. Having multiple RiverTough bearings in operation with proven reliability made it a very simple decision to choose the same Thordon bearing for our new ship.”
With a hull optimized for energy efficiency the 28,000dwt River-class bulker is powered by a pair of 400HP main engines driving a single controllable pitch propeller through twininput, single out-put reduction gearbox. It is the first ship to operate on the Great Lakes with engines that meet EPA Tier 4 emissions standards.
EPA Tier 4 standards entered into force in January 2017, requiring marine engines rated at 600kW and above to be fitted with technologies capable of significantly reducing nitrogen oxide (NOx), sulphur dioxide (SOx) and particulate matter (PM).
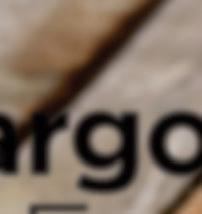
Craig Carter, Vice President Business Development added: “Mark W. Barker is truly a milestone ship for Interlake and we are proud to be associated with what is arguably one of the
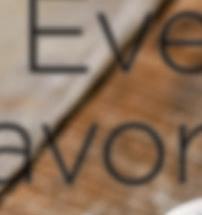
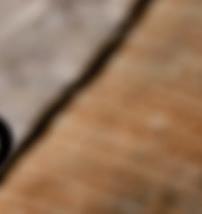
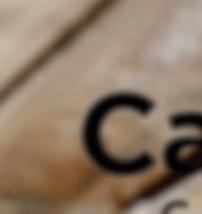
of Every Flavor.
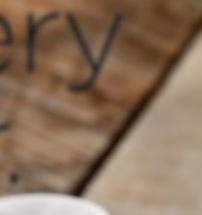
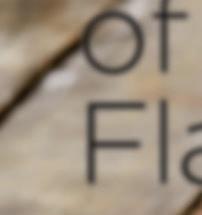
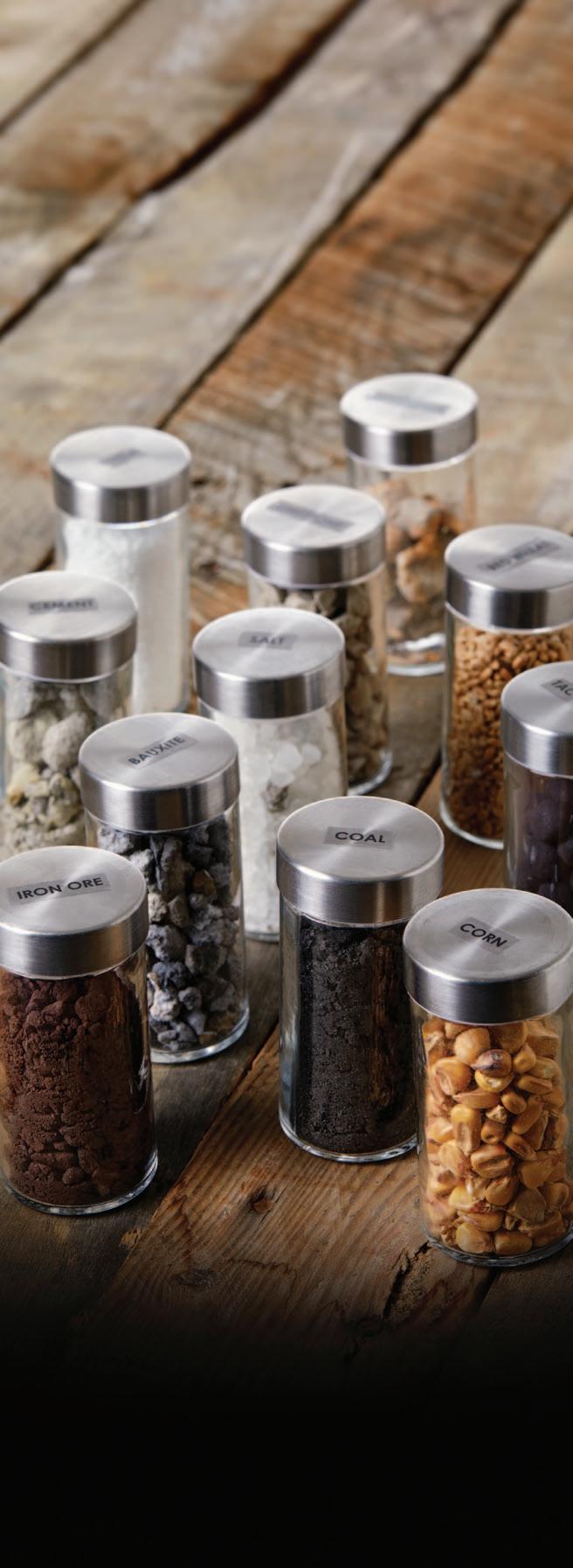
‘Mark W. Barker’ bulker operational with Thordon’s robust RiverTough bearings
most advanced, energy efficient self-unloading bulkers to operate on the Great Lakes.
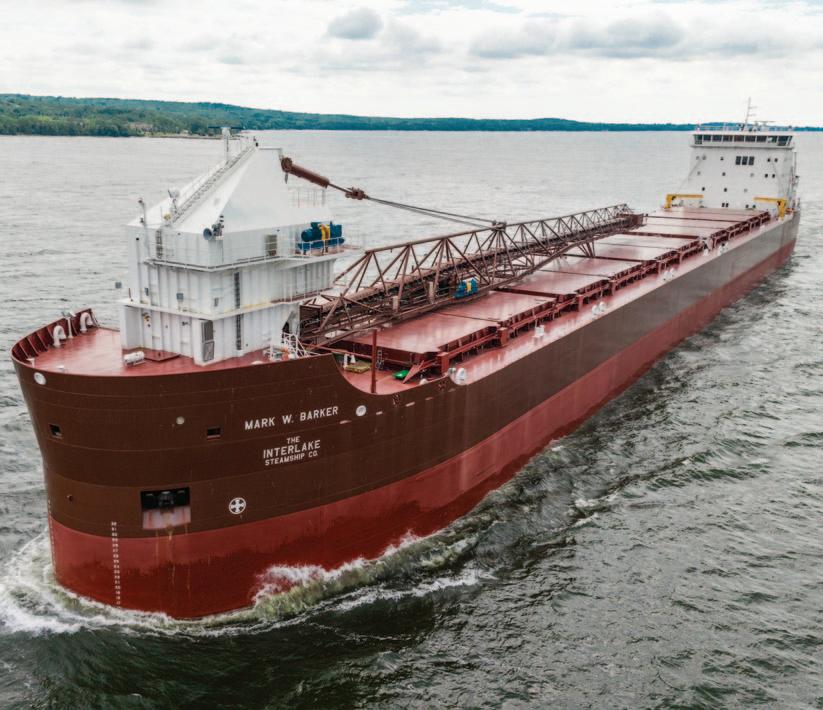
“Our relationship with Interlake Steamship and Bay Shipbuilding dates back to 1998 when we installed propeller shaft bearings to the 25,000dwt Kaye E. Barker Since then, we have enjoyed a very productive, collaborative relationship with both owner and yard and look forward to working together on future projects.”
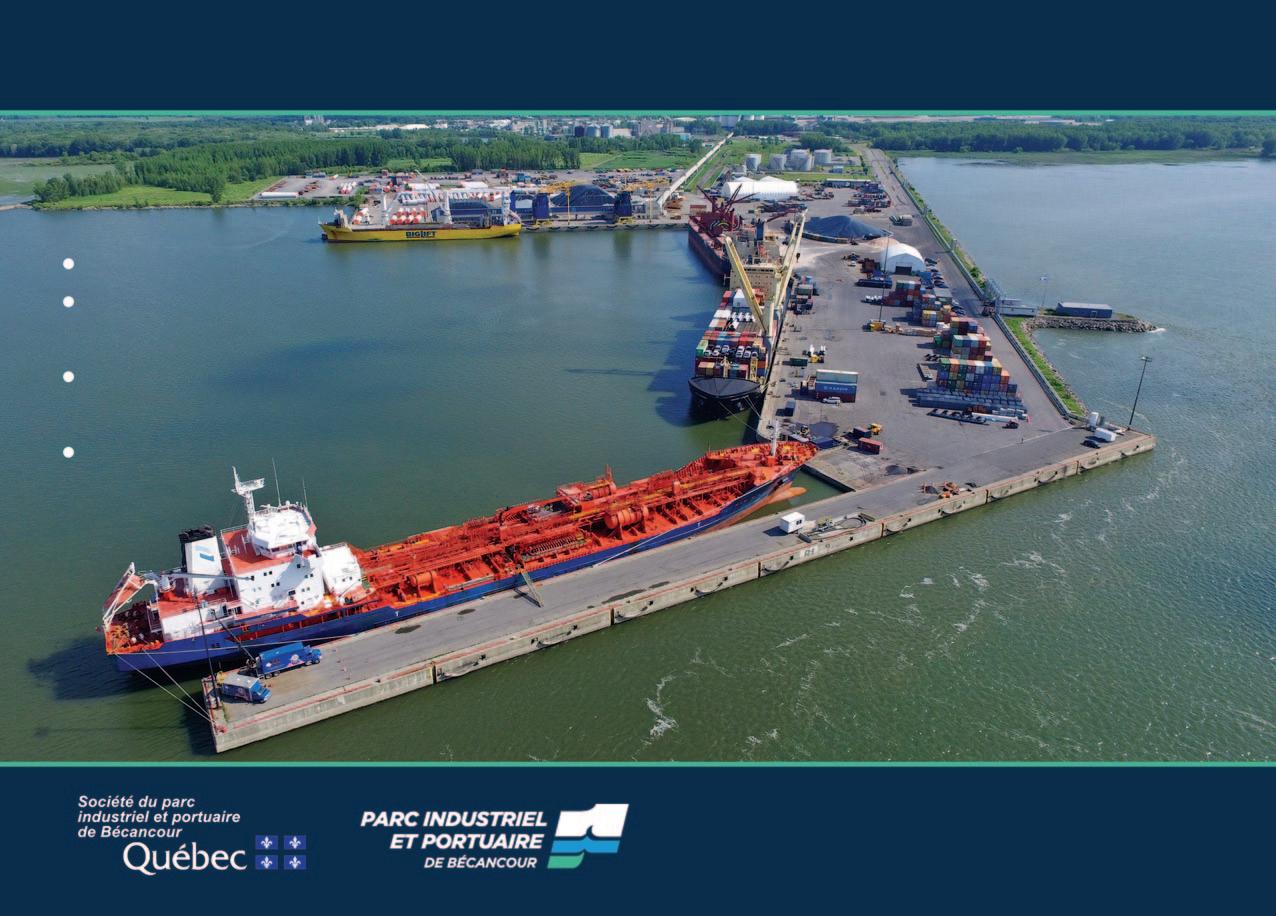
ABOUT THORDON BEARINGS
Thordon Bearings designs and manufactures a complete range of journal bearing and seal systems for marine, clean power generation, pump, and other industrial markets.
The bearing systems are manufactured using Thordon proprietary non-metallic
polymer materials that are lubricated with water eliminating oil or grease usage, meaning zero risk of oil pollution to our rivers, lakes and oceans and elimination
of lubricant costs.
Thordon systems and bearings are available worldwide through over 70 agents and distributors.
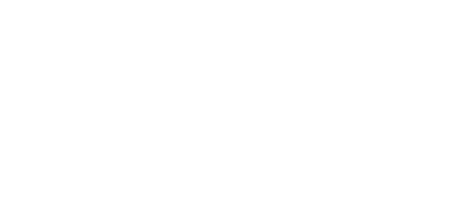

The Toledo-Lucas County Port Authority has shared the results of the Economic Impacts of Maritime Shipping in the Port of Toledo, a report documenting the many contributions made by the Port of Toledo and Great Lakes Seaway Shipping to the City of Toledo, Lucas County, State of Ohio, and the Great Lakes region.
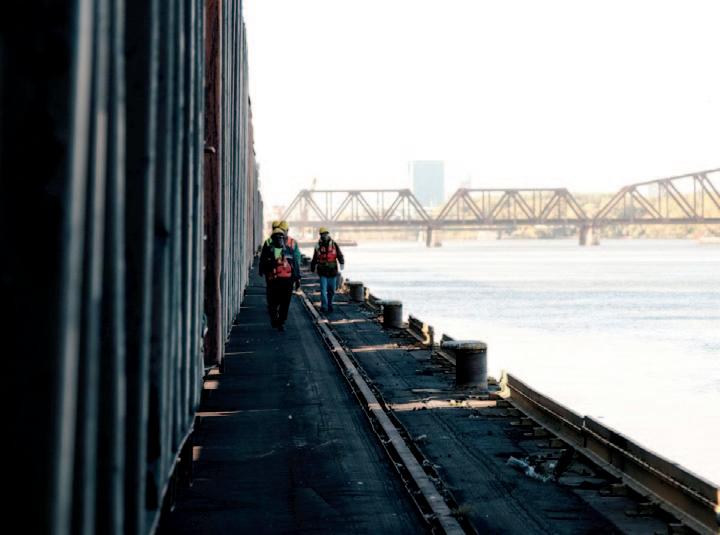
The study reports that in 2022, the Port of Toledo and maritime commerce supported:

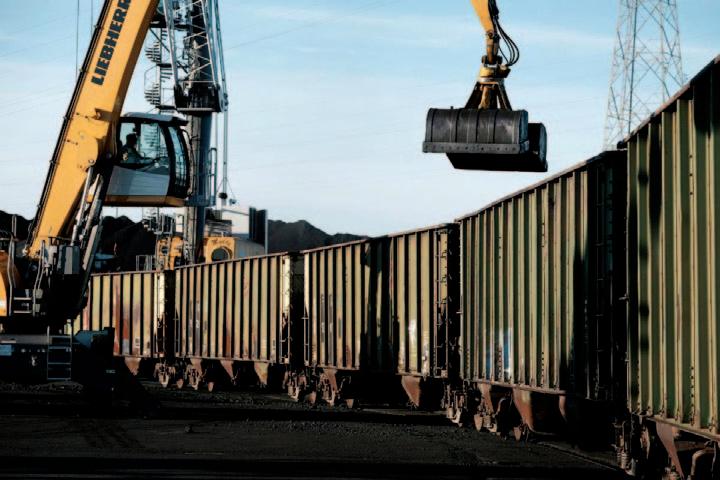
7,971 jobs; v $906.2 million in economic activity; v $708.6 million in personal income and v local consumption expenditures; and $183.2 million in federal and state tax v revenue
“The Toledo-Lucas County Port Authority had an excellent year in 2022,” says Thomas J. Winston, President and CEO of the Toledo-Lucas County Port Authority. “The results from this year’s study indicate an increase of 888 new jobs and more than $237 million in additional economic activity compared to data reported in the 2018 study. This increase can be mostly [attributed] to the addition of the Cleveland-Cliffs Toledo Direct Reduction Plant at Ironville in East Toledo.”
In July, the Economic Impacts of Maritime Shipping in the Great Lakes-St. Lawrence Region, a year-long study of the economic impacts of the entire Great Lakes-St. Lawrence Seaway navigation system was released. The study revealed that Great Lakes-St. Lawrence Seaway shipping is a key driver of the economy, supporting $36 billion in economic activity and more than 240,000 jobs. In 2022, 135.7 million metric tonnes of raw materials and finished goods were delivered by commercial vessels serving critical industries such as agriculture, construction, energy, and steelmaking.
Both studies, compiled from 2022 data, were conducted by economic consultants Martin Associates of Lancaster, Pennsylvania, a global leader in transportation economic analysis and strategic planning. Martin Associates was retained to perform the Great Lakes-St. Lawrence Seaway analysis by a coalition of US and Canadian Great Lakes and St. Lawrence marine industry stakeholders, including the Saint Lawrence Seaway Development Corporation, the St. Lawrence Seaway Management Corporation, the American Great Lakes Ports Association, the Chamber of Marine Commerce, the Lake Carriers’ Association, and the Shipping Federation of Canada.
Port of Toledo supports $906m in economic activity and nearly 8,000 jobs
Middle River Marine celebrates the delivery of Liebherr’s LH 110 material handler
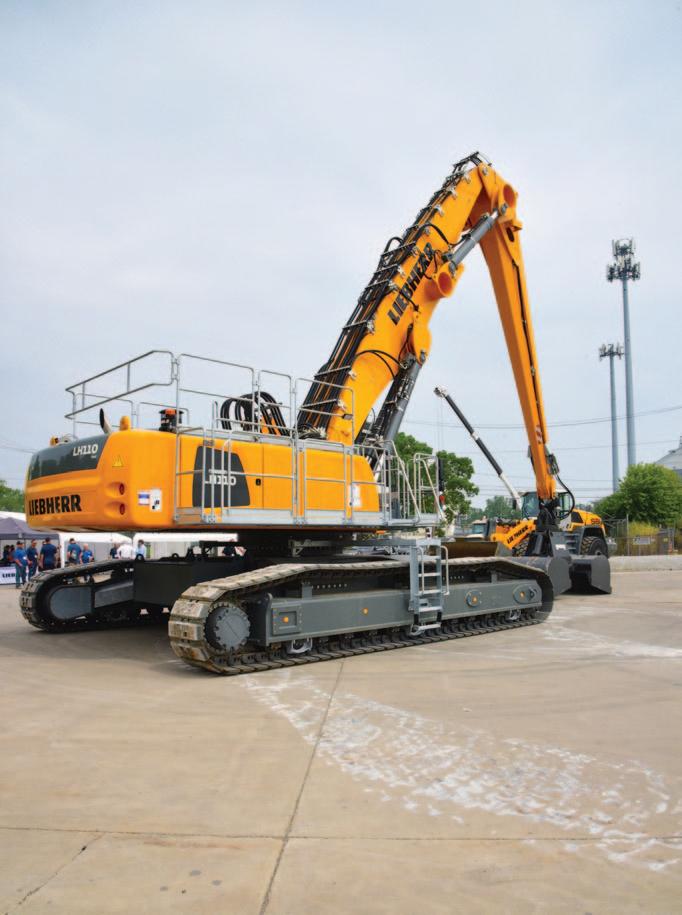
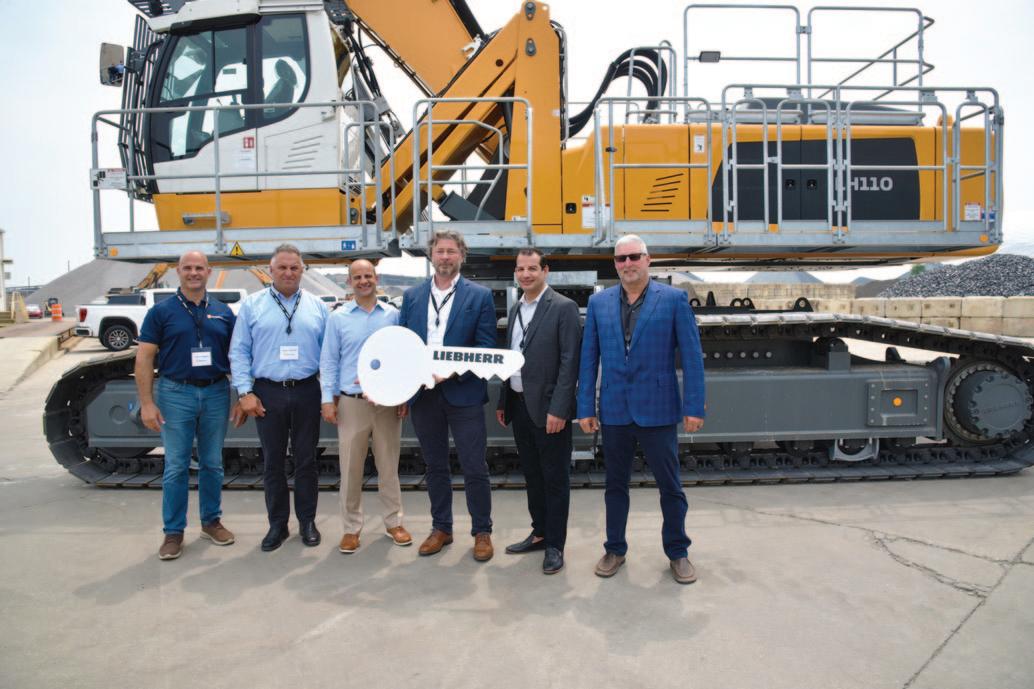
Illinois based company, Middle River Marine (MRM), acquired a newly assembled LH 110 material handler to be stationed at an MRM terminal based in the South Chicago region. To commemorate this delivery, MRM hosted an on-site event recognizing stakeholders, partners, and dealers and showcased various Liebherr machines from the MRM fleet.
Primarily serving the Illinois and Northwest Indiana markets, Middle River Marine (MRM), has taken delivery of Liebherr’s LH 110 Port Litronic material handler at its largest terminal in South Chicago off of the Calumet river. MRM will use this large machine for handling material, such as pig iron, to then be transported by rail, truck, or barge across the nation.
To celebrate this handover, MRM hosted over 60 attendees at its 80-acre terminal site to recognize the newest addition of its growing Liebherr fleet of 15+ machines. This event allowed for local industry leaders and peers to connect and network as well as display many of the Liebherr machines MRM has acquired over the years including multiple L 586 Xpower wheel loaders.
Throughout the event, various industry leaders spoke highlighting the strong familial relationships and values held by each organization in attendance, followed by a luncheon and on-site tours of an MRM boat as well as the terminal grounds equipped with Liebherr equipment.
LH 110 Port Litronic was designed specifically for handling scrap and mixed cargo.
Liebherr’s wide variety of offerings within the earthmoving and material handling product segment provides MRM a full line of highly specialized equipment for all of their individual terminal sites and port application needs.
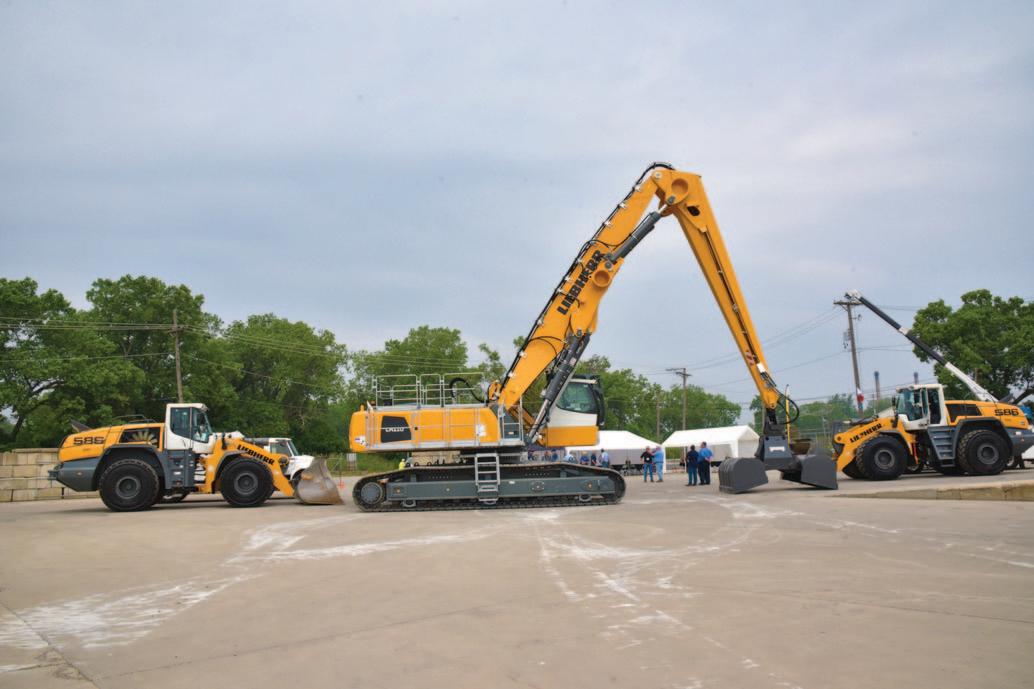
“The main criteria we factored into this purchase is Liebherr’s history of providing dependable, fuel efficient, state-of-the-art equipment backed by quality service and a longstanding relationship in business,” noted Pete Colangelo, MRM Vice President of Terminal Operations.
CARGO AND LOGISTICS
Middle River Marine is a fully integrated bulk material logistics service provider, serving primarily the construction materials, agricultural products, and industrial commodities bulk markets in the Chicagoland region. MRM transportation services include road, rail, and water transport. The company currently offers ten river terminal locations throughout Illinois as well as a vast transportation network to provide optimal transport and
supply chain planning for its customers. MRM continues to provide individualized solutions for each of its customers utilizing its state-of-the-art technology and superior customer service.
President of Middle River Marine, Aaron Halcomb said, “We are extremely excited to partner with Liebherr to expand our fleet and handling capabilities to better serve our customers. Liebherr has become a trusted partner in business to ensure we have dependable, capable, stateof-the-art equipment to meet rigorous demands of our business.”
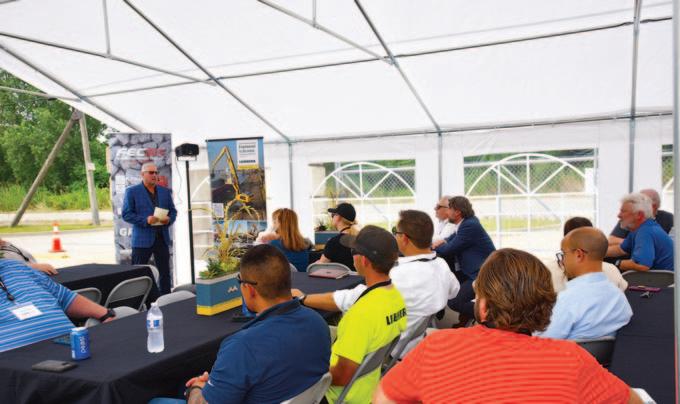
Each of MRM’s locations, including the 80-acre South Chicago terminal where the MRM event took place, offers a variety of bulk transportation services including marine barging & towing, material & aggregate storage, material handling, material inventory management, railcar loading and unloading, transloading, and truck loading and unloading. Each terminal site also offers a variety of Liebherr equipment depending on incoming and departing cargo transport.
A FAMILY BUSINESS
Middle River Marine operates as a subsidiary of Ozinga, a fourth-generation family-owned US-based business providing concrete, bulk materials, energy solutions and transportation logistics throughout the Midwest and Florida. Established in 1928, Ozinga has continuously expanded into a premiere supplier and service provider with a vast service network and deep commitment to their local communities.
“We are proud to be here today, celebrating each of these organizations and the impact they make,” said Aaron Ozinga, President of Ozinga Ventures. “Our partners continue to showcase excellence and advance our mission and core values of serving others and our local communities.”
Ozinga as well as their subsidiaries have acquired approximately 50 Liebherr machines throughout the last decade. Liebherr, also a family-owned company, looks forward to the continued support and partnership with Ozinga and Middle River Marine.
“MRM’s newly acquired LH 110, a flag ship solution within the material handling portfolio of Liebherr, is the result of a trustful, reliable and successful co-operation between multiple familyowned businesses. Middle River Marine, Ozinga, American State Equipment/ Finkbiner, and Liebherr have continued to share the same values and expectations for more than a decade,” said Kai Friedrich, Managing Director of Liebherr USA, Co. “The continuously growing fleet underlines the success and durability of this remarkable relationship. We are proud of
the joint achievements and look forward to future growth.”
SUPERIOR DEALER NETWORK
Liebherr USA, Co. offers an extensive line of earthmoving and material handling machines custom-engineered for special applications promoting efficiency, safety, and reliability for all customers. Liebherr also offers a vast dealer network to support the earthmoving and material handling customers with sales, service, and spare parts needs across the nation. This network provides fast support through qualified Liebherr dealers to assist customers anytime, anywhere.
Based in Illinois and Northwest Indiana, Finkbiner Equipment Company serves as a subsidiary of American State Equipment (ASE). ASE is one of Liebherr’s largest and oldest dealers, with a relationship that goes back approximately 50 years. Their consistent support and established partnership as a Liebherr dealer have been essential in assisting MRM with this latest acquisition.
“We each have a shared commitment to integrity, excellence, accountability, and innovation across all of our operations. These values allow us to build enduring partnerships with like-minded family
organizations,” said Tim Kraut, President and CEO of American State Equipment.
Finkbiner Equipment Company and American State Equipment offer many Liebherr machines and attachments including concrete trailer pumps, duty cycle cranes, deep foundation machines, as well as a wide variety of mining, earthmoving and material handling equipment for many applications.
PORT LITRONIC
The LH 110 port litronic was designed specifically for handling scrap and mixed cargo in port handling operations and offers customers extremely high load bearing capacities as well as a long reach. The machine is weight-optimized allowing for powerful operation and maximum performance at a low cost.
MRM opted to equip its machine with a shorter boom-stick combo for optimal load charts and chose a clamshell attachment for easier handling of aggregate. The LH 110 also comes equipped with the latest Liebherr technology, allowing MRM to adapt the machine to the respective needs of each individual project, assuring maximum material handling performance and efficiency, saving time and money.
SHIP
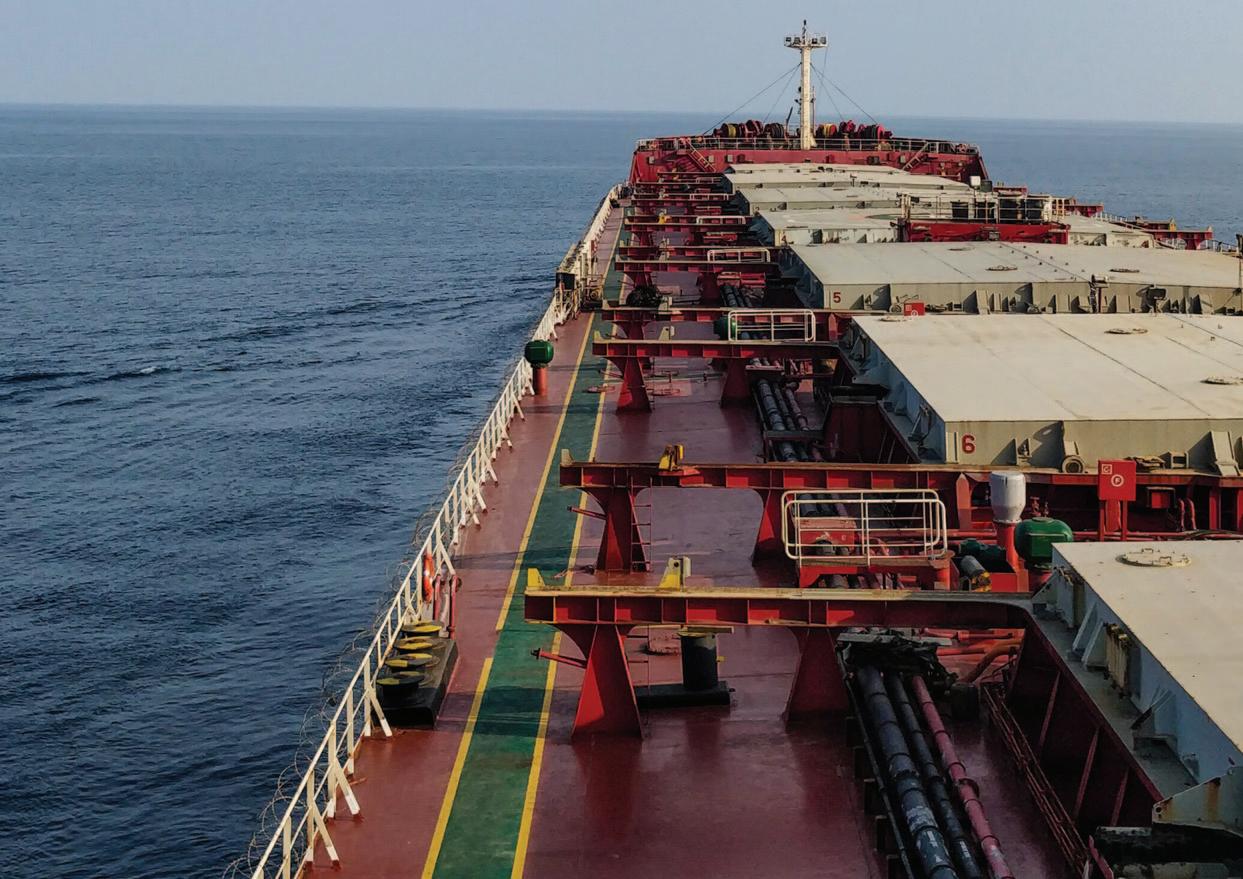
ABOUT LIEBHERR USA, CO.
Liebherr USA, Co. based in Newport News, VA provides sales and service on behalf of nine different Liebherr product segments: earthmoving, mining, mobile and crawler cranes, tower cranes, concrete technology, deep foundation machines, maritime cranes; components, and refrigeration and freezing.
ABOUT THE LIEBHERR GROUP
The Liebherr Group is a family-run technology company with a highly diversified product portfolio. The company is one of the largest construction equipment manufacturers in the world. It also provides high-quality and useroriented products and services in a wide range of other areas.
The Liebherr Group includes over 140 companies across all continents. In 2022, it employed more than 50,000 staff and achieved combined revenues of over €12.5 billion.
Liebherr was founded in Kirchdorf an der Iller in Southern Germany in 1949. Since then, the employees have been pursuing the goal of achieving continuous technological innovation and bringing industry-leading solutions to its customers.
Calhoun Super Structure’s buildings have vital function in the Great Lakes/St. Lawrence Seaway region
Calhoun Super Structure plays a crucial role in bulk handling operations in the Great Lakes/St. Lawrence Seaway region, particularly for equipment manufacturers, logistics providers, and shipping companies. Here are some ways fabric structures are involved in these activities:
1. Storage and warehousing: Calhoun’s fabric structures are commonly used for temporary or semi-permanent storage of bulk materials. Fabric structures provide cost-effective and versatile storage solutions for various commodities like grains, minerals, fertilizers, and construction materials. Equipment manufacturers and logistics providers often utilize fabric structures to store their products or manage inventory during peak seasons.
2. Covering and protection: Calhoun’s fabric structures are employed to cover and protect bulk materials during loading, transportation, and storage. Bulk cargo, such as coal, salt, or aggregates, may be loaded onto opendeck ships or barges. The structures are used to shield the cargo from adverse weather conditions, preventing moisture damage or spillage. Shipping companies rely on these structures to ensure the safe transportation of bulk materials.
3. Environmental Enclosures: Calhoun Super Structure creates environmental enclosures or containment systems. For example, equipment manufacturers involved in bulk handling may require controlled environments for manufacturing processes or maintenance work. Fabric structures provide a costeffective and customizable solution for
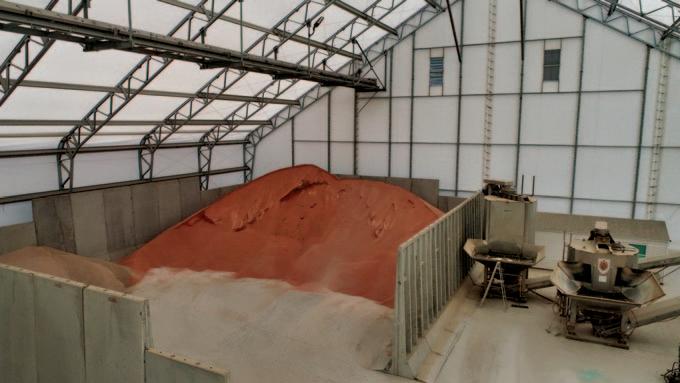
enclosing specific areas, protecting equipment from the elements and providing a controlled work environment.
4. Temporary Infrastructure: Calhoun Super Structure offers temporary infrastructure required for bulk handling operations. The fabric structures can serve as workshops, maintenance facilities, or even office spaces for shipping companies and logistics providers. These structures can be quickly erected and dismantled, making them ideal for short-term projects or seasonal operations.
5. Maintenance shelters: Shipping companies and equipment manufacturers may require maintenance shelters or repair facilities for their vessels, equipment, or machinery. Calhoun Super Structure offers an economical solution for providing temporary or semi-permanent maintenance shelters, protecting equipment from the elements and facilitating repair and
maintenance work.
6. Port facilities: Calhoun’s fabric structures are also used in the construction of port facilities, such as cargo terminals, warehouses, or covered storage areas. These structures can provide additional covered space for storage, handling, and processing of bulk materials, enhancing the efficiency of port operations.
In summary, Calhoun Super Structure is integral to the bulk handling operations in the Great Lakes/St. Lawrence River region. Fabric structures are employed by equipment manufacturers, logistics providers, and shipping companies for storage, covering and protection, environmental enclosures, temporary infrastructure, maintenance shelters, and port facilities. These structures offer flexibility, cost-effectiveness, and adaptability, supporting the efficient handling and transportation of bulk materials in the region.
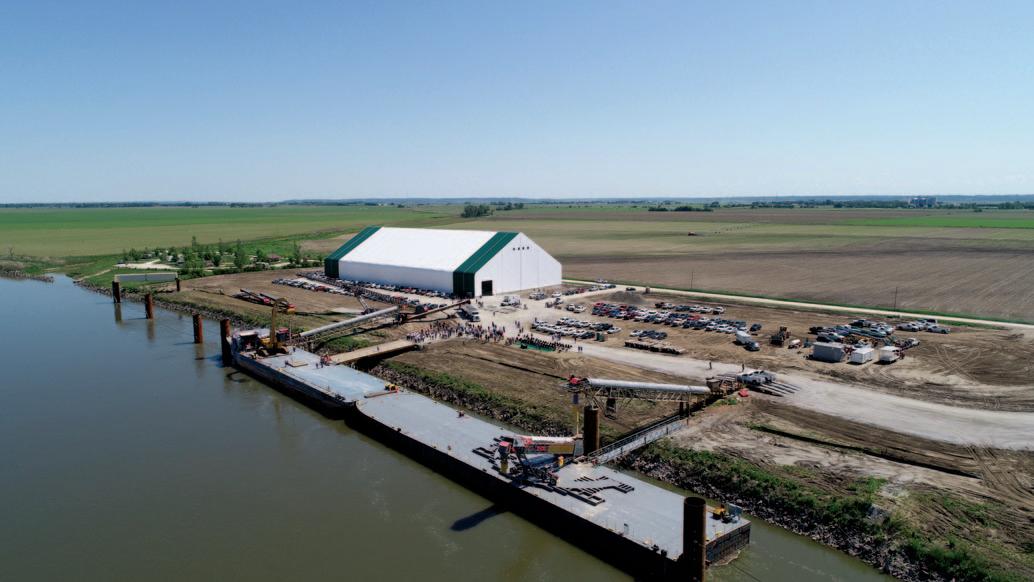
Investments improve freight transport and alleviate congestion at the Port of Windsor

MINISTER OF TRANSPORT ANNOUNCES FUNDING TO IMPROVE FREIGHT TRANSPORT AT THE PORT OF WINDSOR
An efficient and reliable transportation system is essential to making life more affordable for Canadians and combating the rising cost of living. The Government of Canada is committed to ensuring that supply chains grow the economy and create good, middle-class jobs for Canadians, while making them resilient and adaptable to the effects of climate change.
On 26 May, the then-Minister of Transport, the Honourable Omar Alghabra, announced an investment of up to $12.5 million to the Essex Terminal Railway Company, from the National Trade Corridors Fund, for a Cargo Terminal Infrastructure Expansion project at the Port of Windsor.
The project will help build a new warehouse and expand the shorewall at the Port of Windsor. It aims to shift the transportation of goods from trucks to trains and ships, which will reduce pollution and congestion along the Highway 401 corridor. This will make it easier to move steel and aluminium products and attract potential new exports. Additionally, these improvements will prevent shoreline erosion and reduce the risk of flooding due to rising lake water levels caused by climate change. It will also enable the possibility of building a new cargo dock in the future that can be used for different purposes.
The Government of Canada continues to invest to make the country’s supply chain stronger, to boost economic growth and to create more opportunities for our businesses to grow internationally. This represents another long-term commitment to work with stakeholders on important infrastructure projects to address transportation bottlenecks, vulnerabilities, and congestion along Canada’s trade corridors.
The Honourable Omar Alghabra said, “Efficient and reliable transportation is crucial for affordable living and economic growth. This National Trade Corridors Fund investment will help shift towards more environmentally friendly transport-
ation methods, while reducing congestion and emissions. By supporting this project, we contribute to Canada’s economic progress, improve the environment, and make life more affordable for Canadians.”
Irek Kusmierczyk, Parliamentary Secretary to the Minister of Employment, Workforce Development and Disability Inclusion and Member of Parliament for Windsor–Tecumseh, said, “This significant federal investment grows jobs and solidifies Port Windsor’s position as a key trade hub at the centre of North American supply chains and electric vehicle and battery manufacturing. This is another critical piece that unlocks our region’s prosperity.”
Tony De Thomasis, President and CEO, Essex Terminal Railway, Morterm Limited and Motipark Limited, added, “Morterm Limited and the Port of Windsor are excited and very appreciative of the National Trade Corridors Funding to improve Port infrastructure and expand operations, ensuring Windsor-Essex is well equipped and in a more desirable position to access new export markets. Further investment in our region will bring us even closer to bringing to fruition the multimodal hub that this area needs — one that supports supply chains, reduces Port congestion, creates new jobs, and encourages economic development in sustainable and innovative ways.”
Steve Salmons, President and Chief Executive Officer, Windsor Port Authority,
concluded, “This is transformational for our region… Short-sea container shipping on the Great Lakes, and soon to be at Port Windsor, will relieve congestion in the supply chain, reduce GHGs, and increase access to world markets for industry in Windsor and Essex County.”
QUICK FACTS
Relieving Supply Chain Congestion at Canadian Ports is a targeted call under the National Trade Corridors Fund to assist with measures to relieve immediate supply chain congestion and facilitate the movement of goods at Canadian ports
Eligible recipients targeted by the call for proposals include Canadian Port Authorities (subject to the Canada Marine Act), organizations supporting supply chain projects, and Canadian Port Authorities partner organizations. An efficient and reliable transportation network is key to Canada’s economic growth. The Government of Canada, through the National Trade Corridors Fund, is making investments that will support the flow of goods across Canada’s supply chains.
The National Trade Corridors Fund is a competitive, merit-based programme, designed to help infrastructure owners and users invest in the critical transportation assets that support economic activity in Canada. The programme has been allocated a total of $4.6 billion over 11 years (2017–2028).
Budge the sludge: ore mine uses air cannons to unclog chutes
Eagle Mine strives to have the smallest environmental footprint possible (all photos: ©Martin Engineering 2023).
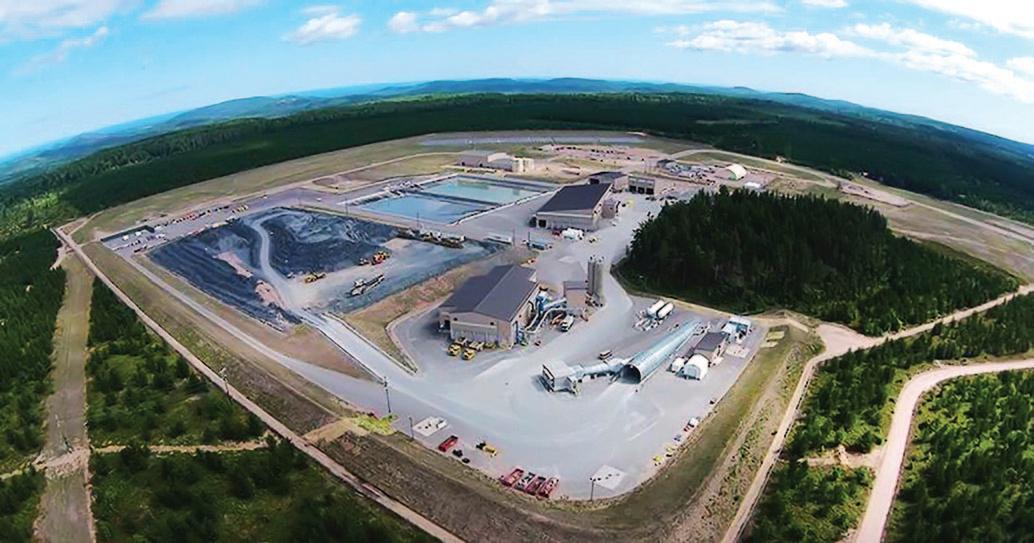
No matter what type of ore is being extracted from a mine, mucking with front loaders can be accompanied by wet fines that cling to every surface, writes Mike Moody/Business Development Manager, Martin Engineering. Once loaded into a hopper or conveyer transfer chute, viscous material can quickly build up on the walls to create bottlenecks, clogging the chute and causing expensive downtime.
Clearing material from hoppers, chutes, bins and vessels can be done using manpower and tools on hand, but safety experts recommend considering a solution that prevents exposing workers to potential hazards. Operators at modern mining sites, such as Eagle Mine located in Western Marquette County of Michigan’s Upper Peninsula, understand that using specialized equipment reduces worker exposure, offers the safest mode of production and provides the most costeffective lasting results.
“Safety is a top priority for us,” said Ted Lakomowski, Lead Reliability Technician at Eagle Mine. “When we experienced
clogging and downtime at the processing mill, the crew naturally swung into action to resolve it, but we immediately sought a safer long-term solution.”
STOPE MINING FOR NICKEL AND COPPER
Owned by Lundin Mining, a globally diversified base metals mining company headquartered in Toronto, Canada, Eagle Mine is the only primary nickel mine in the United States, producing 1.5% of the world’s total nickel production. The first operation permitted under Michigan’s Part 632 Non-Ferrous Mineral Mining Law, it opened in 2014 and is expected to produce 360 million pounds of nickel, 295 million pounds of copper and small amounts of other metals over its estimated nine-year lifespan.
The company extracts approximately 2,200st/pd [short tonnes per day] (2,000t/pd [metric tonnes per day]) from the underground nickel-copper mine using a bench-and-fill stoping process. Accessed from the surface by specialized underground trucks, the vehicles carry
≈100,000 lb (45,400K) loads through a one-mile (1.6km) long and 18ft. (5.4m) diameter ramp shaft descending into the earth at a 13% grade. Stoping is a bottomup method that involves systematically blasting columns of loosened ore that is then mucked by front loaders into trucks and backfilled using cemented and uncemented rockfill.
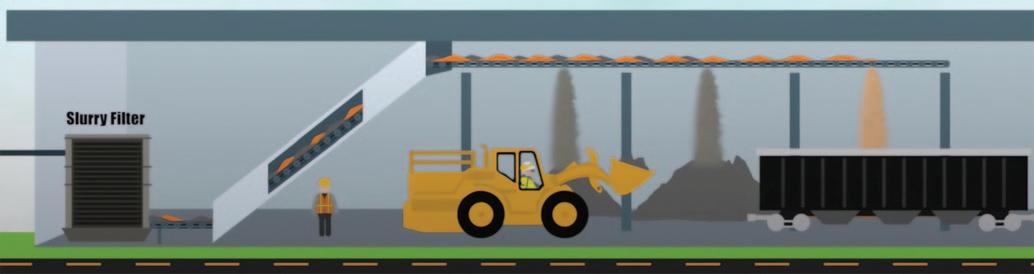
Ore from the mine is stored in a covered coarse stockpile facility prior to transport by road approximately 65 miles (105km) to the Humboldt mill. A former iron ore processing plant, the site was converted and refurbished to accommodate Eagle’s updated processing facility. A three-stage crushing circuit reduces the material to 3/8 inch-minus, then a single stage ball mill grinds it further to sand, where it is mixed into a slurry.
To liberate the nickel and other minerals from the waste materials, a refining process of selective flotation is used, mixing the ore with special reagents and agitating it with devices producing air bubbles. As the oxygenated bubbles rise
through the heavy slurry at the bottom of the chamber, sulfide particles adhere to the surface and collect as a concentrate containing nickel and copper sulphides at the top of the liquid.
The slurry passes through several stages to also release copper concentrates, along with other trace precious metals. The tailings from the plant are safely impounded sub-aqueously in the decommissioned and restored ore pit from the previous plant.
“The end goal is to leave the stoping columns with no voids and the environment around the working areas better than we found it,” Lakomowski said. “It is Lundin’s mission to constantly assess environmental impact and to work with local communities to seek the most sustainable solutions throughout the lifecycle of mining operations.”
HUMIDITY AND ORE PROPERTIES
The clogging issues were found in an undersize chute in the Humbolt milling process. Although material was damp when mucked, it was further exposed to rain, snow or summer humidity during
References
[1] Taylor, John; Wise, Edmund. “Nickel processingExtracting and Refining - From Sulfide Ores”; Encyclopedia Britannica. Sept. 5th, 2003. https://www.britannica.com/technology/nickelprocessing
transport by truck to the mill. “The issue was particularly acute in spring time, when it rains excessively,” Lakomowski explained. “At that time, clogging increased to several times per shift.”
During the crushing process, a mesh screen separates the fines from the remaining aggregate, which are fed back through the process. Fines that pass through a screen fall into a wide-mouthed hopper, leading to a chute that narrows to approximately 8ft (2.5m) wide by 2ft (0.6m) high and — after a dead drop of several feet — slopes abruptly in a ~45º angle of decline. This slope slowed the descent of the fine material for a low impact and centred discharge onto a conveyor belt leading to the ore bins. Material buildup began at the hopper and at the discharge slope, but could also occur at virtually any point, blocking the chute.
Beyond the moisture content, the adherent qualities of the raw material also contributed to the accumulation issue. Some nickel-bearing sulfides can display weak magnetic characteristics at room temperature or higher, which may slightly amplify the adherent nature of the material.[1]
SEEKING SOLUTIONS, FINDING OBSTACLES Clogging would stop the entire crushing process approximately three to four times per shift for as long as an hour, blocking
input of material all the way back to the ore storage area. The breaks in production and ensuing downtime had an immediate effect on the cost of operation. As soon as the clogging was observed, workers quickly began clearing the obstruction by hitting the side of the chute with mallets and poking at the obstruction with long implements.
Eventually, they attacked the clog with 15ft (4.5m)-long air lances from the top of the hopper and bottom of the chute. These methods used a tremendous amount of compressed air and diverted manpower from other essential duties. Moreover, air lances caused excessive splash-back of wet material, which was extremely messy and potentially hazardous.
Recognizing the need for a better solution, Eagle first installed a UHMW polymer lining in the chute. Offering a low coefficient of friction, the lining was bolted to the chute wall and acted like a smooth slide for the material to ride down. Unfortunately, it was less effective against the adherent qualities of the material than hoped.
To supplement the lining, Eagle next installed pneumatic vibrators onto the vessel wall intended to agitate the adhered material and promote its descent down the chute slope. The impacting action was meant to create a vibratory wave across
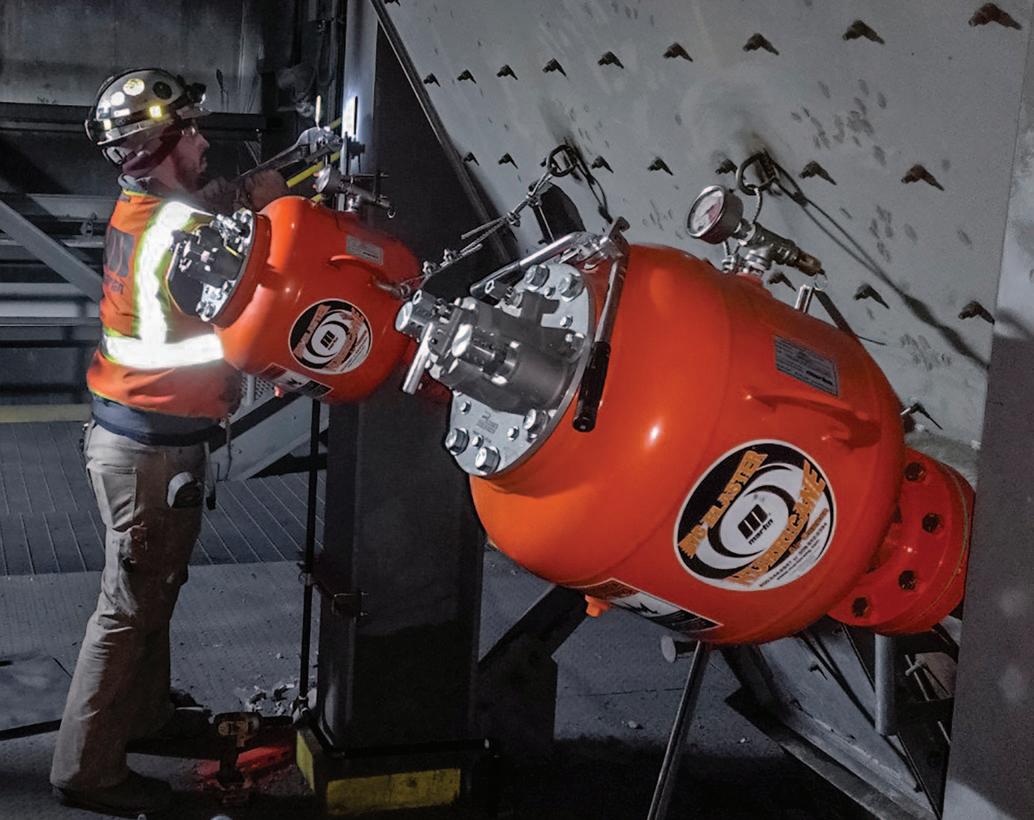
the vessel surface. Instead, the fact that the polymer lining was bolted to the vessel caused it to muffle the vibration of the units, limiting the force to only the impact zone and not much farther.
Although the solutions reduced clogging slightly, labor was still needed to fully evacuate the material from the chutes. “We were forced to default back to air lances, but kept on looking for a better solution,” Lakomowski explained. “Having worked with Martin Engineering in the past, we asked them to come in, examine the issue and offer a safe, effective and affordable solution.”
COMPRESSED AIR USAGE
The technical team at Martin Engineering observed that the previous solutions did not adequately aid the flow of material. The sand-like slurry was still clinging to the surface, creating an abrasive layer that tended to offset the slickness of the UHMW polymer lining, allowing material to build upon itself. The issue was presented at many stages of the process, so a solution was needed throughout the transfer.
“We realized that the air lance solution was only temporary, but was effective in moving material,” said Jason Haynes, Territory Manager for Martin Engineering. “We proposed installing air cannons at strategic points throughout the chute to dislodge material and aid flow, but managers had some initial reservations.”
Many mining operations require
compressed air for some machinery to function, and Eagle is no different. The process of separating nickel and copper from the slurry at the Humboldt facility is dependent on instrument air, which keeps valves operating and the mill drivetrain engaged. Anything which jeopardized compressed air availability and capacity naturally yielded concern for the operation.
“Compressed air is almost a currency here, so we were naturally skeptical of using a solution that impacted pressure,” Lakomowski clarified. “Many in the organization had experience with older air cannon designs and knew the potential drain they could put on a system.”
In the past, large inefficient air cannons could burden a compressed air system and require an excessive amount of energy to develop adequate pressure, push air through the system and retain the pressure during output. According to Lakomowski, compressed air has an estimated energy exchange rate of 8:1. This means that it costs 8x more energy to power a device with compressed air than using direct power, causing the power drain to be more expensive.
AIR CANNONS
Air cannon technology uses compressed air to promote proper flow by quickly filling a tank, delivering a powerful shot to the vessel wall in the direction of the moving cargo, dislodging adhered material and introducing it back into the stream.
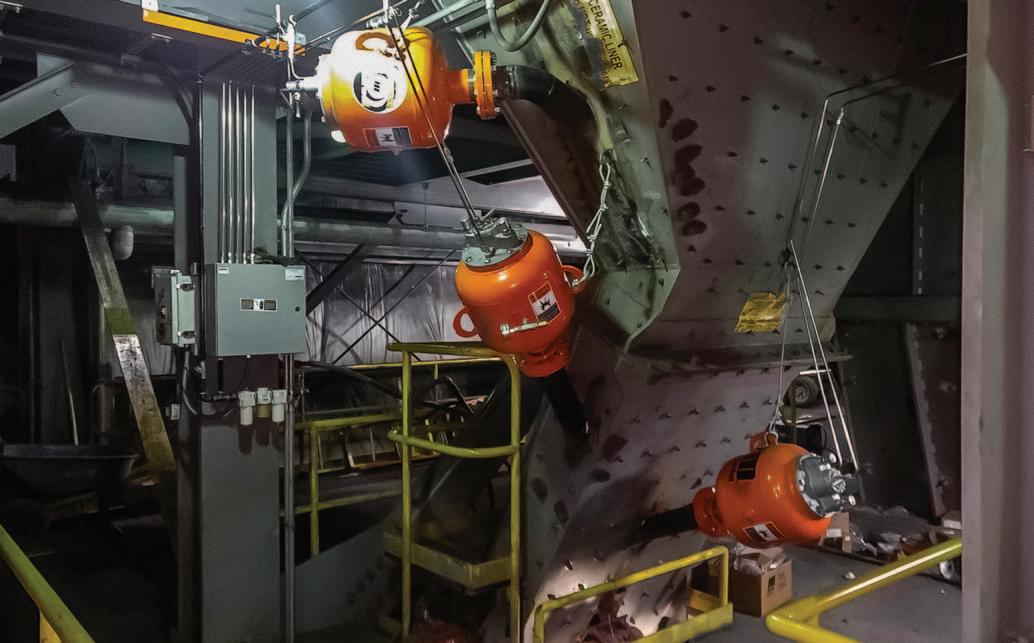
Strategically positioned at a 30º angle, the cannons keep material flowing.
After Haynes detailed the low impact that new air cannon technology has on compressed air systems, Lakomowski advocated for the initial installation of five 35 Liter (9.25 gallon) Martin® Hurricane Air Cannons, followed by two more placed in essential spots in the chute. All of the tanks were accompanied by a 4in. (101mm) pipe assembly ending in fan jet nozzles. Offering more force output than designs double their size with considerably less air consumption, the compact Hurricane Air Cannon tanks measure only 16in. (406mm) in circumference, 24.92in. (633mm) long, weighing 78 lbs (35kg) each. The units fire a shot of air at up to 120PSI (8.27BAR) through the fan jet nozzle, which is 4in. wide where it connects with the pipe assembly then spreads to 12 inches (304mm) at the exit point, distributing the airstream across the surface of the wall with an effective area of up to 11.3 ft3 (320 L).
Designed with safety and low maintenance in mind, the cannons feature a centrally located outward-facing valve assembly that can be replaced within minutes, without the need to remove the tank from the vessel. To prevent the risk of unintentional firing due to drops in pressure, the innovative valve design requires a positive signal from the solenoid in the form of an air pulse to trigger release.
INSTALLATION AND TESTING
For access inside the chute, installers first
removed the lining and cut holes to fit the air cannon pipe assemblies, which pointed at a 30º angle in the direction of the cargo stream. Beginning with five cannons, one unit was placed at the area where material discharged into the hopper, two others were positioned at the hopper slope where the most accumulation was observed and two more were placed along the drop chute. These used straight pipe nozzles to shoot air across the vessel to dislodge adhered material and promote flow.
“The initial installation reduced the amount of downtime, but testing showed it did not cover enough area to fully evacuate adhered material,” said Haynes. “More accumulation built up in transition sections of the hopper and discharge slope than initially thought. So, we installed one more cannon at the top of the hopper and one at the bottom of the chute where it discharged. We also added the fan jet nozzles to the pipe assemblies to cover more area, and that did the trick.”
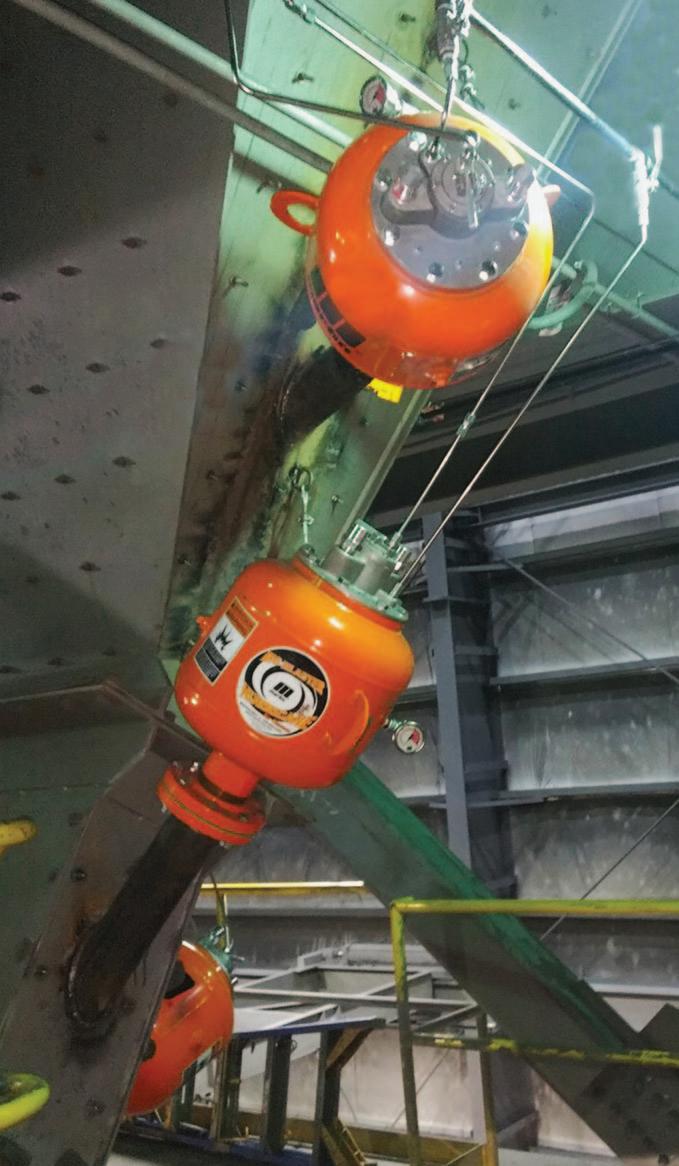
A single solenoid box was installed to control up to ten cannons and was safely located away from the firing area. Connected to a distributed control system (DCS) in a central control room, operators can monitor and adjust firing sequences from a remote location or fire the cannons directly from the solenoid box without needing to interact with the cannons.
RESULTS
Operating on a regular firing schedule of every 1–10 minutes — readjusted for production volume, time of year and moisture level — revealed the seven cannon configuration reduced clogging issues and downtime. This significantly lowered the risk to operators and reduced the cost of operation.
“When I did the cost assessment, I was surprised to discover that there was a 1,000% savings in using the air cannons over the air lances,” Lakomowski said. “It’s a significantly lower effect on our system than initially predicted, and managers are very happy about that.”
The project also improved safety, as workers spent less time diverted from other assignments to use air lances or create vibration by beating on the vessel walls. By being able to perform maintenance on wear parts like valves from the outside of the cannon without tank removal, upkeep can be safely performed by a single technician with no heavy lifting involved.
“Just from a safety aspect, this solution has paid for itself,” Lakomowski concluded.
“The Martin Engineering team was easy to work with, and they were cognizant of our budget restrictions. Overall, this was a successful project.”
ABOUT MARTIN ENGINEERING
Martin Engineering has been a global innovator in the bulk material handling industry for more than 75 years, developing new solutions to common problems and participating in industry organizations to improve safety and productivity. The company’s series of Foundations books is an internationally recognized resource for safety, maintenance and operations training —
with more than 22,000 print copies in circulation around the world. The 500+ page reference books are available in several languages and have been downloaded thousands of times as free PDFs from the Martin website. Martin Engineering products, sales, service and training are available from 17 factoryowned facilities worldwide, with whollyowned business units in Australia, Brazil, China, Colombia, France, Germany, India, Indonesia, Italy, Malaysia, Mexico, Peru, Spain, South Africa, Turkey, the USA and UK. The firm employs more than 1,000 people, approximately 400 of whom hold advanced degrees.
Bulk Storage Inc. supplies vaulted fabric dome for bulk storage
Bulk Storage Inc., a respected supplier of storage facilities, has recently supplied a major bulk storage vaulted fabric dome (pictured).
Bulk Storage Inc. self-performed both the 10ft cast in place concrete foundation walls, as well as the turnkey installation, of the 132x300ft vaulted fabric dome. With five 20’x30’ entrances, the customer is able to easily load and unload the product as needed. A conveyor system was installed with two hopper feeds to bring product directly into the processing facility. With over 22,000 metric tonnes of dry bulk storage, this storage buildings allows the customer to stockpile enough product to wait out the winter freeze and still run efficiently.
ABOUT BULK STORAGE INC .
Bulk Storage Inc., which has been in business since 1989, offers innovative and aesthetically appealing structures are built to solve the needs of its customers for practical year-round storage of salt, sand, fertilizer, and more. Its turnkey design and construction crew not only cuts down on costs, but also puts all the responsibility on itself, giving the customer more time to concentrate on their day-to-day business endeavours.
Bulk Storage Inc. prides itself on wellbuilt, long-lasting structures for all bulk storage needs. Its geodesic domes are built to last, and its in-house design and construction team can meet any building code. It provides all custom-sealed blueprints, specifications, site reviews, and construction materials.
GEODESIC DOMES
Geodesic domes are an ideal solution for salt storage. Its round structure means that it is possible to keep the maximum amount of salt in a minimal amount of space. Its smallest design has a centre point of 25ft with large entrance doors and canopies, making unloading and loading easy and efficient. These buildings are engineered and designed to be resistant to salts’ highly corrosive properties. Only durable and long-lasting materials are used.
TENSIONED FABRIC SALT DOMES
Bulk Storage Inc.’s high-quality fabric domes are a one-of-a-kind solution that combines the efficiency of a wood-framed dome with the cost savings of a tensioned fabric structure. Its in-house mobile construction crew can get tensioned fabric domes installed much quicker than an
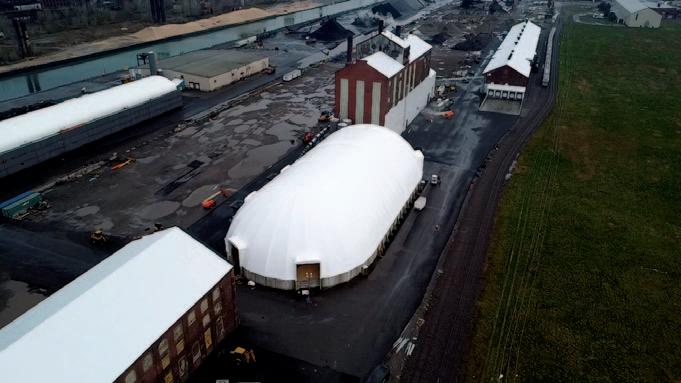
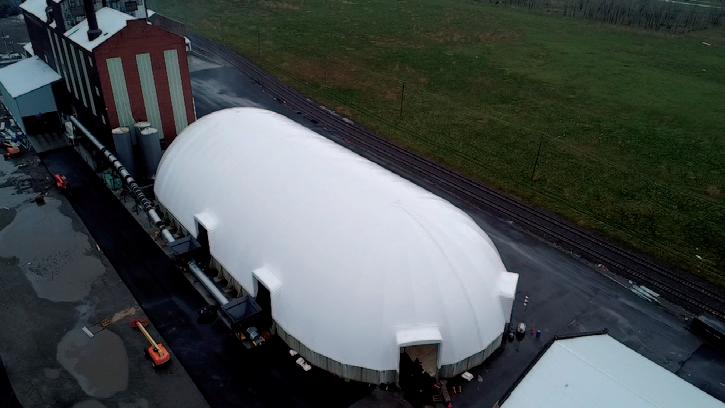
ordinary fabric shed. These structures come with hot-dip galvanized steel trusses and a 15-year prorated fabric warranty, allowing for a cost-effective and efficient salt storage structure that will last for years.
STORAGE BARNS
The same high-level craftsmanship is evident when looking into the company’s storage barns. From New England salt barns to tensioned fabric salt barns Bulk Storage Inc. takes a high level of pride in its work.
NEW ENGLAND WING SALT BARNS
New England wing salt barns have a center aisle of 30 feet for easy inside loading and dumping. The STOREMORE, New England Wing Truss structure is an adaptable, solid wood construction that complements any roofing material making it blend in more easily with its surroundings. It’s easily expandable with wraparound sheltered storage areas. The permanent base wall makes it easy to add covered storage on any side of the building for vehicles and other equipment.
TENSIONED FABRIC SALT BARNS
As with the salt domes, Bulk Storage Inc.’s high-quality tensioned fabric barns are cost-effective solution. They offer the same advantages of the salt domes, and are ideal for customers that have a budget that allows for the installation of a permanent barn structure on the existing concrete wall.
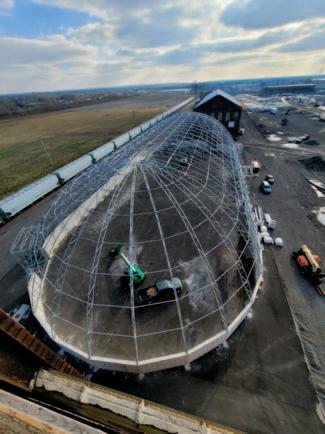
Port-Cartier and Sept-Îles Business Development Corporations announce the consolidation of their Industrial-Port Zones
In late May this year, the Côte-Nord’s two business development corporations announced the consolidation of their respective Industrial-Port (IP) Zones as part of Advantage St. Lawrence, Quebec’s new maritime vision, in partnership with Ministère de l’Économie, de l’Innovation et de l’Énergie (MEIE).
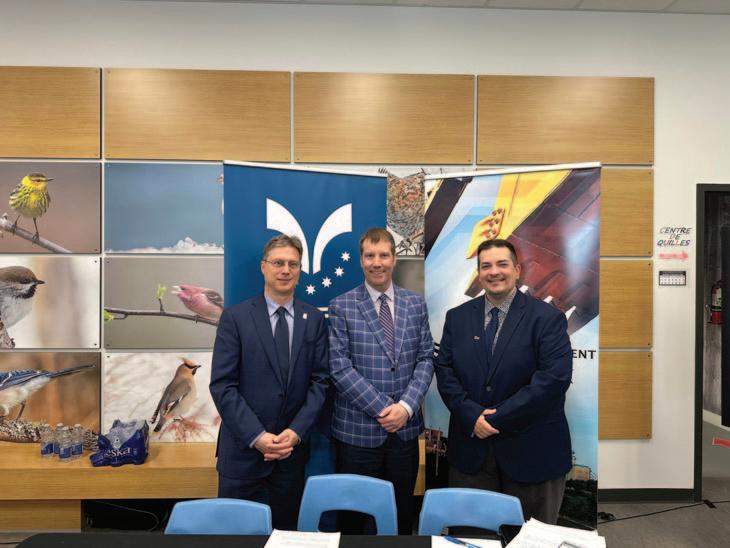
In creating one big zone, MEIE, Développement économique Sept-Îles, and Développement économique Port-Cartier are looking to consolidate their combined potential and attract new international investors and projects.
For Bernard Gauthier, Industrial Commissioner at Développement économique Port-Cartier, and Paul Lavoie, Executive Director at Développement économique Sept-Îles, the move was a nobrainer. The geographical proximity of the two IP Zones and the similar needs of their users will pave the way for many opportunities and greater synergy.
“The combined commercial activities of our two IP zones account for nearly 15% of Quebec’s annual exports. It was time for us to join forces and become a driving economic force in the province,” said Bernard Gauthier.
“Together, we can leverage this increased visibility. Our IP Zones are attracting energy transition projects and providing real options for decarbonizing the iron industry here in Quebec,” explains Paul Lavoie.
“Few people realize that half of all shipping activity on the St. Lawrence, in terms of annual tonnage, passes through the port facilities of Port-Cartier and Sept-Îles. That volume makes this new area one of the largest port complexes in North America, home to world-class shippers and facilities,” said Pierre D. Gagnon, Port of Sept-Îles President and CEO.
ABOUT DÉVELOPPEMENT ÉCONOMIQUE PORT-CARTIER
Développement économique Port-Cartier has been an economic player in PortCartier and the Côte-Nord since 1979. The organization was part of the regional coalitions that made the Sainte-Marguerite 3, Toulnustouc and Romaine dams possible. Développement économique Port-Cartier was also one of the driving forces behind the Port-Cartier sawmill, the opening of the pulp mill (three times), and the bailout of Quebec Cartier Mining Company in the early 2000s, among other things.
ABOUT DÉVELOPPEMENT ÉCONOMIQUE SEPT-ÎLES
Founded in 1974, Développement économique Sept-Îles is a municipal nonprofit that helps bring business projects of all sizes to life. Its mission is to work with
other local socioeconomic players to drive growth and improve the quality of life in Sept-Îles.
ABOUT THE PORT OF SEPT-ÎLES
Boasting diverse, state-of-the-art facilities, the Port of Sept-Îles is North America’s largest ore-handling port, with a projected volume for 2023 of nearly 40 million metric tonnes. It is also recognized as the largest primary aluminum port terminal in the Americas in terms of operational volume.
The facilities at the Port of Sept-Îles play a vital and strategic role in the economy of Eastern Canada. The port is also deeply committed to sustainable development and has pioneered the first environmental observatory on the St. Lawrence to monitor the marine ecosystem.

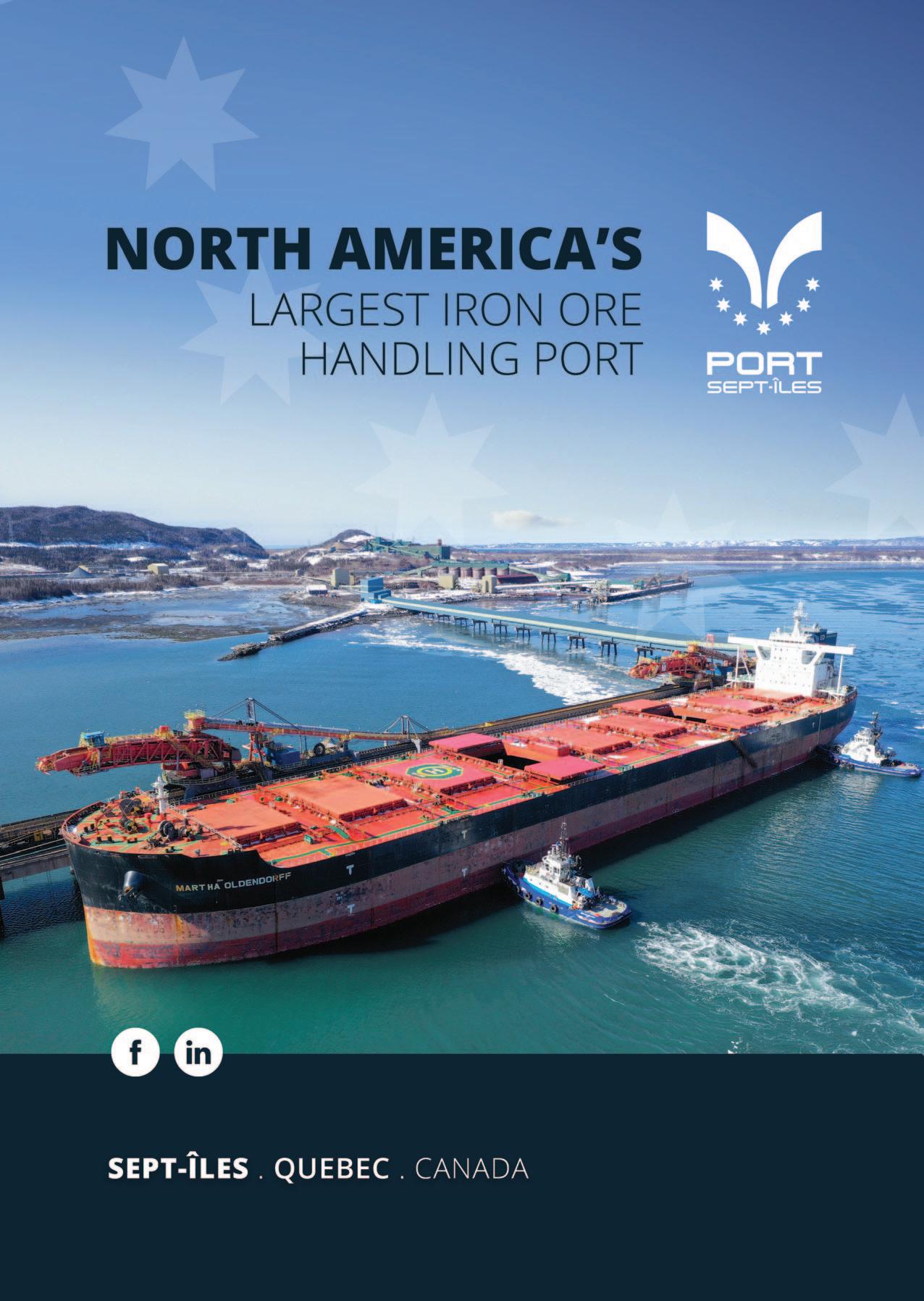
Government of Canada invests in the expansion of the Port of Oshawa
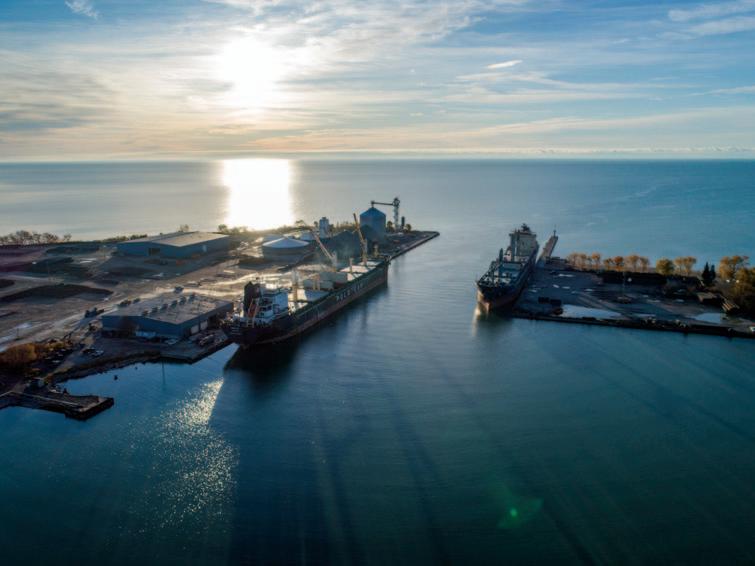
In June last year, the then-Minister of Transport, the Honourable Omar Alghabra, announced close to $14 million for an export expansion project at the Port of Oshawa. As the recipient, the Hamilton-Oshawa Port Authority is contributing $16 million, representing a total investment of almost $30 million.
With this investment, new infrastructure will be built to modernize operations in the port’s main area and position it for growth. Other improvements planned at the port include expanding marine infrastructure, upgrading storage and cargo handling terminals, as well as extending and paving roads in the harbour. This project will also increase grain exports and improve the fluidity of deliveries.
The Government of Canada is investing in well-functioning trade corridors to help Canadians compete in key global markets, trade more efficiently with international partners, and keep Canadian supply chains competitive.
Said the Honourable Omar Alghabra, “This project represents a major opportunity to increase capacity to import and export goods in and out of Ontario through the Port of Oshawa. By supporting
the Hamilton-Oshawa Port Authority, we will improve the movement of goods across Canada’s transportation networks and keep Canadian supply chains competitive.”
Government of Canada contributes to the revitalization of Port Colborne
On 11 January, the then-Minister of Transport, the Honourable Omar Alghabra, Parliamentary Secretary to the Minister of Indigenous Services and Member of Parliament for Niagara Centre, Vance Badawey, and Parliamentary Secretary to the Minister of Canadian Heritage and Member of Parliament for St. Catharines, Chris Bittle, announced an investment of up to $22.7 million to support improvements for the Welland Canal under the National Trade Corridors Fund. This investment will have important benefits for the region, such as relieving supply chain congestion and facilitating the movement of goods at the port.
The $45.3 million project will support the St. Lawrence Seaway Management Corporation in the reconstruction and rehabilitation of three wharves located at the Welland Canal in Port Colborne, Ontario. The project aims to revive these wharves, which are currently out-ofservice, to support operations and increase capacity of the trade corridor.
The Government of Canada is investing to help bolster Canada’s economic capacity and the opportunities for our businesses to expand into global markets. This represents
a long-term commitment to work with stakeholders on strategic infrastructure projects to address transportation bottlenecks, vulnerabilities, and congestion along Canada’s trade corridors.
Said the Honourable Omar Alghabra, “Investing in the rehabilitation of existing infrastructure to improve the quality and the efficiency of our supply chains is crucial to Canada’s economic success and sustainable development. Our government’s investment in the Niagara region will help ensure that the supply chains here in Ontario and throughout our country remain efficient and reliable for future generations.”
Vance Badawey added, “This announcement brings the world to Port Colborne –a game changer for Niagara. The dynamic resources of the Niagara Region are being rediscovered as we chart our future economic path. New business and new opportunities are being created on onceabandoned lands along the Welland Canal and today our government is taking a bold step in strengthening the Niagara Ports Trade Corridor while also opening the door to an expansion of Niagara’s world class tourism market.”
Chris Bittle said, “Today’s announcement is a good example of how the Government of Canada, along with partners such as the St. Lawrence Seaway Management Corporation, continues to improve our infrastructures while supplying Canadians and supporting businesses. The rehabilitation of the wharves will improve multimodal connectivity along trade routes by being close to railways and allowing access to international markets.”
Terence Bowles, President and CEO, The St. Lawrence Seaway Management Corporation, concluded: “The St. Lawrence Seaway Management Corporation welcomes this support from the National Trade Corridors Fund. We look forward to working with all partners to bring these wharves back into service with the goal of adding more fluidity to Canada’s supply chain and strengthening our connection to global markets. Once the work is completed, capacity to handle freight will increase by a million tonnes per year and new marine shipping opportunities will be created for Canadian exporters, along with a dock for cruise ships and the possibility of reduced greenhouse gas emissions.”
Minister of Transport announces funding for the second phase of the Port Weller Dry Docks Cargo Terminal Project
On 24 May, the then-Minister of Transport, the Honourable Omar Alghabra, announced an investment of up to $5.2 million, under the National Trade Corridors Fund, for the second phase of the Port Weller Dry Docks Cargo Terminal Project.
This project will improve the areas of the port that are being used for the handling of cargo. It will also develop around 11 acres of land that is available, but not being used, from the dockside to the cement trans-loading facility, as well as around the cargo laydown and handling area.
As demand for cement continues to rise, and there is less land for port development, this project will increase capacity in the Niagara ports network. It will also improve transportation connections between Niagara ports, making it easier and more efficient to deliver goods to different markets.
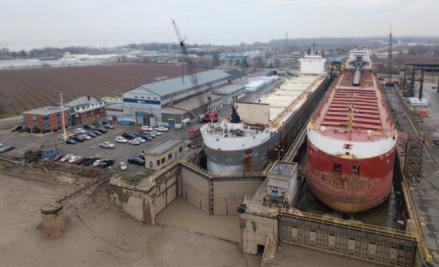
The Government of Canada keeps investing to make the country’s supply chain stronger, to boost economic growth and to create more opportunities for our businesses to grow internationally. This represents another long-term commitment to work with stakeholders on important infrastructure projects to address transportation bottlenecks, vulnerabilities,
and congestion along Canada’s trade corridors.
Said the Honourable Omar Alghabra, Minister of Transport, “The National Trade Corridors Fund improves the strength and efficiency of the supply chain, which is key to the success of Canadian companies in the global marketplace. The dry docks cargo terminal project will increase capacity, improve connectivity, and reduce costs for end-users, especially those impacted by the shortage of domestic supply in Ontario.”
Chris Bittle, Parliamentary Secretary to the Minister of Canadian Heritage and Member of Parliament for St. Catharines, added, “This investment into the Port Weller Dry Docks Terminal Project reaffirms our government’s commitment to working alongside the marine shipping
industry to strengthen our supply chain and increase efficiency. This will improve our region’s ability to handle cargo and is exciting news for economic development in Niagara.”
Vance Badawey, Parliamentary Secretary to the Minister Indigenous Services and Member of Parliament for Niagara Centre, explained, “Today’s announcement signifies the growth of the supply chains along the Niagara Ports Trade Corridor. The investment strengthens Niagara’s international trade performance, in turn, contributing to both Niagara’s and the nation’s economy.”
Ted Kirkpatrick, Director of Business Development and Government Relations, Heddle Shipyards, said, “The investment in the Port Weller Dry Docks facility will strengthen the local supply chain and promote further growth in the marine industry, which will benefit not just our companies but our regional, provincial and national economies.”
Steve Martin, Director of Sales & Business Development, Stubbe’s, concluded, “The Government of Canada’s support of the National Trade Corridors Fund is enabling Canadian businesses to be more competitive in the global market while maximizing efficiencies for local users.”
Canada and the United States Announce the Great Lakes – St. Lawrence Seaway System, Green Shipping Corridor Network Initiative
During the World Leaders Summit at the 27th Conference of the Parties to the United Nations Framework Convention on Climate Change (UNFCCC COP27), Canada and the United States announced their joint work to facilitate the establishment of a Green Shipping Corridors Network in the Great Lakes –St. Lawrence Seaway System.
Under the Initiative, the U.S. Department of Transportation, the U.S. Department of State, and Transport Canada will work with state, provincial, local communities, private-sector, non-governmental leaders and Indigenous Peoples in Canada and the United States to host consultations with ports and other stakeholders, with the goal of facilitating the establishment of a Great Lakes Green Shipping Corridor Network.
The binational Great Lakes – St. Lawrence Seaway System is a unique
commercial waterway reaching into the heartland of North America, extending more than 3,700km (2,000mi) and containing more than 110 ports. More than 200mt (million tonnes) of cargo travel on the waterway each year.
Green shipping corridors are a key means of spurring the early adoption of zeroemission fuels and technologies to place the shipping sector on a pathway to align with the goal of limiting global temperature rise to 1.5° Celsius. Through the Great Lakes –St. Lawrence Seaway System Green Shipping Corridor Network Initiative, Canada and the United States will work with industry to help facilitate the establishment of green corridors throughout the region, including by convening stakeholders and contributing to assessments and analyses relating to alternative fuels and power options within the system.
The Green Shipping Corridor Network
Initiative builds on the work launched under the ‘Joint Statement by the U.S. Department of Transportation and Transport Canada on the Nexus between Transportation and Climate Change’, issued on 25 February 2021. The governments view the Great Lakes – Saint Lawrence Seaway System Green Shipping Corridor Network Initiative as an important element in catalyzing development of the fuels and infrastructure needed to make the transition to low- and zero-emitting shipping, and, on both sides of the border, creating the jobs to make that fuel available and infrastructure development a reality. In the future the Initiative may expand to support green shipping corridors on US and Canadian routes along both countries’ coasts, leverage experience from similar initiatives in other regions, and supplement regional and global efforts already under way.
Port Milwaukee, The DeLong Co., Inc. celebrate grand opening of Agricultural Maritime Export Facility
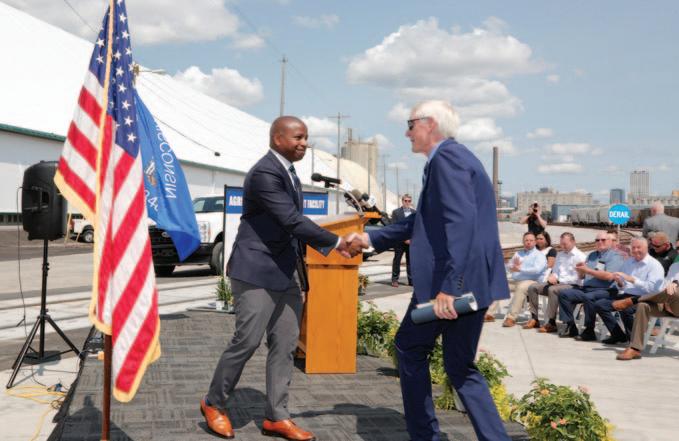
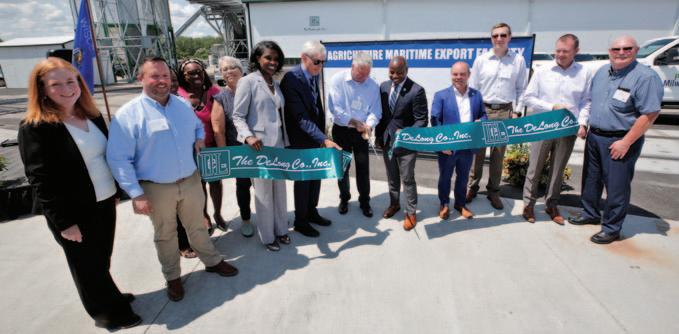
THE LARGEST ONE-TIME INVESTMENT IN PORT MILWAUKEE HISTORY SINCE THE 1950S
On 18 July, Port Milwaukee and The DeLong Co., Inc. celebrated the grand opening of the $40 million Agricultural Maritime Export Facility on Jones Island. Representatives from the Port, DeLong and the City of Milwaukee were joined by Wisconsin Governor Tony Evers, Mayor Cavalier Johnson, and federal, state, and local officials to celebrate the completion of this major investment that will create jobs, support Wisconsin’s agriculture industry, and grow the regional economy.
“Milwaukee is the economic engine for our state and region. This addition to the port’s operations will expand a strong partnership that includes The DeLong Co., the City of Milwaukee, our state and federal partners, Wisconsin agriculture, and world markets,” said Mayor Johnson. “Thank you to our many partners for advancing this continued growth at Port Milwaukee.”
“We want to thank the City of Milwaukee for their partnership on this project. We look forward to being part of the community,” said Bo DeLong, Vice President of Grain, The DeLong Co., Inc.
“Port Milwaukee is an integral link in the Wisconsin economy. In this case, we are connecting Wisconsin farmers, growers, and producers with new international markets,” said Jackie Q. Carter, Director of Port Milwaukee. “The combined support from local, state, and federal officials affirms the importance of this new asset on Jones Island. The development of this facility at Port Milwaukee is a great addition to the city’s marine commerce, and I’m excited to witness the benefits it will create for our maritime economy.”
The facility, located on the west side of Jones Island, will be one of the first on the Great Lakes–St. Lawrence Seaway (GLSLS) System to handle various agricultural commodities via truck, rail and international vessel, including Dried Distillers Grains with Solubles (DDGs). DDGs are an animal feed supplement derived as a byproduct of ethanol high in nutrients. This facility will open Wisconsin’s maritime and agricultural economies to new international markets for this and other products. Future service at the facility may also include the export of Wisconsin-grown soybeans, corn and grain.
AGRICULTURAL MARITIME EXPORT FACILITY DETAILS
Storage capacity: 30,000 metric tonnes of DDGs (or 45,000 metric tonnes of soybeans)
Inbound transportation modes: rail (served by Union Pacific and Canadian Pacific Railroads); truck
Rail track capacity: 100 hopper cars
Outbound transportation modes: vessels with capacity of 7,000 to 22,000 metric tonnes; barges
Load rate: 1,000 metric tonnes per hour
Annual export capacity: 400,000 metric tonnes
Products handled: currently DDGs, eventually other grains and feedstuffs, such as soybean meal
International markets: primarily Western Europe and Northern Africa
The new transload facility includes rail and truck gravity dump hoppers connected to a conveyer system to transport the material into a fabric storage building. Inside the fabric building, a reclaim system conveys product to be loaded into bulk material cargo vessels or barges. Vertical storage structures will be added to handle soybeans and other grain in the future.
The facility is fully operational and in
June 2023 successfully loaded its first vessel of Wisconsin-produced DDGs, which were made with corn from Wisconsin. The Wisconsin Department of Transportation has estimated the DeLong terminal will generate $63 million in new statewide economic impact annually, increasing exports through Port Milwaukee by as much as 400,000 metric tonnes per year.
“This new facility will have a tremendous impact here in the local Milwaukee community and around the state and will help ensure more of our farmers’ best-in-class, Wisconsin-made goods will be shared with folks all over the world,” said Governor Evers. “I want to congratulate the DeLong Company, Port Milwaukee, and everyone that played a role in getting this project over the finish line. Port Milwaukee is a vital point of connection in our state and nation’s supply chain, and this project paints a clear picture as to why we must continue to invest in the success of our transportation systems and cornerstone Wisconsin industries,
especially in Milwaukee.”
“The facility is among the first on the Great Lakes-St. Lawrence Seaway system that can handle a variety of agricultural commodities via truck, rail and international vessels,” said Wisconsin Transportation Secretary Craig Thompson. “It’s an important new resource for both shipping and agriculture, and its impact will be felt statewide.”
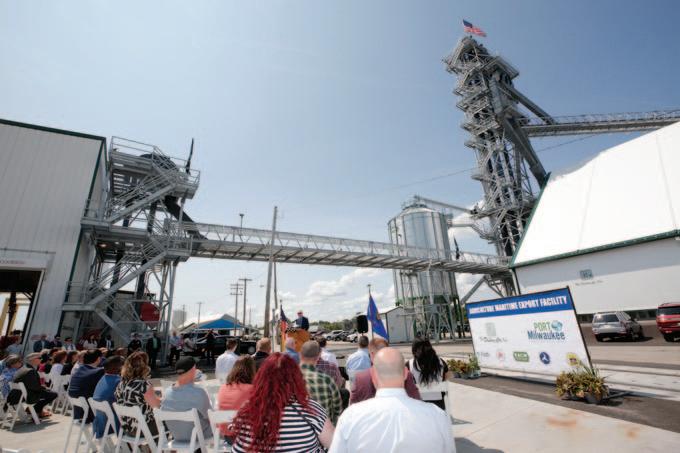
Thanks to a robust public–private partnership, this development is the largest one-time investment in Port Milwaukee since the 1950s. Port Milwaukee was one of the first nationwide grant recipients of the Port Infrastructure Development
Program (PIDP) through the U.S. Department of Transportation. Additional facility funding has been provided by the Wisconsin Department of Transportation, Port Milwaukee, and The DeLong Co., Inc.
ABOUT PORT MILWAUKEE
Port Milwaukee is an economic entity of City government governed by the sevenmember Board of Harbor Commissioners, a panel appointed by the Mayor and confirmed by the Common Council. It administers operations on the 467 acres that make up the port. It promotes shipping and commerce throughout the region by providing access to domestic and international ships, rail, and over-the-road transportation.
ABOUT THE DELONG CO., INC .
The DeLong Co., Inc. is a sixth-generation, family-owned business that is headquartered in Clinton, WI. The company operates 37 locations around the US and comprises six divisions of agricultural and logistical sales and services: grain, exports, agronomy, seed, transportation and wholesale feed. The DeLong Co., Inc is the largest US exporter of containerized agricultural products.
Regional, national and international logisticians count on Port Milwaukee for a turnkey approach to solve their transportation and supply chain needs. Strategically located in the industrial center of the U.S., Port Milwaukee provides premier access to domestic and world markets.
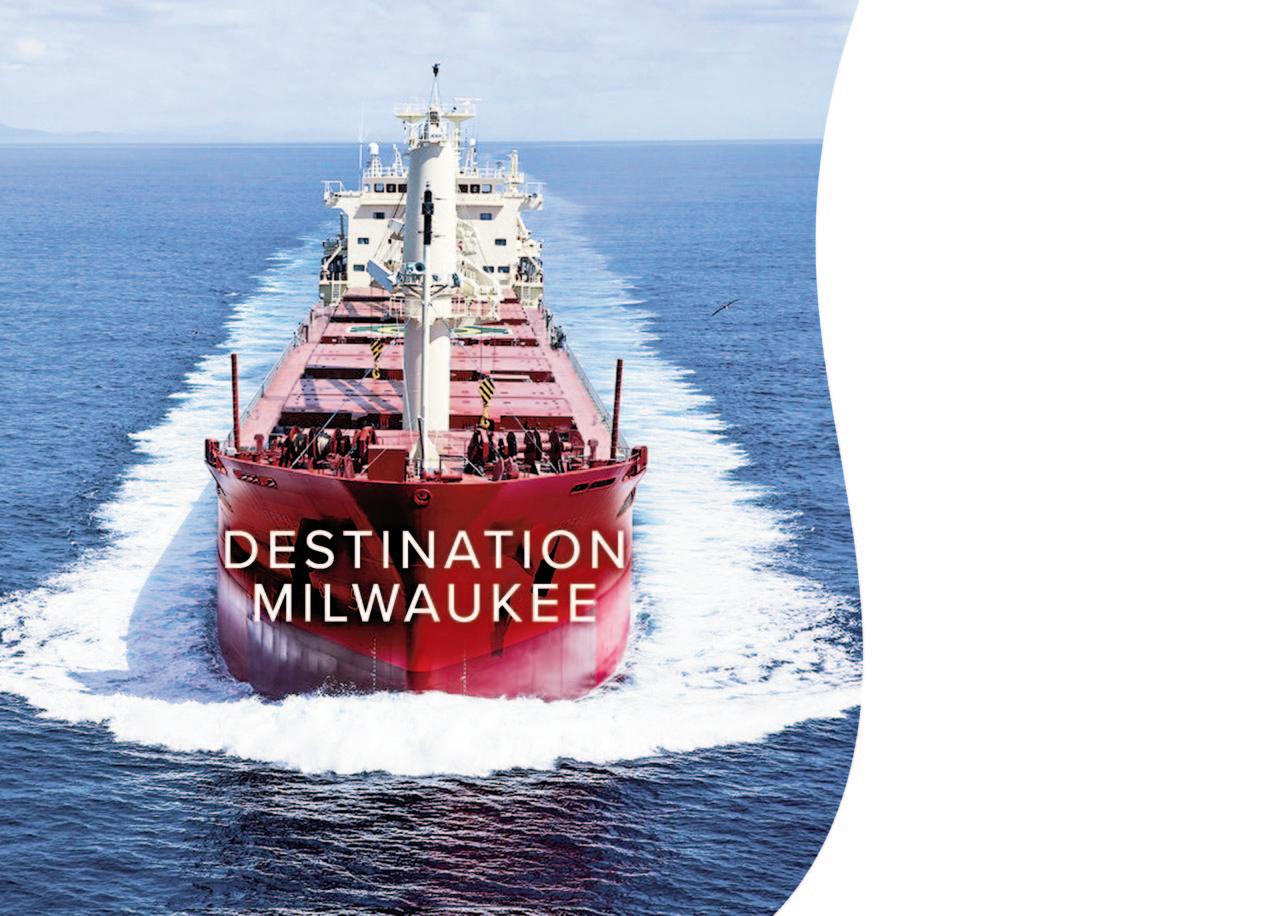
SHIP LOADER SPECIALIST
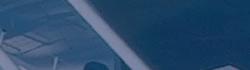


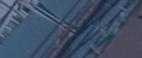
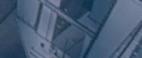
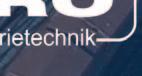

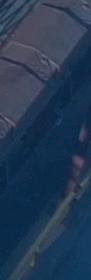
NEUERO produces the most reliable and high-quality bulk ship loaders worldwide. Environmentally friendly with less dust, less noise and more efficiency | neuero.de/en
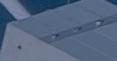
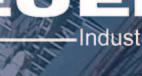
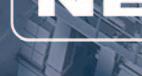
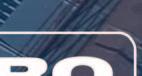
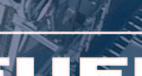
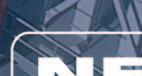
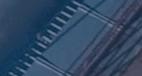



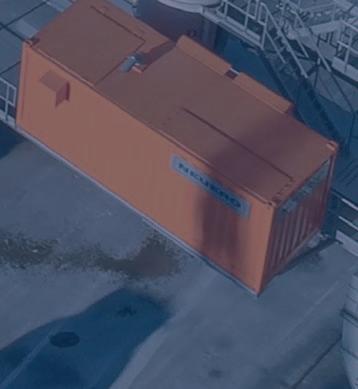
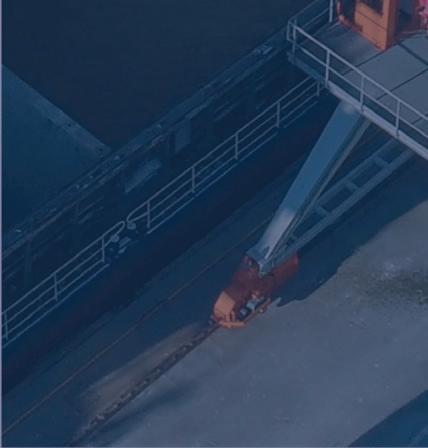
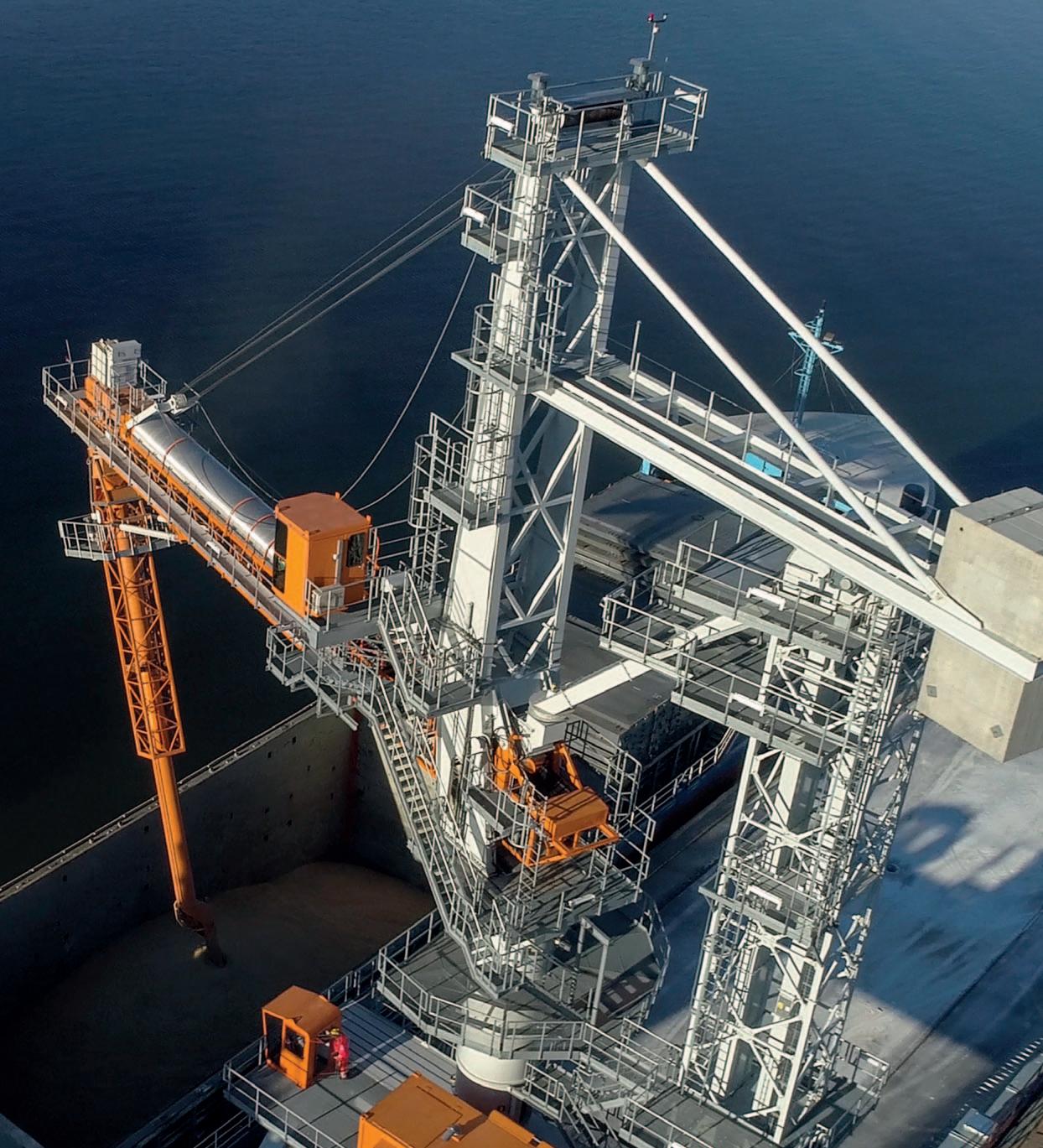
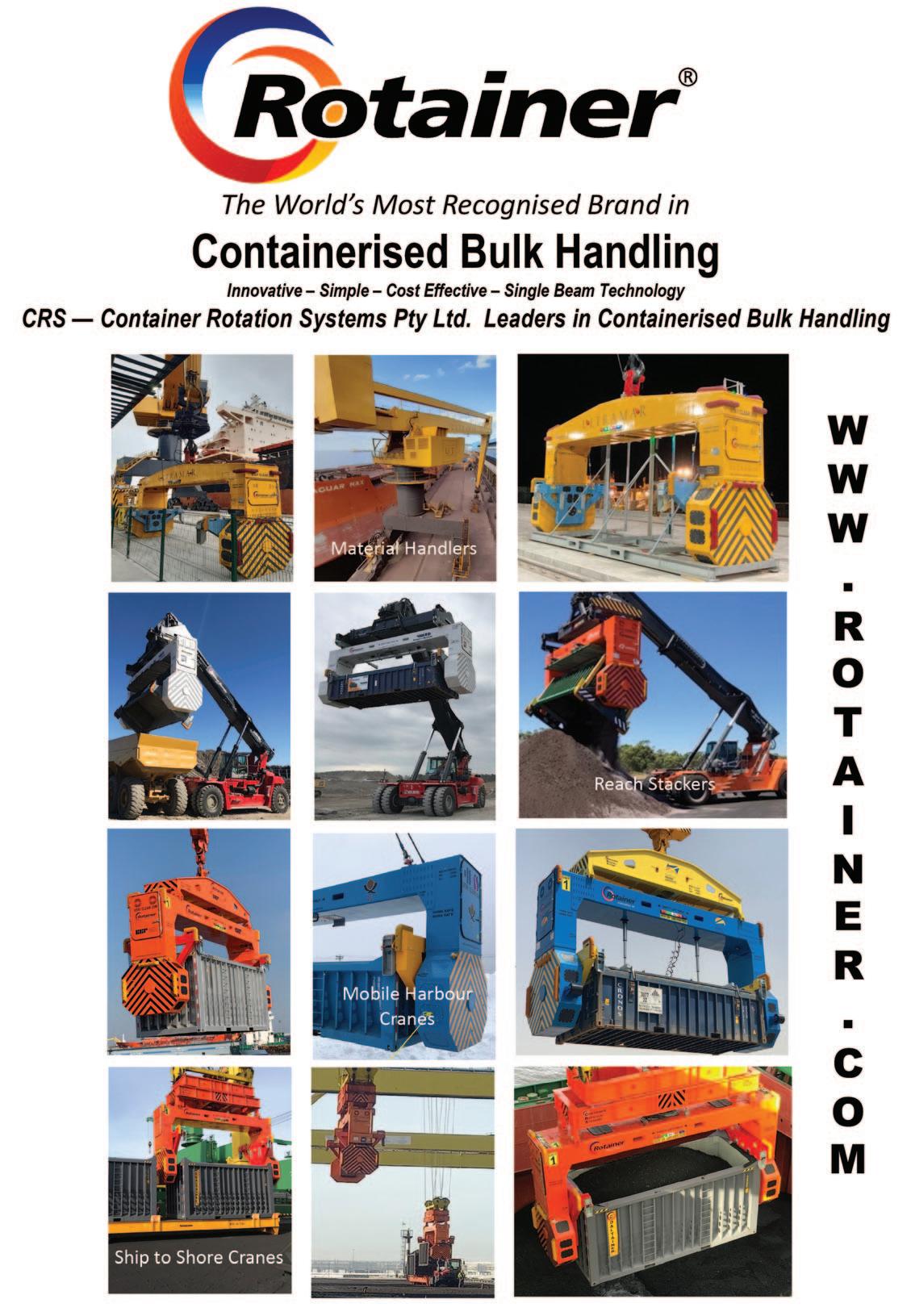