
3 minute read
A risk-based approach to maintenance
from ThinkSafe vol. 2 no. 2 May 2020
by Department of Local Government, Industry Regulation and Safety
Recent worksite incidents prompted the Department to take a close look at the ways industry can improve maintenance using a risk-based approach.
Some of these incidents occurred despite there being a maintenance plan in place.
When large structures, fixed and mobile plant and machinery fail, it can lead to:
catastrophic safety incidents risks to the health and safety of workers disruptions production downtime.
Understanding the safety hazards of structures, plant and machinery will help workplaces to maintain safe operation, manage and reduce the risk of failures.
Knowing the hazards
Large structures, plant and machinery on mine and industrial sites have both common and unique hazards. However, sites may not always be equipped to know the potential hazards and associated risks, and this itself can be a hazard.
Identifying each hazard and measuring it against the likelihood and severity of risk is the first step in a risk-based maintenance approach.
Performing this step early in the process allows designers and manufacturers to mitigate identified hazards and risks during the original design, engineering and development phases. This is done by embedding controls in the maintenance procedures that comply with or exceed recommended relevant standards. When decisions are made about whether or when maintenance tasks are undertaken, the design, manufacturer instructions and Australian Standards must not be compromised.
Therefore it is important to: use the structure, plant or machinery as it was intended; always maintain the original design without removing or adding parts; use only recommended original equipment manufacturer (OEM) parts; follow all design and manufacturer instructions; seek appropriate advice to double-check any inconsistencies.
Risk-based maintenance plans
Individual documented risk-based plans address the safety hazards for every structure, plant and piece of machinery. Maintenance should be planned, actioned and recorded in detail throughout the life of the equipment.
When integrating safety into the risk-based maintenance plan, consider the following.
Life cycle stage of the equipment – Where in the life cycle is this structure/plant/equipment? Current condition of the equipment – Has this item been well-maintained and repaired using authorised or manufacturer parts? Given its current state, how many years will the equipment last in good working order before replacement is necessary?
Communication – Does the work site encourage regular and open communication with all parties about the safety of each item? How does this happen and what are the ways to improve?
Competencies – Are workers and contractors trained and knowledgeable about the item they work with, inspect or maintain?
Safety documentation – Are there documentation, manuals and structural drawings detailing the safety aspects of maintenance and repair? Where are they kept? Are they accessible?
Breakdown or failure – What safety reactions, training, lock-out procedures and temporary safe work-arounds are in place in cases of foreseeable failures or unexpected breakdowns?
Environment – What are the localised impacts of weather and weathering?
Corrosion – What are the specific corrosive effects of substance build up (e.g. salt, minerals, chemicals, dust, grease) that will affect the operation of the item or cause deterioration?
Inspection – Is there scheduled time for thorough inspection and adequate testing to ensure the integrity of each item?
Cleaning – Is the specific item cleaned of dirt and build-up regularly and prior to inspection?
Access – Are there adequate and safe access points to properly inspect, maintain and repair the item?
Interplay – Do any of the above interplay? Will the maintenance or breakdown of one piece of equipment affect other structures, plant or machinery?
Human and organisational factors in maintenance activities
Some of the most catastrophic global industrial accidents were due to maintenance error and skewed risk assessment of the early warnings signs. The Piper Alpha incident is still the most famous catastrophic accident of this nature.
However, maintenance hazards do not exist in isolation and often interact with all levels of the work environment, including human performance.
Understanding and managing human and organisational factors – all elements within a workplace that have an impact on the people who work there – is key to developing and maintaining safe workplaces.
Further information
Structural
SIR No. 274 Structural failure of fixed conveyor stacker
SIR No. 269 Structural failure of a corrugated steel water tank
MSB No. 140 Structural collapse of buildings and temporary structures during wind events
Mechanical
MSB No. 164 Wheels detaching from graders
MSB No. 162 Inspection and maintenance of special purpose lifting plant and hoists
MSB No. 145 Uncontrolled movement and derailment of fixed cranes during storm wind events
NOPSEMA
The Regulator (Issue 1 2020) Managing ageing infrastructure
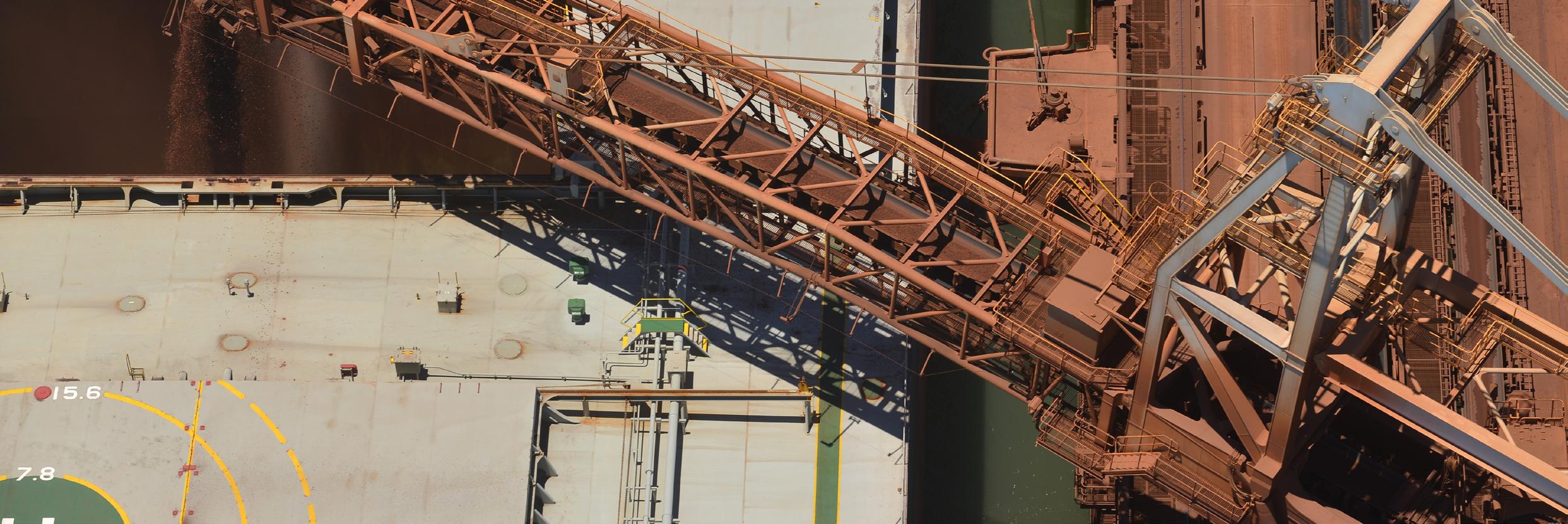