
8 minute read
Randy Borden- He Spoke Bespoke
By James R. Benya, PE, FIES, FIALD
As most lighting designers know, not every luminaire can be found in a catalog or website, especially those with a significant aesthetic relative to the project. While many of us have aesthetic skills that include being creative enough to imagine what a luminaire should look like, a small percentage of us are skilled at manufacturing engineering and realizing our ideas. Most of us, including me, rely upon lighting fixture sales representatives and the companies they represent to help us find the perfect luminaire. And often our visions need a custom or specialty lighting manufacturer to make them come true.
In the history of lighting design in Northern California, a number of companies set up shop, and their products served many markets. Several had great significance to me as a lighting designer, including Gardco, Peerless, Boyd, and Prescolite, most of which have since been acquired as the lighting industry consolidated in the last three decades. What remained were a few smaller and specialty companies, and there was one company, Shaper Lighting, that stood out as being uniquely supportive of lighting designers, interior designers and landscape architects –and especially, architects. It was founded by Hans Shaper (1915-2004), a Holocaust survivor and industrialist who escaped Germany at the beginning of the war and first worked for Sam Herst, the late president of Peerless. He soon started Shaper Lighting Products in Richmond, California in 1952.
Randy Borden, an architect who started using Shaper’s products in the late 1970s, took up Hans’ offer to retire, and Randy bought the company in 1983. Key personnel included his second in command, Allen Reaves, and a decade later, the late Robert Bruce Thompson1 joined them as National Sales Manager. Ultimately, like most Bay Area lighting manufacturers, Randy sold the company to a conglomerate (Cooper Industries) in 2001 and worked there until 2005.
However, corporate work was not for Randy. He chose to start over, continuing to serve the lighting community with a new company, Borden Lighting, making small-run bespoke products that filled the special need of many very hands-on architectural projects. He is, after all, an architect, and his products reflect his aesthetic taste and skills and those of his audience of design professionals with a decidedly modernist architectural leaning.
Over the years I counted on Randy, Allen and Bruce; we’ve stayed in touch, and recently our conversation turned to Randy’s reminiscence. He tuned his talents in lighting as a rookie under the tutelage of Hans and began his transition towards decorative architectural lighting in the purest sense. “Those were exciting times, the very beginning of the groundswell of change from incandescent to compact fluorescent lamps”, he recalls. “When Hans Shaper handed me a small magnetic ballast and a triple tube small fluorescent lamp, he said, ‘This is the future of lighting’.” Randy knew he was on the cusp of a sea change in the lighting industry and that it would set his future course.
At the time, decorative lighting was designed around the incandescent light bulb. To conserve energy—driven by code—compact fluorescent lamps provided a way to make decorative fixtures more energy efficient while also providing longer lamp life.
Randy noted, “At Shaper Lighting, that meant configuring existing incandescent fixtures for compact fluorescent (CF) lamps. At the same time, it enabled new form factors, designed around CF lamps. So, from the mid-80s through the early 2000s, decorative fixtures, as well as commodities such as downlights, fixture design was based on CF lamping for commercial and institutional use.” He also noted, “Technology had its problems with magnetic ballasts and flickering starts for CF lamps,” which were eventually solved by electronic ballasts and improved lamp technology.
Randy and Shaper Lighting, being California-based, were among the first to design families of fixtures specifically for CF lamps, as well as using CF lamps in cataloged and bespoke designs for lighting designers like yours truly.
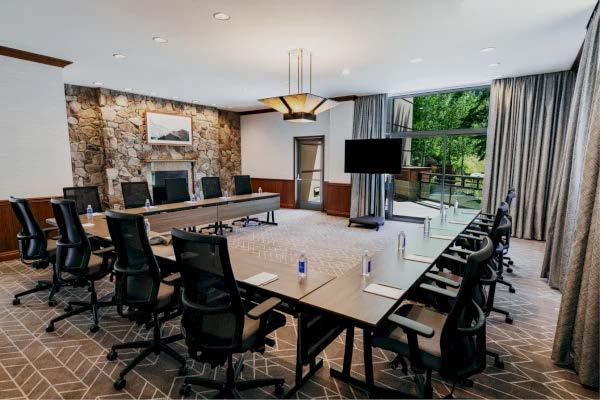
When Randy started Borden Lighting, it was about the time of the first practical white LEDs. He quickly learned that LEDs were not like legacy lamps, but they could be configured as a source for most applications. Randy, like many of us, considered early attempts to make LED lighting to have been the “wild-wild west.” LEDs didn’t have the horsepower to provide useful light. Their efficacy was unimpressive. Heat management was a serious problem. Color temperature and color rendering were worse than compact fluorescent. And flicker…. oh my.
For these and other reasons, LED technology moved very slowly at first. For decorative fixture manufacturers, the first challenge was adapting them to existing products, in many ways like the transition from incandescent to compact fluorescent sources. Then, as the technology advanced and LED manufacturers offered a greater variety of increasingly useable form factors, drivers and supporting hardware, Borden Lighting was able to both readily adopt existing luminaires and create brand new products, many of them not practical using legacy light sources.
Perhaps the hardest part of evolving to using LEDs was learning how to manage heat in a whole new way. Legacy lighting products got hot, so luminaires were designed to use air movement to cool. LEDs could not be allowed to get too hot themselves or their life would be impacted.
THE LED POST LUMINAIRE
In 2009, the author conceived a post-top light for Yosemite National Park using a tunable LED light engine mounted in a heat sink atop the post shining up onto a solid hood above, and a prototype was built by Borden Lighting and demonstrated at the park. Randy Borden then worked with lighting designer David Malman to improve the design for Malman’s specifications at the Presidio National Park, and it became the Borden 922, now the Manning B-922.
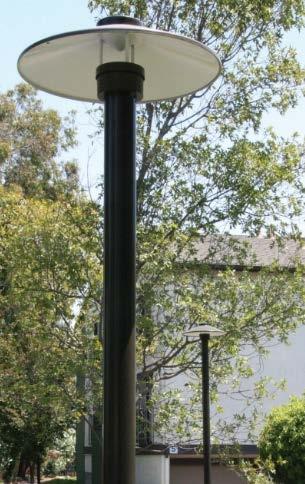
THE WEDGE BOLLARD
In 1997, for a project at the Yosemite Lodge, the author asked Shaper Lighting’s Allen Reaves and Randy Borden to adapt their model 719 wall sconce to mount onto a post to be used as bollard. The result evolved to LED and became the Borden 919, now offered as the Manning Borden Collection B-919.
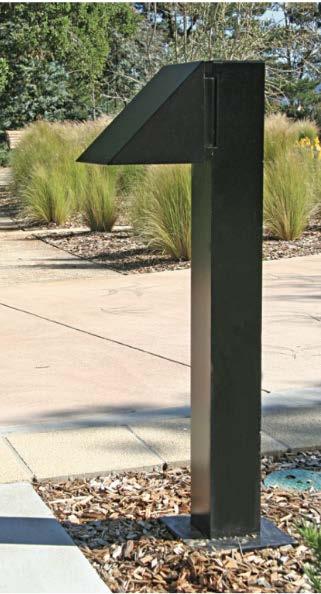
THE FAUX ALABASTER CHANDELIER
In 1988, working with architects SMWM, the author asked Shaper Lighting to engineer and build a distinctive semi-indirect Biax pendant luminaire with a central downlight for use in the event and meeting spaces of the Everline Hotel and Resort (formerly Resort at Squaw Creek), Olympic Valley, CA. Randy Borden and Allen Reaves created two versions, a large version for large spaces and a smaller version for meeting rooms. The luminaire became a part of the Shaper catalog and continued for more than a decade after the Cooper Lighting acquisition.
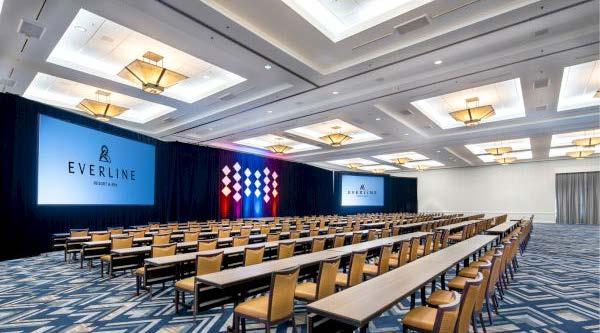
At first this was a problem, but as luminaire designs evolved, heat became less of an issue. By 2014, fixture manufacturers could offer at least 50,000 hours of LED life, and maintenance became a feature and attraction of LED fixtures. For instance, with outdoor lighting (one of Randy’s fortes), LEDs operating 12 hours per day should last 16 years without much maintenance.
Because of his background at Shaper, Randy followed the evolution of LED replacement lamps carefully. There was a certain simplicity to making luminaires with sockets, and for the foreseeable future, screw-based lamps and fluorescent tubes with internal drivers have definite appeal. He points out, “So when the really cool LED ring pendant isn’t producing light, no one can just “change the light bulb”. The fixture may even have to be demounted to change the LED tape and/or the driver.”
He also recognizes that LEDs have allowed fixture design to evolve, creating exciting new form factors. He said, “ADA wall sconces and some pendant fixtures can only be designed with LED modules or tape and drivers that are built-in”.
However, he still has reservations. “I would suggest that not enough time as been given to ‘how to change the light bulb’. There’s probably a joke there about how many maintenance men does it take to change an LED.”
When Randy FINALLY retired, I was broken-hearted. Although I was reassured to see some of his most popular products now in the Manning Lighting catalog (including several that I had something to do with), I was afraid that his absence would leave something missing in lighting design. I sure hope that the enthusiasm for printed lighting and other options gives lighting designers back the ability to speak “bespoke” and the proudly create something that is, for the right client, truly special.
References
Check out the Robert Bruce Thompson Annual Student Light Fixture Design Competition (www.rbtcompetition.org) for more about him and his lifelong commitment to lighting fixture design.
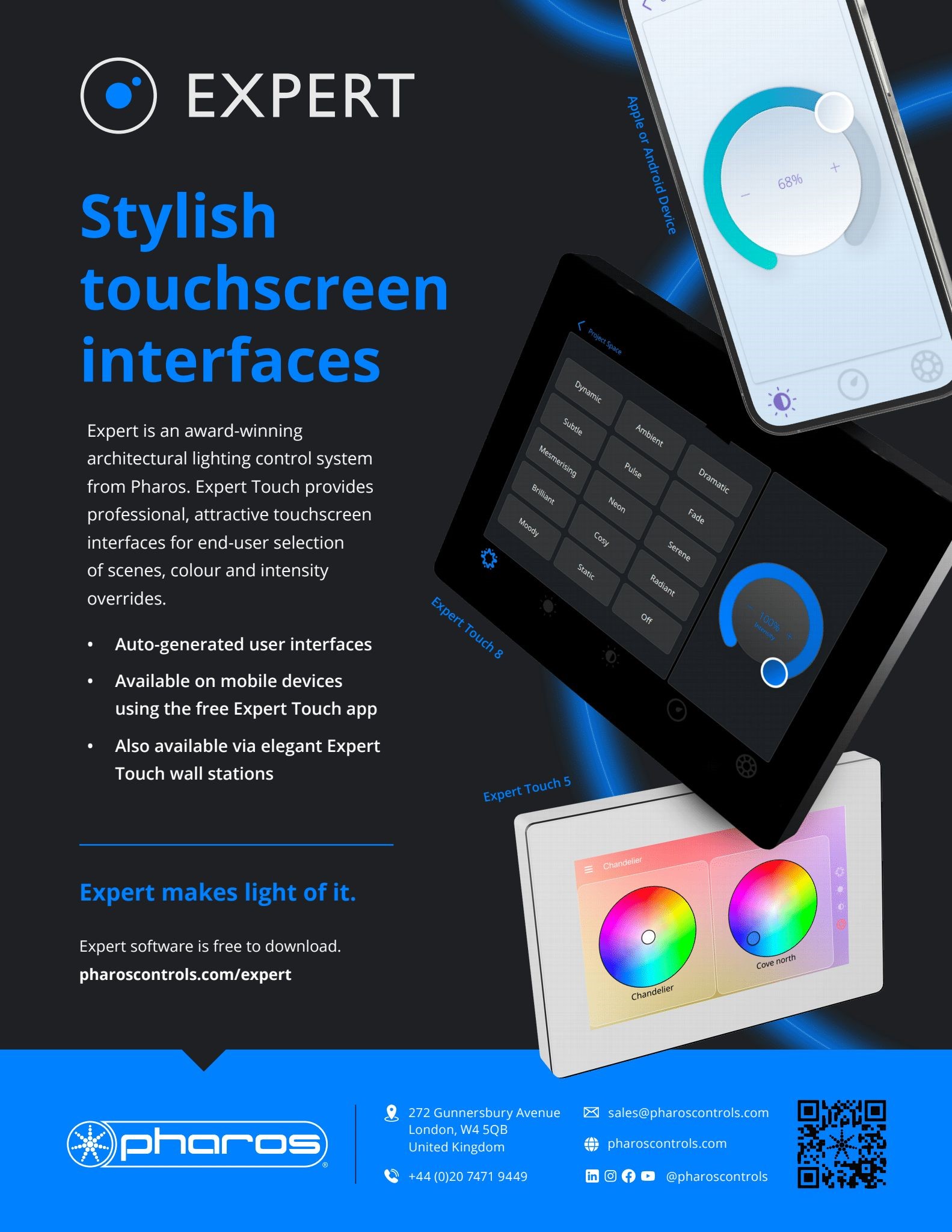