
19 minute read
EARTHWAVE FleetWatcher
Crews are constructing 17 bridges along the corridor and all 17 have drill shaft foundations. Approximately 75 percent of the piers have been constructed. The project includes the construction of two tolled lanes in each direction, an adjacent shared use path from Hero Way to Seward Junction Loop and aesthetic enhancements along the corridor.
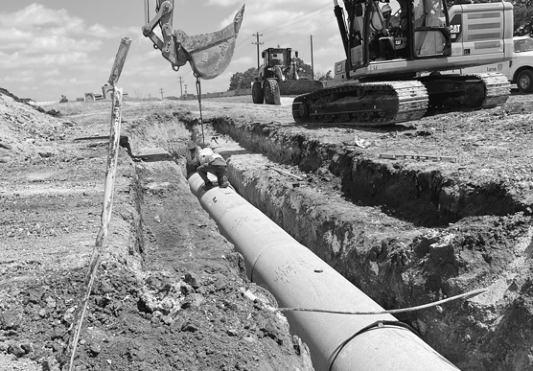
TEXAS from page 32
For the earthwork, subgrade work has taken place for much of the proposed roadway but there is still work to go to get it to final grade.
“To date, the roadway base material has been placed only for a limited portion of the frontage road where a widened shoulder was needed for construction,” said Sexton. “The newly constructed 183A Toll mainlanes will be concrete. The existing U.S. 183 lanes which will function as a non-tolled frontage road are asphalt and will receive a fresh asphalt overlay prior to the end of construction.”
For the retaining walls and MSE walls, precast sections are being installed.
“Most of our retaining walls are Mechanically Stabilized Earth [MSE] walls, for which there is not a traditional ‘foundation,’” said Sexton. “MSE walls use roadway embankment material to anchor the retaining wall panels via a soil mat system between the walls and connected on the inside of each panel. Our next most common retaining wall style is the soilnailed retaining wall which also doesn’t use a traditional foundation. Instead, the nails are drilled and grouted into the existing, adjacent earth. Traditional spread footing retaining walls are limited to use for some of our water quality ponds. In those cases, the foundations may be just a few feet below finished grade as required for the area.” Bridge Construction
Crews are constructing 17 bridges along the corridor and all 17 “have drill shaft foundations and approximately 75 percent of the piers have been constructed,” said Ancira. “The number of lanes varies from two to three. The time to construct a bridge varies depending on weather, traffic conditions, and complexity.”
The new bridges consist of 10.9 mi. of precast concrete and 12 mi. of drainage system pipe will be installed.
“These bridges are similar to others in the region and use precast concrete beams to support a reinforced concrete bridge deck,” said Sexton. “The pedestrian bridge will be steel framed with an Ipe wood deck and will be constructed to match the style of the existing pedestrian bridges on the existing portion of the 183A shared use path. Approximately 76 percent of bridge columns are complete.
“The total length of all the bridges together equates to 2.02 miles, including the pedestrian bridge which is 660 linear feet long,” Sexton added. “The lengths of the bridges vary from 169 feet to 1,160 feet long and carry a different number of lanes depending on the bridge’s purpose. For example, the U.S. 183 U-turn bridges at SH 29 will each have just a single lane, while the SH 29 bridge crossing 183A Toll will carry six total lanes. The project also accounts for future lane expansion with foundation sleeves at the bridge abutments and a drainage system sized for a future third lane in each direction.”
Bridge construction is subject to variables like material and crew availability, construction sequencing, type of bridge, length of bridge, weather and more.
“All these variables play a part in the length of time to complete a bridge and therefore the timeline from one bridge to the next can vary greatly,” said Sexton.
Many detention ponds are currently under construction along the corridor, and more than 64,000 linear ft. of pipe and culvert will be used for the drainage system project wide. The drainage inlets, manholes and junction boxes are precast by Oldcastle Infrastructure based in San Antonio.
“Drainage pipes and structures are buried anywhere from about 8 feet to 40 feet deep,” said Sexton.” Cranes are involved in setting larger precast structures. Smaller structures can be placed using an excavator.”
Over the past year, excavation and earthwork has been a large part of the construction along the corridor, and in the next year, excavation underneath SH 29 will begin.
“For large jobs like these, Lane Construction’s earthwork subcontractor is using a Cat D10 dozer; a large, effective piece of equipment not seen on your average construction site,” said Sexton. “For bridge beam operations, two 350-ton cranes and a 300-ton crane have been instrumental in safely and quickly setting beams in place. Four manlifts are used to transport the crew from the ground to the bridge caps, and one trackhoe is in place to reconfigure the haul trucks and trailers to keep operations moving.”
Utility relocation has progressed smoothly,
“As anticipated, we’ve been able to prioritize the thirdparty utility owners’ relocation work to minimize impacts to construction efforts,” said Sexton. “So far, this work has not impacted project delivery and it appears it will continue to be a non-issue moving forward.”
The precast beams are cast by Texas Concrete Partners based out of Victoria, Texas, the concrete deck panels are cast by Bexar Concrete Works, the MSE wall panels are cast by Tricon, and the steel trusses and overlook platforms for the pedestrian bridge over the San Gabriel River will be fabricated by Contech Engineered Solutions.
The Lane management team also includes Vice President Jason McLear, construction west; Senior Project Engineer Benjamin Jablonksi; and Project Superintendent Julian Sepeda.
“The Mobility Authority, the contractor and the CEI have a great working relationship,” said Ancira. “Open and transparent communication is key to working successfully together.”
There are approximately 105 Lane and subcontractor personnel on-site. The main subcontractors are Ranger Excavating for earthwork activities; Beaird Drilling for bridge drill shafts; SICE for electrical and signage components; D Guerra Construction for waterline utilities; and Oscar Orduno for temporary special shoring.
New materials being brought in include more than 230,000 tons of concrete, more than 21,000 tons of asphalt paving, 325,000 cubic yards of MSE wall aggregates and 148,000 tons of concrete paving aggregates. Additional equipment on-site includes seven large excavators, 11 wheel loaders, four rough terrain cranes, and six dozers.
“The major wear and tear issues that occur are potholes,” said Ancira. “These occur along the existing southbound and northbound lanes of 183A. Repairs are made once it is safe and when minimal impact to the traveling public can be expected. We have on-site mechanics and when needed, thirdparty mechanics are brought in.”
In the Texas area, Lane purchases and rents equipment from local and regional dealerships.
The traffic management plan is working well.
“The project is phased to shift the current lanes toward the outside while the majority of construction activities takes place in the center median,” said Sexton. “Once we shift the lanes back to their original positions, they’ll remain there in the final configuration. With the majority of work focused inside the median of the existing lanes, we’ve managed to maintain nearly full lane capacity during construction so far. The largest anticipated temporary reduction in traffic capacity will occur in the future, when excavation and bridge work at SH 29 occurs.” CEG (All photos courtesy of Texas Central Mobility Authority).
MINOTAUR from page 14 big three providers of precision construction solutions — Leica Geosystems, Topcon and Trimble. This allows equipment owners to add the machine to their fleet with the confidence it can be integrated directly into preferred/existing machine control ecosystems. It also provides rental fleets the ability to easily switch between machine control brands, which allows for excellent rental flexibility based on customer preference.
Powerful Site Loader, Attachment Beast
In its loader configuration, the Case Minotaur DL550 features a 5,500-lb. rated operating capacity (50 percent of tipping load) with 12,907 lb. of breakout force. It features a vertical lift pattern and operates in the ISO control pattern. It also features advanced electro-hydraulic control capabilities where operators can easily dial in total machine responsiveness to low, moderate or aggressive; or independently set tilt, lift and drive speed, as well as loader arm and drive control to best meet the demands of the work.
Case builds the machine standard from the factory with enhanced high-flow auxiliary hydraulics for running the most demanding and high-powered attachments — such as mulching heads and cold planers. Minotaur’s enhanced high-flow hydraulics can deliver up to 41.6 gpm at 4,100 psi via hydraulic quick couplers.
The machine also allows operators to harness all that power with “Hydraulics on Demand”, where the operator can easily select the percentage of auxiliary hydraulic flow to the attachment via the machine’s multi-function display. This allows the operator to dial in attachment performance to their preference or the recommendation of the attachment manufacturer — ensuring both effective and proper operation of the attachment.
“The front coupler featured on this machine is the same as you will find on most compact loaders — this opens the machine up to be used with hundreds of attachments,” said Jacobsmeyer. “We’ve given operators the ability to turn this compact dozer loader into one of the industry’s most versatile and powerful compact machines, and deliver on the awesome capabilities that other manufacturers tried to emulate after the original concepts were announced.”
Fully Connected, Collaborative Fleet Management Case has taken fleet management of compact equipment to an entirely new level with the inclusion of the Case SiteConnect Module — a powerful device that improves

The Case Minotaur DL550 compact dozer loader has pushed through more than 10,000 hours of field tests, in addition to countless customer clinics and typical lab and engineering testing.
the volume, flow and integration of data to the Case SiteWatch telematics platform for real-time monitoring and management of maintenance and service intervals, as well as the analysis of equipment utilization and performance.
It’s also the foundation from which Case has made the collaborative fleet management and remote diagnostics of compact equipment a reality. This enhanced connectivity allows the machine owner to share — with permission — real-time machine information with their Case dealer and the Case Uptime Center in Racine, Wis.
“With both Case and the local Case dealer monitoring machine performance, we’re able to be proactive and anticipate potential equipment needs to maximize uptime,” said Jacobsmeyer. “The goal of these advances is rooted in customer need for maximum uptime, and the Case Minotaur DL550 compact dozer loader delivers that — including the ability to remotely diagnose machine events and drastically shorten response times when service is needed.”
Case achieves these remote service capabilities through the Case SiteManager App (iOS and Android). This app pairs the operator’s phone or device to the machine to enable remote analysis by a certified Case technician, which allows them to diagnose the health of each connected machine through various parameter readings and fault codes. The technician decides as to whether the issue can be addressed remotely — such as clearing codes or updating software — or if it requires a trip to the machine.
“Reducing trips to the field, showing up with the needed parts on the first visit, and the ability to avoid field visits all together by remotely clearing basic codes all drive major savings in time and resources, both for the equipment owner and the dealer service department,” said Jacobsmeyer. “This type of collaborative fleet management has the ability to drive major gains for fleets of all sizes and ensure optimal uptime.”
And in the case of a service need, the Case Minotaur DL550 is built for ease of service with groundline access to grouped service points and checks like every machine in the Case lineup. Service intervals and machine operating information are easily accessed in the machine’s eight-inch LCD display in the cab.
Proudly Manufactured in Wichita, Kan.
The Case Minotaur DL550 compact dozer loader is manufactured in Wichita, Kan., on a dedicated line purpose-built for this one-of-a-kind, industry-first machine. It represents more than six years of development and collaboration between numerous Case plants, personnel, testing facilities and departments.
“The Case Minotaur DL550 embodies our dedication to practical innovation — real world, customer-driven solutions,” said Jacobsmeyer. “Through this, we created a whole new equipment category and we’re delivering the integrated technologies that drive improvements for operators in the field and for business owners at their bottom line.”
New Rockstar Machine Tours North America
In its 180th year in business, Case has proven to be a company on the move — and the development of the Case Minotaur DL550 compact dozer loader is proof of that in both iron and technology. To celebrate the launch of this first-of-its-kind machine, Case is launching a tour of the United States and Canada with more than 30 stops where the machine will be showcased at Case dealer locations.
“We are bringing the excitement of this industry-changing launch to every corner of North America,” said Terry Dolan, vice president — North America, Case Construction Equipment.
“We have more than 180 years of experience in the field, but we’re making moves like a startup, dedicating more time and resources to the field, and spending more time where it counts — with the men and women who run businesses and operate this equipment every day. We can’t wait to see you on tour.”
For more information, visit CaseCE.com/Minotaur.
Common Research Interests Lead to Collaboration On Zip-Form System
RESEARCH from page 10
“We can apply these principles to materials that already have a flatness to them and manufacture pieces that are more efficient in strength and yet use fewer resources,” he explained.
The opportunity to prove it came when Baker ran into Ismail at a conference, found they had common research interests, and invited him to speak to her class. While Ismail was talking to her class about beam optimization, a lightbulb went off over her head: Maybe the Zip-Form system could be used to help Ismail create a beam of complex curvature?
What followed were months of collaboration. Inherent in their discussion was that fabrication methods were inextricable from the design.
As Ismail explained, “We’re trying to develop methods that are fabrication-aware. When we’re actually designing and optimizing the structure, we know how it’s going to be built, and the rules of how it’s going to be built go back into the design process so it’s more circular and not as linear. So, we had months of conversations with Emily and Edmund about the actual mathematical principles behind their ZipForm system. What were the limits? What were the con-
straints? And then we found a way to put that into our structural model.”
Finally, Ismail was ready to see his unorthodox beam design become a reality. Harriss’ computations and Baker’s jig-system were essential to shaping the formwork, which was created at the Fay Jones School’s Build Lab in Fayetteville, where Baker oversees the digital steel lab.
Her method allowed them to make steel formwork with complex curvature like Ismail wanted almost as easily as she could make formwork for a flat beam.
“This is a vast improvement on other methods that might be used to make curving formwork,” she said in describing the process. Common Materials Make Up BeamÊs Concrete
Cameron Murray, an assistant professor of civil engineering at UA who advises Poblete, assisted with the pouring of concrete into the formwork the week prior to the test.
While he said there was nothing unusual about the concrete used, he noted “all of the materials were made in Arkansas. The coarse aggregate was quarried in Hindsville, the sand was from the Arkansas River in Van Buren, the cement was made in Foreman, [and] the water was from Beaver Lake. Concrete is inherently a local material.”
The conventionality of the materials underscored Ismail’s larger goal: he is interested in more efficient and sustainable design, but not necessarily revolutionary new materials. While he is excited about the potential for things like 3-D printed housing, that is decades away, and people need homes now, he said.
“Our group is interested in what is applicable today, like what can we go out and build right now. And that’s why we’re looking at regular strength concrete, regular strength steel, and fabrication methods that are relatively cheap and affordable, which is why this Arkansas project was so exciting. Emily and Edmund had been working on a method that can be replicated anywhere in the world quite easily.”
Beam Successfully ÂFailedÊ Test as Hoped
The actual beam test proved uneventful in the way success often does.
It was designed to carry 8,500 lbs., and beyond that, the goal was to fail safely, in what Ismail describes as a “slow, ductile manner. You don’t want it to collapse suddenly and in a scary way.”
His beam performed the way he hoped, as it exhibited small cracks and minor bowing, or what Poblete described as “flexural cracking and deflection.” The test proceeded through a series of steady weight increases followed by temporary plateaus, the spidering cracks documented by graduate students wielding black markers crawling under and around the beam.
Finally, the load was increased to 12,000 lbs., a weight far above its design strength, at which point an obvious failure occurred when a large chunk finally broke off, according to an article on the university website.
When the test was concluded, Ismail was relieved that his beam had done what it was designed to do, and with a lot less concrete than usual.
Ismal also believes the stress test’s results revealed the tip of the iceberg.
“There’s so much more we can do,” he explained. “There are more complex structures we can design, and then there’s more testing that we can do that gets into much more rigorous things like dynamic loading, testing for vibrations, and all sorts of things that the Arkansas structures’ lab is definitely capable of. So, this was, in a lot of ways, proof that this idea can work, and now we need to actually develop it further.”

Photo courtesy of the University of Arkansas website Graduate students examine the concrete beam for hairline fractures after stress was applied.
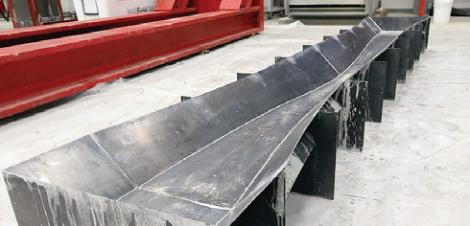
Photo courtesy of the University of Arkansas website A form designed through the Zip-Form system allowed a concrete beam to be poured using less concrete but maintaining strength.
ARNOLD MACHINERY CO.
www.arnoldmachinery.com
Salt Lake City, UT
801-972-4000 Idaho Falls, ID
208-523-0822 Meridian, ID
208-887-6000 Twin Falls, ID
208-733-1715 Sparks, NV
775-356-1511 Las Vegas, NV
702-642-9000 Phoenix, AZ
602-414-1900 Tucson, AZ
520-294-7677
ASCO EQUIPMENT
www.ascoeq.com
Abilene, TX
325-698-2726 Perryton, TX
806-435-7773
Amarillo, TX
806-372-8386 Lubbock, TX
806-745-2000 Clovis, NM
575-742-2726
ROMCO EQUIPMENT CO.
www.romco.com
Austin Round Rock, TX
512-388-2529 877-851-1026 Buffalo Buffalo, TX
903-322-5602 Carmine Carmine, TX
979-278-3570 Corpus Christi Corpus Christi, TX
361-881-4891 Dallas Carrollton, TX
214-819-4100 800-227-6626
Ft. Worth Ft. Worth, TX
817-626-2288 866-966-4602 Houston Houston, TX
713-937-3005 800-865-6998 Longview Longview, TX
903-758-5576 Rio Grande Valley Mercedes, TX
956-565-0100 San Antonio San Antonio, TX
210-648-4600 800-966-4601
SIERRA MACHINERY, INC.
www.sierraelpaso.com El Paso, TX
915-772-0613 Artesia, NM
575-746-6592
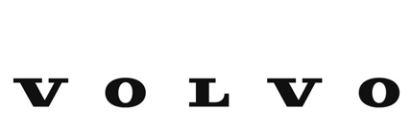
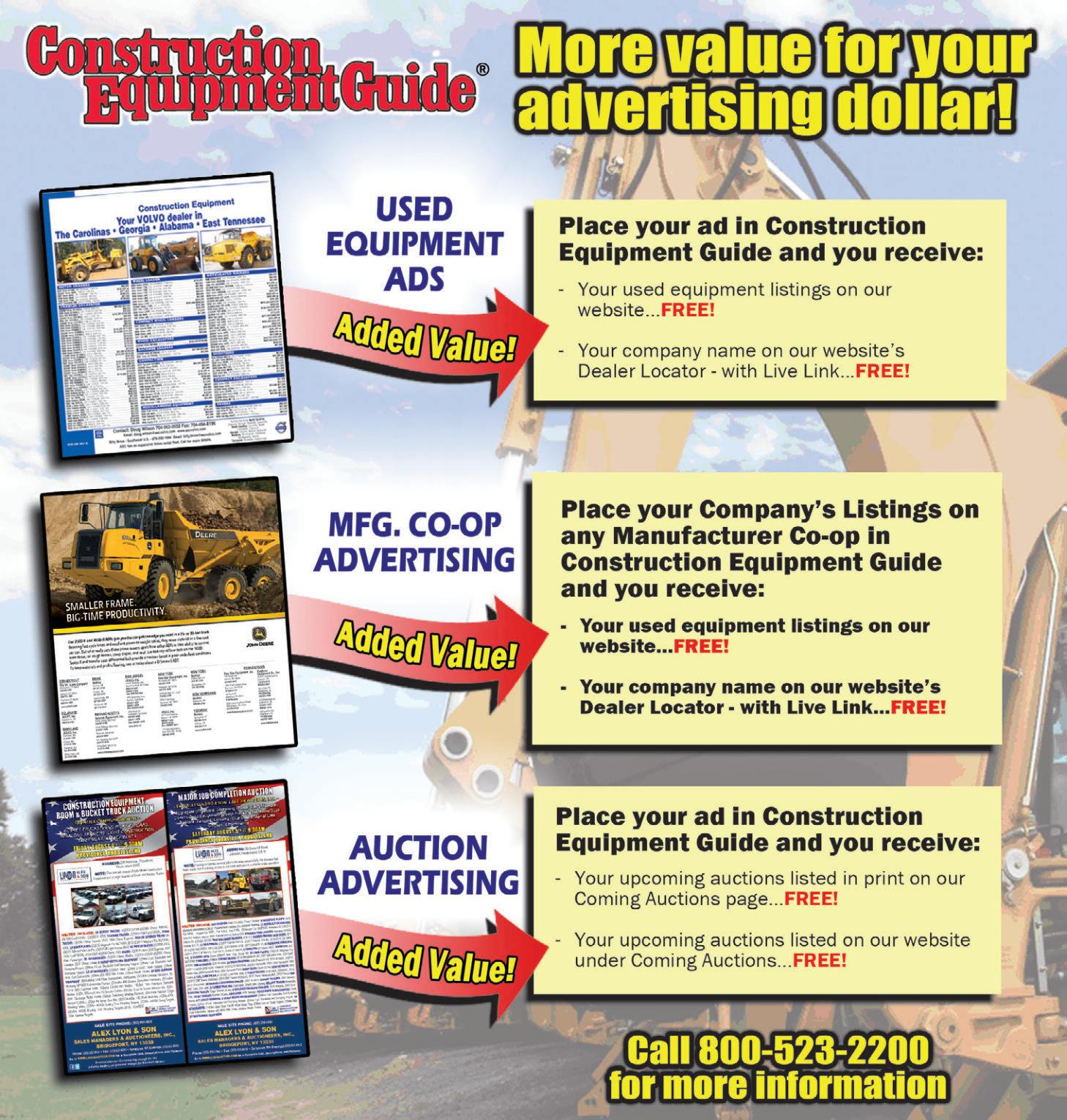
Kirby-Smith Machinery Hires Bo Ross as General Manager of Used Equipment
Kirby-Smith Machinery Inc. (KSM) has hired Bo Ross as its new general manager of used equipment.
Ross brings more than 34 years of heavy equipment industry experience to the position, which includes extensive time in used equipment management positions for other Komatsu distributors, as well as running his own used equipment company.
As general manager, Ross will be responsible for managing KSM’s complete used equipment business, which includes its Komatsu Remarketing program, domestic and international sales, and used equipment operations at the heavy machinery distributor’s 12 locations across Oklahoma, Texas, Kansas and Missouri.
Jeff Weller, chief operating officer of KSM, believes that Ross’ track record for establishing successful policies and procedures that streamline used equipment operations will be important as the company continues to grow. Weller said that KSM went through a long and careful search for its successor to the late David Mehrtens, looking for someone they felt could continue the legacy that Mehrtens started.
“Bo is an experienced leader and a good teammate,” said Weller. “I think and hope that David would approve of the decision we have made in Bo. I am grateful to have him join our organization and excited to see how Bo will put his own fingerprints on the future of Kirby-Smith Machinery.”
Coming from the Komatsu distributor world, Ross has been familiar with KSM for several years. He also had a friendship with David Mehrtens that spanned multiple decades.
“It’s extremely exciting to be a part of the Kirby-Smith family,” said Ross. “Dave built something special here and put a great team in place that has had continued success. I embrace the challenge of building on that foundation, doing everything I can to drive improvements, support our team and lead us forward.”
For more information, call 888/861-0219 or visit kirby-smith.com.

Bo Ross
OKLAHOMA TERRITORY CONSTRUCTION EQUIPMENT
www.oklahomaterritoryequipment.com Oklahoma City, OK 405-917-9191 Tulsa, OK 918-835-7200
Garton Tractor Inc.
www.gartontractor.com 2400 N Golden State Blvd. • Turlock, CA 95382 209-632-3931 Fairfield, CA • 707-425-9545 Merced, CA • 209-726-4600 Modesto, CA 95356 • 209-538-0911 Newman, CA • 209-862-3760 Santa Rosa, CA • 707-586-1790 Stockton, CA 95206 • 209-948-5401 Tulare, CA 93274 • 559-686-0054 Ukiah, CA 95482 • 707-468-5880
CLM EQUIPMENT CO. INC.
www.clmequipment.com Lafayette, LA 337-837-6693 Lake Charles, LA 337-625-5942 Houston, TX 281-598-2500
Kirby-Smith Machinery Names Sam Schneider as GM, Industrial Equip.
Kirby-Smith Machinery Inc. (KSM) has hired Sam Schneider as its new general manager of industrial equipment.
Schneider comes to KSM after having served as regional product manager of Takeuchi Manufacturing since 2014. He has a strong background in equipment dealership development with nearly 20 years of experience related to sales, parts and service support, and is widely regarded in the industry as a “go to” resource for machine knowledge, product training and best-in-class sales practices, according to the company.
Jeff Weller, chief operating officer of KSM, is grateful to add Schneider’s expertise to the leadership of the heavy equipment distributor’s industrial product lines, which include, but are not limited to, known industry manufacturers such as: Takeuchi, Terramac, Gradall, JLG, Multiquip, NPK, Fecon, Sullair, SkyTrak, Thompson, Trail King, Stanley and all related attachments.
“As the saying goes, ‘good things come to those who wait,’ and having long considered Sam to be a turn-key organizational fit for this position, we are grateful to have him officially onboard,” said Weller. “Sam served as a tremendous resource to our team and customers over our past six years with Takeuchi and brings both excellent product knowledge and a wealth of industry relationships with him to KSM.
“He is a terrific addition to our culture and possesses the drive for excellence needed to lead in this important position for our company.”
Schneider, who will be based out of KSM’s Kansas City branch, has worked closely with KSM’s sales team for years and is both humbled and honored to now make KSM his “port of call.”
“I’m grateful for the opportunity to be a part of this amazing company,” said Schneider. “I look forward doing my part to strengthen the legacy that has been built here.”
For more information, call 888/8610219 or visit kirby-smith.com.

BANE MACHINERY INC.
www.banemachinery.com Dallas, TX 800-594-2263 Ft. Worth, TX 800-601-2263 Tyler, TX 800-594-2200
COLUMBIA WESTERN MACHINERY
Columbiawesternmachinery.com 11125 SW Tonquin Road Sherwood, OR 97140 503-454-0902
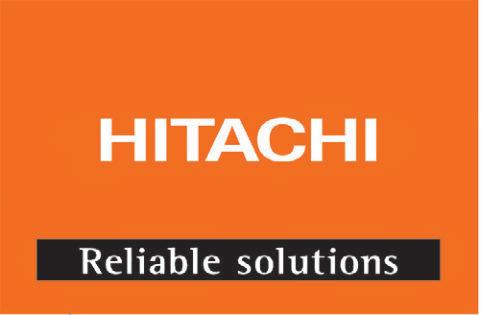