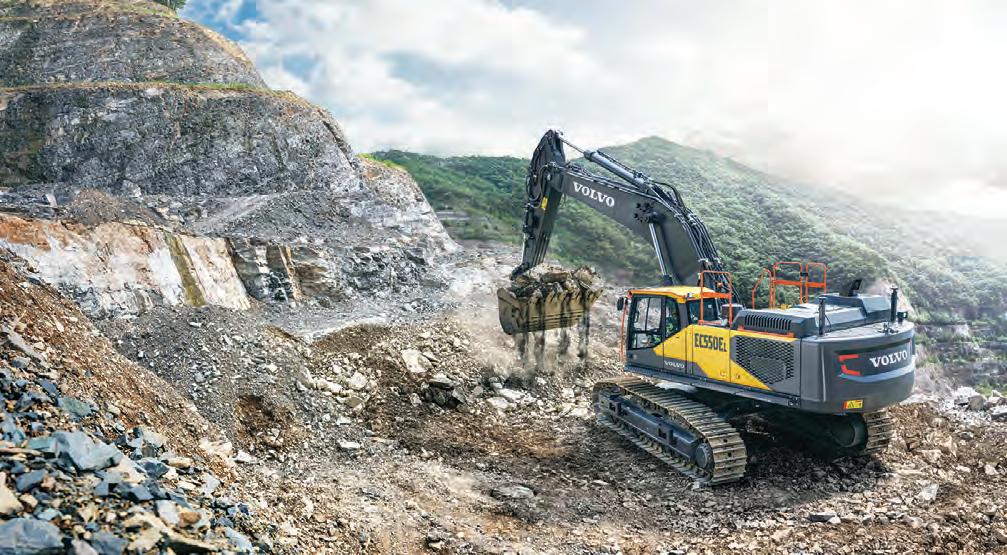
13 minute read
VOLVO INTRODUCES TWO NEW EXCAVATORS IN 50-TON CLASS SIZE
Volvo Construction Introduces Two New Excavators in 50-Ton Class Size
Volvo Construction Equipment is entering the 50-ton class for excavators with two models — the EC530E and EC550E — that have digging and lifting forces normally found in 60ton machines, giving contractors the performance they need to excel in heavy-duty digging, mass excavation and largescale site preparation.
“When Volvo CE enters a new size class, we want to meet the needs of our customers while also making an impression,” said Sejong Ko, product manager, excavators, at Volvo CE. “We’ve done that with the EC530E and EC550E excavators. Contractors get the power of a larger machine at a lower weight, along with additional fuel-saving and uptime-enhancing features.”
The EC530E and EC550E feature the highest engine power in the class, providing high tractive force and swing torque. When coupled with large buckets, the EC530E and EC550E are perfectly suited to fill articulated haulers in the 30- to 40-ton class, requiring fewer passes to load them and reducing cycle times. This combination can boost productivity by up to 20 percent, according to the manufacturer.
Also characteristic of bigger equipment is the super-rigid reinforced undercarriage, providing durability and strength. This is supported by equally sturdy lower and upper frames.
The EC550E undercarriage has a long and wide lower frame, giving it extra stability when working with heavier loads. The undercarriage on the EC530E, meanwhile, shares the same transportation dimensions — and loading convenience — as Volvo’s 48-ton EC480E. Both machines’ boom and arm boast a larger pin size for added strength. Also, like all Volvo excavators, both models are backed by the Volvo Lifetime Frame and Structure Warranty, which covers the frame, boom and arm for the entirety of the initial ownership period.
Fuel Efficiency With IMVT
The electro hydraulics system contributes to a 25 percent improvement in fuel efficiency due to Independent Metering Valve Technology (IMVT) that, due to intelligent electronic control, offers more precise operation and efficiency than a traditional mechanically coupled hydraulic system. Engine pump optimization lowers engine speed while maintaining power.
The EC530E and EC550E offer high levels of control and efficiency for all applications, including creep mode for precise lift-and-carry work and optional Comfort Drive Control (CDC). CDC helps reduce operator fatigue by allowing the excavator to be steered with joystick rollers instead of pedals.
Operators also can select functions like boom/swing and boom/travel priority, which enables one function to take the lead over another. The boom-down speed also can be adjusted, giving optimum control for tasks that require extra precision. New boom-and-arm bounce reduction technology lessens machine shock.
Productivity, Uptime Features
Operators are further assisted by the optional Dig Assist machine control system, powered by Volvo Co-Pilot and designed to deliver excavation accuracy in a fraction of the time of conventional methods.
To increase uptime, hydraulic pilot lines have been removed, reducing the number of couplings needed. Maintenance time and costs are further reduced by the recent extension of Volvo engine oil change intervals to 1,000 hours when using Volvo VDS 4.5 oil.
The EC530E and EC550E are eligible for ActiveCare Direct, Volvo’s advanced telematics service.
For more information, visit volvoce.com/na.
NCCCO Announces First Veterans in VICTOR Program
The first recipients of the VICTOR program were announced recently by the NCCCO Foundation and Heavy Equipment Colleges of America (HEC).
The Veteran In Crane Training Outstanding Recognition (or V.I.C.T.O.R.) award is presented to the top-performing veteran in each HEC training class for NCCCO mobile crane operator certification. HEC runs training classes for veterans both at Fort Irwin Army Base in California and at Joint Base Lewis-McChord location in Washington State.
The four awardees who graduated top of their class are: David Carter and Gabriel Hope (Fort Irwin) and John Bleignier and William Hare (Joint Base LewisMcChord). Each receives a $100 gift card, a YETI tumbler and a Certificate of Achievement plaque.
While receipt of the VICTOR award surprised most awardees, all felt gratified to be so recognized.
“Receiving this award encouraged me to pursue my education and further my career in this industry,” said Carter, while Hope set a goal of getting a crane operating job “so that I can make a career out of it and become a proficient outstanding operator.”
All testified to the quality of instruction they received at HEC and stated their appreciation for the focus on safety and the attention to detail provided by the instructors.
“A central component of the NCCCO Foundation’s mission is to facilitate access by veterans to the construction industry,” said NCCCO Foundation CEO Graham Brent, “particularly in the crane and rigging sector. The V.I.C.T.O.R. program is a small but significant step in that direction.”
“HEC is proud to help veterans and civilians to find rewarding careers in the construction industry,” said HECA CEO Bob Albano, “and the V.I.C.T.O.R. program serves to reward excellence among our veteran students.”
About the V.I.C.T.O.R. Award
The VICTOR Award Program was unveiled at the NCCCO Foundation’s sixth annual industry forum on Veterans Day, Nov. 11, 2021. Eligible participants must be a veteran and have completed the HEC Mobile Crane Training Program. Awards are issued in accordance with the program completion timeline.
About HEC
The Heavy Equipment Colleges of America (HEC) is a private educational and training school specializing in entry level training on mobile earthmoving and lifting equipment at four locations around the country. Programs are designed to teach students the basic fundamentals of equipment operation and to gain experience of immediate value to employers.
For more information, visit www.ncccofoundation.org and www.heavyequipmentcollege.com.
ALASKA
NC MACHINERY www.ncmachinery.com 800-478-7000 Anchorage, AK • 907-786-7500 Dutch Harbor, AK • 07-581-1367 Fairbanks, AK • 907-452-7251 Juneau, AK • 907-789-0181 Prudhoe Bay, AK • 907-659-6900 Wasilla, AK • 907-352-3400
CALIFORNIA
HOLT OF CALIFORNIA
www.holtca.com Pleasant Grove • 916-921-8969
NEW MEXICO
WAGNER EQUIPMENT CO. www.wagnerequipment.com Flora Vista • 505-334-5522 (Rental) La Cruces • 575-647-9700 Albuquerque • 505-345-8411 505-938-2000 (Rental) Hobbs • 575-393-3665 575-393-2148 (Rental) Clovis • 505-235-3294 (Rental) Farmington • 505-327-5331
NORTH DAKOTA
TRACTOR AND EQUIPMENT www.tractorandequipment.com Williston • 701-572-8377
COLORADO
WAGNER EQUIPMENT CO. www.wagnerequipment.com Aurora • 303-739-3000 Denver • 303-433-2727 (Rental) Carbondale • 970-963-7368 (Rental) Commerce City 303-286-2300 (Rental) Colorado Springs • 719-635-1669 719-390-7316 (Rental) Granby • 970-328-2080 (Rental) Gypsum • 970-328-2080 (Rental) Hayden • 970-276-3781 Silverthorne • 970-262-3788 (Rental) Fort Collins • 970-493-5005 (Rental) Grand Junction • 970-242-2834 970-245-6546 (Rental) Pueblo • 719-544-4433 719-544-0088 (Rental) Steamboat Springs 970-871-1990 (Rental) Windsor • 970-278-1750 (Rental) Burlington • (719) 346-5132 719-346-7880 (Rental) Durango • 970-259-2001 970-259-2001 (Rental) Windsor • 970-278-1750
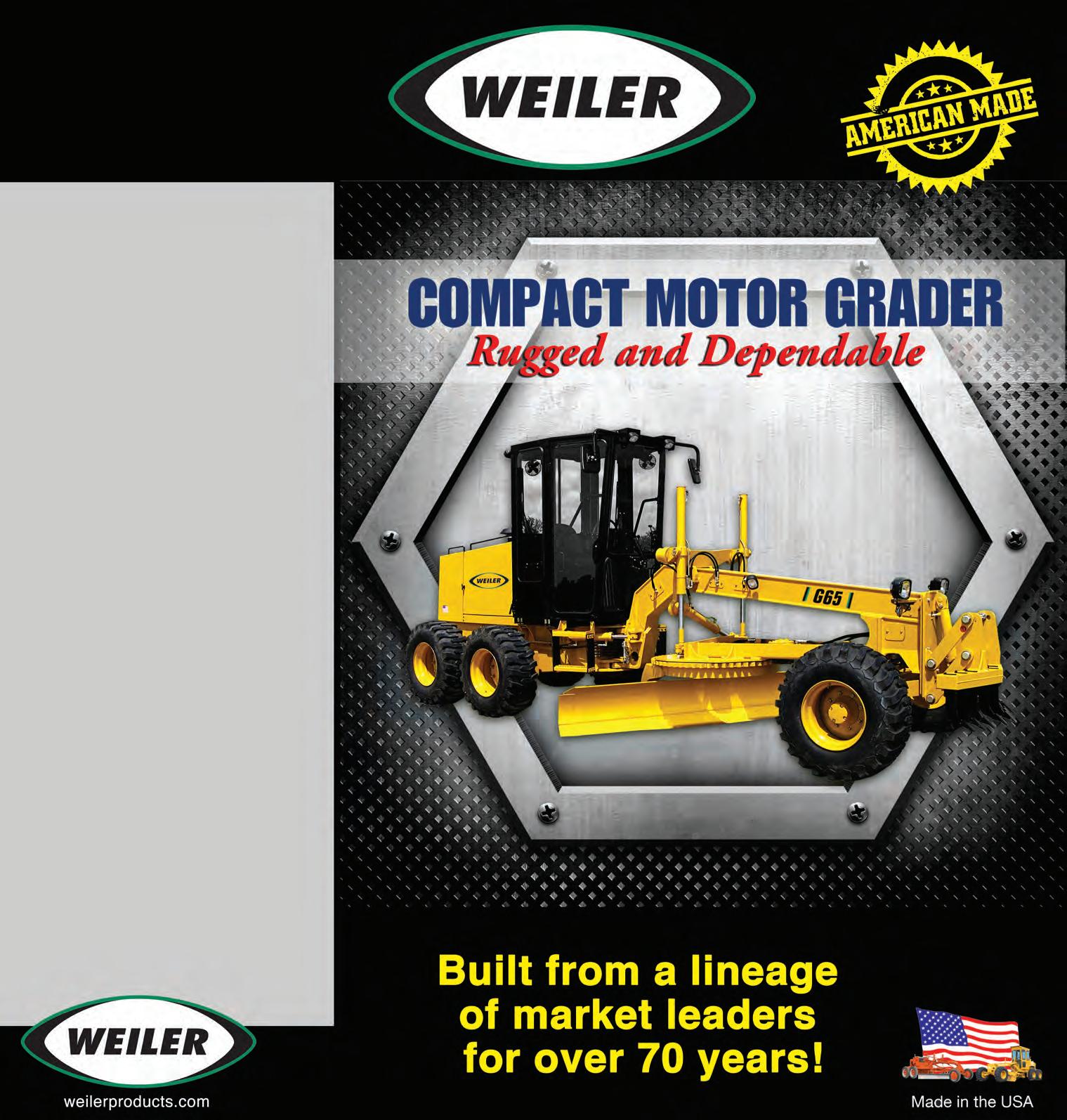
NEVADA
CASHMAN EQUIPMENT
www.cashmanequipment.com 3300 St. Rose Parkway, Henderson, NV 89052 • 702-649-8777 Elko • 775-738-9871 Reno/Sparks • 775-358-5111
WYOMING
TRACTOR AND EQUIPMENT www.tractorandequipment.com Worland • 307-347-4747
MONTANA
TRACTOR AND EQUIPMENT www.tractorandequipment.com Billings, MT • 406-656-0202 Billings-Sgt. • 406-245-4426 Bozeman • 406-585-5800 Great Falls • 406-761-7900 Helena • 406-442-2990
TEXAS
WAGNER EQUIPMENT CO. www.wagnerequipment.com El Paso 915-493-5005 (Rental) 915-821-7651
WASHINGTON
NC MACHINERY www.ncmachinery.com 800-562-4735 Seattle • 425-251-5800 Chehalis • 360-748-8845 Fife • 253-896-0878 Monroe • 360-805-6000 Mt. Vernon • 360-424-4292 Wenatchee • 509-886-5561 Yakima • 509-248-2371
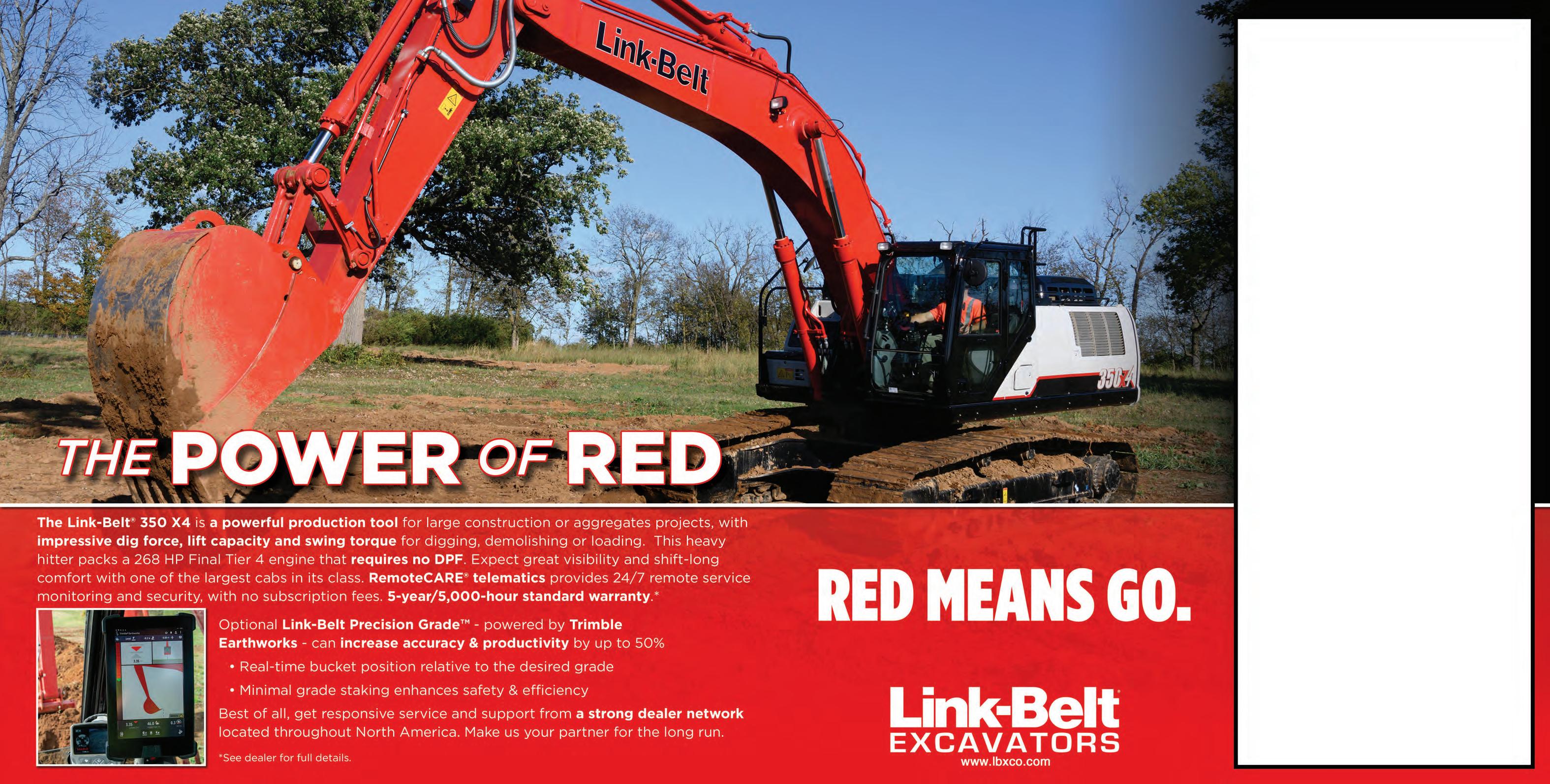
Larger control valve and electronic controls deliver smooth, precise performance and up to 12% faster cycle times
Shift-long comfort from a spacious cab, automotive-grade seat and ergonomically-designed, fullyadjustable arm rests
Award-winning Wide Angle Visual Enhancement System (WAVES) provides seamless 270° panoramic view
Ground-level access to routine service points cuts daily maintenance down to just minutes
Tier 4 Final engines deliver up to 12% improved fuel economy…and no DPF to maintain
Robust undercarriage with innovative side-frame design is easier to clean
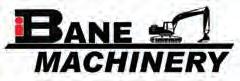
Bane Machinery
2449 Manana Drive Dallas, TX 75220
800-594-BANE (2263)
10505 North Freeway Fort Worth, TX 76177
800-601-BANE (2263)
3402 E. NE Loop 323 Tyler, TX 75708
800-594-2200
www.banemachinery.com
Oklahoma Territory Construction Equipment
3839 West Reno Ave. Oklahoma City, OK 73107
405-917-9191 866-339-6827
2520 E King Street Tulsa, OK 74110 918-835-7200 866-334-6827
www.oklahomaterritoryequipment.com
Nueces Power Equipment
7667 N Sam Houston Parkway Humble, TX 77396
713-247-0066
www.nuecespower.com
Cisco Equipment
1706 S. 1st Street Artesia, NM 88210
800-748-1846
2707 Slaton Hwy. Lubbock, TX 79404
877-745-9595
520 SE Loop 338 Odessa, TX
800-657-3673
620 N. Bell Street San Angelo, TX 76903
800-496-0271
www.cisco-equipment.com
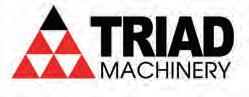
Triad Machinery
1601 E. Bay Street Tacoma, WA 98421
253-722-5600
910 N. Thierman Road Spokane Valley, WA 99202
509-534-1900
1210 Dale Lane Mt. Vernon, WA 98274
360-488-3948
4440 SW Airport Road Prineville, OR 97754
888-662-2940
91251 Coburg Industrial Way Coburg, OR 97408
541-342-7700
18200 NE Riverside Parkway Portland, OR 97230
800-221-8512
www.triadmachinery.com
ASPHALT from page 1 Splash-Free Driving
Permeable pavement, including porous types, is one of the fastest growing technologies in sustainable asphalt roadway engineering.
Developed chiefly for safety advantages, porous pavement reduces splash and spray. Darlene Goehl of the Texas Transportation Institute’s materials and pavements division believes the design also improves improve visibility for drivers.
Impervious surfaces are often the causes of stormwater runoff, according to paving information provider PavingFinder.
The material is placed over a granular working platform on top of a lare stone reservoir, and the surface is made porous by building with open-graded friction coarse aggregate.
“The layer under the porous asphalt has the storage capacity to hold the collected water,” explained PavingFinder.
Highway engineers pour the material in a thin surface layer on conventional pavement. Rainwater sinks into the pavement surface and settles on an impermeable asphalt layer below.
Visibility for drivers improves to the degree that crashes and fatalities can be “significantly” reduced, believes PavingFinder.
Recent developments in stormwater ordinances across the country have begun to require more significant onsite stormwater infiltration and detention.
And, according to the paving information organization, a primary incentive for using permeable pavement is to add a hydrological benefit to a roadway or site design.
Perpetual Pavements
Perpetual asphalt concrete pavement is designed to last 50 years or longer without any repairs below the wearing course or surface level.
The pavement typically has a multi-layered structure which resists fatigue over time, according to the Asphalt Pavement Alliance.
Ralph Isenberg, director of governmental affairs for Reliable Paving, outlined in a blog post an APA research paper on the technology.
The triple-layered structure resists structural damage for as long as the top surface is maintained and replaced.
The goal of perpetual pavement is to be a deep-strength asphalt paving that resists fatigue. It does so by reducing cracking from the bottom-up, said APA.
As they infiltrate the pavement layers, cracks spread out and multiply. Over time the cracks present on the surface of the asphalt pavement.
“Perpetual pavement is designed specifically to resist bottom-up fatigue cracking and structural rutting,” said APA.
These two types of damage are among the worst asphalt pavement can receive. Superior to low-grade pavement exhibits rutting and cracking before their design-life is achieved.
Whereas superior to high-grade traditional pavement proves it uses materials more efficiently.
The pavement also reduces cyclical costs. “As long-term damage is avoided, yearly or multi-yearly-accrued damage doesn’t need to be repaired,” reported APA.
Because the design is more efficient, sections of overly thick asphalt are eliminated. Reconstruction costs are eliminated, as well.
Plus, delays due to maintenance occur less and as a result, maintenance costs drop. Perpetual pavement also reduces the need for non-renewable asphalts and aggregates.
Driverless Vehicles
Goehl of the Texas Transportation Institute said autonomous vehicles will change the way asphalt pavements are constructed. Today’s 12-ft. wide driving lanes will look different in the future.
“If you look at that path where people normally drive, it tends to be on each tire about three foot wide. So, there’s some wander when you drive just naturally within the lane, that kind of distributes the weight of that car over half the lane. So about six-foot total,” she said.
But designers are anticipating changes in road pavement spread to accommodate autonomous vehicle technology, said Goehl.
The result will be a more concentrated load on the pavement within that area, which said will change a bit in how pavement is designed in order to hold that load.
The pavement “will have to be stiffer. We’re still researching how those effects can cause those problems with those vehicles.”
Autonomous vehicles also are at the heart of research into keeping road workers safe.
Last year, the North Dakota Department of Transportation launched an autonomous protection truck for road construction crews in work zones.
Kevin Longley of the American Society of Civil Engineers (ASCE) reported that the state utilized a grant from the Federal Highway Administration to improve work zone safety with an “autonomous impact protection vehicle.”
Impact protection vehicles, driven by humans, protect construction crews from other drivers on the road who are not paying attention to the construction site or have lost control of their vehicle.
A crew member will remotely control the autonomous vehicle, but no humans will be inside during shifts.
The state DOT believes the autonomous vehicle, dubbed the Autonomous Truck Mounted Attenuator (ATMA), will improve safety in work zones by removing the driver from the impact protection vehicle during normal operation.
“The NDDOT remains committed to its Vision Zero initiative and our goal is to eliminate fatalities and serious injuries caused by motor vehicle crashes,” said Panos.
According to ATMA developer Kratos Defense, highway workers are at especially high risk when assigned to drive an impact protection vehicle.
The truck follows behind slow-moving highway maintenance vehicles as a humandriven mobile crash barrier, absorbing the impact of traffic accidentally entering the work zone.
“Driving a TMA is extremely dangerous and drivers are at serious risk of lifelong injury, painful rehabilitation and even death,” said Maynard Factor, business development director of Kratos. “To eliminate this dangerous assignment, Kratos Defense developed the Autonomous TMA [ATMA] by retrofitting standard TMA vehicles with driverless technology to enable unmanned operation.”
The first ATMA systems were deployed in 2017 and have since then been deployed across the United States and Europe.
The unmanned vehicle operates in a multi-vehicle leader/follower configuration with a human driven highway maintenance vehicle, the company said.
In the leader/follower configuration, the system enables the maintenance vehicle, or leader, to transmit navigation data via encrypted V2V communications to the ATMA as the follower.
From there, the ATMA uses the data to follow the leader, unmanned, as it travels along the route. CEG
