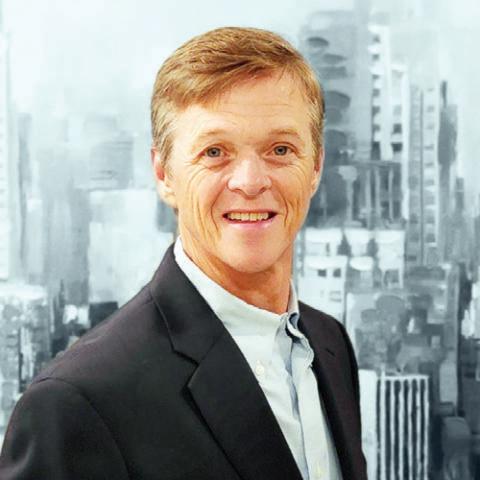
9 minute read
RICHARD KIRKMAN JOINS SUPERIOR AS DIVISION MANAGER
103 BRYAN STREET JACKSONVILLE, FL 32202 PH 904-354-5746 FAX: 904-355-1891
Doosan Portable Air Compressor Model XP825/HP75WCU-T4F Cummins Diesel Powered 825 CFM @ 125 PSI or 750 CFM @ 150 PSI 100 Gallon Fuel Tank for 9 Hour Runtime
600 N. COMMONWEALTH AVE. POLK CITY, FL 33868 PH 863-984-6262 FAX: 863-984-6363
New units in stock Jacksonville & Polk City Financing Available
WE SELL AND RENT EVERYTHING NEEDED FOR ANY ABRASIVE BLASTING JOB RENTALS, SALES, SERVICE, PARTS, COMPRESSORS, GENERATORS, LIGHT TOWERS, ABRASIVE BLASTING EQUIPMENT, DUST COLLECTORS, AIR DRYERS, DEHUMIDIFIERS, MANLIFTS
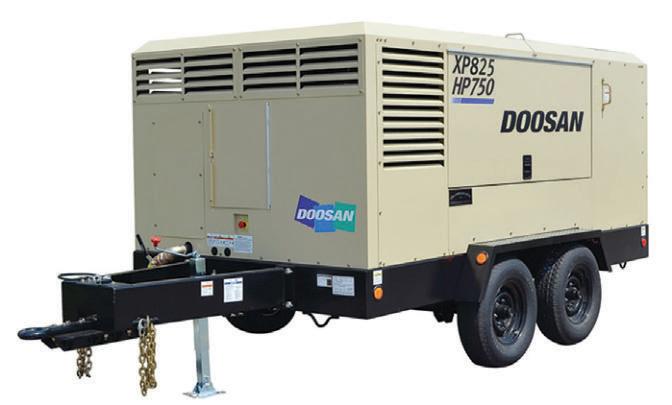
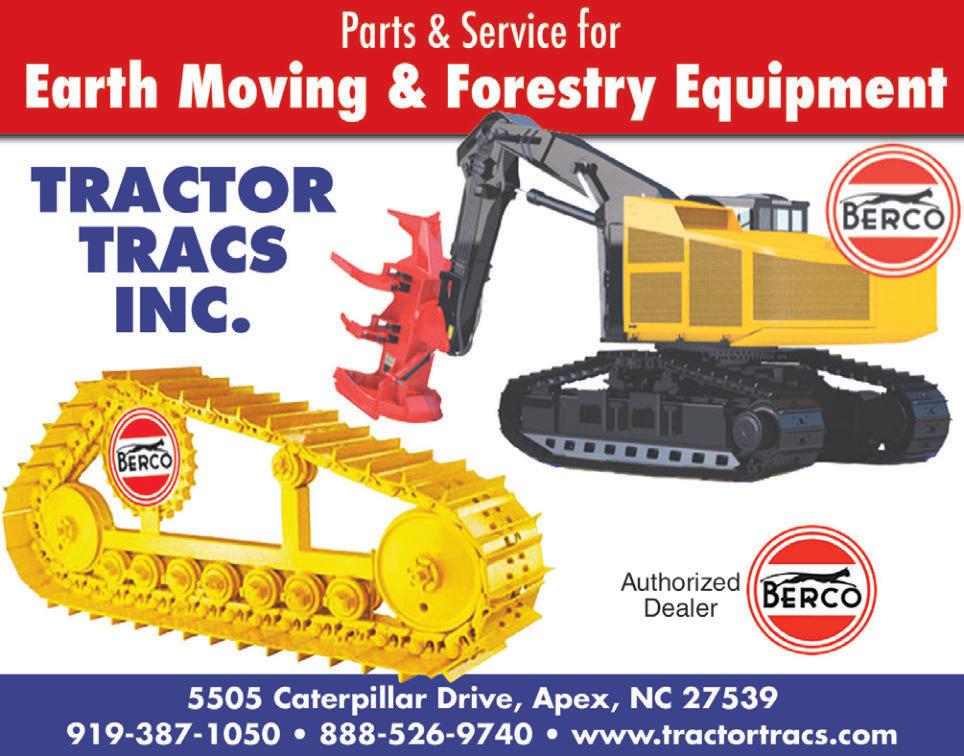
Richard Kirkman
Superior Construction, an American family-owned infrastructure contractor, named Richard Kirkman as its new division manager of the Carolina region.
In his new role, he will develop and pursue large-scale transportation projects across North and South Carolina, helping expand Superior’s robust regional portfolio of heavy-civil work.
“I’m excited for the challenge and opportunity to lead a sector that has experienced significant growth in recent years,” Kirkman said. “Superior is well-positioned to continue delivering high-quality projects and contributing to the success of the Carolinas region, and I’m proud to be a part of that work.”
Kirkman brings with him a wealth of industry knowledge and nearly three decades of experience. With a focus on design-build and value engineering, Kirkman has managed a multimillion-dollar workload of bridge replacement projects throughout his career. He most recently served as a division manager of Blythe Development Company in Charlotte, N.C., managing and pursuing complex heavy civil projects from conception to completion.
Kirkman also has led procurement, labor and cost management efforts for various companies, including Dane Construction and Kirkman Construction, the latter of which he owned and operated.
In addition to his technical expertise, Kirkman is skilled in customer service and talent development, making him a valuable asset to the Superior team, the company said.
“Richard is an exemplary leader, as he has forged important relationships within our industry and mentored numerous professionals who have built successful careers,” said Kevin McGlinchey, Southeast Business Unit president. “We trust him to develop great leaders in his division and maintain the family values Superior esteems while delivering excellent results for our clients.”
For more information, visit superiorconstruction.com.
AED from page 30
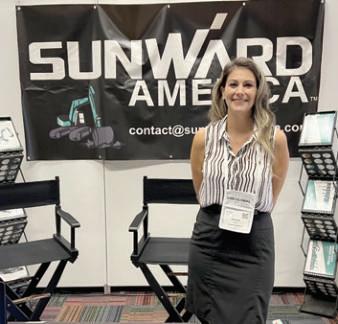
Sunward America Corp was represented at CONDEX by Nichole Stoltz, operations director of the manufacturer of excavators, telehandlers, skid steers and rotary drilling rigs. Midland Machinery Co. Inc.’s new ownership team was introduced at AED. (L-R) are Ben Whiting, partner; Aurelius Chaves, CEO and owner; and Michael Ulbrich, managing partner.
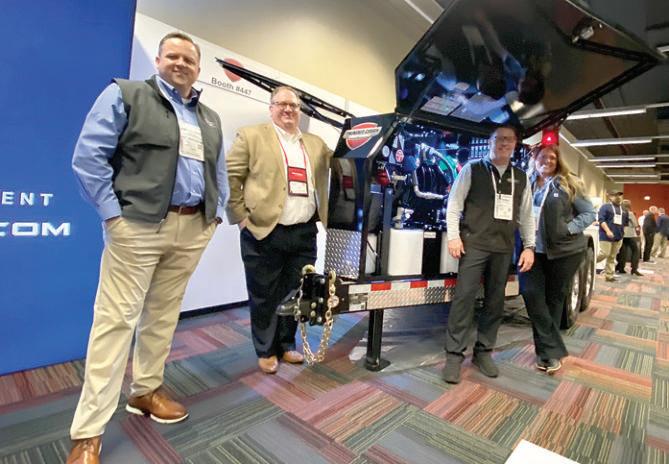
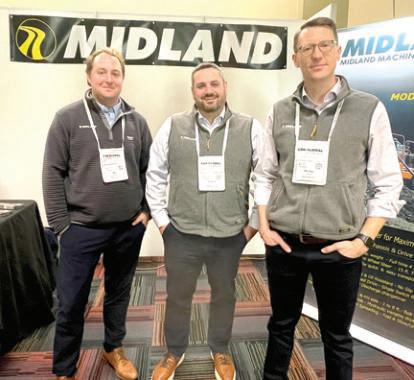
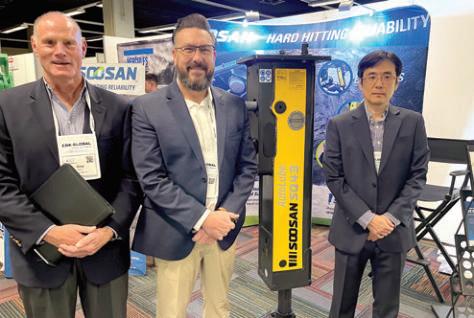
Soosan Heavy Industries displayed the AutoLube SQ43 hammer. (L-R) are Greg Henry, director of sales and marketing; Joe Grojean, central region sales manager; and Sung-Jong Kee, managing director. (L-R) are Thunder Creek’s Larry Lea, Fred Buser, Niki Patterson and Kyle Barton.
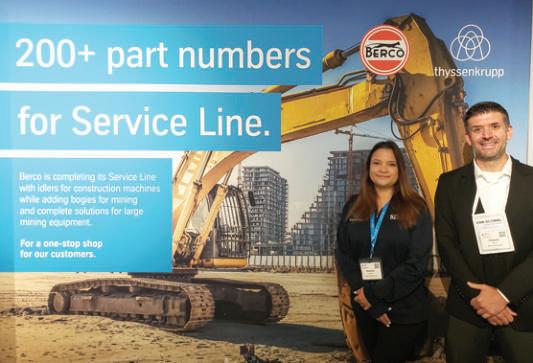
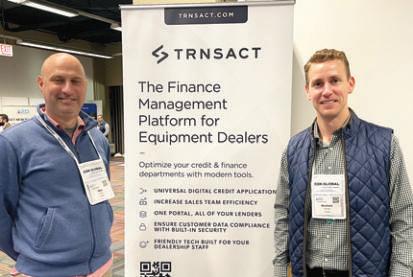
Ross Stites (L), program manager of TRNSACT, and Beckham Thomas, product manager of TRNSACT, were on hand to discuss how you can optimize your company’s credit and finance opportunities with the company’s latest technology.
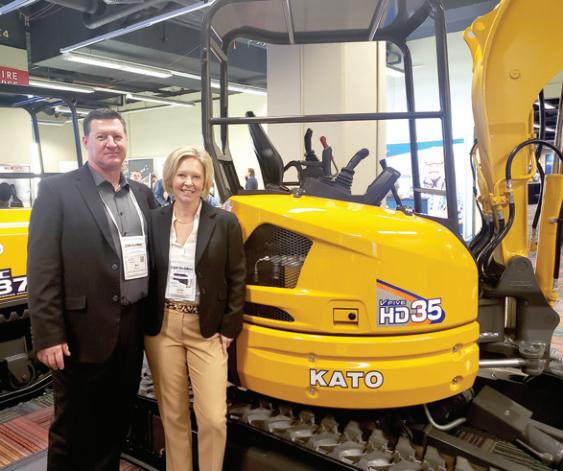
Shannon Johnson and Eduardo Ienne of Berco of America Inc. were at the AED Summit to explain how the company supplies components for tracked earthmoving machinery.

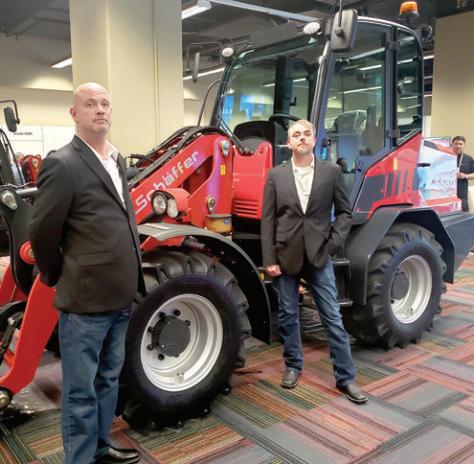


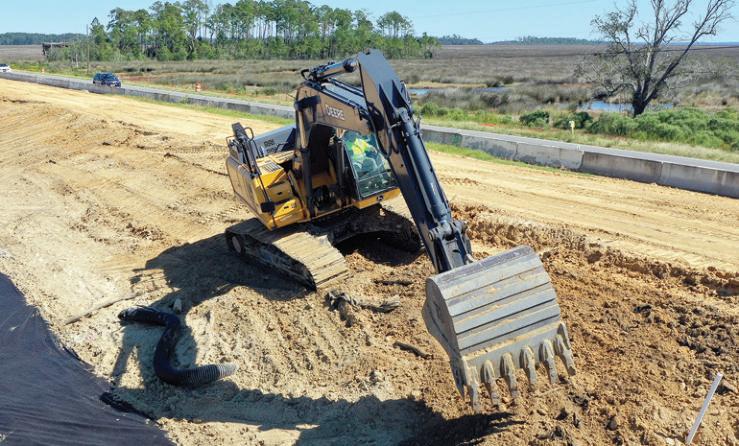
SCDOT photo The construction sequencing is intended to prevent impacting the wetland areas outside of the permitted limits.
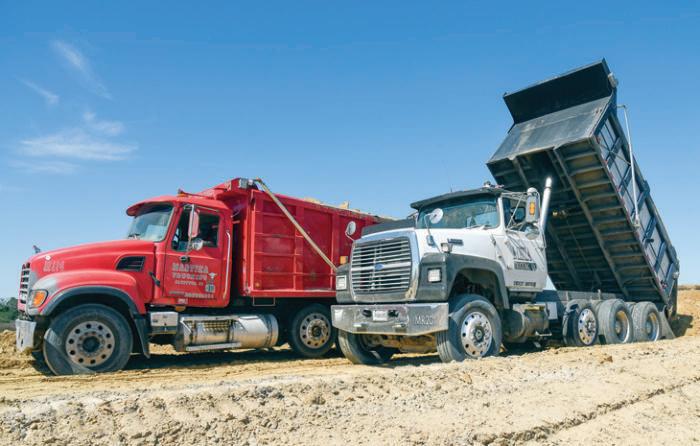
SCDOT photo GDOT also was planning projects in the area involving expansion work on two bridges on U.S. 17.
SCDOT from page 1 direction. Now, a $44.1 million, four-year widening project is under way to help alleviate the congestion. The project was awarded to Reeves Construction Co. and centers on a 5mi. stretch that intersects with SC-315 and will increase two lanes to four, add a divided median, bicycle lanes and other improvements.
“The improvements to the intersection with SC-315 were necessitated by two major factors,” Moore said. “One, increased traffic along this corridor due to regional growth [17,200 vehicles/day in 2020]. Two, increased local economic development and demand at the Savannah Port adds to the traffic and increases the truck volumes.”
The project has been 10 years in the making, hinging largely on coordination with the Georgia Department of Transportation (GDOT). The GDOT also was planning projects in the area involving expansion work on two bridges on U.S. 17.
The biggest challenge is building new roadway in an area that runs through marsh and wetland areas, Moore said.
The project design calls for several measures to be utilized to overcome the challenges, including a granular bridge lift; high strength geotextile fabric; geogrid reinforcement; prefabricated vertical drains; surcharge with settlement monitoring; and detailed construction sequencing with settlement timelines throughout the phases of construction. In addition, the construction sequencing is intended to prevent impacting the wetland areas outside of the permitted limits.
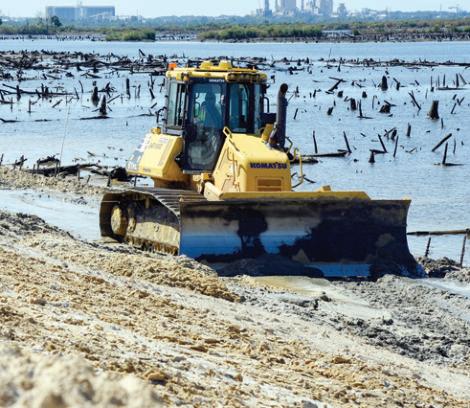
see SCDOT page 70
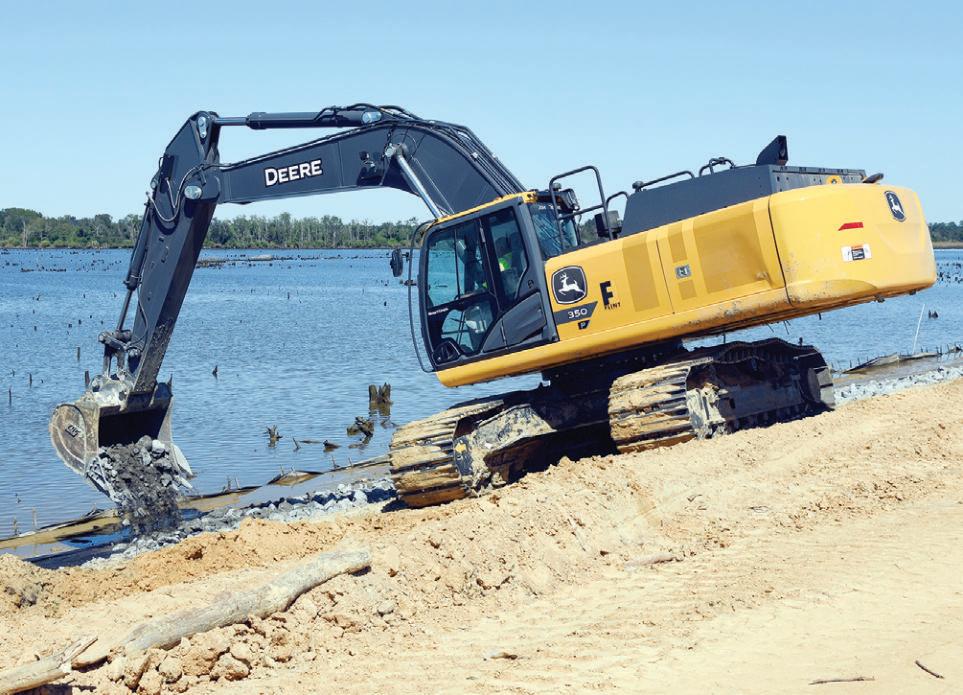
ROBOTICS from page 1
“In an industry often averse to risk, construction professionals will want to see proof of success before widespread adoption of robotics in the field,” wrote Andrew Roe, president of consulting firm AGR Associates.
As he sees it, robots are on construction sites everywhere, performing tasks humans would rather avoid.
Surveying and data collection were automated years ago, but robotic equipment is transforming construction sites all across the United States.
Automated Pile-Driving
Automated technology is being adopted in the movement of construction materials from one location on a job site to another.
Construction companies partnering with manufacturers and integrating technology are crucial to the transformation becoming reality.
Mortenson Construction, partnering with Italian manufacturer Orteco, is using equipment that automatically distributes piles across solar farms. The GPS pile-distribution system was recently used on a large solar project in West Texas.
In the process, Mortenson was able to redirect crews to other more critical tasks and expedite completion of the project’s initial phases.
Roe explained that the machine can free up to 80 percent of the craft workforce traditionally required to mark pile distribution points. The machine can then deliver piles to each location on the solar farm site, according to Mortenson. The pile-distribution system can precisely position piles awaiting the driving process.
The automation continues to the actual pile-driving process, which features GPS-enabled machines from Vermeer. The GPS technology monitors pile installation with half the workforce used traditionally.
Mostaert said that in combination, the autonomous and semi-automated pile driving machines help reduce cost and risk of injuries.
For the pile delivery and driving phases, Mortenson imports location data to the equipment from topographic surveys and CAD files. Robotic Trenching
Engineering, procurement and construction company Black & Veatch has helped develop an exosystem designed for trenching on solar facilities and other projects.
Roe said that the firm worked with Built Robotics on their Exosystem, considered a great fit for trenching because it happens away from critical work.
Tyler Parker, construction tools and technology manager for the firm, noted that the system has proven “to be a low risk, high reward in terms of a knowledge-building opportunity.”
Partnering with Build Robotics, Black & Veatch introduced robotics beginning with 1,000-ft. trench lengths and progressing to 5,000-ft. trenches. The firm then successfully implemented the technology in full on a project last year.
The Built Robotics system uses design data from CAD drawings or survey points, along with operator input. As trenching progresses, said Roe, the system also compiles real-time as-built data, such as trench length, width and location. Based on design data, the system establishes boundaries via Built Robotics’ geofence feature.
To help improve safety on site, reduce production costs and increase productivity and efficiency, similar high-tech robotics systems are featured in other applications.
For example, the Ekso Evo Exoskeleton, a wearable device favored by engineering firm Burns & McDonnell, can reduce the impact of the weight of materials on the human body.
Repetitive Robots
Roe notes that robotics are visible in other construction applications including monitoring of field conditions in areas too dangerous for humans to navigate.
“Spot, a four-legged robot from Boston Dynamics has been used to gather site data and monitor field conditions,” he said.
Construction Robotics offers Semi-Automated Mason (SAM) for bricklaying and Material Unit Lift Enhancer (MULE) to handle heavy material on construction sites.
Husqvarna and Waste Robotics, among other manufacturers, offer a variety of robotic demolition equipment, noted Roe.
ULC Technologies has developed RRES, a robotic roadworks and excavation system that automates inspection and repair of underground utility pipelines and facilities.
Black & Veatch also is partnering with Honda on equipment capable of performing multiple applications, including moving materials, water and supplies to pre-set destinations.
“The team tested the prototype Honda autonomous work vehicle [AWV] at a construction site in New Mexico,” said Roe.
Technology to tackle construction tasks such as painting, drywall finishing and rebar-tying are in various stages of deployment, he said. Challenges to Integration
The challenge to widespread integration of robotics in construction is that many of the firms potentially benefiting are smaller trade and specialty contractors.
“That’s a big ask for a small firm when most of the machines are still relatively new and untried,” said Rob Leicht, a Penn State University associate professor.
He qualified that comment, adding that robots could become more affordable as they become more common.
Leicht believes improvements in transmitting design information to construction also are necessary to move for-

Skid steers are being programmed to pick up and move materials automatically, and backhoes to dig trenches, break up concrete and perform other tasks.
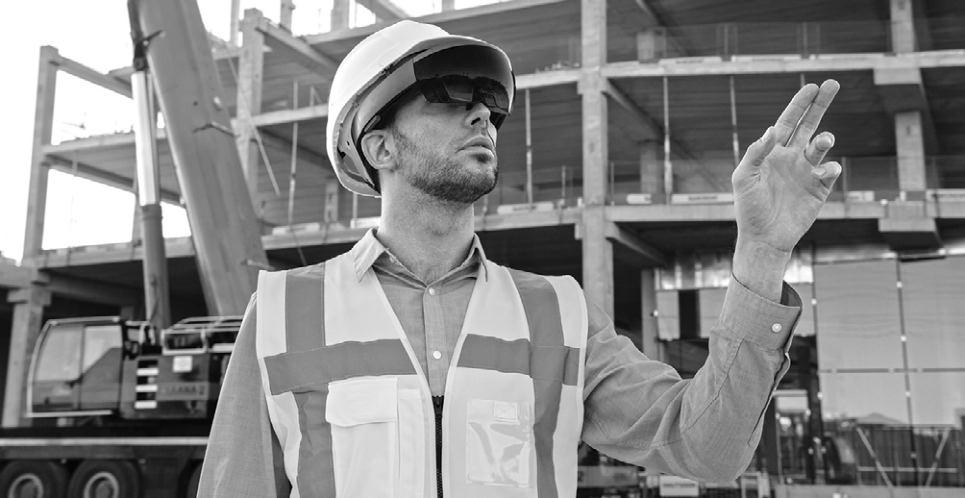