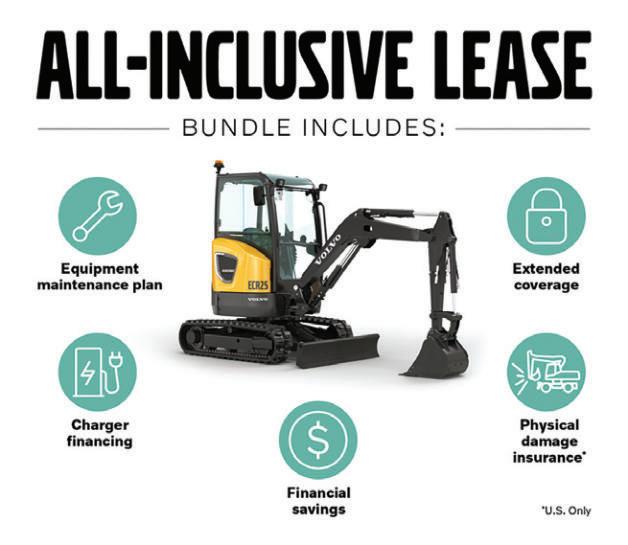
13 minute read
VOLVO CE LAUNCHES ALL-INCLUSIVE LEASE FOR ELECTRIC EQUIPMENT
Volvo Construction Equipment has launched a new financing option for the company’s electric compact equipment that simplifies the ownership experience. This all-inclusive leasing package bundles charging, maintenance, repairs and more — while also providing a better deal compared with items purchased separately. How It Works
Available in the United States and Canada through Volvo Financial Services (VFS), the process to set up an all-inclusive lease for electric machines is the same as with other Volvo CE machines. Customers will work with their local Volvo CE dealer and VFS to set the length of the contract, determine how many hours each machine could operate, and negotiate monthly payments.
Then, within the all-inclusive package, customers also get: • An equipment maintenance plan to help ensure the electric machines stay up and running as they should. Lessees will have the option to bring machines into their Volvo dealer location for maintenance or have a dealer come to them. • Extended coverage for repairs, beyond the factory warranty period. This helps limit some risk by covering machines for a longer time. • Physical damage insurance (currently only available in the United States) in the event of a
Simplifying Ownership covered accident happening that causes damage to the machine. • The option to finance a charger alongside the lease with a single monthly payment. The charger is purchased, not leased, but it’s financed within
Volvo CE Launches All-Inclusive Lease the same terms and rates as the complete package. As an example, if you sign up for a 48-month for Electric Equipment lease, you have the option to pay for your charger in 48 monthly payments as well. And because it’s bundled, you’ll only make one payment per month to VFS. • Save money on the bundle of electric compact machines. This could be up to 15 percent less on the monthly payment than acquiring items separately, depending on the dealership — and is only available through the all-inclusive lease. Another benefit is that the leasing packages come with a simplified early termination option at 24 months. Getting Started To explore financing options, customers can visit the Volvo electric machine site, select the model they’re interested in, and use the “build and quote” tool to configure the model to their needs. If they select the financing application in the tool, a dealer will follow up with them. Customers also can reach out to their local Volvo dealer for a quote. For more information, visit www.volvoce.com.
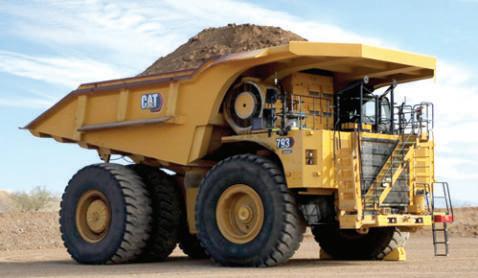
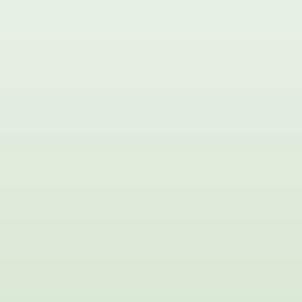

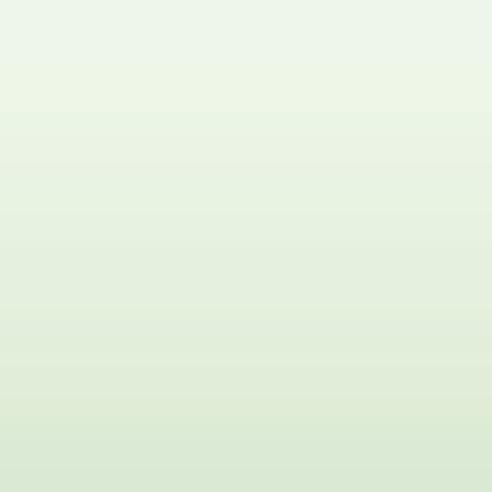
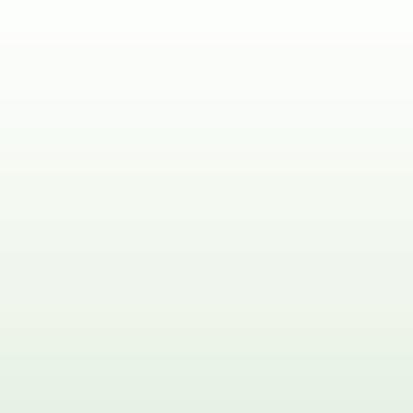
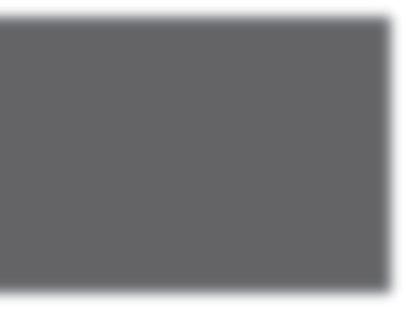
Caterpillar’s first battery electric 793 large mining truck demonstrated at the company’s Tucson Proving Ground.
Caterpillar Demos e-Truck
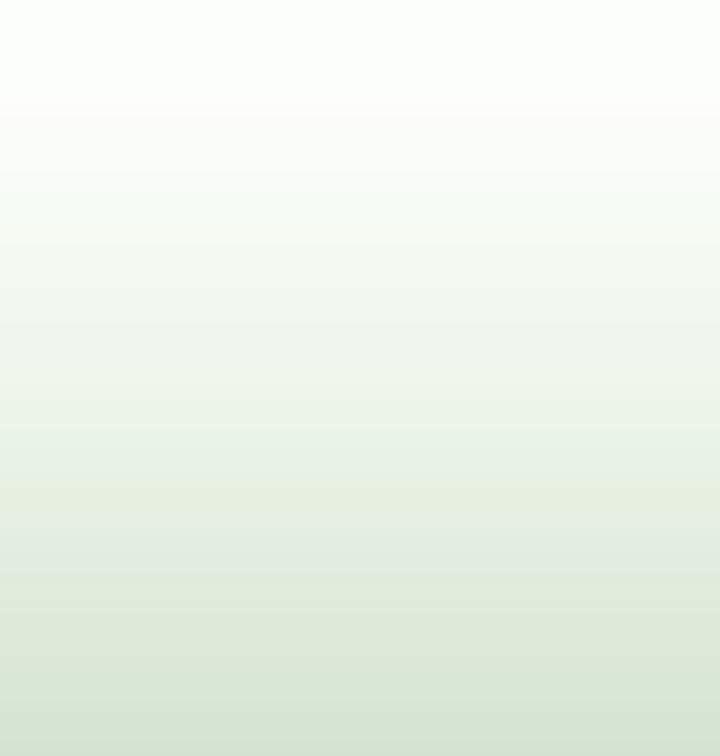
DEBUT from page 58
“The transformation of the Tucson Proving Ground allows Caterpillar to demonstrate our energy transition commitments and serve as a stronger advisor to customers as we navigate the changes together. We know it will take an integrated, site-level solution for miners to achieve their carbon-reduction goals, and we’re here to help as they redefine the way they mine for generations to come,” said Johnson.
As part of the site transformation, the company will install the latest advancements in sustainability technology, including green hydrogen production, natural gas and 100 percent hydrogen reciprocating engine power generation, fuel cell power generation and expanded energy storage systems. The site also will leverage a variety of renewable power sources, including wind, solar and hydrogen, capable of powering the facility and its products as they become electrified.
The transformation of the facility also will serve as a learning platform for optimizing charging and energy management integration.
For more information, visit www.caterpillar.com.
BTI Optimizes Business Telecommunications
COMMUNICATIONS from page 63 on my phone to help resolve it.”
Other businesses also are finding value in simplifying the complexity of their phone systems at a low, flat monthly rate.
Market Contracting Services, a construction firm in Chicago, Ill., had remodeled its facility and planned to purchase costly landline phones for the office, but reconsidered when its technology integrator suggested a better option, according to Esmeralda Macias, the firm’s office manager.
“With the new VoIP smartphones BTI has available, we don’t have to pay for landlines. We can see everything online now through a portal, so can view all incoming and missed calls,” she said.
According to Macias, employees no longer have to sit at a desk to take calls since they can do so anywhere they have an internet connection.
“Even after hours, we can transfer calls to our smartphones. This has translated into better customer support and more sales,” she said.
From a budgetary perspective, the VoIP phone system also has a success. The system not only eliminates current carrier bills, but also includes unlimited local and domestic long distance.
“The landline phones and service were going to cost a lot more. By implementing GoodPhone, we are already way ahead financially — and we are just getting started with using the capabilities of the VoIP phones,” she said.
Business telecom systems have long been complex and costly, leading to user frustration. However, with greater choice in the marketplace today, construction businesses that integrate essentially all required telecom services through VoIP phones at a low, fixed cost can streamline their operations and gain a competitive advantage.
For more information, call 1-800HELPBTI (1-800-435-7284); email info@btigroup.com; or visit https://www.btigroup.com.

CSVT from page 1 CSVT. The project will finish a missing link for the Route 15 corridor and connect travelers with a new four-lane limited access highway between the greater Baltimore area in the south, past Harrisburg (the state capital), through central Pennsylvania, to Rochester, N.Y., and beyond in the north. After being halted in 2008 due to underfunding, construction was finally made possible by Pennsylvania Act 89 of 2013.
The northern section connects PA 147 south of Montandon to U.S. 15 south of Winfield. This includes a bridge over the West Branch Susquehanna River. The southern section will connect U.S. 15 south of Winfield to U.S. 11/15 north of Selinsgrove.
The entire undertaking will be 13 mi. long and will include work on four interchanges as well as construction of 21 bridges. The total package of work on both the northern and southern sections, including design, right-of-way acquisition, and other pre-construction activities, will cost approximately $900 million.
“This project has been planned for decades and is a significant accomplishment,” said District Executive Eric High to the people celebrating the opening of the northern section of the project. “Although much work remains to be completed, these are significant milestones for this long-awaited project and major steps toward achieving its far-reaching benefits in north central Pennsylvania.”
Earthwork has begun on the southern section, with the entire project slated to be opened to traffic in 2027.
The rolling hills of the central part of the state will require some 4.5 million cu. yds. of rock and dirt to be moved for the southern section of the work. A similar amount was moved on the northern part of the project.
“The dirt moved will be relocated to other parts of the project to ensure a good path for the four-lane highway,” said Ted Deptula, PennDOT assistant construction engineer of the project. “This section will require installation of drainage facilities and various culverts. Although flooding is not a big concern in this area, we will be building numerous bridges over smaller streams and adjacent low-traffic-volume roads.”
Project planners and workers have been careful to protect stream valleys in this verdant area.
“We are building culverts to carry waterways from one side of the highway to the other,” said Deptula. “The project footprint has been minimized as much as possible, and to offset unavoidable impacts, we have created wetlands and improved streams elsewhere in the region.” Important Waterway Project planners and workers crafted some impressive bridges to carry the new highway in the northern part of the job. Workers built nine bridges with one nearly a mile long, spanning the west branch Susquehanna River. The river bridge required some impressive piers ranging from 60 ft. to 180 ft. tall. The west branch Susquehanna River is heavily used by recreational boaters. To protect the boaters and for the health of this important body of water, workers built a causeway that enabled the construction team to work on half the bridge at a time. Almost all of the bridges on the project were new. Contractors took other steps to preserve the environment as well as save time. These efforts included locating a concrete batch plant on site and trucks traveling just 10 mi. to get asphalt for the road building. This saved the workers time and required fewer trips to a source for concrete and asphalt.
“The northern section of the four-lane highway had some areas of poor subgrade that was improved with cement stabilization … 4 inches of subbase and 4 inches of cement treated permeable base were used throughout the project,” said Deptula. “The teams then placed a 9-inch long-life concrete pavement. Our crews topped that with 3 inches of longlife asphalt binder and a 2-inch thick surface layer of stonematrix asphalt.”
Deptula believes this road building will provide motorists with a long-life pavement for years to come.
“This new road in both the northern and southern sections will provide faster, safer traffic. It will also benefit local traffic with fewer conflicts from the larger faster-moving through traffic.”
Contractors Trumbull Corporation and New Enterprise Stone and Lime handled the majority of the excavation, bridge building and paving work for the northern section. They worked through the Pennsylvania winter on the excavation so the rest of the building could be done during the construction season.
“It was a bit of a thrill being a part of something so long
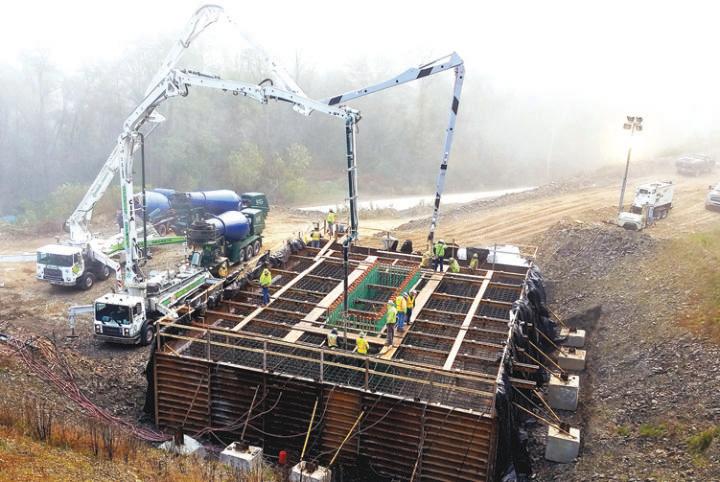
Crews construct a land pier foundation. The first beams for the river bridge are set in place. see CSVT page 80

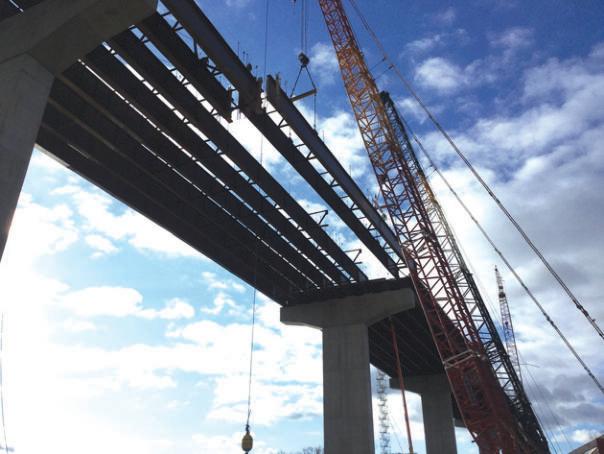
ROBOTICS from page 1
“In an industry often averse to risk, construction professionals will want to see proof of success before widespread adoption of robotics in the field,” wrote Andrew Roe, president of consulting firm AGR Associates.
As he sees it, robots are on construction sites everywhere, performing tasks humans would rather avoid.
“The robots are performing repetitive and sometimes dangerous work — often guided by CAD and BIM data,” said Roe. “With the construction industry facing a labor shortage, the new tools are helping firms keep up with mounting workloads.”
Surveying and data collection were automated years ago, but robotic equipment is transforming construction sites all across the United States.
Automated Pile-Driving
Automated technology is being adopted in the movement of construction materials from one location on a job site to another.
Construction companies partnering with manufacturers and integrating technology are crucial to the transformation becoming reality.
Mortenson Construction, partnering with Italian manufacturer Orteco, is using equipment that automatically distributes piles across solar farms. The GPS pile-distribution system was recently used on a large solar project in West Texas.
In the process, Mortenson was able to redirect crews to other more critical tasks and expedite completion of the project’s initial phases.
Roe explained that the machine can free up to 80 percent of the craft workforce traditionally required to mark pile distribution points. The machine can then deliver piles to each location on the solar farm site, according to Mortenson. The pile-distribution system can precisely position piles awaiting the driving process.
“Our goal isn’t to reduce labor,” said Trent Mostaert, vice president of solar and emerging renewables for Mortenson. “The real goal is to accelerate how quickly we build solar projects. We want to get more out of the labor we have.”
The automation continues to the actual pile-driving process, which features GPS-enabled machines from Vermeer. The GPS technology monitors pile installation with half the workforce used traditionally.
Mostaert said that in combination, the autonomous and semi-automated pile driving machines help reduce cost and risk of injuries.
“Smartly deploying our available workforce on the right aspects of a project and utilizing technology to improve in other areas makes this a reality.”
For the pile delivery and driving phases, Mortenson imports location data to the equipment from topographic surveys and CAD files. Robotic Trenching
Engineering, procurement and construction company Black & Veatch has helped develop an exosystem designed for trenching on solar facilities and other projects.
Roe said that the firm worked with Built Robotics on their Exosystem, considered a great fit for trenching because it happens away from critical work.
Tyler Parker, construction tools and technology manager for the firm, noted that the system has proven “to be a low risk, high reward in terms of a knowledge-building opportunity.”
Partnering with Build Robotics, Black & Veatch introduced robotics beginning with 1,000-ft. trench lengths and progressing to 5,000-ft. trenches. The firm then successfully implemented the technology in full on a project last year.
“The robot did exactly what it was designed to do,” said Parker. “It was very successful.”
The Built Robotics system uses design data from CAD drawings or survey points, along with operator input. As trenching progresses, said Roe, the system also compiles real-time as-built data, such as trench length, width and location. Based on design data, the system establishes boundaries via Built Robotics’ geofence feature.
To help improve safety on site, reduce production costs and increase productivity and efficiency, similar high-tech robotics systems are featured in other applications.
For example, the Ekso Evo Exoskeleton, a wearable device favored by engineering firm Burns & McDonnell, can reduce the impact of the weight of materials on the human body.
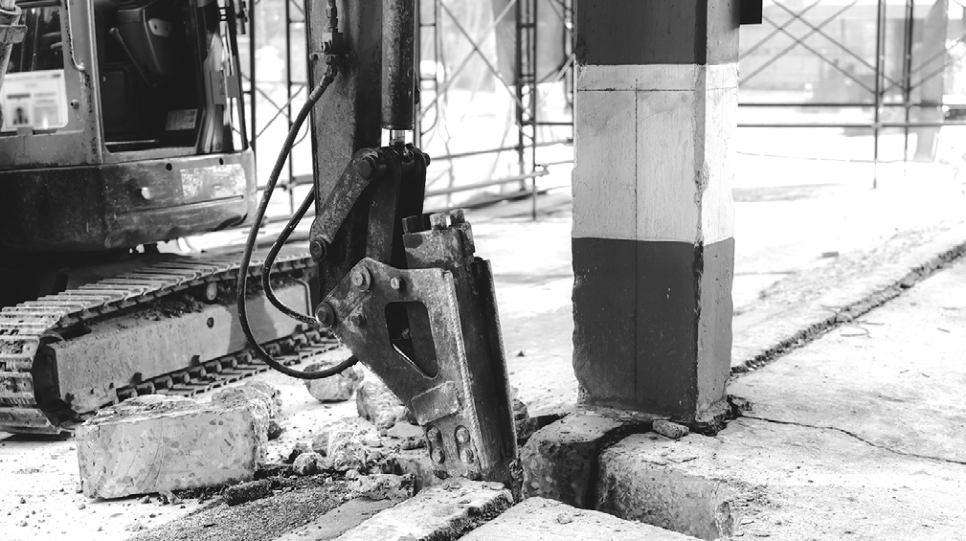
Skid steers are being programmed to pick up and move materials automatically, and backhoes to dig trenches, break up concrete and perform other tasks.
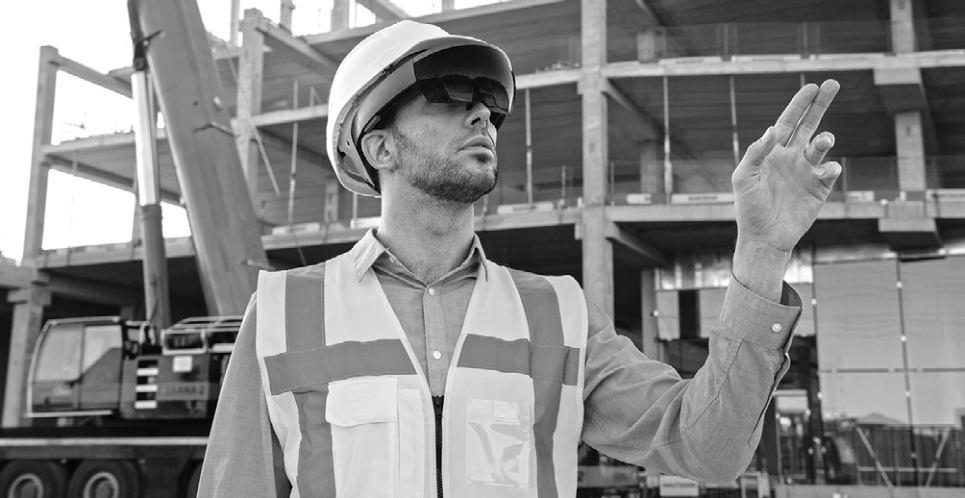
3-2605
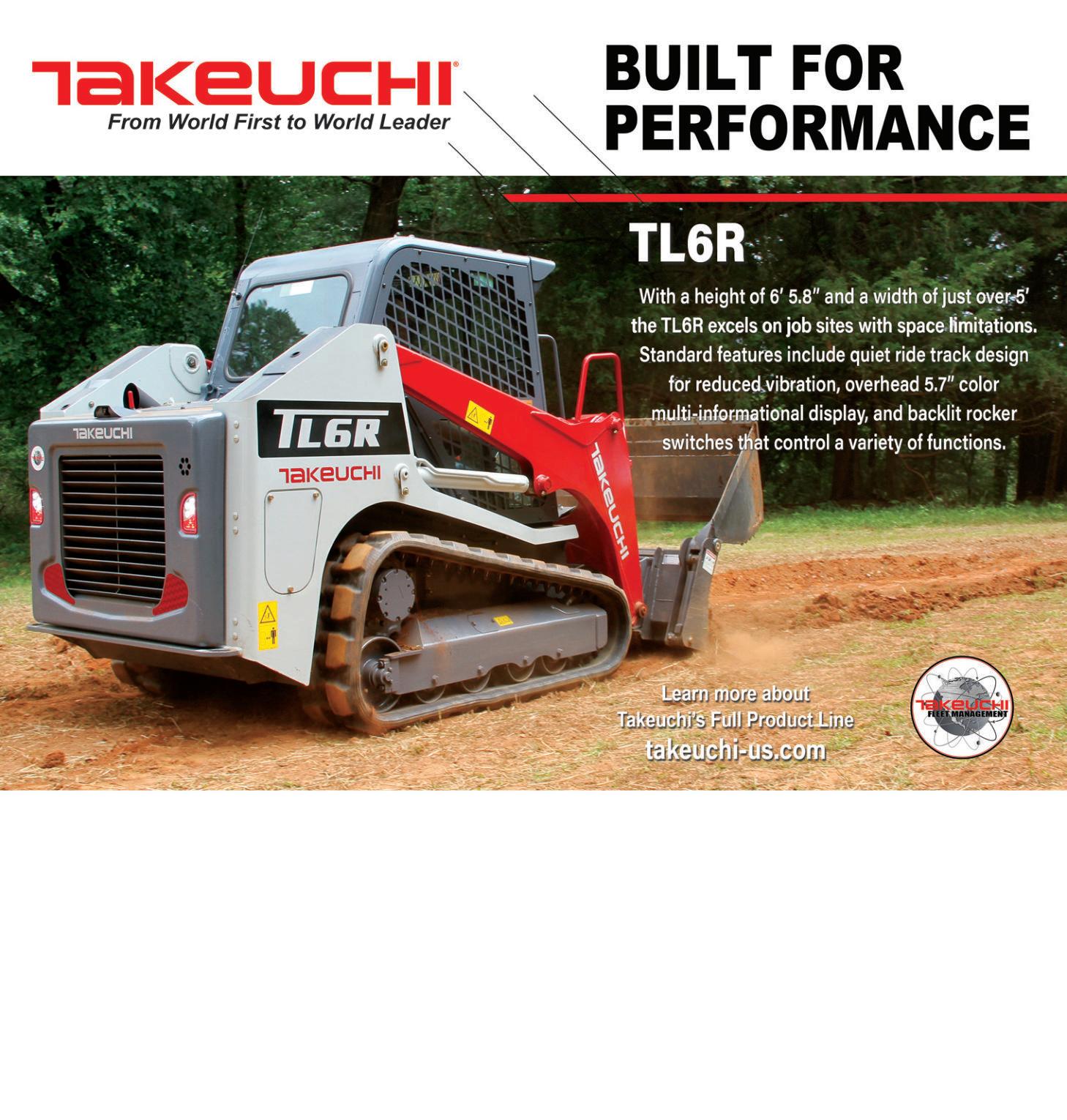
www.andersonequip.com
18 Gorham Industrial Pkwy Gorham, ME 04038 207/591-5482 142 Target Industrial Circle Bangor, ME 04401 207/942-0177 4176 Route 417 Allegany, NY 14706 716/372-8822 720 E Franklin Street Endicott, NY 13760 607/748-3400 115 Middle Road Henrietta, NY 14467 585/334-6770
2140 Military Road Tonawanda, NY 14150 717/877-1992 6317 Thompson Road Syracuse, NY 13206 315/463-8673 912 Albany Shaker Road Latham, NY 12110 518/785-4500 151 Packard Road East Montpelier, VT 05651 802/223-9689 1 Andy’s Way South Charleston, WV 25309 304/756-2800
Greenwood, DE 800/756-9433 Aberdeen, MD 410/575-6580 Upper Marlboro, MD 301/627-3938 Baltimore, MD 410/247-7454 Frederick, MD 301/682-4441
www.chadwick-baross.com
10 Fox Hollow Road Oxford, CT 06478 203/200-8637 67 McGuire Road South Windsor, CT 06074 860/761-0381 15 Katrina Road Chelmsford, MA 01824 978/479-1524 31 James P Murphy Ind. Hwy West Warwick, RI 02893 844/238-7673 www.chappelltractor.com

454 Route 13 South Milford, NH 03055 603/673-2640 251 Route 125 Brentwood, NH 03833 800/616-5666 391 Loudon Road Concord, NH 03301 800/358-6007 www.allislandequipment.com
39 Jersey Street West Babylon, NY 11704 631/643-2605
www.GroffTractor.com
Cranberry Township, PA 724/898-1535 Ebensburg, PA 814/472-7300 Ephrata, PA 717/738-0220 Mechanicsburg, PA 717/766-7671 New Stanton, PA 724/755-0124 State College, PA 814/353-8400 www.medicoce.com
3647 Shafer’s Schoolhouse Rd. Stroud Township, PA 18360 570/420-0877
1500 Highway 315 Wilkes-Barre, PA 18702 800/633-0027
www.gtmidatlantic.com
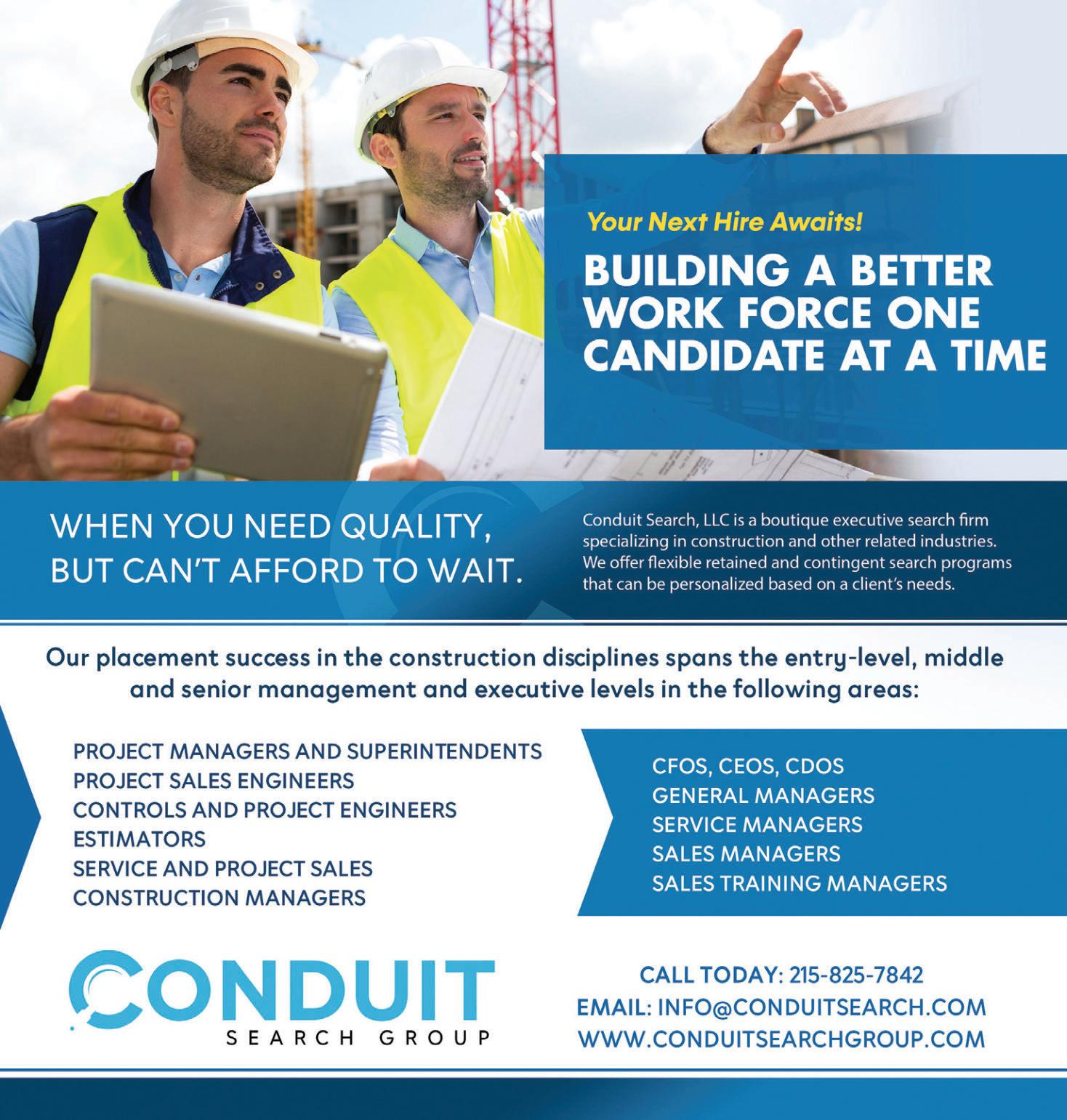