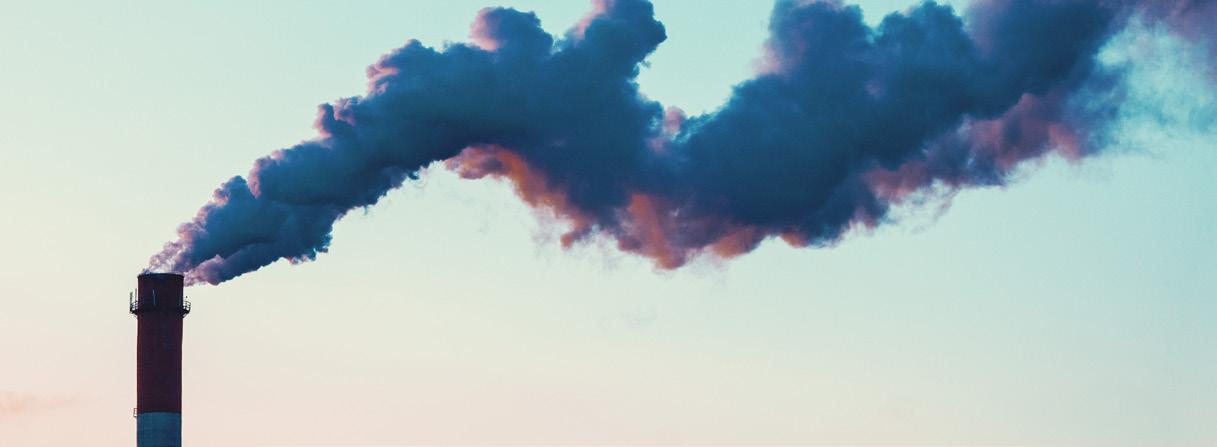
2 minute read
3 Ways to Become More Agile
There’s a recurring theme among the manufacturers who coped the best during the March 2020 national lockdowns - they were agile. Henry Anson, MD of Hennik Research, calls it being “sustainable”, though he adds: “In this instance, I mean building a sustainable business to last and that can withstand seismic shocks such as COVID-19.
“There will be a green element to this as many governments are looking to rebuild their domestic economies on the back of a zero-carbon agenda and will support companies and organisations that embrace this. This sustainability drive will include looking at new business models such as eCommerce, B2B2C and servitisation as manufacturers search for new and more sustainable revenue streams.”
Advertisement
In other words, the more agile your business operations can be, the faster you can adapt to this new world. Yet, only 14% of manufacturing business leaders believe the statement “we are agile and pursue new opportunities that emerge” which highlights the need to become more so. Here are three ways manufacturers can become more agile.
Accept that de-globalization may be the new norm
Traditionally for manufacturers, cost has been the biggest determining factor in sourcing raw materials and component parts. However, it might no longer be possible or viable to source entirely from a particular region. The COVID-19 crisis in particular has been instrumental in exposing the effects of disruption on global supply chains. Tackle any future issues by considering the following:
• Choosing suppliers from alternative countries where doing business may not be as complex, disruptive or expensive
• Optimising your existing plants so they’re operating as efficiently as possible. Automation and digitally-enabled workflows are particularly helpful here as they reduce manual work and boost workforce productivity
• Re-evaluating your global manufacturing and supply chain footprint. You may even need to shorten your overall supply chain cycle time so adapting to changing environments is much easier in future
• Preparing to extend to adjacent products that are countercyclical or based on their demand. For example, being able to manufacture PPE alongside or in place of your regular products
Speed up industry 4.0
Despite the bevy of technological solutions available to the manufacturing industry, large-scale adoption is still rare. Digitalization tends to be very “piecemeal”, as Kevin Bull, our Product Strategy Director, calls it because ‘going digital’ is mostly based on need or market demand.
However, it needs to cascade throughout your whole business if you want to reap the full benefits. These steps will help:
• Digital capabilities need to be addressed from the top. Your senior leadership team needs to clearly communicate this to your wider team and ensure everyone shares a common goal.
• Look beyond information storage systems. A great ERP system can obviously be a huge benefit but it’s not just about consolidating your data. Also look at solutions to improve your asset performance and visibility, such as predictive maintenance, AI and machine learning.
“IM companies have been talking about and piloting new technology solutions for the past few years but have not broadly implemented them at scale.”
Bridge the digital divide
There’s little point in investing in state-of-the-art technology if no-one in your business knows how to use it. Finding the right talent can be tricky too so you’ll need to upskill your employees. Fortunately, 77% of workers are willing to learn new skills or completely retrain to enhance their employability - so take advantage of that.
Bridging this digital divide can help your employees to act or think more proactively when it comes to innovation. This is what propels you towards agility. For example, you might need to perform additional quality assurance (QA) checks as a result of an increase in production volume and market demand. Employees who can think innovatively might have the idea to develop an app to assist with this data capture process. All it takes is a change in mindset and a relatively small amount of training.
“In just a few weeks, you can get people to a level where they’re able to create those sorts of apps to capture that data and automate from there,” says Clothier, Technical Director. “As soon as you capture data, you can automate data flows & make your employees’ lives much easier.”