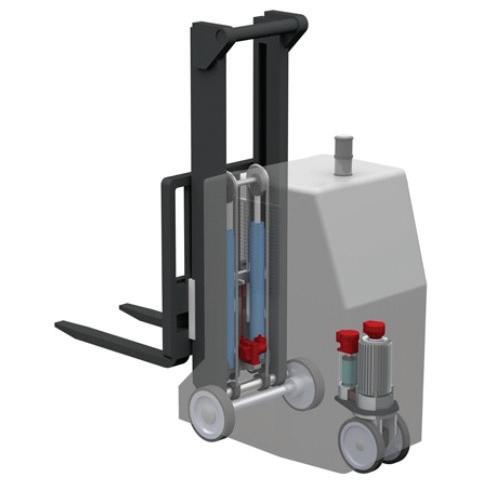
2 minute read
The role of the encoder in AGVs
The British Encoder Products Company looks at the role encoders play in Automated Guided Vehicles and the applications that complement the technology.
Process automation, machine construction and increasing the efficiency of systems or installations require highly precise equipment, and encoders are one such example.
The encoder is not just a rotary encoder. It is part of the automation system, thanks to which it is possible to determine the efficiency of various types of machines. Proper knowledge of encoder functionality and the ability to use them makes it possible to increase productivity – in other words, encoders save time and money.
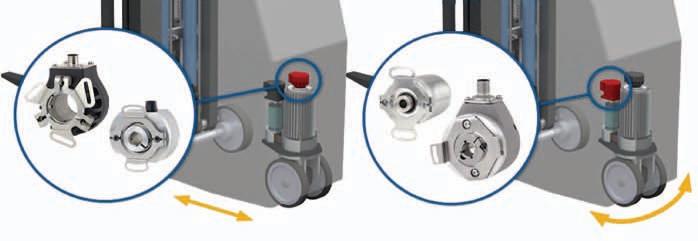
The encoder allows the control of movement, drive, and operation of individual machine components, and then – most notably from a business perspective – the optimisation of operations. Without the supervision provided by the encoder, motion optimisation would not be possible.
Whether you are working on Automated Guided Vehicles (AGV), Automated Guided Carts (AGC), or Autonomous Mobile Robot (AMR), or any of the other designations being used, robots and robotics are becoming increasingly important to the industry, moving parts, and materials in every environment from manufacturing to warehouses, to customer-facing grocery stores.
It is vital that these automated machines do their jobs correctly to ensure precision. For that, the controllers require reliable motion feedback. And that’s where British Encoder Products Company (BEPC) comes in.
Lift control
Many automated vehicles and carts lift materials and products onto and off shelves, floors of warehouses, or other storage areas. To do that repeatedly and reliably, the machines need precise, accurate motion feedback to ensure that products and materials get where they need to go, undamaged. BEPC’s draw wire solutions such as the Model LCX provide reliable motion feedback to ensure that lifts stop at the correct locations, safely moving products and materials where they need to go.
Drive motor feedback
As automated vehicles and carts move around warehouses and other facilities, their motors need reliable motion feedback to ensure they remain in designated transit corridors/areas and to ensure accurate stopping and starting.
BEPC motion feedback devices, including the compact, high-performance Model 15T/H and the economical Model 260, have provided reliable, repeatable motion feedback on motors for more than 50 years. Our engineers and encoder experts understand motor applications and how to determine the right motion feedback device for drive motor feedback.
Absolute feedback for steering assemblies
Steering assemblies require precision to ensure the correct steering angle and drive path. The best way to ensure proper motion feedback in these applications is to use an absolute encoder.
Absolute encoders like the compact 36mm blind hollow bore Model A36HB ensure smart positioning, providing an exact location in a 360-degree rotation.
BEPC offers a range of absolute encoder solutions that can provide motion feedback.
Other applications
There is a range of other functions related to AGVs where encoders play a crucial role. They include conveying, registration mark timing on machines such as automated palletisers, shrink wrappers and pick and place robotics, plus gantry systems and case packers.
Encoders are indispensable wherever precise measurement and supervision of speed, direction of travel, distance travelled, and position of mechanical elements or number of rotations performed is necessary. And with their potential to support significant gains for manufacturing businesses, specifying quality, reliable and highly accurate encoders can be a relatively small investment.