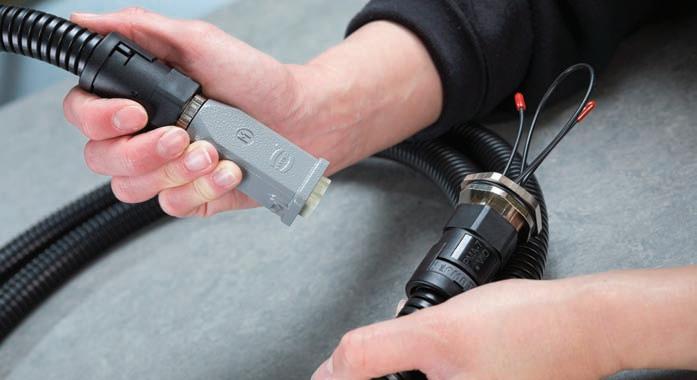
2 minute read
Connectivity solutions for machine building
HARTING has been at the forefront of connectivity for the last 75 years, with a focus on the design and manufacture of its industrial Han range of connectors, which has been supplying machinery, manufacturing and other industries with the three lifelines of data, signals and power since 1956.
Manufacturers are increasingly seeking solutions which allow them to embrace flexible production schedules and new innovations. As a result, the machine-building sector is continually evolving as customers demand more intelligent and adaptable machinery.
The Han-Modular series allows users to create a flexible and versatile solution by combining individual inserts for different transmission media into standard-sized industrial connector housings, enabling a wide range of customisable combination options.
With the new Han-Modular Domino range, machine builders have even more options, thanks to space savings of up to 50%. By dividing the mating face in two, even larger contacts can be accommodated, allowing power, signal, data or compressed air to be combined in one module, reducing the total number of interfaces required.
As a result, assembly areas which are difficult to reach can be equipped more efficiently or even opened up for assembly in the first place. With the addition of the new Domino range, there are now over 250 modules to choose from and many thousands of potential combinations available, increasing design flexibility. They are also compatible with standard components of the Han-Modular series, so they can be easily integrated into existing systems and machinery.
In addition, the Han-Eco range allows machine builders to pre-assemble and mount inserts into housings from the rear, rather than the traditional method of installing cables through the bulkhead before assembling the contact inserts. This method gives users the flexibility to pre-assemble the switch cabinet units and cable harnesses separately.
Han-Eco is manufactured from highperformance polyamide plastic, which complies with standards IEC 61948 and EN 45545-2. The range offers IP65 protection and substantial weight savings compared to traditional metal housings. In addition, the hoods and housings are suitable for both indoor and outdoor applications and are entirely compatible with standard metal Han housings, meaning both variants can be integrated into your production equipment.
As well as current developments, HARTING is also looking to support machine builders in the future with its Connectivity+ strategy. An extensive product portfolio has its benefits but can also create complexity. HARTING will expand and improve its digital offerings, including watch lists, product documentation and engineering data.
Connectivity+ ultimately aims to make workflows and process reliability more efficient and improve sampling for quicker prototypes, helping to enhance the design in process and product production for machine-building solutions.
Alongside connectors, HARTING also designs and builds custom cable assemblies with standard or custom cable lengths and a range of plastic or metal housings. All customised products are built at the company’s manufacturing facility in Northampton and are based on marketleading connectors from the extensive HARTING range, including the Han-Eco and Han-Modular options mentioned above.
Services include installing components, efficiently routing cable harnesses and fabrication. To further assist customers, an in-house design team can create a 3D CAD visualisation of a build beforehand to ensure absolute accuracy before manufacturing begins.
The HARTING manufacturing facility holds ISO 9001 certification for Quality Management, the ISO 14001 Environmental Standard, and UL certification for Wiring Harnesses ZPFW2 / ZPFW8. www.harting.com/UK