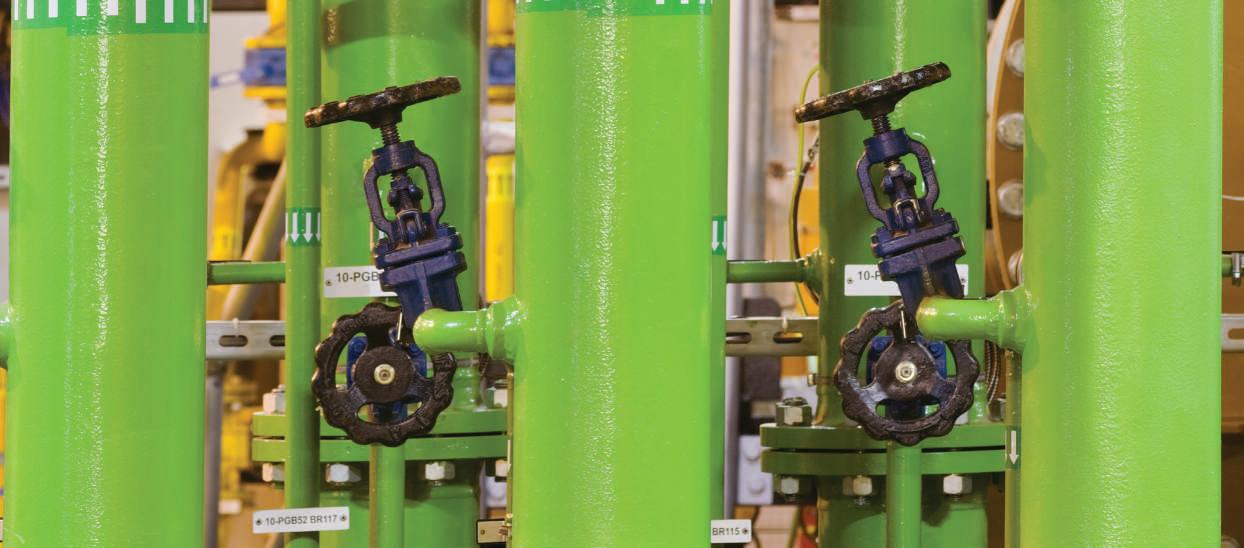
17 minute read
AN OVERVIEW OF BUSINESS MODELS IN INDUSTRIAL GASES
by ChemNews
RAVI RAGHAVAN* Editor – Chemical Weekly
INTRODUCTION
Advertisement
Industrial gases, also referred to as bulk or commodity gases, are produced in relatively large quantities for use in a variety of industrial manufacturing processes. The industrial gas industry comprises establishments primarily engaged in manufacturing industrial organic & inorganic gases in compressed, liquid and solid forms.
The principal industrial gases are derived from air and occur in air in the following proportions: nitrogen (78%), oxygen (21%) and argon (0.9%). Rare gases occurring in and recovered from air in much smaller quantities are krypton, neon and xenon. Carbon dioxide, helium and hydrogen also qualify as important gases, but commercial quantities are derived primarily from other sources.
MANUFACTURING TECHNOLOGIES
Industrial gases are produced commercially by several routes, which can be classified into two broad categories – cryogenic and non-cryogenic. The technology choice deployed is largely determined by: z The number of products that must be supplied (e.g., nitrogen or oxygen or both); z The required production rates for each gas and/or liquid product; and z Required product purities.
CRYOGENIC AIR SEPARATION Cryogenic air separation is the most efficient and cost-effective technology for producing large quantities of oxygen, nitrogen, and argon as gaseous or liquid products. In this process large volumes of air are taken from the atmosphere, compressed, cooled, and liquefied. Through a process of distillation the air is then separated into its major components.
An Air Separation Unit (ASU) using a conventional, multi-column cryogenic distillation process produces oxygen from compressed air at high recoveries and purities. Cryogenic technology can also produce high-purity nitrogen as a useful by-product stream at relatively low incremental cost. In addition, liquid argon, liquid oxygen, and liquid nitrogen can be added to the product slate for stored product backup or by-product sales at low incremental capital and power costs.
Cryogenic distillation is necessary to produce argon. Because argon is only 0.9% of air, it cannot be produced economically unless it is a co-product, usually of a high purity oxygen plant or sometimes of an ammonia plant.
NON-CRYOGENIC PROCESSES Unlike cryogenic plants, which use the difference between the boiling points of nitrogen and oxygen to separate and purify these products, noncryogenic air separation plants use physical property differences such as molecular structure, size and mass to produce nitrogen and oxygen.
The most common technologies used for non-cryogenic air separation plants are: z Pressure swing adsorption (PSA) – used to produce nitrogen or oxygen using different adsorbents; z Vacuum swing adsorption (VSA) – used to produce oxygen; z Membrane separation – used to produce nitrogen gas; and z Ion transport membrane (ITM) – which uses a ceramic membrane to deliver high-purity oxygen.
COMPARISON OF MANUFACTURING TECHNOLOGIES
Within each technology family – cryogenic and non-cryogenic – there are numerous choices that can be made regarding the specifics of process design, machinery configuration and system control. These all have capital cost/energy cost, and operational flexibility / plant reliability trade-offs.
Non-cryogenic plants are less energy efficient than cryogenic plants (for comparable product purity), but may cost less to build, in particular when the required production rate is relatively small.
Non-cryogenic processes are most suitable when high purity product is not required by enduse applications. This is because the physical size of the plant can be reduced as required purity is reduced, and the power required to operate the unit is reduced as well.
Non-cryogenic plants are relatively quick and easy to start up, which is useful when product is not needed full time.
At high production rates, cryogenic processes are the most
cost-effective choice. They can produce very pure end-products; and must be used to produce liquid nitrogen, oxygen and argon.
USE OF INDUSTRIAL GASES
Among the various applications, the petroleum refinery segment holds the largest share in the global industrial gases market. In particular, the demand for hydrogen in petroleum refining has increased significantly in the recent past, owing to stricter environmental legislations imposed by various governments. In refineries, hydrogen is used to remove sulphur from crude oil.
The growing need for alternate sources of energy is also increasing demand for industrial gases. Large-scale gasification plants and oxygen-based gas-to-liquid (GTL), coal-to-liquid (CTL), and coal-to-chemicals plants consume enormous quantities of oxygen. Increasing volumes of LNG have led to considerable demand for nitrogen (for refrigeration purposes).
Industrial gases used in the metals & metal fabrication industry include oxygen, hydrogen, nitrogen, carbon dioxide and acetylene.
INDIAN INDUSTRIAL GAS MARKET
The commercial industrial gases market in India was estimated to have generated revenues of $1.41-bn in 2019. This was up from just $882mn in 2009, indicating an average annual growth rate of 5.1% p.a. for the decade. Within the 2019-2024 timeframe, the industry is expected to see growth from 5.4% p.a., in a low scenario, to 7.2% p.a. in a high scenario. This should see the industry in India achieve revenues of between $1.84-bn to $2.00-bn by 2024.
Major consumers include Tata Steel, JSW, Bhushan Steel and Vedanta, from the metal processing industry, as well as oil & gas, petroleum refineries, petrochemical plants, fertilizer suppliers, etc.
Growth drivers for industrial gases in India include, amongst others: z Expansion by steel companies; z Investments in the oil & gas sector and in refineries; z Growing demand for packaged foods; and z Growth in the healthcare sector.
Major players in the Indian market include: Air Liquid India, Air Water, Bhagirathi Industrial Gases Pvt. Ltd., Bhagwati Gas Ltd., Bhoruka Gases, Bombay Oxygen Corporation Ltd., INOX Air Products, Linde India Ltd., Matheson K Air Pvt. Ltd., and Praxair India.
The global merger of Linde and Praxair has led to the divestment of some assets here in India to meet competition concerns raised by the Competition Council of India (CCI). z In August 2018, Japanese
PROCESS Adsorption Chemical Cryogenic Membrane ITM
STATUS Semi-mature Developing Mature Semi-mature Developing TABLE 1: TECHNOLOGY COMPARISON TABLE
ECONOMIC RANGE [TPD] <150 Undetermined >20 <20 Undetermined
BY-PRODUCT CAPABILITY Poor Poor Excellent Poor Poor
PURITY LIMIT [VOL, %] 95 99+ 99+ ~40 99+
START-UP TIME Minutes Hours Hours Minutes Hours
industrial gas producer, Air Water, took over three locations from
Linde: a gas plant in Bellary (Karnataka), and cylinder filling stations in Hyderabad and
Chennai. The gas plant (1,800tpd capacity), located at the steel plant operated by JSW Steel, delivers oxygen to the latter’s blast furnaces. The cylinder filling stations serve pharmaceutical and auto industries located around Hyderabad and Chennai respectively. These operations took in combined sales of Rs. 3.87-bn in 2018. z The CCI order also forced
Linde to sell its 50% stake in
Bellary Oxygen Co, the 50:50 JV with INOX Air Products, which operates an 855-tpd ASU at the
Bellary site. z The CCI order also forced Praxair to sell three on-site plants at Tata
Steel’s site at Jamshedpur and two cylinder filling stations at Kolkata and Asansol. All were acquired by
Air Water in July 2018. z Linde’s ASUs for Tata Steel at
Jamshedpur (2,550-tpd) and
Kalinganagar (2,400-tpd) and at
SAIL’s Rourkela plant (1,706-tpd), among others, were not affected by the CCI order.
BUSINESS MODELS IN INDUSTRY
The industrial gas market can be classified on the basis of delivery mode, as: z Tonnage supplies; z Bulk delivery; and z Supply in cylinders.
Very small volume users of single gases or gas mixtures typically purchase products in cylinders from distributors of packaged gases. Users with somewhat higher demand purchase liquid products that are stored at their site (in appropriately sized storage tanks) and vaporized as needed. Higher volume users are most economically served by on-site gas production or pipeline supply. TONNAGE SUPPLIES – APPROPRIATE FOR LARGE USERS WHOSE DEMAND FOR GAS IS MORE THAN 30-TPD. The gas supplies are generally made from plants located on or adjacent to the customer premises (on-site). It is very common for large consumers, such as oil refineries and steel plants, to have onsite ASUs or reformers, that provide continuous supplies of gases such as nitrogen, oxygen and hydrogen on demand and via pipeline running through the battery limits of the production site.
Tonnage customers of industrial gases have two options for securing gas supply: z In-house production (IHP); or z External supply (EXS).
In recent years, IHP has accounted for the vast majority of added tonnage capacity, particularly by companies that are cash-rich. As the industrial gas business is a mature one, the skill sets needed to operate the plants are readily available outside of the industry players. For setting up these IHP plants, customers have a range of Indian and global suppliers from whom they can turn to. Global players include Linde, Air Products, Air Liquide, Taiyo Nippon Sanso India (TNSI), Air Water/EIGL, Cryogenic Industries USA and many Chinese suppliers.
Globally, tonnage air separation plants now find use in a growing range of applications including: z Onsite oxygen supply to the chemical industry (e.g., ethylene oxide, methanol and reformer processes); z Onsite oxygen supply to the developing gas-to-liquid (GTL) sector (not very relevant in an
Indian context); and z Nitrogen supply (generally by pipeline) to pressurize oil fields and maintain crude oil production.
The largest part of demand for tonnage gases in India is generated by three steel companies, viz., SAIL, JSW Steel and Tata Steel.
The distribution in tonnage is generally made in gaseous form.
Tonnage plants – especially the EXS ones – are typically designed with some spare capacity to serve bulk and cylinder markets. For example, if the captive requirement of a gas consumer is 800-tpd, the ASU could be designed and built for producing 1,200-tpd, with the extra 400-tpd of gases targeted for other consumers.
There are several advantages of this model to both producer and consumer: z The gas producer gets access to land (free of cost, or at concessional rates) to locate the
ASU. z The gas producer gets access to utilities (such as power), which often is at a concessional rate (especially if the consumer has his own captive generation).
While gas companies typically procure power from state electricity grids at average grid prices of Rs. 7 per kWh, captive players generate their own power from in-house power plants at an average price of Rs. 4 per kWh. z The gas producer is able to size the plant to benefit from economies of scale, which translates to better margins.
Tonnage plants – especially the EXS ones – are typically designed with some spare capacity to serve bulk and cylinder markets. For example, if the captive requirement of a gas consumer is 800-tpd, the ASU could be designed and built for producing 1,200-tpd, with the extra 400-tpd of gases targeted for other consumers.
z Gas supply to the on-site consumer is always by pipeline, which results in savings in logistics. z The on-site consumer benefits from special gas pricing to compensate for the facilities provided to the gas producer.
The producer and consumer typically enter into a Minimum Take or Pay (MTOP) contract. Contracts are iron-clad and specify back-up availability from cryogenic storage of the supplier in the case of any disruption to continuous operations. For gas producers, on-site cryogenic storage also serves as a buffer to store output when the customer takes a shutdown (although the preference is for both client and customer to take planned shutdowns in a coordinated manner).
A point to be noted is that an ASU cannot be tuned below a certain threshold of operating rate and will have to be shut down.
The single most important component of the operating costs is the cost of power, and ASU operators attempt to index the price of gas supplied by them to their cost of electricity.
The Indian industrial gas sector has an unusually large onsite business for a developing country, with a large number of steel clients that have been ‘weaned’ off captively-owned and operated supply solutions in the last decade.
As blast furnaces and refineries have gotten bigger in size, the size of the ASUs needed have also risen. New plants now being built are in the sizes of 1,500-tpd to 2,000-tpd.
BULK DELIVERY – APPROPRIATE FOR MEDIUM USERS WITH DEMAND UP TO 30-TPD. These are made from off-site plants, which may be a standalone plant dedicated to bulk supply (merchant plants), or a tonnage plant (IHP or EXS), with some surplus capacity available for bulk supply (piggy back plants).
Bulk distribution is generally made in liquid form, and typically do not travel a distance beyond 400km (one way). The cryogenic tank typically is sent out on a ‘milk run’ topping up supplies along a predetermined route.
In this model, all assets at the customer end, for receiving, storing and distributing gases – such as tanks, compressors, pumps, pipeline etc. – are owned by the gas producer.
The gas producer typically bears the capital costs of the gas receiving infrastructure at the consumer and charges the consumer a Facilitation Fee (FF), which is typically indexed to inflation. Once the assets are depreciated (say in about five years), the FF represents a direct contribution to the gas producer’s profits.
Except in the case of argon – a relatively high value gas – the FF is the real income in the case of the bulk gases. In this sense, the merchant industrial gas business is akin to renting out capital goods.
Gas plants catering purely to the merchant market are sized in the range of 150-tpd to 200-tpd.
SUPPLY IN CYLINDERS – APPROPRIATE FOR SMALL USERS WITH DAILY REQUIREMENT RANGING FROM 5-50 LITRES Aside of onsite supply, the cylinder market currently dominates gas use in India, as the customer base is fragmented and spread out. These supplies are generally made from offsite locations, which can be merchant plants or ‘piggy back’ plants with cylinder filling facilities, or cylinder filling stations.
The distribution in cylinders is generally made in gaseous form.
Most gas companies have a network of filling stations in each region with overlapping catchment areas from where they are able to serve customers in that region.
Hundreds of gas suppliers play this turf, mostly at a local level. Most suppliers of gas in cylinders typically serve markets up to a distance of about 100-km. Beyond this distance, the costs of logistics – lugging filled cylinders by road to customer and doing the reverse with empty ones – turns out to be too high to make it economically worthwhile. It would not be too much of a stretch to say that moving gases by cylinders is more about moving metal (i.e., the
cylinder) than molecules (i.e., the gas itself), and efficiency improvements can bring significant gains to overall operations. The use of IT tools to track, trace and manage cylinder inventories, both at production site and, just as importantly, at customer end, is still rather poor in India and is an area companies are still to fully address.
While industrial gases are sold in all the aforesaid supply modes, medical gases are sold either in bulk or cylinder modes, and specialty gases are sold only through the cylinder mode.
GLOBAL GAS MARKET, BY TYPE [2017]
Others 4%
Onsite 30% Bulk 27%
Cylinders 39%
MANAGING LOGISTICS
The business of industrial gases can be considered one of managing capex costs and fleet costs.
The business is a 24x7 one, as neither producer nor consumer can afford disruptions in supply, depletion of inventories below critical levels, nor the build-up of inventory beyond the capacity of the storage units.
Suppliers also need to be able to manage variabilities in demand – be
it accelerated or reduced pace of deliveries from agreed norms. Plant outages are managed, if necessary, by arranging supplies from alternate producers, even if they are competitors. In several instances, customers insist on a No Objection Certificate (NOC) from a gas producer to switch suppliers in the event of a supply outage from one supplier, with explicit consent to use the first supplier’s infrastructure for storing gas from the emergency supplier.
Distribution Managers at the ASUs are typically charged with the task of managing logistics, and use IT tools that provide dashboards indicating tank levels, fleet availability, demand patterns, etc. at their important consumers.
To work around the problem of space restrictions at customer end, some gas producers have been offering skid-mounted liquid tanks (mobile units).
While pipeline transfer is efficient, they are as yet restricted to across-the-fence supplies in India, and pipelines are not permitted by regulators to traverse public areas. All tonnage supplies are done through pipelines.
Logistics play an important role in determining the location of a standalone production unit, in particular.
One option is to build small plants and dot the demand landscape with them. The transportation fleet size is then small in number as well as size (as they can do quick turnarounds). The alternative is to build large plants and use larger trucks to ferry loads, larger distances.
A merchant ASU typically does not serve a distance beyond 200-km.
MICROBULK – A MODERN CONCEPT YET TO COME TO INDIA Microbulk is a modern concept for delivery of industrial gases, where the gas is supplied by filling on-site as against the traditional method for smaller volume usage where gas is
supplied by swapping full for empty cylinders and dewars.
Microbulk fills a gap between high-pressure liquid cylinders and bulk storage tanks.
Microbulk gas storage vessels come in a variety of sizes and their use simplifies gas storage and distribution, boosts efficiency, saves money and serves a variety of applications.
Customers using more than two dewars or more than 15 high pressure cylinders per month are good candidates for converting to microbulk. Microbulk storage vessels are now available in sizes from 230-litres to 5,000-litres capacity (likely to go to 10,000-litres), and a range of pressure – from 22-psi to 500-psi.
There are several advantages to using microbulk: z The dedicated tank never leaves customer site, and tank levels can be monitored from offsite; z Enables hands-off reordering, making industrial gas a utility; z Avoids the hassles and dangers of moving cylinders, cylinder banks and heavy liquid dewars; z Reduces overall gas consumption – as it avoids residue wastage that can be as much as 15-20%; z Expand delivery range of gases to 150-km; z Fast fills improve efficiency – a 5,000-litre vessel can be filled in 15 minutes; z High-pressure cylinders replaced by low-pressure tanks; and z A Microbulk tank can last 25-30 years while liquid cylinders last between 3-5 years.
Microbulk is obviously not the solution for all customers. Its sweet spot is for customers who consume between 25,000-cubic feet to 100,000-cubic feet of gas per month, at pressures less than 500-psi. It is not an easy sell as there is a significant asset purchase involved. But it is a contractually secure business that enables locking in of customers for the long-term and so provides opportunity to do additional sales.
While Asia has been a slow adopter of microbulk, the momentum is now picking up. The idea is yet to gain traction in India.
END-NOTES
The business of industrial gases is a mature one, and the fundamentals of the technologies have not changed significantly.
The business is traditional in its operations, but that is changing. Enterprise Resource Planning (ERP) software such as SAP is almost ubiquitous in the industry today, and is widely used for human resource management, business planning, customer resource management (CRM) etc.
The industry has embraced e-commerce a bit slowly, but several initiatives have been initiated in the last couple of years globally. Though online shopping of commodity gases is now available from most industry majors. it is still not very common in India.
Automation has particularly improved the energy efficiency of operations.
Using predictive data analytics for maintenance of equipment is enabling delayed turnarounds to satisfy customer needs, and shifting maintenance from time-based to condition-based schedules.
[*MR. RAVI RAGHAVAN is a member of the Editorial Board of CHEMICAL NEWS and actively associated with all activities of Indian Chemical Council]
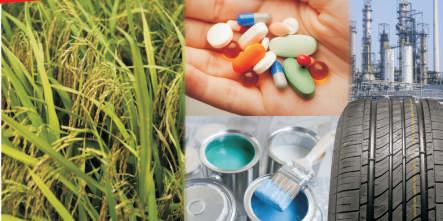