
16 minute read
Detailing the processes needed to keep cars safe
Diversity rules
Formed at the turn of the last century to cater for the needs of defence and the fire brigade, Coventry Climax accidentally arrived on the racing scene in the 1950s
By Lawrence Butcher
The Lotus 32B was powered by a Coventry Climax FPF 2.5 litre engine. Modern day versions of the same engine are probably more reliable and more powerful than in period
Long before Cosworth famously started to provide engines for customer and factory race cars, Coventry Climax was the go-to company for those needing a plug and play racing engine. From diminutive sub-1000cc units to screaming V8s, it produced a myriad of engines, but here we will concentrate on two of its 4-cylinder offerings, the FW series and the FPA, the two engines that helped the brand into motor racing lore.
That Coventry Climax became a byword for post-war racing engines may seem surprising given the history of the company prior to the 1950s. Originally it was founded as Lee Stroyer in 1903, a joint venture between Horace Pelham Lee and Danish born Jens Stroyer. Following the departure of the Dane in 1905 it became Coventry Simplex under the ownership of Pelham Lee. The company manufactured a range of light car and tractor engines, including those used by Shackleton’s trans Antarctic Expedition of 1914.
In 1919, having spent the first war manufacturing generator sets for searchlights, Pelham Lee purchased another company, Johnson & Smith Ltd, and changed its name to Coventry Climax Engines. The old company would continue under separate management while the newly formed Coventry Climax went from strength to strength.
Through the 1920s, production of car engines continued, supplying firms such as Morgan, Crossley and Triumph, but the financial strains of the early 30s saw the company diversify into more industrial applications, including waterpumping equipment. It was this move that laid the surprising foundations for some of its best known racing engines.
Following the Second World War, the key personalities of Walter Hassan (Chief Engineer and Technical director) and Harry Mundy (chief designer) joined the company. One of their first projects was the ‘FW’ engine, FW standing for Feather Weight, which was developed in response to a government tender for a lightweight fire pump engine. That tender was for a pump capable of delivering double the volume of water of the then current units, but weigh half as much. The engine Climax developed easily met the government requirement of producing 35 bhp at 3,500 rpm, in fact putting out 38 bhp, and the company was awarded the contract.
The FW was never intended for automotive use, never mind racing, but when it was displayed at the Earls Court Motor show in 1953 its high power to weight ratio attracted admiring glances from the racing fraternity. This was not surprising, the engine had an alloy block and head, OHC and even in industrial trim, a useful power output. Climax didn’t have any racing plans for the engine, and it was already involved in the development of a bespoke race engine, the FPE (see sidebar), but after some encouragement from constructors (including Cyril Keift, who bought a government surplus fire pump unit in 1953 for use in the Keift 1100 sportscar), Hassan, along with Leonard Lee (MD of Coventry Climax) saw there was potential for a move into the racing market.
The first FWA engine (Feather Weight Automotive) was under development by the end of 1953. Work was done on the porting and valve train, the capacity was upped to 1097cc (to suit the 1100cc racing class) and a pair of SU carburettors were fitted. The upgrades meant that the first FWA’s were good for 71 bhp at 6000 rpm and the first of four prototypes was used by Keift at Le Mans in 1954 (the car dropped out with a differential failure). The engine went on to be developed through various iterations, with capacities up to 1.5 litres and as low as 750cc (for the class that ran to that capacity at Le Mans), culminating in the 1-litre FWG for Formula 2 which revved to 9000 rpm and made just shy of 100 bhp.
The FWE More FWEs were produced than any other, specifically for Lotus to use in its Elite. With a capacity of 1216 cc (though generally referred to as the 1220) in road going trim, the engine featured a single SU carburettor and produced 70 bhp at 6000 rpm. However, in racing tune it had considerably more pep. Chris Tolman, of Tolman Motorsport, has been working with FWs, and FWEs in particular for many years, and the company has developed the engine extensively in pursuit of both reliability and performance. ‘It actually all started with one client, who raced an Elite,’ says Tolman. ‘He was an engineer and had done extensive work on the engines in the past, including with Brian Hart. He approached us explaining how they had been handling the engines, explained why they would break and asked us what we would do to fix it.’
Going back to engineering first principles, Tolman and his engineers quickly realised one of the most pressing problems was the cylinder heads breaking
where the dynamo attached. ‘The first thing we noticed was that there was a counterbore machining for studs, so we put a radius in there,’ notes Tolman. ‘Then we realised that nothing really lined up properly, so [put] everything [on a coordinate measuring machine] and made up new brackets that didn’t put any preload on any of the fasteners.’ Another perennial issue was oil leaks, which were cured by having all of the various fasteners remanufactured to much higher standards than the originals, curing these issues at a reasonable price.
Various traditional modifications to the engines also proved to be somewhat wide of the mark. ‘The blocks, being a post-war, aluminium casting, are not great, but that said, the main bearing studs are actually fantastic,’ says Tolman. ‘Yet people were taking the existing bearing caps out and ‘strengthening’ the bottom end with a plate and cap head bolts. So instead of machining off the cast alloy caps and putting in a steel plate, we’ve remade the centre main caps in 7075 aluminium, which works in conjunction with a stress plate, and that makes for a really strong engine.’
Another area that has come in for Tolman’s attention is the cam carrier, and the company has produced its own fiver bearing aluminium production to replace the cast iron original. ‘That helps a lot with things like the stack height of the cam, because the cam chain tension is a function of where the cylinder head and cam carrier sit,’ says Tolman. ‘Over

years of machining blocks and heads, you end up having to shim the cam carrier higher and higher under each of the bolts. I didn’t like the original cast iron [cam carrier] and it used to twist, so we have made an aluminium carrier, which is thicker than needed and which is then machined to the correct height during the build. That has also saved about 30% on friction, because it is aluminium with a steel bucket follower, rather than cast iron and cast iron.’
The company has developed three different piston versions: a replica of the original design, a variation with cutouts for larger valves and an intruder variant, the latter being intended specifically for race engines to allow fine tuning of compression ratio. ‘That also gives really good squish and a good burn,’ notes Tolman.
Tolman highlights that it has concocted an engine build specification to suit restrictive FIA historic racing regulations, which has great attention paid to areas such as the camshaft grind, and general finessing of the combustion process.
Due to the FIA demands regarding originality, he points out that these engines must also retain a completely mechanical distributor system. ‘We always run electronic ignition where we can, but with the FIA, it has to be clockwork, so we have done a lot of work to get that working well,’ explains Tolman.
One myth Tolman is keen to dispel is that FV engines were designed to be built with large tolerances, due to their original use as a fire pump. ‘The majority of owners think that, but having done the research, they have really tight clearances because its an aluminium engine, and it even says so in the fire pump build manuals from the era.’
He also notes that the real killer of these engines is the vibrations they produce, recounting, ‘the dyno we use is rated to take 2000 bhp drag racing engines, but we’ve done more damage
The Lotus Elite featured the Climax FW engine and was one of the reasons the engine was so prolific

with a little 1200 Climax than any of the big engines. In that respect, it’s a pretty horrible engine and we’ve broken driveshafts on the dyno before.’
The FPF As noted in the sidebar, Coventry Climax was already working on a bespoke, V8 racing engine in 1952, but while development of that stalled, it spawned what would be one of the companies most successful racing products, the FPF inline-four. Designed by Harry Mundy (who actually left the company in 1955 having completed the design, only to return in 1963), it saw service in a host of Grand Prix and sportscar machinery through the late-50s and 1960s.
Originally utilising the cylinder head design of the FPE, it was a twincam, OHV, I4, again, all alloy in its construction. The engine started out with a 1.5 litre capacity for Formula 2 competition, before being enlarged to nearly two-litres for Formula One use, and then 2.2 litres. This was the limit of its original architecture (it was never
initially designed with larger capacities in mind) and in late 1958, a redesign was undertaken to create a 2.5 litre engine, which went on to considerable success with Jack Brabham winning that year’s world championship in a Cooper-Climax.
Though externally similar to the its smaller predecessors, the 2.5 was quite different internally, most notably due to the use of a four-bolt steel main cap design, rather than the cast aluminium, two-bolt system used on earlier engines. The result was an engine that produced 220 bhp in initial trim, rising to nearer 250 bhp in later variants. The engine would be stretched to 2.7 litres for use by Brabham in a Cooper at Indianapolis while a 1.5 litre variant was developed when the Formula One rules switched to that capacity in 1961.
Specialists Crosthwaite and Gardiner, covered elsewhere in this issue for their work with Bugattis, has also carved a niche in the production of Coventry Climax FPF engines. According to owner Ollie Crosthwaite, it began working with the engines because ‘we had a customer in the US that liked good-quality parts for their Climax engines, and he suggested starting to make some new bits. Before we knew it, we had made almost everything.’
The company can now produce entirely new engines of various volumes. ‘We now do the 1.5, 2, 2.5 and 2.7 [litre] engines,’ says Crosthwaite. ‘We have also done one of the later cross-bolted 1.5 litre blocks, and a 2.2. We also do different levels of tune on them – a racy one, and a very racy one.’
The FPE
Coventry Climax decided to enter the race engine market in 1952 following approaches from HMW, Cooper and Connaught at that year’s Motor Show. It started development of the FPE, a 2.5 litre engine intended to suit upcoming rule changes for the 1954 Formula One season. Ultimately, however, the engine would never be used in anger.
Designed by Hassan and Mundy, the FPE was of all alloy construction, with twin overhead cams on each cylinder bank. An interesting feature was that it used the same casting pattern for the cylinder heads, with a ‘front’ cast at both ends of each head, the unused portion machined off later. The engine also had an impressive ‘zero backlash’ gear drive for the camshafts, where the gears were machined, hardened and then ground to very tight tolerances.
Unfortunately, reliability was elusive, with initial problems centering around the valve train, although a number of piston failures were also experienced. It would not be until 1955 that the FPE was running reliably on the dyno, and it certainly made impressive power figures. However, by the time it was nearing being competition ready, the company’s four-cylinder engines were proving popular with racers and the project was sidelined. This was not the end though as in 1966, the development engine was purchased privately, bored out to 3.0 litres, fitted with a Tecalimit Jackson fuel injection system and raced at Silverstone housed in a converted Shannon Formula 3 chassis.
Hinting at the potency of the FPF engines, the 2019 Goodwood Revival featured the sight of the 2.0 litre C&G Climax-engined Lotus 15 of racer Roger Wills out-dragging a 2.5 litre Ferrari Dino down the straight. Crosthwaite explains that there is plenty that can be done to improve performance without falling foul of the regulations. ‘We keep on the legal side,’ he says. ‘The bore and stroke have to be the same [as original], as do the port diameter and valve sizes. But where we make all our power is on the port design and surface finish. Then it’s a case of incremental gains everywhere else.’
Remaking the FPF engines also gave the opportunity to improve areas of
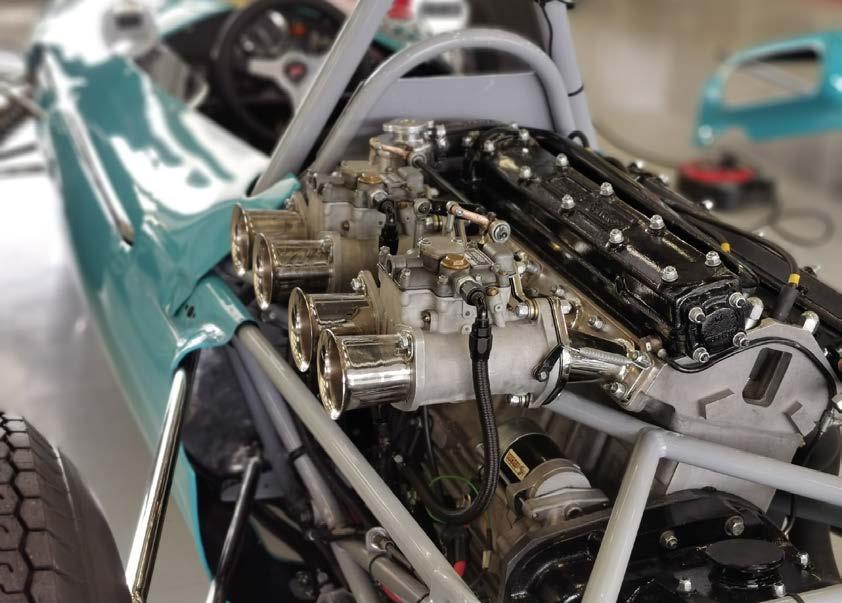
The original 8-cylinder engine was redesigned to a fourcylinder and that was then developed throughout the 1960s in various categories of motor sport
the original that can present reliability issues. For example, Crosthwaite says the crankshafts are a particularly poor design. ‘They were really bad. They were not properly counterweighted and balanced for the weight of the rod and piston, particularly on the 2.5s.’ To address this issue, C&G’s new cranks have dense metal inserts in the counterweights. ‘We did the stress calculations, and the original design puts a load of around 2.5 tons through the centre main bearing. That is why the 2.5s always used to crack at the centre main. It is lots of little things like that which make the difference.’
For the cylinder head development, the company has leveraged computer simulation of the inlet and exhaust pulses to help optimise the port design and cam profiles. ‘It is pretty clever,’ Crosthwaite says. ‘We have run simulations on the cam designs, and everything we simulated we tested back to back on the dyno. It was close enough that our engine builder, who initially thought the simulation wasn’t going to work, had to admit it was pretty good.’
There are also gains to be made by simply making parts more accurately than they were in period. ‘That is a really big thing,’ Crosthwaite remarks. ‘It means things can be assembled more quickly. With some of the parts, if you make them to the original drawings they just don’t fit together. I think it was what they [engineers in the past] called a fitter’s job. They would polish things to size, but
The engine was hard to balance and has even damaged dynos that are capable of managing drag racing engines capable of delivering more than 2000 bhp. Vibration is an engine killer
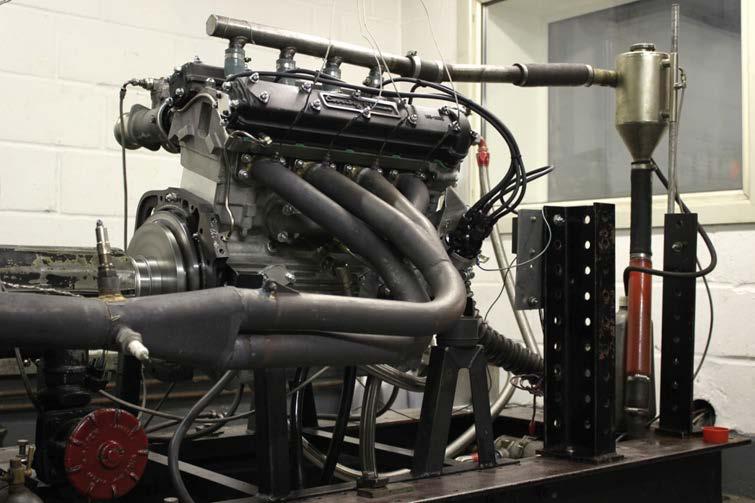
my view is to make things to the right size in the first place. It is a little more expensive to make something to a tighter tolerance, but they go together better. If my customers get parts that won’t fit together, they just moan. It doesn’t matter if they are to factory specs!’
It is testament to the original designs that Coventry Climax engines are capable of producing impressive power even by current standards, and with a dose of modern refinement, they can be raced reliably in historic machinery around the globe.


SUBSCRIPTION OFFER
Save up to 21% with 3 issues of Racecar Engineering for just £13.95
>> Sportscar breakthrough: IMSA racers at Le Mans – see P88 >> Plus! IndyCar cooling secrets revealed – P54

>> BTCC hybrid: UK’s top series embraces new technology – p56
April 2020 • Vol 30 No 4 • www.racecar-engineering.com • UK £5.95 • US $14.50 Dark arts Shining a spotlight on World Rally technology December 2019 • Vol 29 No 12 • www.racecar-engineering.com • UK £5.95 • US $14.50 Corvette C8.R All new mid-engine Le Mans racer breaks cover January 2020 • Vol 30 No 1 • www.racecar-engineering.com • UK £5.95 • US $14.50 Formula 1 2021 What the new rules will mean for teams and fans
F1 CFD study Will the 2021 aero rules really improve the racing? Ferrari 488 Evo Up close and personal with Maranello’s new GT3 car Nissan GT-R LM The inside story of LMP1’s most radical racecar most radical racecar Petrolheads The inside line on Exxon’s GP fuel blending process Hot pants How stricter tests are shaking up the racewear business Can-Am Maverick The tiny UTV racer that’s shaking up the Dakar shaking up the Dakar Formula E goes Extreme We examine the technology behind
December cover_FINAL.indd 1the radical all-electric off-road series
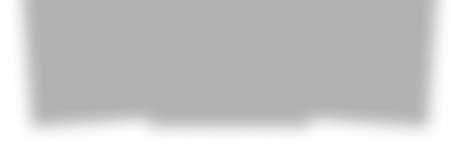
Aerodynamics 101 How wind tunnels work plusinsider tips on using them Japanese Super GT Technical analysis of the 2020 Class 1 GT500 cars
Cover_WRC_Master_REVISED Ford.indd 1 January cover_JD APPROVED_BS.indd 1 26/11/2019 16:43
22/10/2019 14:11
INSIDE EVERY ISSUE
• Unrivalled technical analysis from Formula 1 and Le Mans, to grassroots racing • Written by engineers analysing new products, technical developments, testing and results • Latest news and developments from the major race series across the globe
3GREAT REASONS TO SUBSCRIBE
• You will never miss an issue of this leading source of technical insight and information • Pay less than the shop price, plus FREE delivery to your home • Save up to 21% off the newsstand price FREE worldwide delivery
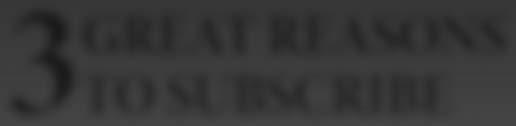
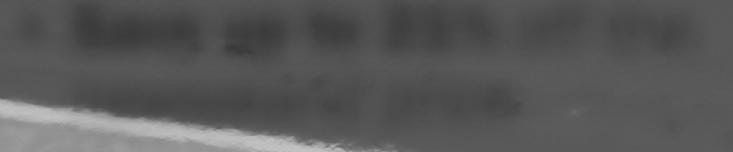
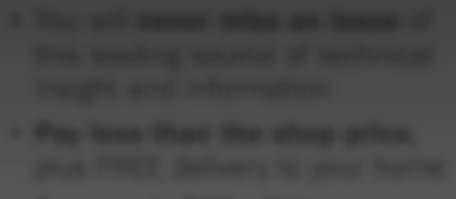


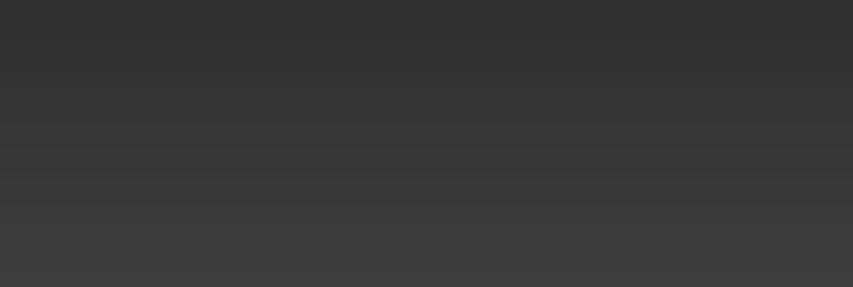
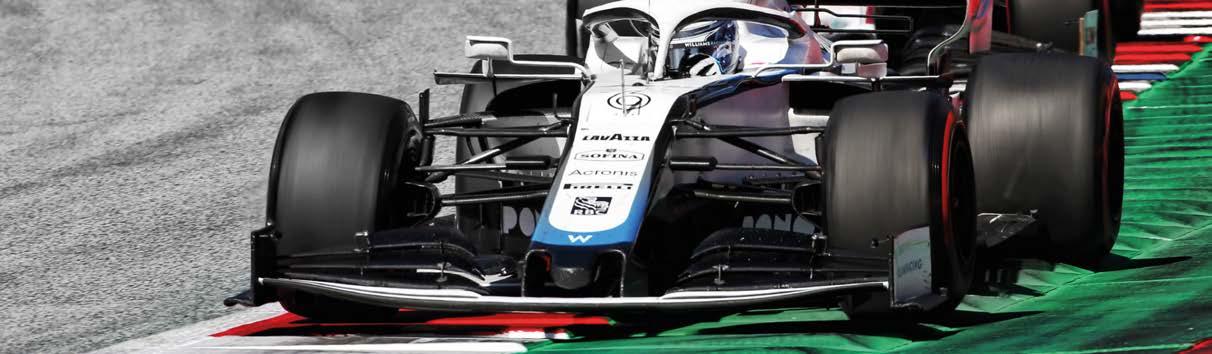

m Phone: +44 (0) 1858 438 443 (quote code CRCG2020) AVAILABLE WORLDWIDE
DIGITAL EDITION ALSO AVAILABLE WORLDWIDE for tablet, smartphone and desktop. To order go to: www.chelseamagazines.com/CRCG2020
>> Plus! IndyCar cooling secrets revealed – P54
January 2020 • Vol 30 No 1 • www.racecar-engineering.com • UK £5.95 • US $14.50 Formula 1 2021 What the new rules will mean for teams and fans