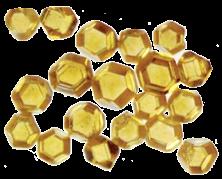
4 minute read
Will the blade be used in a wet cutting or dry cutting application?
Diamonds Metal Matrix
Blade Rotation Blade Rotation
Advertisement
Cutting Edge
MATERIAL BEING CUT
The exposed diamond crystals do the grinding work. The metal matrix or bond holds the diamond in place. Trailing behind each exposed diamond is a bond tail which helps to support the diamond. As the blade rotates through the material, the exposed surface diamonds grind the material.
Exposed Diamond Fracturing and Wearing Away
After several thousand passes through the material, the exposed diamonds begin to crack and fracture. The matrix holding the diamonds also begins to wear away.
Blade Rotation Blade Rotation
Embedded Diamond Cracked Diamond Fragments Are Swept Away
Eventually the diamond completely breaks apart and its fragments are swept away with the material it is grinding. When the blade is cooled with water this material, included with water, produces slurry.
Next Diamond is Exposed and the Cycle Continues
As the old diamonds are fractured and worn away they are replaced by new diamonds and the process continues until the segments are worn down to the core.
#1 Rule for Diamond Blades: Use a Hard Bond to Cut Something Soft and Use a Soft Bond to Cut Something Hard
DIAMOND QUALITY - YOU GET WHAT YOU PAY FOR
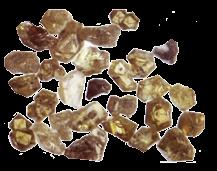
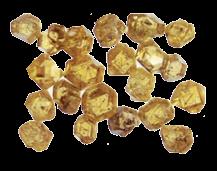
LOW QUALITY
SYNTHETIC DIAMONDS
• Weaker crystals with irregular shape • Shorter life & lower cutting rates • Lower thermal stability • Does not handle steel & hard aggregates well • Jagged points that break causing faster wear & lower cutting & drilling performance • Widely used in low priced dry products
MEDIUM QUALITY
SYNTHETIC DIAMONDS
• Good crystal strength & shape • Good for sawing & drilling applications • Good cutting speed • Handles moderate steel & hard aggregate applications
HIGH QUALITY
SYNTHETIC DIAMONDS
• Strongest crystals • Lasts longer • Withstands high temperatures • Octahedral shape for increased tool life & faster cutting • High impact strength against steel & hard aggregate
TOP 10 REASONS Building Relationships That Last: Why World Diamond Source Offers the Best Value in Diamond Saw Blades
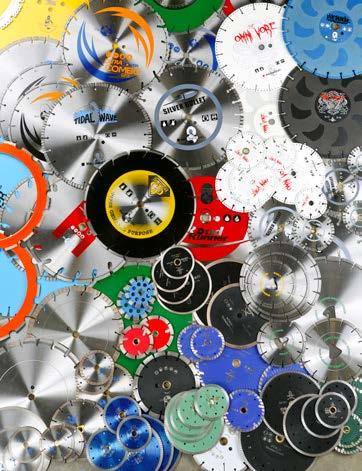
Rising from the humble origins of a small rented office nearly 20 years ago, familyowned and operated World Diamond Source (WDS) is now the industry leader for factory-direct diamond saw blades, core bits, concrete polishing tools, and all other types of diamond tooling. Here are 10 reasons why WDS is the contractors’ go-to supplier:
1. Higher Quality = More Value. Performanceminded contractors always look at the cost per cut from their diamond blade. Buying strictly on dollars alone is a false economy. They know it makes no sense to buy 10 $100 tools when three $250 tools can get the same job done at 25 percent savings. 2. Factory Direct Pricing. WDS built its business by offering factory-direct savings, cutting overhead on the industry’s most comprehensive selection of blades. No one offers a better combination value, service, trust, and savings as WDS. 3. Platinum-Level Customer Service. Contact WDS and you’re in touch with a trusted diamond tooling advisor with the expertise you need to get maximum value from your diamond tooling purchase. What are you cutting? What’s the task? Our people take the time to understand your needs, offering you the best values in the market. 4. Licensed, Insured Supplier. Why bet your project safety and performance on a questionable supplier? For nearly 20 years, WDS has reduced the cutting costs of more than 25,000 contractors, from sole proprietors to the industry’s largest commercial businesses. “Building relationships that last” is more than a WDS company motto. It’s how we earn your business. 5. “The Proof Is in the Pudding.” Put a WDS blade on your saw for 30 days at our risk. If the WDS blade kicks butt, all we ask is you pay for the blade. It’s our way of proving ourselves in the only test that matters, your jobsite. Who else invites you to try before you buy? 6. “OMG” Inventory and Delivery Speed. Why expose your project to needless downtime? The WDS warehouse is packed with nearly $4 million in blades and surface preparation tooling. 7. Continuous, Relentless R&D. WDS’s research and development program is led by the man that also runs WDS, Cliff Maddock. As a familyowned and operated business, Maddock is able to innovate and respond to industry trends on the fly, providing WDS customers with the latest, highest-performing blade technology across all cutting categories. 8. Our Manufacturing Processes. Anyone can copy a WDS blade design. But no one outside of WDS understands the manufacturing process that went into forming that blade. That proprietary process of manufacturing and bonding is a closely-guarded method that differentiates WDS blade performance from poorperforming knock-offs. 9. FREE Catalog. Request your complimentary 116-page copy of the diamond blade cutter’s “industry bible.” Or view it now online at worlddiamondsource.com. The WDS website is the easy, informative way to order the blades you need. 10. Surface Grinding & Polishing Headquarters. If your task is surface preparation requiring metal bond tooling, backing pads, diamond fiber pads, resin polishing pads, resin polishing pads for hand-held and walk-behind machines, and other materials, count on WDS as your one-stop source.
For more information:
Website WorldDiamondSource.com Phone 800.611.8278
Produced by Hanley Wood Strategic Marketing Services Group sms.hanleywood.com