
5 minute read
STEP-BY-STEP
How to create seamless joins in Apollo Slab Tech
Supplied by Sheridan, Apollo Slab Tech is a full-bodied solid surface material, which is selfsupporting in 20mm or 30mm thicknesses. Like other solid surface materials, it is non-porous, hygienic, easy to maintain, and capable of seamless joins. What sets it apart is that Apollo Slab Tech is not backed by a chipboard core. This means installers can create cutouts, edge details, and curves on-site without the need for edging strips.
Advertisement
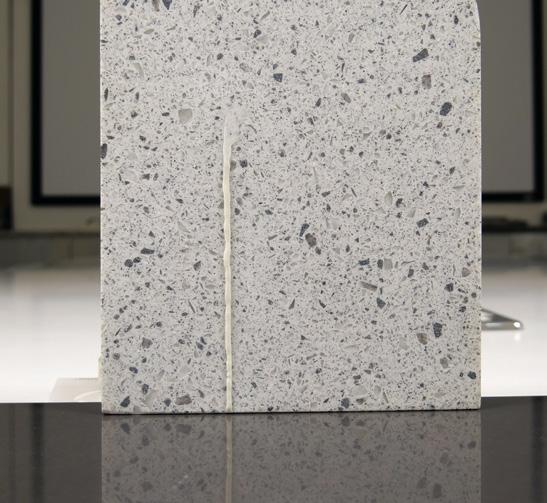
Apollo Slab Tech is available as either a bespoke, made to measure product; or for the more budget conscious or DIY oriented, as modular sections. These modular sections include worktops up to 3m in length and breakfast bars at 900mm wide, as well as splashbacks and upstands. Worktops can also be supplied with integrated sinks in solid surface or Stainless Steel; or simply with the cutouts already precision engineered to specification in a standard worktop size.
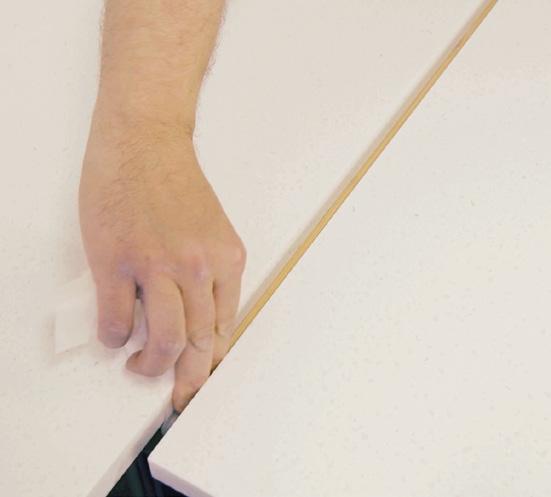
1. Tools Required • Apollo Slab Tech Installation Kit • Random orbital sander plus dust extraction equipment. • Hand router: minimum of 1850W with ½”/12.7mm Colet size. • Straight Trimming Router Cutter (with a guide bearing). • Wide Chisel (minimum 1”/25mm) • Electric saw – with fine tooth blades. • Silicon/ Caulk Gun
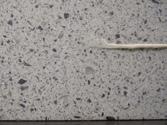

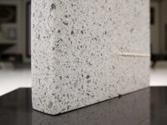

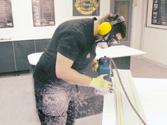

2. Preparation Most kitchens will usually have at least one joint for a corner, or an extended length of worktop. To prepare these joints, use a router fitted with a straight Tungsten Carbide cutter and a long Straight Edge. Position the Straight Edge so the router cutter will skim off about 0.5mm from the faces of each adjoining piece cleanly.
After you have prepared each piece, assemble the joint dry (without adhesive) to ensure the seams are parallel, with no gaps showing, and that the two pieces are level. Once you are happy with the result, clean each face with an alcohol wipe.
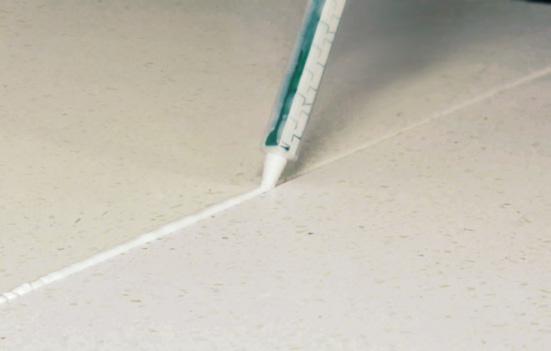
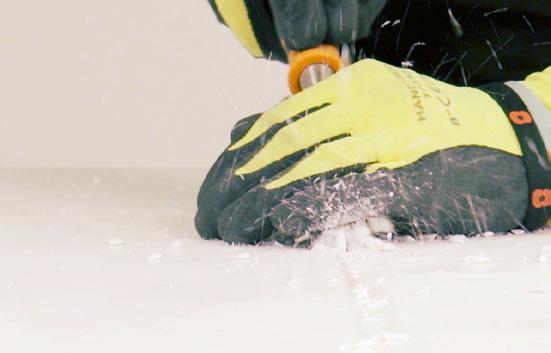

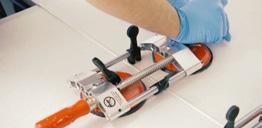
3. Bonding the Joints Ensure your work area is dust free, and place your worktops as close to their final installed position as possible. Apply a bead of Apollo Magna glue to the faces of the join at the top and bottom edges and centerline, then push the two sections together, leaving a 2mm gap.
Apply Masking tape to the underside to prevent dripping, then apply a continuous bead of glue to the join to fill the gap. To close this gap, use G-Clamps, or suction cups to apply lateral pressure, checking to ensure correct alignment. Once clamped, a continuous bead of glue should be ejected from the joint.
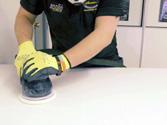
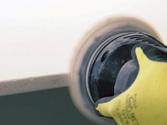
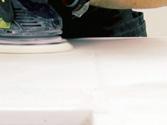
4. Finishing the Joints The glue will cure after around 30-40 minutes. After this has taken place, remove the G-clamps, then using a wide, sharp chisel, remove the glue deposits, keeping the chisel flat to avoid digging into the surface.
To finish the joint, use a random orbital sander with sandpaper pads to refine the surface gradually up to a factory-finish of 240 grit, blending approximately 600mm beyond the seam area while continually moving.
Finish this process with the abrasive pads provided for a smooth, refined result.

www.sheridan-uk.com