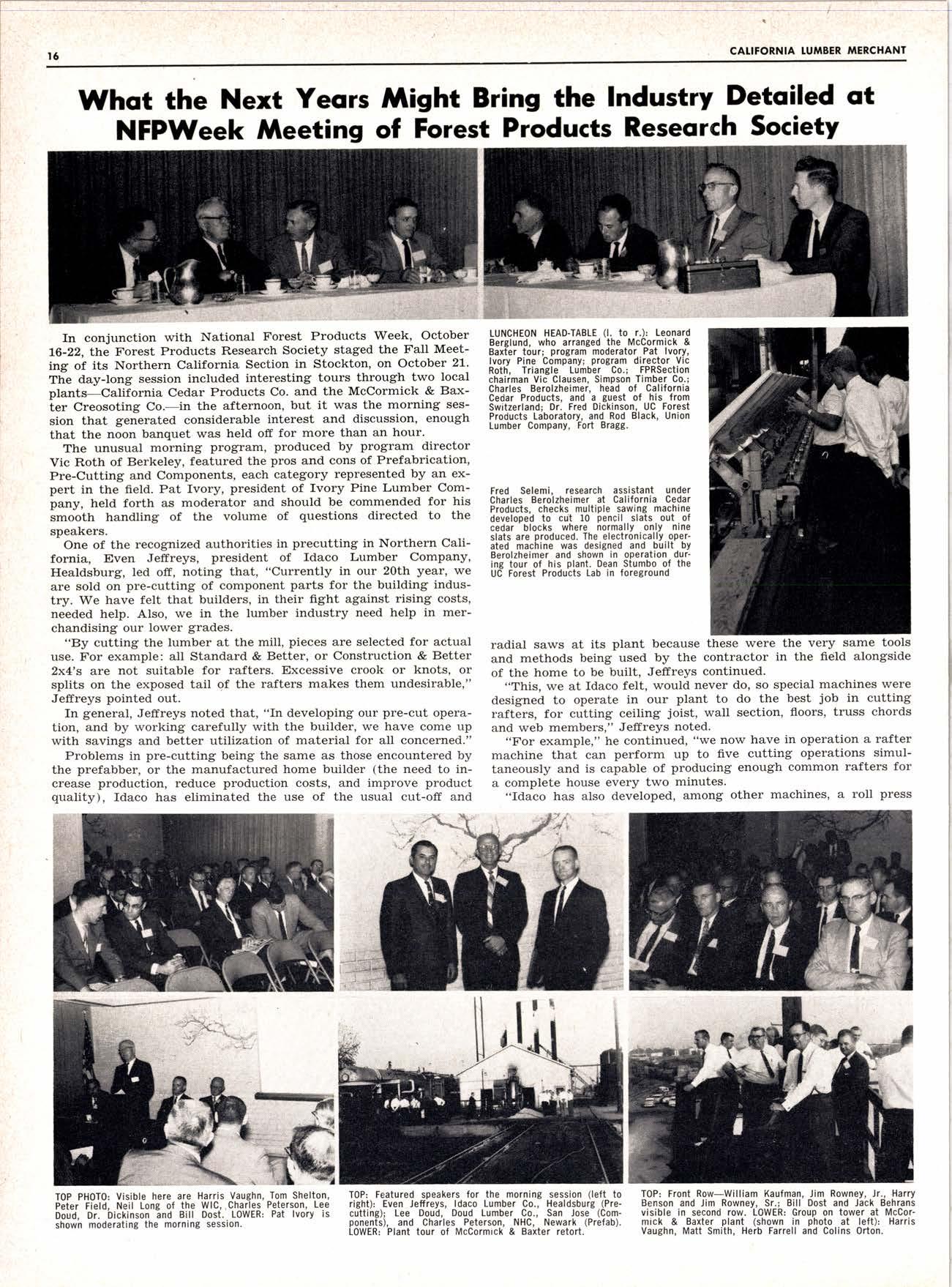
6 minute read
Whqt the Next Yeors Xtight Bring the Industry Detoiled ot NFPWeek lf,eeting of Forest Products Reseqrch Society
In conjunction with National Forest Products Week, October t6-22, ttre F orest Products Research Society staged the Fall Meeting of its Northern California Section in Stockton, on October 21. Tlie day-long session included interesting tours through two local plants-California Cedar Products Co. and the McCormick & Baxter Creosoting Co.-in the afternoon, but it was the morning session that generated considerable interest and discussion, enough that the noon banquet was held off for more than an hour.
The unusual morning program, produced by program director Vic Roth of Berkeley, featured the pros and cons of Prefabrication' Pre-Cutting and Components, each category represented by an expert in the field. Pat Ivory, president of Ivory Pine Lumber Company, held forth as moderator and should be commended for his smooth handling of the volume of questions directed to the speakers.
One of the recognized authorities in precutting in Northern California, Even Jeffreys, president of Idaco Lumber Company' Healdsburg, led off, noting that, "Currently in our 20th year, we are sold on pre-cutting of component parts for the building industry. We have felt that builders, in their fight against risinS: costs, needed help. Also, we in the lumber industry need help in merchandising our lower grades.
"By cutting the lumber at the mill, pieces are selected for actual use. For example: all Standard & Better, or Construction & Better 2x4's are not suitable for rafters. Excessive crook or knots, or splits on the exposed tail of the rafters makes them undesirable," Jeffreys pointed out.
In general, Jeffreys noted that, "In developing our pre-cut operation, and by working carefully with the builder, we have come up with saving:s and better utilization of material for all concerned."
Problems in pre-cutting being the same as those encountered by the prefabber, or the manufactured home builder (the need to increase production, reduce production costs, and improve product quality), Idaco has eliminated the use of the usual cut-off and radial saws at its plant because these were the very same tools and methods being used by the contractor in the field alongside of the home to be built, Jeffreys continued.
"This, we at Idaco felt, would never do, so special machines were designed to operate in our plant to do the best job in cutting rafters, for cutting ceiling joist, wall section, floors, truss chords and members," JeffreYs noted.
"For example," he continued, "we now have in operation a rafter machine that can perform up to five cutting operations simultaneously and is capable of producing'enough common rafters for a complete house every two minutes.
"Idaco has also developed, among other machines, a roll press for the manufacture of metal 'Gri-P-Late' truss. This machine consists of two heavy rolls and acts like a giant wringer that squeezes the connecter plates into the wood member of the truss.
"A survey of manufacturers and pre-fabricators was made in 1959, and we found that in most plants and factories throughout the country the old hand tools similar to those used in the field were still being used in the plants. Idaco Engineering Company, of Oakland, is now manufacturing specialized pre-cutting machinery and I am happy and proud to say that we, right out here on the West Coast, have been able to lead the field and are now shipping this equipment all over the U.S. and Canada," Jeffreys concluded.
Questions from the floor included: "What is your advantage over prefabrication?" (Answer: "Flexibility. Prefabricated wall panels require very close measurement tolerances; foundation and subfloor must be exactly right. Another advantage is transportation. Compare costs of trucking 'solid' load of precut materials to that of a load of panels and 'air'.")
"What is the least amount of homes you can cut economically?"
(Answer: "We can cut one home very satisfactorily.")
"What would I, as a builder, have to pay extra to have you cut one home?" (Answer: "We will do all the pre-cutting on an average 1200 sq. ft. home for approximately 950.00.")
Next "at bat," and covering the field of components, was enterprising San Jose dealer, Lee Doud, head of Doud Lumber Company. Although Dealer Doud acknowledged that "for the retail dealer, components are a real rough go," he noted that if the dealer can control the design of any given job, he can, and will be suecessful in the field.
"F or the component manufacturers," Doud continued, "design is everything. This we have Iearned the hard way. Without desigrr you have nothing. F or if the component has to be manufactured to a special design the economics (i.e.: interchangeability of panels) are lost. We wish to control the design of the components, but not the building in which it is used.
"The architect, the engineer, the draftsmen should be responsible for their desig:ns and use the components effectively and economically," Doud exclaimed. "Ilowever, as for houses, the architect and draftsman seem very reluctant to learn or to use house components-and it seems that when they do desigrr for components in a house, somewhere along the line they mis-cue and cause a lack of economic continuity.
"Because of this, we feel we are forced to go into the field of design. Our design department will specialize on house components only. When a contractor wishes to build a home with the components, we take his ideas of a floor plan and house size, convert it into components and give him a package price. Where we really differ from the manufactured home is in the offering of studless interior partitions instead of a wood pre-fabbed interior," Doud said.
Doud, also active in commercial and industrial building, went on to discuss various new components, including Glu-Lam beams, plywood box beams, the plylvood Vaulted Arch, Troff-Deck and the Stress Skin Panel.
The latter (stressed skin panel), Doud noted, "ReaUy intrigues me. It could be, and probably will be, a tremendous component in home building. It's got everything and can be used in a variety (Continued on Page 82)
SUMMARY OF FIRST NATIONAL HONOLULU, HAWAII
HONOIUIU
HOO-HOO CIUB | 42 P.C). Box 3829 Honolulu, Howqii
A. Proclamation
1. Mayor Neal S. Blaisdell proclaimed NFPW on October 11, 1960.

B. Promotion
1. 500 Ribbons: Forest Green with black lettering 2,.x6" ,,National Forest Products Week, October 76-22; Wood-your Best Buy, Honolulu Hoo-Hdo Club-142', with Hoo-Hoo insignia-worn by all people in wood products and by clerks in lumber yards and stores.
2. 1000 Bumper Stickers: "Lumber-Your Best Buy" distributed and in use on all company rolling equipment, trucks, carriers, pick-ups, etc. as well as individuals automobiles.
3. 200 Natlonal Forest Products Week Bumper Stlckers distributed and used.
4. 1000 "Our Daddy l5 s, Irrrmb,elman" booklets distributed to Department of Public Instruction and sent to architects' children. Also distributed at Lewers & Cooke's Open House for school children.
5. "Western Beolpes" booklet sent to the wives of 1b0 architects and specification writers.
6. Seven wood products Exhiblts on display in downtown store windows or other places of heavy foot tra.ffic. Best exhibit was judged by local Architect and art teacher and won by Midpac Lumber Co., a perpetual trophy of a black cat will be given.
7. One lumber dealer, Lewers & Cooke, Ltd., held Open House all week for school children and the turnout was good.
8. Many hundred copies of litorature was sent to architects and individuals. "Livability Unlimited" was mailed to requests from newspaper ad.
Advertising
1. The two leading newspapers carried 680 inches of paid advertising in the Sunday, October 16, issue. Several lumber dealers had r/z-page ads. The millwork dealers, large and small, also carried ads. Each ad had a "Salute to National Forest Products Week', in it and the slogan, "There's nothing in the World like wooD."
Publicity
1. Along with the newspaper supplements one newspaper, "THE HONOLULU ADVERTISER," ran 144 inches of news stories with photographs. The "HONOLULU STAR-BULLETIN" ran 55 inches of news stories. The news stories were different for each newspaper and they varied from local news to NLMA news release material.
2. At least three radio stations used news stories.
3. One television station ran the Lewers & Cooke open house on its nightly news broadcast showing school children going through the lumber yard.
E. Miscellaneous
1. Honolulu lfoo-Hoo Club No. 142 held a meeting and Concat on October 20 and initiated 10 new members.
NATIONAL F'OREST PRODUCTS WEEK 1961-Suggestions for a better week:
1. Get started by July 1st.
2. Committee should be made up of at least g members and each one assigrred a definite responsibility. One meeting should be held in July, two meeting:s in August and weekly meetings in September and up until the "Week."
3. Things to do that were not done in 1960:
A. Governor's proclamation.
B. Have NF'PW float in Aloha Week parade.
C. Television and radio interviews.
D. Speakers for service clubs (must plan for these in July or sooner.)
E. Every company must exhibit or be fined.
F. Hold NF"PW luau for architects.
G. More "Open Houses."
H. Include outlying islands in "Week."