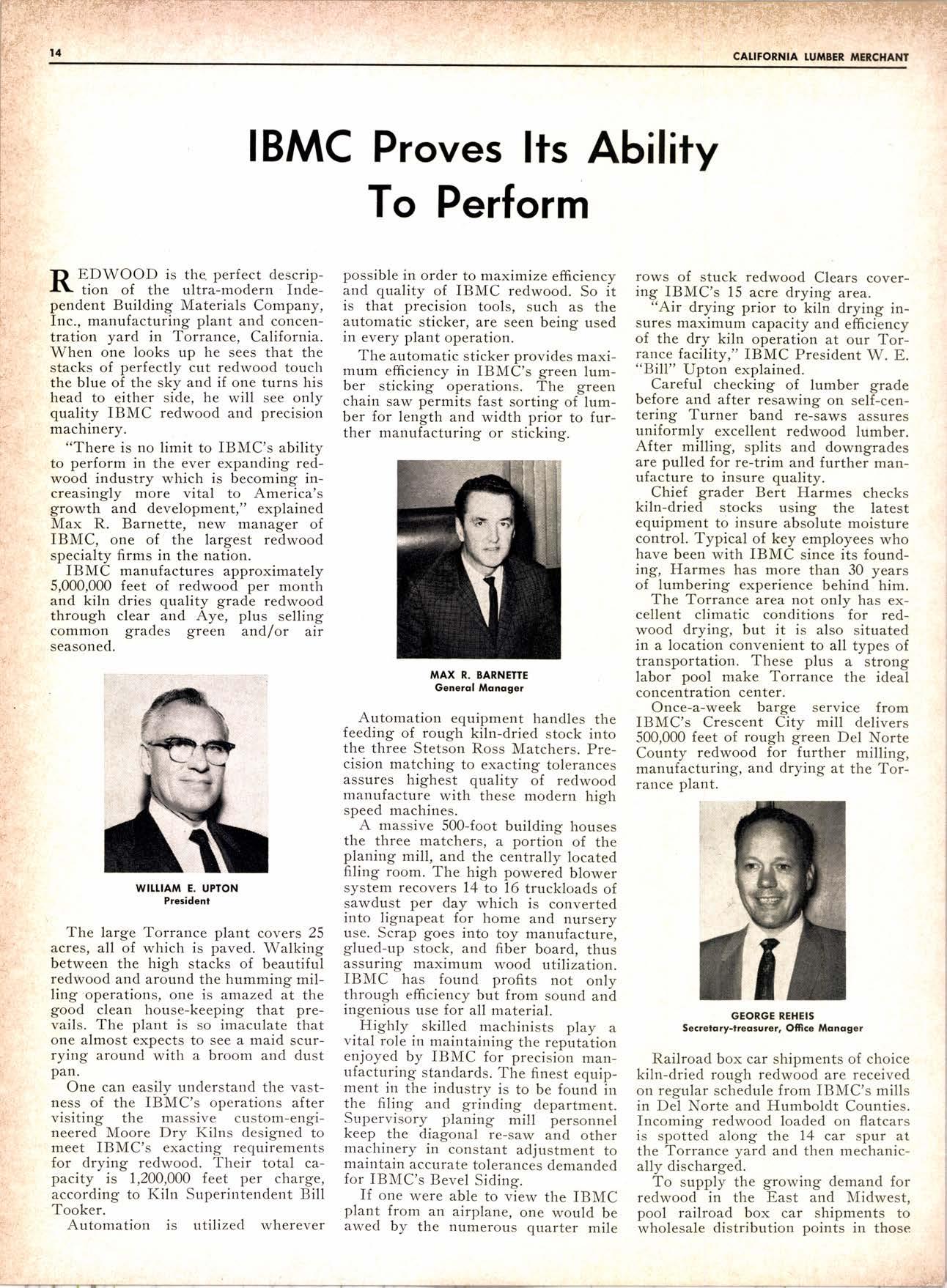
4 minute read
IBMC Proves lts Ability To Perform
D) EDWOOD is the perfect descrip- r\ tion of the ultra-modern Independent Building Materials Company, Inc., manufacturing plant and concentration yard in Torrance, California. When one looks up he sees that the stacks of perfectly cut redwood touch the blue of the sky and if one turns his head to either side, he will see only quality IBMC redwood and precision machinery.
"There is no limit to IBMC's ability to perform in the ever expanding redwood industry which is becoming increasingly more vital to America's growth and development," explained Max R. Barnette, new manager of IBMC, one of the largest redwood specialty firms in the nation.
IBMC manufactures approximately 5,000,000 feet of redwood per month and kiln dries quality grade redwood through clear and Aye, plus selling common grades green andf or air seasoned.
possible in order to maximize efficiency and quality of IBMC redwood. So it is that precision tools, such as the automatic sticker, are seen being used in every plant operation.
The automatic sticker provides maximum efficiency in IBMC's green lumber sticking operations. The green chain saw permits fast sorting of lumber for length and width prior to further manufacturing or sticking.
rows of stuck redwood Clears covering IBMC's 15 acre drying area.
"Air drying prior to kiln dry-ing insures maximum capacity and efficiency of the dry kiln operation at our Toirance facility," IBMC President W. E. "Bill" Upton explained.
Careful checking of lumber grade before and after resawing on self-centering Turner band re-saws assures uniformly excellent redwood lumber. After milling, splits and downgrades are pulled for re-trim and further manufacture to insure quality.
Chief grader Bert llarmes checks kiln-dried stocks using the latest equipment to insure absolute moisture control. Typical of key employees who have been with IBMC since its founding, Harmes has more than 30 years of lumbering experience behind him.
The Torrance area not only has excellent climatic conditions for redwood dryingi, but it is also situated in a location convenient to all types of transportation. These plus a strong labor pool make Torrance the ideal concentration center.
The large Torrance plant covers 25 acres, all of which is paved. Walking between the high stacks of beautiful redwood and around the humming milling operations, one is amazed at the good clean house-keeping that prevails. The plant is so imaculate that one almost expects to see a maid scurrying around with a broom and dust pan.
One can easily understand the vastness of the IBMC's ooerations after visiting the massive- custom-engineered Moore Dry Kilns designed to meet IBMC's exacting requirements for drying redwood. Their total capacity is 1,200,000 feet per charge, according to Kiln Superintendent Bill Tooker.
Automation equipment handles the feeding of rough kiln-dried stock into the three Stetson Ross Matchers. Precision matching to exacting tolerances assures highest quality of redwood manufacture with these modern high speed machines.
A massive 500-foot building houses the three matchers, a portion of the planing mill, and the centrally located filing room. The high powered blower system recovers 14 to 16 truckloads of sawdust per day which is converted into lignapeat for home and nursery use. Scrap goes into toy manufacture, glued-up stock, and fiber_ board, thus assuring maximum wood utilization. IB],IC has found profits not only through efficiency bu1 from sound and ingenious use for all material.
Highly skilled machinists play a vital role in maintaining the reputation enjoyed by IBMC for precision manufacturing standards. The finest equipment in the industry is to be found in the filing and grinding department. Supervisory planing mill personnel keep the diagonal ie-saw and other machinery in constant adjustment to maintain accurate tolerances demanded for IBMC's Bevel Siding.
If one were able to vlew the IBMC plant from an airplane, one would be awed by the numerous quarter mile
Once-a-week barge service from IBMC's Crescent City mill delivers 500,000 feet of rough green Del Norte County redwood for further milling, manuf-acturing, and drying at the Toirance plant.
Railroad box car shipments of choice kiln-dried rough redwood are received on regular schedule from IBMC's mills in Del Norte and Humboldt Counties. Incoming redwood loaded on flatcars is spotted along the 14 car spur at the Torrance yard and then mechanically discharged.
To supply the growing demand for redwood in the East and Midwest, pool railroad box car shipments to wholesale distribution points in those areas averag'e 100,000 feet per day, adding up to 50 to 60 cars per month. IBMC traffic service insures the fast- est routing at lowest cost to the customer.
Some 15 company-owned Peterbuilt diesel trucks and trailers insure prompt delivery of IBMC quality redwood lumber to the California market as well as those in Nevada, Arizona, New Mexico, and West Texas.
Max R. Barnette recently became manager of IBMC and with him came the policy of progress, efficiency, expansion, and quality. He is no stranger to the industry in Southern California for it was in this area that he gained his vast lumber experience before going to Ukiah where he formerly headed Hollow Tree Redwood Company as president and general manager.
Sitting in the president's chair is W. tr. "Bill" Upton, a true pioneer in the lumber industrv who olans for the future as can be-observed at ultramodern IBMC.
(Conti.nued, on Page 34) fop row, from left: rhis volley ore cuslom engineered by the Moore Dry Kiln Compony to meet IBMC's exocting requiremenls for drying redwood. Righf: rhis slicker maximizes the efiiciency of the green lumber sficking opelotion.
Second row, from left: rhis SoQ-foor building houses three Stetson Ross motchers, o pottion of the ploning mill and fhe centrolly locored filing room. l/liddle: rhis high-powered hopper system recovers 14 to I5 truckloods of sqwdust per doy which is converted into lignopeot for home ond nursery use, Righl: onother lood of redwood from the oulomqtic sticker obout to be siqcked owoiiing shipment.

Third row, from left: no one could possibly miss the proud nome of the lirm writlen on the side of rhe dry kiln building. Middle: rhe modern ond ollrqctive mill ofiice. Right: roilrood box cor pool shipments to Eostern ond Midwestern wholesole distribution poinls overoge l00'000 feet per doy.
Bottom row, from left: bonded rough green uppers are obouf to be mechonicolly unlooded from fiof cors sPolted olong the l4-cor spur trock. Middle: unlooded box cor shipmants of choice kiln-dried rough redwood from IBMC mills in Del Norte ond Humboldl counlies. Right: note lhe immoculoie IBMC yord.