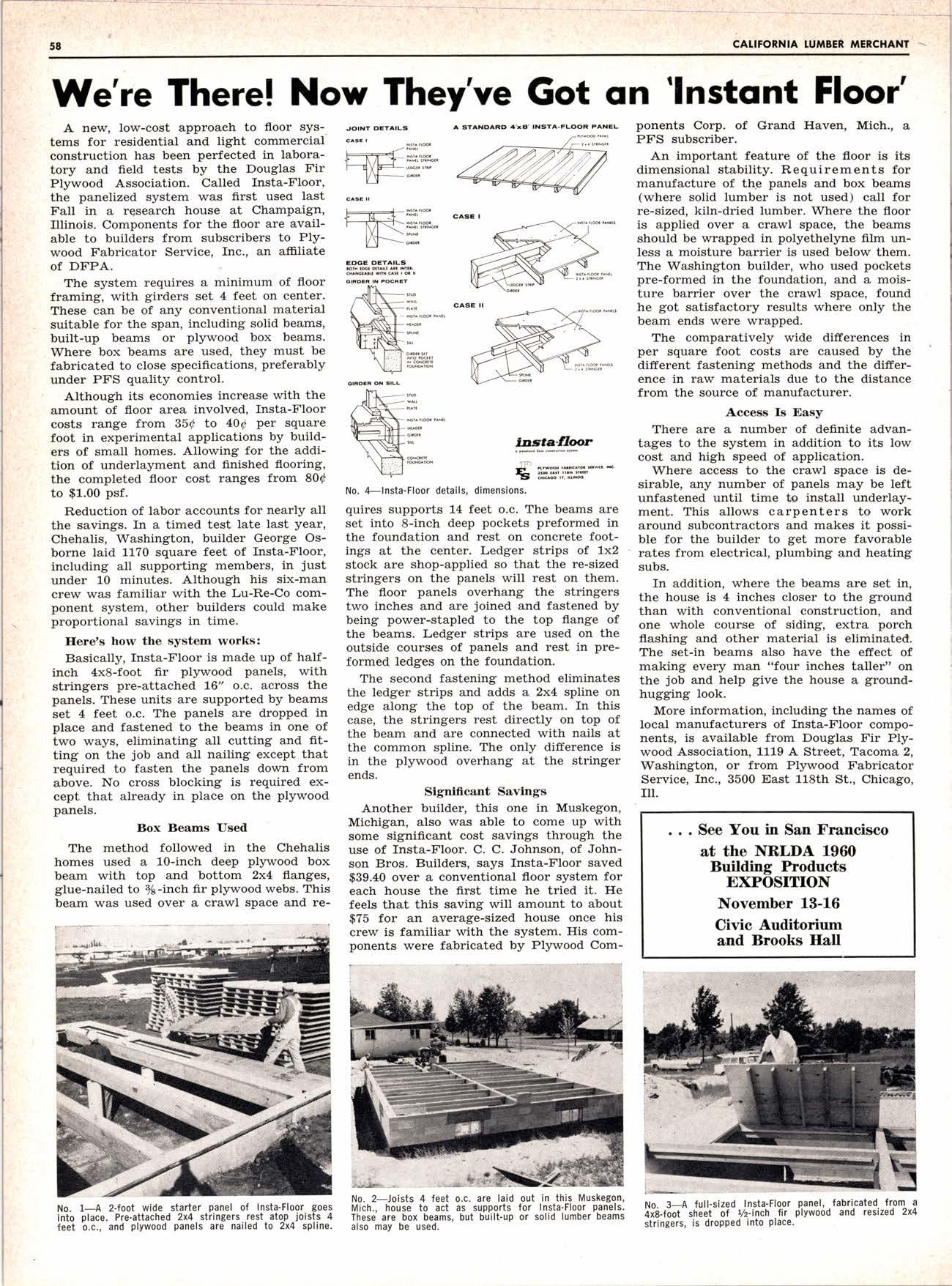
3 minute read
We're Theref Now They've Got on 'lnstont Floor'
A new, low-cost approaeh to floor systems for residential and light commercial construction has been perfected in laboratory and field tests by the Douglas Fir P\rwood Association. Called Insta-Floor, the panelized system was first useo last Fall in a research house at Champaign, Illinois. Components for the floor are available to builders from subscribers to Plywood F abricator Service, Inc., an affiliate of DFPA.
The system requires a minimum of floor framing, with girders set 4 feet on center. These can be of any conventional material suitable for the span, including solid beams, built-up beams or plywood box beams. Where box beams are used, they must be fabricated to close specifications, preferably under PFS quality control.
Although its economies increase with the amount of floor area involved, Insta-Floor costs range from 35d to 4OA per square foot in experimental applications by builders of small homes. Allowing for the addition of underla5rment and flnished flooring, the completed floor cost ranges from 80d to $1.00 psf.
Reduction of labor accounts for nearly all the savings. In a timed test late last year, Chehalis, Washington, builder George Osborne laid 1170 square feet of Insta-F'loor, including all supporting members, in just under 10 minutes. Although his six-man crew was familiar with the Lu-Re-Co component system, other builders could make proportional savings in time.
Ilore's how the system works:
Basically, fnsta-Floor is made up of halfinch 4x8-foot fir plywood panels, with stringers pre-attached 16" o.c. across the panels. These units are supported by beams set 4 feet o.c. The panels are dropped in place and fastened to the beams in one of two ways, eliminating all cutting and fitting on the job and all nailing except that required to fasten the panels down from above. No cross blocking is required except that already in place on the plywood panels.
Box Beams Used
The method followed in the Chehalis homes used a 10-inch deep plywood box beam with top and bottom 2x4 flanges, glue-nailed to ft-inch fir plywood webs. This beam was used over a crawl space and re-
No, 4-lnsta-Floor details, dimensions. quires supports 14 feet o.c, The beams are set into S-inch deep pockets preformed in the foundation and rest on concrete footings at the center. Ledger strips of 1x2 stock are shop-applied so that the re-sized stringers on the panels will rest on them. The floor panels overhang the stringers two inches and are joined and fastened by being power-stapled to the top flange of the beams. Ledger strips are used on the outside courses of panels and rest in preformed ledges on the foundation.
The second fastening method eliminates the ledger strips and adds a 2x4 spline on edge along the top of the beam. In this case, the stringers rest directly on top of the beam and are connected with nails at the common spline. The only difference is in the plywood overhang at the stringer ends.
Stplfica^nt Savlngs
Another builder, this one in Muskegon, Michigan, also was able to come up with some significant cost savings through the use of fnsta-Floor. C. C. Johnson, of Johnson Bros. Builders, says fnsta-F'loor saved $39.40 over a conventional floor system for each house the first time he tried it. He feels that this saving will amount to about $75 for an averag:e-sized house once his crew is familiar with the system. His components were fabricated by Plywood Com- ponents Corp. of Grand Haven, Mich., a Pf,'S subscriber.
An important feature of the floor is its dimensional stability. Requirements for manufacture of thp panels and box beams (where solid lumber is not used) call for re-sized, kiln-dried lumber. Where the floor is applied over a crawl space, the beams should be wrapped in polyethelyne filrn unless a moisture barrier is used below them. The Washington builder, who used pockets pre-formed in the foundation, and a moisture barrier over the crawl space, found he got satisfactory results where only the beam ends were wrapped.
The comparatively wide differences in per square foot costs are caused by the different fastening methods and the difference in raw materials due to the distance from the source of manufacturer.
Access Is Easy
There are a number of definite advantages to the system in addition to its low cost and high speed of application.
Where access to the crawl space is desirable, any number of panels may be left unfastened until time to install underlayment. This allows carpenters to work around subcontractors and makes it possible for the builder to get more favorable rates from electrical, plumbing and heating subs.
In addition, where the beams are set in, the house is 4 inches closer to the ground than with conventional construction, and one whole course of siding, extra porch flashing and other material is eliminated. T'he set-in beams also have the effect of making every man "four inches taller" on the job and help give the house a groundhugging look.
More information, including the names of local manufacturers of Insta-Floor components, is available from Douglas F ir Plywood Association, 1119 A Street, Tacorna 2, Washington, or from PlJrwood F abricator Service, Inc., 3500 East 118th St., Chicago, ilI. See
November