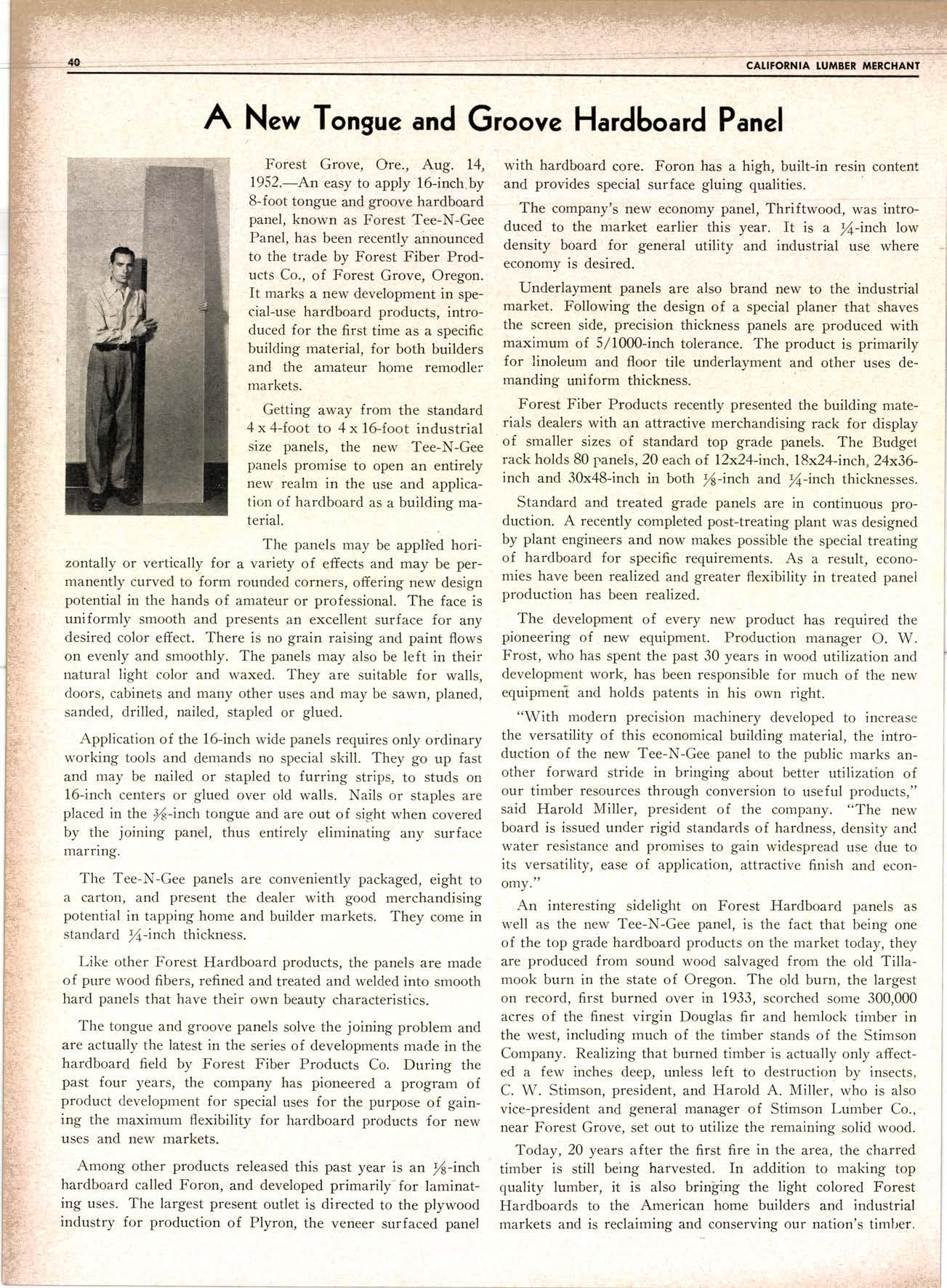
3 minute read
A New Tongue and Groove Hardboard Panel
Forest Grove, Ore., Aug. 14, 1952.-An easy to apply lGinch.by 8-foot tongue and groove hardboard panel, known as Forest Tee-N-Gee Panel, has been recently airnounced to the trade by Forest Fiber Products Co., of Forest Grove, Oregon. It marks a new development in special-use hardboard products, introduced for the first time as a specific building material, for both builders and the amateur home remodler markets.
Getting away from the standard 4 x 4-foot to 4 x lGfoot industrial size panels, the new Tee-N-Gee panels promise to open an entirely new realm in the use and application of hardboard as a building material.
The panels may be applled horizontally or vertically for a variety of effects and may be permanently curved to form rounded corners, offering new design potential in the hands of amateur or professional. The face is uniformly smooth and presents an excellent surface for any desired color effect. There is no grain raising and paint flows on evenly and smoothly. The panels may also be left in their natural light color and waxed. They are suitable for walls, doors, cabinets and many other uses and may be sawn, planed, sanded, drilled, nailed, stapled or glued.
Application of the lGinch wide panels requires only ordinary working tools and demands no special skill. They go up fast and may be nailed or stapled to furring strips, to studs on 16-inch centers or glued over old walls. Nails or staples are placed inthe sfi-inch tongue and are out of sight when covered by the joining panel, thus entirely eliminating any surface marring.
The Tee-N-Gee panels are conveniently packaged, eight to a carton, and present the dealer with good merchandising potential in tapping home and builder markets. They come in standard t/a-inch thickness.
Like other Forest Hardboard products, the panels are made of pure wood fibers, refined and treated and welded into smooth hard panels that have their own beauty characteristics.
The tongue and groove panels solve the joining problem and are actually the latest in the series of developments made in the hardboard field by Forest Fiber Products Co. During the past four years, the company has pioneered a program of product developrnent for special uses for the purpose of gaining the maximum flexibility for hardboard products for new uses and new markets.
Among other products released this past year is an r/s-inch hardboard called Foron, and developed primarily for laminating uses. The largest present outlet is directed to the plywood industry for production of Plyron, the veneer surfaced panel with hardboard core. Foron has a high, built-in resin content and provides special surface gluing qualities.
The company's new economy panel, Thriftwood, was introduced to the market earlier this year. It is a r/a-inch low density board for general utility and industrial use where economy is desired.
Underlayment panels are also brand new to the industrial market. Following the design of a special planer that shaves the screen side, precision thickness panels are produced with maximum of 5/1000-inch tolerance. The product is primarily for linoleum and floor tile underlayment and other uses demanding uniform thickness.
Forest Fiber Products recently presented the building materials dealers with an attractive merchandising rack for display of smaller sizes of standard top grade panels. The Budget rack holds 80 panels, 2O each of lZx24-inch, 18x24-inch,24x36inch and 30x48-inch in both r/s-inch and r/a-inch thicknesses.
Standard and treated grade panels are in continuous production. A recently completed post-treating plant was designed by plant engineers and now makes possible the special treating of hardboard for specific requirements. As a result, economies have been realized and greater flexibility in treated panel production has been realized.
The development of every new product has required the pioneering of new equipment. Production manager O. W. Frost, who has spent the past 30 years in wood utilization and development work, has been responsible for much of the new equipmeni and holds patents in his own right.
"With modern precision machinery developed to increase the versatility of this economical building material, the introduction of the new Tee-N-Gee panel to the public marks another forward stride in bringing about better utilization of our timber resources through conversion to useful products," said Harold Miller, president of the company. "The new board is issued under rigid standards of hardness, density anC water resistance and promises to gain widespread use due to its versatility, ease of application, attractive finish and economy."
An interesting sidelight on Forest Hardboard panels as well as the new Tee-N-Gee panel, is the fact that being one of the top grade hardboard products on the market today, they are produced from sound wood salvaged from the old Tillamook burn in the state of Oregon. The old burn, the largest on record, first burned over in 1933, scorched some 300,000 acres of the finest virgin Douglas fir and hemlock timber in the west, including much of the timber stands of the Stimson Company. Realizing that burned timber is actually only affected a few inches deep, unless left to destruction by insects, C. W. Stimson, president, and Harold A. Miller, who is also vice-president and general manager of Stimson Lumber Co., near Forest Grove, set out to utilize the remaining solid wood.
Today, 20 years after the first fire in the area, the charred timber is still being harvested. In addition to making top quality lumber, it is also brinling the light colored Forest Hardboards to the American home builders and industrial markets and is reclaiming and conserving our nation's timl-rer.
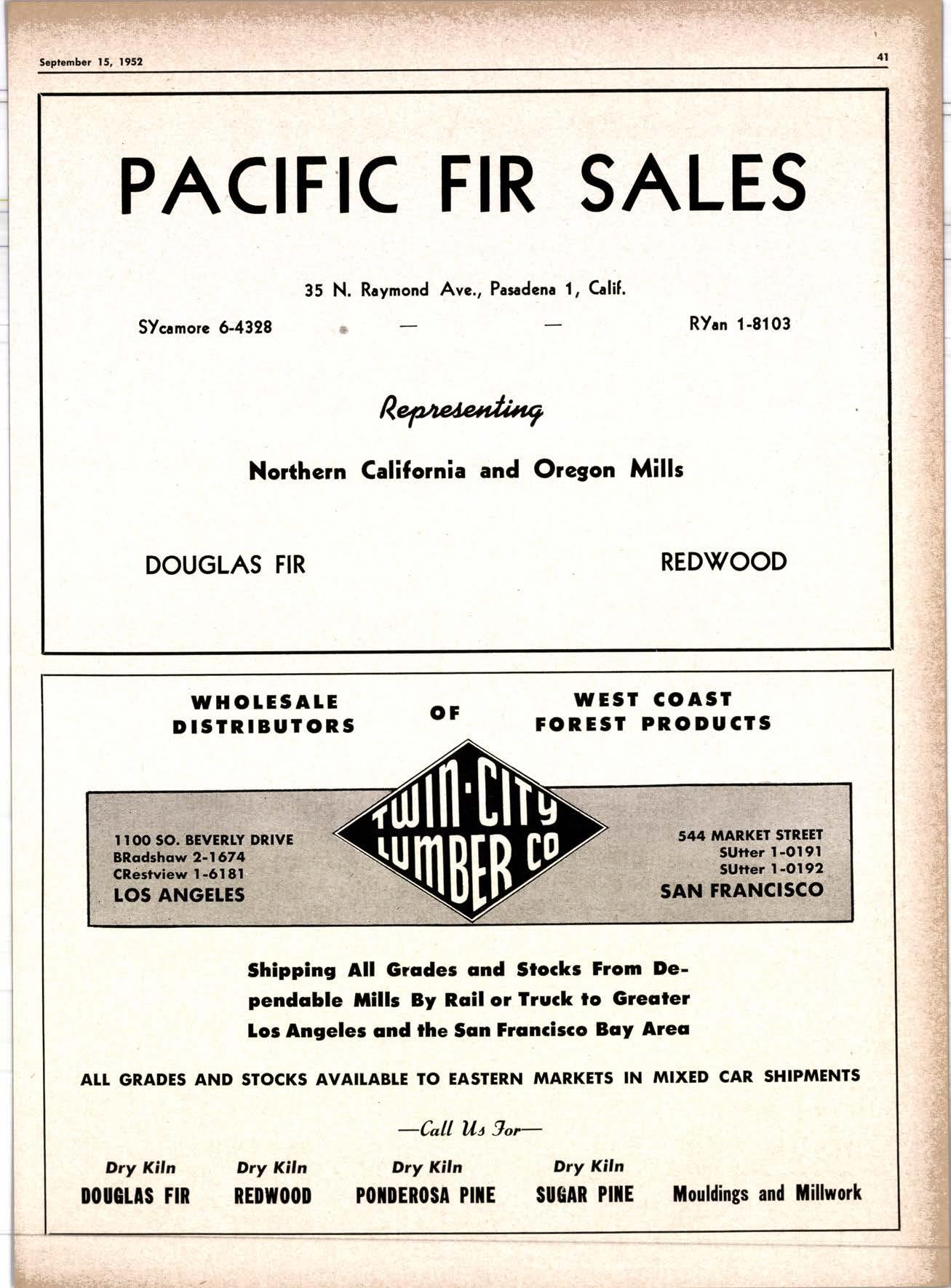