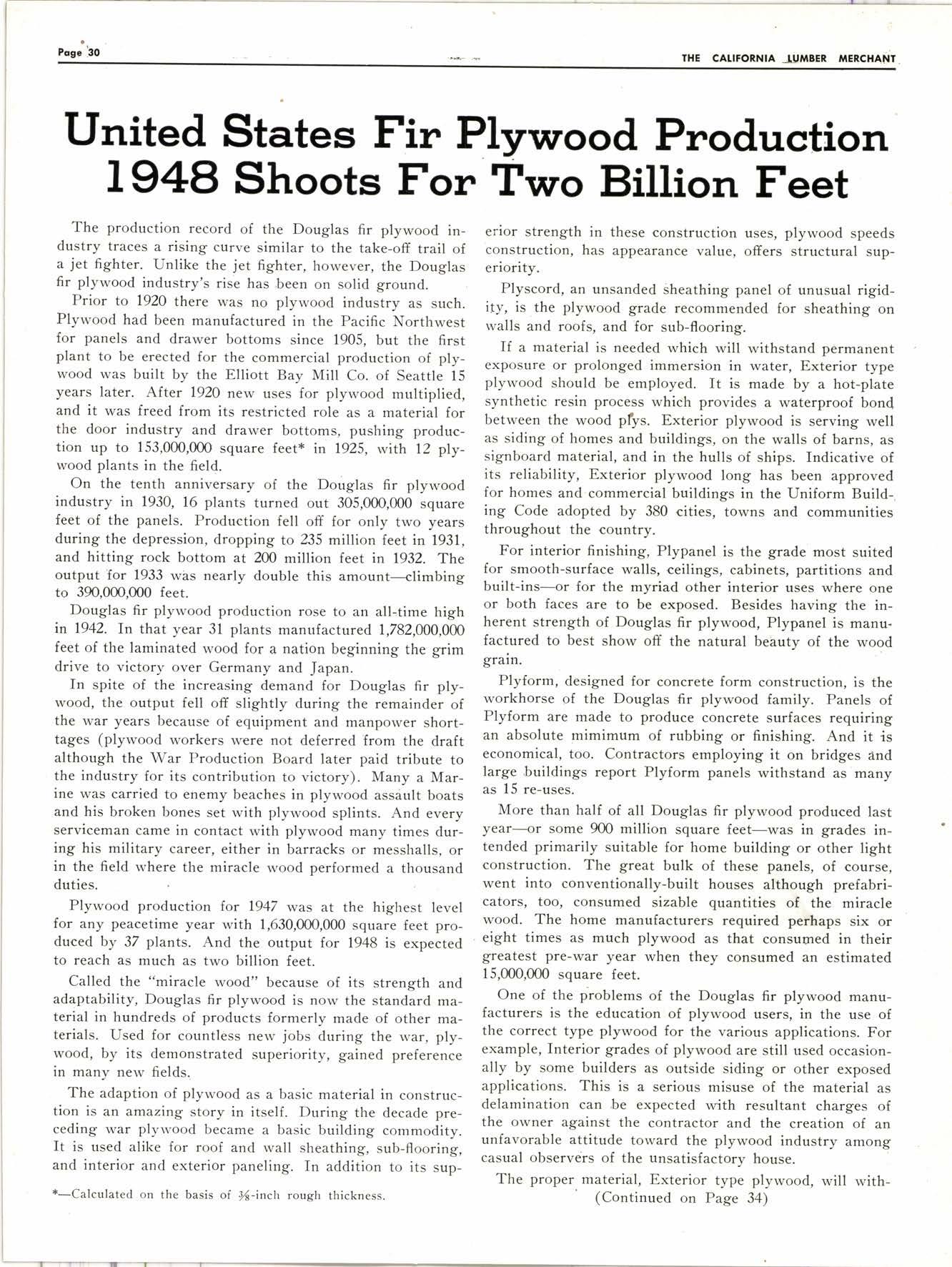
3 minute read
United States Fir Plywood Production 1948 Shoots For Two Biltion Feet
The production record of the Douglas fir plywood industry traces a rising curve similar to the take-off trail of a jet fighter. Unlike the jet fighter, however, the Douglas fir plywood industry's rise has ,been on solid ground.
Prior to 1920 there was no plywood industry as such. Plywood had been manufactured in the Pacific Northwest for panels and drawer bottoms since 1905, but the first plant to be erected for the commercial production of plywood was built by the Elliott Bay Mill Co. of Seattle 15 years later. After 1920 new uses for plywood multiplied, and it was freed from its restricted role as a material for the door industry and drawer bottoms, pushing production up to 153,000,000 square feet* in 1925, with 12 plywood plants in the field.
On the tenth anniversary of the Douglas fir plywood industry in 1930, 16 plants turned out 305,000,000 square feet of the panels. Production fell off for only two years during the depression, dropping to 235 million feet in 1931, and hitting rock bottom at 200 million feet in 1932. The output for 1933 was nearly double this amount-climbing to 390,000,000 feet.
Douglas fir plywood production rose to an all,time high in 1942. In that year 3l plants manufactured 1,782,000,000 feet of the laminated wood for a nation beginning the grim drive to victory over Germany and Japan.
In spite of the increasing demand for Douglas fir plywood, the output fell off slightly during the remainder of the war years because of equipment and manpower shorttages (plywood workers were not deferred from the draft although the War Production Board later paid tribute to the industry for its contribution to victory). Many a Marine was carried to enemy beaches in plywood assiult boats and his broken bones set with plywood splints. And every serviceman came in contact with plywood many times during his military career, either in barracks or messhalls, or in the field where the miracle wood performed a thousand duties.
Plywood production f.or 1947 was at the highest level for any peacetime year with 1,630,000,000 square feet produced by 37 plants. And the output for 1948 is expected to reach as much as two billion feet.
Called the "miracle wood" because of its strength and adaptability, Douglas fir plywood is now the standard material in hundreds of products formerly made of other materials. Used for countldss new jobs during the war, plywood, by its demonstrated superiority, gained preference in many new fields.
The adaption of plywood as a basic material in construction is an amazing story in itself. During the decade preceding war plywood became a basic building commodity. It is used alike for roof and wall sheathing, sub-flooring, and interior and exterior paneling. In addition to its sup*-Calculated on the basis of tfi-inch rough thickness.
erior strength in these construction uses, plywood speeds construction, has appearance value, offers structural superiority.
Plyscord, an unsanded sheathing panel of unusual rigidity, is the plywood grade recommended for sheathing on walls and roofs, and for sub-flooring.
If a material is needed which will withstand permanent exposure or prolonged immersion in water, Exterior type plywood should be employed. It is made by a hot-plate synthetic resin process which provides a waterproof bond between the wood pfys. Exterior plywood is serving well as siding of homes and building's, on the walls of barns, as signboard material, and in the hulls of ships. Indicative of its reliability, Exterior plywood long has been approved for homes and commercial buildings in the Uniform Build-, ing Code adopted by 380 cities, towns and communities throughout the country.
For interior finishing, Plypanel is the grade most suited for smooth-surface walls, ceilings, cabinets, partitions and built-ins-or for the myriad other interior uses where one or both faces are to be exposed. Besides having the inherent strength of Douglas fir plywood, Plypanel is manufactured to best show off the natural bebuty of the wood grain.
Plyform, designed for concrete form construction, is the workhorse of the Douglas fir plywood family. Panels of Plyform are made to produce concrete surfaces requiring an absolute mimimum of rubbing or finishing. And it is economical, too. Contractors employing it on bridges and large buildings report Plyform panels withstand as many as 15 re-uses.
More than half of all Douglas fir plywood produced last year-or some 900 million square feet-was in grades intended primarily suitable for home building or other light construction. The great bulk of these panels, of course, went into conventionally-built houses although prefabricators, too, consumed sizable quantities of the miracle wood. The home manufacturers required perhaps six or eight times as much plywood as that consusred in their greatest pre-war year when they consumed an estimated 15,C100,000 square feet.
One of the problems of the Douglas fir plywood manufacturers is the education of plywood users, in the use of the correct type plywood for the various applications. For example, Interior grades of plywood are still used occasionally by some builders as outside siding or other exposed applications. This is a serious misuse of the material as delamination can ,be expected with resultant charges of the owner against the contractor and the creation of an unfavorable attitude toward the plywood industry among casual observers of the unsatisfactory house.
The proper material, Exterior type plywood, will with- ' (Continued on Page 34)
