
1 minute read
IT'S WHAT'S TlI THE SIIIPMENT THAT COUNTS!
We wholesole o complele line of Wesl Coost lumber for every purPose -speciolizing in DIRECT FROM OUR OWN MILL SHIPMENTS viq CARGO, RAII ond TRUCK of moteriol thol is profitoble for the Retoil Lumber Deoler to hondle. YOU cqn successfully BOOST YOUR sAlEs-which in turn will BoosT YouR PROFIT-when you specify SCHAECHER-KUX prducts from one of our mony mills. Thot is why lve soy: "lT'S WHAT'S lN THE SHIPT,IENT THAT COUNTS" becouse you obtoin the GREATEST VATUE from eoch size, grode ond species
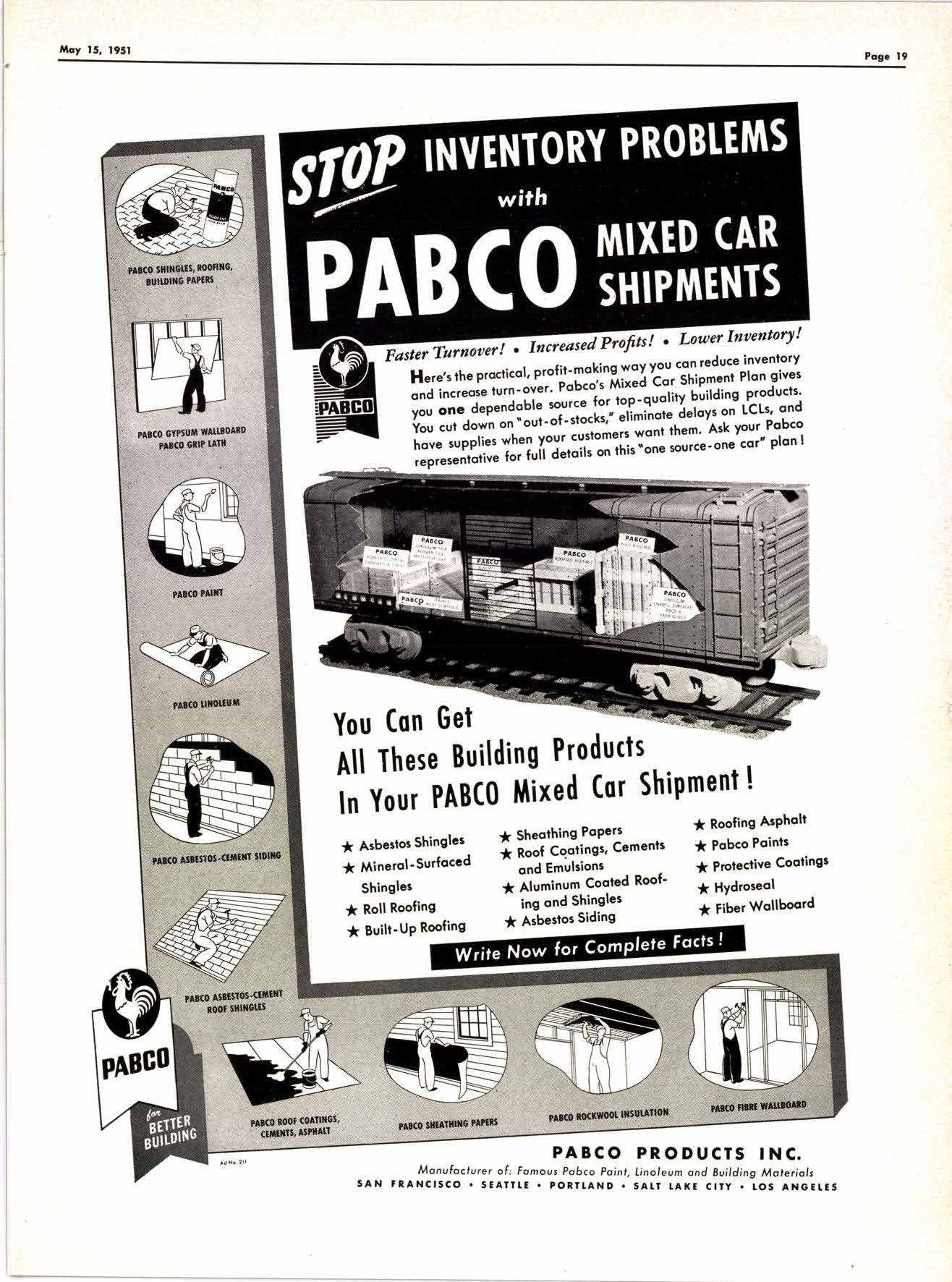
Ncw Dcvclopmcntr in Timbcr Handling
At the invitation of Western Dry Kiln Company, Oakland, a group of Pacific Coast plywood manufacturers and distributors were invited to hear an address by the guest speaker, Ralph Symonds of Australia. Mr. Symonds has an international reputation as an engineer and designer in utilizing of timbers, and was invited to America to discuss the possibilities of introducing some of lris buil<ling methods in this country.
Mr. Symonds opencd the discussion by describing in detail numerous developments made by him sincc 1922 trr the present date covering thc manufacture of large sheets of waterproof plywood conring from the hot plates in sheets without a joint in thc facc in size up to 7'x25', and described a plan now in course of production to manufacture similar sheets 5l' in length by 9'B' high. Specirr,en sheets were on display of other thicknesses ranging from 'l/s" d.own to l/l(f'. The general reaction was that of amazement at the precision work on the pancls dislllaycd. It was ast<lunding to see the "Guarantecd I-abels" that rvere usecl for panels faced rvith highly figured exotic veneers, such as burls, crotch mahogany and numerous other veneers, which in this country are regarded as almost impossible to guarantce against crazing and chccking of the face veneers, and any other defects that are commoll to laminated and veneer panels.
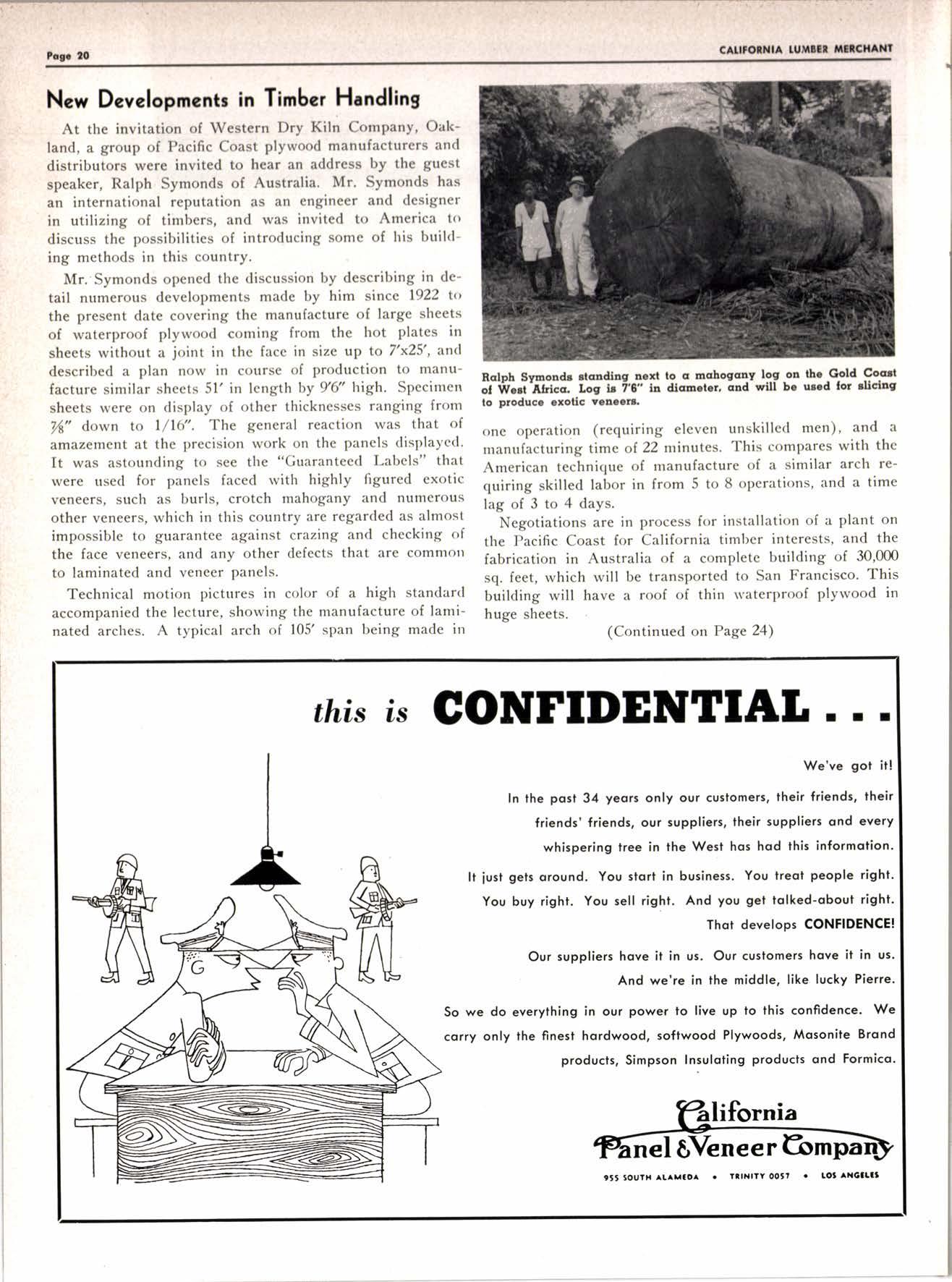
Technical motion pictttres in color of a high standar<l accompanied the lecture, showing the n'ranufacture of laminated arcl.res. A typical arch of 105' span being made irr rudag to produco rxotlc voaooil. one operation (requiring eleven unskilled men), and a rrrantrfacturing time ol 22 ntinutes. This compares with thc American techni<1ue of rrranufacture clf a similar arch requiring skilled labor in from 5 to 8 opcrations, and a time lag of 3 to 4 days.
Negotiations are in Process for installation of a plant on the I'acific Coast for California timllcr interests, and the fabrication in Australia of a complete building of 30,000 sq. feet, which will be transported to San Francisco. This building will have a roof of thin u'aterproof plyrvood in huge sheets.
(Continued on Page 24)