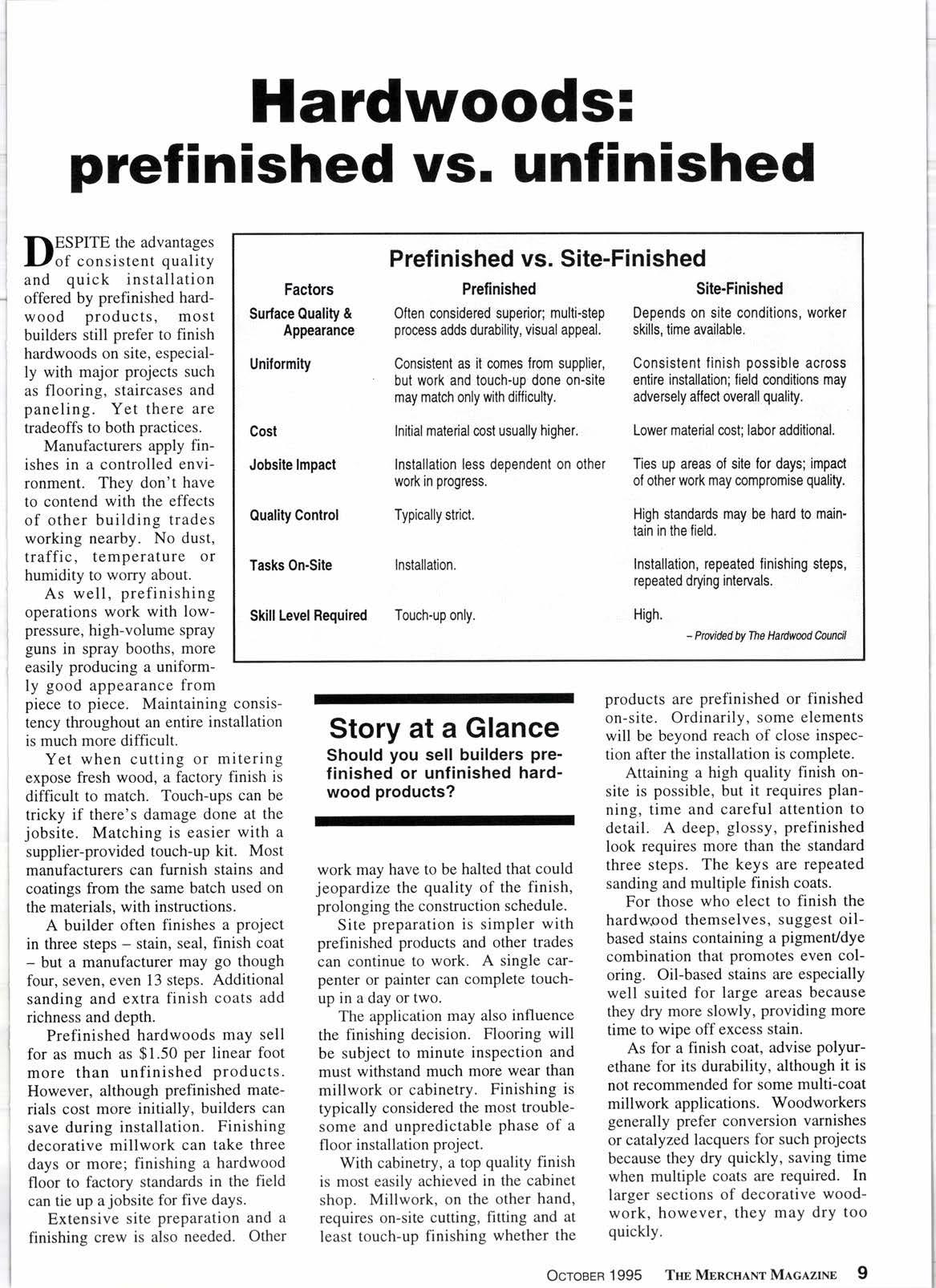
2 minute read
Hardwoods: prefinished vs. unfinished
IESPITE the advantages
Lf of consistent quality and quick installation offered by prefinished hardwood products, most builders still prefer to finish hardwoods on site, especially with major projects such as flooring, staircases and paneling. Yet there are tradeoffs to both practices.
Manufacturers apply finishes in a controlled environment. They don't have to contend with the effects of other building trades working nearby. No dust, traffic, temperature or humidity to worry about.
As well, prefinishing operations work with lowpressure, high-volume spray guns in spray booths, more easily producing a uniformly good appearance from
Prefinished vs. Site-Finished
Factors
Surface Quality & Appearance
Uniformity
Cosl
Jobsite lmpact
Quality Gontrol
Tasks On-Site
Skill Level Required piece to piece. Maintaining consistency throughout an entire installation is much more difficult.
Yet when cutting or mitering expose fresh wood, a factory finish is difficult to match. Touch-ups can be tricky if there's damage done at the jobsite. Matching is easier with a supplier-provided touch-up kit. Most manufacturers can furnish stains and coatings from the same batch used on the materials. with instructions.
A builder often finishes a project in three steps - stain, seal, finish coat - but a manufacturer may go though four, seven, even 13 steps. Additional sanding and extra finish coats add richness and depth.
Prefinished hardwoods may sell for as much as $1.50 per linear foot more than unfinished products. However, although prefinished materials cost more initially, builders can save during installation. Finishing decorative millwork can take three days or more; finishing a hardwood floor to factory standards in the field can tie up ajobsite for five days.
Extensive site preparation and a finishing crew is also needed. Other
Prefinished,
Often considered superibr; multi.step process adds durability, Msual appeal.
Consistent as if comes from supplier, but work and touch-up'done on-site may match only with difficulty.
Initial material cost usually higher. Installation less dependent on olher work in progress.
Typically strict. lnstallation.
Touch-up only.
Story at a Glance
Should you sell builders prefinished or unfinished hardwood products?
work may have to be halted that could jeopardize the quality of the finish, prolonging the construction schedule.
Site preparation is simpler with prefinished products and other trades can continue to work. A single carpenter or painter can complete touchup in a day or two.
The application may also influence the finishing decision. Flooring will be subject to minute inspection and must withstand much more wear than millwork or cabinetry. Finishing is typically considered the most troublesome and unpredictable phase of a fl oor installation project.
With cabinetry, a top quality finish is most easily achieved in the cabinet shop. Millwork, on the other hand, requires on-site cutting, htting and at least touch-up finishing whether the
Site-Finished
Depends on site conditions, worker skills, time available.
Consistent linish possible across entire installation; field conditions may adversely affect overall quality,
Lower malerial cost; labor additional.
Ties up areas of site lor days; impact ol other work may compromise quality.
High standards may be hard to maintain in the tield.
Installation, repeated finishing steps, repeated drying intervals.
High.
- Pwided by me Hardwfu Cancil products are prefinished or finished on-site. Ordinarily, some elements will be beyond reach of close inspection after the installation is complete.
Attaining a high quality finish onsite is possible, but it requires planning, time and careful attention to detail. A deep, glossy, prefinished look requires more than the standard three steps. The keys are repeated sanding and multiple finish coats.
For those who elect to finish the hardwrood themselves, suggest oilbased stains containing a pigment/dye combination that promotes even coloring. Oil-based stains are especially well suited for large areas because they dry more slowly, providing more time to wipe off excess stain.
As for a finish coat, advise polyurethane for its durability, although it is not recommended for some multi-coat millwork applications. Woodworkers generally prefer conversion varnishes or catalyzed lacquers for such projects because they dry quickly, saving time when multiple coats are required. In larger sections of decorative woodwork, however, they may dry too quickly.