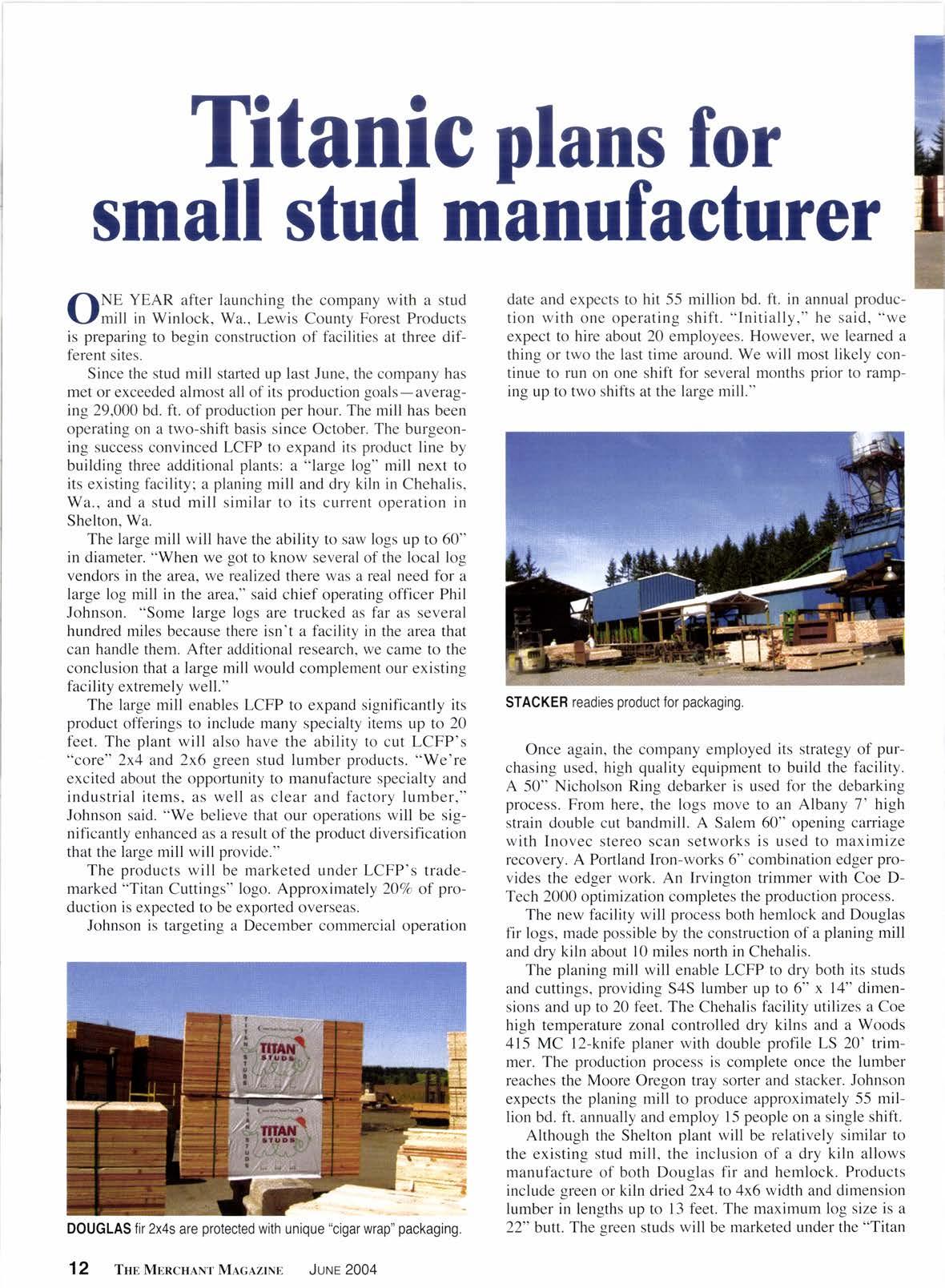
4 minute read
Titanic plans for small stud manufacturer
YEAR after launching the company with a stud \-lmill in Winlock, Wa., Lewis County Forest Products is preparing to begin construction of facilities at three different sites.
1|.}NE
Since the stud mill starled up last June, the company has met or exceeded almost all of its production goals-averaging 29,000 bd. ft. of production per hour. The mill has been operating on a two-shift basis since October. The burgeoning success convinced LCFP to expand its product line by building three additional plants: a "large log" mill next to its existing facility; a planing mill and dry kiln in Chehalis, Wa., and a stud mill similar to its current operation in Shelton, Wa.
The large mill will have the ability to saw logs up to 60" in diameter. "When we got to know several of the local log vendors in the area, we realized there was a real need for a large log mill in the area," said chief operating officer Phil Johnson. "Some large logs are trucked as far as several hundred miles because there isn't a facility in the area that can handle them. After additional research, we came to the conclusion that a large mill would complement our existing facility extremely well."
The large mill enables LCFP to expand significantly its product offerings to include many specialty items up to 20 feet. The plant will also have the ability to cut LCFP's "core" 2x4 and 2x6 green stud lumber products. "We're excited about the opportunity to manufacture specialty and industrial items, as well as clear and factory lumber," Johnson said. "We believe that our operations will be significantly enhanced as a result ofthe product diversification that the large mill will provide."
The products will be marketed under LCFP's trademarked "Titan Cuttings" logo. Approximately 207o of production is expected to be exported overseas.
Johnson is targeting a December commercial operation date and expects to hit 55 million bd. ft. in annual production with one operating shift. "Initially," he said, "we expect to hire about 20 employees. However, we learned a thing or two the last time around. We will most likely continue to run on one shift for several months prior to ramping up to two shifts at the large mill."
Once again, the company employed its strategy of purchasing used, high quality equipment to build the facility. A 50" Nicholson Ring debarker is used for the debarking process. From here, the logs move to an Albany 7' high strain double cut bandmill. A Salem 60" opening carriage with Inovec stereo scan setworks is used to maximize recovery. A Portland lron-works 6" combination edger provides the edger rvork. An Irvington trimmer with Coe DTech 2000 optimization completes the production process.
The new facility will process both hemlock and Douglas fir logs, made possible by the construction of a planing mill and dry kiln about l0 miles north in Chehalis.
The planing mill will enable LCFP to dry both its studs and cuttings, providing S4S lumber up to 6" x 14" dimensions and up to 20 feet. The Chehalis facility utilizes a Coe high temperature zonal controlled dry kilns and a Woods 415 MC l2-knife planer with double profile LS 20' trimmer. The production process is complete once the lumber reaches the Moore Oregon tray sorter and stacker. Johnson expects the planing mill to produce approximately 55 million bd. ft. annually and employ l5 people on a single shift.
Although the Shelton plant will be relatively similar to the existing stud mill, the inclusion of a dry kiln allows manufacture of both Douglas fir and hemlock. Products include green or kiln dried 2x4 to 4x6 width and dimension lumber in lengths up to l3 feet. The maximum log size is a 22" butt. The green studs will be marketed under the "Titan
Stud" brand name. while the kiln dried studs will be marketed as "Titan Regal Studs." The Shelton Mill is majority owned by LCFP and will operate under the name Mason County Forest Products.
The mill includes a significant amount of equipment manufactured by Salem Equipment and software and controls provided by MPM Engineering. The mill will use a Valon Kone 800 Debarker. Logs are then run through an MPM optimized log bucking system.
The system allows management to make real-time decisions about production based on current market prices," said Mason County Forest Products general manager Gary Snider. "The optimization is a real asset. It allows us to manufacture products that the market wants today, rather than a week too late."
The headrig includes a Salem 5' high-strain twin bandmill and Iggesund Chipping heads. A Salem EDLF system with MPM optimization will be used to feed the primary breakdown. From this point, the cants will flow to a Ukiah 4"x30" board edger with Coe D-Tech optimization and a Ukiah 6"x30" gang edger. Finally, the lumber will be sorted and stacked by a USNR 27 bin pusher log sorter and stacker.
The planing mill, which is not included in the sawmill, includes a Stetson Ross 2O-knife narrow lumber planer and 7' to 13' PET trimmer. The dry kilns are Coe high pressure, high temperature zonal controlled dry kilns.
Snider expects to produce 145 million bd. ft. annually on a two-shift basis of about 100 workers. In total, the expansion should boost LCFP's and its affiliates' capabilities to nearly 350 million bd. ft. of lumber a vear.
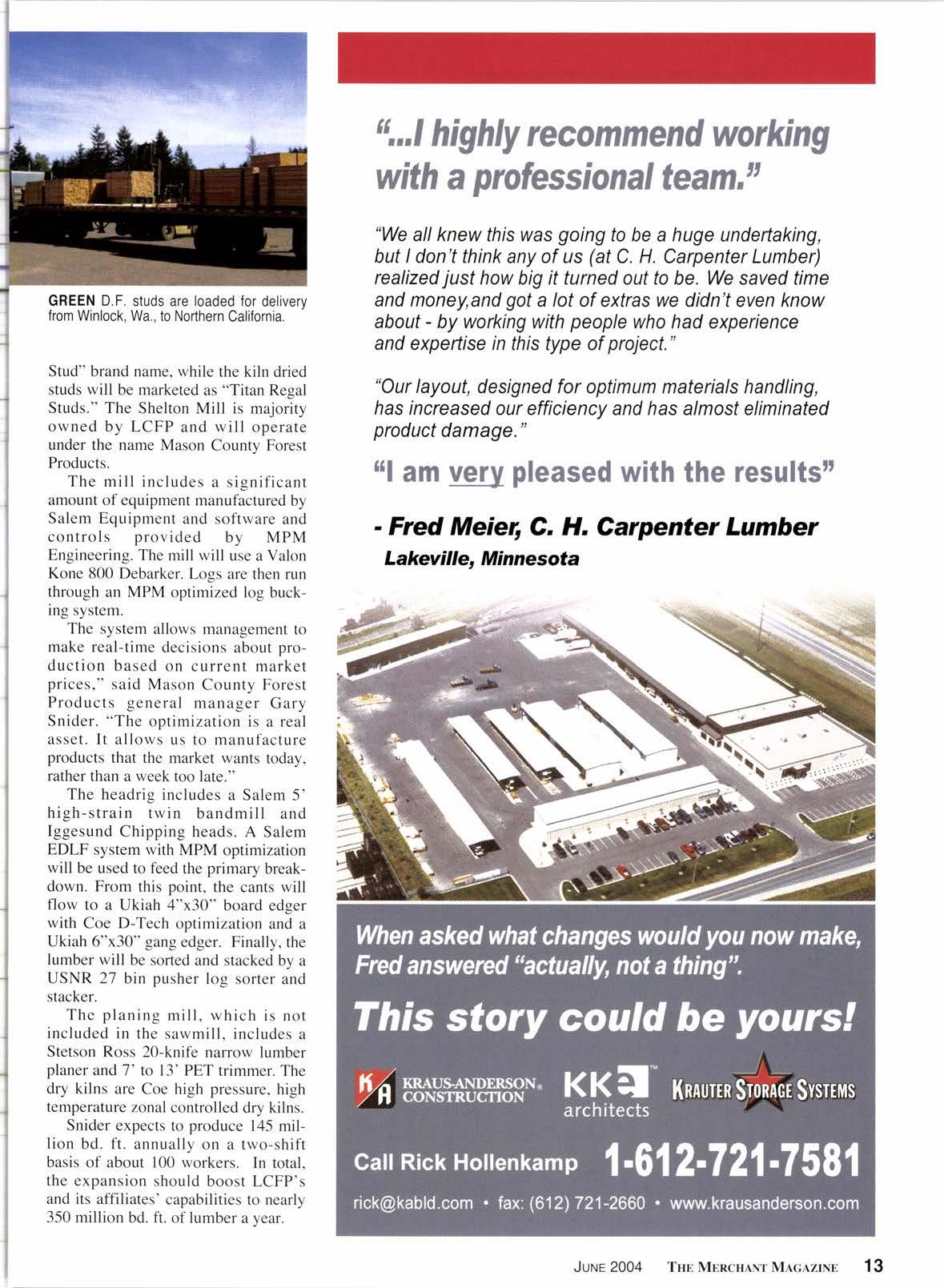
"We all knew fhis uyas going to be a huge undertaking, but I don't think any of us (at C. H. Carpenter Lumber) realized just how big it turned out to be. We saved time and money,and got a lot of extras we didn't even know about - by working with people who had experience and expertise in this type of project."
"Our layout, designed for optimum materials handling, has increased our efficiency and has almast eliminated product damage."