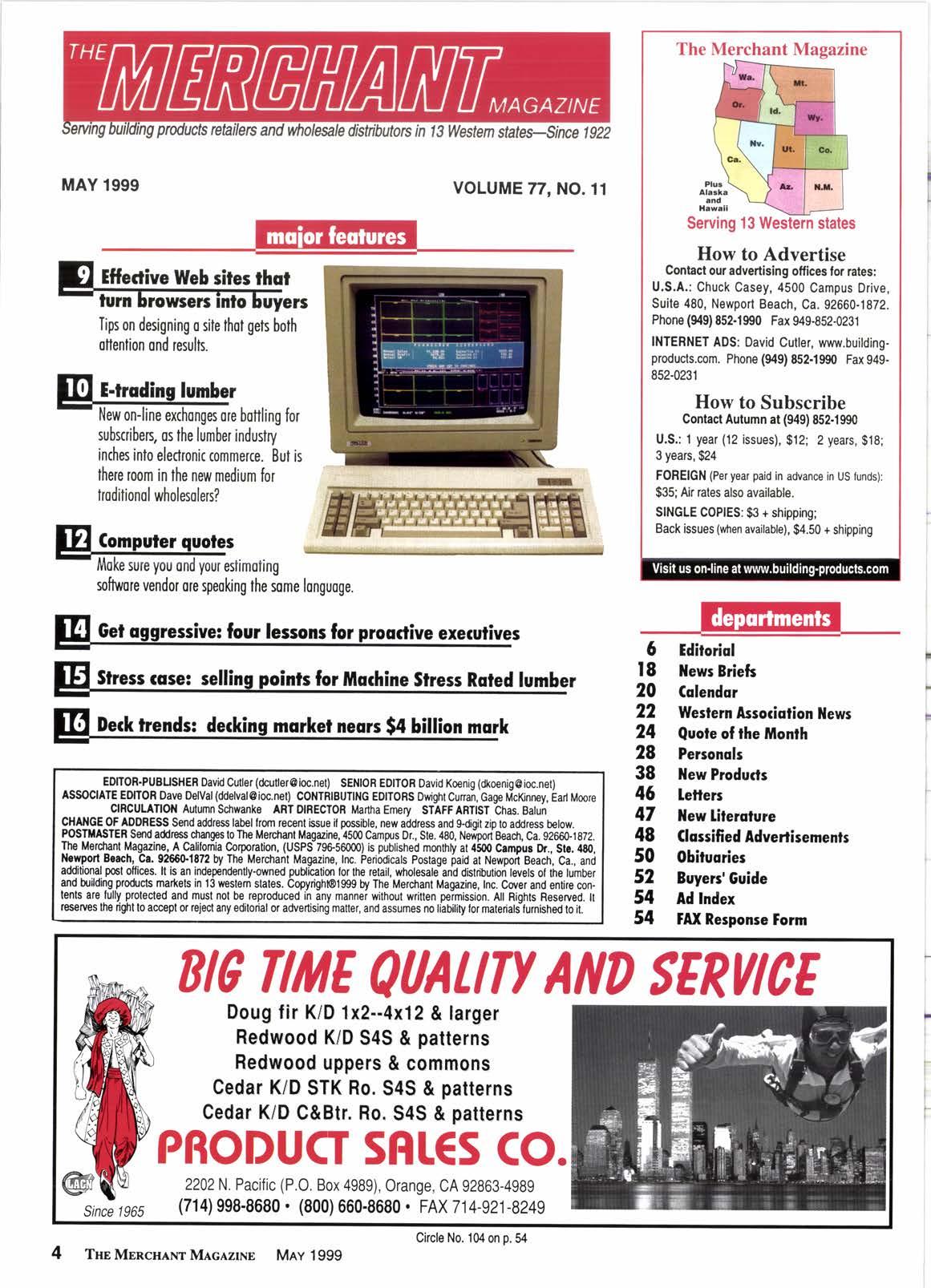
2 minute read
Products
Engineered Wood ProductsI-joist (residential and commercial), laminated veneer lumber, billet beams, rim board, glulam beams (industrial and architectural).
Particleboardunderlayment, industrial, stepping. 0riented Strand Boardsheathing, floorirg, Struc l. Smart System Sidingpanel, lap, soffit, EZ panel. TechShieldradiant barrier sheathing. Easyriser - engineered stair stringer system. Plus GDF studs and dimension, redwood products and treated hem-fir.
We service and deliver to the Southern California and Las Vegas markets.
Please call today and let us demonstrate how we can best serve your needs. Now and in the future.
MAY 1999
Tips on designing o site thot geh both ottention ond results.
voLUME 77, NO.11
Plua Alaaka and Hawall
Serving 13 states
How to Advertise
Contact our advertising offices for rates: U.S.A.: Chuck Casey, 4500 Campus Drive, Suile 480, Newport Beach, Ca.92660-1872. Phone (9{9) 852.1 990 Fax 949-852-0231
INTEFNET ADS: David Cutler, www.building. producls.com. Phone (949) 852.19!n Fax949852-0231
How to Subscribe
@'New on-line exchonges ore bottling for subsoibeq os the lumber indu$ry inches into eledronic commerce. But is lhere room in fie new medium for troditionol wholesolers?
@'Moke sure you ond your estimoting softwore vendor ore speoking the some longuoge.
EDITOR-PUBUSHER David Cutler (dcutlsr@ioc.net) SENIOR EDITOR David Koenig (dkoenig@ioc.net)
ASSOCIATE EDITOR Dave Delval (ddslval@ioc.net) COI{TRIEUilNG EDITORS Dwigt Cunan, Gage lilcKinney, Eart Moore CIRCULAilOil Autumn Schwanke ART DIRECTOR lilartha Ennry STAFF ARTTST Chas. Batun
CHAIIGE OF ADDRESS Send address label lrom recent issue il possible, new address and gdigit zip to address betow.
POSITASTER Sgld addtoss dla€es to Ih€ Merdant Magazine,4500 Canpos Dr., Sts. 4S0, N€iport &adl, Ca. 9200S1872.
The MordEnt Magazin€, A Calilomia Corporation, (USPS 79056000) is published mmhly at {i'00 Crnrpus It., Sh, /tEo, l|owpotl Boach,_Cr, 9266{l-1672 by Th€ Merdant Magazine, Inc. Peribdcals Postage iraid at Newport Beach, Ca., and additional po6t ollices. lt is an independsntlyrwned pudiEtion lor the retail, tvholesale and distributioi tevels ol the lumber and fuilding!rcdic1s markek in 13 wsstem statss. Copyrightol999 by Ths Mefdtant Magazine, Inc. Cover and entire con. lents ars lully prolected and must not be reproduced in any mannei without wrinen permis$on. All Rights Resewed. lt Ieserws
Contact Autumn at (949) 852.1990 U.S.: 1 year (12 issues), 912; 2 years, 918; 3 years, $24
FOREIGN (Per year paid in advance in US funds): $35; Air rates also available.
SINGLE COPIES: $3 + shipping; Back issues (when available), $4.50 + shipping

It's Not Tlailer l?ash Any More
Whether you call them trailers, mobile homes or manufactured housing, that segment of the housing market has been undergoing significant changes in the last decade. These developments mean that suppliers need to prepare for new needs and wants by both builders and the consumers who buy them.
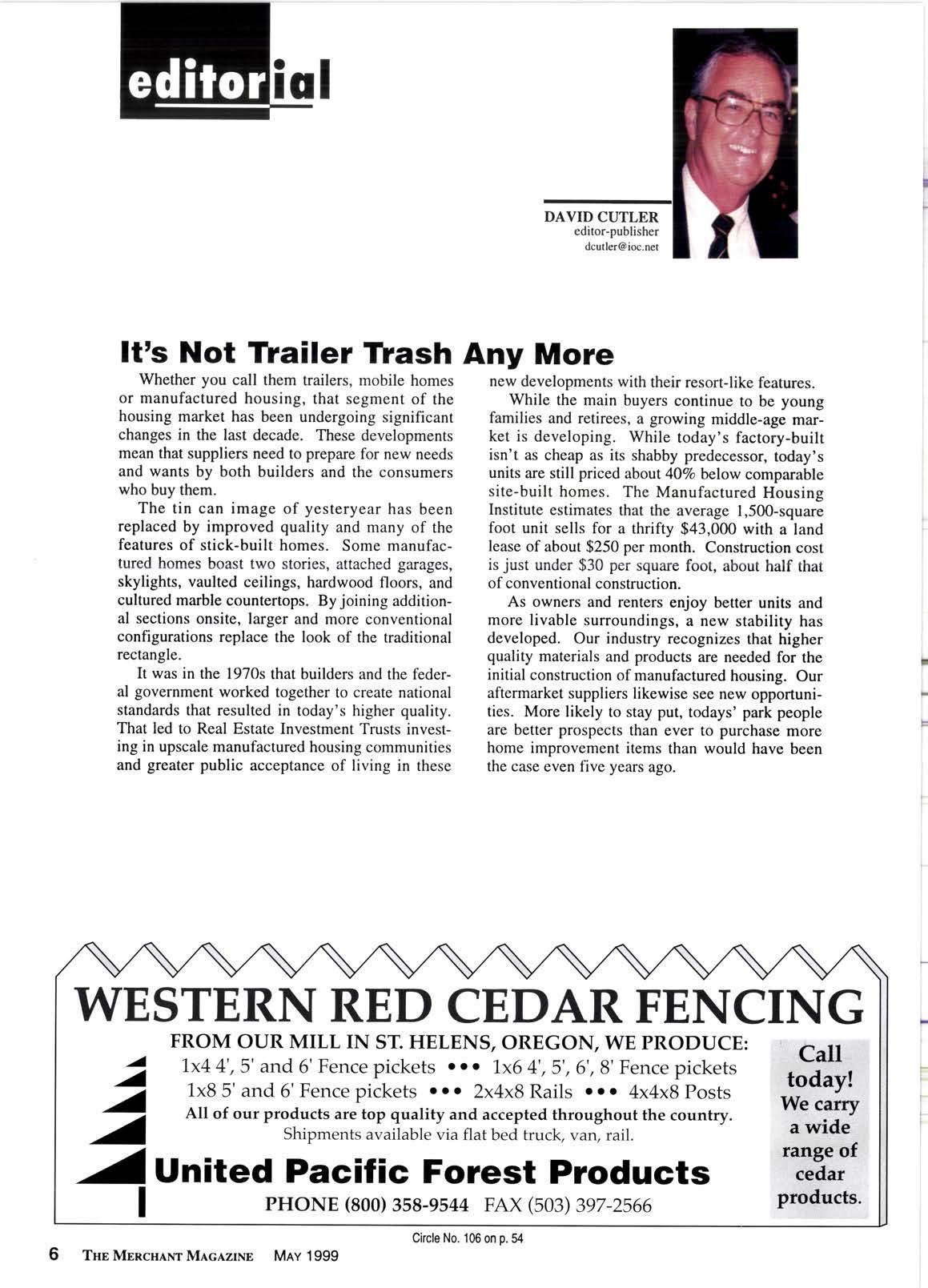
The tin can image of yesteryear has been replaced by improved quality and many of the features of stick-built homes. Some manufactured homes boast two stories, attached garages, skylights, vaulted ceilings, hardwood floors, and cultured marble countertops. By joining additional sections onsite, larger and more conventional configurations replace the look of the traditional rectangle.
It was in the 1970s that builders and the federal government worked together to create national standards that resulted in today's higher quality. That led to Real Estate Investment Trusts investing in upscale manufactured housing communities and greater public acceptance of living in these new developments with their resort-like features. While the main buyers continue to be young families and retirees, a growing middle-age market is developing. While today's factory-built isn't as cheap as its shabby predecessor, today's units are still priced about 40Vo below comparable site-built homes. The Manufactured Housing Institute estimates that the average 1,500-square foot unit sells for a thrifty $43,000 with a land lease of about $250 per month. Construction cost is just under $30 per square foot, about half that of conventional construction.
As owners and renters enjoy better units and more livable surroundings, a new stability has developed. Our industry recognizes that higher quality materials and products are needed for the initial construction of manufactured housing. Our aftermarket suppliers likewise see new opportunities. More likely to stay put, todays' park people are better prospects than ever to purchase more home improvement items than would have been the case even five years ago.