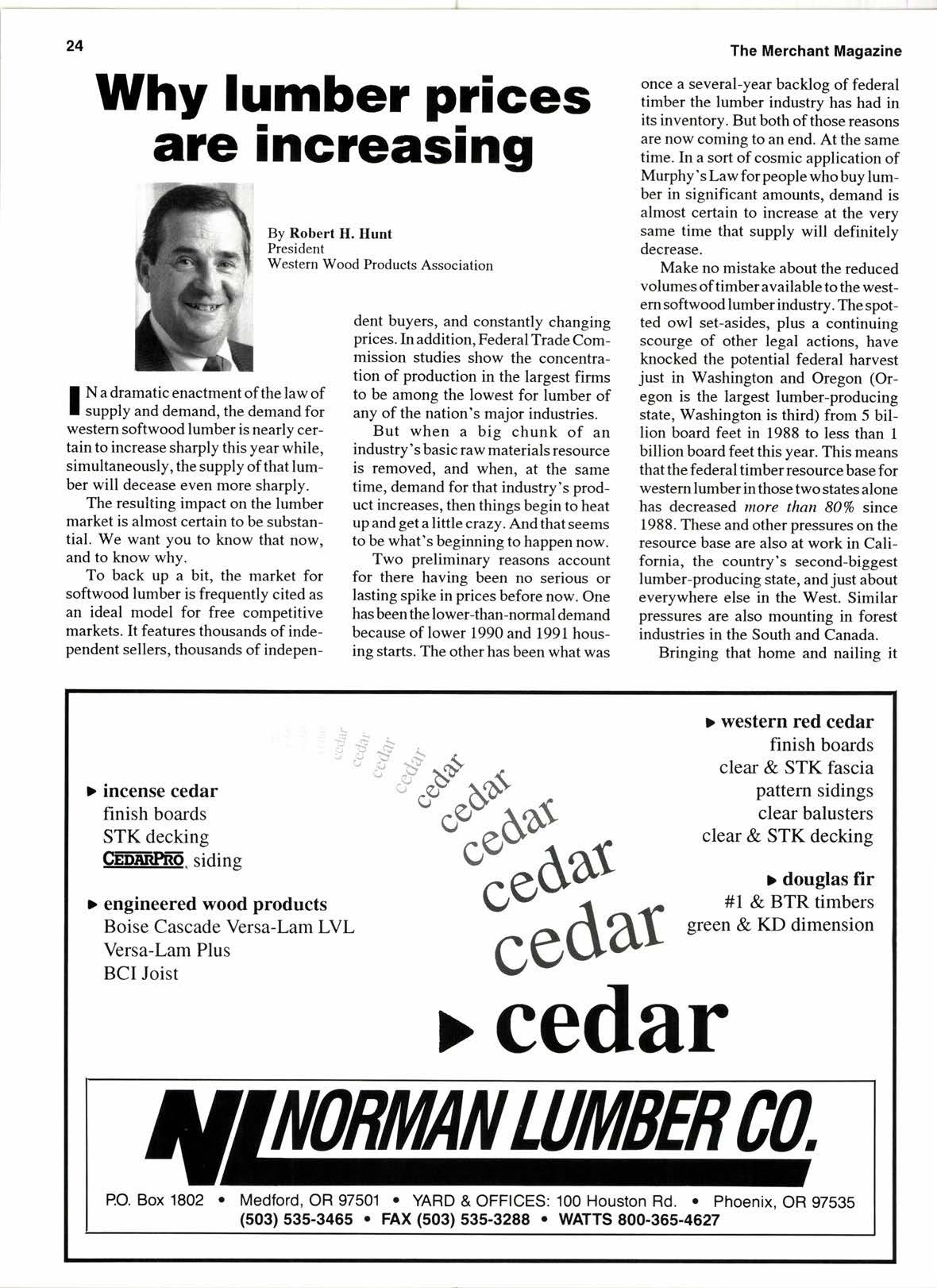
4 minute read
Why lumber prices are Increasrng
By Robert H. Hunt President Western Wood Products Association
I N a dramatic enactment of the law of I supply and demand, the demand for westem softwood lumber is nearly certain to increase sharply this year while, simultaneously, the supply of that lumber will decease even more sharply.
The resulting impact on the lumber market is almost certain to be substantial. We want you to know that now, and to know why.
To back up a bit, the market for softwood lumber is frequently cited as an ideal model for free competitive markets. [t features thousands of independent sellers, thousands of indepen- dent buyers, and constantly changing prices. In addition, Federal Trade Commission studies show the concentration of production in the largest firms to be among the lowest for lumber of any of the nation's major industries.
But when a big chunk of an industry 's basic raw materials resource is removed, and when, at the same time, demand for that industry's product increases, then things begin to heat up and get a little crazy. And that seems to be what's beginning to happen now.
Two preliminary reasons account for there having been no serious or lasting spike in prices before now. One has beenthe lower-than-normal demand because oflower 1990 and 1991 housing starts. The other has been what was once a several-year backlog of federal timber the lumber industry has had in its inventory. But both of those reasons are now coming to an end. At the same time. In a sort of cosmic application of Murphy's Law for people who buy lumber in significant amounts, demand is almost certain to increase at the very same time that supply will definitely dectease.
Make no mistake about the reduced volumes of timber available to the westemsoftwood lumber industry. The spotted owl set-asides, plus a continuing scoruge of other legal actions, have knocked the potential federal harvest just in Washington and Oregon (Oregon is the largest lumber-producing state, Washington is third) from 5 billion board feet in 1988 to less than 1 billion board feet this year. This means that the federal timber resource base for western lumber in those two states alone has decreased more than 80% since 1988. These and other pressures on the resource base are also at work in California, the country's second-biggest lumber-producing state, and just about everywhere else in the West. Similar pressures are also mounting in forest industries in the South and Canada. Bringing that home and nailing it down: federally-owned forests provide about 60 % of the timber needed by mills in Oregon, m orc than 30 7o in Washington, and 40-50% of the supply for mills in ldaho, Montana and California.
So no matter how you look at it, less timbera whole lot lessis going to be available. It doesn't matter that housing starts will almostcertainly increase. It doesn't matter that remodeling continues to boom (its requirements for lumber have doubled in the last decade), or that the do-it-yourself market is growing almost daily.
And, as we all know by now, it doesn't matter that trees are the only major commodity resource in the world that renews itself: that just keeps comingback. Oil doesn't. Steel doesn't. Concrete and masonry don't. Aluminum doesn't. No other resource does. But, maybe because it's hard to chain yourself to a bauxite mine, timber is the resource everybody isup in arms about.
At any rate, there is no nice or soft or easy way to say this. Although there may soon be the strongest demand for western softwood lumber that has existed in years, the cold hard fact is that substantially less of it will be available.
One bright spot in all thisand there is oneis lumber's inflation factor. For the period running from
October, 1979, through December, 1991, the overall rate of inflation was 87.6%.If lumber's inflation rate had matched that, the price per thousand board feet last December would have been $6 I 5 per thousand board feet (Douglas fir, wholesale FOB mill) instead of the $296 it actually was. Under the circumstances, that's a good thing to be able to point to. And, at the moment, that's about all we can point to with pleasure.
There are reasons for this. One of the most important has been the plentiful and continuous flow of raw material coming from our forests up to now, helping to keep supply and demand in balance, stabilizing costs, and playing a big part in making Americans the best-housed population on the planet. But things are changing. Believe me, we wish even more than you do that it were different. Our industry has never faced anything like this or even approaching this. But our mills continue to close, injunctions continue to be filed, timber sales continue to be halted. It all eventually leads to moving affordable housing further out of reach for more and more people. And, amazingly, through it all, and lying in the face ofall logic and reason, the people who brought all of this about continue to be cheered. As the beer commercial says, "Why ask why?"
So that's the situation as we see it now.
And we wanted you to know.
L-P Agrees to Acquire Tricon
Louisiana-Pacific Corp. has reached an agreement in principle to acquire certain assets of Tricon Forest Products, Inc., a wholesale lumber trading business in Lake Oswego, Or. The agreement was announced jointly by L-P and Robert M. Simpson, Tricon's president.
The agreement, which is subject to approval of L-P's board of directors, would establish a wholesale lumber trading activity for L-P managed by Simpson and employing the current staff of Tricon.
"This acquisition adds another important customer service dimension to our lumber business," said Harry A. Merlo, L-P's chairman and president. "We're pleased to add Robert Simpson to our tearn and gain his outstanding trackrecord in wholesale lumber sales."