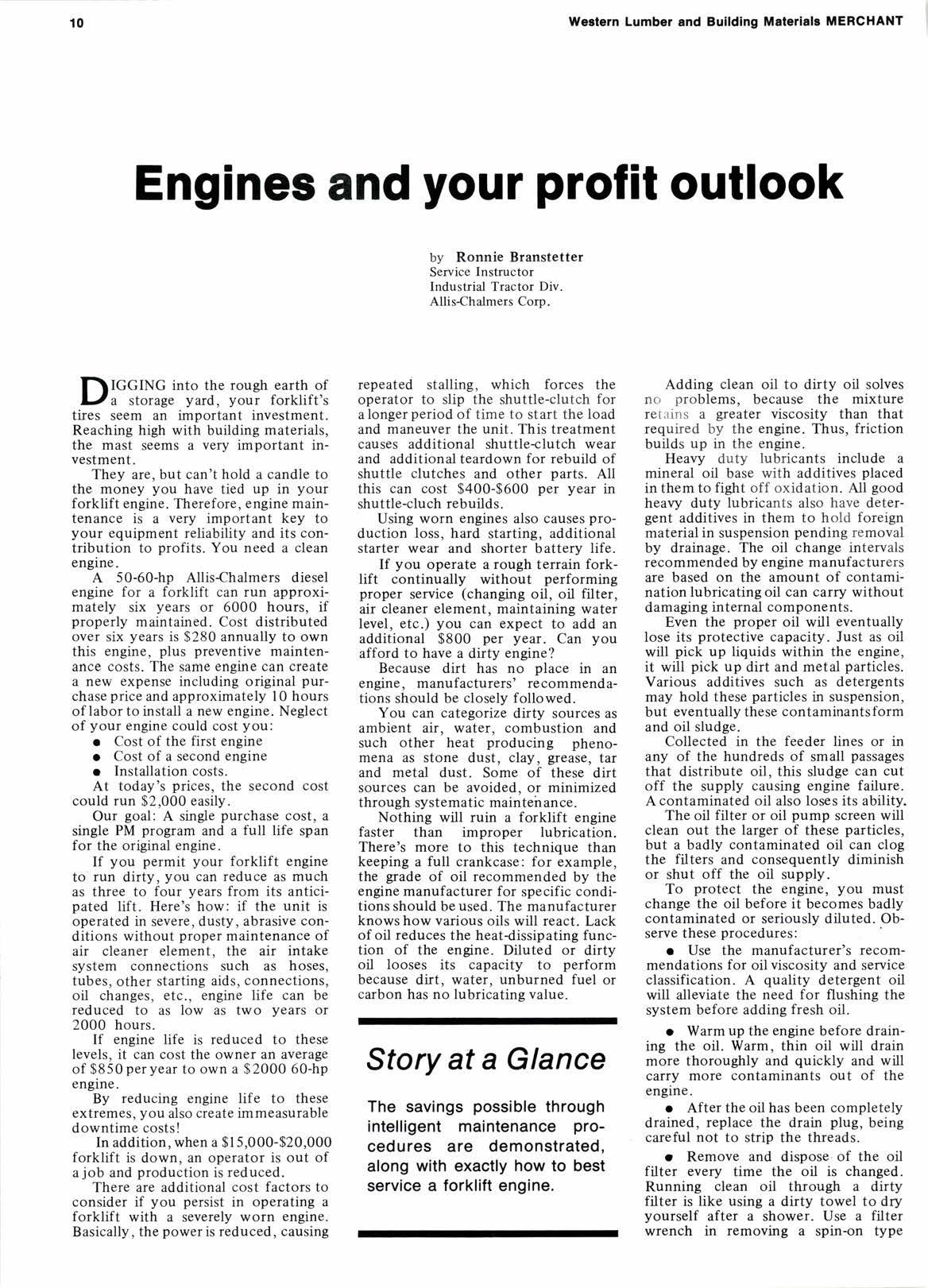
3 minute read
Engines and your profit outlook
by Ronnie Branstetter Service Instructor Industrial Tractor Div. Allis{halmers Corp.
l-llcClttC into the rough earth of Va s167^te yard, your forklift's tires seem an important investment. Reaching high with building materials, the mast seems a very important investment.
They are, but can't hold a candle to the money you have tied up in your forklift engine. Therefore, engine maintenance is a very important key to your equipment reliability and its contribution to profits. You need a clean engine.
A 50-60-hp Allis{halmers diesel engine for a forklift can run approximately six years or 6000 hours, if properly maintained. Cost distributed over six years is $280 annually to own this engine, plus preventive maintenance costs. The same engine can create a new expense including original purchase price and approximately l0 hours of labortoinstall a new engine. Neglect of your engine could cost you: o Cost of the first engine o Cost of a second engine r Installation costs.
At today's prices, the second cost could run $2,000 easily.
Our goal: A single purchase cost, a single PM program and a full life span for the original engine.
If you permit your forklift engine to run dirty, you can reduce as much as three to four years from its anticipated lift. Here's how: if the unit is operated in severe, dusty, abrasive conditions without proper maintenance of air cleaner element, the air intake system connections such as hoses, tubes, other starting aids, connections, oil changes, etc., engine life can be reduced to as low as two years or 2000 hours.
If engine life is reduced to these levels, it can cost the owner an average of $850 peryear to own a $2000 60-hp engine.
By reducing engine life to these extremes, you also create immeasurable downtime costs!
In addition, when a $15,000-$20,000 forklift is down, an operator is out of ajob and production is reduced.
There are additional cost factors to consider if you persist in operating a forklift with a severely worn engine. Basically, the power is reduced, causing repeated stalling, which forces the operator to slip the shuttle-clutch for a longer period of time to start the load and maneuver the unit. This treatment causes additional shuttle<lutch wear and additional teardown for rebuild of shuttle clutches and other parts. All this can cost $400-$600 per year in shuttle-cluch rebuilds.
Using worn engines also causes production loss, hard starting, additional starter wear and shorter battery life.
If you operate a rough terrain forklift continually without performing proper service (changing oil, oil filter, air cleaner element, maintaining water level, etc.) you can expect to add an additional $800 per year. Can you afford to have a dirty engine?
Because dirt has no place in an engine, manufacturers' recommendations should be closely followed.
You can categorize dirty sources as ambient air, water, combustion and such other heat producing phenomena as stone dust, clay, grease, tar and metal dust. Some of these dirt sources can be avoided. or minimized through systematic mainteiance.
Nothing will ruin a forklift engine faster than improper lubrication. There's more to this technique than keeping a full crankcase: for example, the grade of oil recommended by the engine manufacturer for specific conditions should be used. The manufacturer knows how various oils will react. Lack of oil reduces the heatdissipating func- tion of the engine. Diluted or dirty oil looses its capacity to perform because dirt, water, unburned fuel or carbon has no lubricating value.
Story at a Glance
Adding clean oil to dirty oi] solves no problems, because the mixture retains a greater viscosity than that required by the engine. Thus, friction builds up in the engine.
Heavy duty lubricants include a mineral oil base with additives placed in them to fight off oxidation. All good heavy duty lubricants also have detergent additives in them to hold foreign material in suspension pending removal by drainage. The oil change intervals recommended by engine manufacturers are based on the amount of contamination lubricating oil can carry without damaging internal components.
Even the proper oil will eventually lose its protective capacity. Just as oil will pick up liquids within the engine, it will pick up dirt and metal particles. Various additives such as detergents may hold these particles in suspension, but eventually these contaminantsform and oil sludge.
Collected in the feeder lines or in any of the hundreds of small passages that distribute oil, this sludge can cut off the supply causing engine failure. A contaminated oil also loses its ability. The oil filter or oil pump screen will clean out the larger of these particles, but a badly contaminated oil can clog the filters and consequently diminish or shut off the oil supply.
To protect the engine, you must change the oil before it becomes badly contaminated or seriously diluted. Observe these procedures: o Use the manufacturer's recommendations for oil viscosity and service classification. A quality detergent oil will alleviate the need for flushing the system before adding fresh oil. o Warm up the engine before draining the oil. Warm, thin oil will drain more thoroughly and quickly and will carry more contaminants out of the engine. o After the oil has been completely drained, replace the drain plug, being careful not to strip the threads. o Remove and dispose of the oil filter every time the oil is changed. Running clean oil through a dirty filter is like using a dirty towel to dry yourself after a shower. Use a filter wrench in removing a spin-on type