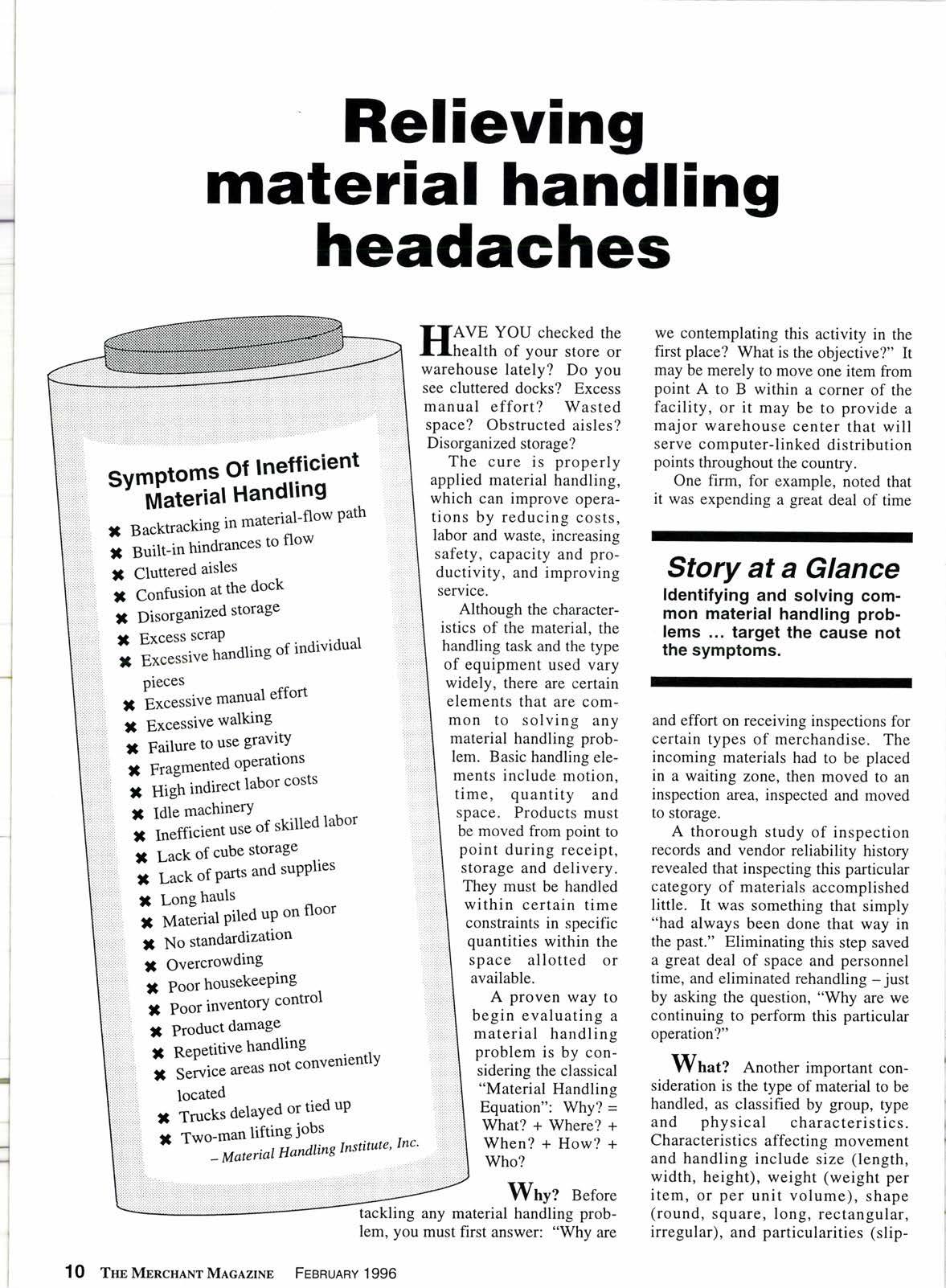
4 minute read
Relievingmaterialheadacheshandling
HfJiJ"",ffff:f l"'::
warehouse lately? Do you see cluttered docks? Excess manual effort? Wasted space? Obstructed aisles? Disorganized storage? The cure is properly applied material handling, which can improve operations by reducing costs, labor and waste, increasing safety, capacity and productivity, and improving servlce.
Although the characteristics of the material, the handling task and the type of equipment used vary widely, there are certain elements that are common to solving any material handling problem. Basic handling elements include motion, time, quantity and space. Products must be moved from point to point during receipt, storage and delivery. They must be handled within certain time constraints in specific quantities within the space allotted or available.
A proven way to begin evaluating a material handling problem is by considering the classical "Material Handling Equation": Why? = What? + Where? + When? + How? + Who?
Wnyr Before tackling any material handling problem, you must first answer: "Why are we contemplating this activity in the first place? What is the objective?" It may be merely to move one item from point A to B within a corner of the facility, or it may be to provide a major warehouse center that will serve computer-linked distribution points throughout the country.
One firm, for example, noted that it was expending a great deal of time
Story at a Glance ldentifying
and solving common material handling problems ... target the cause not the symptoms.
and effort on receiving inspections for certain types of merchandise. The incoming materials had to be placed in a waiting zone, then moved to an inspection area, inspected and moved to storage.
A thorough study of inspection records and vendor reliability history revealed that inspecting this particular category of materials accomplished little.It was something that simply "had always been done that way in the past." Eliminating this step saved a great deal of space and personnel time, and eliminated rehandling - just by asking the question, "Why are we continuing to perform this particular operation?"
Wnutf Another important consideration is the type of material to be handled, as classified by group, type andphysical characteristics.
Characteristics affecting movement and handling include size (length, width, height), weight (weight per item, or per unit volume), shape (round, square, long, rectangular, irregular), and particularities (slip- pery, fragile, sticky, explosive, frozen). lYnenZ includes the amount of material moving in a given period of time over a specific route, as well as the condition of the load (configuration, makeup of load, batch sizes). Seasonal or periodic variations also must be taken into account. Is one boxcar received per month, or one per day?
Many racking and shelving systems, for instance, are designed to store and display certain-sized products. Everything to be stocked must be taken into consideration to fully answer the "What?" question before the racks are selected.
Wne.e? describes the movement of product. Factors include the travel path, distance to be moved, and equipment and building limitations to movement.
When? also includes the time when materials are to be delivered, from the receiving area to the storage area, display area, sales counter and, finally, the jobsite.
Howt refers to the handling method to be employed. It covers the plan for the operation - including the layout - and specific techniques and equipment that may be required. For example, when selecting a lift truck, you must consider the type of load (pallet), load size, load weight, anticipated travel path's length and direction (horizontal, vertical, inclined), throughput (number of moves per hour), and conditions (indoor, outdoor, terrain, lighting, temperature).
Wnor Labor requirements also should be specified. The all-important human factor in the equation defines responsibility as well as manpower needs.
For example, one store discovered that its second shift consistently performed certain material handling tasks less efficiently than its first shift under seemingly identical conditions. Productivity was less and mistakes more frequent.
Investigations revealed that, by and large, second-shift personnel were predominantly part-timers, lower paid and newer employees, who felt little identity with the store, and little or no stake in running it profitably. They had infrequent contact with the general manager and owner.
The: .rEq:uiipment, : DCG|S|On
Choosing, the proper equip.meiit for a handling, ,task can bC a, chal. lengihg job.;:,,Kcep in mind the fol. lowing key f,aetors before beginr ning the selection process:
L... nefin" thc problem. It is astounding how often the real problem requiring a handling solution is not understood or fully anaIyzCd- Often the first question that should be asked is, 'Does this handling step really have to be performed at all?"
2... Lootr to the future. Remember that installing another row, oif,sh,elving may provide a temporary solution today, but will it creato,:more problems:::than it solves in ihe future? Equipment selectidn,,should,be, plaiined,,wlth an eye on tomorrow
3.., Ru-e-ber the systems concept ,Rarely if ever is:an,:activ. ity performed: without affecti,ng, other operations or being affected by them:, The,,re*uipment :being selebted shbuld::plat a pafi in,,the overall goals of the facility. [t's noticonfined to one small corner of the, waiehouser.,,Each..individual
Management immediately took steps to reduce turnover, provide incentives and cultivate teamwork.
Material handling is never performed in a vacuum, as an entity unto itself. Rather, it is an integral part of other activities and functions, including inventory control, warehousing and safety. The knowledgeable man- ager must be able to identify the material handling problems that exist within these other functions. And he must treat them as handling problems, not allowing them to be obscured as "inventory problems," "merchandising problems," and the like, otherwise he may be treating the symptom of the problem, rather than the cause.
Iift huaL:iS:part of a,,total,r:material handling:system.
4... K""p it simple. .Do,n't pur:sue unneceSsary sophisticaf,ion, *hen it's not warranted. For example, take advantage of gravify when possible. Make sure your eiistirig, equipment is fultry, utiliCed before additional investments are made, M C,sure:qUalifiedperson. hel: are:available to,tqlfer care of the, €quipmCnt after it is,purchased and rn use.
5... Don'toverspecify.It makes little sense to buy the most expensive, heaviest-duty equipment available for a light-duty opefa,tion, or one with a short anticipated life. As well; whenever possibte, use a standard design instead of a more costly custom piece of:equipment.
6.,. Chec,tr the alternatives. Don.l.t, selecl a, partiCular way ,of accomplishing the job on the advice ofjust one equipment sup- plier. You ulay,,,be,overlookirng better, less expensivC methods and equipment.
- Material Handling'lnstitute, Inc.
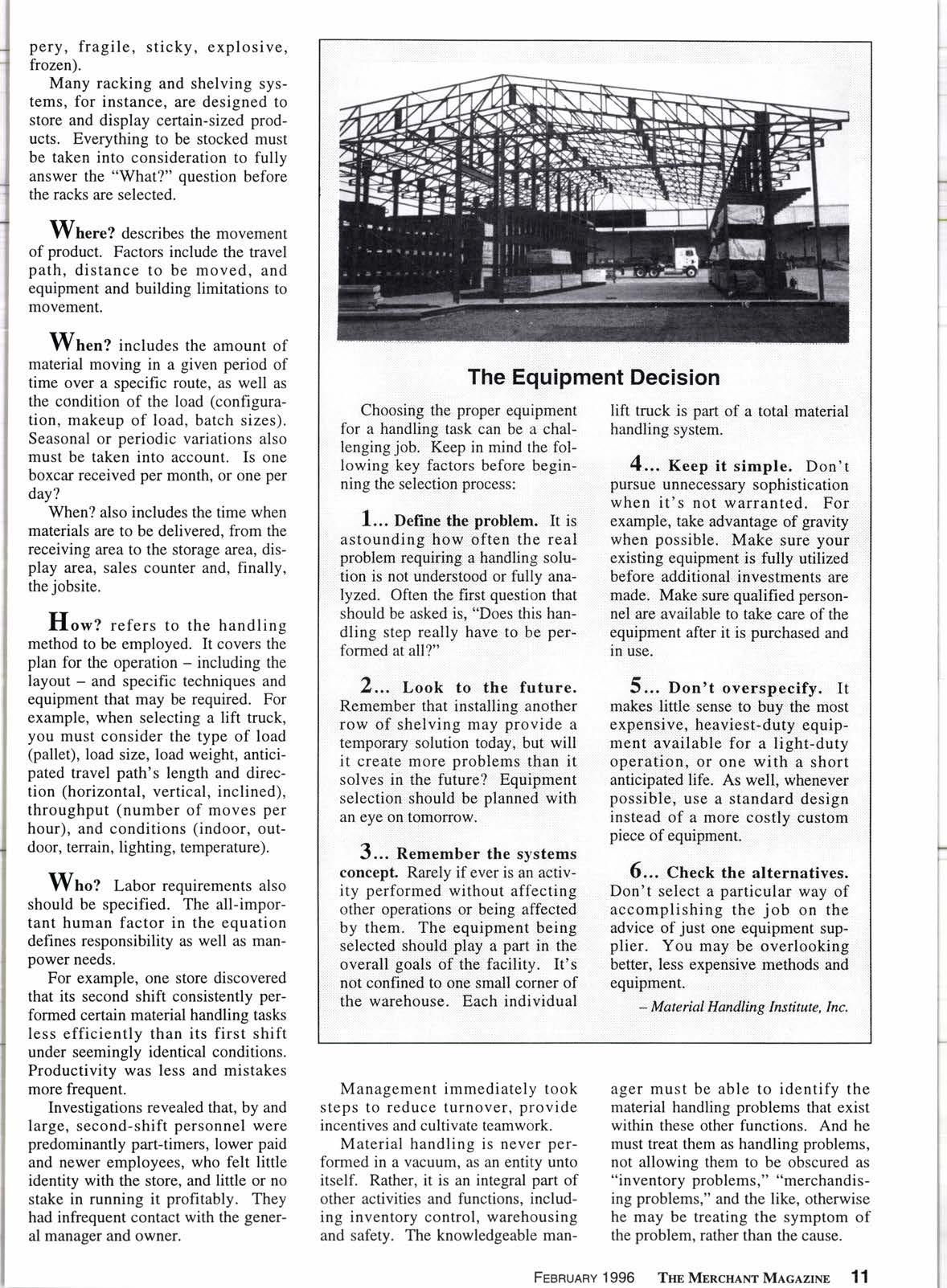