
3 minute read
DOUGLAS FIR DELIVERS COASTER CUSTOMER TO CHEMONITE@
J.H. Baxter provided 550,000 board feet of Chemonite treated Douglas fir for the Twister II roller coaster. The large volume tested the performance of everyone involved, but the schedule was met with J.H. Baxter integrating components into the treating schedule for more than two months until the job was complete.
Put in service on Memorial Day of 1995, the Twister II is now providing riders 3,400 feet of fasrpaced thrills.
BEAMS Bulkheads Docks
t one time or another, everyone has experienced the excitement of a scream-filled roller coaster ride. For over a century, Elitch Garden's Twister I, rated as one of the top ten coasters in the world, has delivered riders thrill after thrill, without fail. When Elitch moved to a new location near Denver's Mile High Stadium, they decided to build a new roller coaster.
From the beginning, Twister II was a challenge to vendors. Twenty tons of nuts and bolts, five tons of nails and 3,250 gallons of paint were required. After considering the possibility of steel construction, Elitch Gardens chose to stay with the beauty, flexibility and proven reliability of wood. They also decided to stay with their original supplier, Denver's Kellogg Lumber. Chemonite was named the preservative of choice. Laboratory comparisons show Chemonite is the superior wood preservative for treating Douglas fir. It's the only waterborne preservative that penetrates deep enough to assure compliance with AWPA and state and local standards.
Performance on Schedule
Since the roller coaster is a centerpiece in the park's new construction, it had to be completed on schedule without complications or timely setbacks.
For over half a century, Chemonite has provided unparalleled protection of Douglas fir, and other hard-to-treat wood, against decay and wood-destroying insects.
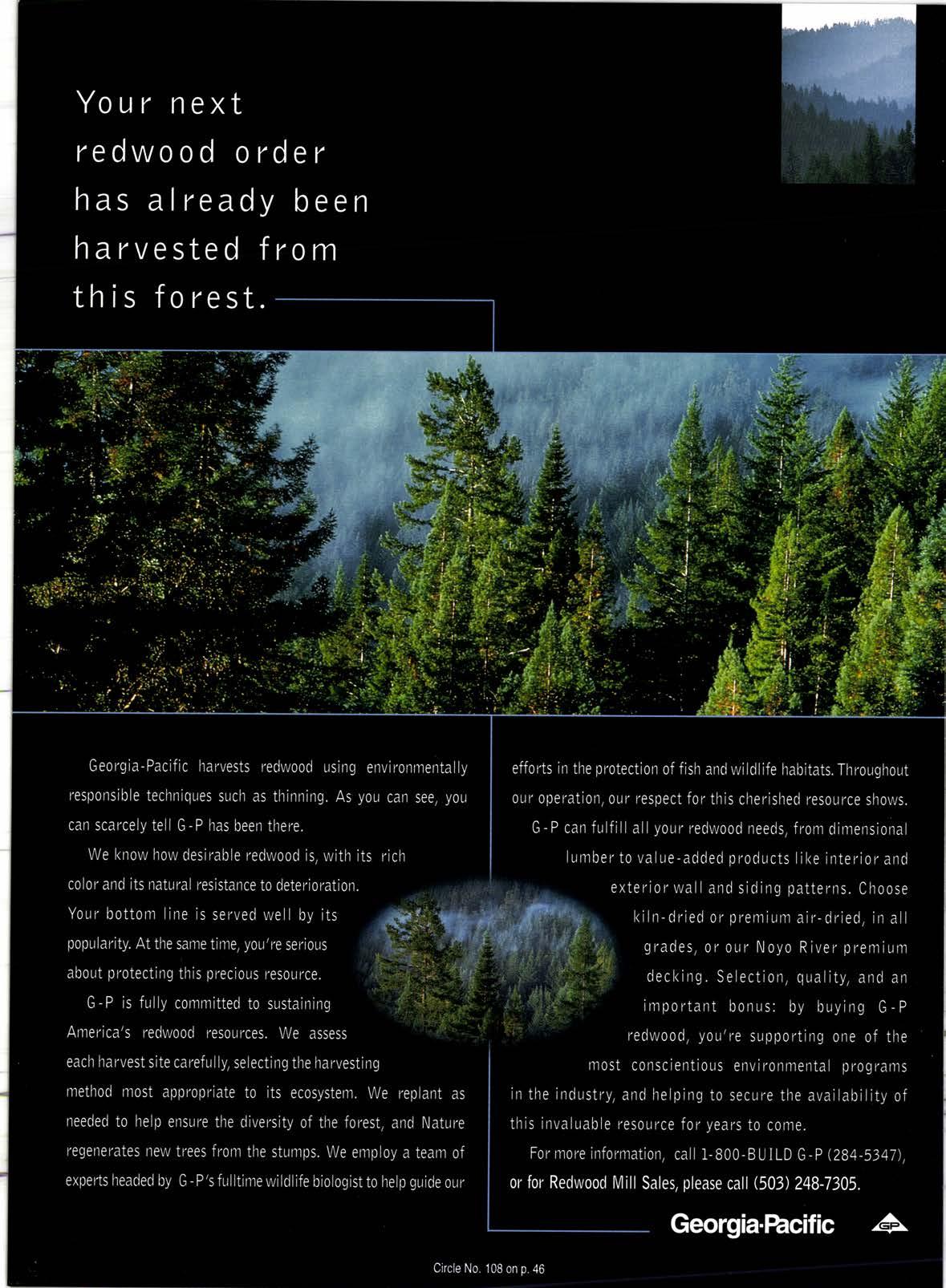
got to know when to hold them and know I when to fold them." This card players' expression aptly describes the dilemma facing owners of aging lift trucks. On one hand, owners want to hold them as long as possible to maximize the return on their investment. On the other hand, holding on to old, inefficient equipment can coJt money.
Instead of retiring the aging trucks, companies tend to repair them - and often end up paying more to maintain the old trucks than new ones would cost. Plus. a hidden cost exists since these trucks are not as productive as they once were. Calculating the optimum time to replace your lift trucks can reduce maintenance costs, improve productivity and increase profitability.
Among the factors that determine a lift truck's efficiency are the type of truck, severity of application, hours in use (per month and per year), and the type and frequency of maintenance. Typically, because they contain fewer moving parts, electric lift trucks have a longer economic life than internal combustion trucks.
Although maintenance costs gradually increase as trucks age, at a certain point, they go up more sharply. According to Hyster Co., at about 10,000 hours of use,
Story at a Glance
Determining the most cost effective time to replace a lift truck ... consider truck type, usage and maintenance frequency.
internal combustion trucks' maintenance costs are at a steeper incline, while maintenance costs for electric trucks begin to skyrocket at about 12,000 to 14,000 hours. Major overhauls, major component replacement and frequent minor repairs tend to drive costs even higher.
Optimally, equipment should be replaced when maintenance costs exceed its resale value. Maintenance and operating costs increase each year, while the resale value of the equipment decreases.
"Sometimes a business will want to put $5,000 a year into repairing a lift truck only worth $2,000 to $4,000," said Hyster's Mike Hanson. "That's not very cost effective. If the repairs were made, the lift truck would still be worth only $2,000 to $4,000."
The application the lift truck faces also affects its life. Those exposed to temperature extremes, brine or corrosives will experience shorter economic lives. Meanwhile, lift trucks operating in clean warehouses with wide aisles should have longer lives.
The monthly use of a lift truck determines how long it can operate economically. Based on 170 hours per month (2,000 hours per year), the average internal combustion truck can operate economically for five to six years, the average electric truck for about seven years. If the trucks are run more than this each month, replacement time will be accelerated.
The ratio commonly used is that one engine hour equals 40 automotive miles. To make a comparison, multiply the number of hours of engine operation by 40. For example, assume a lift truck's hour meter reads 4,000 hours. The equivalent reading on an automobile's odometer will equal 160,000 miles.
Another consideration in determining a truck's econom-