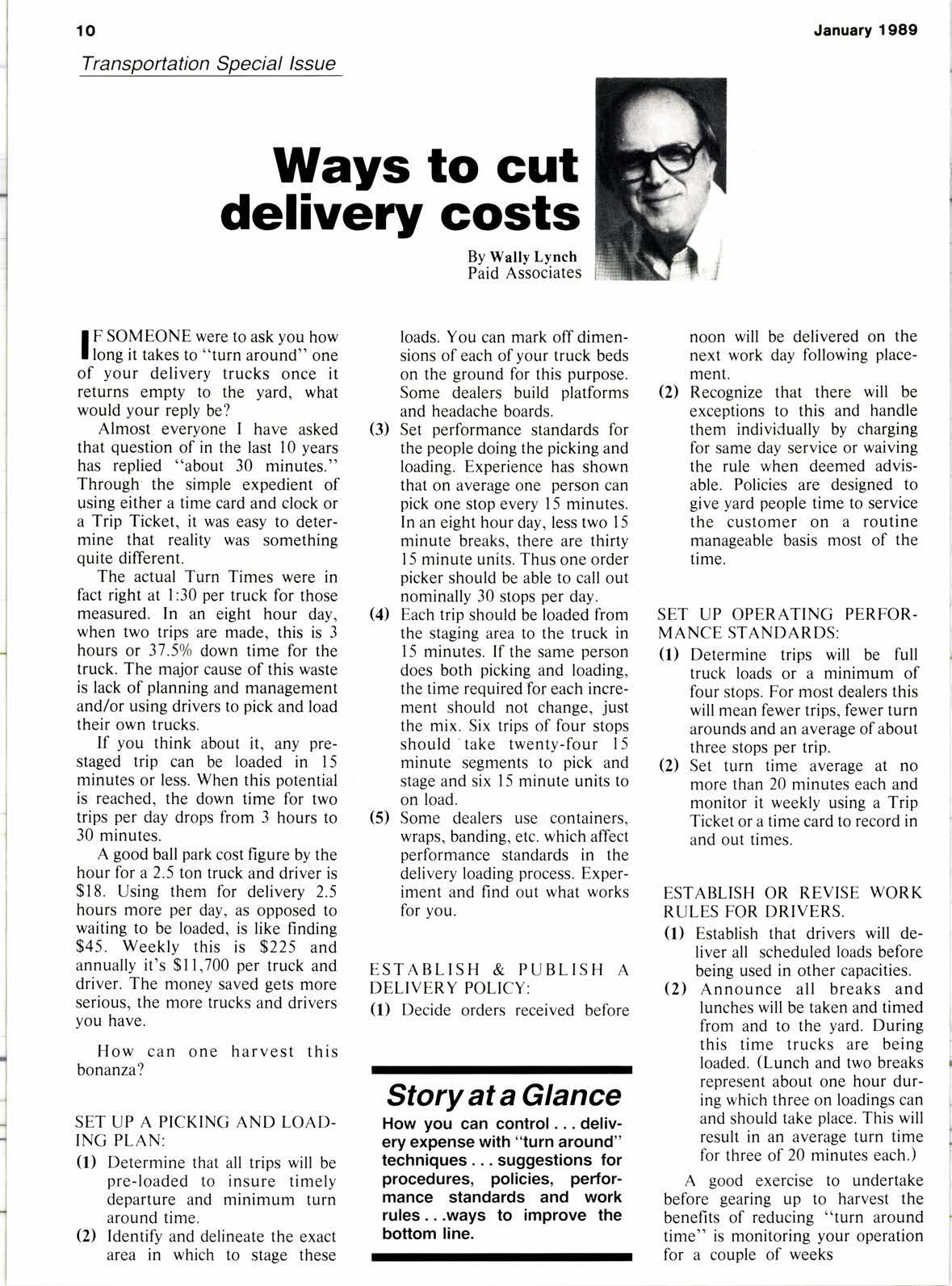
3 minute read
Ways to cut delivery costs
By Walty Lynch Paid Associates
I F SOMEONE were to ask you how I long it takes to "turn around" one of your delivery trucks once it returns empty to the yard, what would your reply be?
Almost everyone I have asked that question of in the last l0 years has replied "about 30 minutes." Through the simple expedient of using either a time card and clock or a Trip Ticket, it was easy to determine that reality was something quite different.
The actual Turn Times were in fact right at l:30 per truck for those measured. In an eight hour day, when two trips are made, this is 3 hours or 37.50/o down time for the truck. The major cause of this waste is lack of planning and management and/or using drivers to pick and load their own trucks.
If you think about it, any prestaged trip can be loaded in l5 minutes or less. When this potential is reached, the down time for two trips per day drops from 3 hours to 30 minutes.
A good ball park cost figure by the hour for a 2.5 ton truck and driver is $18. Using them for delivery 2.5 hours more per day, as opposed to waiting to be loaded, is like finding $45. Weekly this is $225 and annually it's $11,700 per truck and driver. The money saved gets more serious, the more trucks and drivers you have.
How can one harvest this bonanza?
SET UP A PICKING AND LOADING PLAN:
(1) Determine that all trips will be pre-loaded to insure timely departure and minimum turn around time.
(2) Identify and delineate the exact area in which to stage these loads. You can mark off dimensions of each of your truck beds on the ground for this purpose. Some dealers build platforms and headache boards.
(3) Set performance standards for the people doing the picking and loading. Experience has shown that on average one person can pick one stop every l5 minutes. In an eight hour day, less two l5 minute breaks, there are thirty l5 minute units. Thus one order picker should be able to call out nominally 30 stops per day.
(4) Each trip should be loaded from the staging area to the truck in 15 minutes. If the same person does both picking and loading, the time required for each increment should not change, just the mix. Six trips of four stops should take twenty-four l5 minute segments to pick and stage and six 15 minute units to on load.
(5) Some dealers use containers, wraps, banding, etc. which affect performance standards in the delivery loading process. Experiment and find out what works for you.
ESTABLISH & PUBLISH A DELIVERY POLICY:
(1) Decide orders received before
Story at a Glance
How you can control .. delivery expense with "turn around" techniques. suggestions for procedures, policies, performance standards and work rules. .ways to improve the bottom line.
noon will be delivered on the next work day following placement.
(2) Recognize that there will be exceptions to this and handle them individually by charging for same day service or waiving the rule when deemed advisable. Policies are designed to give yard people time to service the customer on a routine manageable basis most of the time.
SET UP OPERATING PERFORMANCE STANDARDS:
(1) Determine trips will be full truck loads or a minimum of four stops. For most dealers this will mean fewer trips, fewer turn arounds and an average of about three stops per trip.
(2) Set turn time average at no more than 20 minutes each and monitor it weekly using a Trip Ticket or a time card to record in and out times.
ESTABLISH OR REVISE WORK RULES FOR DRIVERS.
(1) Establish that drivers will deliver all scheduled loads before being used in other capacities.
Q) Announce all breaks and lunches will be taken and timed from and to the yard. During this time trucks are being loaded. (Lunch and two breaks represent about one hour during which three on loadings can and should take place. This will result in an average turn time for three of 20 minutes each.)
A good exercise to undertake before gearing up to harvest the benefits of reducing "turn around time" is monitoring your operation for a couple of weeks