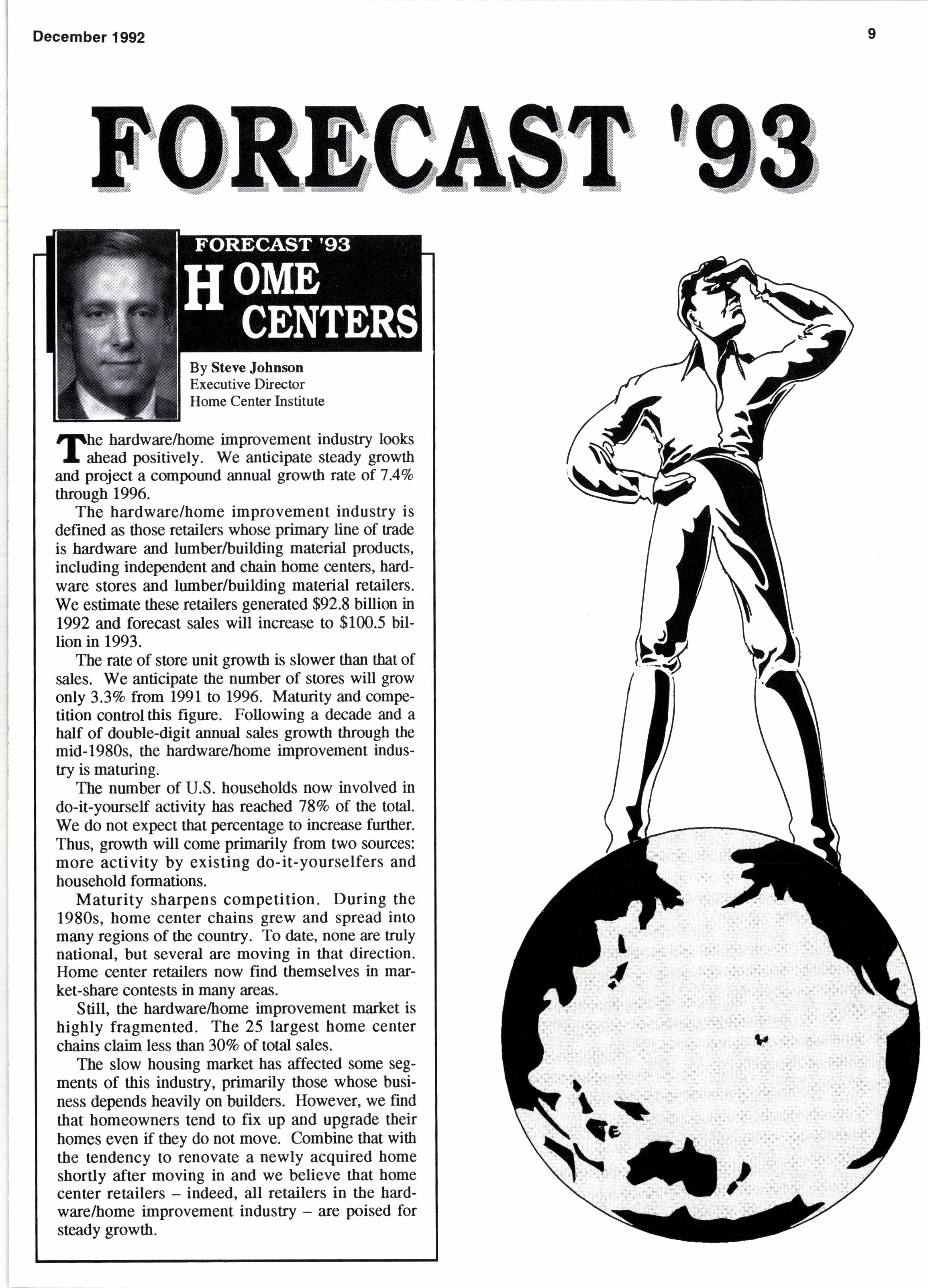
18 minute read
F&RRffiAffiry Ggtff
By Steve Johnson Executive Director Home Center Institute
r[he hardware/home improvement industry looks I ahead positively. We anticipate steady growth and project a compound annual growth rate of 7.4Vo through 1996.
The hardware/home improvement industry is defined as those retailers whose primary line of ftade is hardware and lumber/building material products, including independent and chain home centen, hardware stores and lumber/building material retailers. We estimate these retailers generated $92.8 billion in 1992 and forecast sales will increase to $100.5 billion in 1993.
Tbe rate of store unit growth is slower than that of sales. We anticipate the number of stores will grow only 3.3Vo from 1991 to 1996. Maturity and competition control this figure. Following a decade and a half of double-digit annual sales growth through the mid-1980s, the hardware/home improvement industry is maturing.
The number of U.S. households now involved in do-it-yourself activity has reached 787o of the total. We do not expect that percentage to increase further. Thus, growth will come primarily from two sources: more activity by existing do-it-yourselfers and household formations.
Maturity sharpens competition. During the 1980s, home center chains grew and spread into many regions of the country. To date, none are truly national, but several are moving in that direction. Home center retailers now find themselves in market-share contests in many areas.
Still, the hardware/home improvement market is highly fragmented. The 25 largest home center chains clraim less than30Vo of total sales.
The slow housing market has affected some segments of this industry, primarily those whose business depends heavily on builders. However, we find that homeowners tend to fix up and upgrade their homes even if they do not move. Combine that with the tendency to renovate a newly acquired home shortly after moving in and we believe that home center retailers - indeed, all retailers in the hardwarelhome improvement industry - are poised for steady growth.
By Ernert J. Stcbbln Exocutivc Managcr National Hardwood Lumbcr Association
trbe rccession is over and sligbt growth in tbe econo- I my is on the horizon for 1993. Depending on where tbey sit, most economists are predicting Gross Domestic Product growtb between l% and 3% in 1993 in both tbe U.S. and Canada. This follows a possible 1.5% GDP 8trowtb tbis year.
The conventional wisdom on Wall Street sees the economy'tnuddling tbrough" next year, but we still hear comments that the federal government - tbrough the Federal Reserve System - should stimulate growth. That prospect seems unlikely based on recent reports of the chairman of tbe Fed's 12 districs. Most Fed managers report prospects from retailers, manufacturers and bankers look steady and are growing slowly with no real surpises. Therefore, no real action is likely on money supply.
There will be no major recovery in 1993. Like the ltefore we look into the future, let's look at a few IJrecent events: July 1990, spotted owl added to threatened species list resulting in less softwood timber for harvest and closing of sawmills; 1991, environmental pressures hit eastern hardwood forests cutting available timber.
Concerned with job loss in the primary sawmill industry, s0ate economic developmerit departrnents encouraged secondary (value added) industry, resulting in more firms competing for dwindling lumber supplies, higher prices and more secondary manufacturers vying for a static customer base. Because of raw material losses and a shrinking customer base, moulding producers have had to look for altemative material supplies and explore foreign market development.
While imported species arc not a panacea, they may mitigate the demand for domestic species. They can replace or substitute for dwindling domestic species if the chain of disribution will accept change. The builder, remodeler and specilier must be educated on substitute species. They must be convinced a shortage exists. Some think it's a maneuver by suppliers to raise prices.
The wood moulding and millwork industry faces a growing domestic and world rrarkeL Since the boom years of the late '70s, the value of wholesale hardwood and softwood moulding product shipmens has increased from $757 million in 1979 to $1,067 bilton 1990. While inflation played a role, WMMPA members' production increased from 300,339,000 board feet in 1983 to 399,8U5N board feet in 1991.
A similar increase has been experienced in export markets where softwood moulding exports increased from 115,915,258 meters in 1989 to 422,794,599 meters in 1991. For the first six months of.1992, shipments contest between tbe tortoise and the hare, slow and steady wins the race. No manufacuring s€c1or in today's Nortb American economy is prepared to lead tbe cbarge. Nei0er bome building, commercial building nor the aulomobile industry is strong enough. While all are important s€gments of our overall economy, none are the burning engines of economic growth they were in the past
Wbat does tbis mean for tbe bardwood lumber industry? Bas€d on conversations with NHLA meurbers, slow and steady growth is a good scenario. Because the industry is diverse in boh geography and market sec{ors, facors affecring individual memben ar€ not comparable; bowever, here are some thoughts I've heard expressed.
Manufacturers and sawmill operators are concerned about winter timber supplies. Wbolesale finns are worried about winter inventcies of sawlogs for related reasons. Sawmills are concerned about high stumpage prices (dircctly related to a shortage of timber supplies) because they end up in the final cost of their product. Wholesalers are concerned because higher product prices create more opportunities for oe final customer to use softwood and non-wood substitutes in place of hardwood
(coninued on page 14)
By Bernard J. Tomasko Executive Vice President Wood Moulding & Millwork Producers Association
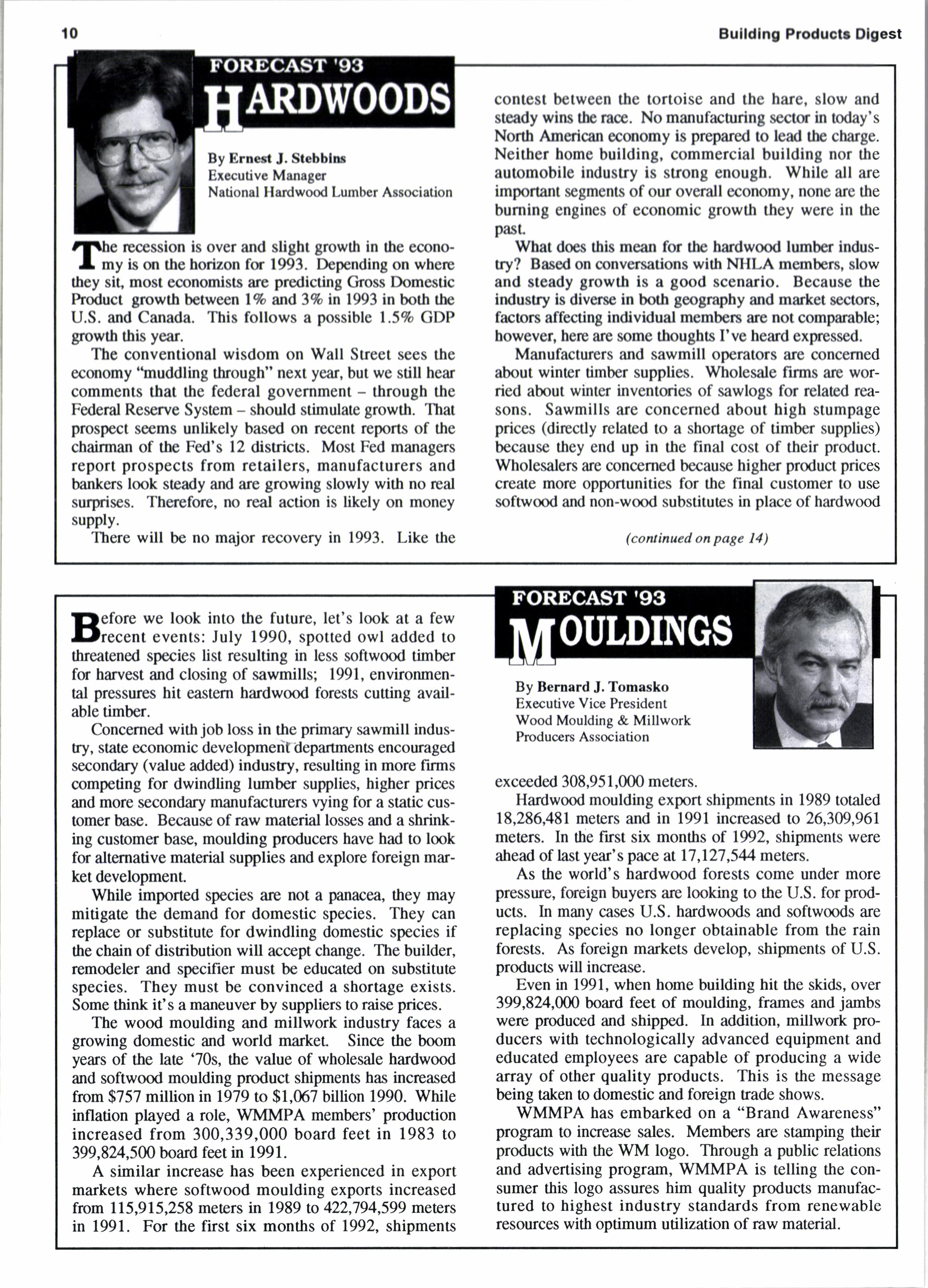
exceeded 308,95 1,000 meters.
Hardwood moulding export shipments in 1989 totaled 18,286,481 meters and in 1991 increased to 263@,961 meters. In the frst six months of 1992, shipments were ahead of last year's pace at 17,127,54 meters.
As the world's hardwood forests come under more priessure, foreign buyers are looking to the U.S. for products. In many cases U.S. hardwoods and softwoods are replacing species no longer obtainable from the rain forests. As foreign markets develop, shipments of U.S. products will inoease.
Even in 1991, when home building hit the skids, over 399,824,000 board feet of moulding, frames and jambs were produced and shipped. In addition, millwork producers with technologically advanced equipment and educated employees are capable of producing a wide array of other quality products. This is the message being taken to domestic and foreign trade shows.
WMMPA has embarked on a "Brand Awareness" program to increase sales. Members are stamping their products with the WM logo. Through a public relations and advertising program, WMMPA is telling the consumer this logo assures him quality products manufactured to highest industry standards from renewable resources with optimum utilization of raw material.
t|aheAmerican Wood Preservers Institute deals with ! issues - mostly outside lumber treating plant and sawmill gates - that affect our ability to manufacture and sell rea@d wood products.
Arkansas Gov. Bill Clinton has successfully pursued his immediate objective of getting elected president. What does his presidency mean for Eeated lumber markets? Not that much, in my view, in the sense that the stage had already been set for 1993, regardless of which candidate was elected. This is generally good news.
Spring '93 will see gradual improvement in housing and related market sectors, including treated wood product sales. High hopes for "change" could translate into general consumer confidence and renewed spending. Couple this with pent up demand for housing after three weak years and we can be mildly optimistic.
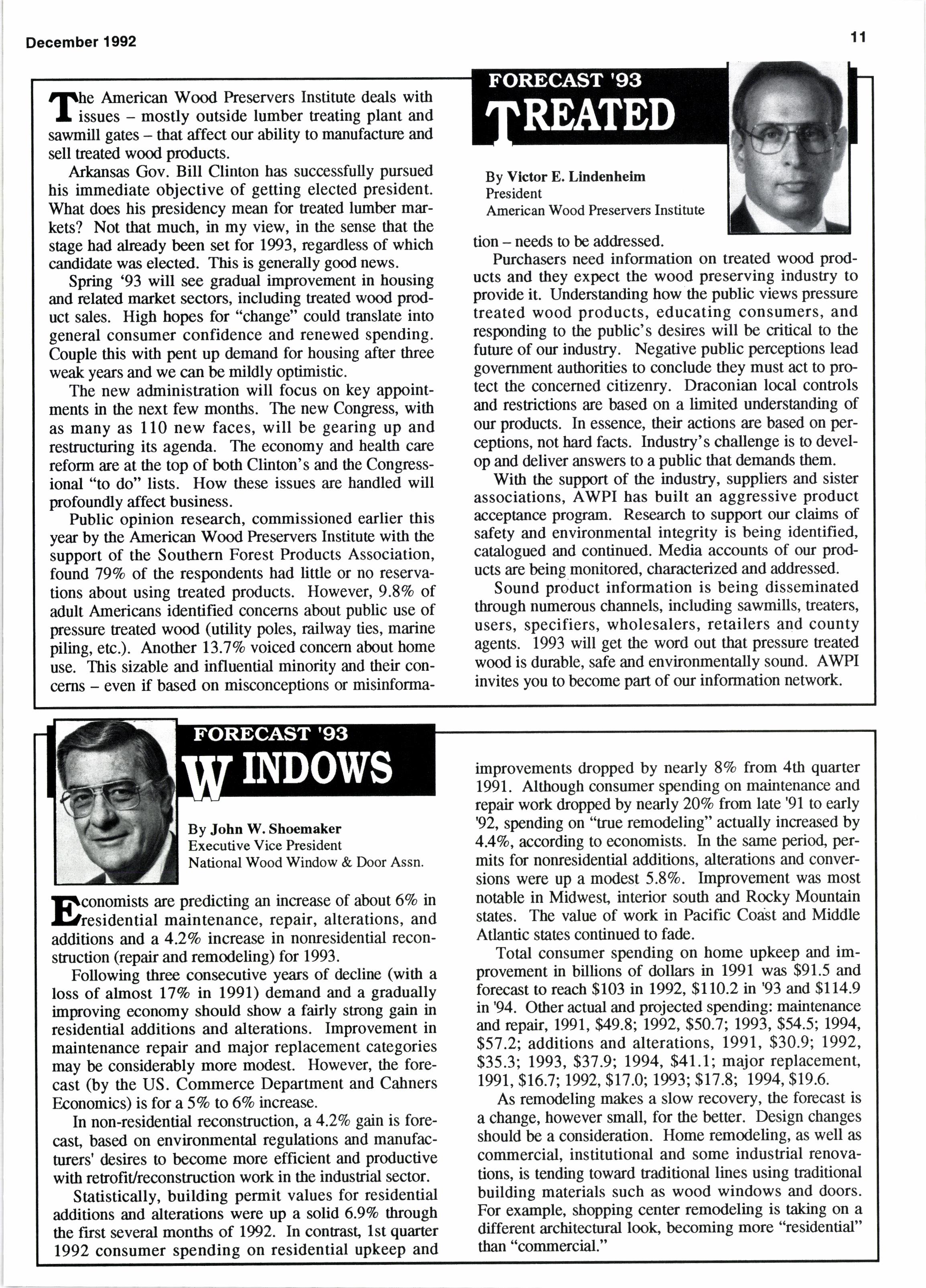
The new administration will focus on key appointments in the next few months. The new Congtess, with as many as 110 new faces, will be gearing up and restrucfiring its agenda. The economy and health care reform are at the top of both Clinton's and the Congressional "to do" lists. How these issues are handled will profoundly affect business.
Public opinion research, commissioned earlier this year by the American Wood Preservers Institute with the support of the Southern Forest Products Association, foundT9?o of the respondents had little or no reservations about using treated products. However, 9.87o of adult Americans identified concerns about public use of pressure fteated wood (utility poles, railway ties, marine piling, erc.). Another l3.7Vo voicnd concern about home use. This sizable and influential minority and their concerns - even if based on misconceptions or misinforma-
By Ylctor E. Llndenheln President American Wood Preservers Institute
tion - needs to be addressed.
Purchasers need information on treated wood products and they expect the wood preserving industry to provide it. Understanding how the public views pressure treated wood products, educating consumers, and responding to the public's desires will be critical to the future of our industry. Negative public perceptions lead govemment authorities to conclude they must ilct to prG tect the concerned citizenry. Draconian local controls and restrictions are based on a limited understanding of our products. In essence, their actions are based on perceptions, not hard facts. Industry's challenge is to develop and deliver answers to a public that demands them.
With the support of the industry, suppliers and sister associations, AWPI has built an aggressive product acc€ptance progam. Research to support our claims of safety and environmental integrity is being identified, catalogued and continued. Media accounts of our products are being monitored, characterized and addressed.
Sound product information is being disseminated through numerous channels, including sawmills, treaters, users, specifiers, wholesalers, retailers and county agents. 1993 will get the word out that pressure Eeated wood is durable, safe and environmenraily sound. AWPI invites you to become pafi of our infonnation netwmk.
By John lV. Shoemaker Executive Vice President National Wood Window & Door Assn.
pconomists are predicting an increase of about 67o in lZresidential maintenance, repair, alterations, and additions and a 4.2Vo increase in nonresidential reconstruction (repair and remodeling) for 1993.
Following three consecutive years of decline (with a loss of alnost l74o rn 1991) demand and a gradually improving economy should show a faidy strong gain in residential additions and alterations. Improvement in maintenance repair and major replacement categories may be considerably more modest. However, the forecast (by the US. Commerce Department and Cahners Economics) is for a SVo to 6Vo increase.
In non-residential reconstruction, a 4.2Vo gun is forecast, based on environmental regulations and manufacurers' desires to become more efficient and productive with refofit/reconstruction work in the indusUial sector.
Statistically, building permit values for residential additions and alterations were up a solid 6.97o through the first several months of 1992. In contrast, lst quarter 1992 consumer spending on residential upkeep and improvements dropped by nearly 87o from 4th quafier 1991. Although consumer spending on maintenance and repair work dropped by nearly 204o from late'91 to early 92, spending on "true remodeling" actually increased by 4.4Vo, rcarding to economists. h the same period, permits for nonresidential additions, alterations and conversions were up a modest 5.87o. Improvement was most notable in Midwest, interior south and Rocky Mountain states. The value of work in Pacific Coast and Middle Atlantic statos continued to fade.
Total consumer spending on home upkeep and improvement in billions of dollars in 1991 was $91.5 and forecast to reach $103 in 1992, Sll0.2 in '93 and $114.9 in'94. Other actual and projected spending: maintenance and repair, 1991, $49.8; 1992,$50.7;1993, $54.5; 1994, $57.2: additions and alterations, 1991, $30.9; 1992, $35.3; 1993, $37.9; 1994, $41.1; major replacement, 1991, $16.7; 1992,$17.0;1993; $17.8; 1994, $19.6.
As remodeling makes a slow recovery, the forecast is a change, however small, for the better. Design changes should be a consideration. Home remodeling, as well as commercial, institutional and some industrial renovations, is tending toward naditional lines using traditional building materials such as wood windows and doors. For exarnple, shopping center remodeling is taking on a different architecural loolq becoming more "residential" than "commercial."
By Robcrr H. Hunt Prosidcnt Wostcrn Wood hoductr Ae$ciation
f,Jo industry bas been more affect- Iled by Oe economic slowdown than lumber manufruring in the 12state western woods region of tbe U.S. WWPA believe.s the economy is ready 30 r€build, but will environmental constraints in tbe west allow enougb raw material (timb6) to meet the lumber needs?
Short term, the answer is yes. Long term, we're looking for the final answer.
It may be more positive than we Oink because - strangely enoughtbe world's environment will be better off if more struculres are built of wood than alternative nnterials.
Most of the set aside is public timber - federally managed national forests or timber operated by the Bureau of Land Management. This bas forced the western industry to rely on privately held forests which cannot offset the loss of production from federal lands. Nevertheless, log stocks are ample enough to meet expected demand for the coming months. A year ago, many western mills drew logs from a variety of sources, thinking demand would be up in 192. Since it wasn't, that raw material is available.
Loolc for things to tighten in 1993 especially if the economy improves. Surplus reserves will be worked down and the indusry will be operating from limited sources of supply. When that happens, supply and demand imbalances are apt to bring volatility in lumber prices as we have seen this year.
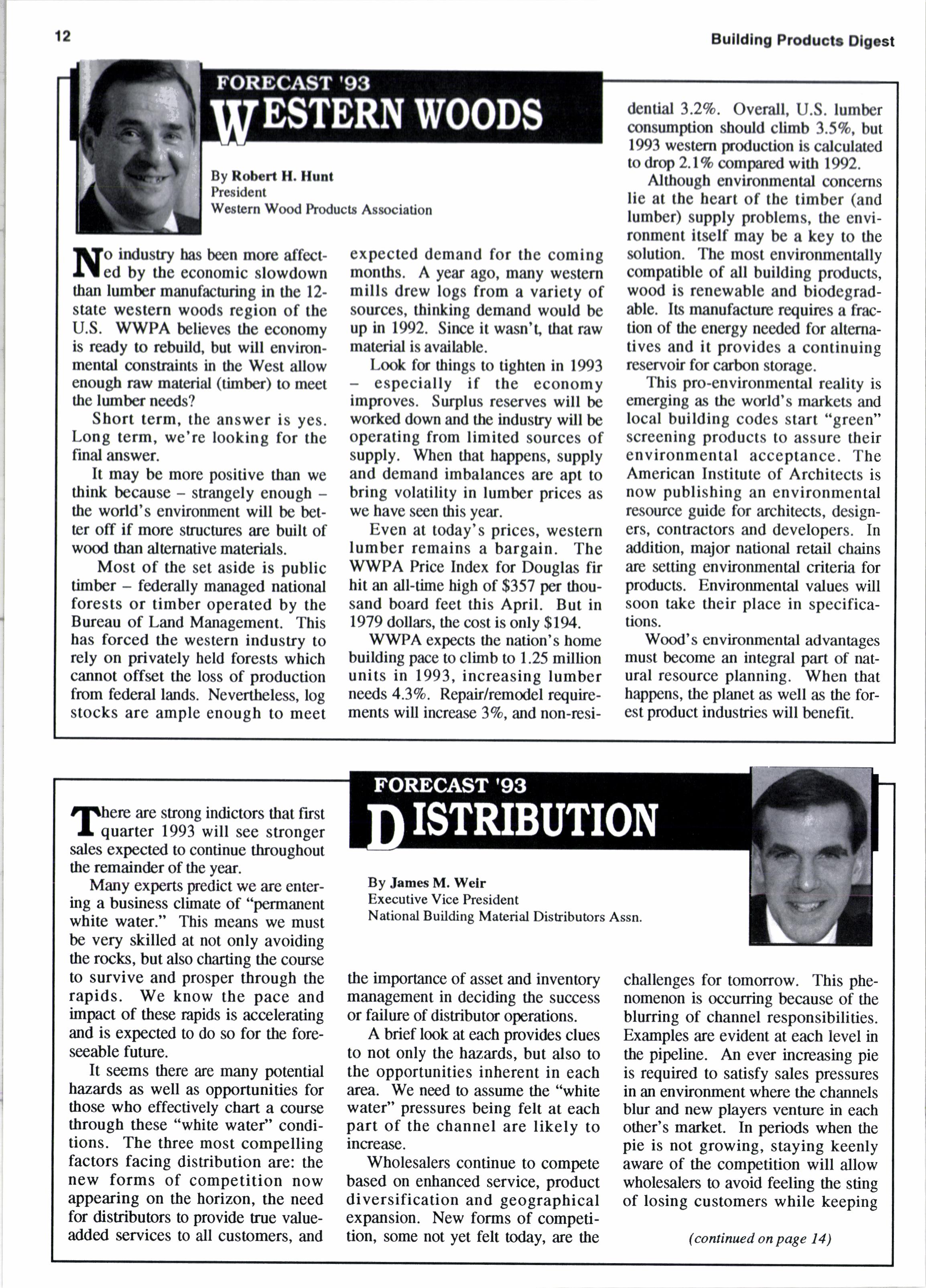
Even at ioday's prices, western lumber remains a bargain. The WWPA Price Index for Douglas fir hit an all-time high of $357 per thousand board feet this April. But in 1979 dollars, the cost is only $llX.
WWPA expects the nation's home building pace to climb to 1.25 million units in 1993, increasing lumber needs 4.3Vo. Repair/remodel requirements will increase 3Vo, and non-resi- dential 3.2%. Overall, U.S. lumber onsumpion should climb 3.5%, but 1993 western production is calculated to drop 2.1% compared wirh 1992. tflhere are strong indictors that frst I quarter 1993 will see stronger sales expected to continue throughout the remainderof the year.
Althougb environmental @ncerns lie at the heart of tbe timber (and lumber) supply problems, the environment itself may be a key to Oe solution. The most environmurtally compatible of all building producrs, wood is renewable and biodegradable. Its manufacture requires a fraction of he energy needed for alternatives and it provides a continuing reservoir for carbon storage.
Tbis pro-environmental reality is emerging as the world's markets and local building codes start "green" screening products to assure their environmental acceptance. The American Institute of Architects is now publishing an environmental resource guide for architects, designers, contractors and developers. In addition, major national retail chains are s€tting environmental criteria for products. Environmental values will soon take Oeir place in specifications.
Wood' s environmental advantages must become an integral piut of natural resource planning. When that happens, the planet as well as the forest product industries will benefit.
Many experts predict we are entering a business climate of "permanent white water." This means we must be very skilled at not only avoiding the rocks, but also charting the course to survive and prosper through the rapids. We know the pace and impact of these rapids is accelerating and is expected to do so for the foreseeable future.
It seems there are many potential hazards as well as opportunities for those who effectively chart a oourse through these "white watet''conditions. The three most compelling factors facing distribution are: the new forms of competition now appearing on tle horizon, the need for distributors to provide true valueadded services to all cus0omers. and
By James M. Welr Executive Vice President National Building Material Disbibutors Assn.
the importance of asset and inventory management in deciding the success or failure of distributm operations.
A brief look at each provides clues to not only the hazards, but also to the opportunities inherent in each area. We need to assume the "white water" pressures being felt at each part of the channel are likely to increase.
Wholesalers continue to compete based on enhanced service, product diversification and geographical expansion. New forms of competi[ion, some not yet felt today, are the challenges for tomorrow. This phenomenon is occurring because of the blurring of channel responsibilities. Examples are evident at each level in the pipeline. An ever increasing pie is required to satisfy sales pressures in an environment where the channels blur and new players venture in each other's market. In periods when the pie is not growing, staying keenly aware of the competition will allow wholesalen to avoid feeling the sting of losing customers while keeping (continued on page 14) lfflll the upward trend of the UU structural panel industry be maintained in 1993? We think so, even though our predictions were developed during a period of uncertainty in the national mood preceding the November election.
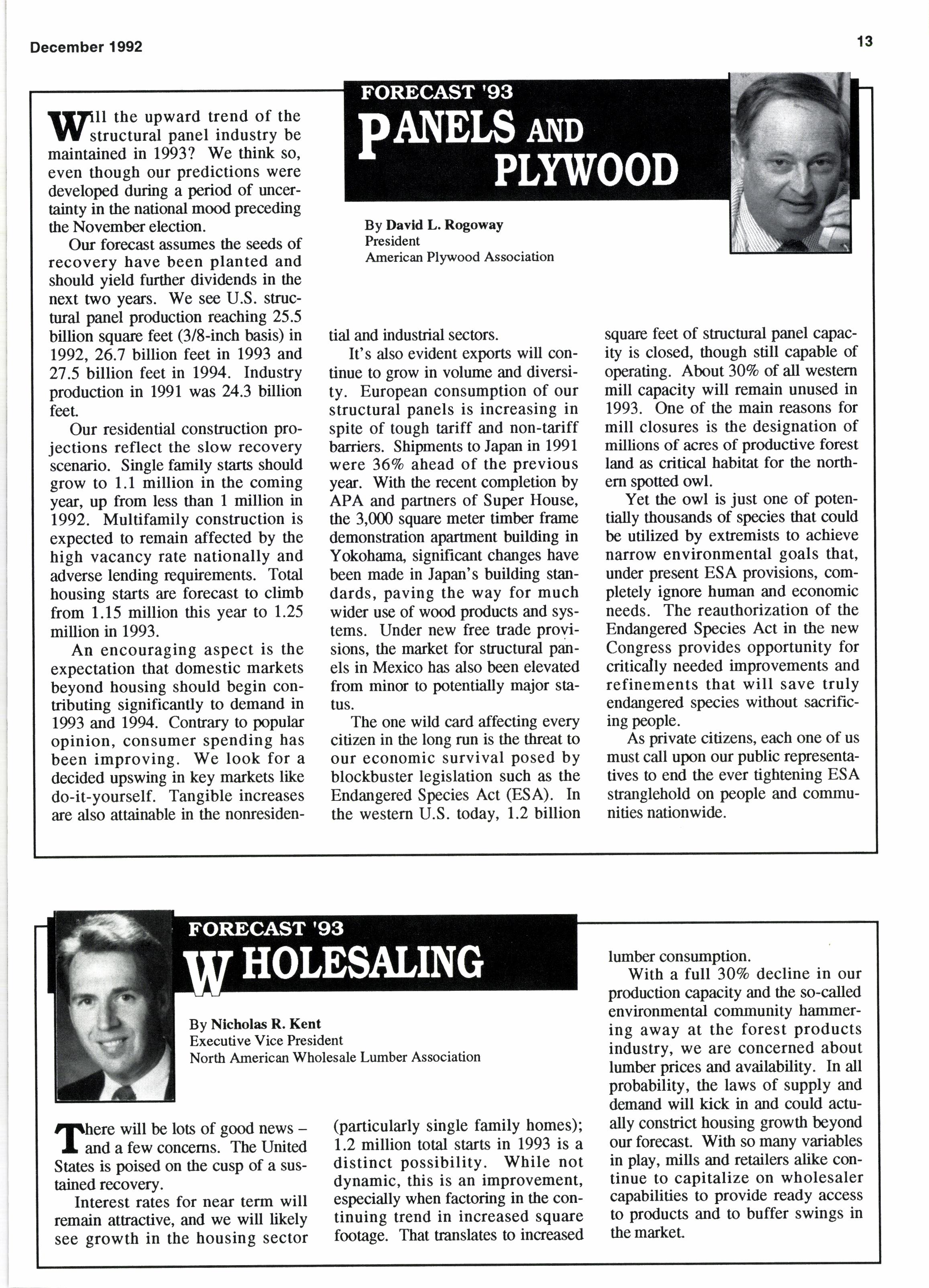
Our forecast assumes the seeds of recovery have been planted and should yield further dividends in the next two years. We see U.S. structural panel production reaching 25.5 billion squarc feet (3/8-inch basis) in 1992,26.7 billion feet in 1993 and 27.5 billion feet in 1994. Indusffy production in 1991 was 4.3 billion feet
Our residential construction projections reflect tle slow recovery scenario. Single fanily starts should grow to 1.1 million in the coming year, up from less than I million in 1992. Multifamily construction is expected to remain affected by the high vacancy rate nationally and adverse lending requirements. Total housing starts are forecast to climb from 1.15 million this year to 1.25 million in 1993.
An encouraging aspect is the expectation that domestic markets beyond housing should begin contributing significantly to demand in 1993 and 19!X. Conrary to popular opinion, consumer spending has been improving. We look for a decided upswing in key markets like do-it-yourself. Tangible increases are also attainable in the nonresiden-
By Davld L. Rogoway President American Plywood Association
tial and industrial sectors.
It's also evident expor8 will continue to grow in volume and diversity. European consumption of our structural panels is increasing in spite of tough tariff and non-tariff barriers. Shipments to Japan in 1991 were 36Vo ahead of the previous year. With the recent completion by APA and partners of Super House, the 3,000 square meter timber frame demonstration aparEnent building in Yokohama significant changes have been made in Japan's building standards, paving the way for much wider use of wood products and systems. Under new free trade Provisions, the market for sructural panels in Mexico has also been elevated from minor to potentially major status.
The one wild card affecting every citizen in the long run is the threat to our economic survival posed by blockbuster legislation such as the Endangered Species Act (ESA). In the western U.S. today, 1.2 billion squarc feet of strucural panel capacity is closed, though still capable of operating. About 304o of all western mill capacity will remain unused in 1993. One of the main reasons for mill closures is the designation of millions of acres of productive forest land as critical habitat for the northern spotted owl.
Yet the owl is just one of potentially thousands of species that could be utilized by extremists to achieve naffow environmental goals that, under present ESA provisions, completely ignore human and economic needs. The reauthorization of the Endangered Species Act in the new Congress provides opportunity for critically needed improvements and refinements that will save truly endangered species without sacrificing people.
As private citizens, each one of us must call upon our public representatives to end the ever tightening ESA stranglehold on people and communities nationwide.
By Nlcholas R. Kent Executive Vice President North American Wholesale Lumber Association
tlahere will be lots of good newsI and a few concems. The United Sta8e,s is poised on the cusp of a sustained recovery.
Interest rates for near term will remain attractive, and we will likely see growth in the housing sector
(particularly single family homes);
1.2 million total starts in 1993 is a distinct possibility. While not dynamic, this is an improvement, especially when factoring in the continuing trend in increased squitfe footage. That hanslates to increased lumber consumption.
With a full307o decline in our production capacity and the so-called environmental community hammering away at the forest products industry, we are concerned about lumber prices and availability. In all probability, the laws of supply and demand will kick in and could actually consuict housing growth beyond our forecast. With so many variables in play, mills and retailers alike continue to capitalize on wholesaler capabilities to provide ready access to products and to buffer swings in themarket
By Kerl W. Llndber3 President Soutbern Forest Products Agsociation
fust as the daily weather varies across lhe nation, so iJ does the extended forecast for the lumber indusry in 1993. Partly cloudy in the west wirh stonns in the ancient forests; partly sunny in the south with a wamr front continuing in southern pine producing territory. The economy remains uncerlain, but we expect to get a better fix on it with the initial actions of the new president.
The southern pine lumber industry is prepared to either ride out a stonn or make hay while the sun shines because for the past eight years it has diversified demand through the Marketing Marathon program.
The program's key strategy is relying less on the diminished home-building market and morc on develop ment of new, value-added markets such as exports, industrial, repair & remodeling, engineered wood systems and treated residential. As a result, southern pine production has zoomed from l0 billion board feet to what may reach 14 billion board feet for 1992, during a period when housing starts tailed ofl plunging to a 46 year low in 191.
Mexico is showing enonnous potential for exports of southem pine, and preliminary work is underway in the Middle Fast to stimulate demand. A promising furniture market is opening up, while more and better timber
Dlstrlbutlon Forecast
( continued from page I 2) watch for how to serve a potentially different customer base.
Value-added services are in the eyes of the beholder. Not all customers in this new environment need, want, nor are willing to pay for the sane services. Flexibility will be the key to the wholesaler's ability to serve each customer's unique requirements.
These services are value-added when the customer perceives them as being provided in a manner more efficient/effective than they could perforrr them for thenselves or have them done by the competition. Wholesalers looking to maintain their market share and seize new opportunities will closely moniton the special requirements of their customer base and stay as close to them as possible.
Asset and inventory management have always been key management barometers. In the "white water" environment, they can be critical, perhaps unforeseen, hazards inflicting the heaviest darnge. Wholesalers can no longer look to growth to solve all ills. Financial management and partnerships with suppliers and customers will determine the companies that prosper in an environment of constant change. Study after study points to the fact that profitable wholesalers are those who consistently out-perfomr their b,ridges, morc marine applications and steady progress in using southcm pine for highway sound barrien occur. competition. These companies accomplish this through incremental management improvements and constant monitoring of these two critical financial measures - asset and inventory miuragement.
Development of sbop grades will talce advantage of ftesh demand for southem pine for mouldings, paneling, window stock and otber industrial uses. Empirical design values based on the In-Grade Testing Progran give southem pine advantages and we'rc developing a lmd rcsistance frctor design manual o intnoduce reliability-based design formulations into structural wood construction. Finally, tbe treated markets keep booming as bomeowners tum to decks, gazebos, sheds and otber outdoor living amenities.
Certainly tber,e is competition. The lumber industry has !o fight off concr,ete, steel and plastic, even though we have the environmental edge on these non-wood products, plus aesthetic and construction advantages. Competition from foreign species imported from Cbile and Russia will only get stronger.
But our greatest problem is timber supply. Preservationists struck first and hardest in the Pacific Northwest, using spotted owls, timber sale appeals and litigation to stop harvesting not just on public lands, but on private land as well. The same tactics are being used in the South, with the endangered red<ockaded woodpecker and a last ditch fight over the definition of wetlands.
Although tbe South recognizes its temporary benefit from timber supply constraints in the West, it knows it's only a matter of time before the straitjackets are fastened in our region. We hold out hope and will exert every effort o convince the public and elected officials that we are responsible stewards who grbw, harvest and replenish trees to produce lumber, plywood and paper the nation needs for useful products, tbousands ofjobs and a healthy economy.
Hardwood Forecast
(continued from page I 0) lumber. Lumber buyers in the furniture, millwork, flooring and industrial markets seem to have analyzed the concerns of both sawmillers and wholesalers in that they are doing their best to book business longer ahead. Adding up observations from these three sectors gives a clear look at ttre big picnre.
What pressures will slow economic growth place on a trade association such as NHLA in 1993? I think we will be listening to our customers (members). Just like their hardwood lumber customers, members want us to deliver a better product in 1993, and I expect there will be some price resistance at the margin. Right now, we are strerched to the limit to deliver programs members tell us they want: public education, legislative affairs, hardwood promotion, training programs, inspection service and it goes without saying, promulgating and teaching standard grading rules. A recent membership poll showed that NHLA members believe public education (on forestry issues) is the No. I progmm the association should continue to work on.
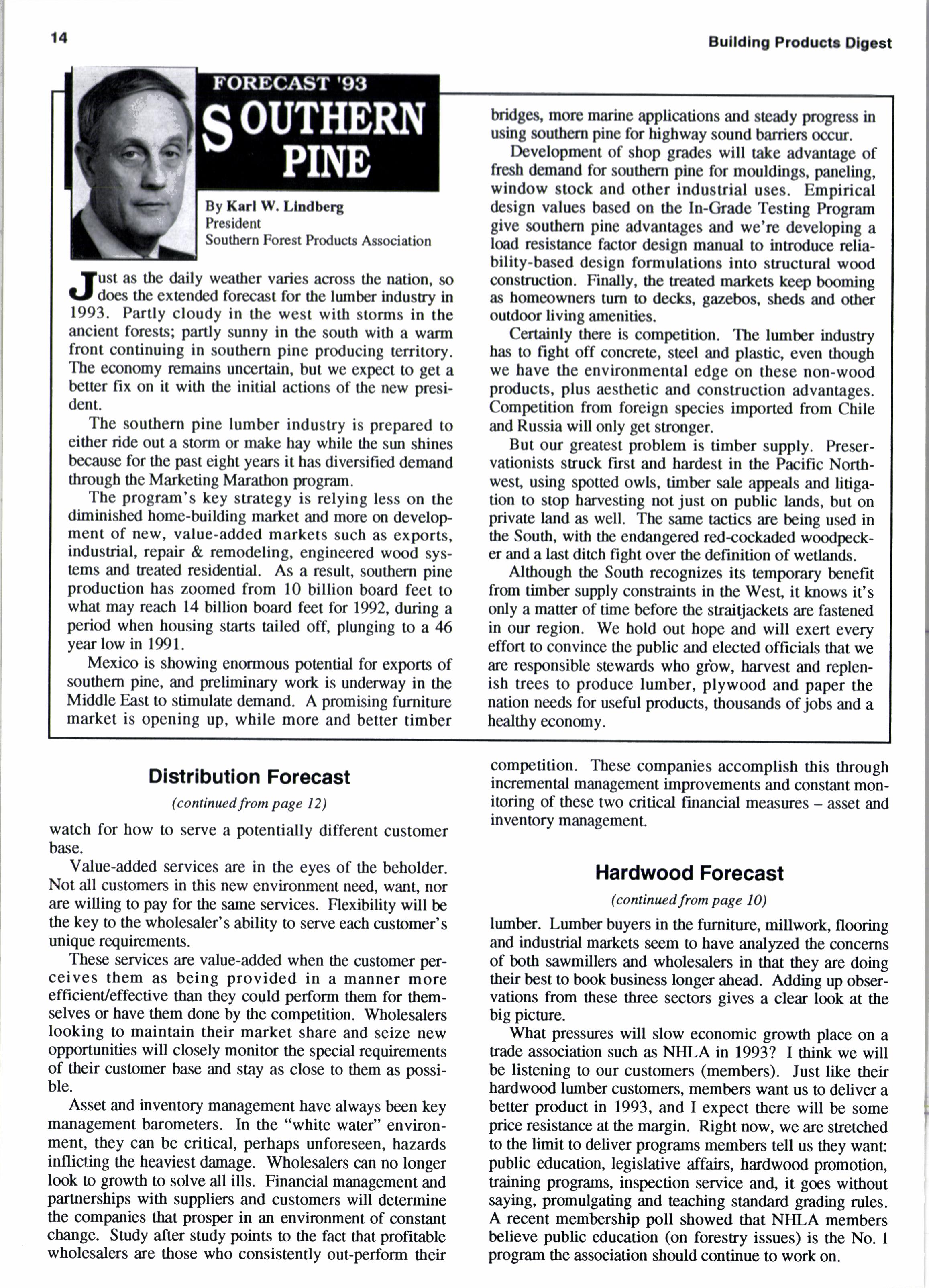
l\espite economic downturns, engiIJneered lumber products (ELP) will continue o gather greater market share over the rest of the decade.
A large part of the growth will come in the repair and remodeling market where expenditures could climb to over $100 billion by the end of the 1990s, George Carter, George Carter & Affiliates, forecasts.
Lack of knowledge on the Part of builders, architects and retailers is about the only negative seen ahead for ELP which includes wood I-beams, laminated veneer lumber (LVL), glulam beams, parallel strand lumber (PSL) and parallel chord trusses. Increased consumption of all ELP except wood I-beams is anticipated.
Story at a Glance
Opportunities in engineered lumber products market will continue to climb ... $100 billion possible by end of decade Gonsumption will increase for all ELP excePt wood l-beams which will be replaced by parallel strand lumber.