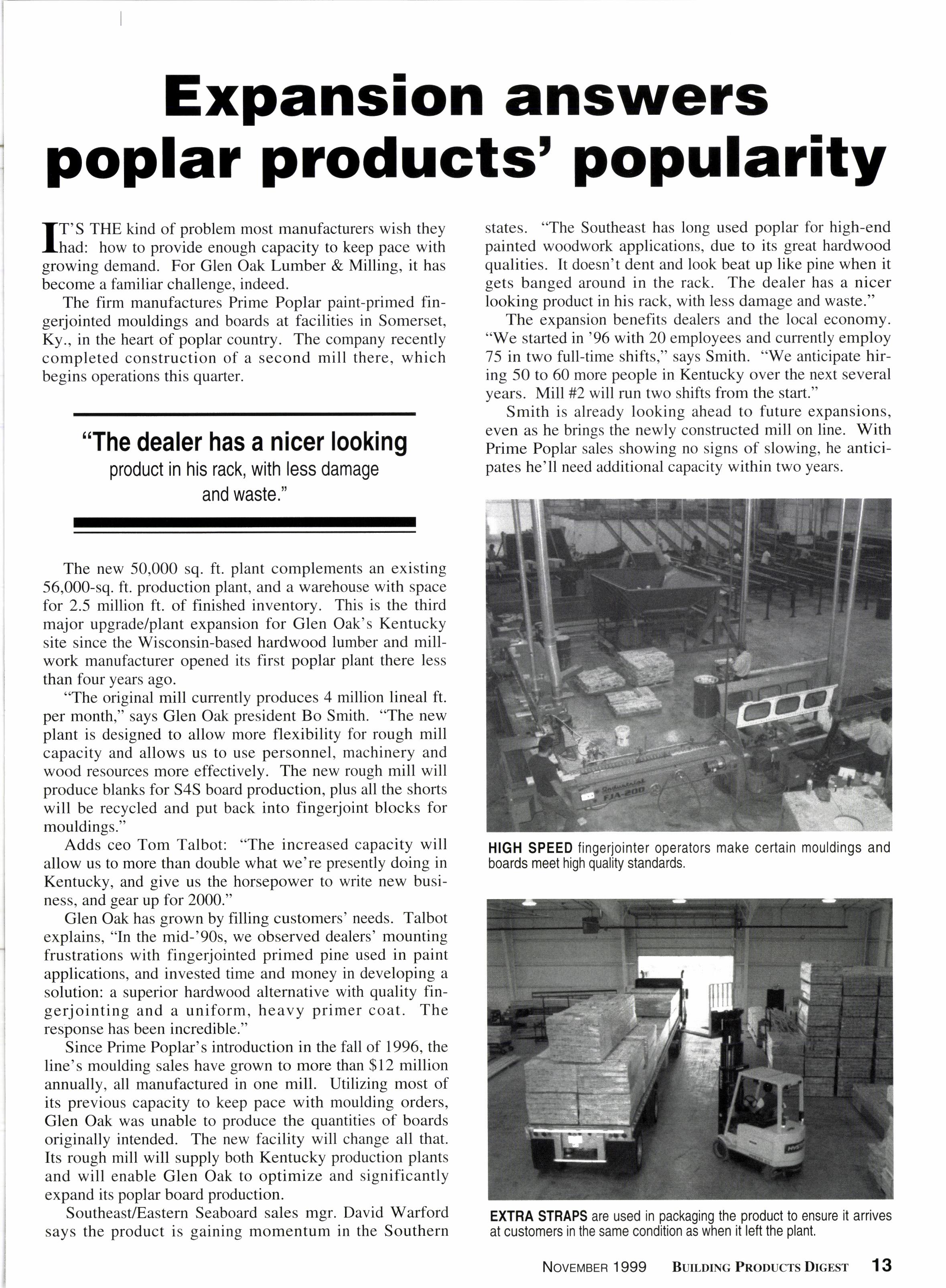
2 minute read
Expansion answers popl ar products' popularity
fT'S THE kind of problem most manufacturers wish they lhad: how to provide enough capacity to keep pace with growing demand. For Glen Oak Lumber & Milling, it has become a familiar challenge, indeed.
The firm manufactures Prime Poplar paint-primed fingerjointed mouldings and boards at facilities in Somerset, Ky., in the heart of poplar country. The company recently completed construction of a second mill there, which begins operations this quarter.
states. "The Southeast has long used poplar for high-end painted woodwork applications, due to its great hardwood qualities. It doesn't dent and look beat up like pine when it gets banged around in the rack. The dealer has a nicer looking product in his rack, with less damage and waste."
The expansion benefits dealers and the local economy. "We started in '96 with 20 employees and currently employ 75 in two full-time shifts," says Smith. "We anticipate hiring 50 to 60 more people in Kentucky over the next several years. Mill #2 will run two shifts from the start."
Smith is already looking ahead to future expansions, even as he brings the newly constructed mill on line. With Prime Poplar sales showing no signs of slowing, he anticipates he'11 need additional capacity within two years.
The new 50,000 sq. ft. plant complements an existing 56,000-sq. ft. production plant, and a warehouse with space for 2.5 million ft. of finished inventory. This is the third major upgrade/plant expansion for Glen Oak's Kentucky site since the Wisconsin-based hardwood lumber and millwork manufacturer opened its first poplar plant there less than four years ago.
"The original mill currently produces 4 million lineal ft. per month," says Glen Oak president Bo Smith. "The new plant is designed to allow more flexibility for rough mill capacity and allows us to use personnel, machinery and wood resources more effectively. The new rough mill will produce blanks for S4S board production, plus all the shorts will be recycled and put back into fingerjoint blocks for mouldings."
Adds ceo Tom Talbot: "The increased capacity will allow us to more than double what we're presently doing in Kentucky, and give us the horsepower to write new business, and gear up for 2000."
Glen Oak has grown by filling customers' needs. Talbot explains, "In the mid-'90s, we observed dealers' mounting frustrations with fingerjointed primed pine used in paint applications, and invested time and money in developing a solution: a superior hardwood alternative with quality fingerjointing and a uniform, heavy primer coat. The response has been incredible."
Since Prime Poplar's introduction in the fall of 1996, the line's moulding sales have grown to more than $12 million annually, all manufactured in one mill. Utilizing most of its previous capacity to keep pace with moulding orders, Glen Oak was unable to produce the quantities of boards originally intended. The new facility will change all that. Its rough mill will supply both Kentucky production plants and will enable Glen Oak to optimize and significantly expand its poplar board production.
Southeast/Eastern Seaboard sales mgr. David Warford says the product is gaining momentum in the Southern
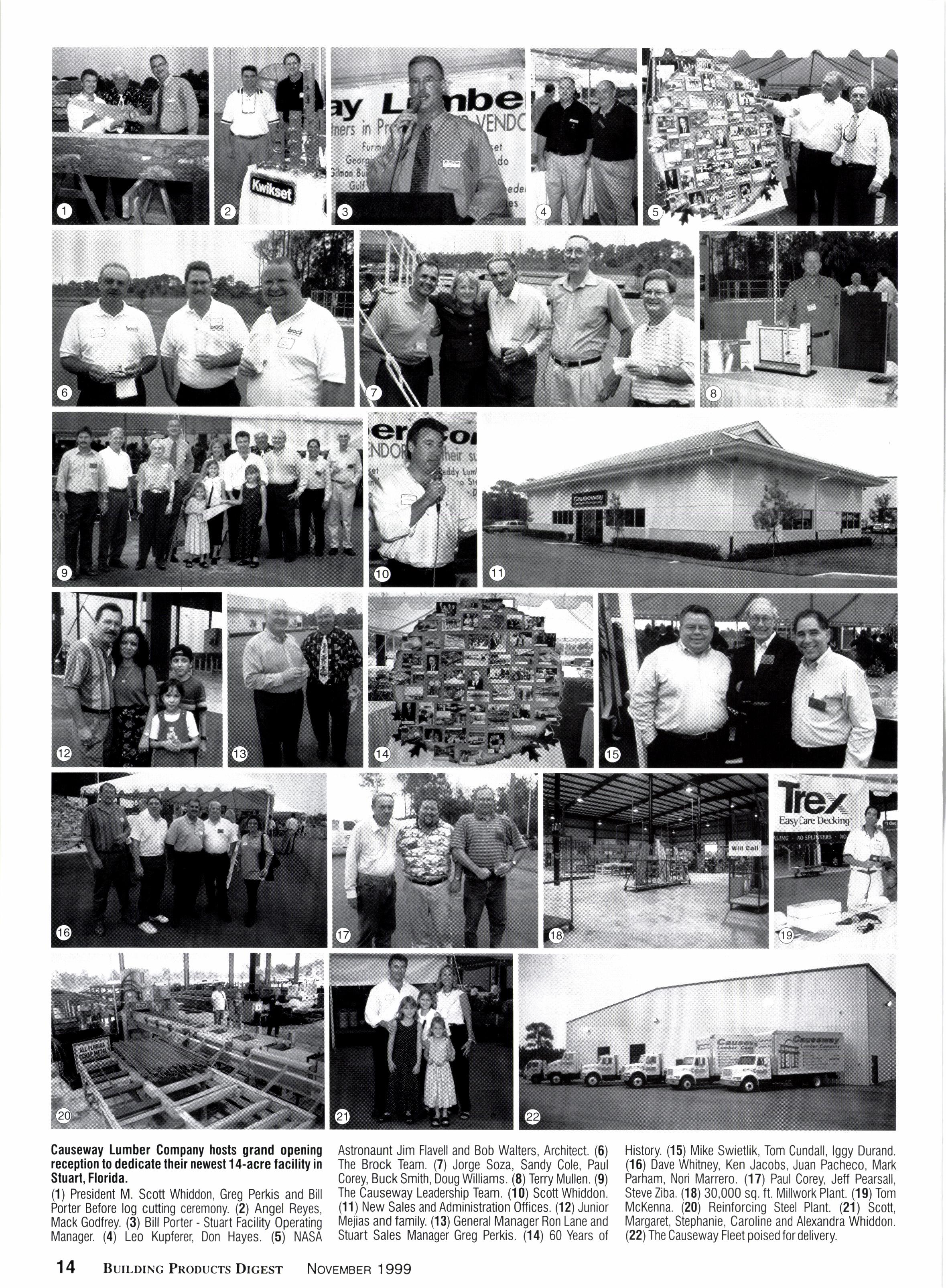