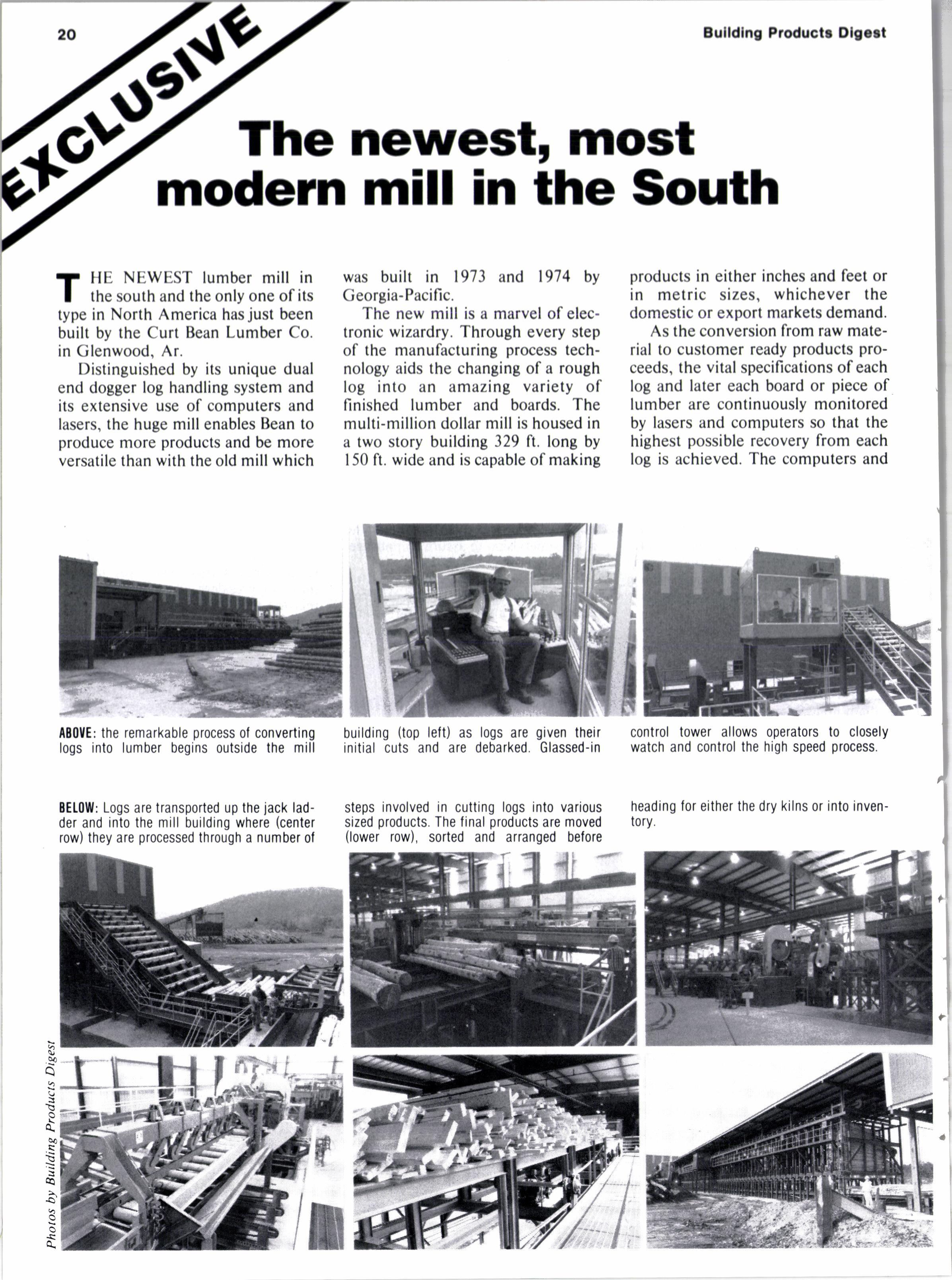
4 minute read
The newest, most modern mill in the South
T HE NEWEST lumber mill in I the south and the only one of its type in North America has just been built by the Curt Bean Lumber Co. in Glenwood. Ar.
Distinguished by its unique dual end dogger log handling system and its extensive use of computers and lasers, the huge millenables Bean to produce more products and be more versatile than with the old mill which was built in 1973 and 1974 by Ceorgia-Pacific.
The new mill is a marvel of electronic wizardry. Through every step of the manufacturing process technology aids the changing of a rough log into an amazing variety of finished lumber and boards. The multi-million dollar mill is housed in a two story building 329 ft.long by 150 ft. wide and is capable of making products in either inches and feet or in metric sizes, whichever the domestic or export markets demand.
As the conversion from raw material to customer ready products proceeds, the vital specifications ofeach log and later each board or piece of lumber are continuously monitored by lasers and computers so that the highest possible recovery from each log is achieved. The computers and their human operators can decide whether to cut for recovery or go for grade yield, seeking the maximum amount of product.
As the new mill gears up, production is gaining daily. Curt Bean is maintaining production at the old facility at a constant level so customers can rely on their usual supply of company products as the old mill is replaced by the new.
The appetite of the mill is huge. The former mill needed 85 log trucks daily to feed its saws; the new one needs 110 log trucks each day. The entire production is southern yellow pine.
Reports on the early production from the new mill have been enthusiastic about the quality of the products. "The investment in advanced technology has meant not only greater quantity, but a higher level of quality as well," notes Curt Bean.
Story at a Glance
l.|ew southern pine mill uses the latest in computer and lasertechnology to speed production, improvequality. itistheonlyone of irrs type in North America.
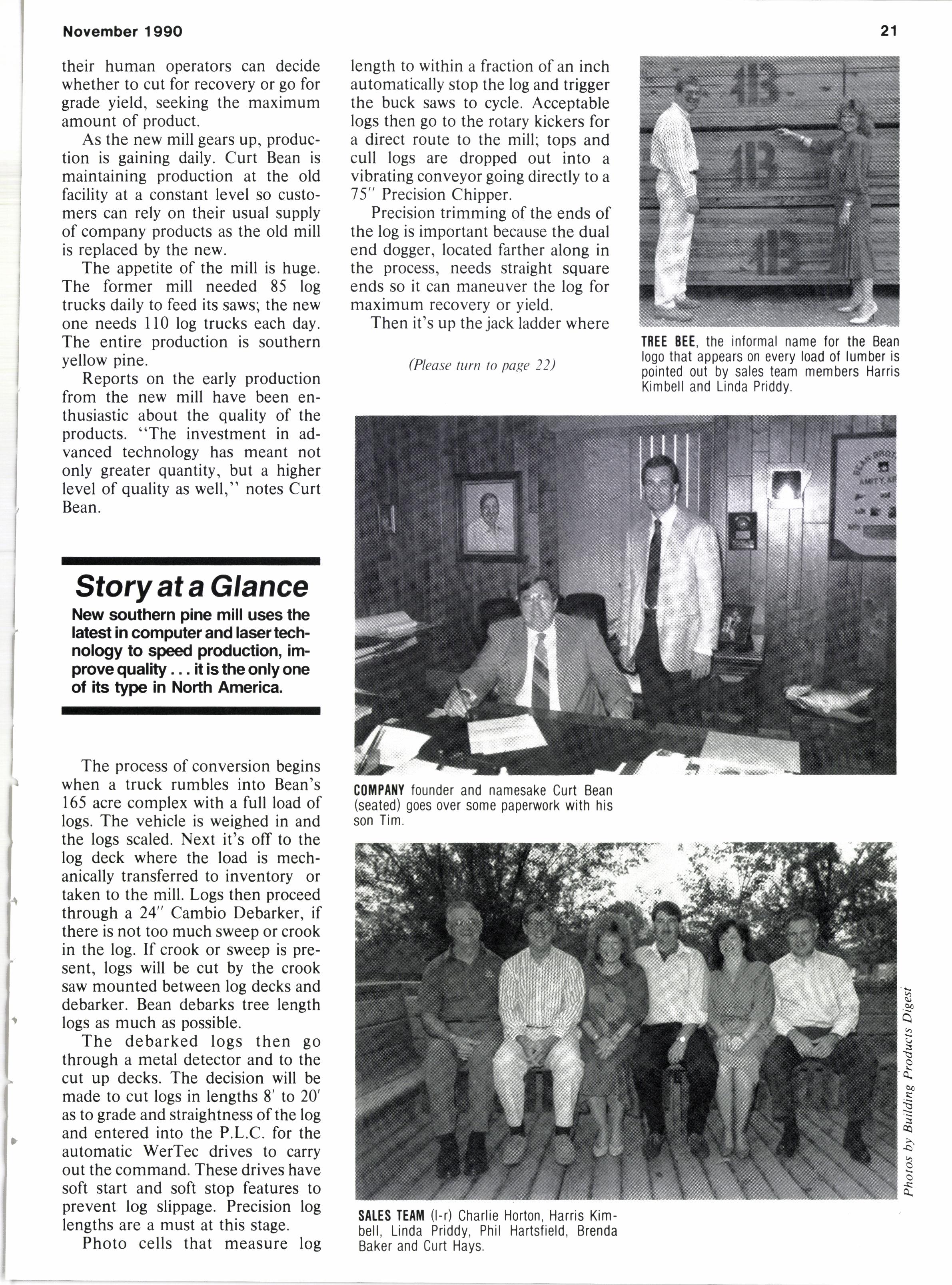
The process ofconversion begins when a truck rumbles into Bean's 165 acre complex with a full load of logs. The vehicle is weighed in and the logs scaled. Next it's off to the log deck where the load is mechanically transferred to inventory or taken to the mill. Logs then proceed through a 24" Cambio Debarker, if there is not too much sweep or crook in the log. If crook or sweep is present, logs will be cut by the crook saw mounted between log decks and debarker. Bean debarks tree length logs as much as possible.
The debarked logs then go through a metal detector and to the cut up decks. The decision will be made to cut logs in lengths 8' to 20' as to grade and straightness of the log and entered into the P.L.C. for the automatic WerTec drives to carry out the command. These drives have soft start and soft stop features to prevent log slippage. Precision log lengths are a must at this stage.
Photo cells that measure log length to within a fraction of an inch automatically stop the log and trigger the buck saws to cycle. Acceptable logs then go to the rotary kickers for a direct route to the mill; tops and cull logs are dropped out into a vibrating conveyor going directly to a 75" Precision Chipper.
Precision trimming of the ends of the log is important because the dual end dogger, located farther along in the process, needs straight square ends so it can maneuver the log for maximum recovery or yield.
Then it's up the jack ladder where
(Please turn to page 22)
Bsan'g New Mlll (Contlnued from pate 2l )
the logs enter the mill building for the first time. Here they are fed into the log optimizer where an operator, in a glass cage, manipulates scores of buttons on a computer console. Logs are XY scanned by the lasers and evaluated by computers as to length and diameter.
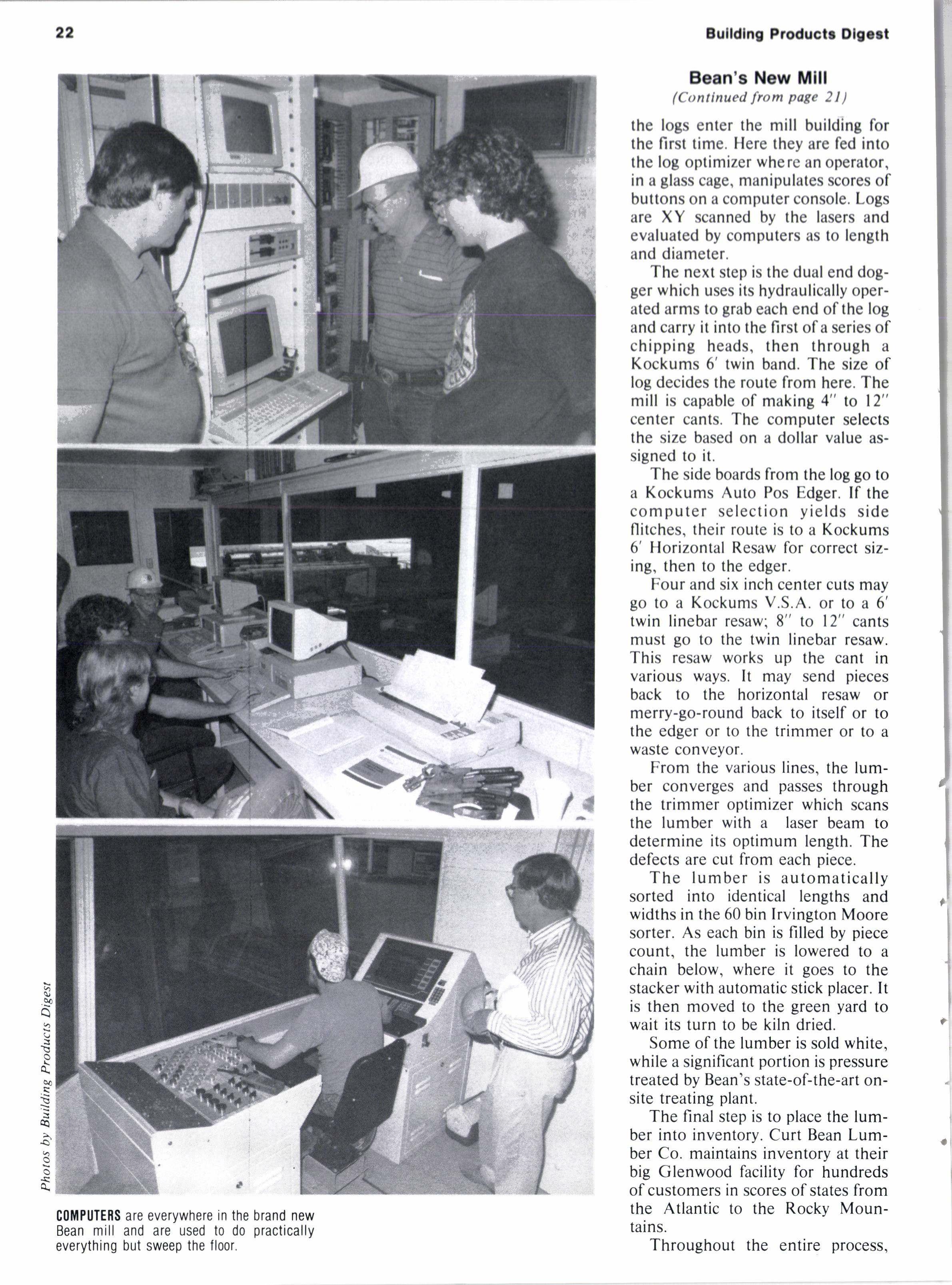
The next step is the dual end dogger which uses its hydraulically operated arms to grab each end of the log and carry it into the first of a series of chipping heads, then through a Kockums 6' twin band. The size of log decides the route from here. The mill is capable of making 4" to 12" center cants. The computer selects the size based on a dollar value assigned to it.
The side boards from the log go to a Kockums Auto Pos Edger. lf the computer selection yields side flitches, their route is to a Kockums 6' Horizontal Resaw for correct sizing, then to the edger.
Four and six inch center cuts may go to a Kockums V.S.A. or to a 6' twin linebar resaw; 8" to 12" cants must go to the twin linebar resaw. This resaw works up the cant in various ways. It may send pieces back to the horizontal resaw or merry-go-round back to itself or to the edger or to the trimmer or to a waste conveyor.
From the various lines, the lumber converges and passes through the trimmer optimizer which scans the lumber with a laser beam to determine its optimum length. The defects are cut from each piece.
The lumber is automatically sorted into identical lengths and widths in the 60 bin Irvington Moore sorter. As each bin is filled by piece count, the lumber is lowered to a chain below, where it goes to the stacker with automatic stick placer. It is then moved to the green yard to wait its turn to be kiln dried.
Some of the lumber is sold white, while a significant portion is pressure treated by Bean's state-of-the-art onsite treating plant.
The final step is to place the lumber into inventory. Curt Bean Lumber Co. maintains inventory at their big Glenwood facility for hundreds of customers in scores of states from the Atlantic to the Rocky Mountains.
Throughout the entire process, firm, and USNR, furnishing the trimmer, sorter and stacker equipment.
Like the true entrepreneur that he is, Curt Bean's decision to invest in building his advanced mill reflects his faith in the company, his employees, his customers and the American economy.
(Please turn to page 24 ) both logs and later lumber and boards have been monitored by the latest, most sophisticated electronic devices available. Hardhatted lumbermen inside the well-lighted building often spend as much time looking at computer screens as they do at logs. Never tiring lasers aid production decisions in the fast paced mill.
The main companies involved in building and equipping the showcase mill are Kockums Cancar, a Canadian firm furnishing the mill floor equipment, High Tech Engineering of Hot Springs, Ar., an engineering