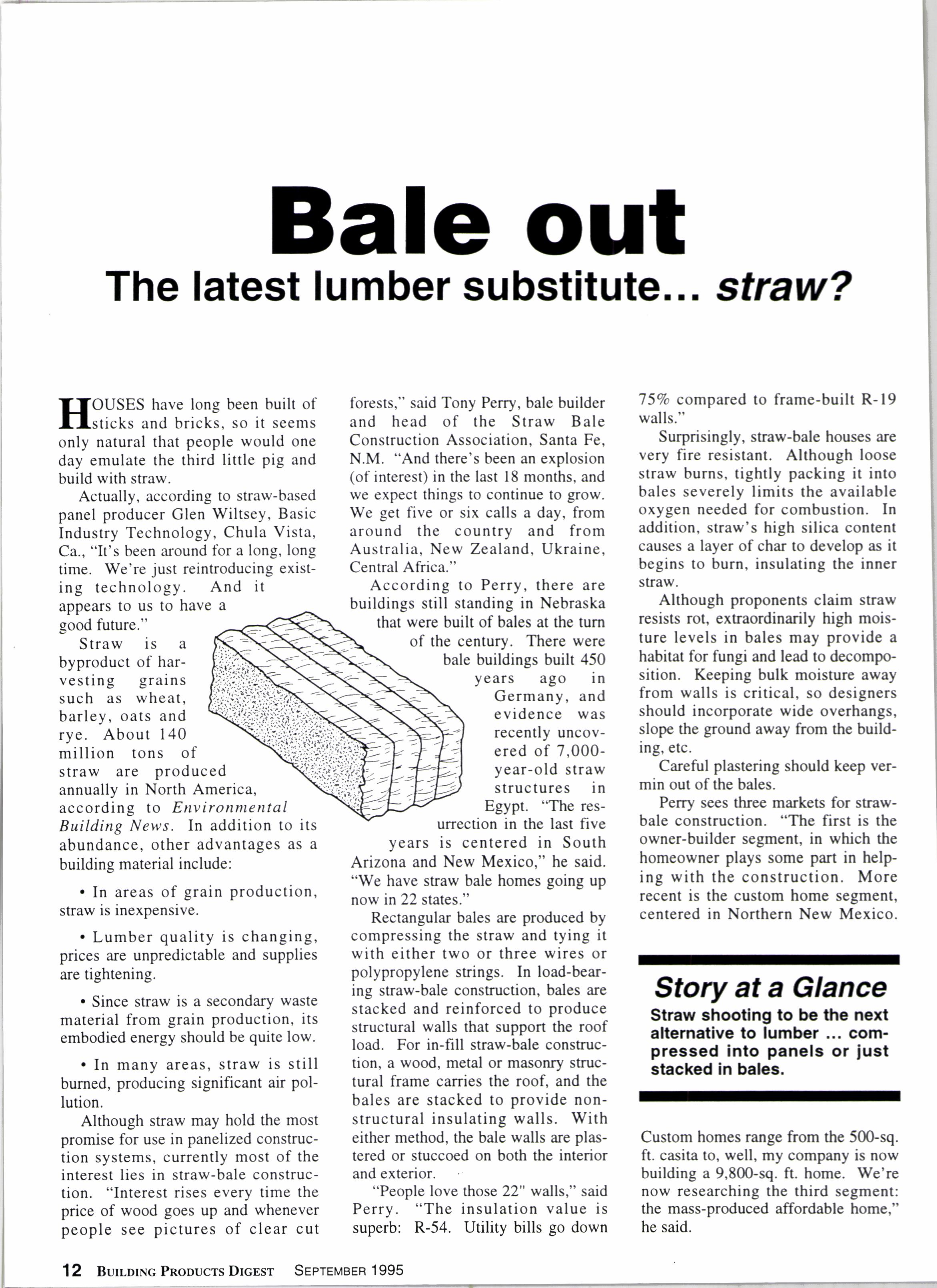
5 minute read
Bale out The latest lumber substitute... straw?
EI'OUSES have long been built of llsticks and bricks, so it seems only natural that people would one day emulate the third little pig and build with straw.
Actually, according to straw-based panel producer Glen Wiltsey, Basic Industry Technology, Chula Vista, Ca., "It's been around fbr a long, long time. We're just reintroducing existing technology. And it appears to us to have a good future."
Straw is a byproduct of harvesting grains such as wheat, barley, oats and rye. About 140 million tons of straw are produced annually in North America, according to Environntental Building News. In addition to its abundance, other advantages as a building material include:
. In areas of grain production, straw is inexpensive.
Lumber quality is changing, prices are unpredictable and supplies are tightening.
Since straw is a secondary waste material from grain production, its embodied energy should be quite low.
. In many areas, straw is still burned, producing significant air pollution.
Although straw may hold the most promise for use in panelized construction systems, currently most of the interest lies in straw-bale construction. "Interest rises every time the price of wood goes up and whenever people see pictures of clear cut forests," said Tony Perry, bale builder and head of the Straw Bale Construction Association, Santa Fe, N.M. "And there's been an explosion (of interest) in the last l8 months, and we expect things to continue to grow. We get five or six calls a day, from around the country and from Australia. New Zealand. Ukraine. Central Africa."
According to Perry, there are buildings still standing in Nebraska that were built of bales at the turn of the century. There were bale buildings built 450 years ago in Germany, and evidence was recently uncovered of 7,000year-old straw structures in Egypt. "The resurrection in the last five years is centered in South Arizona and New Mexico," he said. "We have straw bale homes going up now in 22 states."
Rectangular bales are produced by compressing the straw and tying it with either two or three wires or polypropylene strings. In load-bearing straw-bale construction, bales are stacked and reinforced to produce structural walls that support the roof load. For in-fill sraw-bale construction, a wood, metal or masonry structural frame canies the roof, and the bales are stacked to provide nonstructural insulating walls. With either method, the bale walls are plastered or stuccoed on both the interior and exterior.
"People love those 22" walls," said Perry. "The insulation value is superb: R-54. Utility bills go down
75?o compared to frame-built R-19 walls."
Surprisingly, straw-bale houses are very fire resistant. Although loose straw burns, tightly packing it into bales severely limits the available oxygen needed for combustion. In addition, straw's high silica content causes a layer of char to develop as it begins to burn, insulating the inner straw.
Although proponents claim straw resists rot, extraordinarily high moisture levels in bales may provide a habitat for fungi and lead to decomposition. Keeping bulk moisture away from walls is critical, so designers should incorporate wide overhangs, slope the ground away from the building, etc.
Careful plastering should keep vermin out of the bales.
Perry sees three markes for strawbale construction. "The first is the owner-builder segment, in which the homeowner plays some part in help ing with the construction. More recent is the custom home segment, centered in Northern New Mexico.
Story at a Glance
Straw shooting to be the next altemative to lumber compressed into panels or just stacked in bales.
Custom homes range from the 50Gsq. ft. casita to, well, my company is now building a 9,80Gsq. ft. home. We're now researching the third segment: the mass-produced affordable home," he said.
Yct it sccms impractical lilr rctail yards to carry balcs. "It's too bulky. You don't want t0 have to warehouse it," explained Perry. "But there are a number of tools and currently homemade products that a retailer could provide, such as special configuration wire pegs and rebar cut to length." As well, there are now businesses that "office broker" straw bales.
The best straw supplier is the nearest farm. Southern Colorado farmers now regularly call Perry and other association members to ask how much straw they need baled for the next building season. "We've gotten calls from rice fields in California, but that's too far to ship it," said New Mexico-based Perry. "You want to get it from the farm to an lS-wheeler to the jobsite."
Mo.e practical as resaleable building products are compressedstraw panels. They are lighter, easier to handle and more similar to traditional building products, reducing apprehension among builders as well as building code officials.
The first "compressed agricultural fiber" panels were introduced 60 years ago in Sweden (see sidebar at right) and have been used extensively in Europe.
At least 10 companies are currently building or planning to build strawpanel manufacturing facilities in North America, including in Texas, Montana, California and Oregon. Plants are already up and running in England and Australia.
When straw is compressed under high temperature, the fibers bond together without any adhesives (some companies do use adhesives). The compressed layers are often faced with Kraft paper, or can be finished with a plastic coating or wood veneer. Typical panels will be 4'x8' or 8'x16', 2" to 4-3/4" thick, for use as exterior walls, roofs, interior partition walls, floors and insulation.
Despite offering good R-values and resistance to fire, earthquakes and hurricane winds, the panels are catching on slowly in the U.S. "People resist change - unless there's a reason to change, such as rising lumber costs," explained Basic Industry Technology's Glen Wiltsey. "People have been building with wood 2x4s for so long, there's a resistance to building with panels rather than lumber."
The company plans to begin ship- ping its Agri-Board panels this fall, but don't expect it to be available through your favorite distributor. "Immediately all of our production will be shipped overseas, to Asian, Latin American, South African markets," Wiltsey said. "Those areas badly need housing and are not so resistant to new materials. Domestic penetration will be gradual."
Use in construction should also be eventual for this renewable and plentiful resource.
N6w Straw :Pa,nel,: Plant,,.On,r.,Lihe
Production :has rbegun at::Stramit USA's new :Perryton,, Tx,, plant, of interior wall paneli made from wheat sua*.
The solid, durable and reported- ly fire resistant EnviroPanel Interior Wall Systems are formed through heat and pressure extrusion using the pioneering Stramit Process.
In 1935, Swedish inventor Theodor Dieden discovered that heating and comprCsiing straw released its own natural "resin." Ten years later in England, under the guidance of Thorsten Mosesson, tha operation was refined into what:is: now knOwn, as,,the,:St{4fr{t Process.
In the Stramit Process, straw is fed into a semiautomatic machine, requiring m,inimum ::labor. :The: straw is compressed and heated through metal plates to 500T. The only thiee fa* :rnaterials roquired through the entire process are straw, paper and glue. No binder glue or cement is added to the straw core.
"Half a century after its creation,: the Stra4it PT oce:ss shows promise: :of reVolutionizing, the wat we look at construction by blending environmental concern with streamlined production. By giving farmers :the added valuo for their crops and providing a us" ior a waste byproduct, we are converting a liability into a national asset,'i said Stramit USA ceo Cindy Thyfault.
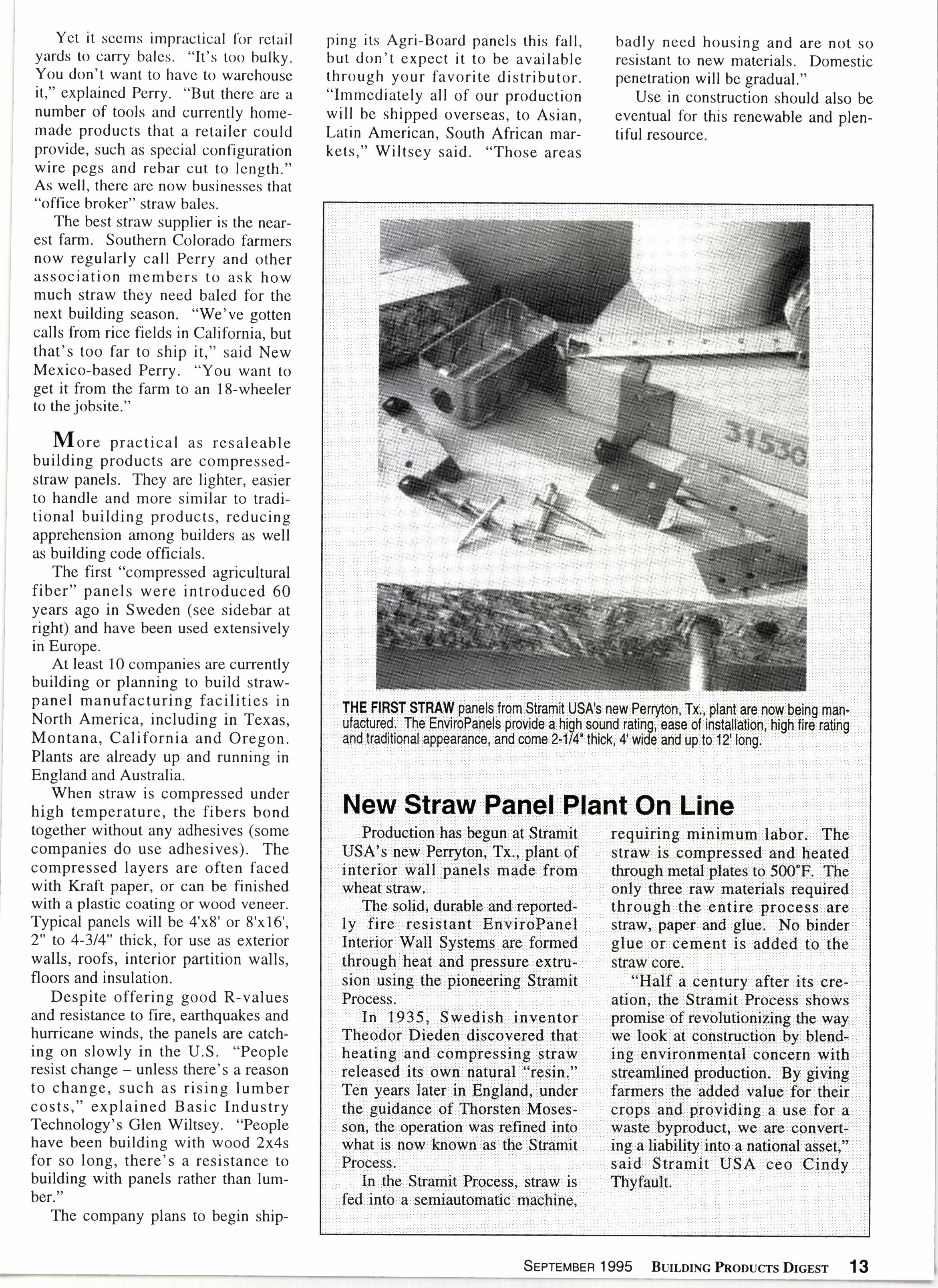