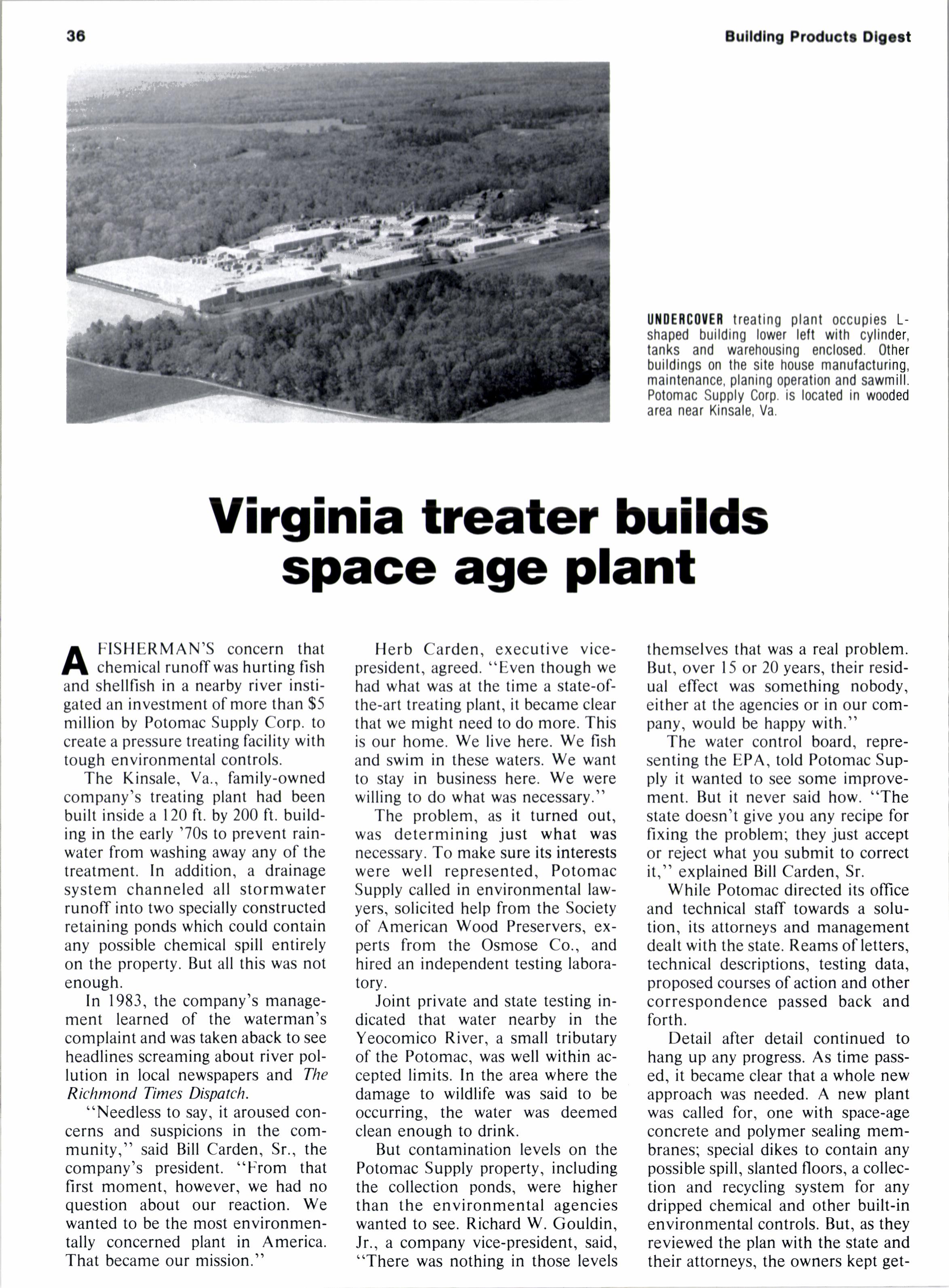
4 minute read
Virginia treater builds space age plant
FISHERMAN'S concern that chemical runoffwas hurting fish and shellfish in a nearby river instigated an investment of more than $5 million by Potomac Supply Corp. to create a pressure treating facility with tough environmental controls.
The Kinsale, Va., family-owned company's treating plant had been built inside a 120 ft. by 200 ft. building in the early '70s to prevent rainwater from washing away any of the treatment. In addition, a drainage system channeled all stormwater runoff into two specially constructed retaining ponds which could contain any possible chemical spill entirely on the property. But all this was not enough.
In 1983, the company's management learned of the waterman's complaint and was taken aback to see headlines screaming about river pollution in local newspapers and lhe Richmond Times Dispatch.
"Needless to say, it aroused concerns and suspicions in the community," said Bill Carden, Sr., the company's president. "F'rom that first moment, however, we had no question about our reaction. We wanted to be the most environmentally concerned plant in America. That became our mission."
Herb Carden, executive vicepresident, agreed. "Even though we had what was at the time a state-ofthe-art treating plant, it became clear that we might need to do more. This is our home. We live here. We fish and swim in these waters. We want to stay in business here. We were willing to do what was necessary."
The problem, as it turned out, was determining just what was necessary. To make sure its interests were well represented, Potomac Supply called in environmental lawyers, solicited help from the Society of American Wood Preservers, experts from the Osmose Co., and hired an independent testing laboratory.
Joint private and state testing indicated that water nearby in the Yeocomico River, a small tributary of the Potomac, was well within accepted limits. In the area where the damage to wildlife was said to be occurring, the water was deemed clean enough to drink.
But contamination levels on the Potomac Supply property, including the collection ponds, were higher than the environmental agencies wanted to see. Richard W. Gouldin, Jr., a company vice-president, said, "There was nothing in those levels themselves that was a real problem. But, over | 5 or 20 years, their residual effect was something nobody, either at the agencies or in our company, would be happy with."
The water control board, representing the EPA, told Potomac Supply it wanted to see some improvement. But it never said how. "The state doesn't give you any recipe for fixing the problem; they just accept or reject what you submit to correct it," explained Bill Carden, Sr.
While Potomac directed its offrce and technical staff towards a solution, its attorneys and management dealt with the state. Reams of letters, technical descriptions, testing data, proposed courses ofaction and other correspondence passed back and forth.
Detail after detail continued to hang up any progress. As time passed, it became clear that a whole new approach was needed. A new plant was called for, one with space-age concrete and polymer sealing membranes; special dikes to contain any possible spill, slanted floors, a collection and recycling system for any dripped chemical and other built-in environmental controls. But, as they reviewed the plan with the state and their attorneys, the owners kept get- ting the same message: This will solve the problems in the plant, but there's still the problem of stormwater runoff. Dripping lumber fresh from the retort could leak into the soil or wash away during heavy rains.
The solution was to put a roof over every bit of treated lumber, which, in this case, meant constructing five-acres-worth of warehouse: a building 570 ft. long and 260 ft. wide. Everything from the bays where kiln-dried pine is unloaded for treating to the loading docks where trailers sit ready to be filled with treated lumber is enclosed. The state responded by awarding what appears to be the only no-discharge permit ever given a pressure treated lumber plant in this country.
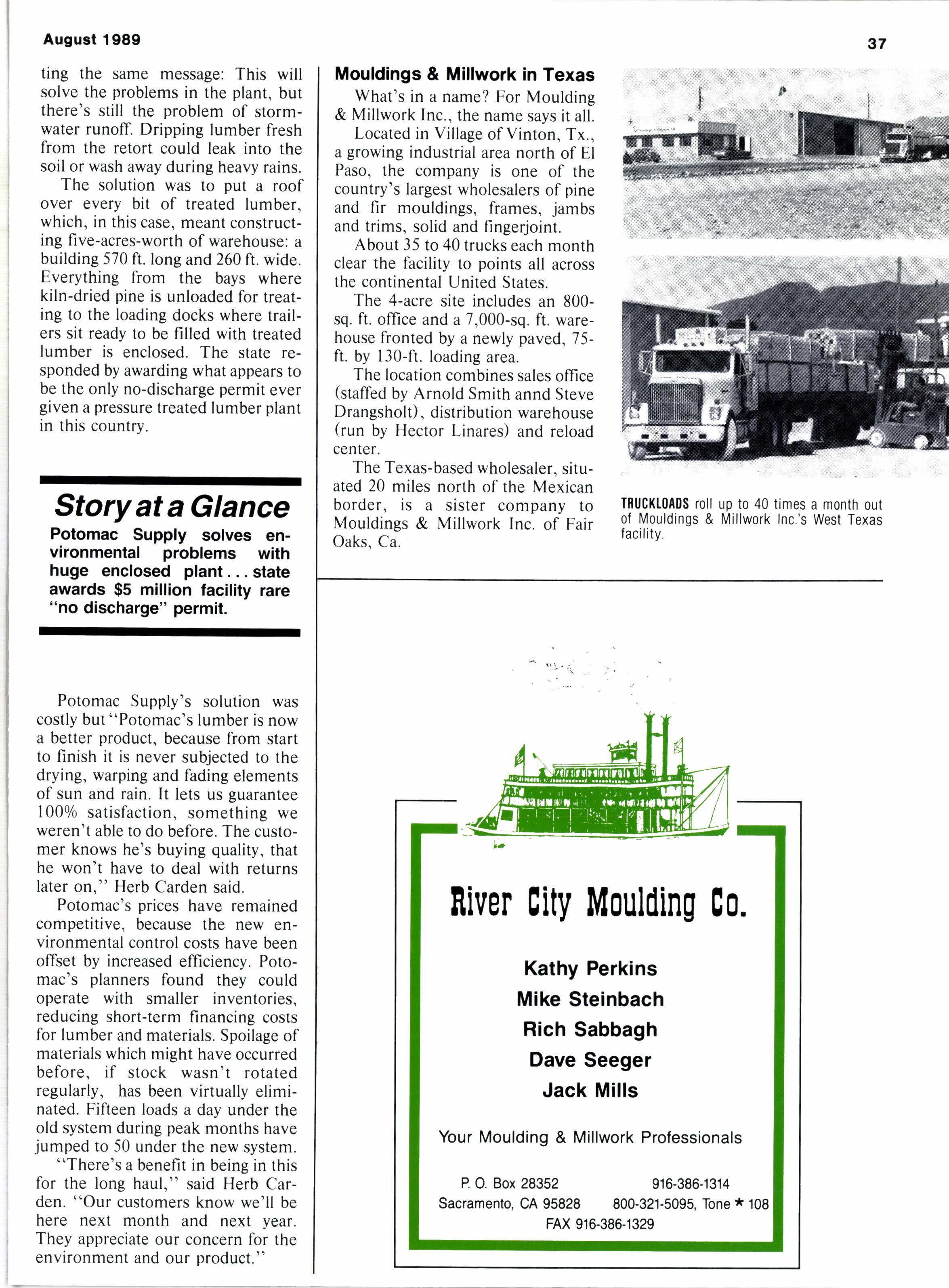
Story at a Glance
Potomac Supply solves environmental problems with huge enclosed plant. .. state awards $5 million facility rare "no discharge" permit.
Potomac Supply's solution was costly but "Potomac's lumber is now a better product, because from start to finish it is never subjected to the drying, warping and fading elements of sun and rain. It lets us guarantee l00o/o satisfaction, something we weren't able to do before. The customer knows he's buying quality, that he won't have to deal with returns later on," Herb Carden said.
Potomac's prices have remained competitive, because the new environmental control costs have been offset by increased efficiency. Potomac's planners found they could operate with smaller inventories, reducing short-term financing costs for lumber and materials. Spoilage of materials which might have occurred before, if stock wasn't rotated regularly, has been virtually eliminated. Fifteen loads a day under the old system during peak months have jumped to 50 under the new system.
"There's a benefit in being in this for the long haul," said Herb Carden. "Our customers know we'll be here next month and next year. They appreciate our concern for the environment and our product."
Mouldings & Millwork in Texas
What's in a name? For Moulding & Millwork Inc., the name says it all.
Located in Village of Vinton, Tx., a growing industrial area north of El Paso, the company is one of the country's largest wholesalers of pine and fir mouldings, frames, jambs and trims, solid and fingerjoint.
About 35 to 40 trucks each month clear the facility to points all across the continental United States.
The 4-acre site includes an 800sq. ft. office and a 7,000-sq. ft. warehouse fronted by a newly paved, 75ft. by 130-ft. loading area.
The location combines sales office (staffed by Arnold Smith annd Steve Drangsholt), distribution warehouse (run by Hector Linares) and reload center.
The Texas-based wholesaler, situated 20 miles north of the Mexican border, is a sister company to Mouldings & Millwork Inc. of Fair Oaks. Ca.
TRUCKI0AI|S roll up to 40 times a month out of Mouldings & Millwork Inc.'s West Texas faci
Mike