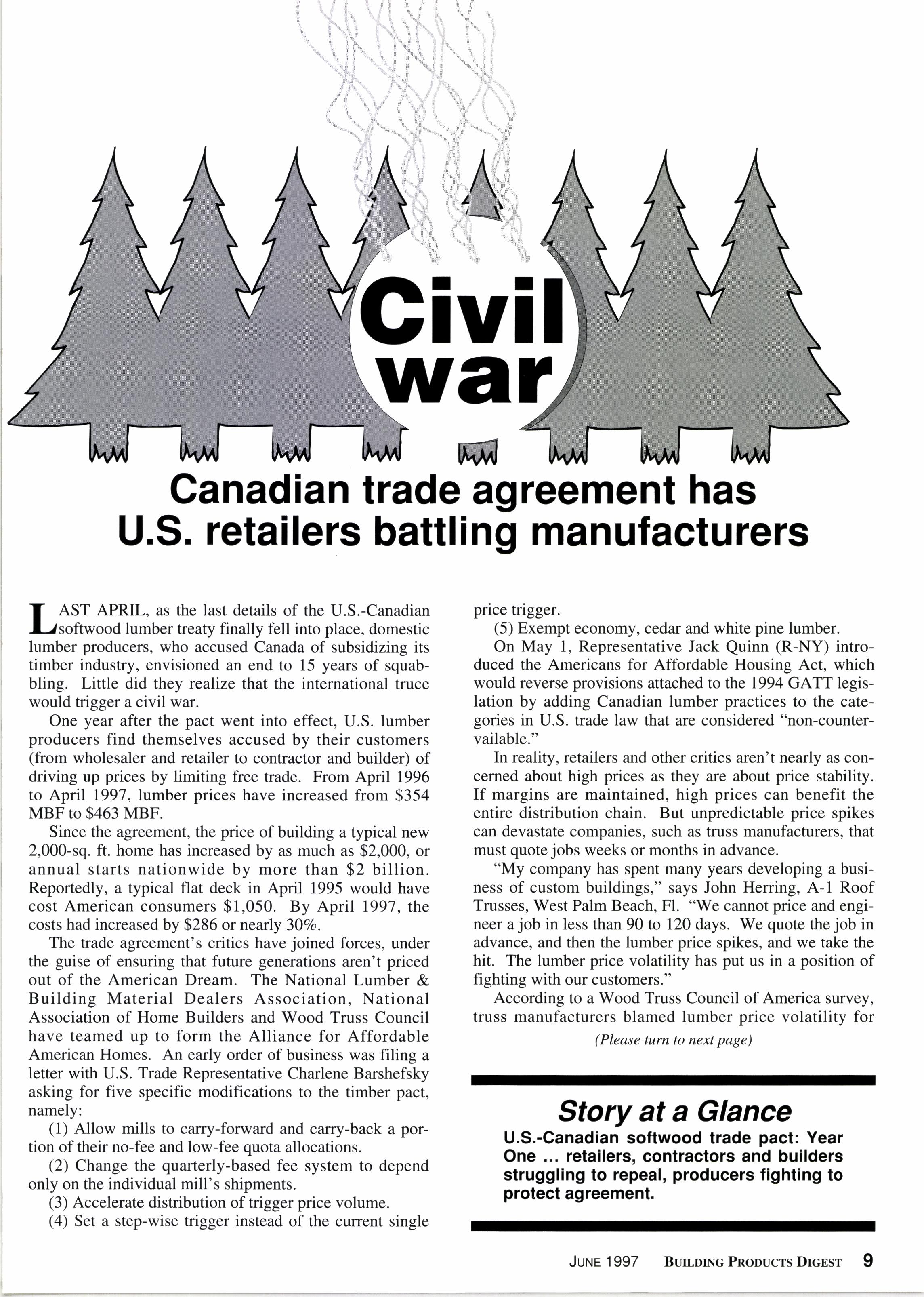
2 minute read
ivil a jil
Canadian trade agreement has U.S. retailers battling manufacturers
f AST APRIL, as the last details of the U.S.-Canadian I-Jsoftwood lumber treaty finally fell into place, domestic lumber producers, who accused Canada of subsidizing its timber industry, envisioned an end to 15 years of squabbling. Little did they realize that the international truce would trigger a civil war.
One year after the pact went into effect, U.S. lumber producers find themselves accused by their customers (from wholesaler and retailer to contractor and builder) of driving up prices by lirniting free trade. From April 1996 to April 1997, lumber prices have increased from $354 MBF to $463 MBF.
Since the agreement, the price of building a typical new 2,000-sq. ft. home has increased by as much as $2,000, or annual starts nationwide by more than $2 billion. Reportedly, a typical flat deck in April 1995 would have cost American consumers $1,050. By April 1997, the costs had increased by $286 or nearly 30Vo.
The trade agreement's critics have joined forces, under the guise of ensuring that future generations aren't priced out of the American Dream. The National Lumber & Building Material Dealers Association, National Association of Home Builders and Wood Truss Council have teamed up to form the Alliance for Affordable American Homes. An early order of business was filing a letter with U.S. Trade Representative Charlene Barshefsky asking for five specific modifications to the timber pact, namely:
(1) Allow mills to carry-forward and carry-back a portion of their no-fee and low-fee quota allocations.
(2) Change the quarterly-based fee system to depend only on the individual mill's shipments.
(3) Accelerate distribution of trigger price volume.
(4) Set a step-wise trigger instead of the current single pnce tngger.
(5) Exempt economy, cedar and white pine lumber.
On May 1, Representative Jack Quinn (R-NY) introduced the Americans for Affordable Housing Act, which would reverse provisions attached to the 1994 GATT legislation by adding Canadian lumber practices to the categories in U.S. trade law that are considered "non-countervailable."
In reality, retailers and other critics aren't nearly as concerned about high prices as they are about price stability. If margins are maintained, high prices can benefit the entire distribution chain. But unpredictable price spikes can devastate companies, such as truss manufacturers, that must quote jobs weeks or months in advance.
"My company has spent many years developing a business of custom buildings," says John Hening, A-1 Roof Trusses, West Palm Beach, Fl. "We cannot price and engineer a job in less than 90 to l2O days. We quote the job in advance, and then the lumber price spikes, and we take the hit. The lumber price volatility has put us in a position of fighting with our customers."
According to a Wood Truss Council of America survey, truss manufacturers blamed lumber price volatility for (Please tum to next page)
Story at a Glance
U.S.-Canadian softwood trade pact: Year One retailers, contractors and builders struggling to repeal, producers fighting to protect agreement.