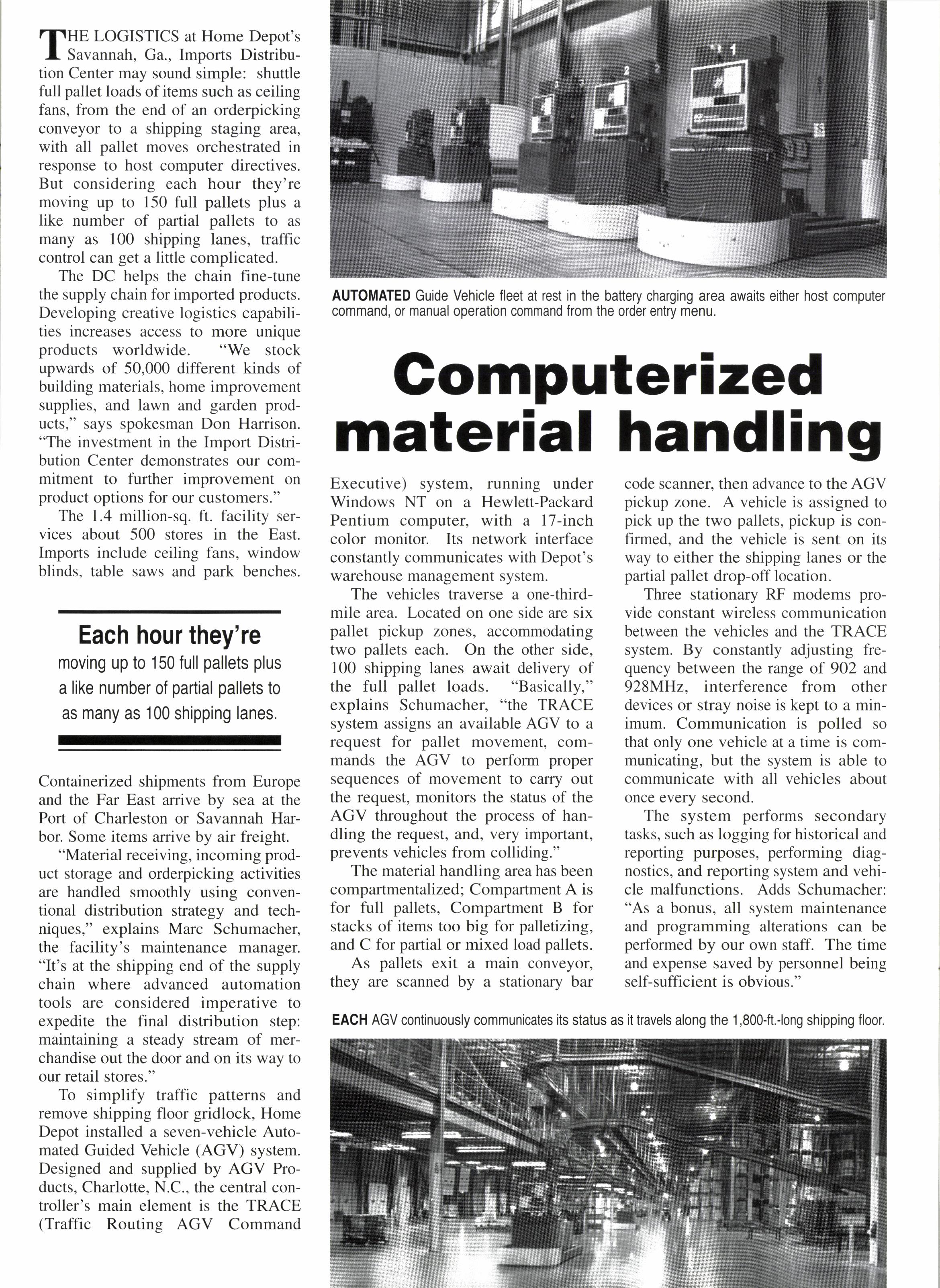
1 minute read
Gomputerizedmaterial handling
Executive) system, running under Windows NT on a Hewlett-Packard Pentium computer, with a l7-inch color monitor. Its network interface constantly communicates with Depot's warehouse management system.
The vehicles traverse a one-thirdmile area. Located on one side are six pallet pickup zones, accommodating two pallets each. On the other side, 100 shipping lanes await delivery of the full pallet loads. "Basically," explains Schumacher, "the TRACE system assigns an available AGV to a request for pallet movement, commands the AGV to perform proper sequences of movement to carry out the request, monitors the status of the AGV throughout the process of handling the request, and, very important. prevents vehicles from colliding."
The material handling area has been compartmentalized; Compartment A is for full pallets, Compartment B for stacks of items too big for palletizing, and C for partial or mixed load pallets.
As pallets exit a main conveyor, they are scanned by a stationary bar code scanner, then advance to the AGV pickup zone. A vehicle is assigned to pick up the two pallets, pickup is confirmed, and the vehicle is sent on its way to either the shipping lanes or the partial pallet drop-off location.
Three stationary RF modems provide constant wireless communication between the vehicles and the TRACE system. By constantly adjusting frequency between the range of 902 and 928MHz, interference from other devices or stray noise is kept to a minimum. Communication is polled so that only one vehicle at a time is communicating, but the system is able to communicate with all vehicles about once every second.
The system performs secondary tasks, such as logging for historical and reporting purposes, performing diagnostics, and reporting system and vehicle malfunctions. Adds Schumacher: "As a bonus. all system maintenance and programming alterations can be performed by our own staff. The time and expense saved by personnel being self-sufficient is obvious."