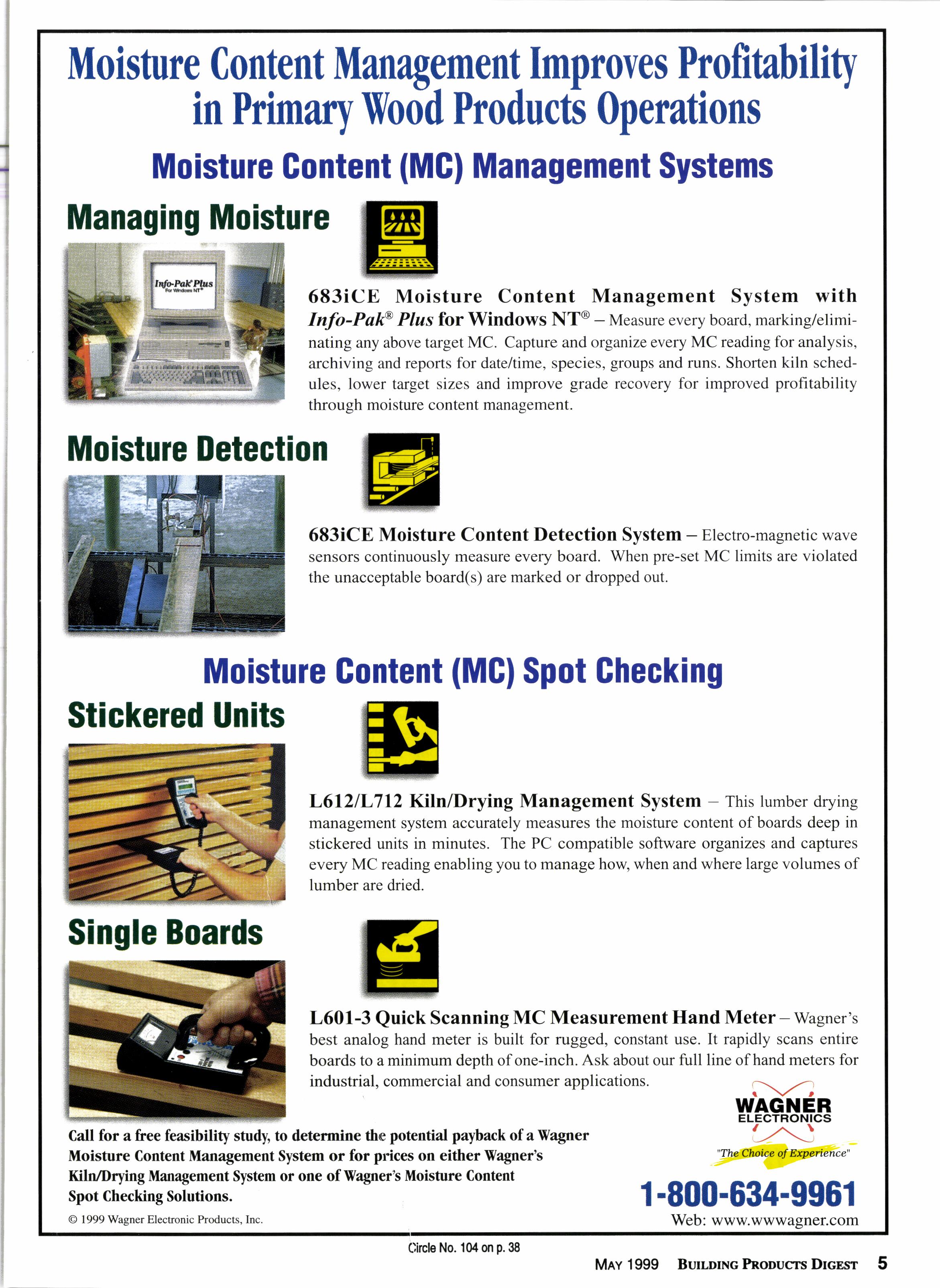
2 minute read
Moisture Content Managgment Improves Profitability in Primary Wood Products 0perations
Moisture Gontent (MGl Management Systems
Managing Moisture
683iCE Moisture Content Management System with Info-Pak@ Plas for Windows NT@ - Measure every board, marking/eliminating any above target MC. Capture and organize every MC reading for analysis, archiving and reports for date/time, species, groups and runs. Shorten kiln schedules, lower target sizes and improve grade recovery for improved profitability throush moisture content manasement.
Moisture Detection
683iCE Moisture Content Detection System - Electro-magnetic wave sensors continuously measure every board. When pre-set MC limits are violated the unacceptable board(s) are marked or dropped out.
Moisture Content (MC) Spot Ghecking Stickered Units
L6l2/L712 Kiln/Drying Management System - This lumber drying management system accurately measures the moisture content of boards deep in stickered units in minutes. The PC compatible solhvare organizes and captures every MC reading enabling you to manage how, when and where large volumes of lumber are dried.
Single Boards
L601-3 Quick Scanning MC Measurement Hand Meter - wagner's best analog hand meter is built for rugged, constant use. It rapidly scans entire boards to a minimum depth of one-inch. Ask about our ful1 line of hand meters for industrial, commercial and consumer applications.
Call for a free feasibility study, to determine the potential payback of a Wagner Moisture Content Management System or for pdces on either Vagner's KilM)rying Management System or one of Wagrer's Moisturrc Content Spot Checking Solutions.
It's Not Tlailer l?ash Any More
Whether you call them trailers, mobile homes or manufactured housing, that segment of the housing market has been undergoing significant changes in the last decade. These developments mean that suppliers need to prepare for new needs and wants by both builders and the consumers who buy them.
The tin can image of yesteryear has been replaced by improved quality and many of the features of stick-built homes. Some manufactured homes boast two stories, attached garages, skylighs, vaulted ceilings, hardwood floors, and cultured marble countertops. By joining additional sections onsite, larger and more conventional configurations replace the look of the traditional rectangle.
It was in the 1970s that builders and the federal government worked together to create national standards that resulted in today's higher quality. That led to Real Estate Investment Trusts investing in upscale manufactured housing communities and greater public acceptance of living in these new developments with their resort-like features. While the main buyers continue to be young families and retirees, a growing middle-age market is developing. While today's factory-built isn't as cheap as its shabby predecessor, today's units are still priced about 4OVo below comparable site-built homes. The Manufactured Housing Institute estimates that the average 1,5(X) square foot unit sells for a thrifty $43,000 with a land lease of about $250 per month. Construction cost is just under $30 per square foot, about half that of conventional construction.
As owners and renters enjoy better units and more livable surroundings, a new stability has developed. Our industry recognizes that higher quality materials and products are needed for the initial construction of manufactured housing. Our aftermarket suppliers likewise see new opportunities. More likely to stay put, todays' park people are better prospects than ever to purchase more home improvement items than would have been the case even five years ago.
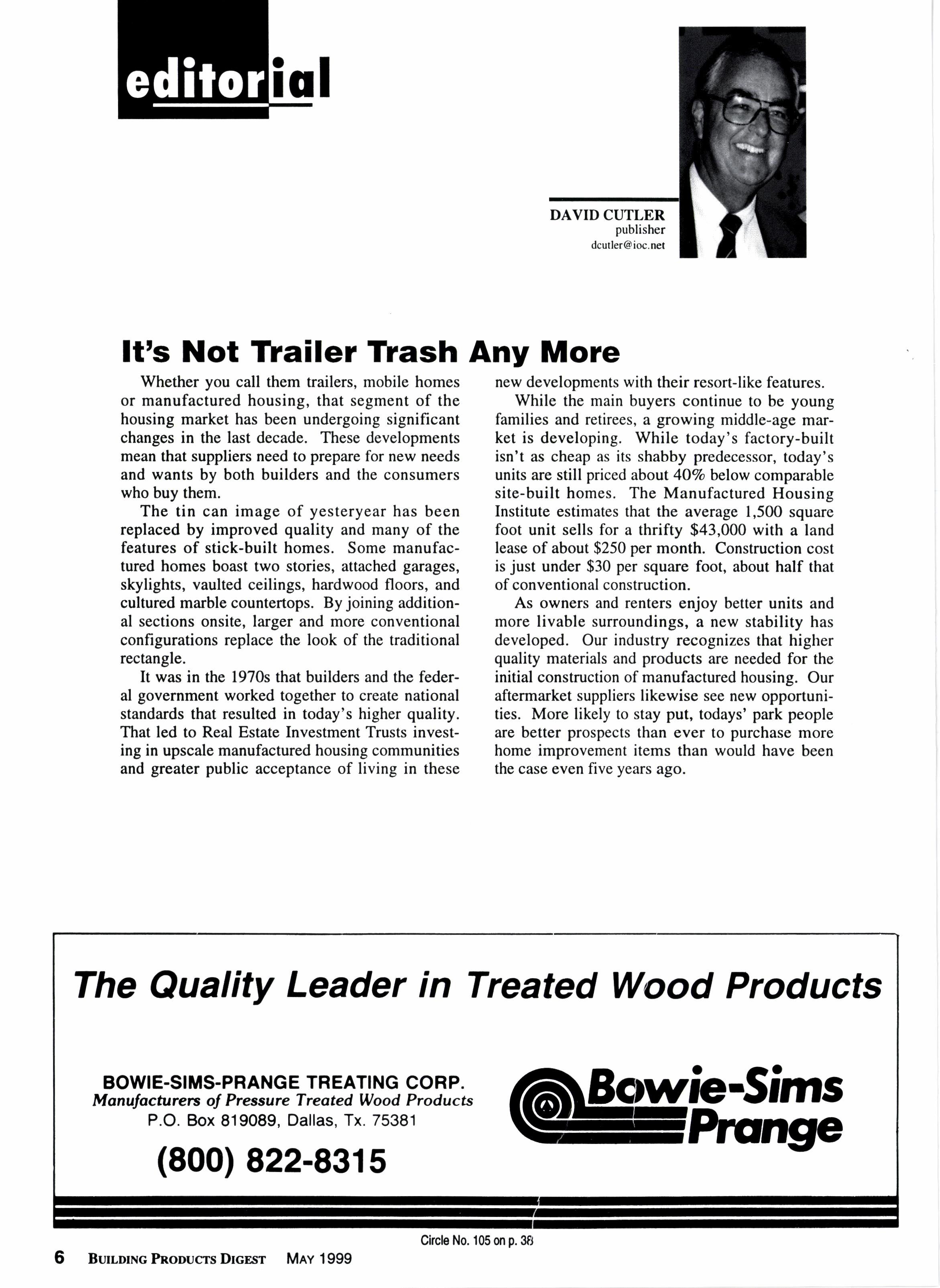
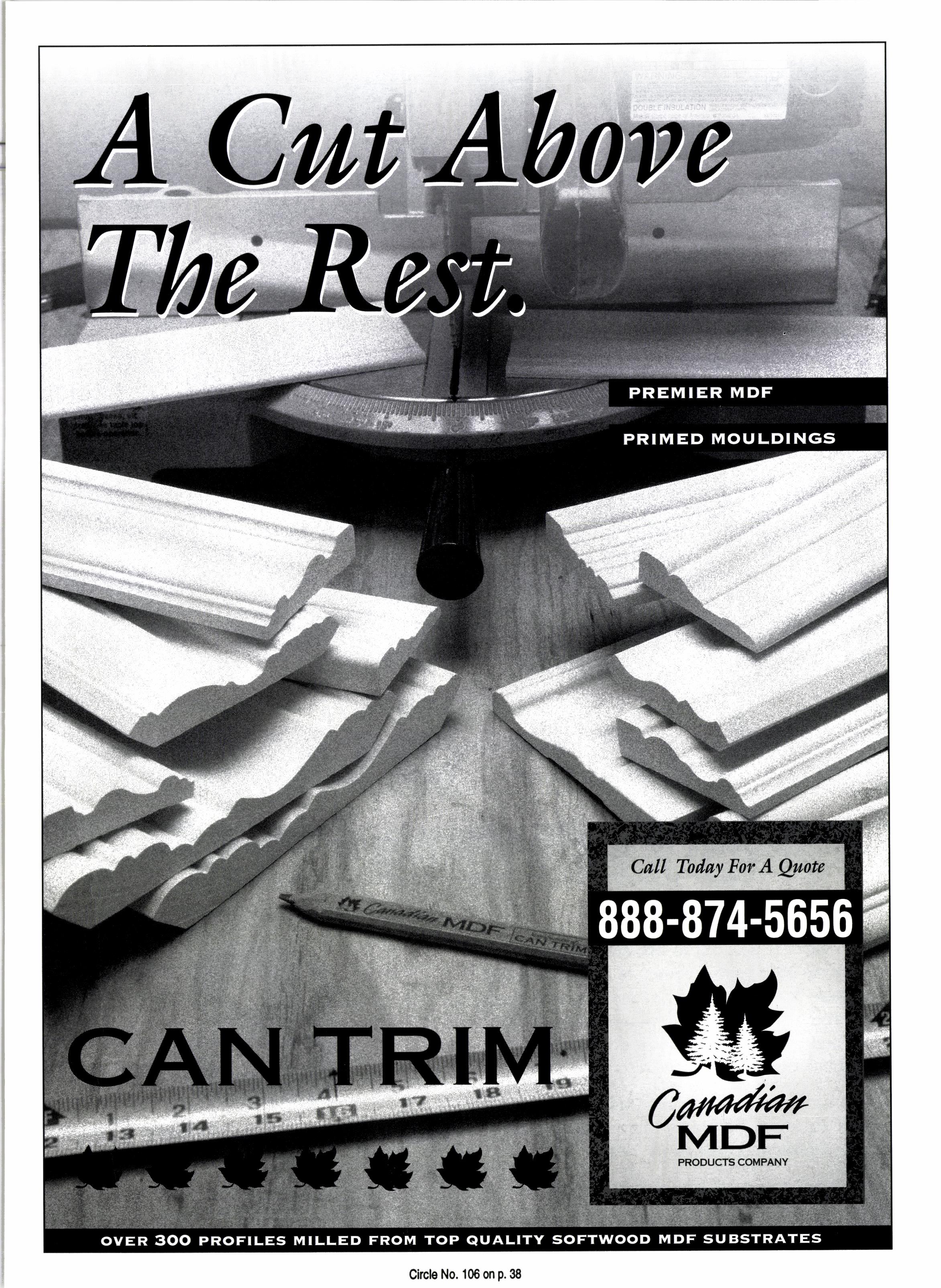