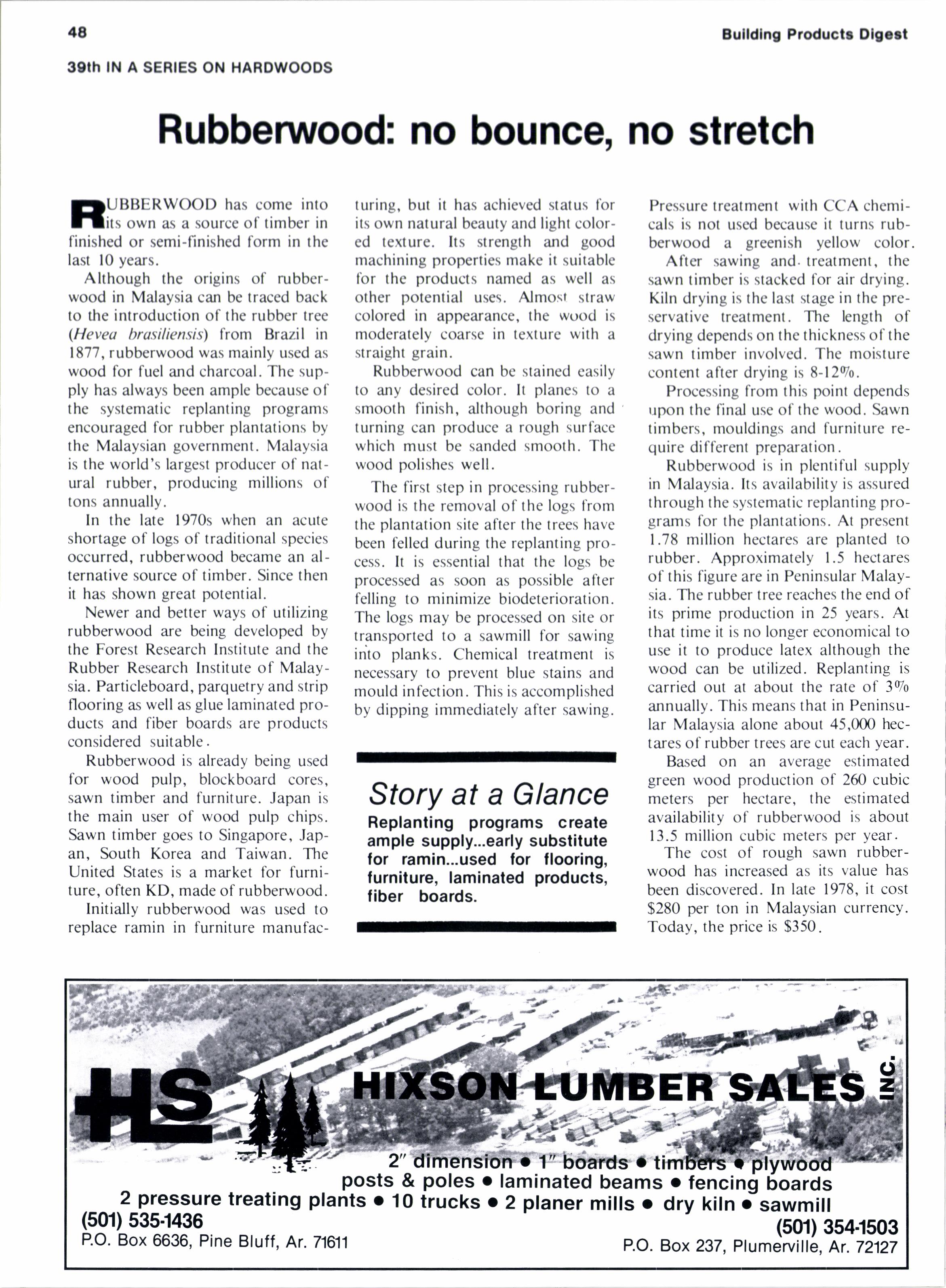
2 minute read
Rubberwood: no bounce, no stretch
FTUBBERWOOD has come into flits own as a source ol'timber in finished or semi-finished form in the last l0 years.
Although the origins of rubberwood in Malaysia can be traced back to the introduction of the rubber tree (Hevea brasiliensis\ liom Brazil in 1877, rubberwood was mainly used as wood for fuel and charcoal. The supply has always been ample because ol' the systematic replanting programs encouraged for rubber plantations by the Malaysian government. Malaysia is the world's largest producer of natural rubber, producing millions of tons annually.
ln the late 1970s when an acute shortage of logs of traditional specics occurred, rubberwood became an alternative source of timber. Since then it has shown great potential.
Newer and better ways of utilizing rubberwood are being developed by the Forest Research lnstitute and the Rubber Research Institute of Malaysia. Particleboard, parquetry and strip flooring as well as glue laminated products and fiber boards are products considered suitable.
Rubberwood is already being used for wood pulp, blockboard cores, sawn timber and furniture. Japan is the main user of wood pulp chips. Sawn timber goes to Singapore, Japan, South Korea and Taiwan. The United States is a market for furniture, often KD, made of rubberwood.
Initially rubberwood was used to replace ramin in furniture manufac- turing, but it has achieved status lbr its own natural beauty and light colored texture. lts strength and good machining properties make it suitable lbr the products named as well as other potential uses. Almosl straw colored in appearance, the wood is moderately coarse in texture with a straight grain.
Rubberwood can be stained easily to any desired color. lt planes to a smooth finish, although boring and turning can produce a rough surl'acc which must be sanded smooth. The wood polishes well.
The flirst step in processing rubberwood is the removal of the logs l'rom the plantation site after the trees have been felled during the replanting process. It is essential that the logs be processed as soon as possible aller felling to minimize biodeterioration. The logs may be processed on site or transported to a sawmill for sawing into planks. Chemical treatment is necessary to prevent blue stains and mould infection. This is accomplished by dipping immediately after sawing.
Story at a Glance
Replanling programs create ample supply...early substitute lor ramin...used for llooring, furniture, laminated products, f iber boards.
Pressure treatment with CCA chemicals is not used becausc it turns rubberwood a greenish yellow color.
After sawing and. treatment, the sawn timber is stacked for air drying. Kiln drying is the last stage in thc preservative treatmenl . The length of drying depends on the thickness ol the sawn timber involved, The moisture content after drying is 8-1290.
Processing from this point depends rrpon the final use ol'the wood. Sawn timbers, mouldings and furniture require difltrent preparalion.
Rubberwood is in plentiful supply in Malaysia. lts availability is assured through the systcmatic replanting programs for the plantations. At present 1.78 million hectares are planted to rubber. Approximately 1.5 hectares of this figure are in Peninsular Malaysia. The rubber tree reaches the end of its prime production in 25 years. At that time it is no longer economical to use it to produce latex although the wood can be utilized. Replanting is carried out at about the rate of 390 annually. This means that in Peninsular Malaysia alone about 45,000 hectares of rubber trees are cut each year.
Based on an average estimated green wood production of 260 cubic meters per hectare, the estimated availability of rubberwood is about 13.5 million cubic meters per year.
The cost of rough sawn rubberwood has increased as its value has been discovered. In late 1978, it cost $280 per ton in Malaysian currency. Today, the price is $350.