
2 minute read
Thought Leadership
Article by Rick Becerra | December 2021
Accelerating Automation - BlueCrest technology is driving operational efficiencies and helping organizations master today’s market challenges
Rick Becerra Vice President Sortation Solutions & Strategy
By Rick Becerra
E-commerce growth continues to escalate. The pandemic saw volumes spiral at an unprecedented rate and global sales are estimated to approach the $5 trillion mark in 2021. But what of the other mail items that make up daily postal volumes? While the ratio of letters and flats to e-commerce parcels has declined, the fact remains that there is still so much mail out there. There is also a shortage of available labor to process this volume.
Lack of labor.
The lack of labor and the rate of employee turnover related to the processing of letter and flat mail is a major challenge for today. It is also a clear opportunity for postal operators to reassess processes and to identify required next steps to better position for a complex and changing environment. Automation is key.
In such a climate, automation and operational efficiency is key. The technology exists to enable operations to streamline workflows, consolidate labour, reduce facility footprints and increase processing throughput. For example, a typical organization might be running two legacy sortation systems running at 22,000 items per hour, requiring two or more operators per system. Today, a high-speed sortation system such as the BlueCrest Vantage can run at twice that speed, effectively providing a one-machine-for-two replacement. In this scenario, only one operator is required, not to mention additional savings on annual software spend (because one system has been eliminated), savings on consumed items and savings related to equipment service and uptime.
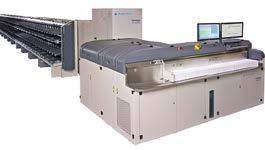
Operational efficiency means more.
Operational efficiency is not simply focused on labor. It’s about providing an optimal response to developing market conditions and building in the capacity to become strategically agile. We talk to customers about the five pillars of operation: application; interface; data models; data management;
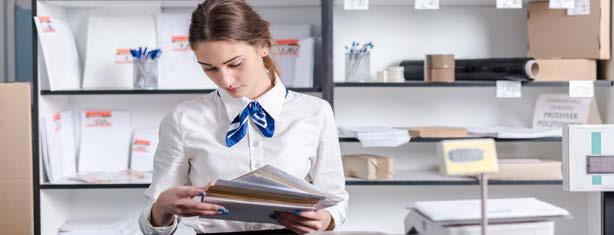
Rick Becerra, VP
security and control. In other words, we get to know their application (what they’re trying to achieve) and their workflow (their means of achieving it). A high-speed sorting operation may consist of multiple sites, different processes and a range of sortation machines all of which add complexity, inefficiency and cost. Our SortEngine™ 360 software platform enables organisations to connect multiple sites to optimize technology usage and efficiencies and consolidate all mail and parcel processing requirements. Not only can organisations achieve multi-site optimization within their operations, but they can rapidly understand equipment usage patterns, identify any under-utilized systems and increase capacity without adding additional hardware. Organizations running multiple sorting machines in one location can now consolidate all their processing needs into one sorter per location and network them all together with SortEngine™ 360. In a complex and challenging market – one where experienced and skilled labor is hard to find - it is astute use of technology and automation that is providing the win. BlueCrest know-how is helping operations across the globe to drive cost-savings, heighten process efficiency and achieve operational excellence in letter and parcel sortation.
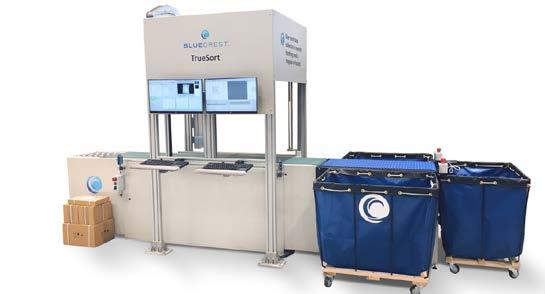