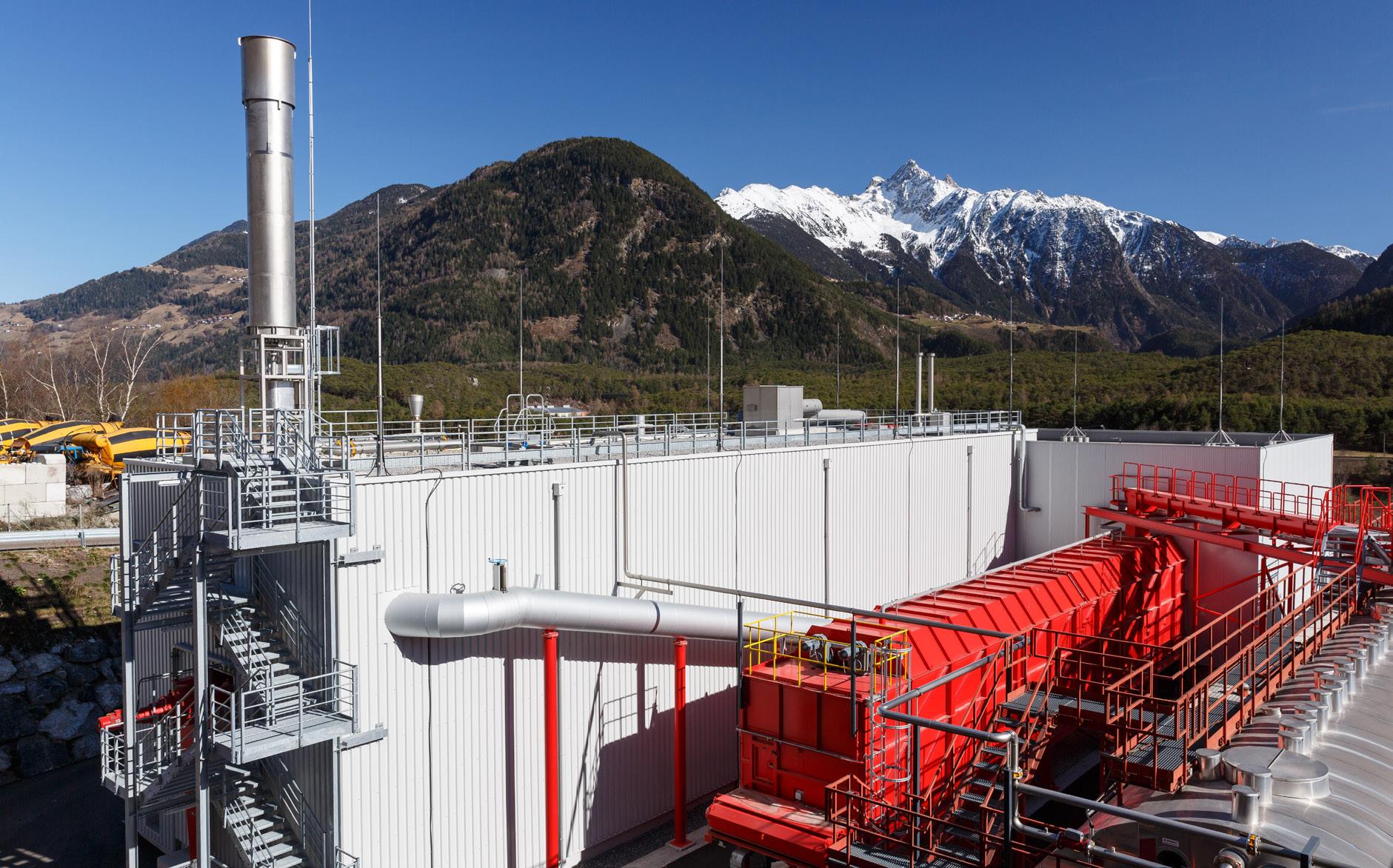
3 minute read
TTV Thöni Continuous High Solids Anaerobic Digestion
The TTV technology is distinguished by a high level of operational reliability and an exceptional biogas yield. The plug flow digester designed by us are for 'dry' organic waste, particularly when impurities are high. Key components such as the accessible, heated digester floor and the robust and powerful paddle-shaft are proven and patented, making them unique to us. Due to the special construction of the TTV digester, sediments and contaminants are continuously discharged. And so a continuous, safe operation of the digester is guaranteed.
TTV technology is developed, designed, manufactured, assembled, and commissioned by us; all core components come from a single source. This results in a high-quality standard as well as continuous system development and support.
Conditioning of the input (biowaste)
Incoming organic waste is shredded, followed by separation into fine and coarse fractions using a linked star screen (> 80mm). The fine fraction (less than 80 mm) is then passed through a mag- netic separator. For intermediate storage of the pre-treated substrate, there are several solutions available, e.g., automated TBM bunker modules, crane bunker systems, etc. When necessary, structural lignin material is used to achieve an optimal C/N ratio and an ideal input composition for subsequent process steps.
Digestion
The TTV digester is continuously fed via an intermediate storage bunker, either via a twin-shaft mixer and hydraulic piston pump or directly via
The digestion process inside the digester is based on an anaerobic, thermophilic, and completely biological process, classed as continuous High Solids Anaerobic Digestion (cHSAD or less commonly, so-called Dry AD). The process temperature inside the digester equals approximately 35–55 °C, and the input has an average dry substance content of 20-35%. The residence time is approximately 14-21 days, depending on specific project requirements. The controlled residence time of the material in the digester guarantees in-digester hygienization when running the digester thermophilic at 55°C and therefore process regulatory compliance.
The temperature and level in the digester, the quantity of gas produced, and the gas pressure are monitored continuously. The controlled end-to-end migration of the material through the digester, referred to as the plug flow process, means that the digestion process is biologically and mechanically easy to supervise. It is also extremely reliable in operation, providing a high and consistent yield of biogas.
TTV agitators are known for being able to handle hard materials and make sure that different substrates are broken down evenly and continuously. The dimensions of the paddles and shaft guarantees high stirring efficiency and a virtually unlimited service life—even under the highest loads. This is achieved by the unique and patented shape of the paddle head, which is made of highly wear-resistant steel. The special combination of paddle design and configuration prevents sedimentation by up to 100% and continuously transports potential sediment to the digester outlet while simultaneously counteracting the formation of floating layers. In this way, the digester needs minimal maintenance in the long-term, even if the input material contains significant and relatively heavy impurities. Due to the dimensioning of the agitator shaft and the special construction of the bearing, no mechanical support of the shaft is required inside the digester. The bearing and seal are accessible from the outside and can be serviced, if necessary, at any fill level of the digester.
The patented steel floor of the digester "hangs" between the two side walls made of concrete and can be reached through an inspection passage. The curved base of the digester and the patented agitator makes it impossible for sediments or other impurities to settle in the digester. Externally accessible heating elements are attached to the floor, through which the digester is heated. The floor panel has no direct connection with the concrete floor slab underneath, allowing checking of the digester base easily at any time.

TTV digesters are available in modular designs: single, double, and triple digesters. In multiple configurations, two or three digesters are struc- turally linked but operated independently. The digesters are made from reinforced concrete, including a preshaped curved steel bottom; optionally, the single digester module can also be made entirely of steel. Standard sizes (nominal digester capacity) are: 1,050 m³ to 3,850m³.
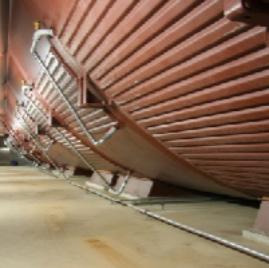
Conditioning of the digestate (separation) and products of digestion
At the end of the digestion process, the digestate is pumped to the Thöni screw presses (TSP), where it is dewatered. Some liquids are recirculated in the digestion process and used for humidifying the fresh input material. The remaining liquids are stored in tanks and used as fertilizer in agriculture.
The solid part undergoes a further aerobic composting process in special composting units. On the basis of its experience, we can even provide solutions for liquid-free operation. These use innovative technologies for part stream digestion or technical digestate treatment options, tailor-made to customer requirements.
Biogas can either be turned into electricity on-site using a combined heat and power (CHP) station and fed into the public grid, or it can be turned into biomethane using a gas upgrading system and fed into the public gas network.
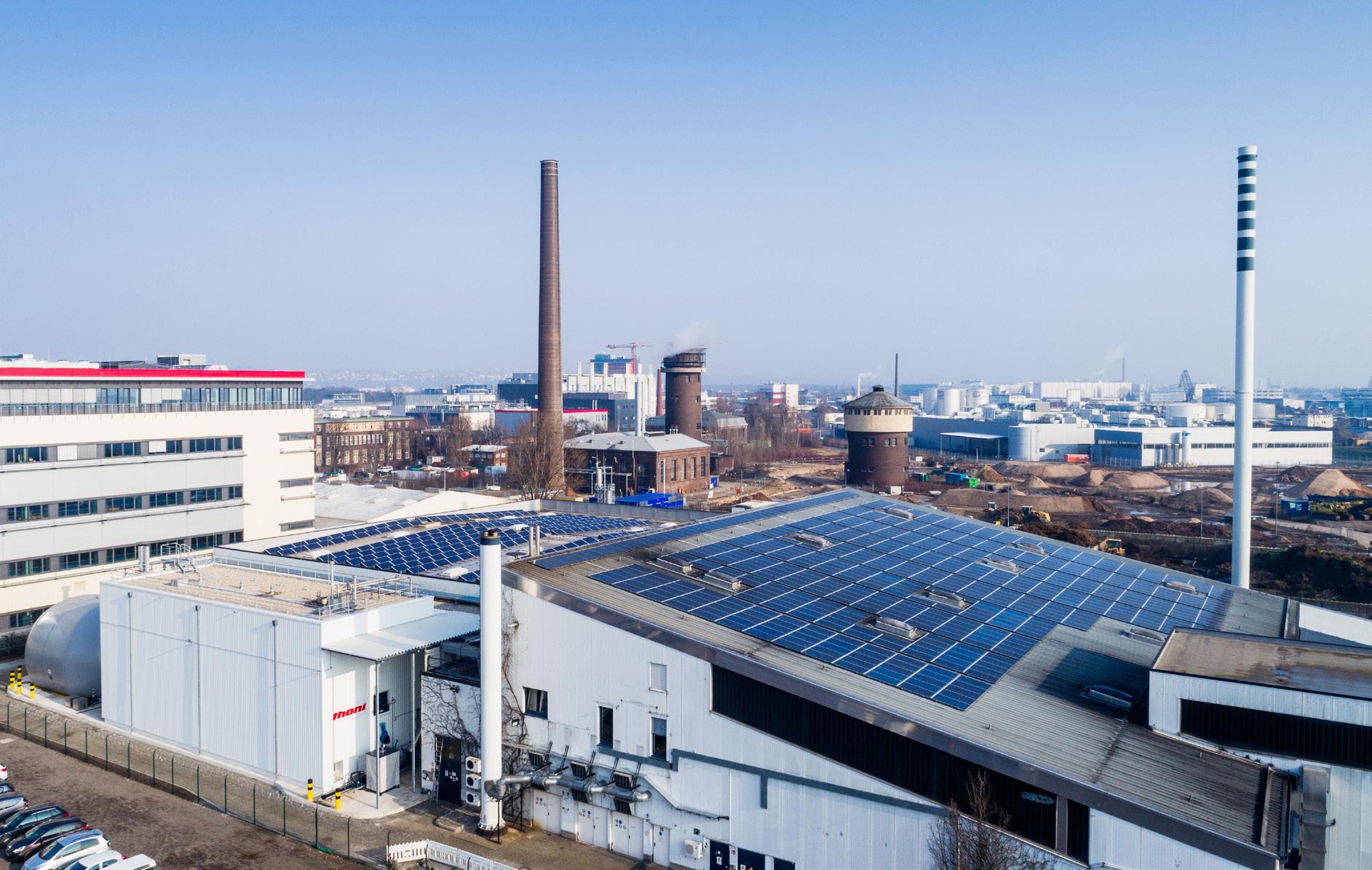
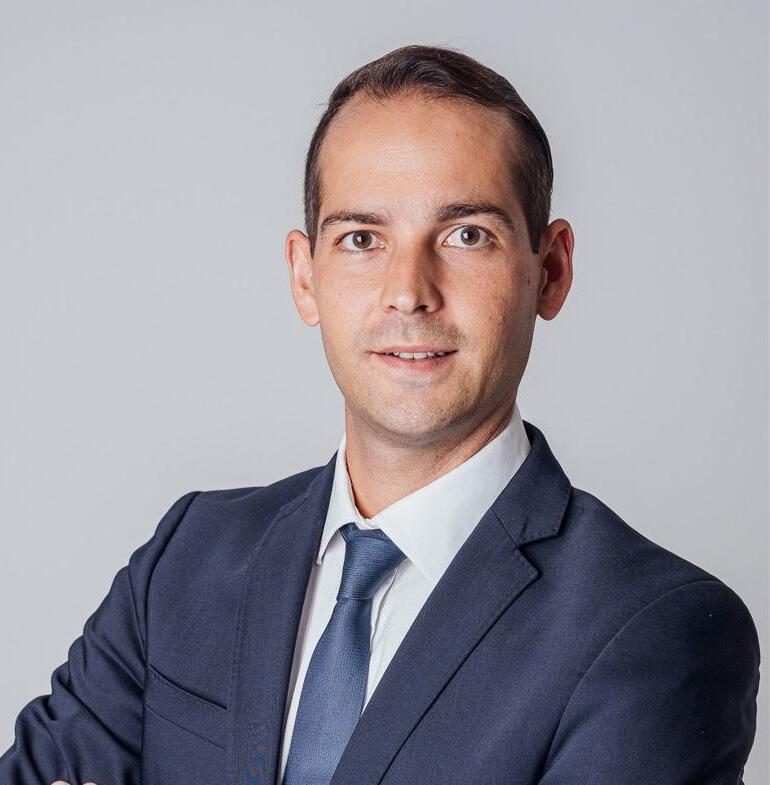
Biomethane can be used to make energy at certain places, like hospitals, schools, etc. By means of cogeneration, or it is used at filling stations as compressed natural gas (CNG) for vehicles. Overall, digestion plants with TTV technology integrate closed-loop material-recycling with energy by producing quality compost and fertilizer that can be declared with RAL quality assurance.
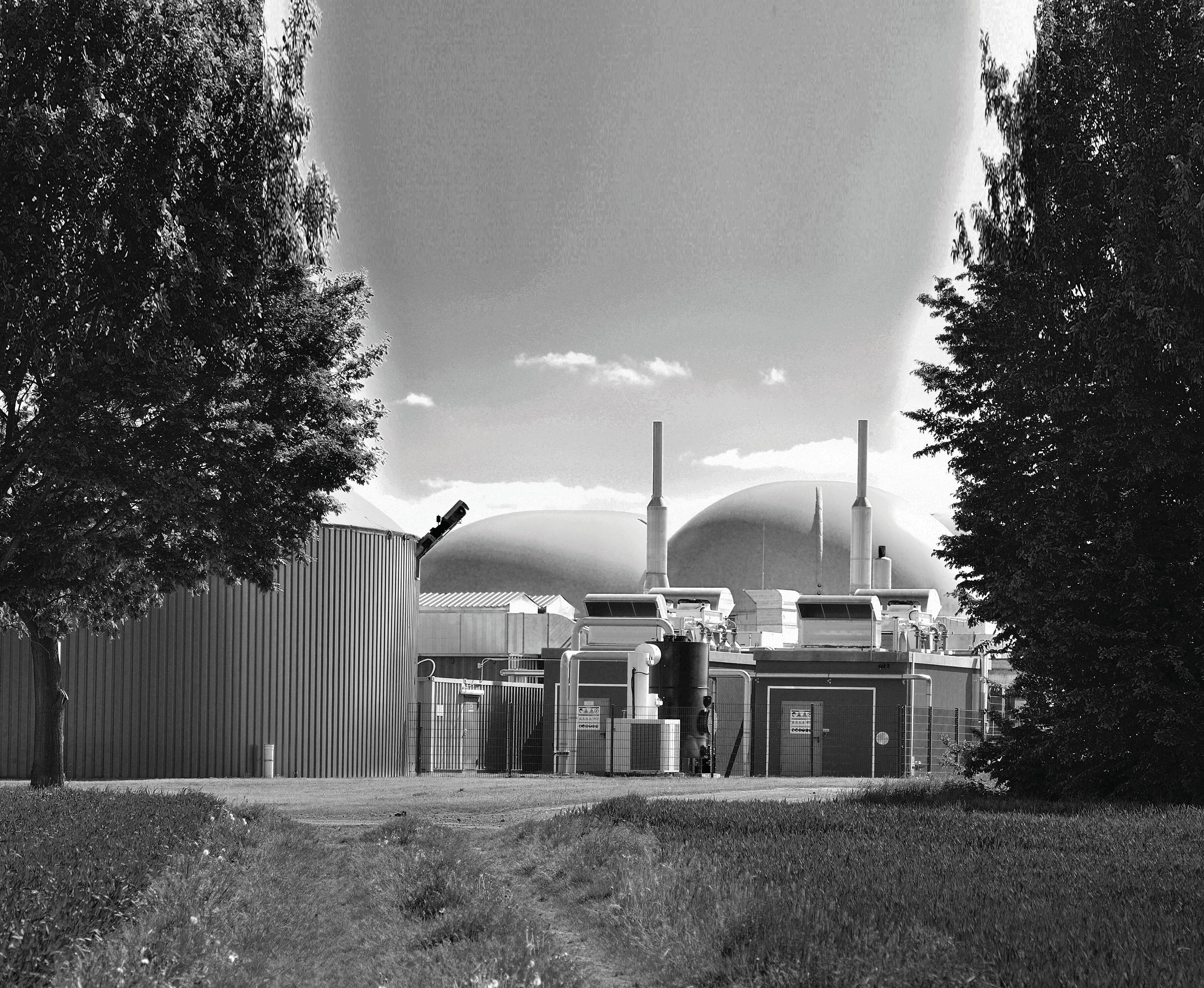
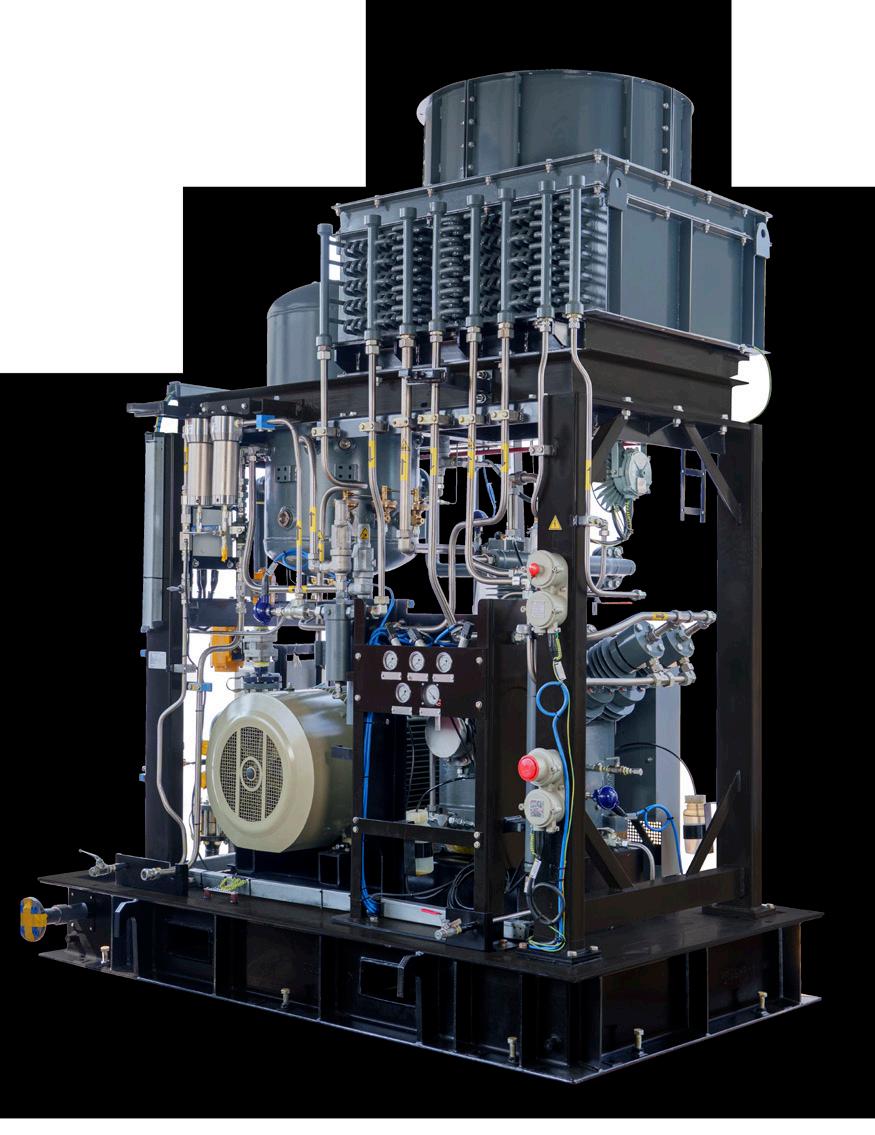