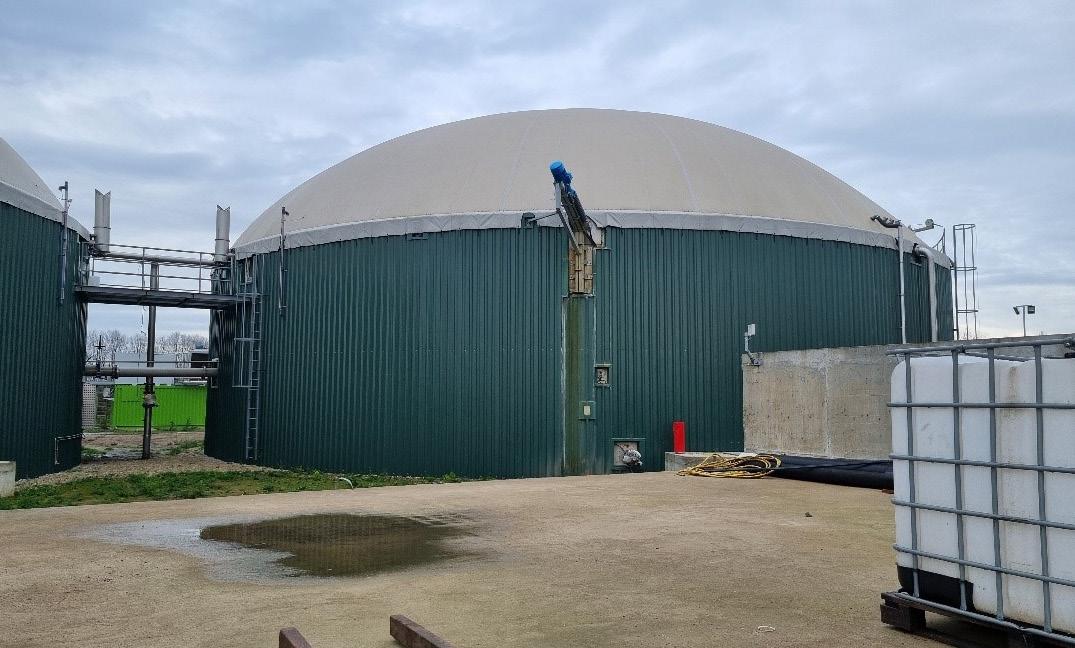
4 minute read
Upstream supply chain in biogas plants: A Croatian perspective
Introduction and function of the biogas plant
The suppliers of input raw materials will primarily be local farmers, whose fields are located in the immediate vicinity of the power plant. Input raw materials will be corn silage, molasses from sugar production, straw, chicken droppings, and cattle manure. Bovine slurry (cow dung) and chicken excrement will be used as additional liquid input raw material, which will be brought from farms in the surrounding area.
The raw material that comes in is processed, fermented in a biogas plant (with a reten- tion time of more than 60 days), and then stored in the final warehouse until it can be taken to the fields. Fermented organic manure will be given to the farmers who initially signed a contract to take manure. Farmers take the fermented liquid manure from the final storage facilities with tank trucks and bring the useful fertilizer to their agricultural fields and areas.
The biogas produced after anaerobic digestion gas is stored in gas membranes above the fermenter and is then converted into electrical and thermal energy via a biogas cogeneration unit with a generator. The electricity that is made will be sent to or sold to the local electricity distributor's network.
The thermal energy of the cogeneration unit is used as process heat for fermentation and for heating the premises of the facility for management and supervision (< 20% of the total thermal energy is used for heating the fermenter and the facility for management).
In the case of non-use of heat energy, the heat energy is drained via the forced cooler.
Suppliers of input raw materials
The power plant operator produces raw materials in their fields.
For one part of the raw materials, they will sign a delivery contract with local and nearby farmers. The farmers will agree to hand over or bring to the plant the required amount of corn silage that is grown in the field each year. In the same contract, the offtake of the digestate or fermented organic manure will be promised to the individual farmers. Through the addition of slurry from cattle manure, the quantity of raw materials increases (compared to corn silage), this means that the farmer receives 30% more fermented slurry than the supplied amount of corn silage (1:1.30).
Farmers use the final femented organic manure (quality fertilizer), which is returned to their fields and meadows.
Substrates and energy yield
Quantities and composition of incoming raw materials
The delivery and purchase of raw materials corn silage, sugarcane, and cattle manure is planned, and the following annual quantities of raw materials, which will be used in the biogas plant, have been calculated:
However, the possibility of using other raw materials cannot be ruled out, such as:
• Expired food products (if they are hygienically safe)
• Spoiled, layered seed
• Sugar noodles, sugar beet, beet leaf, molasses
• Fruit pulp, residues from vegetable and fruit processing
• Seeds, peels, fallen fruit
• Remains of uneaten food
• Remains from the brewery
• Residues from milk and cheese production
• Residues from oil production (if they are free of extraction agents)
Storage, dosing and delivery of incoming raw materials

Corn silage will be brought to the plant once a year during harvest (August and September). Its weight will be measured on a scale, and then the silage will be stored in a trench silo. The operator will provide the necessary compaction of the silage in the mobile silo with a heavy-duty dosing vehicle. All of the raw materials that are brought in will be weighed, and the amount of substrate brought in will be written down in a book about the supply of raw materials.
The substrate mixture consists of liquid from the separation, recirculate from the fermenter, corn silage, molasses and slurry of cattle manure. This mixture of liquid and solid raw materials will be pumped through PE plastic pipes using pumps, and during the day, in a certain quantitative ratio, will be dosed into the biogas plant.
During the flow time of the mixed raw materials, through mesophilic fermentation of the organic part of the dry matter, biogas is produced in the fermenters. The raw material gradually flows through a natural overflow from the fermenter to the post-fermenter. The level in the fermenters is recorded by a pressure measuring device (level measurement) and regulated with the pumping process.
From the post-fermenter, the liquid raw material is pumped to the separator, which will separate the rest of the solid part and the fermented liquid. The liquid residue from the separation is collected in the separator pit, which is located near the separation device and serves effectively as a recirculate in the dosing pit for mixing the new substrate or is pumped through a local pumping shaft to the final lagoon.
The final substrate will be pumped from the final lagoon into the tank of the vehicle via the docking station. The pumped quantities, which are removed from the warehouse, will also be registered and entered in the raw materials book.
Through the processing and fermentation of raw materials, the organic dry fraction of approximately 50%. Due to the closed system, the constituent parts of the materials (N, P, and K) remain equal at 1:1. Only nitrogen (N) will change into a more favorable form of intake for plants, but its quantity will not change. Manure from the biogas plant is considered, due to its various positive properties, as a valuable fertilizer for plants.
Positive features:
• Good homogeneity
• Low odor load
• Good hygienic properties
• Easier availability of fertilizer to plants due to the effect of liquid dilution
• It can be quickly filtered into the soil
• There is no effect from corroding plants, etc.