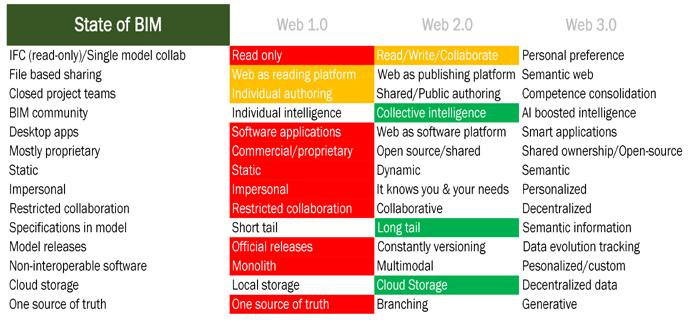
6 minute read
State of BIM and what Web3.0 brings for the construction industry?
Construction sector is regarded as inert, archaic industry where change is slow, it needs decades to be rolled out. Not to mention changes in process, where it comes so slowly that whole industry is built around ‘digitizing the process’. If we would look at today’s software, platforms, digital tools, most of them are built to produce same output from same input that was used decades ago. With the dawn of BIM, which was introduced in 2002, (already twenty years ago!), everyone was excited about what benefits and change it will bring to the built world. More excitement came with introduction of BIM Bew-Richards maturity levels with a vision of full integration of systems, databases and information. The problem is that the maturity matrix is not to scale. The ‘progress bar’ seems to be stuck. Yes, those who embrace the change are blessed with new BIM features, functions and tools. But still, these new features produce same output from the same input as twenty years ago. Not everything is black and white, there are few examples of paperless (drawingless) cases. Mostly in Scandinavian countries. That is something different, so let’s look and maybe we will find some clues what could boost the vector of innovation.
The process depends on input and output and that is our first clue. If you will have same input and if you will have same rules for an output, there’s a limit of how much you can improve processing. You can optimize it, add more processing power, but there’s a cap to how much it will improve. Having different inputs and output creates a shift of productivity (unfortunately it goes both ways), but that is what we can we learn from those few demos that where done. It is not expected that few projects with novel processes will show 50 percent faster design, or 30 percent saved materials, but if these projects weren’t worse, it is already better because novel processes have an overhead, it is called ‘figuring out a process’ and if the project is completed in same or slightly longer time it is still a win for the team. If ‘figuring out’ part would be removed from the project, it shows that there’s a big potential for process improvement. That is why pilots and leading standardization initiatives are so important. One is to pave out the process another is to capture it and reuse.
Advertisement
That is what those few demo projects show. Norway is one of first countries that as an owner invested in paving the road of unknown processes and are looking to standardize workflows to reach and capture the benefits of digital construction. They launched some of their strategic infrastructure projects with a requirement not to use paper or drawings in these projects. Today, almost a third of all bridge projects are done that way. Øystein Ulvestad, responsible for development of drawingless workflows at Sweco Norway was one of key figures in these projects. He says that going paperless gave a lot of benefits:
• Less errors in planning and execution due to detailed 3d-model,
• All involved parties always work on the latest revision (models are hosted in the cloud),
• Data is ready for machine-readability (automation is the future),
• Easier for remote cooperation as BIMmodels are more universal than drawings,
• BOQ is in the model,
• Faster revisions,
• Parametric design can be used (quick changes and reusable design scripts).
There’s not much data about productivity increase, because it is hard to measure, but when BIM-models were introduced as basis for drawings (about 10-15 years ago) project change orders for the Norwegian Road Authorities were reduced from around 19 percent to 8 percent. It is 50 percent improvement! It only shows that the potential is there.
But Øystein also mentioned challenges that come with model-based drawingless design. Drawings in some cases even have advantage, such as display of concepts, repeating details, and the design id more flexible. That is much harder to do in a BIM-model. Also, the vast amount of information in a BIM-model can become a problem without good ways of sorting, filtering, and presenting the right data to the right people, at the right time. Another concern he has is how data is stored. While as built-drawings can be stored as a set of PDF documents, BIM-models often contain digital links to other documents, making it very hard to keep everything together, as having static documents can easily lose links to documents and other models. And the main question he raised “Will the IFC-files we use today be readable in the future?”
As we covered it earlier, there’s a limit to what you can achieve with process optimization without the whole approach revamp. We can already see that there’s a problem with data exchange even if modern BIM workflows are introduced. File exchange is already showing its limitations. Data sync between files, different versions of the same file cannot be managed (branches), even with evolution of IFC is not the real interoperability that everyone is dreaming about. Not to mention, that suppliers are out of this AEC ‘game’ altogether. Digital twins, asset information models are all manual setups which require meticulous data and information management during the project and lengthy configuration to achieve digital twin status for the model.
Have reached the end of the road? Absolutely not. BIM didn’t come from nowhere. At first it was a technological shift that let multidimensional data management which was the effect of databases, then it was powerful computers with cutting-edge graphics that allowed managing of the data locally – a supercomputer on a desktop, and then the Internet with its protocols (http, ftp, etc.) which connected all this into one single network of unparalleled productivity.
At that time, it was not AEC that utilized all these technologies first – advanced search engines, e-commerce, financial technologies were built on the that infrastructure years earlier. If we look at what history of digital transformation shows in different sectors - Lo and Behold there are a lot of parallels and same problems as AEC sector is having. There’s are series of terms used to describe the maturity of Internet maturity – Web X.0. With a dawn of the Internet, it was Web 1.0, then Web 2.0 was introduced in 2004 as a concept of the future Internet technologies. With an advent of blockchain and AI more and more conversations about decentralized, semantic, personalized web experience began to arise. Web 3.0 term was introduced which incorporated all these aspects in around 2016. Limits of how deep you can personalize experience with standards of Web 2.0 are already becoming apparent. Security of blockchain, unmatched speed of querying and multidimensional analytics of data in graph databases and multiply everything with AI boosted insights, that is what will lead the development of web for next decade or more.
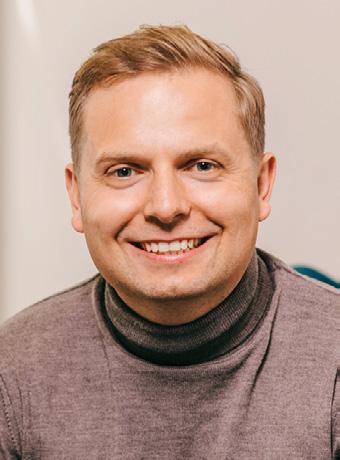
What is it in it for AEC? It is tempting to draw parallels between BIM maturity levels by just comparing numbers (BIM L1 = WEB 1.0, BIM L2 = WEB 2.0, and so on), but let’s look at it objectively. Here’s a table of Web X.0 definitions that somewhat represents same technological aspects of BIM maturity.
Let’s compare where BIM is in the context of existing paradigms. Some aspects are not directly convertible, but parallels can be drawn. Web maturity has underlying cutting-edge technologies and their use cases in mind, and it works as a very good baseline to evaluate a state of BIM. Comparison below is done taking the most common tools and workflows in mind, excluding experiments, or non-mainstream platforms.
Result shows that current state of BIM is still far from utilizing all the technological capabilities in the market. There are a lot of very advanced data management tools for AEC sector that might easily cover the Web 3.0 specification, but one tool alone won’t change an industry. Industry needs whole infrastructure to create an interconnected ecosystem for building design, construction and management. Every bottleneck counts and there are a lot of them in current state.
Let’s try and define what infrastructure would make that difference, for Web 3.0 to work with BIM (or vice versa) and what might be parts of such ecosystem. There are three main parts, that need to be solved.
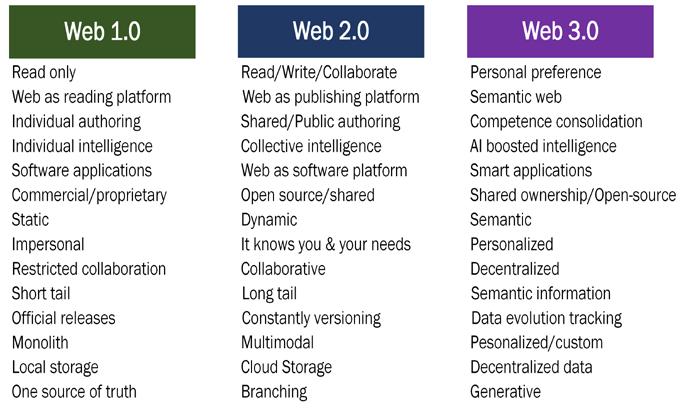
• Open Data Model (Semantic and Modular) with metadata in graph database, to enable Model View Definition to be useful. That would enable features like partial data sharing for a specific design task. Not less, not more. Or Model state change on delivery and automatic conversion to Asset Information Model and much more.
• Open API specification for online tools. This would allow real interoperability in data creation and management, including suppliers’ data. Also, Asset Information Model to Digital Twin conversion by just plugging in sensors through the same API.
• Asset Lifecycle Ledger in a Building Information or Real Estate blockchain, allowing tracking of all the assets throughout its lifecycle with backtracking and other analyses that might be done on it.
These parts would enable full integration of data across whole industry and leading technologies would follow, such as AI learning would be possible with open data model which will then bring AI boosted design suggestions. Also, individualized designer experience, where designer job stack would be individualized by preference and inclination. CDEs as model hosting and source control where feature set would not be directed towards file management but productivity, analytics and data generation, all data connected into one or few flows, a BuildVerse – a MultiVerse for AECMO industries. generative design, analytics, and holistic