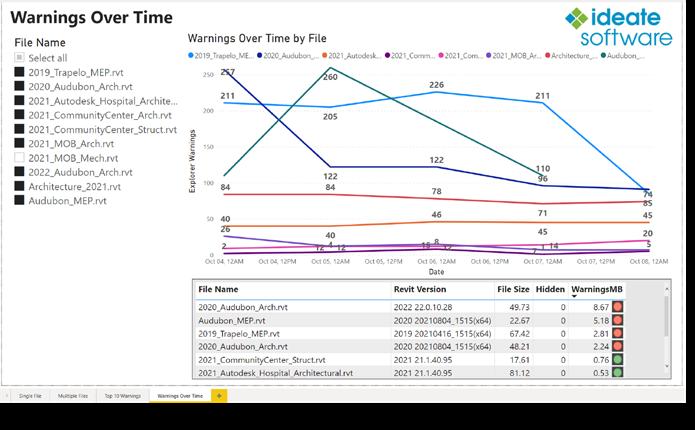
10 minute read
Take Care of Your Revit Models
By Steve Deadman, Customer Success Manager UK/EMEA, Ideate
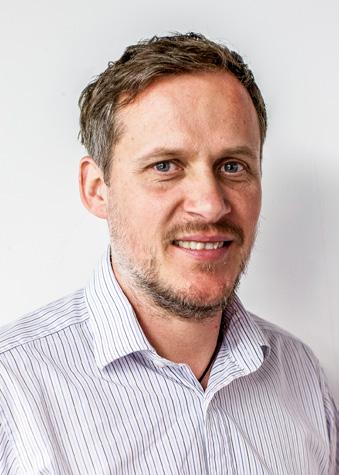
Advertisement
Software
A well-working Revit model is a thing of beauty. Starting with expressing the vision of the architect and continuing through the prevention of clashes and the streamlining of construction and maintenance activities, these powerful models provide visualizations that help everyone involved in every aspect of a structure’s lifecycle save time and money by speeding the process and reducing costly mistakes.
The strength of a Revit model comes from the massive amounts of data within it. While critical for a model to perform as needed, too much data can bog the file down and cause challenges. Managing all the data in a Revit model may sound like a daunting task. But it doesn’t have to be. By knowing what causes problems, recognizing symptoms of unhealthy models, and using proven Revit plugins to proactively audit files and to clean up problem items, Revit users in all disciplines can keep their models in good working order and their projects moving along smoothly.
What Makes A Revit Model Sick? Too Much Data
With Revit models, it is possible to have too much of a good thing. The “good thing” is the data, but too much of it creates problems.
How do models get too much data? Where does all that extra data come from?
To save time and avoid having to recreate work, Revit users often copy/paste information and link to previous projects. When done correctly, these activities are helpful. When done incorrectly, they can bring in massive amounts of unnecessary data associated with the file that clogs up the model and negatively impacts model performance.
Here are just a few common activities that can bring in unneeded data that when left in the Revit file, contributes to an unhealthy model:
1. Loading Unvetted Families
2. Linking and Binding Revit Files
3. Linking, Importing, or Exploding CAD Files
4. Transferring Project Standards
5. Inserting Views and Schedules
6. Creating a large quantity of lines and text objects
An Excessive Number of Warnings
Besides too much data, another factor that can cause Revit model performance problems is an excessive number of warnings. Unlike a Revit error dialog, which requires you to stop what you are doing and resolve the issue, Revit warnings simply inform you of a condition that you may or may not be aware of that may or may not affect your work. Because the program allows users to move past the warning, many people continue with what they are doing and push addressing the warnings to the back burner. They may fully intend to deal with the warnings later, but interruptions, looming deadlines, and a plethora of other distractions get in the way of returning to the warnings, and the number climbs to a point that impacts the model’s performance.
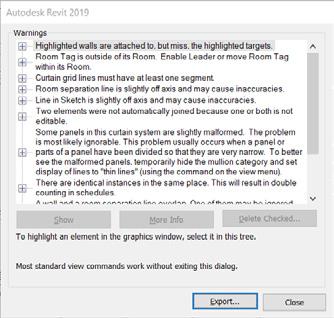
Symptoms Of An Unhealthy Model
Model health and standards issues are typically progressive problems; they start off small and slowly creep in, so you will be able to spot signs that indicate problems are accumulating. Keep your eye out for:
• Slow model performance
- Dialog boxes that take an excessively long time to load
- Slow commands
- Slow opening views
• “Save” issues
• Long model sync times
• Linework that jumps while you pan and zoom
• Printing and exporting problems
• Model upgrade difficulties
• Crashing
When your model exhibits any of the signs above, don’t wait! It is critical that you take action to address these challenges, which left unchecked can lead to these dreaded error messages:
• “Unrecoverable error”
• “A fatal error has occurred”
• “Missing elements”
• “This model is incompatible with…”
Because serious problems generally occur after several smaller problems have built up, the models impacted are usually complex and the clean-up process can be incredibly time consuming and difficult, causing delays that impact employee and customer satisfaction.
Stay On Top Of It With Periodic Health Checks
You’re probably familiar with the phrase, “An ounce of prevention is worth a pound of cure.” Those words apply to Revit health checks! It is much easier to stop the problems associated with unhealthy models than to try to repair a model on its deathbed.
Where to Start
I recommend using Ideate Software plugins for Revit. Yes, I work for Ideate Software today, but I used the products for more than 10 years before joining the company. And I joined the company because I KNOW that the products work and that they address real challenges faced by Revit users. As a customer, I experienced how the Ideate Software team connects with the Revit community for feature requests and works with users during beta testing to ensure the products perform as expected and deliver exceptional value. I am confident that their solutions will help you keep your Revit models running smoothly. Here are some ways you can use Ideate Software plug-ins for Revit to improve the health of your models:
1 You can push large amounts of model health check and QA/QC-related data from your Revit model into Microsoft Excel for review in Excel and Power BI with Ideate BIMLink. In Excel or Power BI, it is easy to identify and flag QA/QC issues or areas that indicate model health problems.
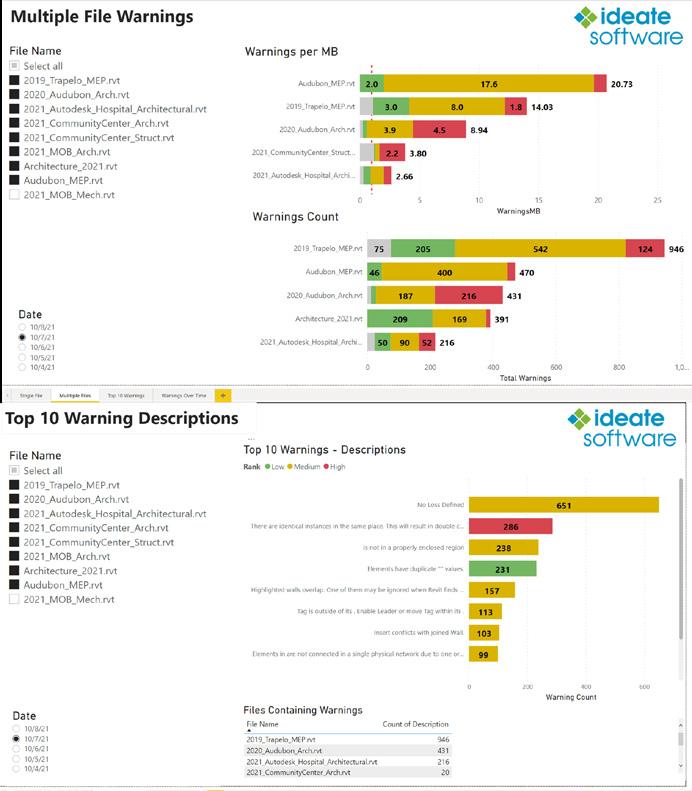
To make it easy for users to select the items to review in Excel, Ideate BIMLink comes with 300+ preconfigured links, which are a series of parameter data mapped together that can be exported to Excel for review. These links, which are customizable, are grouped into several categories, including Health Check and Quality Control. And, because exporting large quantities of data from multiple files can take quite a bit of time, Ideate Software developed Ideate Automation, which automates the process at a time set by you, so you can run the export overnight, and the next day, your data will be in Excel, ready for review.
2 Use Ideate Explorer to dig deeper into your models than possible in Revit to find and fix problem areas. This model browser, as opposed to the Revit project browser, makes it easy to perform on-demand reviews of QA/ QC tasks such as finding and removing CAD imports; addressing group usage; querying a selection of elements to determine if they are pinned, flipped, modelled as in-place families; and much more. Helping you gain even greater control over your data are three features built into Ideate Explorer:
• Too many warnings can bog down a Revit model. You can easily and quickly manage them with Ideate Software’s Warnings Manager, which ranks warnings based on importance, notifies users when their models contain high-ranking warnings, and allows users to correct problems using tools in Revit when the Warnings Manager dialog box is open.
• Use the Navigate function move through view-based elements in a Revit project. Use it to find unused sheets and views; find and filter legends, schedules, sheets, or views by category and/or keyword; and to customize working environments without altering the project browser.
• Search within set parameters for elements such as unused annotations, design options, in-place usage, structure usage/area scheme, revisions, and more with the Query function.
3 The more people that work on a file, the more chances there are for non-standard styles to make their way into the model. Whether a person doesn’t have the style guidelines, unintentionally uses their preferences over the standards, or imports/links to files that bring in their related styles, incorrect styles can impact your documentation, and unused styles can bloat your file size and impact model performance. Resolve all these problems with Ideate StyleManager, which gives users the capability to analyse, merge, or delete non-standard Revit styles more reliably, more quickly, and more accurately than is possible with the style management system built into Revit.
There’s More!
Although this article provides a wealth of details about how Ideate Software plugin tools for Revit help companies maintain Revit model health, it’s just a sampling. In addition to Ideate BIMLink, Ideate Automation, Ideate Explorer, and Ideate StyleManager mentioned above, they have two more products:
• IdeateApps – Streamline common Revit tasks with this collection of productivity and efficiency tools
• Ideate Sticky – Live-link non-BIM data from an Excel, Word, or PDF document into Revit projects
If you work in Revit or lead a team that works in Revit, you owe it to yourself to learn more about Ideate Software plugins. Visit www.ideatesoftware.com for clear product descriptions, blog posts with step-by-step instructions on specific workflows, short how-to videos, and robust Help files. And the team, myself included, sincerely wants to help you succeed and get the most value possible out of your investment in both Revit software and Ideate Software plugins for Revit.
Visit us at www.ideatesoftware.com and reach out to us at sales@ideatesoftware.com to start the discussion on how Ideate Software plug-ins for Revit can help you have better performing Revit models.
Did you know that 5D comes before 3D?

We frequently refer to the Dimensions in BIM, as 2D, 3D, 4D, 5D and so on. 5D is the dimension for cost. Since the dimensions are numbered, it suggests a sequence, where one seems to come after the other. Everybody is familiar by now with 3D and the geometrical model itself, the digital twin.
However, did you know that 5D comes before 3D? Before 2D even?
Every single construction project will define cost information before any model or sketch is produced. Because all projects will have an investment budget, that defines the scope and target the design needs to aim towards.
In business cases, we are already talking about 5D. And it is that early, that we should begin defining the basis of the cost data structure.
Dimensions are therefore opposite to what the sequence suggests, parallel, and not one after the other.
This is why, we should imagine them not as a barchart , where the amount of development seems to grow as the previous dimension is being defined:
Have you ever considered all dimensions and the information that will be produced for each of them in the ICT/BEP, before starting a new project?
Quantity Surveyors or cost specialists working and producing the fifth dimension (5D-Cost information), not only look at 3D geometries, but also 2D drawings and any other written descriptions in the project material, even when they have not yet been defined, because cost needs to cover for everything necessary for the project in the early stages.
They work with all dimensions at the same time because changes in any dimension, will impact directly and indirectly the cost information.
Dimensions are all interconnected and should be revised and updated every time a change occurs.
For this reason, ICT agreements and BIM Execution Plans (BEP) must include minimum requirements and conditions on how to produce the project material, not only for the final delivery, but also along the design process to facilitate the control around these specialist discipline deliveries.
In order to build good standards and grow maturity around these areas, it is necessary to involve, among others, the planners/ schedulers and commercial specialists in the BIM strategy development process. Only in this way will the process take into account the output required by the disciplines not directly involved in producing design material. This is necessary in order to take full advantage of the information produced and incorporate it in the project design.
• Agreement regarding types of outputs (2D, 3D...) for the project information: Diagrams, schedules, details, landscaping, finishes, inventory and equipment… File formats.
• Level of information for each of the design phases

• Scheduled dates for submission after the quality assurance processes, time assigned for quantification and estimation, time remaining for quality checks and clarifications....
• How client deliverables, existing elements or objects out of project scope will be identified in the project material in order to differentiate them.
• How will change be managed, both scope change and design change
• What design material supersedes all others, Specification, models or drawings/ diagrams? So when an error is identified a decision can be taken.
• Document naming and Naming conventions.
Cost management and cost control processes will use the information above, in order to produce:
• Pre-tender estimates;
• Post tender estimates;
• Cost planning;
But inverted as bars, that begin simultaneously, and will progress and develop in the time line, all at the same time, in a parallel way.
While setting up the project, it is necessary that the BIM coordinators and Quantity Surveyors meet to discuss and agree, among other things, the following:
• How many buildings will the project material be split into? Is there a need for an independent model file, and an independent specification document, for each of the buildings or will they be combined?
• Is there a schedule of areas included, what was agreed in the contract and what are the current values, split by net/gross, by building, internal and external areas, and by floors.
• Risk Analysis
• Change management,
• Pricing variations;
• Interim valuations and payment.
Cost plans, estimates, BoQ´s (Bill of quantities), final accounts have historically all been managed as singular activities disconnected from previous or future phases and unrelatable between projects. As cost specialists, we need to begin seeing our deliveries as integrated in the project, and not disjointed as they have historically been.
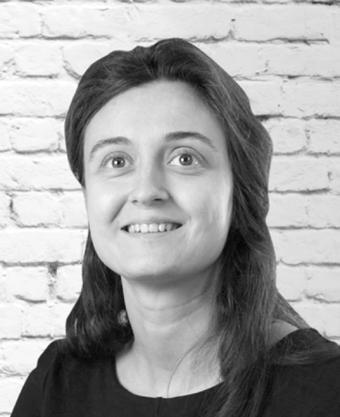
Further more, we should begin changing our mindset and linearity perception of projects.
We look at projects as a linear process,
• we plan them as linear
• we cost them as linear
How do we improve our budget accuracy, as well as our project control while also storing valuable commercial information along the project lifecycle?
The answer is: by perceiving projects as circular. This requires standardization of our data, allowing us to close the loop on project cost circularity.
Automated and standardised data will uncover the potential for cost specialist to be able to:
• Analyse the data of all client projects
• Predict deviations (time, cost, risk, etc)
• Provide more accurate trends to calculate risk and contingency more precisely it can only be achieved as an integrated collaborative process.
• Inform data accuracy based on the quality of data used on the algorithms, predictions, and calculations.
That is why, the Digital QS needs to understand the 3D process and the tools used but does not need to be the expert. This requires regular communication in order to help each other to succeed.
It beings an integrated process, we should not wait until the design is delivered, but work parallel with the design to make sure the output is what is needed and expected. We should not forget that quality is everyone’s responsibility, as well as cost being everyone’s responsibility.
Changes in other dimensions intrinsically affect the whole project, and therefore, it’s everybody’s responsibility to ensure information is aligned to minimise the impact.
Use your network for help and advice. KOSMOS is a consultancy focused on Digital Cost Management, and we would love to have you in our network. Write to us on LinkedIn, we are more than happy to help and discuss.
Ultimately, BIM implementation will allow Value Driven Cost Management since

BIM is forcing integrated design (project) delivery, where the QS (Quantity Surveyor)/ Cost Manager and design team design together.
We need to be aware of what collaboration means. In this regard, it will be the design itself as a direct and automated output of quantities. The quality of those quantifications will be driven by the process and having well defined requirements, and only by being involved in the decisions can good quality data output be achieved.