
8 minute read
HOW TO SANITIZE YOUR GEAR
BY MORGAN TILTON
An array of solutions exist to help keep gear clean and COVID-free, though there is no silver bullet.
Advertisement
Operators in the aerial adventure industry are grappling with the reality of COVID-19 and the sanitation measures needed to stem transmission of the virus. Countless touchpoints and shared equipment—such as harnesses and helmets—made of materials that can’t just be cleaned with any ol’ chemical puts sanitizing and disinfecting at the top of the list of challenges to overcome as restrictions ease and doors gradually reopen.
Many park owners must consider a spectrum of guidelines including city, county, state, or national mandates—some more strict than others. Some jurisdictions choose to carry absolutely no coronavirus safety requirements at all. There is one unified conclusion among experts, though, regarding park sanitization: there is no blanket solution that will work for every single park, piece of equipment, and installation.
THE SIMPLEST SOLUTION?
Soap and water have long been the recommended cleaning agent for aerial operations, and that hasn’t changed with COVID-19. A gentle wash with lukewarm water and soap can clean harnesses and a variety of surfaces and remove the threat of coronavirus.
International Safety Components (ISC), for example, which designs and manufacturers work-at-height safety equipment for a variety of industries, recommends cleaning its products with soap or mild detergent and water that is 104ºF.
Then, most sources agree, the gear should be rinsed with cold water and airdried in a well-ventilated area. It should be put back into use only after it is thoroughly dry. That can take several hours or a day, of course, which has its limitations.
But even if washing is doable, there’s no hard conclusion on the quantity and type of soap or duration of washing, says Edelrid distributor and Tree-mendous CEO Gerhard Komenda.
Another option may be to simply let the gear dry if it’s damp from sweat or rain, and thus allow any coronavirus to die. Unfortunately, there’s little agreement
regarding how long the coronavirus can survive on various surfaces. During the Adventure Park Insider International Huddle in late May, Pit Bangerter of the Swiss Adventure Park Association noted (with mild surprise) that authorities there approved the group’s proposal for a 12-hour drying-out time between uses. However, as Steve Woods of Vertex Instructor Training, a European provider of training and consultancy for off-ground activities noted, studies show the virus can survive for up to 72 hours on some surfaces.
IT’S COMPLICATED
So, while the means to sanitize and disinfect gear exists, it isn’t always practical. “There isn’t a simple solution. Not having an answer has become an answer in its own right,” says Iain Ridehalgh, senior sales manager at ISC.
Ridehalgh is also a director of the Work at Height Safety Association (WAHSA), an association in the U.K. that sets standards for manufacturers and codes of practice for equipment use. Following the COVID-19 outbreak, Ridehalgh also became chairperson of an industry effort internally dubbed the “Vertex working group,” a collective of adventure park stakeholders who are analyzing ways park operations can mitigate the risks of coronavirus transmission.
“We’ve been collecting recommendations for operators for how to disinfect [protective equipment]. We’ve learned that it will not be possible to find a common thread, because there’s such a wide array of advice for different chemicals that don’t apply to all instances,” says Ridehalgh.
Follow manufacturer guidelines. Operators will need to reach out to manufacturers regarding how to disinfect each respective piece of protective equipment on site. The next step is to determine if those specific cleaning procedures are safe, repeatable, and realistic for their operation.
“Some of the guidance might be productive in killing the coronavirus, but it might not be practical in a working environment,” says Ridehalgh. He explains that operators need to do a thorough cross-assessment of chemical usage. For example, when bleach is used for general cleaning, controls need to be in place to protect employees, such as wearing gloves. If the cleaning product is aggressive, there needs to be ventilation, breathing protection, and masks.
ISOPROPYL ALCOHOL: PROS AND CONS
Clearly, as equipment is cleaned to stifle the spread of COVID-19, overall safety management is crucial. Isopropyl alcohol (or isopropanol) is an effective disinfectant that many manufacturers say is safe to use on harnesses (and many other materials and surfaces). Isopropanol works relatively quickly, too: it only takes about 30 seconds to defeat the coronavirus.
Edelrid is one company that recommends isopropyl alcohol to clean equipment, says Komenda. “Edelrid ran stress tests on harnesses with repeated treatment of isopropyl alcohol, and found there was no tangible weakening of the material,” he says. “You need to use a [mixture] that is 70 percent isopropanol.” Pure 100 percent isopropanol evaporates too quickly to be effective, and “if you have less than 60 percent, [sanitizing] becomes pointless,” Komenda says. He notes that 70-proof isopropanol can be purchased, or that distilled water can be manually mixed with pure isopropanol to achieve the 30/70 ratio.
For hard surface or non-porous gear— including plastic or metal items such as helmets, smart belays, and buckles—operators can use a spray bottle of the isopropanol mixture to coat and wipe down the gear, says Komenda. “You don’t want any droplets to become a film.”
No isopropanol on fiber ropes! Take note: isopropyl alcohol may weaken fiber ropes, according to research completed by Teufelberger, a manufacturer of steel wire and fiber ropes and plastic strapping.
“Static ropes are either polyester or a mix of nylon and polyester. Slings are Dyneema,” a composite fabric, says Rob Manson, the segment manager for life safety and recreation ropes at Teufelberger. The company took ropes with each of those constructions and soaked them in 30-percent distilled water and 70-percent isopropyl alcohol mixture, and then dried the ropes using standard wash guidelines.
“We saw a 2- to 4-percent strength loss with each type of rope,” says Manson, and adds, “Using antibacterial wipes along the length of the rope would be less impact, but not as effective [at extinguishing coronavirus] as a thorough soak. The caveat is: we don’t know what the long-term impact of these cleaning methods would be.”
Mason says Teufelberger plans to continue these tests when alcohol and disinfectant wipes become more available so the company can produce a definitive rope-cleaning guideline, “but the medical field needs these supplies more than we do right now,” he says.
STEAM CLEANING
Commercial steaming units are another purifier to consider, according to Bahman Azarm, CEO at Outdoor Ventures, which operates seven aerial adventure parks, and Ropes Park Equipment, which manufactures and supplies a variety of products for aerial adventure operations.
“We purchased a commercial steaming unit, and we are a manufacturer of harnesses that we use at our own parks, so we were able to do testing on our own product,” says Azarm. “These steaming units are used for disinfecting hospitals, and cleaning services use them to clean grout.”
For harnesses, though, Azarm says, “We use the steaming unit at a very low pressure, at a very high temperature (220-230ºF). And we use a dry steam, so that we don’t get the material wet.”
Outdoor Ventures also produced a video for customers to learn about new health and safety protocols used in its parks. “It is just as important to show your customers we are doing these things to protect them, so they feel good about wanting to come to the park,” he says.
WILL NEW SOLUTIONS EMERGE?
Other, creative solutions could be in the works. How soon they wil be available—if at all—is uncertain. Here are two ideas percolating in the aerial adventure realm:
Hydrogen peroxide fogger. Zip line builder Xtreem Ziplines is developing a machine that uses a hydrogen peroxide solution to safely disinfect gear in any work environment in just five minutes, according to company president Craig W. Dick.
Imagine a customized rack on wheels inside a portable room, Dick explains: “You load the racks with the configuration you purchased—it could be helmets, bags, and harnesses, for instance. You open the front doors, push the rack in, sensors signify it’s in the right position, the doors lock, the machine runs through its cycle—it creates a dry fog—and then a dehumidifier runs.” Then, you pull the rack out from the backside of the portable room and the gear is disinfected.
The hydrogen peroxide solution is EPA-approved, non-corrosive, and kills 99.99 percent of all germs, including coronavirus, according to Dick. Xtreem Ziplines is working on becoming a distributor of the solution, which is said to be clear-drying, and does not require a rinse or leave a residue, Dick adds.
Dick expects the first prototype to be complete by the end of July. If it proves effective, the final product, he believes, could be ready for the market soon thereafter.
Disinfecting “grenade.” In France, “a lot of [adventure] parks are waiting for Desinfectant One Shot Total to become available on the market again—it’s sold out. I think it’s the best option for adventure parks to clean equipment,” says Challenge Access owner, technical director, and designer Jean-Michel Sarrazin.
Sarrazin describes the product as “a canister that acts like a grenade. You diffuse it inside a closed room to quickly sanitize everything inside, and use a fan to evacuate all of the air afterwards.” According to Sarrazin the process takes a mere 15 minutes, and is used in hospitals and ambulances. While that sounds promising, it’s not likely to be available in the U.S. anytime soon. “The disinfectant doesn’t exist in the U.S., and would be very complicated to bring here, because it’s a chemical product,” Sarrazin says.
DO YOUR RESEARCH
Finally, operators should check with their local jurisdictions to ensure their procedures meet any new requirements, says Association for Challenge Course Technology (ACCT) executive director Shawn Tierney. Operators will need to tailor their health and safety plans to fit their specific regulations, circumstances, and customers.
For direction, operators can visit the online resource map on the ACCT website, where they can access COVID-19 resources. In addition, Scott Andrews, policy director for ACCT, recommends that all operators review the Centers for Disease Control and Prevention (CDC) guidelines, as well as the United States Department of Labor “Guidance on Preparing Workplaces for COVID-19.”
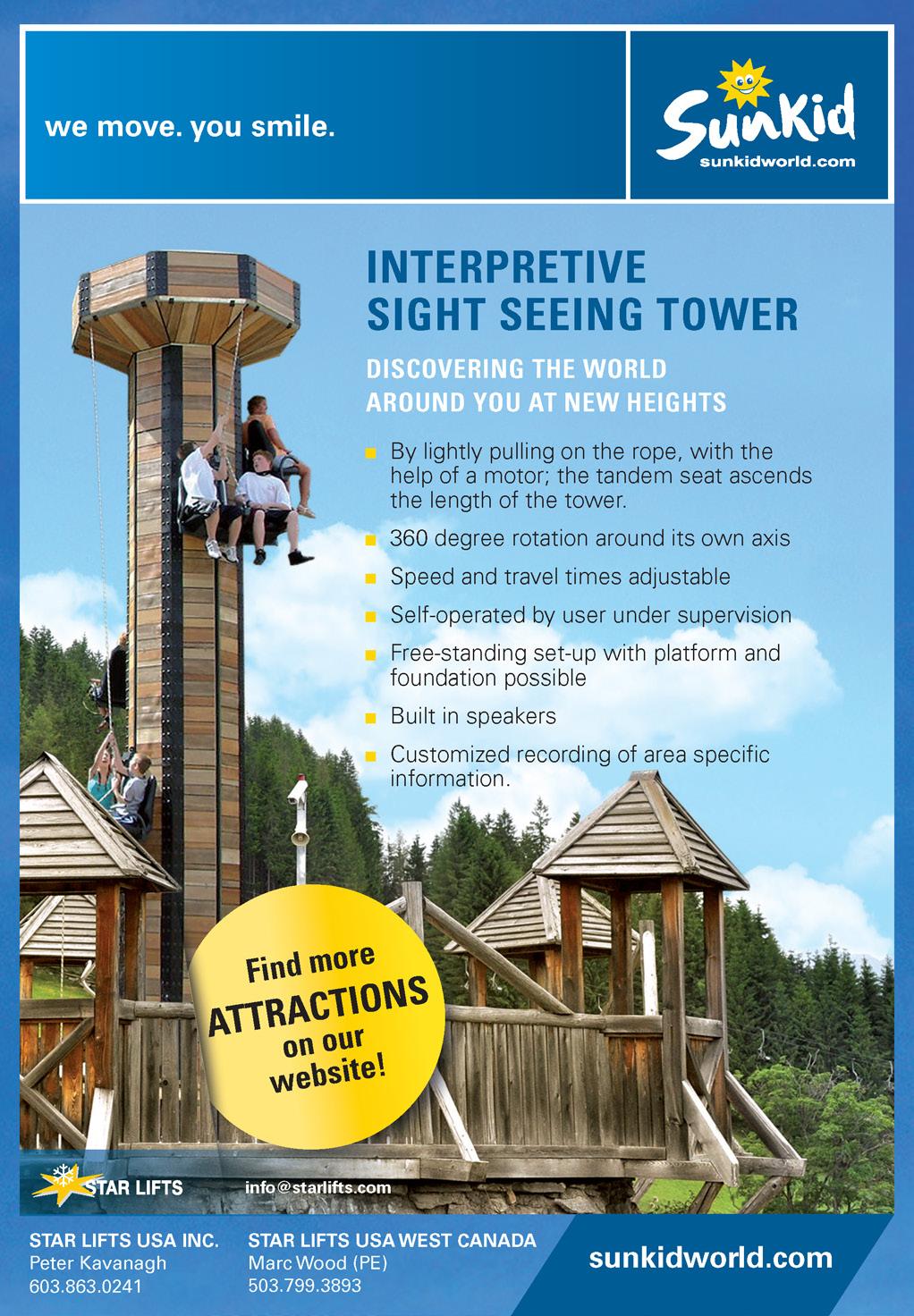
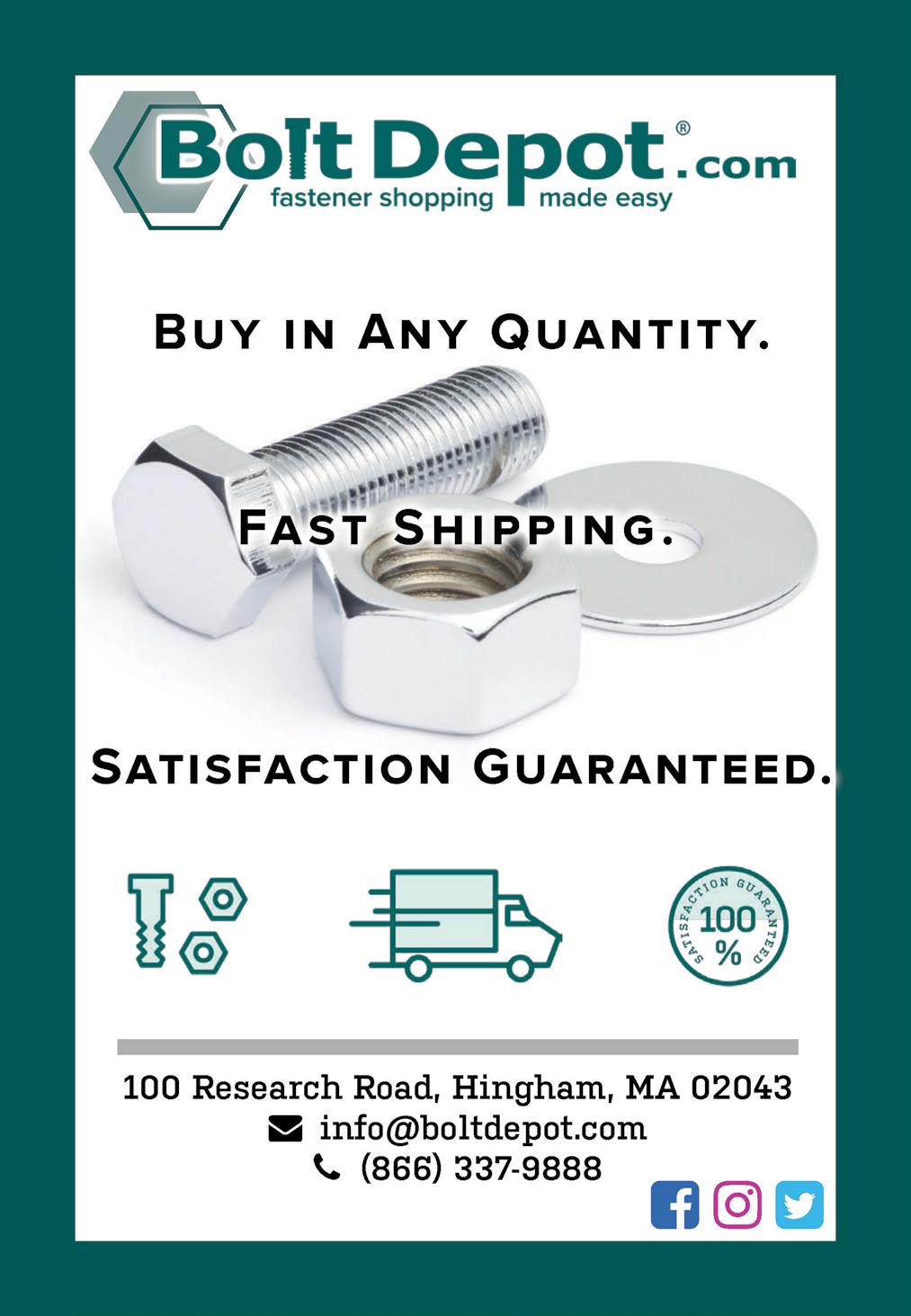
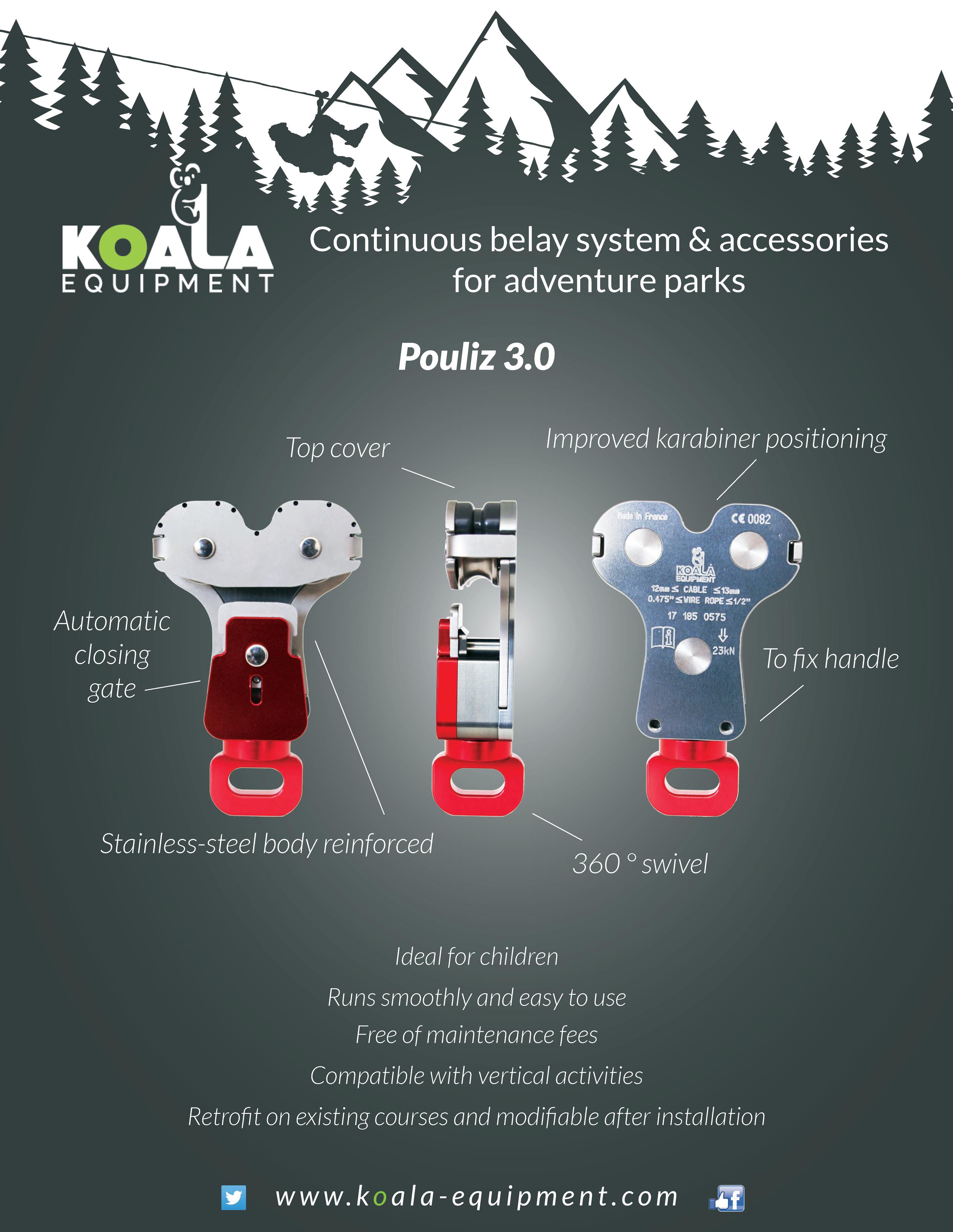