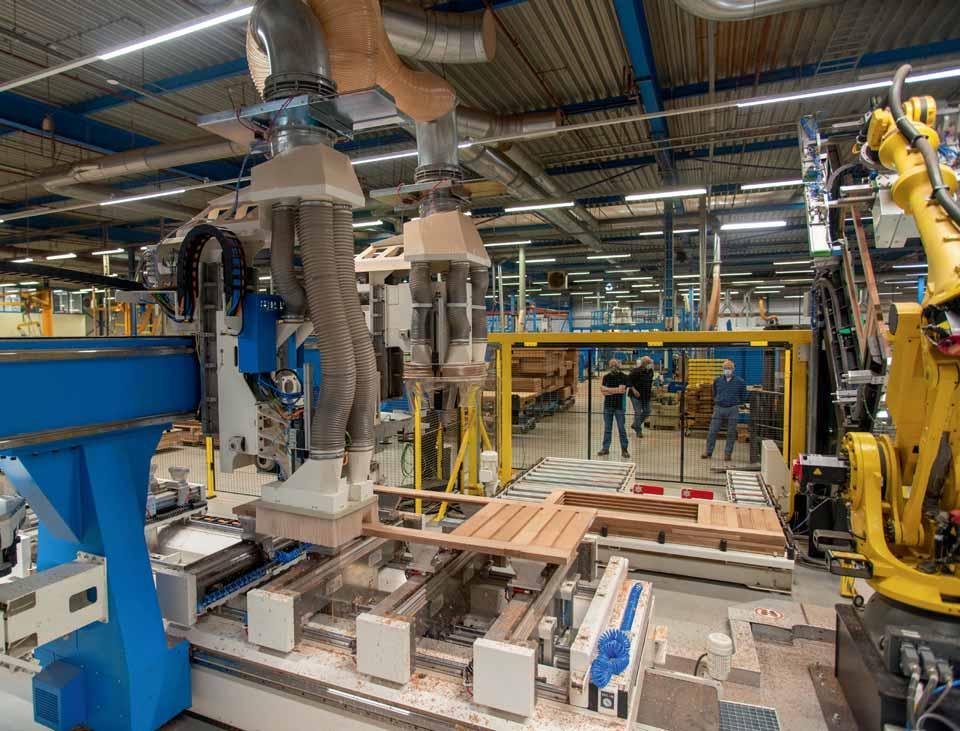
12 minute read
Gerobotiseerde deurenlijn
by BDUmedia
Optimale flexibiliteit en productiecapaciteit
Nieuwe gerobotiseerde productielijn Kegro Deuren
TEKST EN FOTO’S Kees de Vries
2
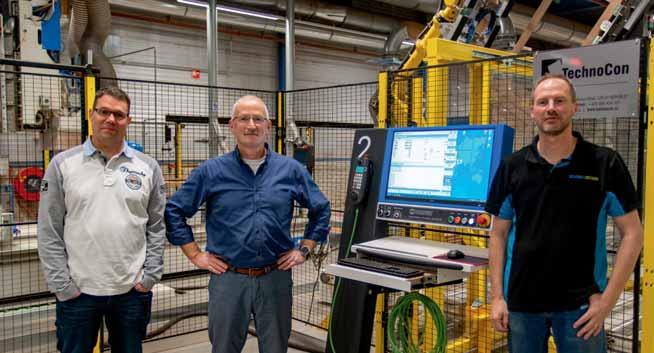
De modernste gerobotiseerde veertig meter lange deurenstraat van het land is momenteel aan het proefdraaien bij Kegro Deuren in Groesbeek. Alle deuren worden in één opspanning afgewerkt, iets dat zowel productiesnelheid als de afwerkkwaliteit zeer ten goede komt. Timmerfabrikant praat met technisch directeur Chris Hendriks over dit technische hoogstandje. “Je praat over maatwerk. Een standaard lijn voldoet ons niet.”
Ten tijde van het gesprek zijn ongeveer 250 testdeuren inmiddels van de nieuwe deurenlijn van Kegro afgekomen. Het is een fractie van de capaciteit van de vier cnc-bewerkingscentra die door twee robots worden beladen. Achter de nieuwe deurenstraat hoort een hele nieuwe manier van programmeren, bewerken en beheren. Het is nu zaak om de nieuwe software te gaan vullen met de grote verscheidenheid aan deurprofielen en bewerkingen die Kegro in het assortiment heeft. Directeur Chris Hendriks zegt: “De nieuwe lijn biedt ons nieuwe bewerkingsmogelijkheden, verbeterde kwaliteit, maatvoering, flexibiliteit, veiligheid en arbeidsomstandigheden.” De nieuwe productielijn bestaat uit vier cnc-machines type Mercury H15 en twee Fanuc-robots van het type M-900iB/280L (longarm). Iedere cnc-machine bevat drie bewerkingsmotoren: een twee-, een vier- en een vijfasser. Verder beschikken de cnc-machines over twee roterende
1 De installatie telt twee productiecellen die elk bestaan uit een robot (rechts) en twee cnc-machines. 2 Technisch directeur Chris Hendriks, geflankeerd door links
Paul Wollenberg (cnc-programmeur) en rechts Martien van
Loenen (afdelingsleider cnc).
magazijnen met ieder veertien gereedschapsplaatsen, een kettingmagazijn met zestig gereedschapsplaatsen en twee aggregaat magazijnen met ieder twee plaatsen. Voor verdere snelheid is de straat uitgerust met automatisch verstelbare vacuümtafels. Een vacuümunit en bedieningsterminal completeren het geheel. De twee robots zijn tussen de machines geplaatst om elk twee cnc-machines te beladen. Zij kunnen een maximaal deurgewicht van 100 kg aan.
3.000 gereedschapswissels per dag
Een belangrijk kenmerk van het ontwerp is de grote hoeveelheid (Leitz) gereedschappen waarmee kan worden gewerkt. In totaal is per machine plaats voor 92 gereedschappen. Een speciaal aangestelde ‘tooling engineer’ houdt het gereedschap in topconditie. Alle gereedschappen zijn voorzien van door de machine uit te lezen chips met daarop relevante data zoals afmetingen en maximale draai- en bewerkingssnelheid. Hendriks: “De keerzijde is dat veel gereedschap wisselen ten koste gaat van de output en kostenverhogend werkt. In samenwerking met hoofdaannemer van het project en leverancier Houfek is er een secondenjacht op de wisseltijden geweest. Gemiddeld zullen er circa 3.000 gereedschapswissels per dag plaatsvinden. Bij een seconde meer wisseltijd verlies je dus feitelijk één uur productietijd.” Dit geldt ook voor het op- en afleggen van de deuren door de robot. “Deze downtime kun je niet voorkomen, maar moet wel zo kort mogelijk zijn. Bij het wisselen van stapels kunnen we dit nu zonder tijdverlies doen.” Voor de bewerking en plaatsing op de rollenbaan worden de deuren aangemeld met een handscanner. Daarna is per deur de barcode bekend, de lengte, breedte, plaats in de stapel, hoogte boven de rollenbaan en het NC-Hops-bewerkingsprogramma. De data wordt doorgestuurd naar een server onder een uniek stapelnummer. De operator bevestigt dit nummer met een barcodesticker op de bovenste deur. Hendriks: “Alle deuren kunnen door elkaar worden bewerkt, zolang we ze maar kunnen stapelen.”
3
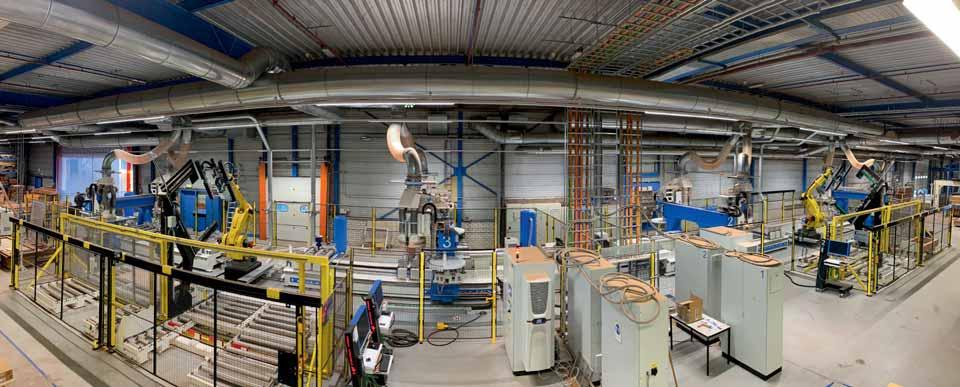
Dirigenten
De robots zijn de dirigenten van het proces en zorgen voor alle logistieke handelingen. De afloop gebeurt als volgt: de onbewerkte deur wordt op de rollenbaan klaargezet om door de robot in de zogenoemde gravity table te worden geplaatst. Deze vertelt de robot precies waar hij de deur vast heeft voor het op de millimeter nauwkeurig positioneren op de cnc-machine. Ook wordt hier de barcode gecontroleerd. Vervolgens wordt het cnc-programma van een server gehaald en doorgestuurd naar de machine. De robot pakt vervolgens de deur opnieuw op, positioneert deze op de cnc-machine voor bewerking. Na bewerking blaast de robot de deur schoon en legt deze op de uitvoer rollenbaan. Wanneer de laatste deur van een stapel is opgelegd moet de
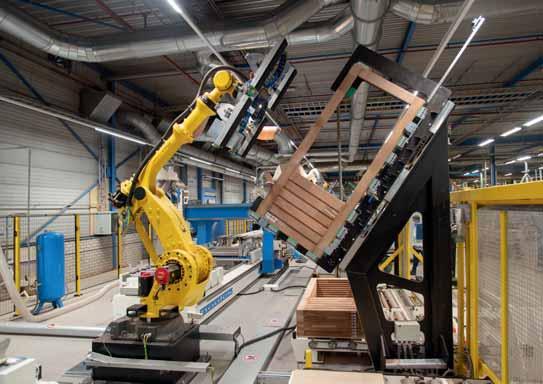
bodemplaat van de onbewerkte deuren op de bewerkte rollenbaan worden gelegd. Om te voorkomen dat de cnc-machines eerst leeg moeten lopen kan de bodemplaat tijdelijk in de gravity table worden opgeslagen zonder dat dit deuren van de volgende stapel in de weg zit. Het stapelen is een nauwkeurige klus en belangrijke voorwaarde voor een ongestoorde afloop. Hendriks: “Alle deuren liggen altijd met de buitenzijde naar boven en krijgen een barcode op de linker onderhoek. Al die zogenoemde zero points in een stapel moeten recht boven elkaar liggen. Zeker bij wisselende deurmaten vergt dat aandacht.” Door alle deuren altijd met de buitenzijde naar boven te stapelen worden vergissingen in de draairichting voorkomen. Op het uiteinde van de robot zit de zogenoemde Gripper, een vacüumsectie die zich automatisch instelt op de breedte van de deur zodat er maatonafhankelijk kan worden gewerkt. Met de komst van NC Hops 7 doet de nieuwste generatie besturingssoftware zijn intrede bij de Groesbeekse fabriek. Hendriks: “Daar waar voorheen NC Active, NC Studio en Alphacam werden gebruikt volstaat nu alleen NC-Hops. Vertaalslagen worden zo voorkomen.” Ook kunnen de bewerkingsmotoren, gereedschappen en vacuümschotels in de software worden geladen om de programma-afloop te simuleren en mogelijke crashes te voorkomen. “Veel bewerkingen of posities die we voorheen zelf moesten programmeren, zijn nu in de software opgenomen. Een op locatie ingemeten deur is nergens recht of haaks. Om bijvoorbeeld een slot of scharnier op een ingemeten deur te positioneren moest voorheen veel geprogrammeerd worden. Dit gaat nu automatisch.”
Afzuiging
De 40 m lange installatie wordt omringd door een veiligheidskooi en in twee productiecellen verdeeld met ieder een robot en twee cnc-machines. Om toegang tot een cel te krijgen moet de operator zich aanmelden bij de toegangsdeur. De hele cel stopt dan met produceren en start pas
3 De hele deurenstraat meet veertig meter. 4 De robot tilt de deuren eerst in de gravity table. Hier wordt de barcode gelezen voor het laden van het programma en wordt de deur exact gepositioneerd voor oplegging op de cnc-machine. 5 In totaal is per machine plaats voor 92 gereedschappen. 6 Een dubbele kooi bij de rollenbaan maakt het be- en afladen van deuren mogelijk terwijl de cnc-machines door blijven draaien. Betreding van de kooi is alleen mogelijk met een persoonlijke veiligheidscode. Gebruik daarvan stopt de productiecel.
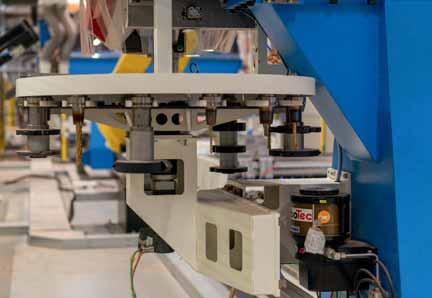
weer op als de operator zich bij het verlaten van de cel ook digitaal heeft afgemeld. Hendriks: “De installatie is groot, de robots krachtig. Dat legt veel nadruk op procedures en procesbeheersing.” Zware motoren die zware profileringen met maximale snelheid in één arbeidsgang frezen leveren ook een maximaal spaanaanbod. De omtreksnelheid van de profielfrezen bedraagt 360 km/ uur, en dat is ook de snelheid waarmee de spanen worden gelanceerd. Er is veel aandacht aan de vorm van de afzuigkappen besteed en in samenwerking met Leitz en Atemag worden er voor alle profielfrezen in totaal 44 spanenkappen gebouwd die gestuurd meebewegen tijdens het frezen. Een stuurklep in de afzuiging zorgt ervoor dat alleen de freesmotor die daadwerkelijk freest wordt afgezogen. De vacuümschotels zijn zelfreinigend. Kegro wil het afblazen uitbannen. Dit project is hiervoor een pilot.
Drie lijnen
Met de nieuwe investering beschikt Kegro met de MKM en de Hüllhorst (tijdelijk) over drie lijnen. De nieuwe cnc’s
5
hebben veel meer mogelijkheden. “Het oude uitfaseren en het nieuwe infaseren is een belangrijke succesfactor van dit project”, aldus Hendriks. “We leveren deuren voor houten, kunststof en aluminium kozijnen. Volgens specificatie of opgemeten, waar dan ook in Nederland, in kozijnen van 1900 tot nu. Het leveringspakket van Kegro is te omvangrijk om alles van te voren te testen.” Hoofdaannemer en leverancier van de installatie is Houfek, in Nederland vertegenwoordigd door Kamp Machinetechniek. Technocon leverde de Gripper, gravity table en Axelent-veiligheidskooi. Selato levert de robotbesturing en de link tussen scanners, robots, cnc-machines. NC-Hops-software is van Direkt CNC-Systems. Leitz levert de gereedschappen.
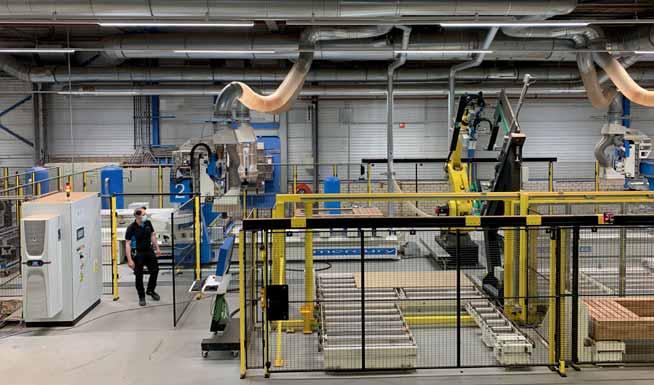
Gelamineerd hout?

Natuurlijk. Van Withagen HOutprodukten
CH12/0549
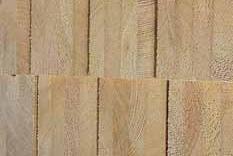
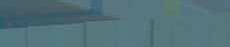
SGS COC-2385
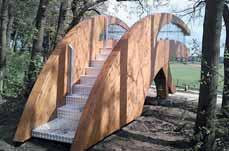
Vilam® staat voor VIgerlassen en LAMineren. Wij maken nagenoeg foutvrij Europees naaldhout ; 100 % PEFC gecertificeerd CH12-0549. Vilam® Europees Lariks in diverse gangbare maten uit voorraad leverbaar. Opbouw uit 24 mm lamellen; rift / halfrift; geen vlam aftekening, radiaal zichtvlak. Vilam® Europees Lariks en Vuren standaard met KOMO certificaat BRL 2902. Geschikt voor het maken van o.a. ramen, deuren, kozijnen, trappen en vliesgevels. Meer informatie en voorbeelden kijk op www.vilamhout.nl
Exportweg 1 9482 WP Tynaarlo T. 0592 - 274280 F. 0592 - 273524 info@vilamhout.nl info@withagenhoutprodukten.nl Directe levering op locatie van gelamineerd vurenhout tot 1m1 hoog en 18m1 lang! Maatwerk in gelamineerd hout zoals gebogen hout, spanten, liggers en kolommen. Bijna 1000 kopmaten in 1 tot 2 weken te leveren, ook met bewerkingen en verbindingen. Voor dragende toepassingen in gelamineerd hout
www.withagenhoutprodukten.nl
Mooie producten verdienen het beste gereedschap
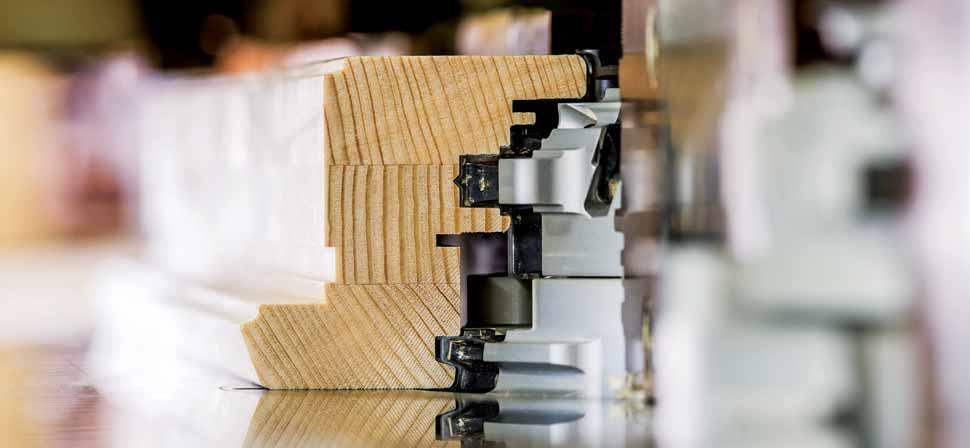
Voelbaar beter! Het is een gewoonte van makers om de vinger toppen langs het bewerkte materiaal te laten glijden. Zo voel je elke oneffenheid en elke afwijking in het oppervlak. Een kwestie van ervaring. Hoewel Leitz niet bij elke opdracht mee kan kijken en voelen, weet het wel uit ervaring welk gereed schap voor welke bewerking het beste is en het mooiste resultaat geeft. Gewoon omdat Leitz al meer dan 100 jaar helpt om eindproducten in de meest uiteenlopende materialen voelbaar beter te maken.
Bijvoorbeeld met de Leitz ProfilCut Q frezen. Kenmerkend zijn de naslijpbare profielmessen die zelfs na het slijpen diameter- en profielconstant zijn. De omstel- en insteltijden zijn kort, hetgeen resulteert in minder productieverlies. Daarnaast biedt een hoog toerental de mogelijkheid voor het snel en kwalitatief bewerken met een snijsnelheid tot wel 120 m/s. De snijkanten zijn van diamant of hardmetaal met een standtijdverhogende coating en de frezen zijn voorbereid voor uitrusting met een code of chip voor een geautomatiseerde productieomgeving.
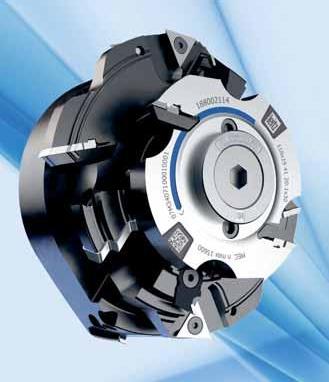
Lijmen en opsluiten cnc-gestuurd
Noviteiten Bos Machines Vianen
De afgelopen periode heeft Bos Machines in Vianen niet stil gezeten. Klantgesprekken staan aan de basis van recent doorgevoerde en geïntroduceerde innovaties op het gebied van de massieve houtbewerking. Zo is er sinds kort ook een nieuwe volledig cnc-gestuurde opsluitbank voor kozijnen en deuren.
TEKST Kees de Vries FOTO’S Bos Machines
Na de BMH Gluemaster automatische lijmopbrengmachine doet Bos nog een extra stap in productieautomatisering met de recent gerealiseerde BMH Pressmaster, een volledig cnc-gestuurde opsluitbank voor kozijnen, ramen, en deuren. Hiermee realiseert de Nederlandse machinefabrikant een langdurige sectorwens om ook deze processtap te automatiseren. Door de beschikbaarheid van nieuwe technieken en aansturingssoftware is het Bos gelukt een betrouwbaar opsluitsysteem te ontwikkelen. Daarbij is een belangrijk uitgangspunt dat de nieuwe Pressmaster geschikt is voor de
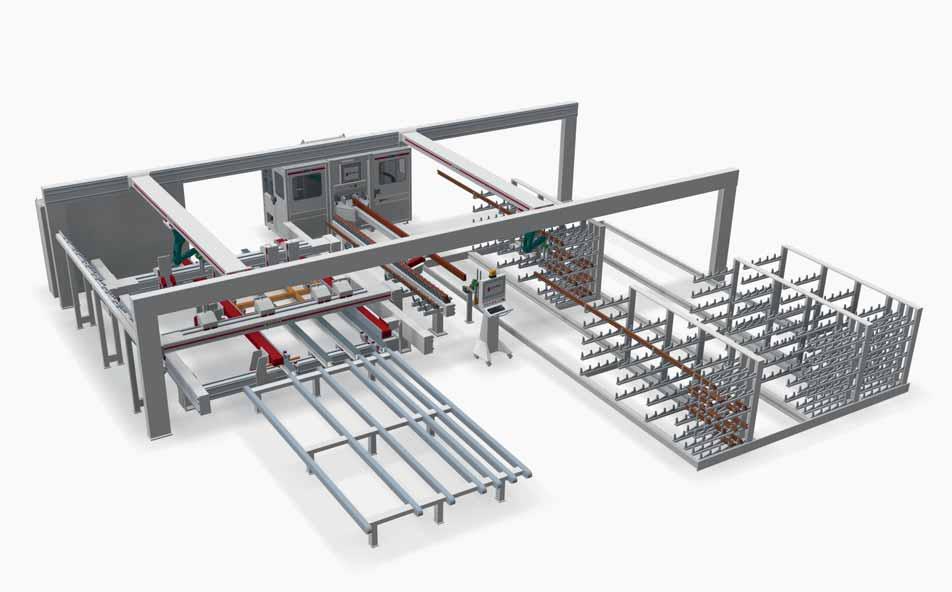
1 De nieuwe BMH Pressmaster volledig automatische cnc-opsluitbank. 2 De BMH Framemaster voor houtskeletbouwers, maar ook kozijnfabrikanten. 3 BMH Windowmaster 10, het nieuwe compacte model.
specifieke producten zoals we die in Nederland kennen. De basis van de BMH Pressmaster wordt gevormd door een horizontale opsluitbank die aansluit bij traditionele principes. Groot verschil echter is dat alle bewegingen elektronisch zijn aangestuurd voor optimale controle en flexibiliteit. Het aanbrengen van de lijm en deuvels vindt plaats via de in het systeem geïntegreerde BMH Gluemaster. Ook het aanbrengen van lijm in de dorpels vindt automatisch plaats. Gebruikers kunnen stapsgewijs doorgroeien naar een Pressmaster, door eerst te gaan werken met de Gluemaster en deze in een later stadium te integreren. Met een minimale opsluitmaat van 260 x 300 mm tot maximaal 3500 x 5400 mm kan een zeer breed scala aan ramen, deuren en kozijnen worden opgesloten. Diverse lay-out mogelijkheden, inclusief automatische aanvoer van onderdelen is mogelijk. De aansturing vindt plaats via de eigen 3D Master-software, desgewenst samen met het bestaande werkvoorbereidingspakket van de klant. Hierdoor ontstaat een compleet geïntegreerde oplossing met één aanspreekpunt voor machine en aansturingssoftware. De voorbereiding voor de productie van de BMH Pressmaster is gestart en zal eind april 2021 gereed zijn voor installatie.
BMH Framemaster
Een andere uitbreiding op het BMH-programma is de Framemaster die aansluit op wensen van zowel de prefab houtskeletbouwindustrie voor elementenhout en de kozijnindustrie voor spouwlatten en randhout. De Framemaster is naar klantbehoefte leverbaar in diverse uitvoeringen. Alle denkbare zaag-, frees- en boorbewerkingen zijn mogelijk. Een meer uitgebreide uitvoering is leverbaar voor de productie van spouwlatten, rekwerken en stelkozijnen. Ook deze noviteit is inmiddels in productie en zal begin 2021 gereed zijn voor installatie bij de klant. Bij de Framemaster is een 3D Master-module geïntegreerd voor optimale aansturing en koppeling aan het werkvoorbereidingsprogramma.
Compacte BMH Windowmaster 10
Noviteit in het BMH-programma cnc-bewerkingscentra is het compacte model de BMH Windowmaster 10. Hoewel qua formaat en snelheid het kleinste model, zit de Windowmaster 10 desalniettemin boordevol nieuwe innovaties. Zo is de machine naast de standaard vijfassige robotmotor voorzien van vijftig gereedschapsposities en servogestuurde afzuigkappen. Dit compacte model is standaard uitgevoerd met de nieuwste generatie BMHmachinesoftware. Naast een gemakkelijk te begrijpen bediening met veel grafische afbeeldingen, ondersteunt de software de bediener door de bewerkingsprogramma’s desgewenst in 3D te simuleren. Ook de standtijden van de gereedschappen worden bewaakt. Alle productiedata kan worden geanalyseerd. De Windowmaster 10 is voorzien van een nieuw vormgegeven bewerkingstafel. Een slimme constructie ondersteunt optimale benutting van de robotmotor. Het resultaat is tot een 30 procent-investeringsreductie in gereedschappen ten opzichte van alternatieve machines.
Topline
Om meer capaciteit uit de bewerkingsmachines te halen introduceerde Bos in 2020 de TopLine-bewerkingstafels met gedeelde onafhankelijk van elkaar in te zetten duo-klemmen. Hierdoor is op de bewerkingstafel zowel aan de voor- als aan de achterzijde een werkstuk te laden en zijn te allen tijde twee werkstukken in de machine te bewerken, ook van verschillende lengte. Bij de Windowmaster 20 en 30 is dit optioneel, bij de Windowmaster 40 en 50 inmiddels standaard. De BMH Windowmaster 50 TopLine behoort dan ook tot Bos’ topsegment. Standaard uitgevoerd met de eigen BMH-software en vier bewerkingstafels leent deze zich uitermate goed voor automatische productielijnen. De eerste twee machines hebben inmiddels hun weg naar de klant gevonden. Transportsystemen rondom BMH-machines vormen een belangrijk onderdeel voor het productieproces. Naast de BMH Loadmaster voor het automatisch beladen van een afkortlijn, heeft Bos in 2020 nieuwe varianten ontwikkeld voor het automatisch beladen van de BMH Windowmaster vanaf etagewagens.
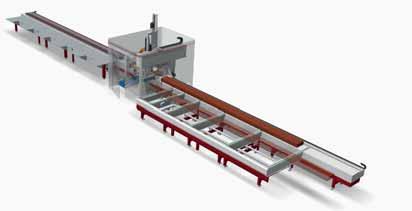
2
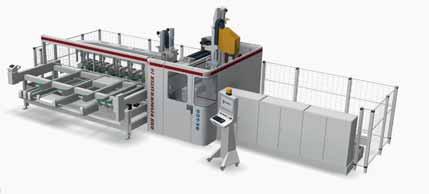