
9 minute read
Hoogwaardige deuroplossingen voor de gebouwen van morgen
Reinaerdt produceert hoogwaardige deur- oplossingen voor de gebouwen van morgen
De deurenfabriek uit Haaksbergen biedt haar producten aan op zowel de Nederlandse als Duitse markt en heeft naast een ruim dealernetwerk ook te maken met onder andere de timmerindustrie en de aannemerij. Het bedienen van deze klantgroepen vraagt een maximale flexibiliteit van de organisatie. Met een sterke focus op vakmanschap innoveert Reinaerdt op materiaal, product en proces.
Deuren spelen volgens Reinaerdt een belangrijke rol in veiligheid, het comfort en de duurzaamheid van gebouwen waarin we wonen en werken. “Een klant vraagt niet alleen naar het dichten van een opening in de muur, maar om kwalitatief hoogwaardige deuroplossingen om veiligheid en comfort te borgen. En dat in de door opdrachtgever of architect gewenste uitstraling, zegt business developer Frank Verdaasdonk”.
Innovatie op product en materiaalniveau
De gebouwen van morgen stellen hoge eisen op het gebied van veiligheid (brand, rook inbraak, vluchten) en comfort (geluid). Steeds vaker is sprake van een combinatie van eisen. Alle prestaties zijn als elementen getest en gecertificeerd. Deze elementen zijn ook achteraf te plaatsen en demontabel voor hergebruik. Helemaal passend bij de trend van modulair bouwen en weer een stap richting een circulaire toekomst, zegt Verdaasdonk. Ook op het gebied van materiaalgebruik staat Reinaerdt bekend om innovatie: als alternatief voor gecertificeerd tropisch hardhout produceert Reinaerdt veel utiliteitsdeuren met een raamwerk van bamboe. Deze grassoort met een fraaie uitstraling is kwalitatief net zo goed als tropisch hardhout én het heeft alle mogelijke brand- en duurtesten doorstaan. Een groot voordeel van snelgroeiende bamboe is dat het al na 5 jaar geoogst kan worden en veel CO2 opslaat. Massieve bamboebalken zijn zelfs CO2-neutraal over de gehele productlevenscyclus.
Flexibele organisatie
Reinaerdt innoveert op productniveau en materiaalgebruik, bovendien maakt het gebruik van Quick Response Manufactoring (QRM), zegt Frank Verdaasdonk. QRM leidt tot kortere doorlooptijden en meer rendement. “Wij hebben onze productieprocessen zodanig ingericht dat er ingespeeld kan worden op de grote variatie in orders zonder dat dit gevolgen heeft voor kwaliteit en leverbetrouwbaarheid. Net als bij Lean stellen wij de klantvraag centraal.”
Processen van morgen
Met een gloednieuw machinepark dat binnenkort volledig operationeel is, speelt Reinaerdt in op de veranderende vraag vanuit de markt, zegt Nick Kamers, werkzaam als operations manager bij Reinaerdt. De klantvraag is flexibeler geworden. Het computergestuurde machinepark van Reinaerdt is in staat om, zonder ombouwen, alle variaties door elkaar te fabriceren. ,,Het maakt niet uit of een deur breed, kort, smal of lang moet zijn, wel of geen gemonteerde accessoires heeft: ze kunnen door elkaar heen worden gemaakt.’’ Dat veranderende productieproces vraagt dus ook om machines die ongevoelig zijn voor omstellingen. Kamers: “Reinaerdt heeft daarom flink geïnvesteerd in een betrouwbaar proces waarbij eventuele verstoringen geëlimineerd worden. Het gaat om geavanceerde, data- gestuurde machines, maar wel met bewezen techniek. Op die manier halen wij maximaal rendement.”
Produceren op montagevolgorde
Zo kan een ‘moeilijk’ product – bijvoorbeeld een combinatiedeur die moet voldoen aan bepaalde prestatie-eisen op het gebied van brand, geluid en inbraak – als standaard worden verwerkt. Verdaasdonk: “Reinaerdt is in staat om op montagevolgorde te produceren. We maken dus niet honderd toiletdeuren die vervolgens over alle verdiepingen van een nieuw gebouw verspreid moeten worden. Nee, we maken deuren per verdieping: een paar toiletdeuren, een meterkastdeur, een toegangsdeur. Onze machines kunnen dat aan.” De inrichting van onze productieprocessen vraagt een verschuiving van werkzaamheden en dat heeft impact op de medewerkers. Voor de nieuwe manier van werken is scholing belangrijk. “Wij leiden onze medewerkers verder op om samen met Reinaerdt te groeien”.
Bouwproces
Reinaerdt beschouwt zichzelf niet alleen als een deurenleverancier, maar als onderdeel van de bouwketen. Het bedrijf is inzetbaar in het hele proces, van ontwerp tot en met montage, van deur tot kozijn. Om een foutloos en beheersbaar bouwproces te garanderen is het belangrijk om in een zo vroeg mogelijk stadium simpele en complexe vraagstukken te beoordelen en uit te werken. Tegenstrijdigheden en onvolledigheden in wensen en eisen kunnen hierdoor worden uitgesloten. Reinaerdt is klaar voor de Wet Kwaliteitsborging. Onze producten zijn direct toepasbaar, compleet en voldoen aan alle gevraagde specificaties. Kortom: Reinaerdt is totaalleverancier. Samen met ketenpartners maakt het bedrijf de stap naar een circulaire toekomst, om de volgende generatie een toekomstbestendige woon-, werk- en leefomgeving te geven.
Spraakmakende projecten met deuren van Reinaerdt
Amare, Onderwijs- en Cultuurcomplex (Den Haag)
Voor dit nieuwe culturele knooppunt van de stad heeft Reinaerdt ruim 1100 deuren geproduceerd en gemonteerd, waaronder 90 minuten brandwerende deurstellen en 130 speciaal ontwikkelde deuren met een dikte van 71 millimeter en een geluidwerendheid van liefst 48 dB.
Grandaire (Berlijn)
Deze luxe woontoren is een echte eyecatcher aan de Alexanderplatz. Reinaerdt heeft samen met dochteronderneming in Saterland verschillende producten geleverd en gemonteerd, zoals schuifelementen, brede montagekozijnen en vochtwerende elementen voor de badkamers. De woningtoegangsdeuren zijn 30 minuten brandwerend, rookwerend, inbraakwerend en geluidwerend.
Binnenwanden en deuren voor MorgenWonen
Als onderdeel van VolkerWessels produceert Reinaerdt alle kant-en-klare binnenwanden en deuren voor MorgenWonen, een concept van VolkerWessels. MorgenWonen wordt gezien als de grensverleggende bouwstandaard en staat voor duurzaam, onderhoudsarm, betaalbaar en zonder energiekosten. Alle woningelementen worden in één dag in elkaar geklikt en staat het casco. Daarna vindt de afwerking plaats, inclusief het plaatsen van binnenwanden en deuren van Reinaerdt. Dit artikel is gesponsord door Reinaerdt Deuren)

Met een stalen lans worden de strips de grond in gedrukt. Foto: Carel Kramer/Cofra
Vijf keer de aarde rond met drains voor luchthaven Manilla
Veruit het grootste project uit de bijna honderdjarige geschiedenis van Cofra is de grondverbetering voor de nieuwe luchthaven van Manilla in de Filippijnen. Daarin verwerkt het grondverbeteringsbedrijf maar liefst 200.000 kilometer drain; vijf keer de aarde rond. Ook voor moederbedrijf Boskalis is het het grootste project dat het in haar geschiedenis alleen, dus niet in combinatie, heeft aangenomen. De totale aanneemsom voor Boskalis bedraagt 1,5 miljard euro. Het ingenieursbureau dat ter plekke toeziet op de landwinnings- en grondverbeteringsactiviteiten wil zelf de kwaliteitsbewaking uitvoeren. Vandaar dat inmiddels vijf van de zes drainage testketels uit het eigen laboratorium naar Manilla zijn overgevlogen. In Amsterdam bouwt Cofra koortsachtig nieuwe testopstellingen om de kwaliteitsbewaking voor de rest van de productie te kunnen waarborgen. De BioDrain wordt niet toegepast in Manilla.
Voor het bouwrijp maken van een nieuw terrein voor een busremise in Purmerend is inmiddels 100.000 strekkende meter BioDrain verwerkt.
Stalen lansen
Bij verticale drainage is het zaak dat de strips, om te beginnen, onbeschadigd de grond in gaan. Dat gebeurt met dikke stalen lansen die de drains precies op de gewenste diepte plaatsen. Zodra ze daar zitten, moeten de gootjes in de geribbelde kern een uitweg bieden voor grondwater dat diep in de bodem zit opgesloten. Geholpen door extra grondbelasting op maaiveld wordt dat naar boven geperst. In plaats van twee of drie jaar tijd zoals met alleen bovenbelasting, is het consolideren van de bodem met verticale drainage in drie maanden tot een jaar gepiept. De sterkte en stabiliteit zijn dan flink toegenomen en zettingen doen zich nauwelijks meer voor.
Die gootjes moeten dan wel al die tijd open blijven staan en niet verstopt raken met klei, veenresten of ander bodemmateriaal. Daarvoor zit dat vlies om de kern. De poriën daarvan moeten niet te groot, maar ook weer niet te klein zijn. Ze moeten precies de fijne bodemdeeltjes tegenhouden, maar water doorlaten. En de drain moet ook blijven werken, als hij na verloop van tijd een bocht maakt of scherpe knik, omdat de bodem is ingeklonken. Zelfs twee of drie knikken mogen de waterafvoercapaciteit niet noemenswaardig beïnvloeden. Van den Horn: “Het is een gevoelig samenspel tussen bodem en drain, dat we voortdurend bewaken met onderzoeken in ons eigen testlaboratorium.”
Die gevoeligheid is de reden dat het ontwikkelingstraject van de biobased drain zo’n tijd in beslag nam. Cofra is zeker niet het eerste bedrijf dat polypropyleen in haar product probeert te vervangen door een kunststof op basis van melkzuur. Maar de sterkte, de waterafmateriaal is weliswaar composteerbaar, maar vooral in een industriële composteerinstallatie zoals die in gebruik is bij afvalverwerkers. In de bodem, onder water afgesloten van zuurstof en uv-straling breken de drains niet af, maar blijven misschien wel honderd jaar intact. In dat opzicht is er weinig verschil met de gebruikelijke drains van PP. Het uiteindelijke doel is een materiaal dat na verloop van tijd afbreekt, zodat er niets in de bodem achterblijft dat daar niet thuishoort.
voercapaciteit, de poriegrootte... Alle eigenschappen moeten gelijk blijven om de werking van de drain te garanderen. Opdrachtgevers die voor een paar miljard een nieuw vliegveld in zee laten aanleggen, willen niet het risico lopen dat de consolidatiemethode niet werkt, omdat de producent met een andere grondstof is gaan werken.
Duurder dan klassieke drain
Ze zullen zich sowieso wel eens op het achterhoofd krabben, aangezien ze voor de BioDrain voorlopig twee keer zoveel moeten betalen als voor de klassieke drain. Dat komt onder andere doordat PLA’s niet aan te slepen zijn. Iedereen die met kunststof werkt, wil overschakelen op biobased en het aanbod van de grondstoffen is nog beperkt.
Geïnstalleerd in de bodem is de prijs van de BioDrain nog altijd 1,5 keer die van het klassieke exemplaar. Op het totale bedrag van een landaanwinning of dijkversterking betekent dat misschien een bescheiden extra kostenpost, maar Van den Horn weet ook wel dat dat argument bij onderhandelingen en aanbestedingen niet altijd indruk maakt. Daarom is hij blij met de eerste twee projecten waar de opdrachtgever budget over had voor een duurzame oplossing.
Terwijl Cofra zich moeite getroost om de BioDrain aan de man te brengen en de prijs omlaag te krijgen, kijkt het bedrijf ook nog voorbij de horizon. Het
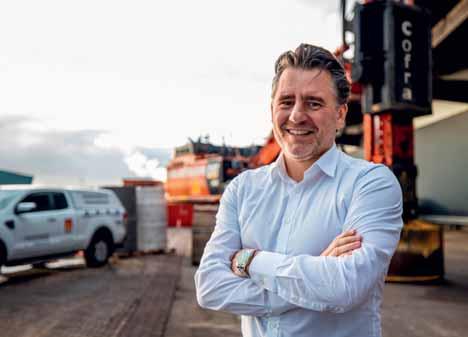
Algemeen directeur Paul van den Horn van Cofra. Foto: Mathieu Peters
Papieren drains
Het gebruik van de papieren drains waarmee verticale drainagetechniek zo’n zestig jaar terug begon, als alternatief voor zandkolommen, ziet de Cofrabaas niet terugkomen. “Dat stuitte al op problemen, want water en papier gaan niet goed samen. Ook niet als je het voorziet van een coating”.
De zoektocht naar een drain die na een jaar of twee uit elkaar valt, is dus al gestart. Dat is nog complexer dan de zoektocht die nu achter de rug is. Dat vergt opnieuw aanpassing van de receptuur en alles wat daarbij komt kijken.
Innoveren in stapjes
“Wij hebben ons de afgelopen jaren natuurlijk best eens de vraag gesteld of het niet zonde was van alle moeite de ontwikkeling van die biobased drain enkel te richten op de grondstof”, besluit Van den Horn. “Vroegen ons af of we ons niet beter meteen konden richten op de ontwikkeling van een drain die na twee jaar spontaan uit elkaar valt. Maar we geloven dat innoveren beter werkt in stapjes, dan dat je in één keer een reuzensprong probeert te maken, met het gevaar dat je de overkant niet haalt. De ontwikkeling van de BioDrain betekent echt een enorme stap. Een gigantische stap. Maar we zijn ook realistisch: we zijn er nog niet.”