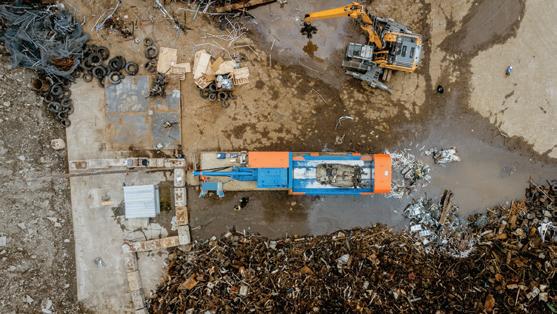
2 minute read
TECHNOLOGY COMPOSITION
The Kappa shear baler is built with a heavy-duty internal structure that increases the weight of the machine compared to similar products on the market. Taurus units are also made with extra heavy-duty steel hydraulic piping with double-welded inside and outside couplers, ensuring the 420-bar high pressure of the hydraulics does not leak. Taurus designs and constructs each surface in a way that ensures that the throughput per hour of the Kappa remains consistent throughout the machine’s life cycle when properly maintained. All Taurus machines are completely assembled prior to delivery to ensure manufacturing fines are removed from the hydraulics circuits.
The Kappa shear baler is equipped with advanced technology, including patented over stroke on each wing that provides maximum power in compression. Its design allows for compression forces of up to 650 tons on each wing, allowing large items to be manipulated into the shear box for processing. The shear head of the Kappa is equipped with double cutting cylinders and prismatic guides which reduce wear and ensure reliable cutting operation. The machine does not require foundations or special permits, making it an efficient and cost-effective solution that causes little disruption to existing recycling processes.
Operation
The Kappa’s intuitive cabin controls and an optional remote control allows for quick and simple adjustments. The touchscreen control system constantly monitors and optimizes the squeezing and cutting process. The system minimizes downtime since maintenance can be planned efficiently and performed before costly repairs are needed. Numerous programs for different scrap types can be selected at the touch of a button, such as full stroke, partial stroke, relative stroke, and baling. When service is required on Taurus shear balers in North America, ELV Select Equipment makes remote service and parts available to ensure that downtime is limited.
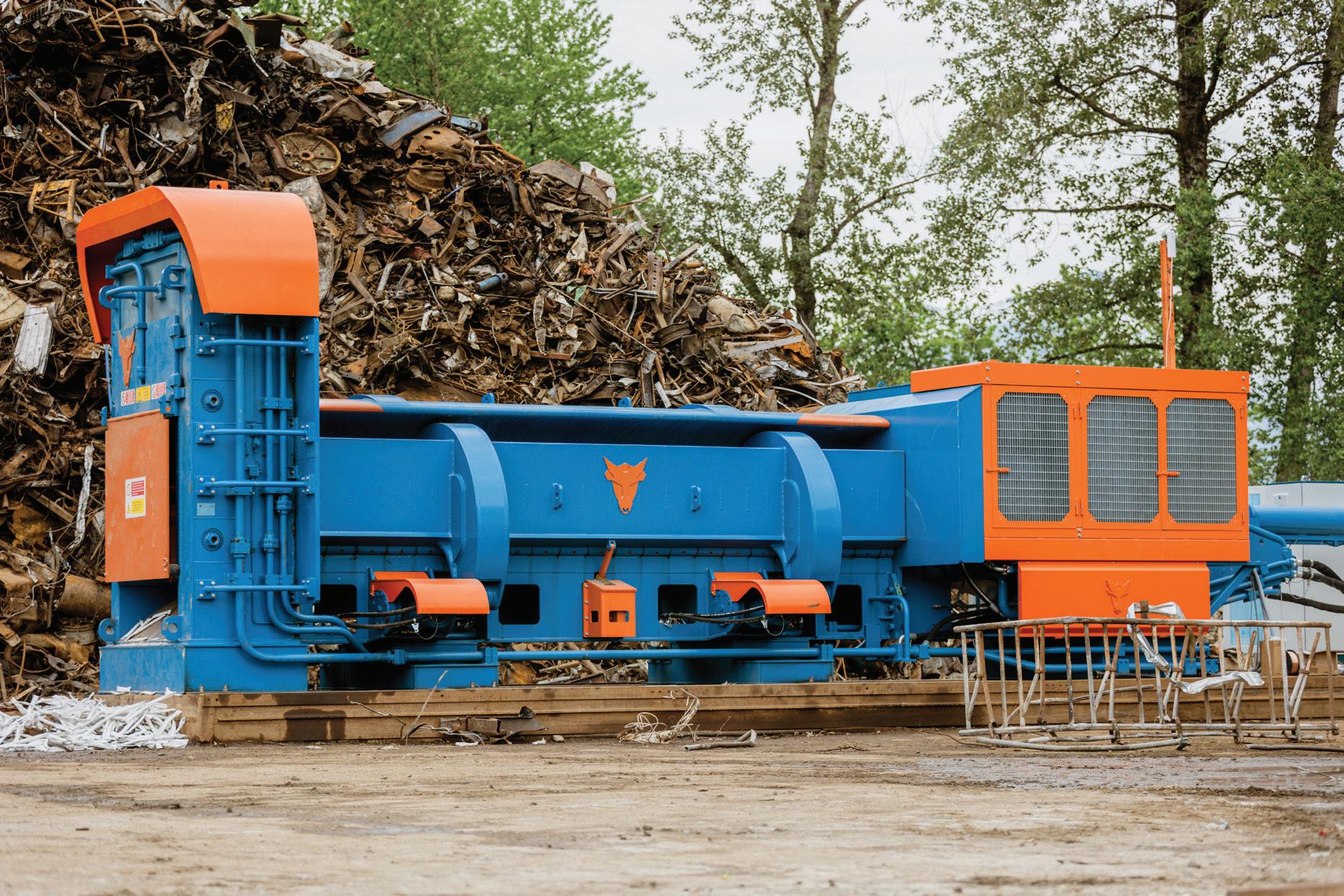
1
2 MACHINEX II-RAM SERIES
HARRIS EQUIPMENT CENTURION

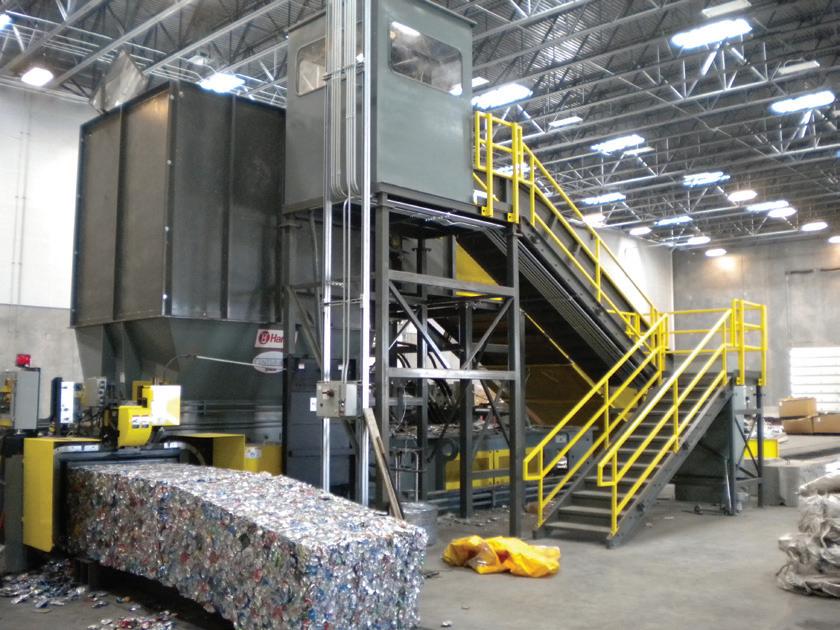
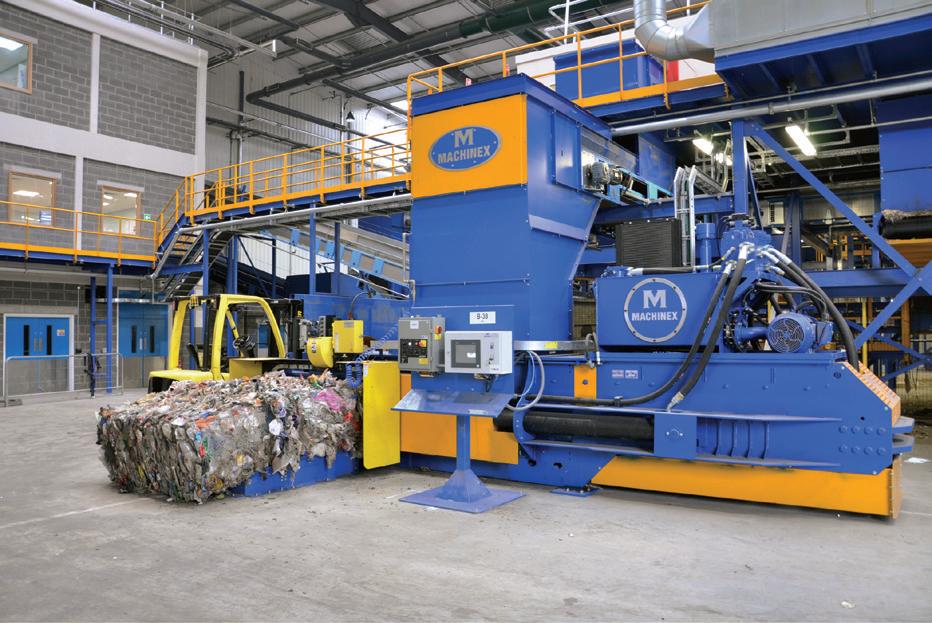
1high-capacity balers are designed to maximize density while reducing operating costs. According to Machinex, the exclusive pre-fill valve offers a dry cycle time of up to 2.7 times faster than similar machines, resulting in a significant reduction in energy consumption while also increasing the main ram cycle speed in both forward and reverse modes. Maintenance is simple with convenient bolt-on liners, allowing for easy upkeep and minimal downtime. Additionally, the II-RAM balers feature a single-plate frame construction for maximum strength and durability.


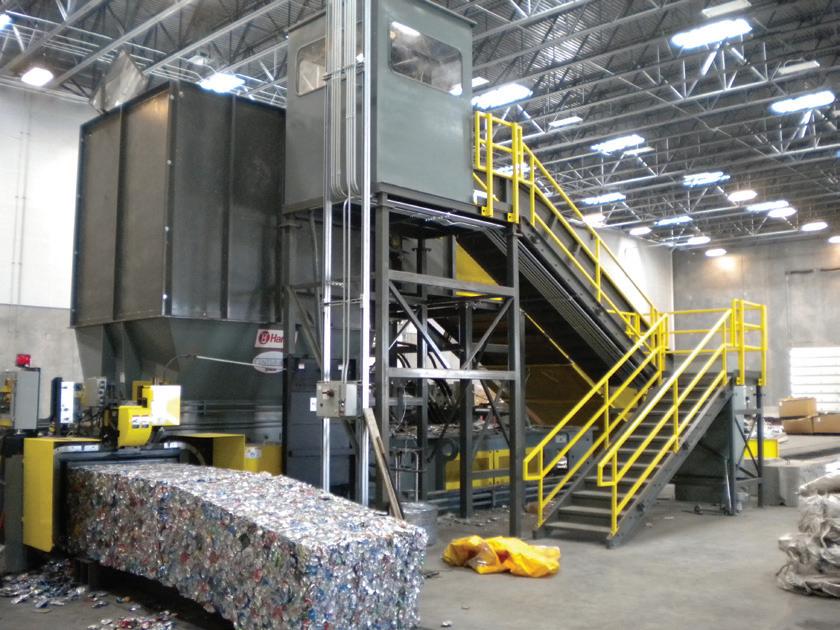
3
AMERICAN BALER W828 SERIES
4
SIERRA INTERNATIONAL MACHINERY REB-4
2Centurion is a high-performance two-ram baler designed specifically for medium- to high-volume applications. The multi-purpose Centurion features a 13-inch bore main cylinder and, like all Harris two-ram balers, has a solid one-piece body design. The machine features laser-guided hydraulic ram cylinders and electronic pumps for millimetre precision control on each cycle, in addition to a reinforced bale chamber with thicker and additional interlocking ribs. The large shear knife is thicker and taller than traditional tworam baler knives to handle the increased shear force from the main ram cylinder.
3Series of two-ram balers is ideal for most paper, plastic, and non-ferrous metal baling applications. Recently upgraded, the W828 models now come with a power unit and manifold block designed with off-theshelf Parker Din Cartridge valves on the manifold and standard directional control valves. Available with either a 43-inch-wide frame or 60-inch-wide frame, the W828 Series of two-ram balers offer several charge box opening lengths, single-side sheet construction, and sequenced motor start-up with an Economizer mode to shut down motors when they’re not in use.
4
Sierra International Machinery’s REB-4 two-ram baler is ideal for non-ferrous metals, OCC, natural HDPE, and paper. Sierra’s patented dual-compression door technology means materials can exceed 30 inches above the cutting knife, and with a force of 55 tons per door, the material is pushed below the knife and into the chamber, resulting in a 20 to 40 percent increase in production capacity. By minimizing the area requiring shearing by 90 percent when fully closed, the REB-4 reduces shear and hydraulic shock while optimizing energy consumption, cutting costs and ensuring a longer lifespan for the baler’s blades and structure.