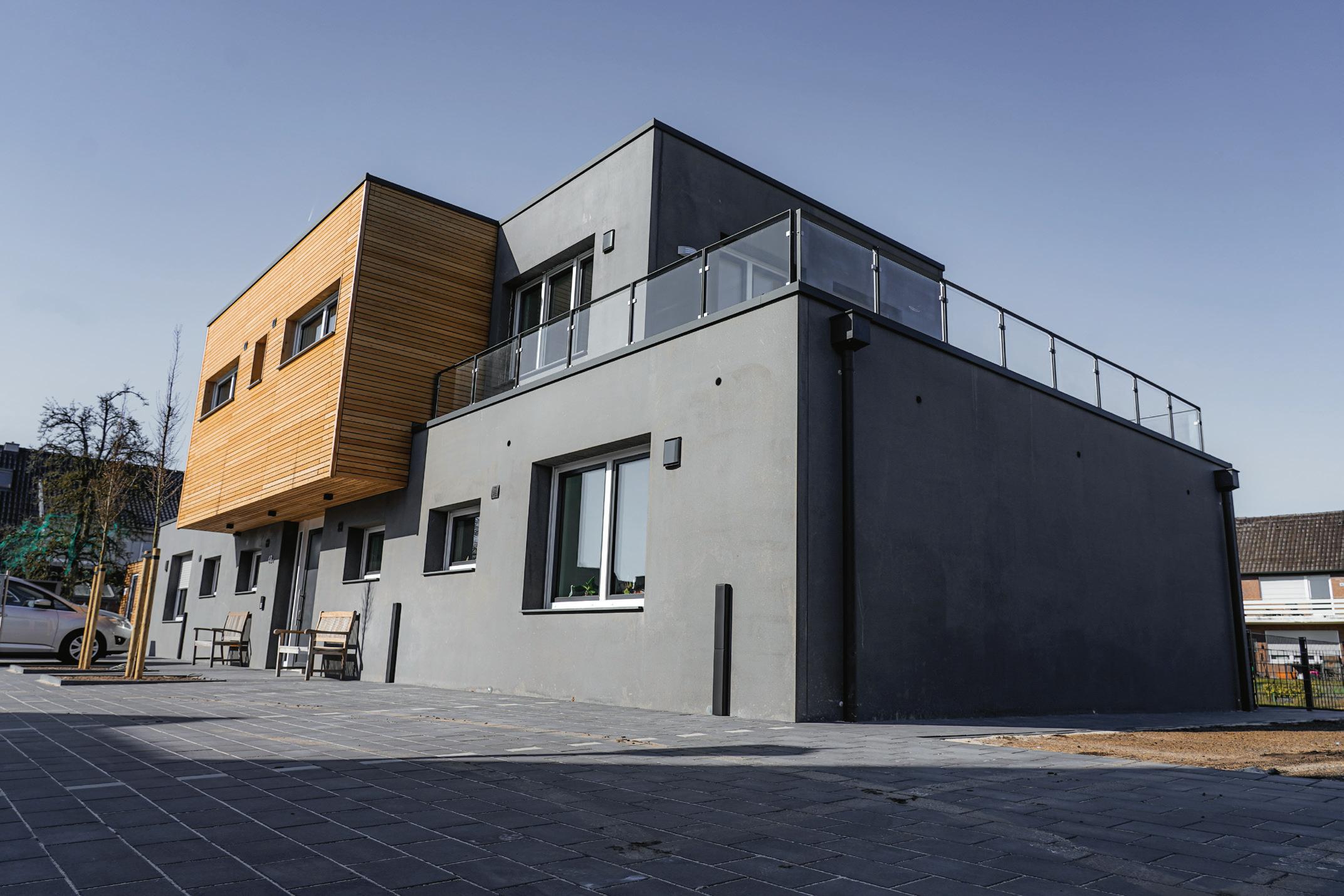
3 minute read
BÜSCHER BUILDS HOUSE MADE FROM 75 PERCENT C&D WASTE
KEESTRACK’S ZERO-EMISSIONS EQUIPMENT POWERED THE SUSTAINABLE PROJECT
Even with decades of experience in the industry, Büscher, a concrete producer based in Germany, recently took on a project that was something it had never tried before: building a house made out of 75 percent recycled construction and demolition (C&D) waste.
When Büscher first started out in 1961, it made concrete like everybody else – with gravel, sand, cement, and water. Now, the company has changed the recipe so that 100 percent construction and demolition waste replaces the sand and gravel completely in the prefab load-bearing and non-load-bearing interior wall elements. The outside walls, however, are not made out of recycled materials.
Through its disposal service offerings, Büscher routinely received a lot of C&D waste which was recycled into aggregates for road construction. Since this material was difficult to sell and was available in high stock quantities, brothers Wolfgang and Hans-Jürgen Büscher started to explore other ways that the materials could be reused. Their conclusion was to use this C&D waste as a raw material for prefab concrete and concrete elements.
Research And Development
The idea was sustainable, but it was hard to convince both authorities and specialists in the field that it was feasible. Getting 100 percent prefab concrete certified was difficult, and it took Büscher eight years of research and development to get approval.
“Concrete specialists, laboratories, and certification specialists were very doubtful this could be done,” said Wolfgang Büscher. “They all said it is impossible and not legal.”
Büscher gave researchers from laboratories and universities the parameters of what the company wanted to achieve with the materials, and waited to see if it could withstand the tests.
“By now, all scientific research has been done and it shows exactly what is possible with 100 percent recycled prefab concrete and concrete elements. The new material functions perfectly, and the recipe has changed at Büscher,” says Hans-Jürgen Büscher.
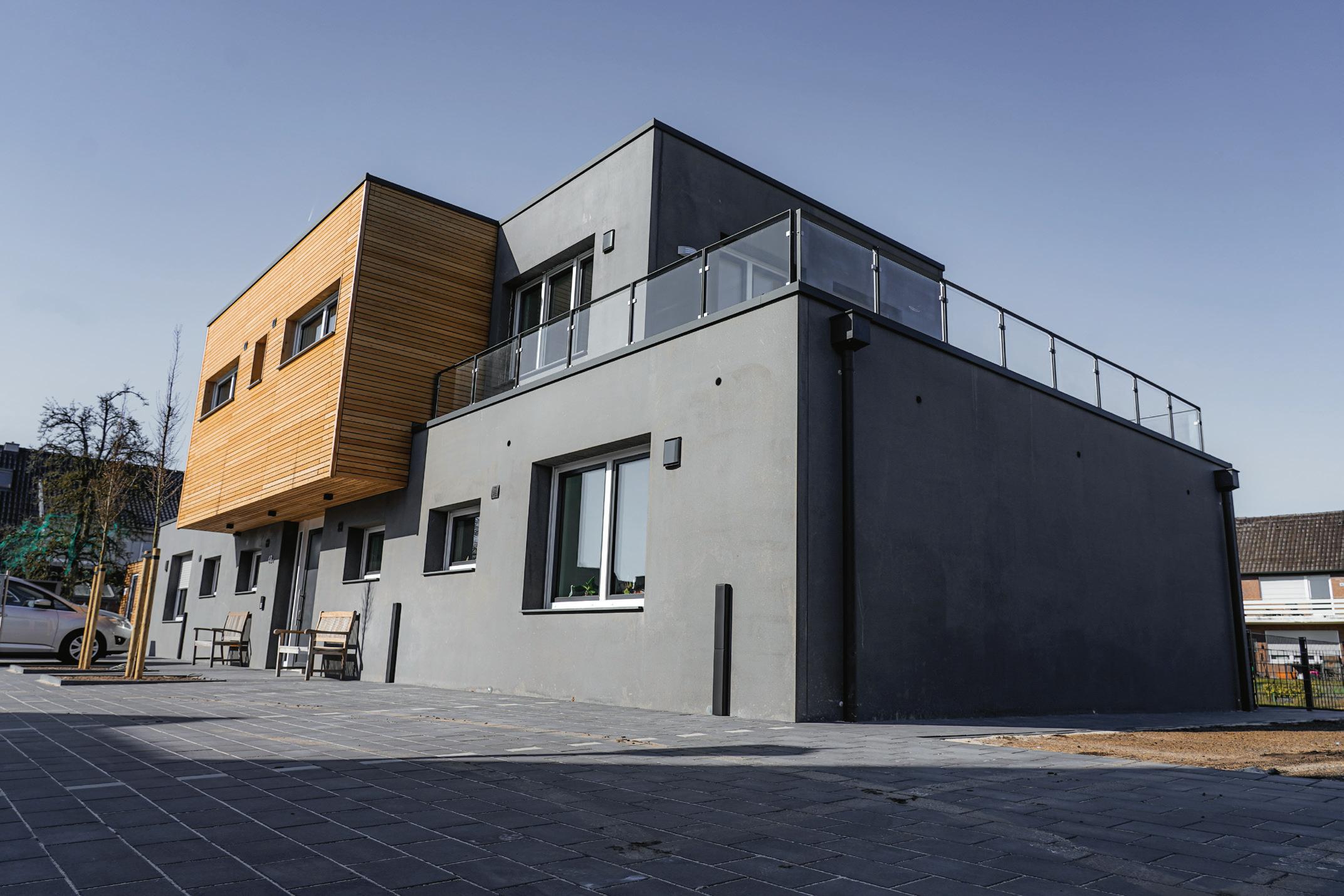
According to Büscher, the main advantage of the certified production process is the efficiency of resources. The company is using local, highly available C&D materials that produce a sustainable, climate-neutral product with less carbon dioxide emissions. This also saves on transport costs, since the materials are already on hand.
“No costly raw materials are used, so the price of the end products is also cheaper. A real win/win situation,” says Thomas Overbeeke, operations manager at Büscher.
While the research took nearly a decade, it took Büscher only four months to build the entire house. Built with paint-ready prefab elements, the piping and electricity are all integrated into the prefab panels which have a smooth surface so no plaster is needed. And when it is time to demolish it, the house will be recycled into new concrete using the Büscher method.
Sustainable Production
Since Büscher believes that a sustainable product should be produced with sustainable equipment, the Büscher site is equipped with solar panels delivering up to 323 kW/h of renewable electricity. This electricity is not only used to power the concrete facility, but also powers an electric Keestrack R3e ZERO impact crusher and a K4e ZERO screen.
The choice to use Keestrack crushing and screening equipment is part of Büscher’s goal to minimize its ecological footprint. When plugged into the grid, the R3 and K4 produce zero carbon emissions with energy savings totalling approximately 152kWh. Operational and maintenance costs have also decreased drastically since there is no engine on board to maintain.
The R3e ZERO is equipped with a vibrating feeder with a pre-screen of 1,200 mm by 920 mm to optimize crushing results
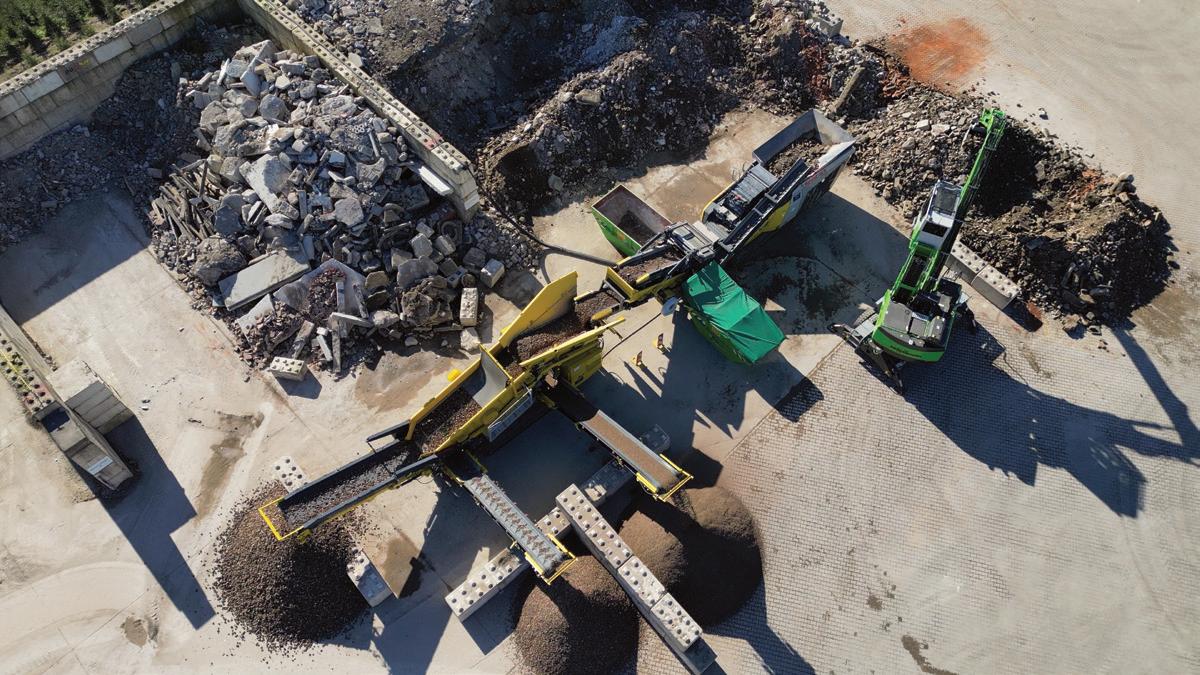
Thomas Overbeeke Operations Manager, Büscher
and minimize wear. The machine has an inlet opening of 770 mm by 960 mm and a rotor diameter of 1,100 mm. The installed wind sifter eliminates contaminations of plastics, wood, or paper, and the overband magnet separates out metals.
The K4e ZERO offers high productivity with a capacity of up to 350 tph. The double-deck screen box of 4,200 mm by 1,500 mm, standard heavy-duty plate apron feeder, and a hydraulic adjustable screen angle give it enhanced screening capabilities. The numerous options and screen decks available make the K4 suitable for a wide range of applications. The Büscher recycling site chose to have the fine and middle fraction conveyor on the same side of the screen to improve accessibility for the wheel loader.
Both Keestrack machines at Büscher are equipped with remote controls to operate the crusher and screen from the excavator and come equipped with a Keestrack-er UMTS system. The telematics software system provides real-time data and analytics that enables users to check the location of the machines and see if they are working correctly.
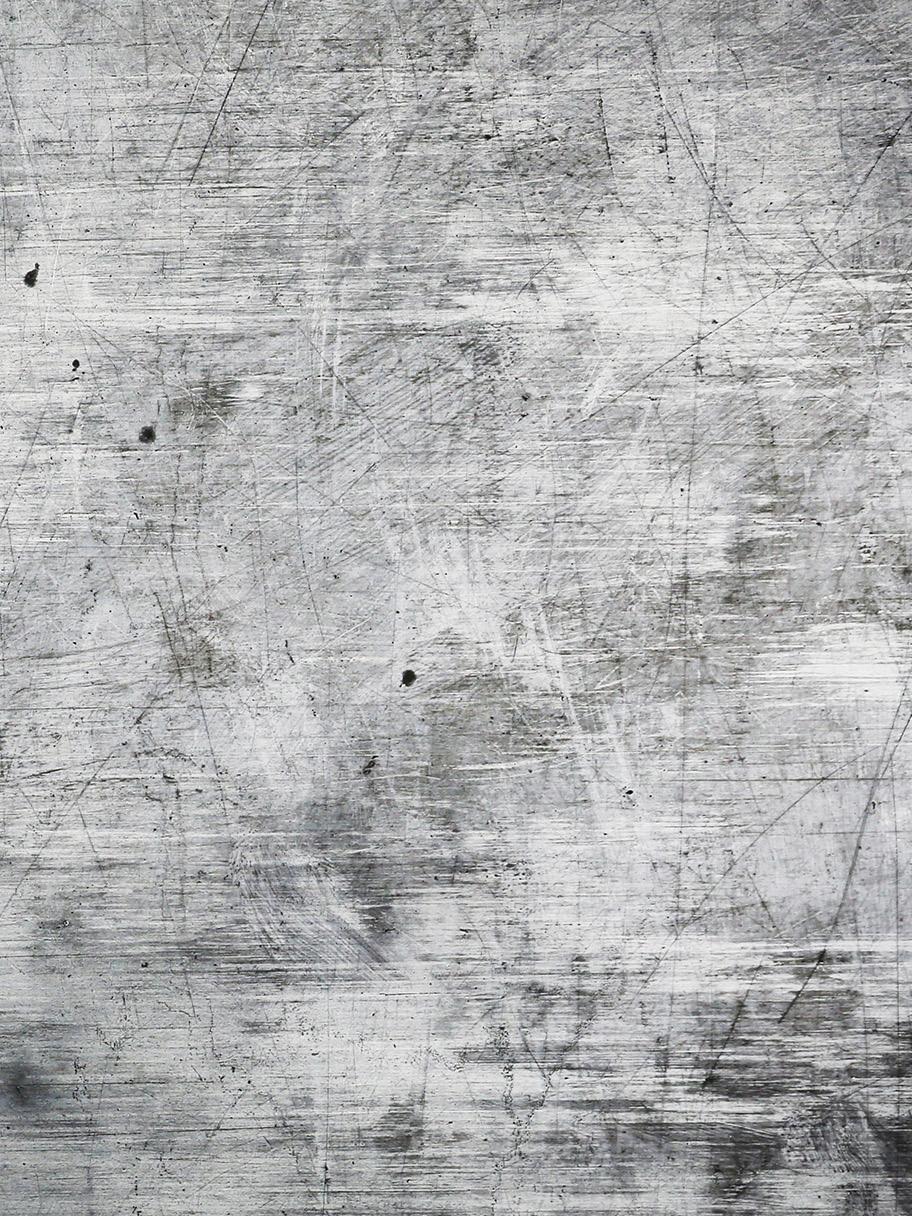
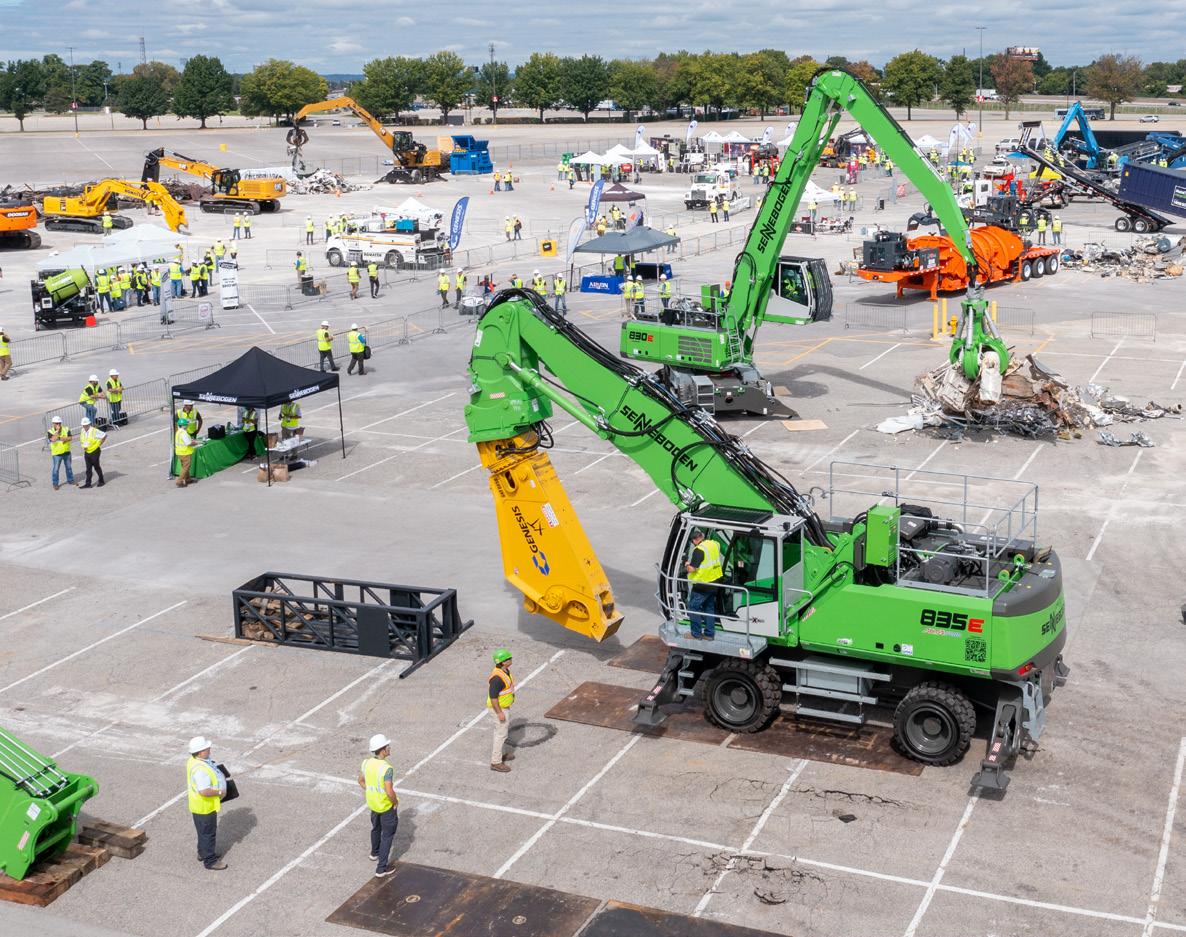