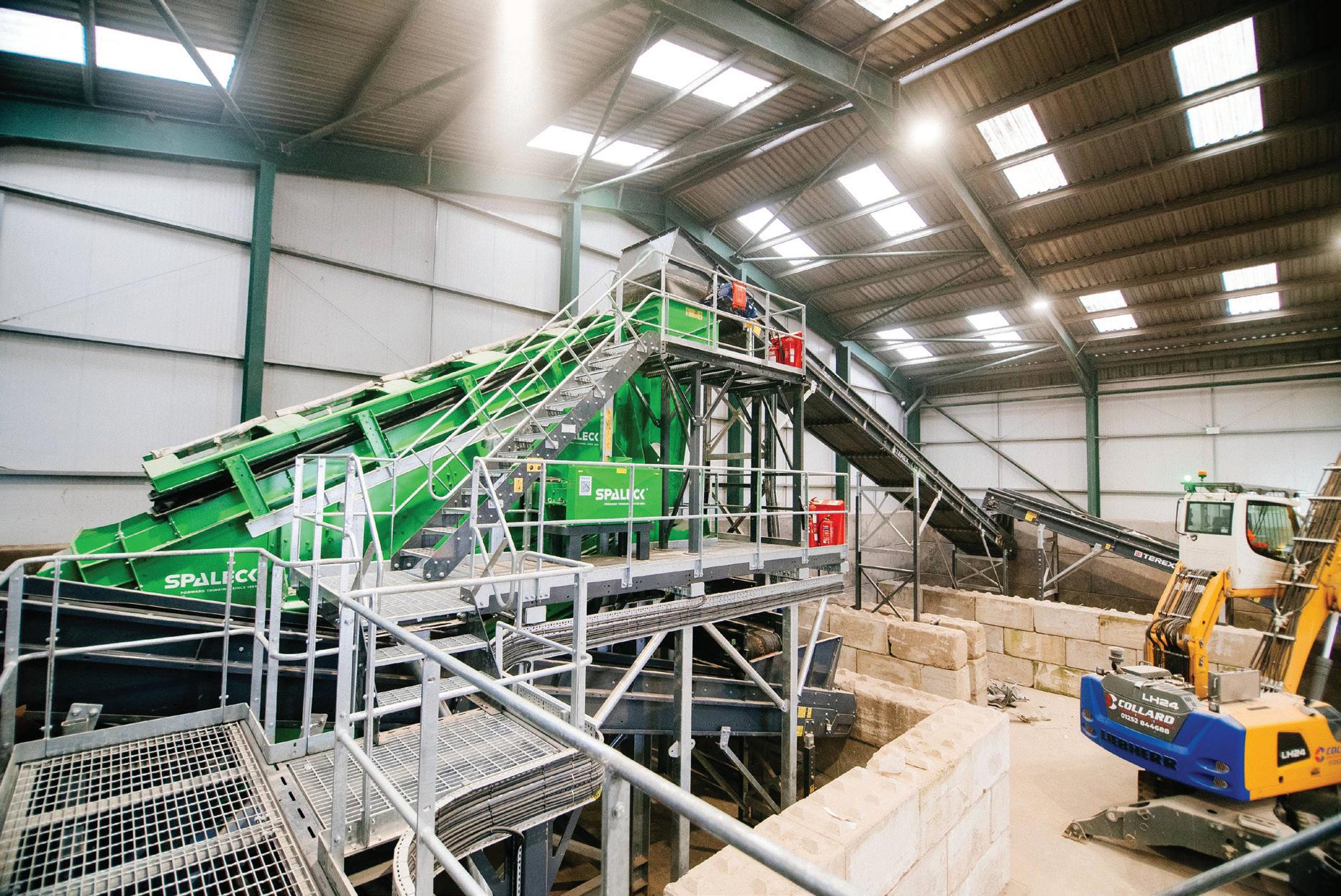
3 minute read
FIRST TEREX RECYCLING SYSTEMS PLANT INSTALLED AT C&D AND C&I RECYCLING FACILITY
THE PLANT WILL HELP COLLARD GROUP RECOVER CLEANER PRODUCTS OF HIGHER VALUE
Collard Group has chosen a Terex Recycling Systems plant to increase the processing capacity of its site and recover cleaner products of higher value without adding to the manual labour requirements. Collard Group initially intended to upgrade the plant, but opted for a full plant installation after being pleased with the first phase of the installation.
A Customized Solution
The plant, which is the first Terex Recycling Systems installation, was tailored to suit Collard Group’s site and the material which would be fed into it. Terex Recycling Systems developed a process that incorporated advanced mechanical separation that increases Collard Group’s processing capacity and recovers products of a higher purity than what was previously achieved. The team worked with space constraints such as fitting the plant inside and around the existing building, all while planning the installation around Collard Group’s site works, including the erection of a new building.
Close collaboration between all parties ensured our requirements in terms of output were met, whilst also keeping the plant footprint to a minimum to aid their site operations.
Robert Collard Managing Director, Collard Group
“Terex Recycling Systems and Molson Green worked with us to ensure the design, delivery, and installation of our new plant worked around our site operations, also taking into con- sideration our site preparation works to include foundations, building modifications, and power supply,” says Robert Collard, managing director at the Collard Group. “Close collaboration between all parties ensured our requirements in terms of output were met, whilst also keeping the plant footprint to a minimum to aid their site operations.”
SORTING, SEPARATING, AND SUCCESS
The process starts with skip material being loaded into a waste feeder and conveyed to a combi screen, which separates material into four size fractions using a combination of 3D and flip-flow screening (0 to 10 mm, 10 to 50 mm, 50 to 100 mm, and over 100 mm). Overband magnets recover ferrous metals from 0 to 10 mm, 10 to 50 mm, and 50 to 100 mm, and air separators remove light material from 10 to 50 mm and 50 to 100 mm. A manual quality control picking station has operators working to remove any remaining contaminants from the 10 to 100 mm heavy fraction.
Following this, an eddy current separator recovers non-ferrous metal from the 10 to 100 mm heavy fraction. Another manual picking station has operators recovering materials such as wood, card, and plastic from the over 100 mm fractions, and an overband magnet recovers ferrous metal. Finally, an air separator removes light material from the over 100 mm fractions.
The outcome is a plant that is processing skip waste – a mixture of commercial and industrial (C&I) and construction and demolition (C&D) waste – to produce 0 to 10 mm fines, ferrous metals, clean 10 to 100 mm heavy fraction (inert), non-ferrous metals, wood, plastic, paper, and card, and clean over 100 mm heavy fraction (inert) materials.
“We are delighted to have sold and installed Terex Recycling Systems’ first plant to the Collard Group,” says Thomas McKiver, sales director at Molson Green, distributor of Terex Recycling Systems. “This plant will help them achieve their desired targets of increasing processing capacity and to recover greater percentages of cleaner recycling products, thus diverting more material from landfill.”
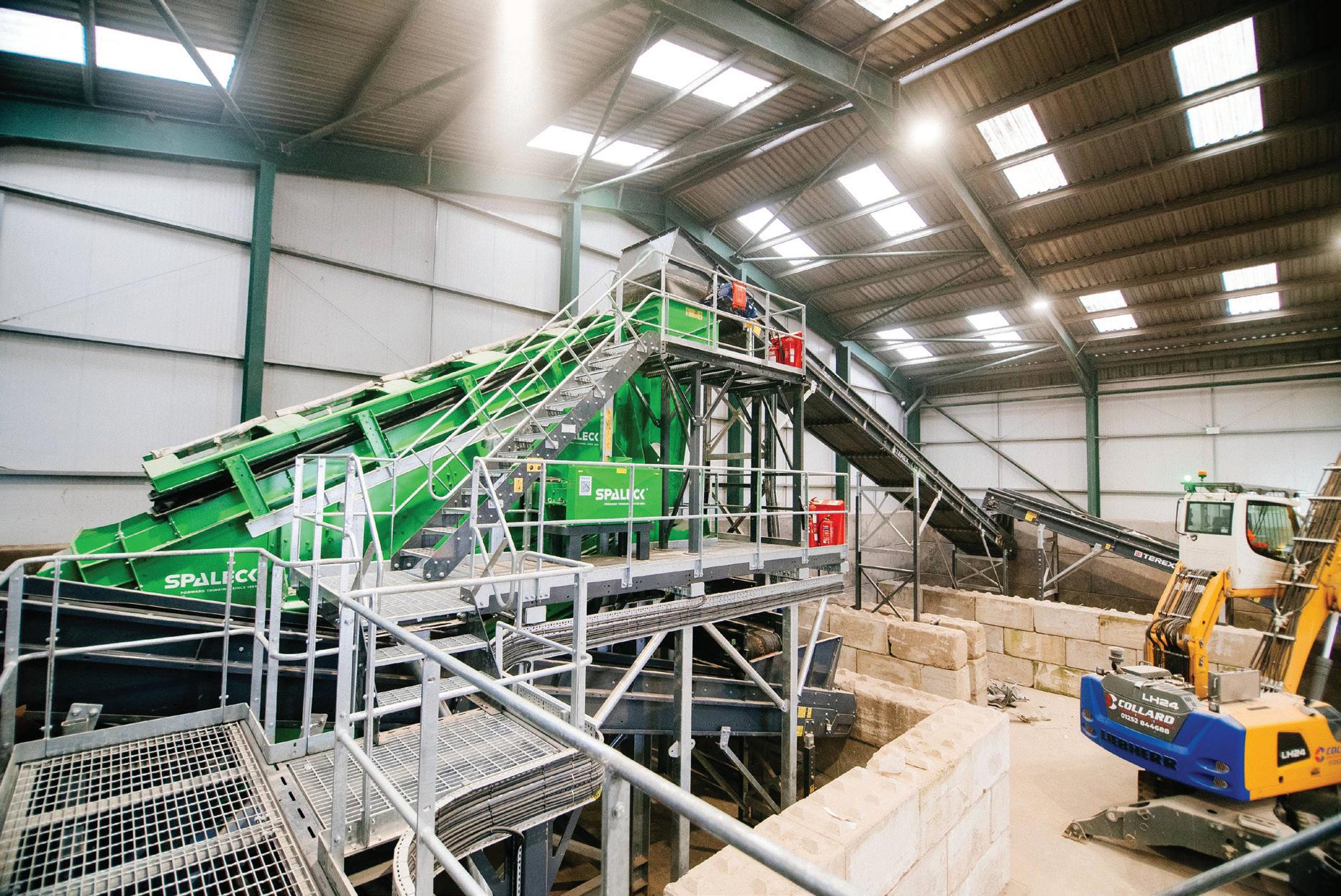
A Growing Network
This installation comes on the heels of Terex Recycling Systems expanding its distributor network to include Powerscreen of California, and Frontline Machinery and Voghel in Canada. All three distributors will represent the full range of Terex Recycling Systems’ modular recycling solutions for their respective territories. These new appointments have been made following the recent amalgamation of the sales teams for Terex Recycling Systems and ZenRobotics.
“In the next 10 years, stationary recycling systems are expected to grow more than double compared to the mobile recycling equipment,” says Marcel Vallen, sales manager of North America at Terex Recycling Systems and ZenRobotics. “Selling affordable and modular recycling systems, with the latest cutting-edge technologies, is what customers across North America are looking for. Every operator knows how important it is to have local sales, service, and parts support. Thanks to a well-established relationship with other Terex brands, Powerscreen of California, Frontline Machinery, and Voghel are well-placed to seamlessly integrate Terex Recycling Systems and ZenRobotics into their operations. They are great partners to have and are essential to our success in the North American market.”