
6 minute read
Veolia Water Technologies and the next generation of Water Distillation Technology
In this issue of Industrial Process News, we are pleased to feature Veolia Water Technologies as our Water Treatment Solutions and Services Company of the Month.
Veolia Water Technologies is the UK’s leading provider of water treatment solutions and services. Originally founded in Paris in 1853, it has been trading in the UK for over a century, providing customers with access to a wealth of water treatment experience and expertise across multiple sectors. Amongst its many services and solutions for the industrial sector, Veolia can provide process and wastewater recovery systems as well as industrial wastewater and sewage treatment. Veolia also specialises in providing water pretreatment for all types of feed water and influent, in addition to technology for the production of manufacturing process water.
Based in High Wycombe, Buckinghamshire –with offices in Birmingham, Stoke-on-Trent and Glasgow – Veolia Water Technologies provides a range of solutions designed to tackle the evolving challenges of water processing. One of its latest solutions is the next generation of its distillation technology, Polaris™ 2.0. This latest iteration of its successful technology has been developed in response to the advancements made in pharmaceutical manufacturing, which require a constant supply of water for injection and pure steam.

At its heart, water distillation is a simple process. Water is fed into the system via the feed water inlet and then heated in an evaporation chamber, producing steam and water mist. The vapourised, gaseous substance is then passed through a separator, which removes any prevailing water droplets containing bacteria and endotoxins. Following this, the pure steam passes into a condenser system before emerging as hot water for injection. A dedicated vent line also allows for the removal of any non-condensable gases from the process.
The Polaris™ 2.0 range offers an array of standard units with different capacities in order to meet all needs and requirements. These can be equipped with an extensive number of optional extras that allow the customer to tailor the product to their needs. However, despite optional differences, all Polaris™ 2.0 units are designed and built in compliance with ASME Bioprocessing Equipment (BPE) standards. All Polaris™ 2.0 units are also fitted with a Siemens HMI Comfort Panel installed with new validated and certified software to guarantee compliance with FDA CFR21 Part 11 and GAMP V.
The newest generation of Polaris™ products comes in two skids. The first is the Polaris™ 2.0 Multiple Effect Distiller (MED), designed to guarantee a steady supply of hot water for injection (WFI) with capacities ranging from 250 to 4,500 litres per hour. With a varying number of columns to optimise utility consumption, Polaris™ 2.0 MED has been designed to reduce energy and water consumption. It utilises a falling film distillation process to ensure efficiency and a fast startup and has insulated heat exchangers and columns to reduce the amount of energy lost. Furthermore, with a blowdown level of just 10%, water waste is kept to a minimum.
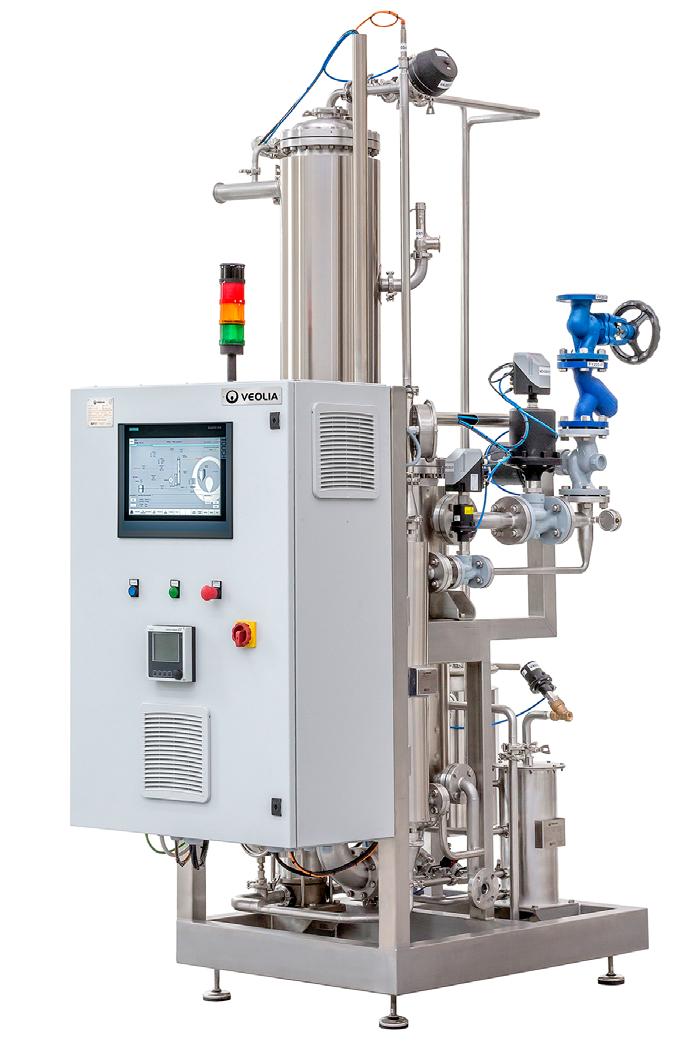
The MED is also operationally smart; this enables customers to monitor key metrics at all times, including the conductivity and temperature of WFI. For those looking to add enhanced functionality, features such as a feed water tank, blowdown cooler, automatic feedwater valve, sanitisation and automatic drain and sight glass on the columns can be added.
The second skid available is the Polaris™ 2.0 Pure Steam Generator (PSG). This provides users with a rapid-response pure steam supply, which can be used for a variety of applications, such as sterilisation in place (SIP) for bioreactors and vessels, product terminal sterilisation, lyophilizer sterilisation and sterile facility HVAC humidification.
This model is available in a range of sizes capable of producing 300 to 3,000 kilograms of pure steam per hour and up to 4 barg. Advanced droplet separation features and an integrated thermal degasser, for the removal of non-condensable gases, ensures quality and compliance with EN285. As with the MED, insulated heat column and heat exchangers, PID pressure and control and an intuitive display are all standard.
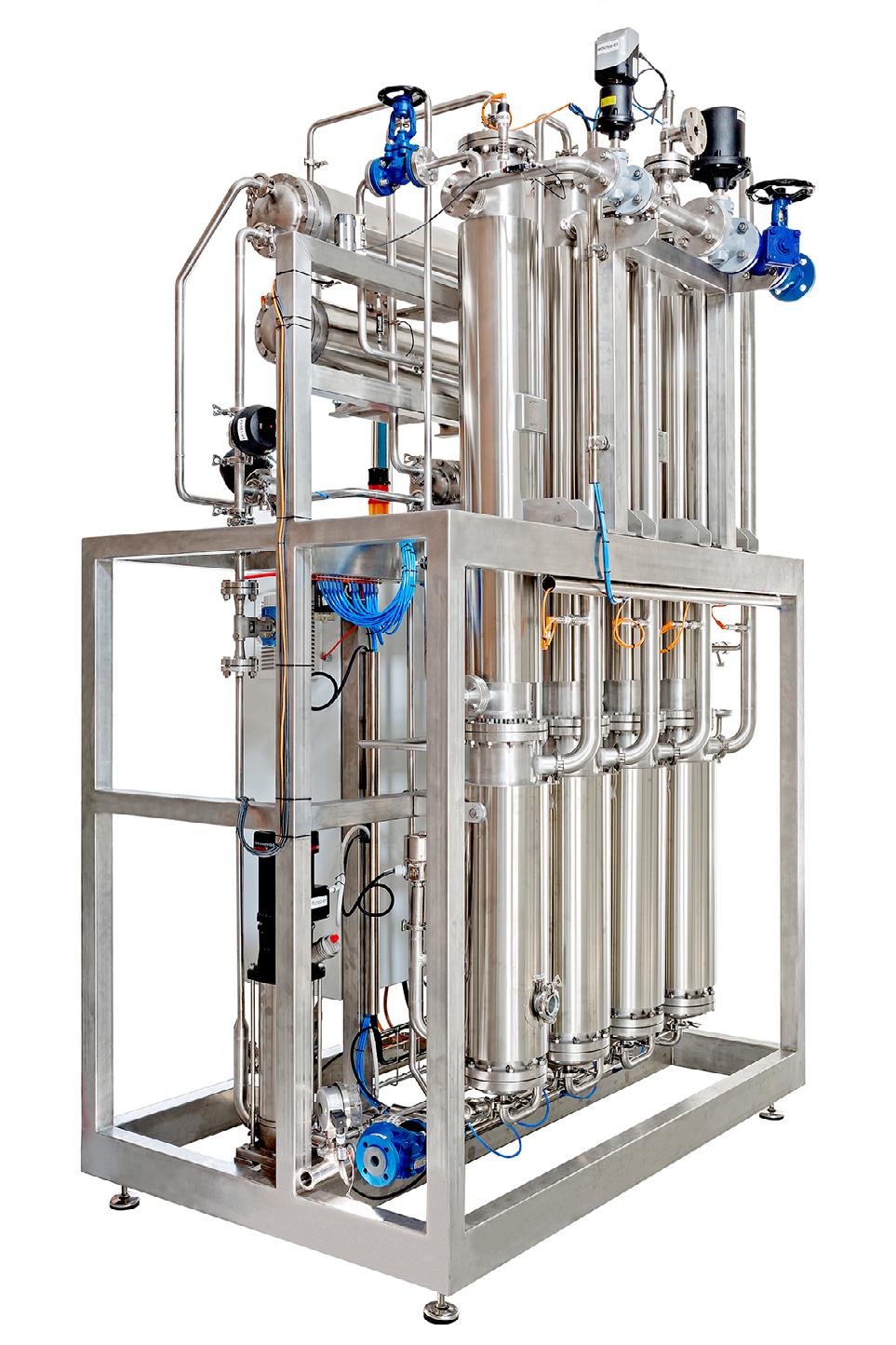
The new Polaris™ 2.0 range modernises the established distillation process by allowing for the incorporation of Veolia’s Hubgrade system – a cloud-based monitoring service that provides all necessary operational information and alerts in addition to advanced data analysis. This enables faster on-site issue resolution and facilitates easier collaboration with Veolia’s engineers. With this in mind, Veolia Water Technologies offers a full suite of servicing and after-sales support that utilises its technological solutions to prevent, predict and remediate issues before they arise.
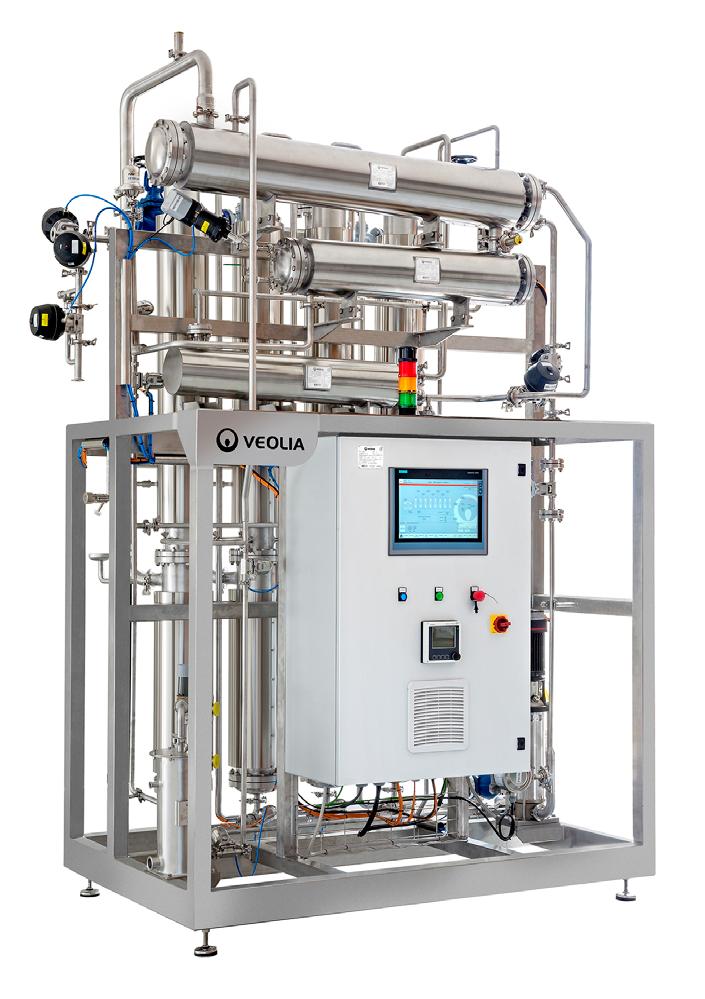
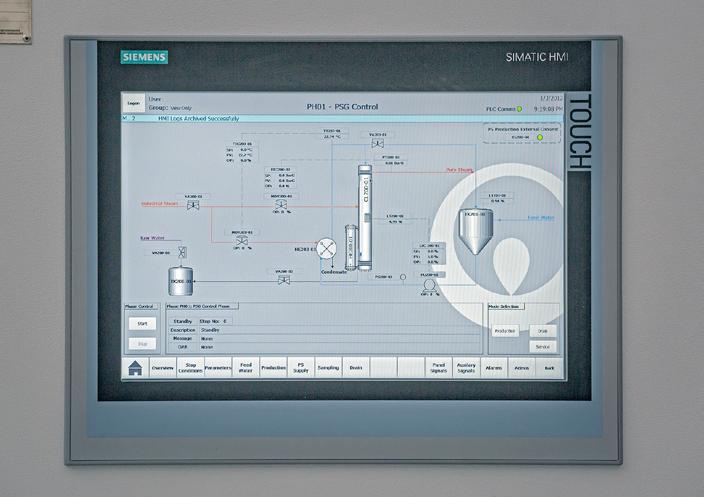
In addition to these digital aids, both models have 304 stainless steel frames that allow for easy maintenance. Veolia Water Technologies also has a full suite of packages designed to ensure continued functionality and efficient production. This includes a combination of preplanned services and real-time repairs based on data inputs via Hubgrade – significantly reducing the likelihood of costly downtime.
Regardless of which Polaris™ 2.0 model is chosen, customers can take advantage of a range of benefits specifically designed to enhance production and aid cleaning processes within pharmaceutical manufacturing facilities. Whether this is saving water and energy via the efficient production of WFI and pure steam, having the flexibility to scale output in line with demand or taking advantage of smart maintenance through integration with Hubgrade.
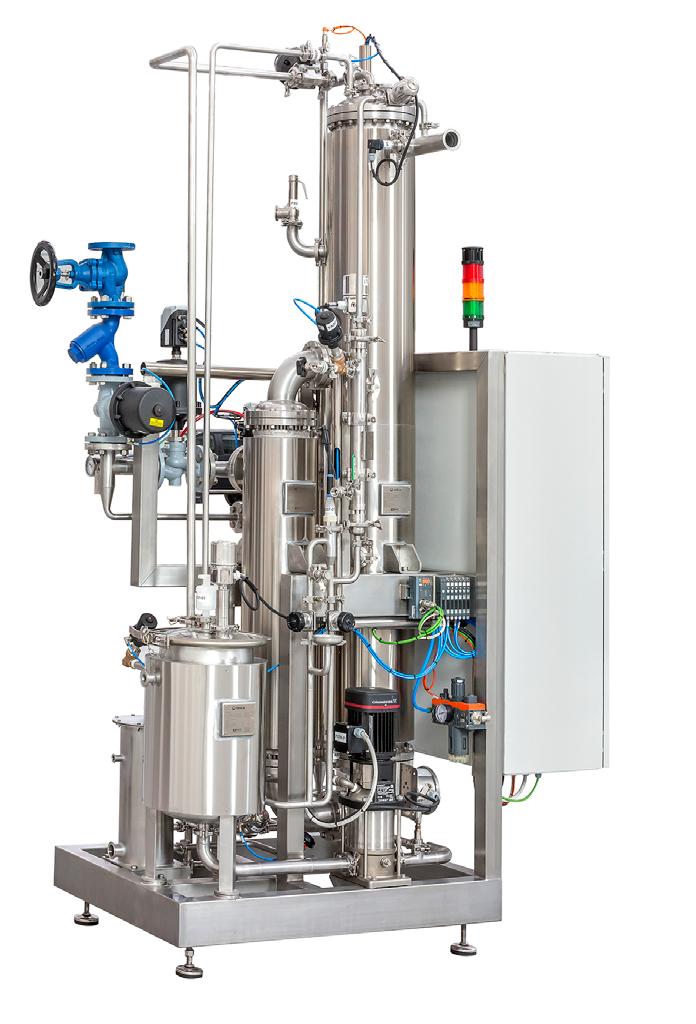
Distillation methods for the production of WFI and pure steam have stood the test of time. However, Veolia Water Technologies continues to demonstrate that by evolving existing methods and improving them with modern technology, simple methods of production can continue to be the best option for a broad range of applications.
Finally, when determining which system is best for your needs, there are a number of technical considerations to take into account as well as the specific needs of your operation. Rest assured, the team of experts from Veolia Water Technologies will be able to advise which system best suits your needs and support you throughout the implementation process.
If you want to find out more about our water treatment solutions, download a brochure or contact a sales representative, please visit: www.veoliawatertechnologies.co.uk